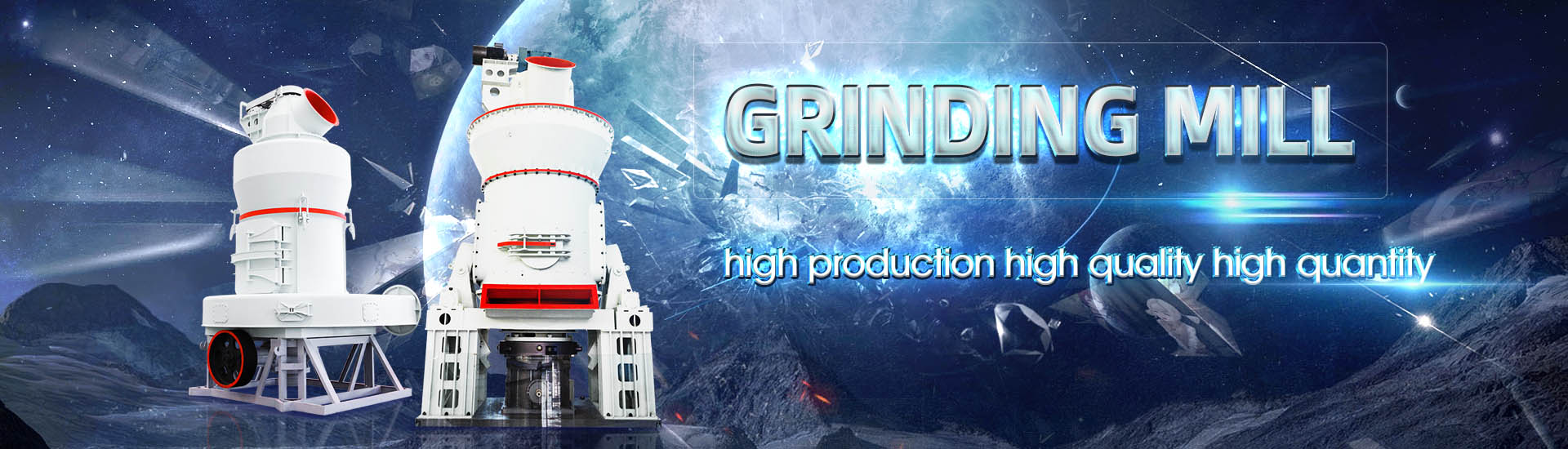
WP800 ore mill exhaust gas generation
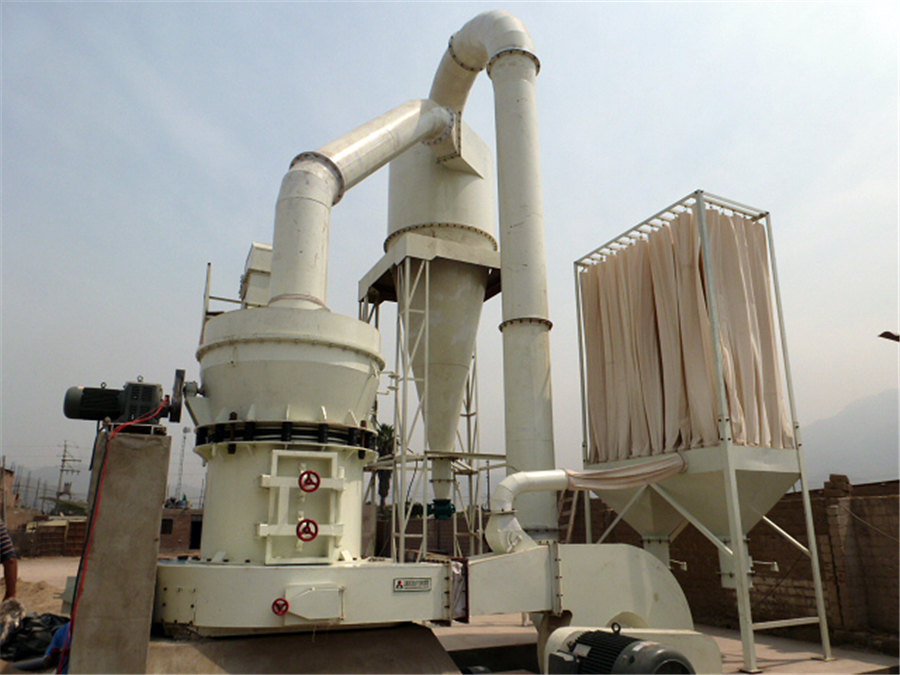
ReviewWaste heat recovery in iron and steel industry using
2023年12月1日 For the rolling mills, an averaged potential power of 687 kW per ton generated each hour was revealed from six examinations, while for the EAF exhaust gas, an averaged 2021年3月10日 To this end, the performance of an ORC unit coupled with different waste heat resources such as hot air from clinker cooling, exhaust gas from rolling mill reheating furnace, A review of industrial waste heat recovery system for power Waste heat recovery systems produce power from exhaust heat downstream turbines and engines, avoiding the use of polluting fossil fuels responsible for NOx, SOx and CO2 ORC systems for waste heat recovery from gas turbines and 2023年4月15日 Furthermore, HRSG uses selective catalytic reduction equipment to reduce the concentration of nitrogen oxides in the exhaust gases released into the environment They Current progress of process integration for waste heat recovery in
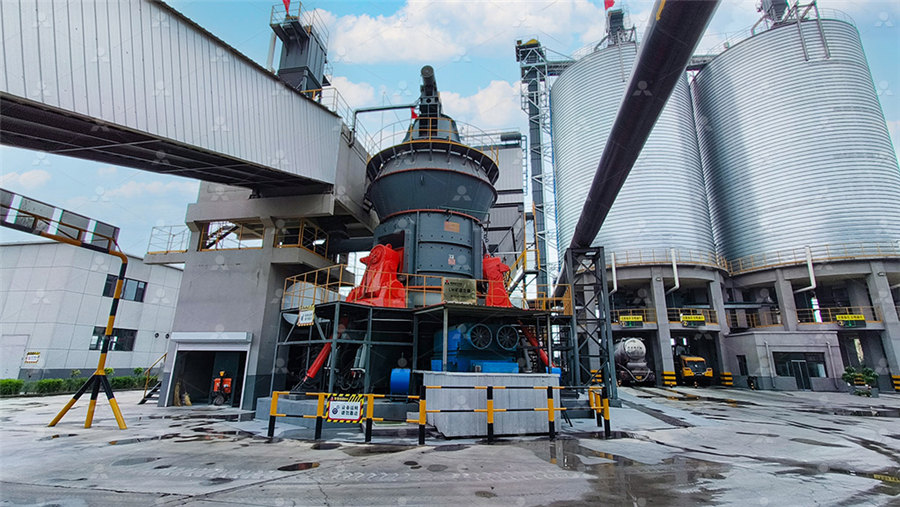
Performance evaluation of an ORC unit integrated to a waste heat
2017年9月1日 Based on these technologies, we develop possible process layouts including the transition to Oxyfuel ladle preheating, onsite utilization of the CO2rich product gas and off 2013年7月1日 This study models ORCs powered by three heat sources over a range of energy scales and compares results of each case The heat sources are energy recovery from Organic Rankine cycles in waste heat recovery: a comparative studyA waste heat recovery system extracts thermal power from the exhaust gas of the industrial plant to feed the ORC module via the intermediate fluid This fluid, usually oil, pressurized water or Organic Rankine Cycle for waste heat recovery systems Exergy2019年9月11日 The organic Rankine cycle (ORC) subsystem recovered energy from the exhaust gases of internal combustion engines to produce mechanical power Through a A Waste HeatDriven Cooling System Based on Combined Organic
.jpg)
Process flow diagram: Waste heat recovery, steam generation and
The furnace exhaust gas is used to produce saturated steam in a heat recovery unit Technoeconomic case study on Oxyfuel technology implementation in EAF steel mills – Concepts for 2022年7月10日 Effect of moisture in heat source to performance of power generation cycles is studied Moisture in heat source increases cycle net power output and reduces cycle exergy Exploring lowgrade heat in exhaust gases with moisture via power 2017年2月1日 This work focuses on the characterization of heat generation during dry fracture by direct impact of a tantalum ore Moreover, an attempt was made to quantify the heat energy loss to the Heat generation model in the ballmilling process 2017年2月13日 Flue gas recirculation (FGR) has been implemented for exhaust gas emissions reduction in iron ore sintering However, the mechanism of NO x reduction through FGR is still unclear In this paper, the laboratory potgrate sintering test showed a 30% reduction in gas flow and 1551% reduction in NO x emissions achieved with a 30% FGR ratio, and the sinter NO x Reduction in the Iron Ore Sintering Process with Flue Gas
.jpg)
Exhaust Gas Treatment in Thermal Power Plants: A Review
International Journal of Advances in Scientific Research and Engineering E(ijasre)ISSN : 2454 8006 DOI: 1031695/IJASRE201933630 Volume 5, Issue 11 November 2019Kiln Energy Recovery Evaluation Potency, in Cost estimate, GJ/hour in USD 000 No Energy Recovery Risk 1 Kiln offgas for coal mill hot gas 1419 100 low 2 Kiln offgas for rotary dryer air preheater 1368 200 low 3 Kiln heat loss for kiln air preheater 111 200 medium 4 Kiln offgas for rotary dryer air hot gas ~100 2,000 medium 5 Kiln off Study of rotary kiln offgas energy recovery for coal mill hot gasDownload scientific diagram Airflue gas cycle of coalfired power plant from publication: An investigation of performance characteristics and energetic efficiency of vertical roller coal mill Airflue gas cycle of coalfired power plant ResearchGateExergoeconomic analysis of the power generation system using blast furnace and coke oven gas in a Brazilian steel mill Silvia Nebra The rational use of energy has become a priority for all industries in Brazil, mainly after the energy rationing in 2001Exergoeconomic analysis of the power generation system using blast

Maximizing Sintering Plant Heat Recovery 1 Energy Balance in
On the other hand, cooling gas temperature rises up to the level of 180 degC, cooling capability may decrease Fig8 compares the temperature of ore and gas in both types Sintered ore temperature at outlet of cooler rise approx 30 degC in circulation type Temperature difference is small enough not to affect sinter plant commercial Per tonne of coke that is produced, approximately 470Nm 3 of coke gas are produced 60% of this volume is typically needed for internal processes; the remaining part can be used for power generation with GE’s Jenbacher gas engines resulting in approximately 400kWh Per tonne of steel produced through the LD process approximately 50Nm 3 of converter gas are released Blast Furnace, Coke Gas and Converter Gas for Power Production2018年8月1日 Within the cross‐industry approach of Carbon2Chem® the synthesis of methanol from steel mill exhaust gases is a promising way to close the carbon cycle based on additional sustainably produced H2Methanol Synthesis from Steel Mill Exhaust Gases: Challenges for 2017年9月1日 The transitional change on the implementation of iso 14001: 2015 in Copper Ore Mill Case studyThe transitional change on the implementation of iso 14001:
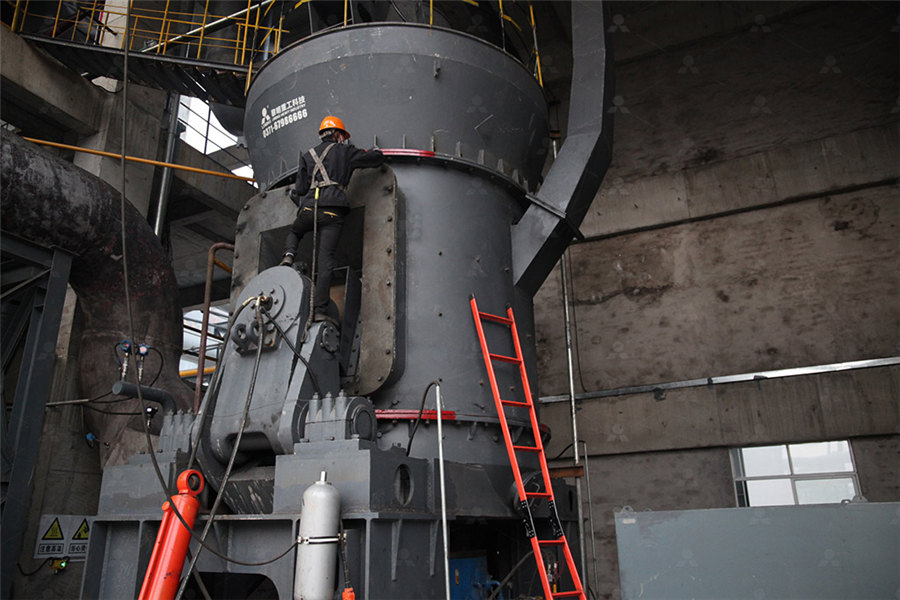
Busch rolling mill fume control
• Iron Ore Mining • Lead Ore and Zinc Ore Mining • Copper Ore and Nickel Ore Mining • All Other Metal Ore Mining • Dimension Stone Mining and Quarrying • Construction Sand and Gravel Mining • Hydroelectric Power Generation 水力发电 • Fossil Fuel 化石燃料2024年5月1日 Volume fraction of water vapor in the exhaust gas of the air preheater outlet % 155: 84: Water dew point of the exhaust gas of the air preheater outlet °C: 533: 427: Acid dew point of the exhaust gas of the air preheater outlet °C: 914: 871: Total flow of the exhauststeam: t/h – 1322: Amount of water recovered in the exhauststeam A green and efficient lignitefired power generation process 2012年12月1日 Energy audit was carried out for a steel bar Rerolling mill Measurements were made for fuel consumption before and after the installation of a recuperatorWaste Heat Recovery in Steel Bars ReRolling Mill2022年7月10日 Heat load characteristics of a 120 °C wet exhaust gas is examined and shown in Fig 1 at different moisture contents (u)The results resemble those in Maalouf et al (2016) where a typical “Raw Mill” exhaust gas was used Initially, the gas temperature drops quickly with the release of the heat, until the dew point is reached, and the curve become flatExploring lowgrade heat in exhaust gases with moisture via
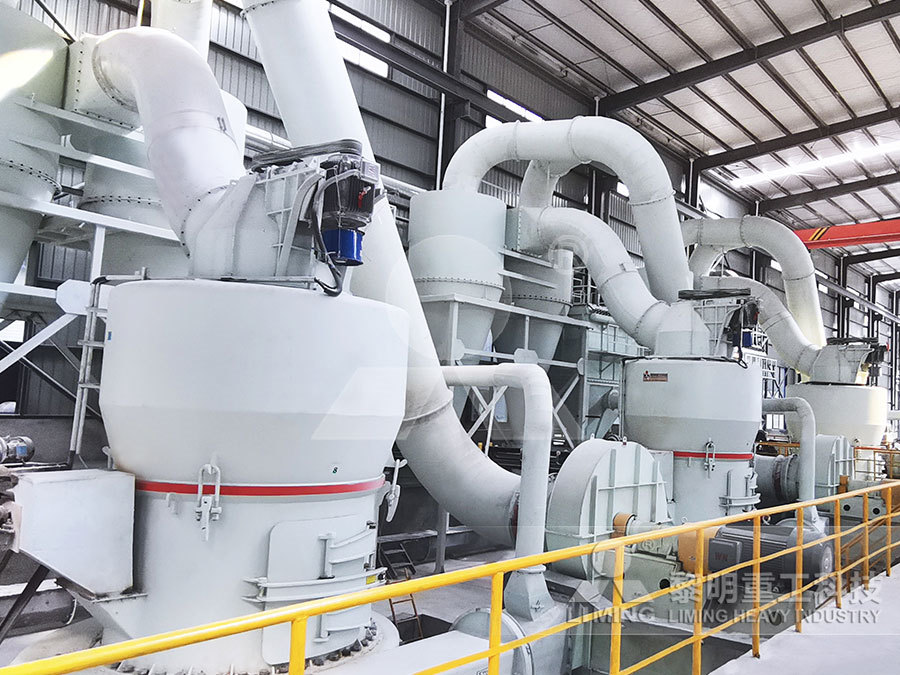
Blast Furnace an overview ScienceDirect Topics
Lump ore may be charged directly to a blast furnace but only after it has been suitably sized and screened to remove overand in Fundamentals of Thermal and Nuclear Power Generation, 2021 Blast furnace gas Blast furnace gas is produced from the blast furnace in a steel mill This gas has 23% of carbon monoxide, 60% of nitrogen, and 14% of 2020年11月9日 This paper primarily proposes hydrogen generation by reaction of silicon slag with water via wet grinding Meanwhile using hydrogen generated realized the purification of MGSi by flotation(PDF) Hydrogen generation during the purification of metallurgical 2022年5月16日 In the present work, the contemporary exhaust gas treatment systems (EGTS) used for SOx, PM, and NOx emission mitigation from shipping are reviewed Specifically, Marine Exhaust Gas Treatment Systems for Compliance with the 2020年8月30日 Abstract The recovery and reuse of waste heat offers a significant opportunity for any country to reduce its overall primary energy usage Reuse of waste heat improves the ambient air quality by reducing both industrial pollution and greenhouse gas emissions from industries This paper presents an estimation of thermal waste heat potential in five energy Estimation of waste heat and its recovery potential from energy
.jpg)
Power Generation for the Pulp and Paper Industry GE Vernova
We decided to rely on GE [Vernova]’s proven aeroderivative gas turbine technology to improve the efficiency, power output and lifetime of our power generation assets, while reducing the cost of electricity and improving our plant’s profitability" In 1998, DS Smith Paper Italia built a 100MW paper mill in the Tuscan province of Lucca2022年7月1日 In addition to these options, there has been a steady increase in the attention paid to carbon capture, utilization, and storage (CCUS) in recent years [6, 7]The concept of CCUS is that CO 2 is captured from the flue gas emitted by power or industrial processes or even from the atmosphere, and the captured CO 2 is used in the manufacturing of products or is Analyzing flue gas properties emitted from power and industrial 2018年7月30日 This review explores circular economy principles in regard to ethanol production from papermill sludge Environmental sustainability and renewability over fossil fuels make second generation (PDF) Wastes from pulp and paper mills A review of 2020年3月31日 GAS TURBINE DIRECT EXHAUST GAS In the vitrified tiles plant in India with design capa city of 36 mill m for single stage absorption chiller is from 07 to 09, while for m ore GAS TURBINE DIRECT EXHAUST GAS INTEGRATION
.jpg)
Exhaust Aftertreatment Technology for Engine Driven Generator
A Exhaust inlet carrying PM B Filter extracts PM C Outlet exhaust PM within EPA limit Diesel Particulate Filter (DPF) B C A Figure 3 NO Injection Ammonia (Urea) Nitrogen Oxides Ammonia Nitrogen Water/Steam SCR Catalytic Converter Diesel Exhaust Gas Selective Catalytic Reduction (SCR) NH3 N2 H2O Figure 2 Figure 1, 2 and 3 depict three 2011年1月1日 until the exhaust gas [27][28][29][30]In previous studies on the use of the catalyst for iron ore or mill scale the waste generation factor developed was 3493kg per ton (PDF) Recycling of mill scale in sintering process Science of new pelletizing plant, next to the iron ore beneficiation plant at Vargem Grande, in Nova Lima – MG – Brazil The plant was designed to produce 70 Mt/y of pellets with expected startup in 2008 This paper shows the gas flow distribution rearrangement done during the design phase of the project The gas flow pattern suggested in theGAS FLOW IMPROVEMENT IN A PELLETIZING PLANT 1 ABM 2013年9月1日 This paper advances a novel lignitefired power generation process based on a OPSB (boiler with an open pulverizing system) and the recovery of water from millexhaust after the comprehensive An environment friendly and efficient lignitefired power generation
.jpg)
Methanol Synthesis from Steel Mill Exhaust Gases: Challenges
2018年8月20日 As blast furnace gas is by far the largest steel mill exhaust gas stream, its utilization plays a crucial role in reducing the CO 2 emissions In addition to the development of novel catalysts for an integrated methanol concept, optimized reaction conditions for commercially available catalysts have to be determined to achieve fast implementation in the near future2019年3月29日 Energy recovery of 142 GJ/hour can be achieved with additional environmental benefit from 803% reduction in consumption of fossil fuel for coal mill hot gas generation Discover the world's researchStudy of rotary kiln offgas energy recovery for coal mill hot gas2009年8月1日 Mill scale is an iron oxide waste generated during steelmaking, casting and rolling Total generation of mill scale at JSWSL is around 150 t/day and contains 60–70%FeO and 30–35%Fe2O3Recycling of steel plant mill scale via iron ore ResearchGateThe flue gas is recirculated back to the raw mill using a precalcinator arrangement The kiln gas is used to sweep the mill of finely ground raw feed particles The temperature in the raw mill is typically between 90 and 120°C In this manner the raw Kiln Exhaust Gas Treatment Options
.jpg)
Heat generation model in the ballmilling process
2017年2月1日 This work focuses on the characterization of heat generation during dry fracture by direct impact of a tantalum ore Moreover, an attempt was made to quantify the heat energy loss to the 2017年2月13日 Flue gas recirculation (FGR) has been implemented for exhaust gas emissions reduction in iron ore sintering However, the mechanism of NO x reduction through FGR is still unclear In this paper, the laboratory potgrate sintering test showed a 30% reduction in gas flow and 1551% reduction in NO x emissions achieved with a 30% FGR ratio, and the sinter NO x Reduction in the Iron Ore Sintering Process with Flue Gas International Journal of Advances in Scientific Research and Engineering E(ijasre)ISSN : 2454 8006 DOI: 1031695/IJASRE201933630 Volume 5, Issue 11 November 2019Exhaust Gas Treatment in Thermal Power Plants: A ReviewKiln Energy Recovery Evaluation Potency, in Cost estimate, GJ/hour in USD 000 No Energy Recovery Risk 1 Kiln offgas for coal mill hot gas 1419 100 low 2 Kiln offgas for rotary dryer air preheater 1368 200 low 3 Kiln heat loss for kiln air preheater 111 200 medium 4 Kiln offgas for rotary dryer air hot gas ~100 2,000 medium 5 Kiln off Study of rotary kiln offgas energy recovery for coal mill hot gas
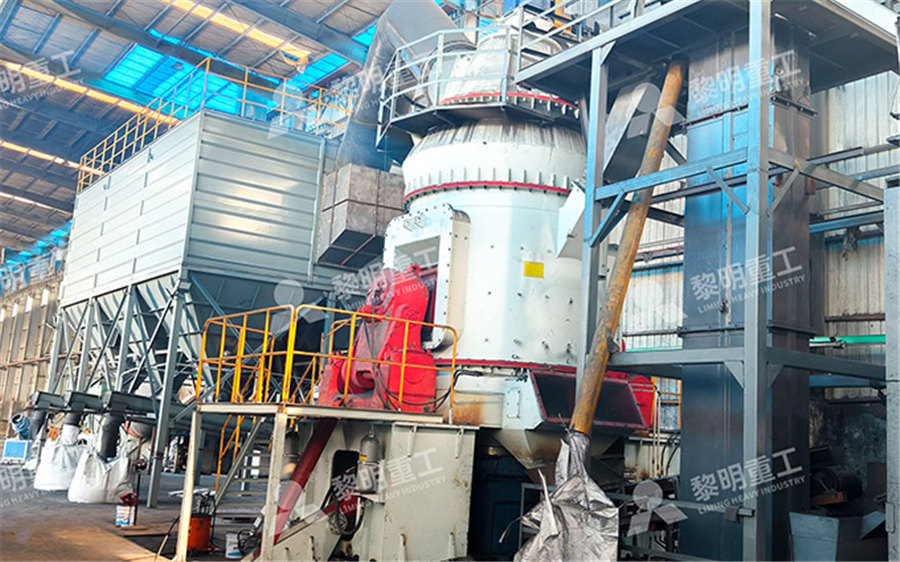
Airflue gas cycle of coalfired power plant ResearchGate
Download scientific diagram Airflue gas cycle of coalfired power plant from publication: An investigation of performance characteristics and energetic efficiency of vertical roller coal mill Exergoeconomic analysis of the power generation system using blast furnace and coke oven gas in a Brazilian steel mill Silvia Nebra The rational use of energy has become a priority for all industries in Brazil, mainly after the energy rationing in 2001Exergoeconomic analysis of the power generation system using blast On the other hand, cooling gas temperature rises up to the level of 180 degC, cooling capability may decrease Fig8 compares the temperature of ore and gas in both types Sintered ore temperature at outlet of cooler rise approx 30 degC in circulation type Temperature difference is small enough not to affect sinter plant commercial Maximizing Sintering Plant Heat Recovery 1 Energy Balance in Per tonne of coke that is produced, approximately 470Nm 3 of coke gas are produced 60% of this volume is typically needed for internal processes; the remaining part can be used for power generation with GE’s Jenbacher gas engines resulting in approximately 400kWh Per tonne of steel produced through the LD process approximately 50Nm 3 of converter gas are released Blast Furnace, Coke Gas and Converter Gas for Power Production
.jpg)
Methanol Synthesis from Steel Mill Exhaust Gases: Challenges for
2018年8月1日 Within the cross‐industry approach of Carbon2Chem® the synthesis of methanol from steel mill exhaust gases is a promising way to close the carbon cycle based on additional sustainably produced H22017年9月1日 The transitional change on the implementation of iso 14001: 2015 in Copper Ore Mill Case studyThe transitional change on the implementation of iso 14001: