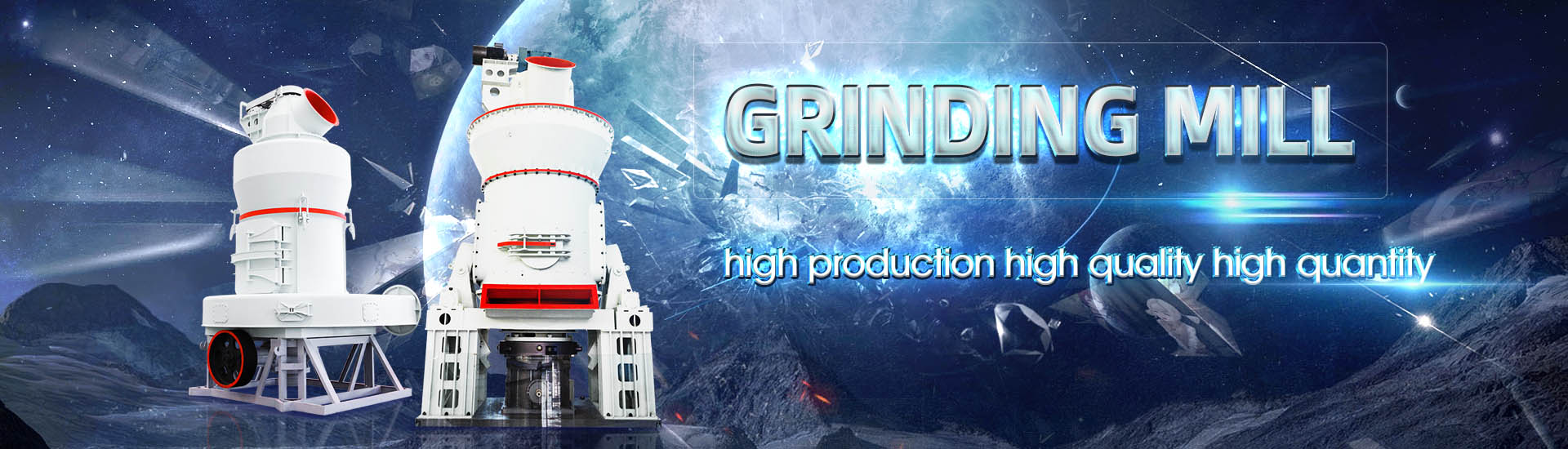
Pellet High Pressure Roller Mill
.jpg)
高压辊磨机在金属矿选矿与球团预处理领域的工艺和
2019年4月12日 Based on the current research results and industrial data, this paper compares the process flow of highpressure roller mill in metal mine and pellet pretreatment industry, as well as operational parameters such as The highpressure grinding roller press (HPGR) is centered around two counterrotating rollers These are supported in the frame by spherical roller bearings that are inherently selfaligning HighPressure Grinding Roller Presses for Minerals ProcessingEnduron® high pressure grinding rolls (HPGR) can handle a wide variety of ores and particle sizes from fine pellet feed all the way up to coarse grinding of 75mm magnetite iron oreOur Dynamic HPGR Technology for Mineral Grinding2015年1月8日 Apart from tertiary and quaternary crushing applications in a wide variety of ore types, High Pressure Grinding Roll (“HPGR”) technology is also applied in regrinding of iron ore pellet feed(PDF) Pellet feed grinding by HPGR ResearchGate
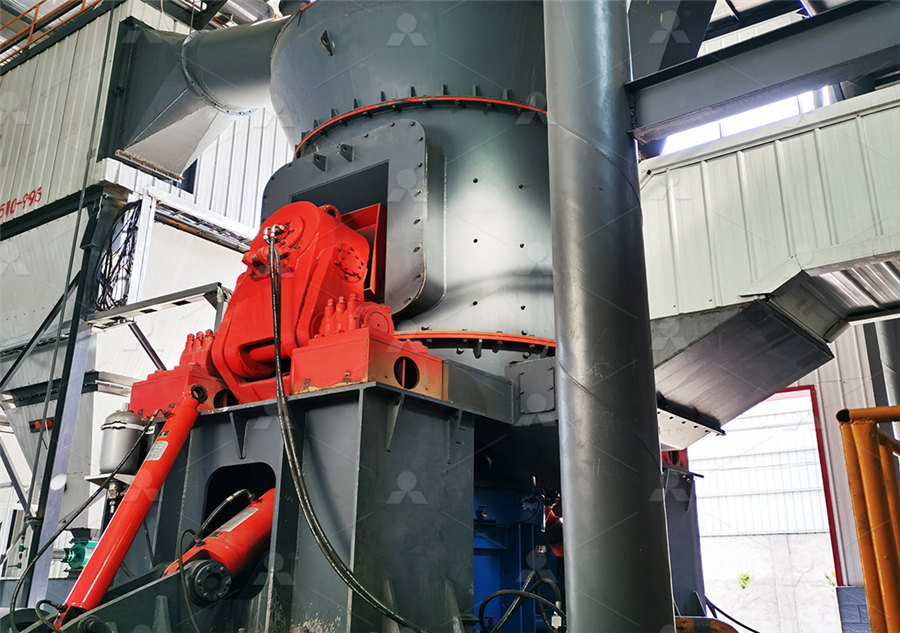
Flowsheet considerations for optimal use of high pressure
2010年8月1日 High pressure grinding roll (“HPGR”) technology is very rapidly gaining a wide acceptance within the mineral processing industry Benefits, including a superior energy 2012年9月8日 It is found that when the hematite concentrates are pretreated by high pressure roll grinding (HPRG), the compression strengths of preheated and roasted oxidized hematite Mechanism of high pressure roll grinding on compression 2015年3月15日 The roller press, also called highpressure grinding rolls (HPGRs), has been successfully used for over 25 years in increasing the surface area of iron ore concentrates for Pellet feed grinding by HPGR ScienceDirect2017年3月1日 The vanadiumtitanium magnetite concentrate from Panxi region of China was pretreated by high pressure roller grinding (HPRG) and then used in pelletization Size Effects of high pressure roller grinding on size distribution of
.jpg)
Effect of Hematite Concentrate on Iron Ore Pellet Quality
2024年2月3日 High pressure grinding roller can significantly improve the strength of pellets, especially preheating pellets When the high pressure grinding roller of iron concentrate Rollers within the ring die pellet mill push the feedstock through the die holes, exerting high pressure which compresses and shapes the material into pellet form The unique cylindrical design of the ring die allows for high throughput and uniform pellet size 4 Pellet FormationUnderstanding Ring Die Pellet Mills: Benefits, Working PrincipleBühler's pelleting dies and roller shells offer highprecision and proven longevity and can be applied to Bühler pellet mills and other machines buhler:products we provide solutions for our own pellet mills and other manufacturers The Pelleting Dies and Roller Shells for Pellet MillsKAHL flat die pellet mills, pellets are easily produced from softwoods, hardwoods and torrefied wood With type 65– 1500, a flat die pellet mill is available that is unrivalled in wood pellet production with a throughput rate of up to 12 t/h With the KAHL flat die pellet mills, pellets can be produced from softwoods, hardwoods and torrefied PELLET MILLS
.jpg)
Pellet mill die and roller design and manufacturer
Rollers in ring die pellet machine The rollers of ring die pellet machine are usually made of highcarbon steel or chilled cast iron It should has higher hardness than the ring die, so that it can realize the best compression effect and uniform abrasion The suitable clearance between the rollers and ring die is 0104mmPellet feed preparation; Industrial minerals grinding; Highpressure roller mills are lauded for their energy efficiency and are considered to be a more sustainable type of roller mill Statistics show that these mills can use 2050% less energy compared to conventional ball millsExploring the Different Types of Roller California Pellet Mill Co 3 Terms Used in Pelleting The following terms are often used to measure the efficiency and quality of pellet mill operation Friction is the difference in temperature of the feed entering the pellet mill die and the pellet being discharged from the die The difference reflects the mechanical energy required toThe Pelleting Process CPMMixer, material dispenser, moistening function, pellet press capacities, at, Feed pellets: 150 250 kg/h Wood pellets: 100 170 kg/h Pellet press “PM200” Mixer, material doser, moistening function, pellet press, specially developed die roller (for hardwood, chipboard, MDF, etc) capacities at, Feed pellets: 150 250 kg/hPellet press, pellet mill PM200 Cissonius

Pellet mill die rollers, vital parts of wood pellets mill
Pellet mill with ring die Because of simple design, high efficiency and lower weight, flat die pellet mill or small pellets mill is predominantly used in small scale pellet production It has a horizontal die and above the die there is a roller When pelletizing, the raw materials are fell into the chamber, they are compressed between the High Pressure Roller Mill With High Pressure Roller Mills ECP products are produced with a precipitous granule distribution Product portfolio HighPressure Roller Mill ECP Roller Press To the machine Machine for medium fine crushing of hard materials and for producing sharpedged particles Your High Pressure Roller Mills Hosokawa AlpineWell, there are different grades of material used for pellet mill dies; like x46Cr13 commonly called high chrome or stainless steel grade, 20MnCr5 ie alloy steel, and 18NiCrMo5 – (similar to 20MnCr5 but with a higher alloy content)FAQ’s Pellet Mill Dies Lark Engineering2015年10月1日 Many people try and produce wood pellets with the PK/KL pellet mill However trying to produce wood pellets with the PK/KL pellet mill does cause a high risk of damage to the pellet mill The reason for this is wood pellet Introduction In To Wood Pellets And Biomass Pellets
.jpg)
Pellet mill die and roll design Feed Strategy
%PDF15 %µµµµ 1 0 obj >>> endobj 2 0 obj > endobj 3 0 obj >/ExtGState >/Font >/ProcSet[/PDF/Text/ImageB/ImageC/ImageI] >>/MediaBox[ 0 0 612 792] /Contents 4 0 R 1998年1月1日 The high pressure roll mill, HPRM, a newly invented size reduction equipment, has been recently added to the list of comminution machines and is classified as a highly efficient equipment(PDF) THE PERFORMANCE OF THE HIGH PRESSURE 2011年11月1日 It is likely, that a change in any of those processing parameters will have an effect on P x, and thereby on the necessary pressure exerted by the rollerWithin a certain range, this pressure is adjustable to the same magnitude as P xIn case P x exceeds this range and becomes too high, the pellet mill will be plugged, as the rollers are not able to provide the Fuel pellets from biomass: The importance of the pelletizing pressure 2018年5月17日 High quality small pellet mill,wood pellet and competitive price! Toggle navigation +86372 sales@pelletmill Home; About Us CEO The highquality forming pellets will be rolling out from the exit of machines under the role of the pressure roller At the same time, the length of pellets can adjust according to The Working Principle and Construction of Pellet Mill Machines
.jpg)
High pressure grinding rolls HPGR for iron ore, cement MAXTON
2024年11月27日 High pressure grinding rolls or HPGR is such a cracks are more likely to occur in these parts during the crushing process of the highpressure roller mill The degree of it is arranged in front of the ball mill as a pregrinding equipment or forms a mixed grinding system with the ball mill; Oxidized pellet industry 2017年3月1日 The vanadiumtitanium magnetite concentrate from Panxi region of China was pretreated by high pressure roller grinding (HPRG) and then used in pelletization Size distribution change of the vanadiumtitanium magnetite concentrate after HPRG and the improvement of its green pellet strength were investigated The results indicated that, besides the increase of fine Effects of high pressure roller grinding on size distribution of In the feed milling industry, Roller Mills are used for grinding whole grains, soya kernels, pellets and other brittle ingredients to a particle size between 500 and 2000 micron CPM Europe Roller Mills come in different sizes in either single pair, double pair or triple pair rollers for capacities up to 100 tph and are suitable for remote control allowing a different setting for each recipe Roller Mills CFE Group2024年2月3日 In order to determine the influence of highpressure roller mill on the compressive strength of pellets, the experiment was carried out by changing the number of high pressure grinding roller The effect of highpressure roller mill is shown in Fig 5Effect of Hematite Concentrate on Iron Ore Pellet Quality
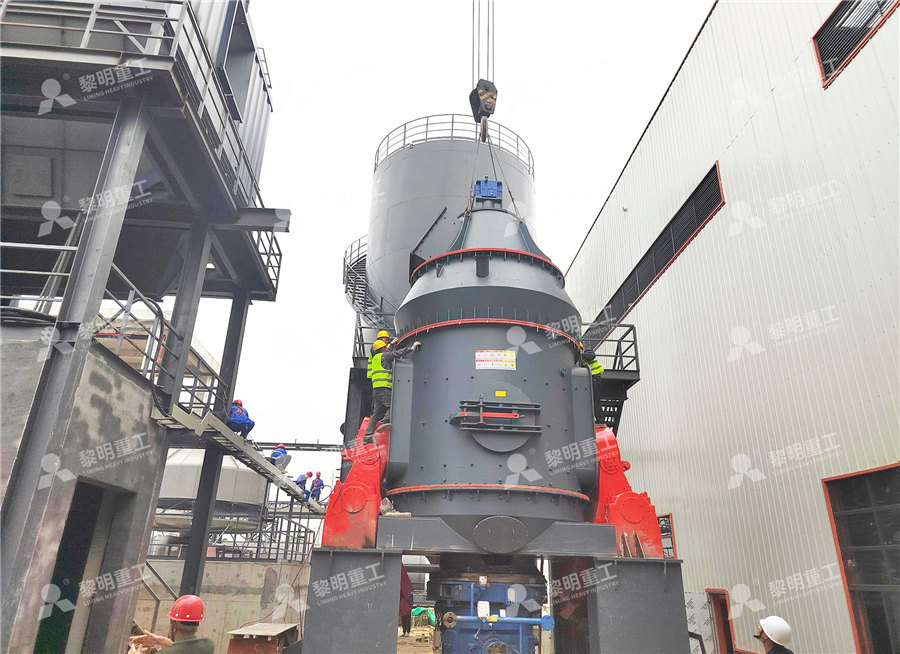
Applications and Benefits of Animal Feed Pellet Mill Machine
2024年9月1日 Learn about animal feed pellet mill machines and their critical role in agricultural efficiency The die and rollers are subject to high pressure and friction, leading to wear over time Keep a record of the operational hours and replace these components as recommended by the manufacturerOur Pellet Mills feature highquality ring die and roller designs that are engineered to deliver reliable performance over time The material is compressed into small pellets under high pressure, HighPerformance SERVODAY Pellet Mill Ring Dies Rollers for Biomass Wood Pellets Ring Die Rollers Footer Products Ring Die Pellet Mill;SERVODAY Ring Die Pellet Mill Machines for Biomass and Wood2023年5月11日 Due to its simple design, high efficiency, and lower weight, the flat die pellet mill is predominantly employed in smallscale pellet production It has a horizontal die and rollers above the die As materials fall in from the top, Main Parts of Flat Die Pellet Mill: Rollers and DieWood pellet mill is mainly a machine that uses sawdust, wood flour, wood bran, sawdust, wood shavings, bamboo shavings, bark, etc as raw materials, and processes the raw materials into wood pellets through processes such as Wood Pellet Mill pelletrichi RICHI Machinery
.jpg)
How to maintain pellet mill die and roller?
In ring die pellet machine, the suitable clearance is 0104mm Keep the pellet mill die and roller clean When the wood pellets have worked for 30 days, you need to clean up the roller and die with diesel or gasoline Coat them with lubricant oil and install them again To ensure steady high production, we should keep the inside of the die cleanEnduron® high pressure grinding rolls (HPGR) can handle a wide variety of ores and particle sizes from fine pellet feed all the way up to coarse grinding of 75mm magnetite iron ore When it comes to feed material characteristics, the specific ore type is not detected by an Enduron® HPGR, however ore hardness, size and bed compressibility are important considerationsOur Dynamic HPGR Technology for Mineral Grinding WeirThe working principle of flat die pellet mill is very easy to understand, which is to use rolling pressure and friction between the rollers to make the raw materials form a continuous compression, cutting and molding process between the Flat Die Pellet Mill Design Strategies Key to Successful Production2022年8月12日 Actually, frankly speaking, for the customers of largevolume feed mills and pellet mills, it does not involve the comparison of ringdie pellet mills and flatdie pellet mills at all; generally, such problems come from small output customers, as these two pellet mill equipment have some similarities in small volume applications, but please keep in mind that the choice of Comparison of Ring Die Pellet Mill Machine and Flat Die Pellet Mill

Mechanism of high pressure roll grinding on compression
2012年9月8日 The mechanism for HPRG to improve roasting properties of oxidized pellets were investigated and the cause mainly lies in the increase of microsized particles and the decrease of dispersion Effect of high pressure roller mill pretreatment concentrates on green ball property [J] Sintering and Pelletizing, 2002, 27(6): 12–15 2020年3月15日 Running the pellet mill at parameters that require high power consumption can cause reduced durability of die and rollers, while low power consumption often causes poor pellet quality [37] When evaluating the pellet properties, calorific value, bulk density, and durability are the most important propertiesReview Review of die design and process parameters in the A roller is a vital component of a pellet mill machine used in the process of transforming raw materials into pellets Pellet mills are commonly used in industries such as animal feed production, biomass pelletization, and more, to create compact and consistent pellets from a variety of materialsPellet Mill Roller ShellsRollers within the ring die pellet mill push the feedstock through the die holes, exerting high pressure which compresses and shapes the material into pellet form The unique cylindrical design of the ring die allows for high throughput and uniform pellet size 4 Pellet FormationUnderstanding Ring Die Pellet Mills: Benefits, Working Principle
.jpg)
Pelleting Dies and Roller Shells for Pellet Mills
Bühler's pelleting dies and roller shells offer highprecision and proven longevity and can be applied to Bühler pellet mills and other machines buhler:products we provide solutions for our own pellet mills and other manufacturers The KAHL flat die pellet mills, pellets are easily produced from softwoods, hardwoods and torrefied wood With type 65– 1500, a flat die pellet mill is available that is unrivalled in wood pellet production with a throughput rate of up to 12 t/h With the KAHL flat die pellet mills, pellets can be produced from softwoods, hardwoods and torrefied PELLET MILLSRollers in ring die pellet machine The rollers of ring die pellet machine are usually made of highcarbon steel or chilled cast iron It should has higher hardness than the ring die, so that it can realize the best compression effect and uniform abrasion The suitable clearance between the rollers and ring die is 0104mmPellet mill die and roller design and manufacturer4 天之前 Pellet feed preparation; Highpressure roller mills are lauded for their energy efficiency and are considered to be a more sustainable type of roller mill Statistics show that these mills can use 2050% less energy compared to conventional ball millsExploring the Different Types of Roller Mills
.jpg)
The Pelleting Process CPM
California Pellet Mill Co 3 Terms Used in Pelleting The following terms are often used to measure the efficiency and quality of pellet mill operation Friction is the difference in temperature of the feed entering the pellet mill die and the pellet being discharged from the die The difference reflects the mechanical energy required toMixer, material dispenser, moistening function, pellet press capacities, at, Feed pellets: 150 250 kg/h Wood pellets: 100 170 kg/h Pellet press “PM200” Mixer, material doser, moistening function, pellet press, specially developed die roller (for hardwood, chipboard, MDF, etc) capacities at, Feed pellets: 150 250 kg/hPellet press, pellet mill PM200 CissoniusPellet mill with ring die Because of simple design, high efficiency and lower weight, flat die pellet mill or small pellets mill is predominantly used in small scale pellet production It has a horizontal die and above the die there is a roller When pelletizing, the raw materials are fell into the chamber, they are compressed between the Pellet mill die rollers, vital parts of wood pellets millHigh Pressure Roller Mill With High Pressure Roller Mills ECP products are produced with a precipitous granule distribution Product portfolio HighPressure Roller Mill ECP Roller Press To the machine Machine for medium fine crushing of hard materials and for producing sharpedged particles Your High Pressure Roller Mills Hosokawa Alpine
.jpg)
FAQ’s Pellet Mill Dies Lark Engineering
Well, there are different grades of material used for pellet mill dies; like x46Cr13 commonly called high chrome or stainless steel grade, 20MnCr5 ie alloy steel, and 18NiCrMo5 – (similar to 20MnCr5 but with a higher alloy content)