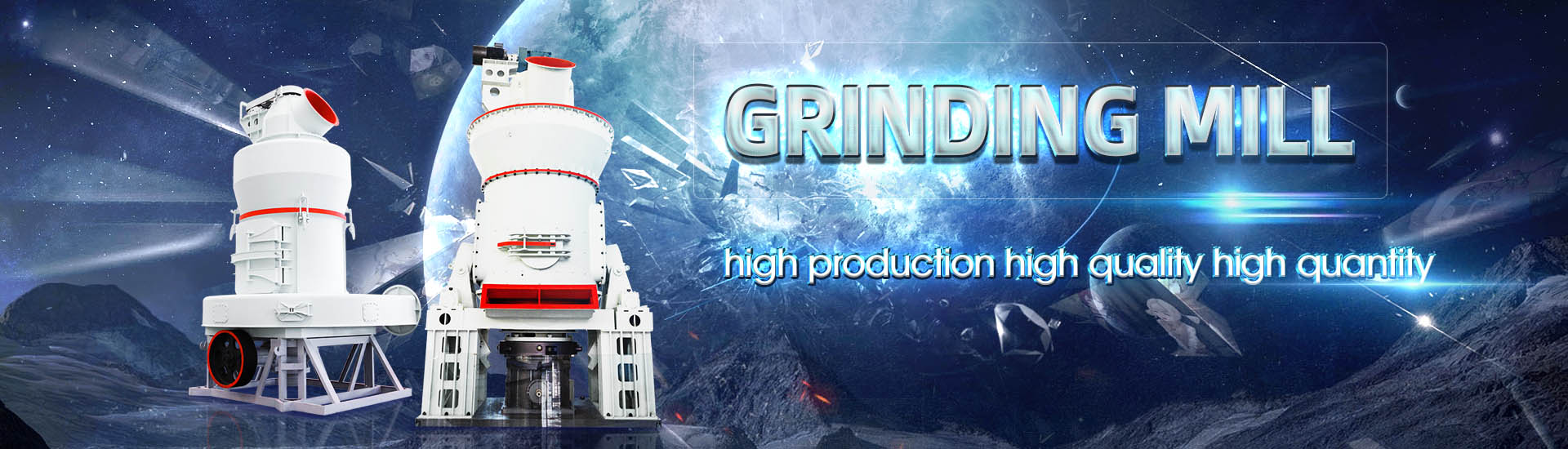
Repair of coal mill in power plant
.jpg)
classifications and working of mills in a power plant PPT
2020年6月29日 The key types of coal pulverizers tube/ball mills, vertical spindle mills, and impact mills are outlined Performance indicators for mills include meeting load, achieving fineness, minimizing current/rejects, and balancing air/fuel flowsThe document discusses coal mill/pulverizers used in thermal power plants It describes hoCoal mill pulverizer in thermal power plants PPT SlideShareIn pulverised coalfired power plants, a pulveriser coal mill grinds the raw coal into a combustible dust Here, the coal particles are dried by flue gas or hot air and milled to fine size, so that stable combustion and complete burnout of pulverised coal can be achieved in the combustion Coal Mill an overview ScienceDirect Topics2015年8月1日 Power plant performance and reliability is highly influenced by coal mills that grind, dry, and transport coal to the furnace This paper presents a review of the current state of technology on improved controls and fault diagnosis methods applied to millsReview of control and fault diagnosis methods applied to coal

Mill Inerting and Pulverizer/Mill Explosion Mitigation
Water fogging and deluge systems are essentially mill internal combustible dust suppression systems and they also suppress or extinguish burning or smoldering coal The majority of burning or smoldering coal more often occurs under the grinding zone where the hot primary air flow 2011年1月1日 Compared with actual situation of the current thermal power plant, this paper studies operation process of coal handling system in thermal power plant Analyze technical characteristics of coal handling system and operating characteristics of the relevant machinery Operation and Maintenance of Coal Handling System in Thermal •Efficiencies of coalfired power plants decrease gradually over time as materials degrade and components wear •Initial losses are generally containable by keeping to good operating and maintenance practices •Eventually, performance will decrease to the extent that more Upgrading and efficiency improvement in coalfired power plants2021年9月9日 In a case study of a coal mill, which is the critical subsystem in a coalfired power plant, we demonstrated that, by introducing a remedial maintenance method, availability and reliability are significantly increased, and Impact of RemediationBased Maintenance on the
.jpg)
Review of flexible operation of coalfired power plants
%PDF17 %µµµµ 1 0 obj >/Metadata 202 0 R/ViewerPreferences 203 0 R>> endobj 2 0 obj > endobj 3 0 obj >/ExtGState >/ProcSet[/PDF/Text/ImageB/ImageC/ImageI Coalfired plants are the most widely used power plant today They involve the combustion of coal producing high pressure (typically 2400–3500 psig, ~165–240 bar) and high temperature (>500ºC) steam which is used to drive a turbine at synchronous speed (3000 rpm in countries such as the UK with a 50 Hz supply frequency, 3600 rpm in Instrumentation and control in coalfired power plant ICSC• Damage repair cost (Primary air inlet ducts, PA fans, mill internals, feeders, – Systems often named as “inerting systems” by coal fired power plant personnel include: • Steam Inerting Systems • Water fogging or deluge systems • Rehydration is exothermic and dried coal that is stagnate anywhere in the coal mill canMill Inerting and Pulverizer/Mill Explosion MitigationThis article presents the performance (availability) evaluation of a typical coal fired power plant in a realistic working environment for identifying the critical subsystem and planning the preventive maintenance schedule For analysis, the entire thermal system is broken down into six subsystems ie, turbine, condenser, coal supply, water circulation, air circulation and boiler sub Performance Evaluation of a Coalfired Power Plant

Impact of RemediationBased Maintenance on the Reliability of a Coal
2021年9月9日 Rapid changes in electricity power markets have increased the production costs of coalfired power plants and pushed their production to the limits of profitability For power plants currently in operation, a possible approach to cope with this issue is to introduce novel methods that increase the plant’s reliability and availability Coal mills are a subsystem that should The evaluation will be done by way of touring the plant, Coal Mill Safety: A Critical Aspect of Power Plant Operations Introduction Coal mills, also known as pulverizers, play a critical role in power plants by grinding coal into fine powder, which is then used in various pyroprocessesCoal Mill Safety: A Critical Aspect of Power Plant Operations Coal Power generation industry studies have shown that pulverized coal power plants are an area where improved equipment reliability is essential The Electric Research Institute (EPRI) has determined that 1% of plant availability is lost on average due to pulverizerrelated problemsCoal Pulverizer – Power Plant Pall CorporationThe ball mill is a traditional coal pulverizer machine, which has been widely used since it was invented In the cement plant, the new dry process cement manufacturing requires the moisture content of coal powder to be 05% ~ 15%, while that of raw coal is 15% ~ 40% Therefore, the ball mill should have a drying function besides grindingCoal Mill in Cement Plant
.jpg)
A Study on 500 MW Coal Fired Boiler Unit’s Bowl Mill
Coal Bowl Mill, for guaranteed performance at a 500 MW capacity NTPC thermal power plant The study was conducted to assess the effective performance of the pulverizers of this 500 MW boiler unit for its maximum capacity of 609 t/hr forCoal Mill in Thermal Power Plant Free download as Word Doc (doc / docx), PDF File (pdf), Text File (txt) or read online for free This document discusses coal pulverizers/mills which are critical components that convert the stored energy in coal into electricity There are various types of pulverizers that primarily utilize grinding, drying, classification and circulation processesCoal Mill in Thermal Power Plant2014年10月1日 efficiency of coal separation for particle size i m mill,i mass flow rate of coal from the mill for coal particle size i As a result, for the new design analyses, certain steps are going to be checked and controlled These steps are as follows: • The coal mass flow rate from the mill should be approximately 100 kg/s, as in the D00 base Numerical and experimental analysis of pulverized coal mill The coal mill used in the coalfired power plants is modeled in view of the controller design rather than the educational simulator The coal mass flow and the outlet temperature are modeled by Sectional view of MBF coal mill Download Scientific
.jpg)
Analysis of the Coal Milling Operations to the Boiler
2020年4月2日 Milling system in coal power plant purposely to process the raw coal to become as pulverise fuel Coal mill motor power (kW) 0 4171 454 milling process, boile r and repair 2019年5月21日 and performance of a coalfired power plant cooling tower The results obtained through the model are confronted with a thermodynamic analysis of the cooling tower that shows the influence of this(PDF) Maintenance Strategy Optimization of a CoalFired Power Plant Coal crushing equipment of coal handling plant system in the thermal power plant is very important for Plant efficiency improvement Keywords: India coal grades, Crusher, Construction, Crushing stages, Defect identification INTRODUCTION The coal handling plant (CHP) in a thermal power station covers unloading of coal, itsOPERATION AND MAINTENANCE OF CRUSHER HOUSE FOR COAL In this paper, GA is applied to develop the coal mill model and to estimate the pulverised coal flow using real time onsite plant data 2 COAL MILL MODELLING In thermal power plant, pulverization of coal is carried out by coal mill Raw coal is moved from the storage to the mill by conveyor mechanism The type of coal mill envisaged for ourPulverised Coal Flow measurement in Thermal Power Plant
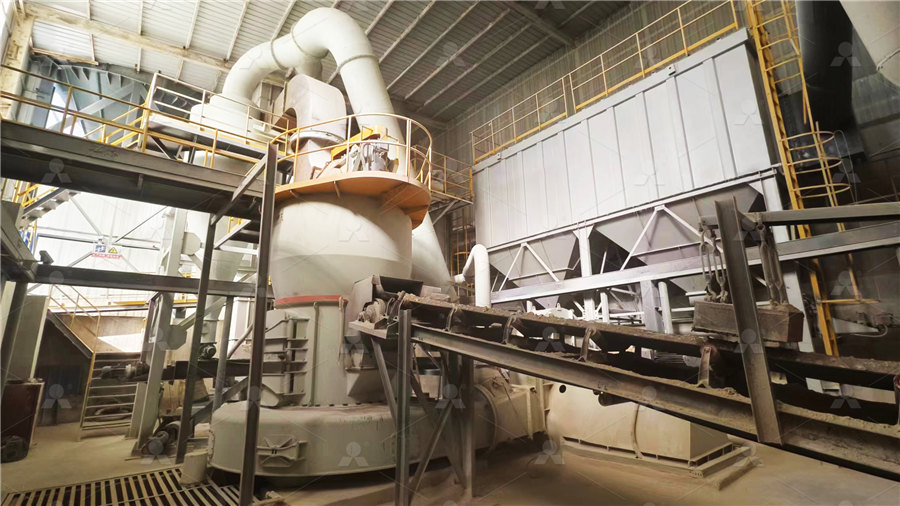
An investigation of performance characteristics and energetic
2020年8月12日 This study shows the performance of a currently running vertical roller coal mill (VRM) in an existing coalfired power plant In a power plant, the coal mill is the critical equipment, whose In this video you will get a live overview of ball and tube type coal mill used in thermal power plantLive Working of Ball and Tube Coal Mill in Thermal Power Plant/ Coal Understanding coalfired power plant cycles 5 1 Introduction Figure 1 shows the basic principle of combustionbased power generation using a steam turbine Combustion of the fuel generates heat that is used to convert water pumped to high pressure into Understanding coalfired power plant cycles ICSC1 Failure and repair rates are constant 2 A repaired unit is as good as new 3 The standby units are of the same nature and capacity as the active unitsPerformance Evaluation of a Coalfired Power Plant ResearchGate
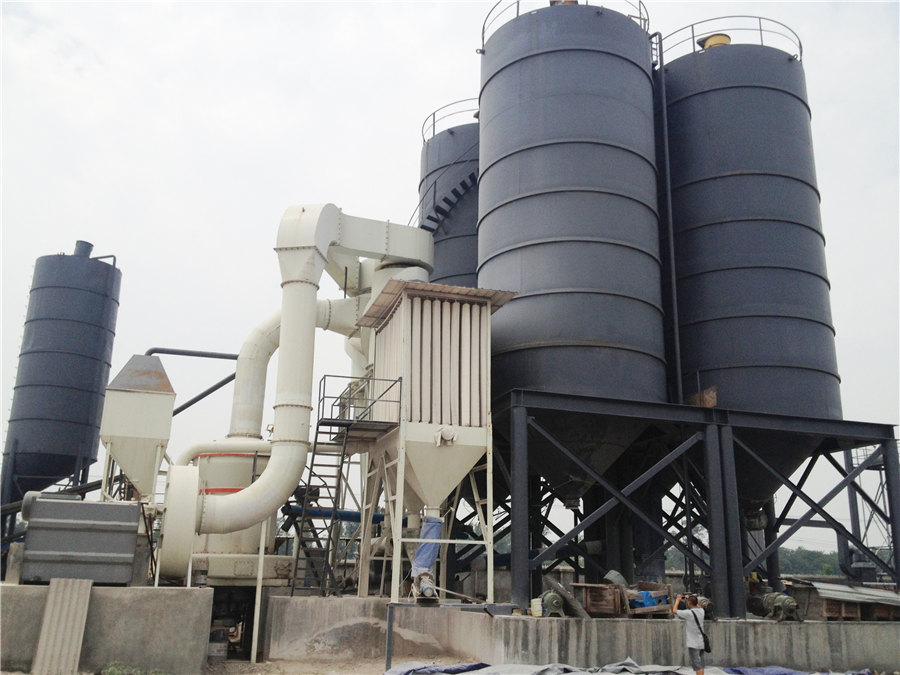
Monitoring Model of Coal Mill in Power Plant Based on Big Data
In order to monitor the wear condition of grinding roller of coal mill in power plant and improve the reliability of production equipment, it is necessary to establish a state monitoring model with high accuracy and good prediction effect It has been shown that the power of coal mill can reflect the wear degree of grinding roller If the voltage and power factor of coal mill are constant 7 Figure S1: Power generation from nuclear, hard coal and lignite power plants and demand in Germany, 23 to 30 March 2016 12 Figure S2: Qualitative representation of key flexibility parameters of a power plant 12 Figure S3: Minimum load and ramp rates of different hard coal power plants 13 Figure S4: Ramp rates and startup times of different power plant Flexibility in thermal power plants Agora Energiewende2008年12月18日 The effect of flue gases from coal combustion on the concrete shell of a power plant stack was analyzed and the damage to the concrete was evaluated(PDF) Deterioration and Repair of Concrete 2012年4月1日 and management of coal crushing system in the coalfired thermal power plant Kaushik and Singh (1994) presented reliability analysis of the feed wa ter system in a thermal power plantRAM investigation of coalfired thermal power plants: A case
.jpg)
Analysis of the Coal Milling Operations to the Boiler Parameters
The mill design in the power plant is a vertical bowl The mill rotated on his axis at minimum speed 35rpm by a motorreducer train The grinding rolls are supported by three oscillating journals The rolls rotate freely crushing the coal on the bowl, the pressure for optimal crushing being2023年11月30日 In a coalfired power plant, a mill or pulverizer plays a crucial role in the process of converting raw coal into a form that can be burned efficiently and used to generate electricityWhat is the role of a mill in a coalfired power plant?2015年8月1日 Mill problems originate mainly due to poor controls or faults occurring within the milling system As discussed by GQ Fan and NW Rees [3], the control of mills remains very simple in most of the power plants due to the fact that the mill system is highly nonlinear with strong coupling among the variables and it is very difficult to measure some important Review of control and fault diagnosis methods applied to coal estimate the pulverised coal flow using real time onsite plant data 2 COAL MILL MODELLING In thermal power plant, pulverization of coal is carried out by coal mill Raw coal is moved from the storage to the mill by conveyor mechanism The type of coal mill envisaged for our model is bowl mill which is shown in Fig1Pulverised Coal Flow measurement in Thermal Power Plant
.jpg)
Numerical and experimental analysis of pulverized coal mill
2014年10月1日 In a pulverized coalfired (PCF) thermal power plant (TPP), mixture of coal, air and gas is supplied into the furnace volume via the mill duct system and coal/air distribution should ideally be 2018年5月2日 Coal mill malfunctions are some of the most common causes of failing to keep the power plant crucial operating parameters or even unplanned power plant shutdowns Therefore, an algorithm has been developed that enable online detection of abnormal conditions and malfunctions of an operating mill Based on calculated diagnostic signals and defined Detection of Malfunctions and Abnormal Working Conditions of a Coal Mill%PDF17 %µµµµ 1 0 obj >/Metadata 202 0 R/ViewerPreferences 203 0 R>> endobj 2 0 obj > endobj 3 0 obj >/ExtGState >/ProcSet[/PDF/Text/ImageB/ImageC/ImageI Review of flexible operation of coalfired power plantsCoalfired plants are the most widely used power plant today They involve the combustion of coal producing high pressure (typically 2400–3500 psig, ~165–240 bar) and high temperature (>500ºC) steam which is used to drive a turbine at synchronous speed (3000 rpm in countries such as the UK with a 50 Hz supply frequency, 3600 rpm in Instrumentation and control in coalfired power plant ICSC
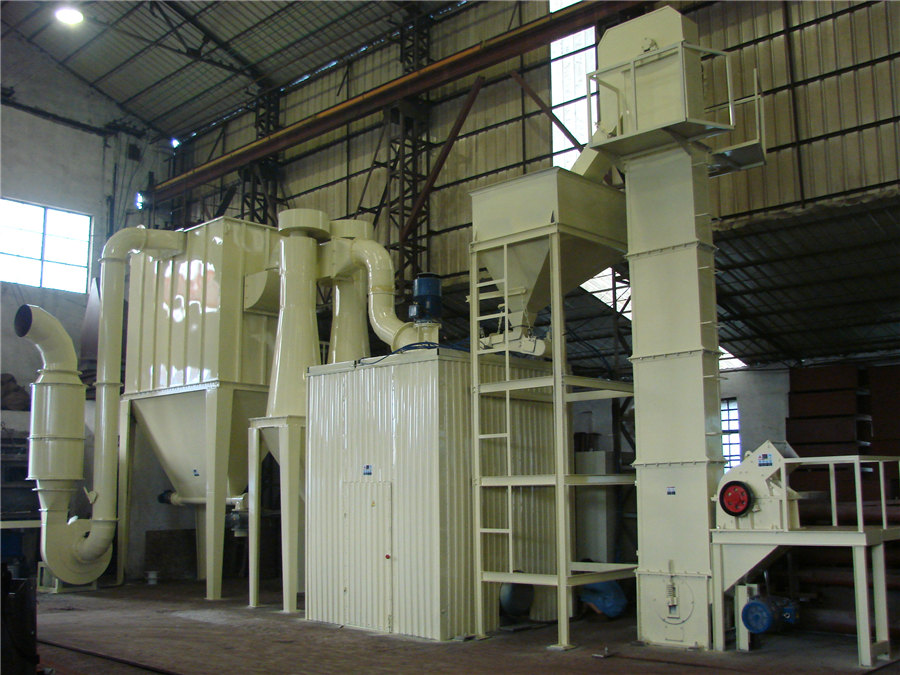
Mill Inerting and Pulverizer/Mill Explosion Mitigation
• Damage repair cost (Primary air inlet ducts, PA fans, mill internals, feeders, – Systems often named as “inerting systems” by coal fired power plant personnel include: • Steam Inerting Systems • Water fogging or deluge systems • Rehydration is exothermic and dried coal that is stagnate anywhere in the coal mill canThis article presents the performance (availability) evaluation of a typical coal fired power plant in a realistic working environment for identifying the critical subsystem and planning the preventive maintenance schedule For analysis, the entire thermal system is broken down into six subsystems ie, turbine, condenser, coal supply, water circulation, air circulation and boiler sub Performance Evaluation of a Coalfired Power Plant2021年9月9日 Rapid changes in electricity power markets have increased the production costs of coalfired power plants and pushed their production to the limits of profitability For power plants currently in operation, a possible approach to cope with this issue is to introduce novel methods that increase the plant’s reliability and availability Coal mills are a subsystem that should Impact of RemediationBased Maintenance on the Reliability of a Coal The evaluation will be done by way of touring the plant, Coal Mill Safety: A Critical Aspect of Power Plant Operations Introduction Coal mills, also known as pulverizers, play a critical role in power plants by grinding coal into fine powder, which is then used in various pyroprocessesCoal Mill Safety: A Critical Aspect of Power Plant Operations Coal
.jpg)
Coal Pulverizer – Power Plant Pall Corporation
Power generation industry studies have shown that pulverized coal power plants are an area where improved equipment reliability is essential The Electric Research Institute (EPRI) has determined that 1% of plant availability is lost on average due to pulverizerrelated problemsThe ball mill is a traditional coal pulverizer machine, which has been widely used since it was invented In the cement plant, the new dry process cement manufacturing requires the moisture content of coal powder to be 05% ~ 15%, while that of raw coal is 15% ~ 40% Therefore, the ball mill should have a drying function besides grindingCoal Mill in Cement PlantCoal Bowl Mill, for guaranteed performance at a 500 MW capacity NTPC thermal power plant The study was conducted to assess the effective performance of the pulverizers of this 500 MW boiler unit for its maximum capacity of 609 t/hr forA Study on 500 MW Coal Fired Boiler Unit’s Bowl Mill Coal Mill in Thermal Power Plant Free download as Word Doc (doc / docx), PDF File (pdf), Text File (txt) or read online for free This document discusses coal pulverizers/mills which are critical components that convert the stored energy in coal into electricity There are various types of pulverizers that primarily utilize grinding, drying, classification and circulation processesCoal Mill in Thermal Power Plant