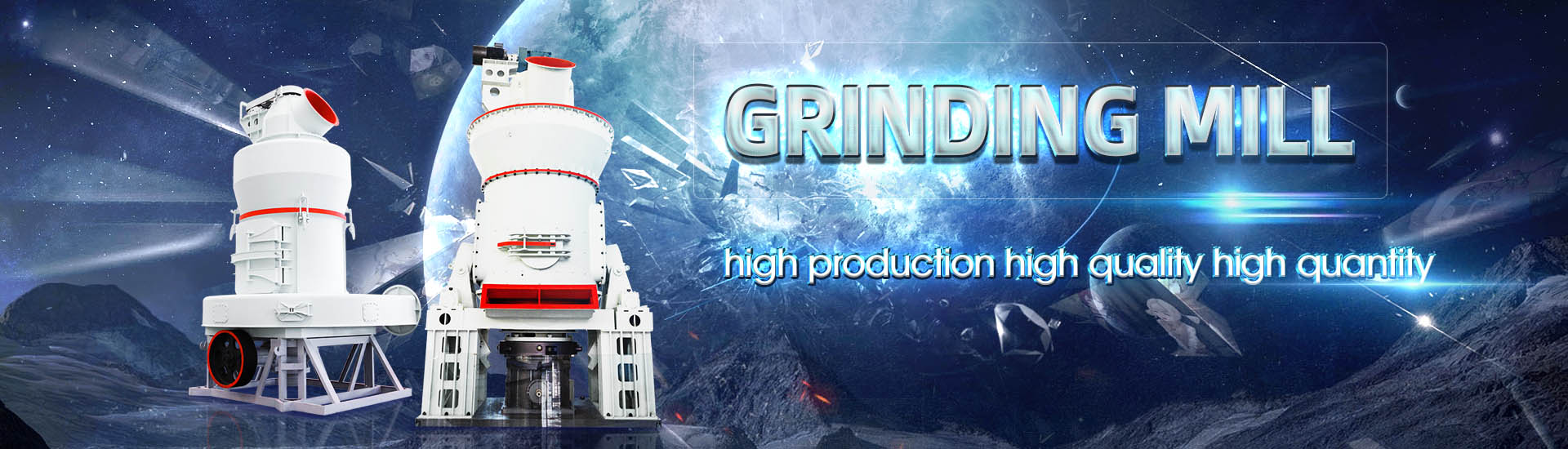
Alumina ash, overhaul slag, aluminum electrolyte crusher
.jpg)
Efficient lithium recovery from electrolytic aluminum slag via an
2024年2月1日 The electrolytic aluminum industry generates a large amount lithium (Li)containing electrolytic aluminum slag (EAS) annually, and this can result in severe 2023年4月25日 This article analyzes and summarizes the composition and hazards of the overhaul slag and the current development status of domestic and international electrolytic 电解铝大修渣处置研究进展2024年5月23日 16 Million metric tons of spent carbon electrodes modify carbonrich solid wastes from aluminum electrolysis are produced annually, threatening ecosystems by cyanide The recycling of carbonrich solid wastes from aluminum 2024年2月1日 In this paper, an innovative process of sulfuric acid roasting and water leaching is proposed, which can efficiently and environmentally recover F, Al and Li from overhaul slag A novel approach for extracting lithium from overhaul slag by low
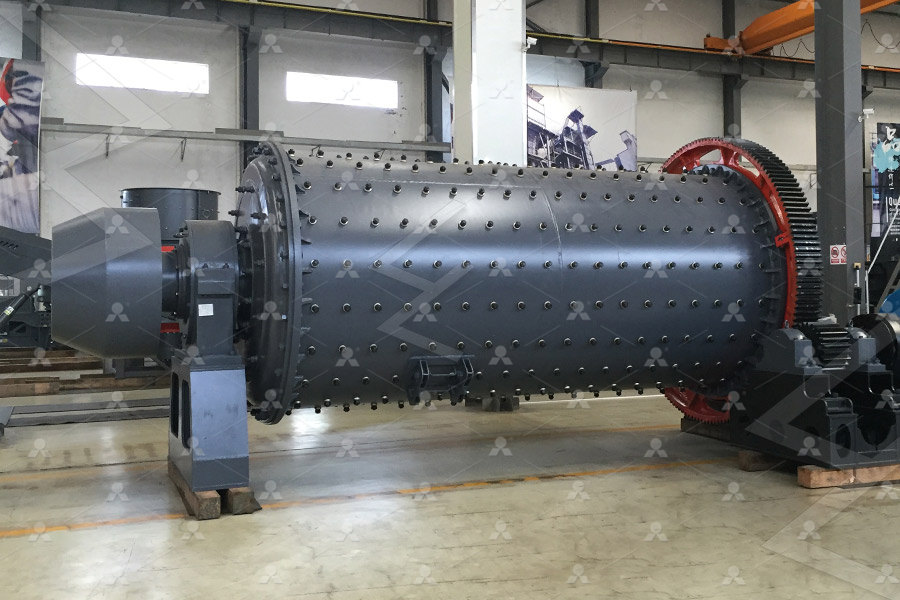
Clean Process for Selective Recovery of Lithium Carbonate from
2023年9月1日 This study employed hydrometallurgical processes to selectively leach lithium from Licontaining aluminum electrolyte slag, using sodium carbonate solution as the leaching Aluminium ash and slag are produced from molten slag cooling in the electrolytic aluminium production process,the recycling and utilization of the electrolytic aluminium ash and slag is Recycling and Utilization of the Electrolytic Aluminium Ash and Slag2024年7月24日 The lithium was selectively recovered and enriched from spent aluminum electrolyte slag by using calcium salt roasting transformation followed by HBL121solvent Cleaner Process for the Selective Extraction of Lithium from Spent 2024年1月1日 A novel approach for lithium recovery from waste lithiumcontaining aluminum electrolyte by a roastingleaching process Anode carbon residue is produced in the production Efficient lithium recovery from electrolytic aluminum slag via an
.jpg)
Research Progress of Electrolytic Aluminum Overhaul Slag Disposal
2023年4月25日 This article analyzes and summarizes the composition and hazards of the overhaul slag and the current development status of domestic and international electrolytic 2019年2月26日 Aluminum ash is an industrial waste residue produced during alumina electrolysis and aluminum processing and casting In the experiment, alumina powder with a purity of 9897% was prepared by (PDF) Preparation of Alumina from Aluminum Ash 2023年9月1日 Lithium (Li)bearing aluminum electrolyte slag is an inevitable byproduct of the aluminum industry, and improper disposal or stacking it may lead to potential environmental hazards This study employed hydrometallurgical Clean Process for Selective Recovery of Lithium 2019年4月9日 The alumina slag consisted mainly of alumina (αAl2O3), calcium hexaluminate (CaAl12O19), gehlenite (Ca2Al2SiO7), and small amounts of hercynite (FeAl4O7), and metallic iron (MFe)SemiSmelting Reduction and Magnetic Separation
.jpg)
Preparation of Alumina from Aluminum Ash by Sintering with
2019年2月1日 Aluminum ash is an industrial waste residue produced during alumina electrolysis and aluminum processing and casting In the experiment, alumina powder with a purity of 9897% was prepared by sintering with sodium hydroxide and the process conditions affecting the dissolution rate of Al 2 O 3 from aluminum ash were studied The best process conditions for 2021年11月1日 Dissolution behavior of overhaul slag from aluminum reduction cell in a cryolitebased molten salt system Jianping Yang X Lu Fanyue Meng Abstract The crusting/agglomerating behavior and heat transfer process upon feeding of smeltinggrade alumina into aluminum electrolyte were investigated using a suspended weighing device Improved CFD modeling of full dissolution of alumina particles in 2022年1月3日 Ferrotitanium slag was used as a sintering aid to prepare highperformance alumina (Al2O3) ceramics by pressureless sintering at different temperatures The bulk density, apparent porosity, bending strength, and hardness of the 99 wt% Al2O3 ceramics after sintering at 1420 °C were 391 g/cm3, 016%, 38937 (± 761) MPa, and 1564 (± 016) GPa On the Fundamental Research on the Densification of Alumina The main components in the aluminum slag are metallic aluminum, alumina, aluminum nitride, fluoride salts, chloride salts, as well as the elements such as iron, silicon, magnesium, and calcium The secondary aluminum dross is generated by separation of metallic aluminum from aluminum slag and is toxic and harmful, which pollutes the environmentTechnical Report International Aluminium
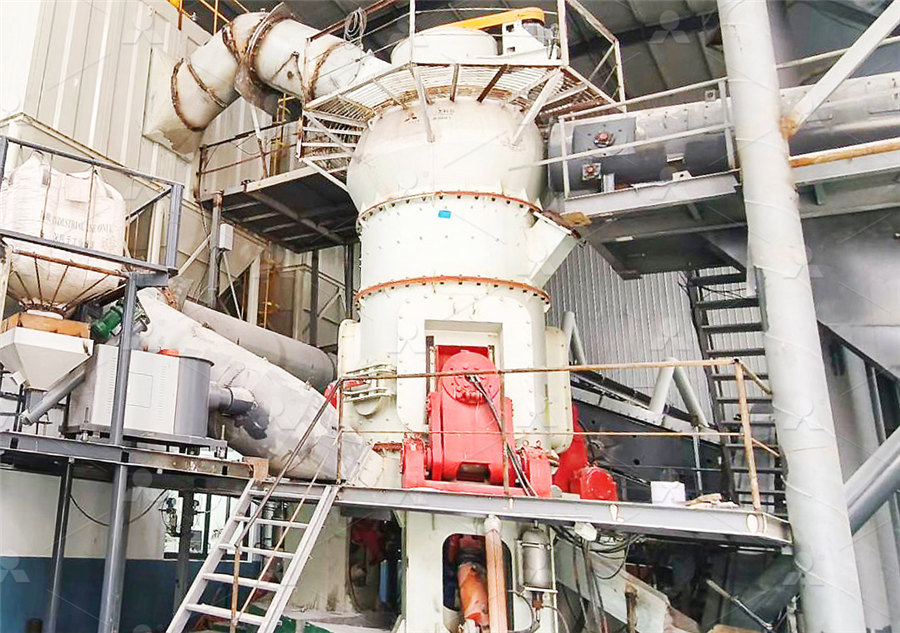
The recycling of carbonrich solid wastes from aluminum
2024年5月23日 16 Million metric tons of spent carbon electrodes modify carbonrich solid wastes from aluminum electrolysis are produced annually, threatening ecosystems by cyanide and fluoride pollution Here, we review carbonrich solid wastes with focus on sources and hazards, detoxification, separation, recovery, recycling and disposal Treatment techniques 2023年10月1日 Currently, the green resource utilization in the aluminum electrolysis industry mainly focuses on the solid waste treatment of aluminum electrolysis tank overhaul slag, the resource utilization of waste cathodes, and the recovery of electrolytic tank waste heat There are few reports on lithium recovery from waste aluminum electrolytes [16,17]A novel approach for ultrasonic assisted organic acid leaching of 2015年1月1日 The cogasification of biomass together with fossil fuels, like coal, intends to reduce the related CO 2 emissions, because of a CO 2 neutral life cycle of biomass [1]Due to their extensive gas purification, gasification based processes have shown additional environmental advantages compared to combustion ones, ie nearly no emissions of sulfur Ash melting behavior and slag infiltration into alumina refractory 2020年1月2日 The invention discloses a fluorineretaining agent for overhaul slag of an aluminum electrolytic cell The fluorineretaining agent comprises the following components of, by mass, 80100 parts of calcium sulfate, 6080 parts of calcium oxide, 5070 parts of calcium hydroxide and 3060 parts of calcium chloride The invention further discloses a method for Fluorineretaining agent for overhaul slag of aluminum
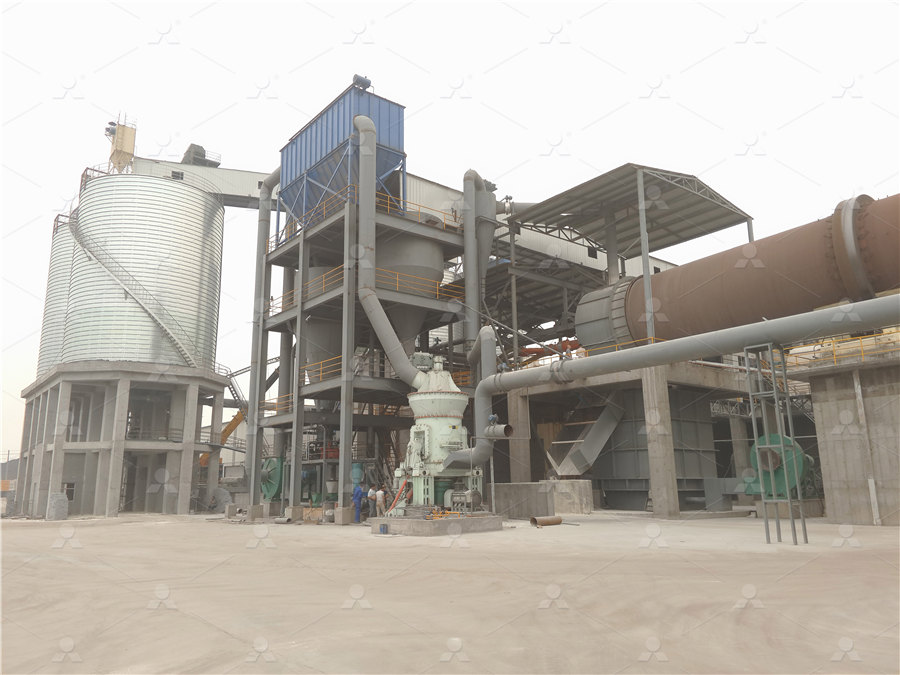
Kinetics of aluminum extraction from roasting activated fly ash by
2023年11月9日 The process of extracting aluminum with sulfuric acid from highalumina fly ash activated by roasting with Na2CO3 and NaOH as raw materials ware studied The results revealed that the aluminum in fly ash activated by sodium carbonate reached 932% under the optimum conditions (30% H2SO4, 90°C, 120 min, and liquidtosolid ratio was 5:1) 2013年6月15日 The fly ash with alumina composition from 45 to 55 % has been found in China in last 10 years, which attracts great attention from Chinese government and related alumina industry Chinese government and its stateowned enterprises have successfully extracted the Al as alloy product from the highalumina fly ash However, to recycle the calcium silicate slag as Thermal activation on calcium silicate slag from highalumina fly ash 2023年5月20日 Due to chemical corrosion and erosion by molten aluminum liquid and electrolyte, the carbon anode of the aluminum electrolytic cell would fall off into the electrolyte during the primary aluminum electrolysis process to produce spent anode carbon (SCA), which has been listed as one of the typical hazardous solid wastes in the National Hazardous Waste Regeneration of raw materials for aluminum electrolysis from 2023年4月13日 Aluminium is produced by electrolysis using alumina (Al2O3) as raw material and cryolite (Na3AlF6) as electrolyte In this HallHéroult process, the energy consumption is relatively large, and A comprehensive review of aluminium electrolysis and the waste
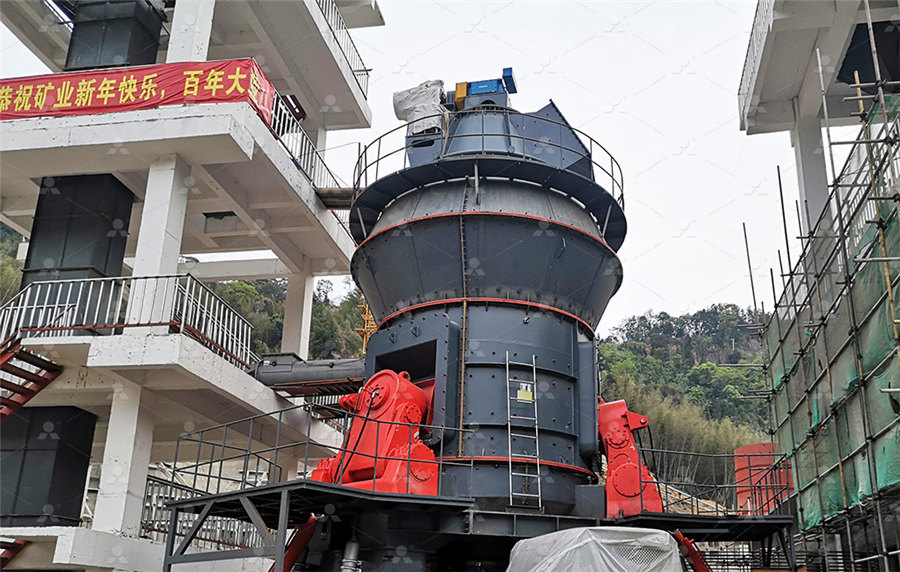
Aluminum extraction technologies from high aluminum fly ash De Gruyter
Coal fly ash (CFA), an industrial byproduct of hightemperature combustion of coal in coalfired power plants, is one of the most complex and largest amounts of industrial solid wastes generated in China It is widely recognized that CFA should be considered as a potential alumina resource to substitute bauxite In this review, the features of highalumina fly ash and aluminum recovery 2022年10月9日 Where, γ c refers to the yield of flotation concentrate (%); A c (%) and A f (%) are the ash content of flotation concentrate and feed material, respectively 3 Results and discussion 31 Characterization of raw carbon anode slag The cumulative particle size result is shown in Figure 1From Figure 1, the content of fraction size of 0125 mm–0074 mm (3076%) Recovery of carbon and cryolite from spent carbon anode slag of 2023年8月2日 The highvalue, green and harmless purification of aluminum electrolysis comprehensive solid waste can not only reduce its harm to the environment and soil but also separate and recover the highvalue rare elements This study aims to develop a process for recovering and treating waste aluminum electrolytes by sulfuric acid roasting The results of Sustainable Recovery of Fluorine from Waste Aluminum Electrolyte 2023年10月1日 Crush and grind the waste aluminum electrolyte fine Fig 1 (b) shows the particle size analysis, and the results show that the average particle size of the treated aluminum electrolyte powder is 4528 μm Fig 1 (c) shows the XRD diagram, which shows that the waste aluminum electrolyte mainly comprises Na 3 AlF 6, CaF 2, LiF, K 2 NaAlF 6, and A novel approach for ultrasonic assisted organic acid leaching of
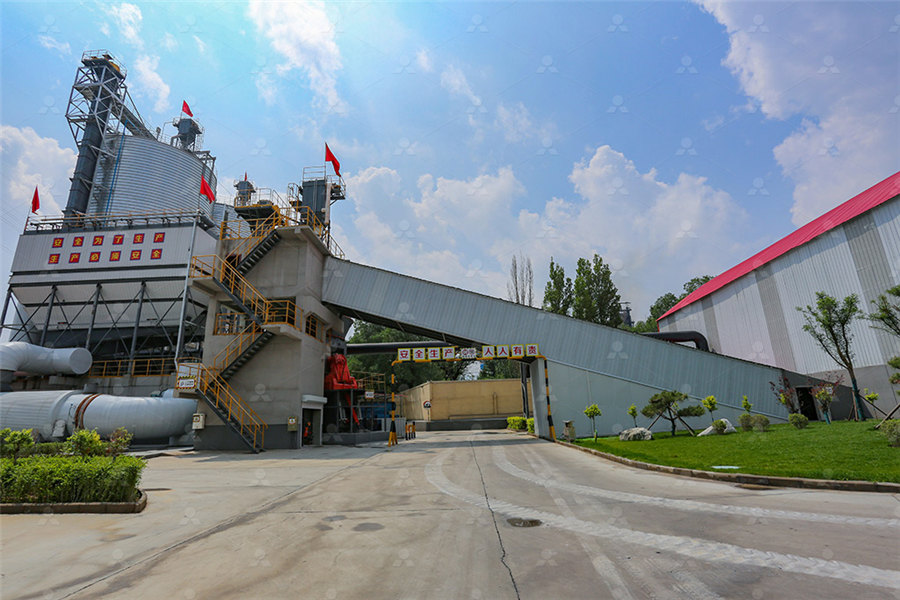
Synthesis strategies of alumina from aluminum saline slags
2023年4月1日 Comparing with other materials, the aluminum industry is energy intensive with a notable difference between primary and secondary production (174–186 MJ/kg and 10–20 MJ/kg, respectively) (Abdulkadir et al, 2015)The reason by which secondary aluminum production consumes much less energy is because its raw material is aluminum scrap and primary 2023年5月20日 Due to chemical corrosion and erosion by molten aluminum liquid and electrolyte, the carbon anode of the aluminum electrolytic cell would fall off into the electrolyte during the primary aluminum electrolysis process to produce spent anode carbon (SCA), which has been listed as one of the typical hazardous solid wastes in the National Hazardous Waste Regeneration of raw materials for aluminum electrolysis from 2021年10月1日 At present, there are more and more researches on the resource utilization of aluminum ash, which are mainly in the areas of foaming agents for lightweight materials in construction [5], extraction of metallic aluminium [6], leaching of rare and precious heavy metals [7,8], the firing of ceramics[9], preparation of polymeric aluminum chloride and nano alumina, A novel approach for lithium recovery from waste lithium 2014年12月5日 The dissolution process of alumina in a threedimensional 300 kA aluminum reduction cell was modeled and simulated employing our custom code A twoparticle phase population balance model (TPPBM) was proposed by dividing solid phase into two groups consisting of small and large size alumina particles separately A CFDTPPBM coupled model CFD simulation of dissolution process of alumina in an aluminum
.jpg)
Novel process for the extraction of lithium carbonate from spent
2020年12月1日 The rapid development of the electrolytic aluminum industry in China and the increasing demand for aluminum products have led to the development of many lowgrade bauxite mines with an average Li 2 O content of at least 058% (Wang et al, 2013)Due to the use of this lowgrade bauxite in the electrolytic aluminum process, the content of lithium in the 2021年3月16日 By Alton Tabereaux, Contributing Editor Spent potlining (SPL) disposal is one of the largest environmental waste management challenges confronting worldwide primary aluminum smelters due to its toxicity The International Aluminium Institute (IAI) asserts that 16 million tons of SPL were generated from primary aluminum production in 2019,1 making it the The SPL Waste Management Challenge in Primary Aluminum2023年6月2日 This paper presents experimental data on the dependence on alumina and calcium fluoride concentrations of the viscosity of the industrial electrolytes NaFAlF3CaF2Al2O3 with cryolite ratios (CR Efficient extraction and recovery of lithium from waste aluminum DOI: 101016/jresconrec2023 Corpus ID: ; Efficient extraction and recovery of lithium from waste aluminum cryolite electrolyte @article{Tang2023EfficientEA, title={Efficient extraction and recovery of lithium from waste aluminum cryolite electrolyte}, author={Chaobo Tang and Jiahui Wang and Shenghai Yang and Xianpan Zhang and Shuai Li and Yanqing Lai Efficient extraction and recovery of lithium from waste aluminum
.jpg)
A HighEfficiency Alkali Circulation Process for Alumina Extraction
2023年1月30日 The present article is focused on extraction alumina from high alumina fly ash using an improved hydrochemical method with highefficiency alkali circulation and mild reaction conditions The alumina leaching behavior and corresponding reaction mechanism of the process were systematically investigated The results revealed that the alumina extraction efficiency 2018年10月1日 After the delivery of alumina to the aluminum industry, alumina is reduced to aluminum metal through an electrolytic process (Gil, 2005) In 2010, a total of about 56 million tons of aluminum metal was globally produced (approximately 18 million tons of scraps were recycled), compared to about 28 million tons in 1990 (more than 8 million tons of scraps were Hazardous aluminum dross characterization and recycling 2016年10月24日 The industrial aluminum reduction cell is an electrochemistry reactor that operates under high temperatures and highly corrosive conditions However, these conditions have restricted the measurement of key control parameters, making the control of aluminum reduction cells a difficult problem in the industry Because aluminum electrolysis control Progress in Aluminum Electrolysis Control and Future Direction 2019年2月26日 Aluminum ash is an industrial waste residue produced during alumina electrolysis and aluminum processing and casting In the experiment, alumina powder with a purity of 9897% was prepared by (PDF) Preparation of Alumina from Aluminum Ash

Clean Process for Selective Recovery of Lithium
2023年9月1日 Lithium (Li)bearing aluminum electrolyte slag is an inevitable byproduct of the aluminum industry, and improper disposal or stacking it may lead to potential environmental hazards This study employed hydrometallurgical 2019年4月9日 The alumina slag consisted mainly of alumina (αAl2O3), calcium hexaluminate (CaAl12O19), gehlenite (Ca2Al2SiO7), and small amounts of hercynite (FeAl4O7), and metallic iron (MFe)SemiSmelting Reduction and Magnetic Separation 2019年2月1日 Aluminum ash is an industrial waste residue produced during alumina electrolysis and aluminum processing and casting In the experiment, alumina powder with a purity of 9897% was prepared by sintering with sodium hydroxide and the process conditions affecting the dissolution rate of Al 2 O 3 from aluminum ash were studied The best process conditions for Preparation of Alumina from Aluminum Ash by Sintering with 2021年11月1日 Dissolution behavior of overhaul slag from aluminum reduction cell in a cryolitebased molten salt system Jianping Yang X Lu Fanyue Meng Abstract The crusting/agglomerating behavior and heat transfer process upon feeding of smeltinggrade alumina into aluminum electrolyte were investigated using a suspended weighing device Improved CFD modeling of full dissolution of alumina particles in
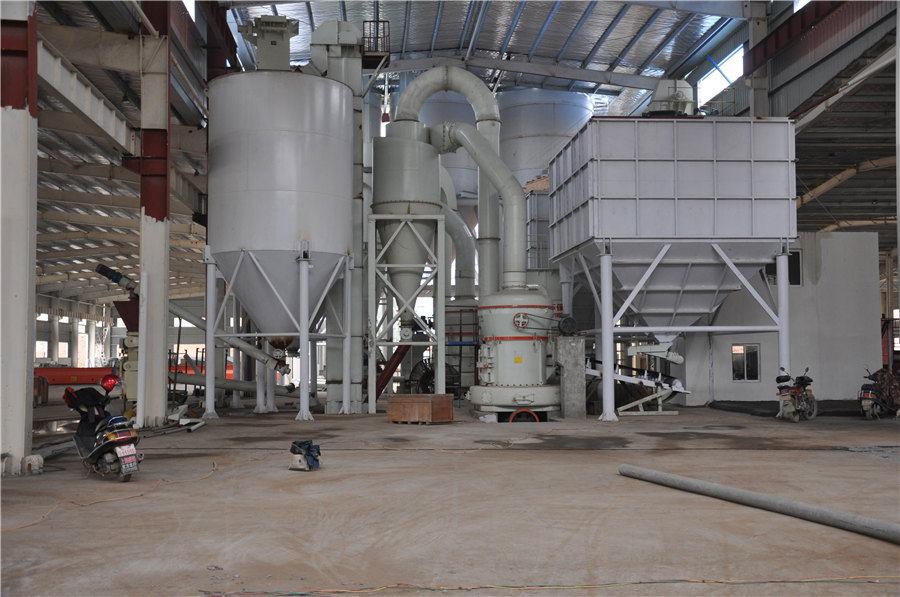
Fundamental Research on the Densification of Alumina
2022年1月3日 Ferrotitanium slag was used as a sintering aid to prepare highperformance alumina (Al2O3) ceramics by pressureless sintering at different temperatures The bulk density, apparent porosity, bending strength, and hardness of the 99 wt% Al2O3 ceramics after sintering at 1420 °C were 391 g/cm3, 016%, 38937 (± 761) MPa, and 1564 (± 016) GPa On the The main components in the aluminum slag are metallic aluminum, alumina, aluminum nitride, fluoride salts, chloride salts, as well as the elements such as iron, silicon, magnesium, and calcium The secondary aluminum dross is generated by separation of metallic aluminum from aluminum slag and is toxic and harmful, which pollutes the environmentTechnical Report International Aluminium2024年5月23日 16 Million metric tons of spent carbon electrodes modify carbonrich solid wastes from aluminum electrolysis are produced annually, threatening ecosystems by cyanide and fluoride pollution Here, we review carbonrich solid wastes with focus on sources and hazards, detoxification, separation, recovery, recycling and disposal Treatment techniques The recycling of carbonrich solid wastes from aluminum 2023年10月1日 Currently, the green resource utilization in the aluminum electrolysis industry mainly focuses on the solid waste treatment of aluminum electrolysis tank overhaul slag, the resource utilization of waste cathodes, and the recovery of electrolytic tank waste heat There are few reports on lithium recovery from waste aluminum electrolytes [16,17]A novel approach for ultrasonic assisted organic acid leaching of

Ash melting behavior and slag infiltration into alumina refractory
2015年1月1日 The cogasification of biomass together with fossil fuels, like coal, intends to reduce the related CO 2 emissions, because of a CO 2 neutral life cycle of biomass [1]Due to their extensive gas purification, gasification based processes have shown additional environmental advantages compared to combustion ones, ie nearly no emissions of sulfur