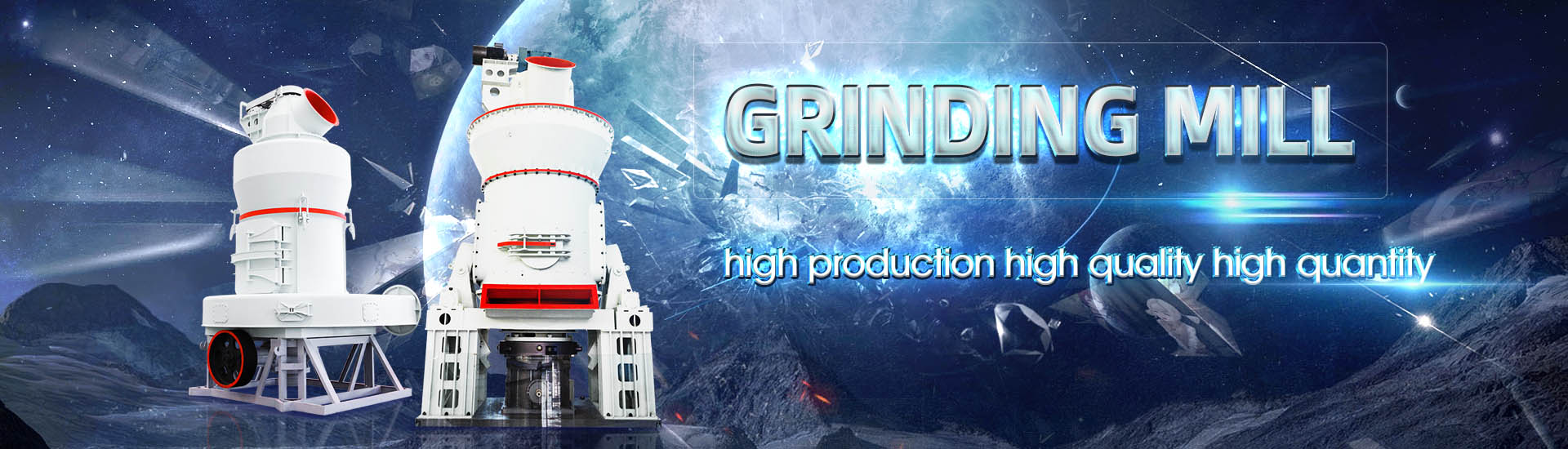
Coal mill bearing cooling

Rolling Bearings in Vertical Mills Built by Gebr Pfeiffer AG, Germany
Vertical roller mills for grinding cement raw meal and coal are the standard today in numerous cement plants achieved in the past few years in the areas of maintenance, wear protection, Depending of the type of rolling mill, dedicated roll cooling systems are required to fulfill the required functions Examples are suitable roll cooling and lubrication systems to fully utilize the GENERAL ASPECTS OF ROLL COOLING FOR HOT COLD 2015年11月1日 Coal mills are bottleneck in coal–fired power generation process due to difficulty in developing efficient controls and faults occurring inside the mills In this paper, a dynamic A unified thermomechanical model for coal mill operationRelative measurement of cooling performance of different Cold Mill Lubricants Heated aluminum block, instrumented with thermocouples, was cooled in a standard test using sprays of various Roll in Hot and Cold Rolling Mills Society of Tribologists and
.jpg)
An investigation of performance characteristics and energetic
2020年8月12日 In a power plant, the coal mill is the critical equipment, whose effectiveness impacts the overall power plant efficiency Uniform coal feeding mass flow rate and required 2019年8月1日 Cooling system is widely used in deep coal mines of China for the increasing heat hazard Although the greatly controlled air temperature and relative humidity ensured a certain Computational evaluation of cooling system under deep hot and ALSTOM Power, Stuttgart, builds modern highcapacity beater wheel mills for pulverising coal in atmospheric steam power plants These beater wheel mills are used to pulverise the crude Rolling Bearings in ALSTOM Beater Wheel Mills Schaeffler Group2024年1月1日 The study investigates the main challenges associated with high temperatures and heat damage in deep coal mining, and proposes several cooling schemes based on Numerical analysis and performance evaluation of cooling system
.jpg)
7,000,000 KILOWATTS OF INSTALLED EXPERTISE Flender
Hydrodynamic bearings rely on the formation of a lubricant bearing film generated by the rotation of the gear unit flange – the lubricant is supplied to the bearing on the inlet side This 2020年8月12日 Obtained results indicate that grinding pressure, primary air (PA) temperature and mill motor current have a tendency to rise by increasing coal feeding mass flow rates for An investigation of performance characteristics and energetic 2020年7月1日 During the operation of No2 boiler in a power plant, the fracture of a coal mill shaft occurred The fracture causes of the coal mill shaft were found by macroscopic inspection, metallographic Fracture failure analysis of coal mill shaft ResearchGateWe supply upgraded cylinders and air bags as well as replacement seal kits for the hydraulic ram cylinders on vertical grinding mills / pulverizers Upgraded Cylinders Vertical grinding mill ram cylinder units perform a vital role in the RAM CYLINDERS CHASE International
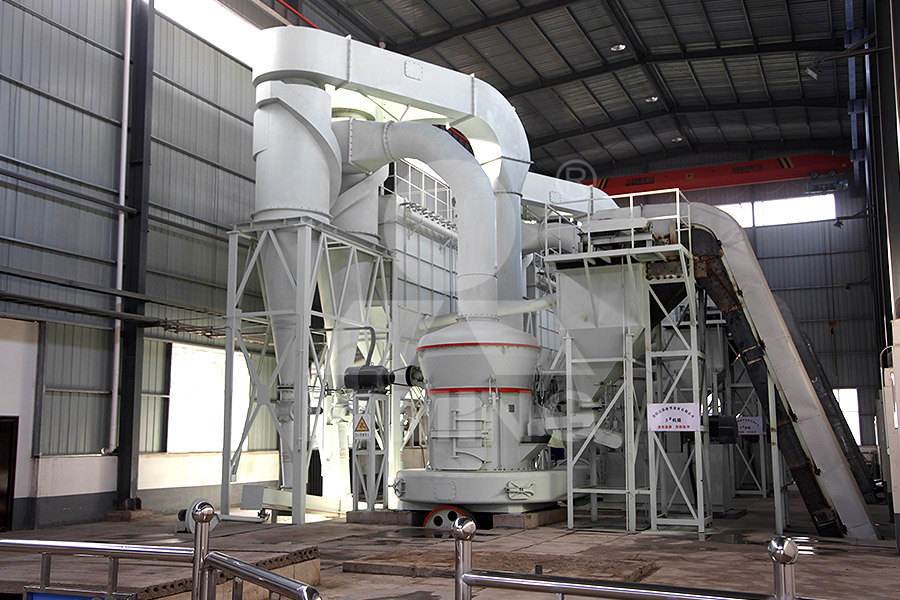
01 NGC Gears
Coal Mill Gearboxes 12 Gearboxes for Cooling Tower and Desulfurization Pumps 12 mill foundation through thrust bearing and its housing Characteristics Modular design, good component interchangeability Longer bearing life, more reasonable lubrication distributionscale from water cooled Support Roller Assemblies, coal mill bearings, pipes, liquid ring pumps, catalytic crackers, green liquor lines, cooling towers, compressors, and any system that develops mineral scale and calcium carbonate deposits Anion D’Scale is completely biodegradable and after its use can be disposed of in most municipal wasteAnion D’Scale Application: Kiln Trunnion Bearings D’ScalingOur ATOX® Coal Mill has large rollers with great grinding capability of virtually all types of raw coal The rollers work harmoniously with a highlyefficient separator and feed sluice to consistently and reliably deliver coal meal to your desired fineness and moisture levelATOX® Coal Mill FLSmidth CementAdvantages of air swept coal mill The feeding device of the airswept coal mill adopts a louvertype structure with oblique air intake, which enhances the heat exchange capacity of the mill and can effectively prevent material blocking at the entrance of the coal mill; optimize the support system, improve the lubrication structure, and reduce system resistanceAir Swept Coal Mill Cement Plant Machinery
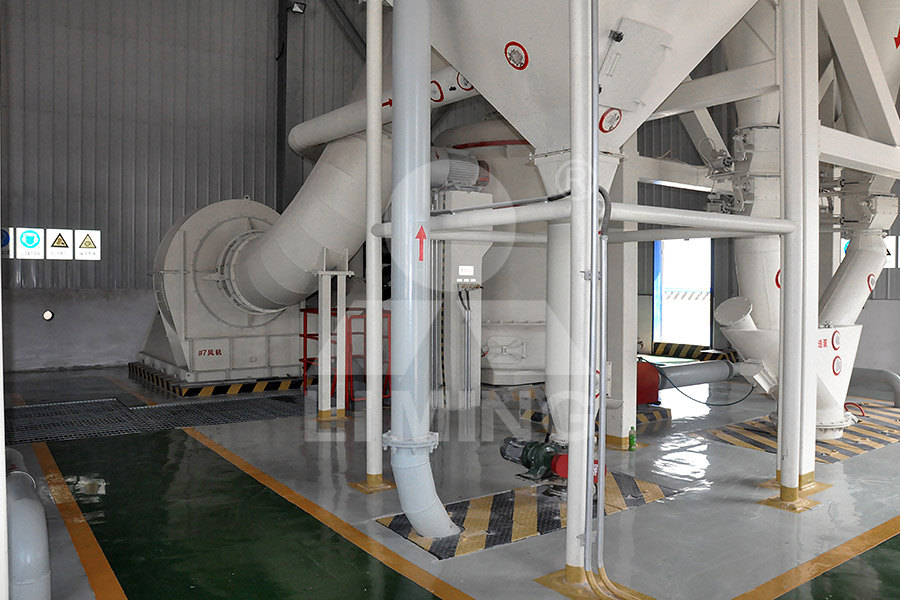
Rolling Bearings in Vertical Mills Built by Gebr Pfeiffer AG, Germany
reliability of the mills and their rolling bearings Bearings supporting the grinding rollers in the vertical mill Floating bearing end: Doublerow cylindrical roller bearing (series NNU41) Locating bearing end: spherical roller bearing (series 231) Fine product Feed material SLS high efficiency classifier for accurate classification Entirely 2024年9月22日 Turbine Bearing Cooling System: Steam turbines are the heart of many industrial operations, Coal, Gas, and Oilfired Power Plants: use of both electricity and heat This reduces the need for external energy sources, lowering costs and minimizing the mill’s carbon footprint Mechanical Drive:Turbine Bearing Cooling System EMS Power Machines2018年7月31日 Furthermore, in a modern cooler the cooling air produced by cooling fans should be more than 2 Nm 3 /kgcl which is defined as installed specific cooling air The total cooling air volume, however, was 1540 Nm 3 /kgcl despite all fans were running on more than 90% of their full capacities having no margin to meet the probable overloadsDevelopment of Cooling Performance of Clinker Cooler Process The most typical bearing among rolling mill bearings is the roll bearing Roller bearings are important components used to support the rollers and maintain Skip to content About Us About Us; For bearings contaminated by cooling water and iron oxide scale, the rings will continue to deteriorate during useThe Ultimate Guide To Rolling Mill Bearings AUBEARING
.jpg)
Failure Analysis of Pulverized Coal Injection (PCI) Mill Grinding
2024年8月6日 In an integrated steel plant, the pulverized coal injection (PCI) mill plays an important role in providing pulverized coal to the blast furnace The main purpose of using PCI coal is to reduce the hot metal production cost through the utilization of noncoking coal and to extend the available coke oven life Any unplanned outage of the PCI mill leads to increase in Previous Post Next Post Contents1 COAL PREPARATION AND FIRING11 INTRODUCTION12 2COAL RESERVES13 CHARACTERISATION OF COALS BY CHEMICAL131 31 Major components132 32 Minor Components14 4CHARACTERISATION BY PHYSICAL AND MECHANICAL PROPERTIES141 41 Coal Storage142 42 Variation of Physical and COAL PREPARATION AND FIRING INFINITY FOR CEMENT EQUIPMENTThere are many process fans that find applications in cement industry such as raw mill fans, induced draft fans, cooling fans, raw mill exhaust fans, coal mill fans and cooler exhaust fans Raw mill fans: Raw mill fan in cement industry The 6 Main Process Fans in Cement factoryThe innovative Flender vertical mill drives for grinding coal, raw meal, clinker and slag 7,000,000 KILOWATTS supply of fresh oil upstream of every single bearing ensures bearing cooling and dissipates the heat from the mill Extremely highquality oil supply systems are used here7,000,000 KILOWATTS OF INSTALLED EXPERTISE Flender
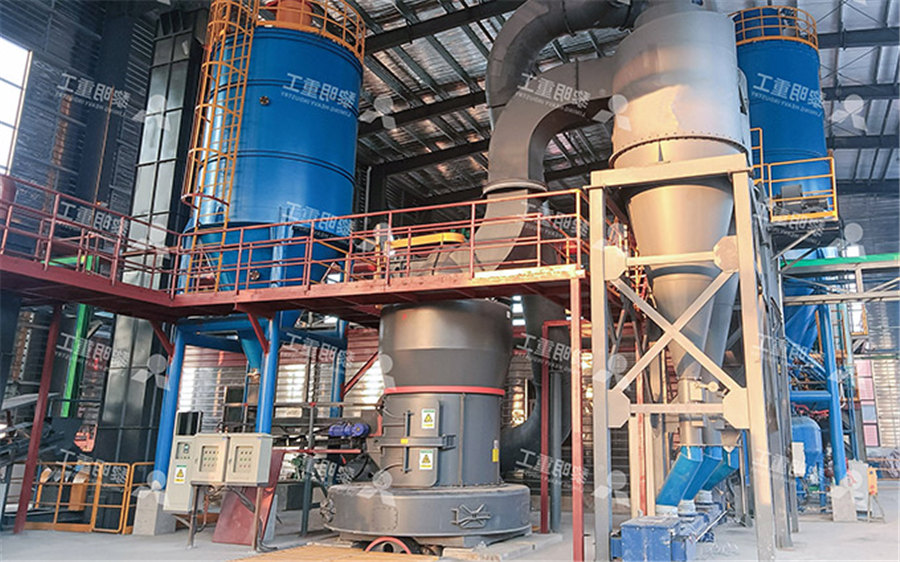
Four Ways To Improve The High Temperature Problem Of Ball Mill
6 天之前 The problem of high temperatures in ball mills is a prevalent problem that needs to be addressed to improve their performance and efficiency By implementing the solutions discussed in this article, such as proper lubrication, regular maintenance, and the use of cooling devices, the temperature of a ball mill can be effectively controlledCHASE International is a global parts supply specialist providing many of the world’s premium brands to power and process customers across the worldBRANDS CHASE International2020年8月12日 In a power plant, the coal mill is the critical equipment, whose effectiveness impacts the overall power plant efficiency Uniform coal feeding mass flow rate and required particle size and temperature at the outlet channel throughout with better classifier performance are crucial indicators that characterize the coal mill performanceAn investigation of performance characteristics and energetic 2023年1月15日 Coalfired power plants with direct aircooling condensers (DACCCFPP) are watersaving, ecofriendly and thus widely installed in regions rich in coal but short of water As such regions have better geological conditions for CO 2 storage, retrofitting these plants with carbon capture techniques provides a costefficient way to reduce carbon emissions and retain Dynamic modeling and comprehensive analysis of direct aircooling coal
.jpg)
A Study on 500 MW Coal Fired Boiler Unit’s Bowl Mill
Section of coal bowl mill Table 1 Guaranteed coal conditions for mill performance evaluation Coal Moisture % 20 Coal HGI 55 Mill Outlet Temperarure °C 80 Mill Air Flow T/hr 102 Coal Fineness (% passing trough 200 mesh) 70% passing through 200 mesh and 90% passing through 50 mesh Differental Pressure 300 mmwc Coal Output from Mill 609 t/hr1927 First Loesche coal mill delivered for the Klingenberg power station in Berlin 1953 500th coal mill plant sold worldwide 1961 Introduction of hydraulic spring assembly system 1965 Construction of first pressure mill (LM 122 D) 1980 Delivery of first modular coal mill (LM 263 D) 1985 Delivery of first selfinerting coal grinding plant (LM 212 D) for the steel industry (PCI LOESCHEMILLSA 5000 T /d Cement production line started in April 2009, which is equipped with a limestone singlestage hammer mill machine, model PCF2022, with the maximum material particle size of 1000 mm ×1000 mm ×1500 mm, the output Causes and Solutions of Bearing Problem of Hammer explained with regard to cooling and lubricating effects Depending of the type of rolling mill, dedicated roll cooling systems are required to fulfill the required functions Examples are suitable roll cooling and lubricationsystems to fully utilize the advantages of HSS rolls in hot strip mills, and selective roll cooling systems as aGENERAL ASPECTS OF ROLL COOLING FOR HOT COLD
.jpg)
Pulverizing Ball Mill Failures Machinery Lubrication
No coal, no fire No fire, no steam No steam, no electricity At this utility each of the two generating units employ six pulverizers, each on a continuous basis Each mill pulverizer is responsible for about 130 megawatts of power When the 2010年2月1日 Coolers are utilized on lubricating oil reservoirs of large rotating equipment to control viscosity and reject heat Lube oil cooler performance is impacted by a number of plantspecific variables Supplemental Cooling of Turbine Lube Oil Power EngineeringThe roller bearing assemblies are carried in replaceable bearing bushes screwed to the webs of the grinding mill and transmitting forces exclusively by way of static friction This new feature allows simple, fast and costeffective elimination of damage at the bearing seat, caused e g by faulty operation, simply by replacing bushespalla VIBRATING MILL mbecoalandminera'@'lcoal mill pulveriser lube oil The pulveriser grinds the coal to dust in rotating grinding rollers and sieves, so that it can be used as fuel The pulveriser lube oil is subjected to extreme levels of very fine particles, and many power plants believe the plant coal mill pulveriser lube oil CJC

CONTACT CHASE International
CHASE INTERNATIONAL LIMITED Banksia House, Mill Lane, Heatley, Lymm, Cheshire, WA13 9SG • +44 (0) 1925 • EORI No GB0This document discusses coal pulverization in power plants It covers various topics related to coal pulverizers including: Types of coal and reasons for pulverizing coal like improved efficiency and combustion control Two types of pulverizer firing systems direct and indirect Different types of pulverizers classified by speed tube mills, bowl mills, and impact mills Key Coal Mills in Thermal Power Plant PDF Mill (Grinding) Scribd2019年9月28日 Detecting classifiercoal mill damage using a signal Bearing 3379%, Pulley 503%, and produce a centrifugal damage The heat exchanger highly influences the series of cooling (PDF) Detecting classifiercoal mill damage using a2023年5月11日 Flow measurement of five seal air pipes at a coal mill using the heater method at a coal fired To protect the bearings from coal cooling air is extracted from the 13th stage of a Flow measurement of five seal air pipes at a coal mill using the
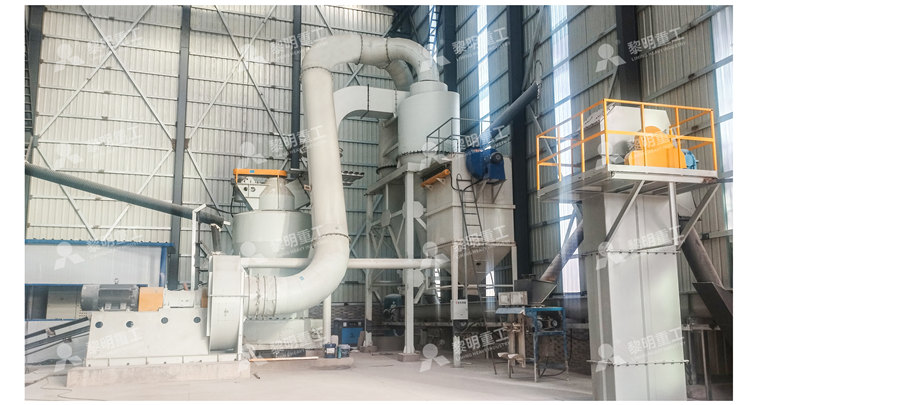
Fracture failure analysis of coal mill shaft ResearchGate
2020年7月1日 During the operation of No2 boiler in a power plant, the fracture of a coal mill shaft occurred The fracture causes of the coal mill shaft were found by macroscopic inspection, metallographic We supply upgraded cylinders and air bags as well as replacement seal kits for the hydraulic ram cylinders on vertical grinding mills / pulverizers Upgraded Cylinders Vertical grinding mill ram cylinder units perform a vital role in the RAM CYLINDERS CHASE InternationalCoal Mill Gearboxes 12 Gearboxes for Cooling Tower and Desulfurization Pumps 12 mill foundation through thrust bearing and its housing Characteristics Modular design, good component interchangeability Longer bearing life, more reasonable lubrication distribution01 NGC Gearsscale from water cooled Support Roller Assemblies, coal mill bearings, pipes, liquid ring pumps, catalytic crackers, green liquor lines, cooling towers, compressors, and any system that develops mineral scale and calcium carbonate deposits Anion D’Scale is completely biodegradable and after its use can be disposed of in most municipal wasteAnion D’Scale Application: Kiln Trunnion Bearings D’Scaling
.jpg)
ATOX® Coal Mill FLSmidth Cement
Our ATOX® Coal Mill has large rollers with great grinding capability of virtually all types of raw coal The rollers work harmoniously with a highlyefficient separator and feed sluice to consistently and reliably deliver coal meal to your desired fineness and moisture levelAdvantages of air swept coal mill The feeding device of the airswept coal mill adopts a louvertype structure with oblique air intake, which enhances the heat exchange capacity of the mill and can effectively prevent material blocking at the entrance of the coal mill; optimize the support system, improve the lubrication structure, and reduce system resistanceAir Swept Coal Mill Cement Plant Machineryreliability of the mills and their rolling bearings Bearings supporting the grinding rollers in the vertical mill Floating bearing end: Doublerow cylindrical roller bearing (series NNU41) Locating bearing end: spherical roller bearing (series 231) Fine product Feed material SLS high efficiency classifier for accurate classification Entirely Rolling Bearings in Vertical Mills Built by Gebr Pfeiffer AG, Germany2024年9月22日 Turbine Bearing Cooling System: Steam turbines are the heart of many industrial operations, Coal, Gas, and Oilfired Power Plants: use of both electricity and heat This reduces the need for external energy sources, lowering costs and minimizing the mill’s carbon footprint Mechanical Drive:Turbine Bearing Cooling System EMS Power Machines
.jpg)
Development of Cooling Performance of Clinker Cooler Process
2018年7月31日 Furthermore, in a modern cooler the cooling air produced by cooling fans should be more than 2 Nm 3 /kgcl which is defined as installed specific cooling air The total cooling air volume, however, was 1540 Nm 3 /kgcl despite all fans were running on more than 90% of their full capacities having no margin to meet the probable overloadsThe most typical bearing among rolling mill bearings is the roll bearing Roller bearings are important components used to support the rollers and maintain Skip to content About Us About Us; For bearings contaminated by cooling water and iron oxide scale, the rings will continue to deteriorate during useThe Ultimate Guide To Rolling Mill Bearings AUBEARING