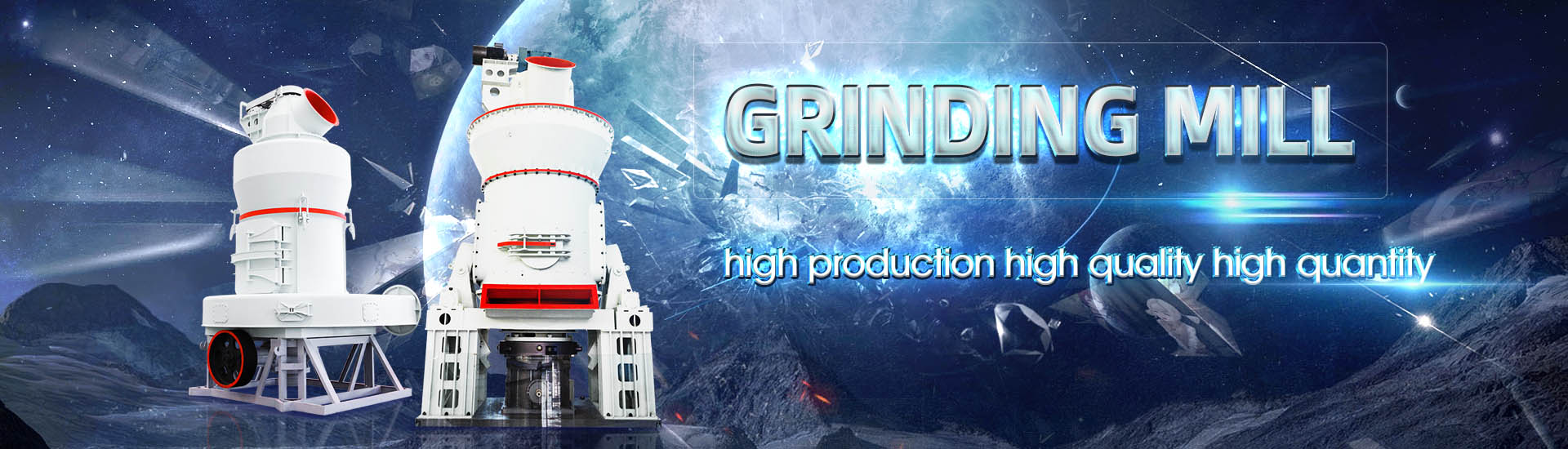
Abrasive powder making process

Abrasive Processing an overview ScienceDirect Topics
These irregularities reduce the induction period of bone growth on the implant surface One of the most commonly used methods is abrasive processing Abrasives are used either in bound form (cemented or sintered abrasive belts, circles and bars) or in free powdered form2024年3月26日 Toughness: An abrasive needs to withstand the pressure exerted during the grinding process Grain Structure: Determines the efficiency and finish of the abrasive action What Makes Abrasive Minerals Special? What is Abrasive: Definition, Types, Applications Safety2020年1月1日 AWJ process is classified into abrasive water injection jet and abrasive slurry jet on the basis of the different ways of mixing between abrasive and water This study explores Abrasive Water Jet Machining process: A state of art of reviewAbrasive Grain Processing Abrasive grains for both bonded and coated abrasive products are made by graded crushing and close sizing of either natural or synthetic abrasives Raw 1131 Abrasives Manufacturing US EPA
.jpg)
Introduction to Abrasive Based Machining and Finishing
2020年5月11日 In this chapter, each of the developed processes that utilize abrasives (applied in bonded or loosely) has been discussed with fundamental mechanism, process These findings advance our understanding of abrasive machining processes and provide valuable insights for optimizing abrasive tool designs and machining strategies for enhanced surface Advanced Abrasive Processing Technology and Applications2023年1月31日 Highprecision abrasive machining is an essential process for highvalue manufacturing It involves machines, processes and systems often reflected in highperformance grinding and/or abrasive machines, a complex High Precision Abrasive Machining: Machines, Postprocessing with abrasives depends on mechanical action between the hard abrasive particles on softer substrate The nonconventional postprocessing methods use different Abrasive and nonconventional postprocessing techniques to

MICRO MACHINING PROCESSES
hard abrasive particles, constant powder feeding devices andmaskingtechnology Introduction 5 Micropattern making process for the AJMM Park et al (2004) Microgrooving of glass using microabrasive jet machining, Journal of Materials Processing Technology 146 (2004) 234–240Formulas for MRR in abrasive jet machining process Establish analytical formula for MRR (Modeling) Condition for equal MRR in ductile and brittle materials in AJM How material removal rate can be increased? Process capability of Abrasive Jet Machining – Process, Parameters, An abrasive is a material, often a mineral, that is used to shape or finish a workpiece through rubbing [1] which leads to part of the workpiece being worn away by frictionWhile finishing a material often means polishing it to gain a smooth, reflective surface, the process can also involve roughening as in satin, matte or beaded finishes In short, the ceramics which are used to cut, Abrasive Wikipedia1 Steel: Steel structures are one of the most popular substrates for powder coating It's durable, strong, and versatile, making it a prime choice for various industries Powdercoated steel is commonly seen in automotive parts, appliances, outdoor furniture, and industrial equipmentPowder Coating Process Explained – A Detailed Breakdown
.jpg)
Abrasive Powder Diamond CBN Abrasives for Polishing and
Abrasives Powder Diamond and cubic boron nitride (CBN) abrasives for grinding wheels and dicing blades, and micron powders for polishing and lapping applications Hyperion Materials Technologies manufactures a full line of diamond and cubic boron nitride (cBN) mesh and powders for all of your abrasives needsThe Lapping Powder The abrasive powder for lapping comes in the form of silicon carbide, aluminum oxide, boron carbide, diamond powders (also see Page 38 “Lapping with Diamond”), or similar products In addition, the quality criteria are the particle size, size distribution, hardness, shape, and number of edgesAbrasive Powder for Lapping Abrasive Powder Types Stahli USAAbrasive, sharp, hard material used to wear away the surface of softer, less resistant materials Included within the term are both natural and synthetic substances, ranging from the relatively soft particles used in household cleansers and jeweler’s polish to the hardest known material, theAbrasive Types, Grades, Uses Applications BritannicaSilicon Carbide Grinding Powders for fine grinding or rough polishing of semiconductors, ceramics and ferrous materials Softer than diamond but harder than aluminum oxide Normally used as a slurry Silicon Carbide Powder (or SiC) is designed for grinding and lapping operations where high precision finishes are required and processing costs are importantSilicon Carbide Powder is Abrasive Polishing Powders Grinding Polishing Powders
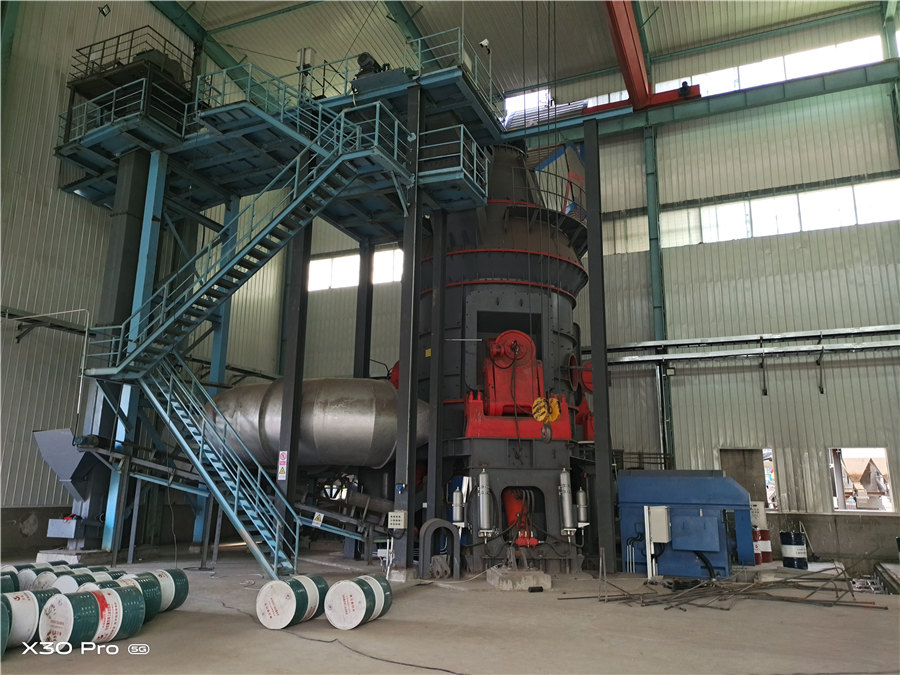
1131 Abrasives Manufacturing US EPA
11312 Process Description17 The process description is broken into three distinct segments discussed in the following sections: production of the abrasive grains, production of bonded abrasive products, and production of coated abrasive products Abrasive Grain Manufacturing 2020年7月1日 Both types of MAPs can polish various shapes of workpieces due to their selfadaptability and selfsharpening Lin et al [12] studied the freeform surface of SS304 material using sintered alumina MAPs They studied the machining efficiency of this magnetic abrasive tool, and obtained the optimal parametric condition in the MAF processModeling of material removal in magnetic abrasive finishing process 2015年1月1日 Honing is the finishing process that renders the smoothest surface texture and the greatest accuracy The abrasive is made into a slab (stone, stick), and is moved in a rapid oscillating motion over the surface (usually a hole) to be finished (Figure 33 a)Superfinishing is a variant in which oscillating motion is imparted to a fairly large stone, and the surface pressure Abrasive Processes ScienceDirect2022年11月1日 MultiCriteria Decision Making of Abrasive Water Jet Machining Process for 2024T3 Alloy Using Hybrid Approach November 2022 Advances in Science and Technology – Research Journal 16(5):155162MultiCriteria Decision Making of Abrasive Water Jet Machining Process
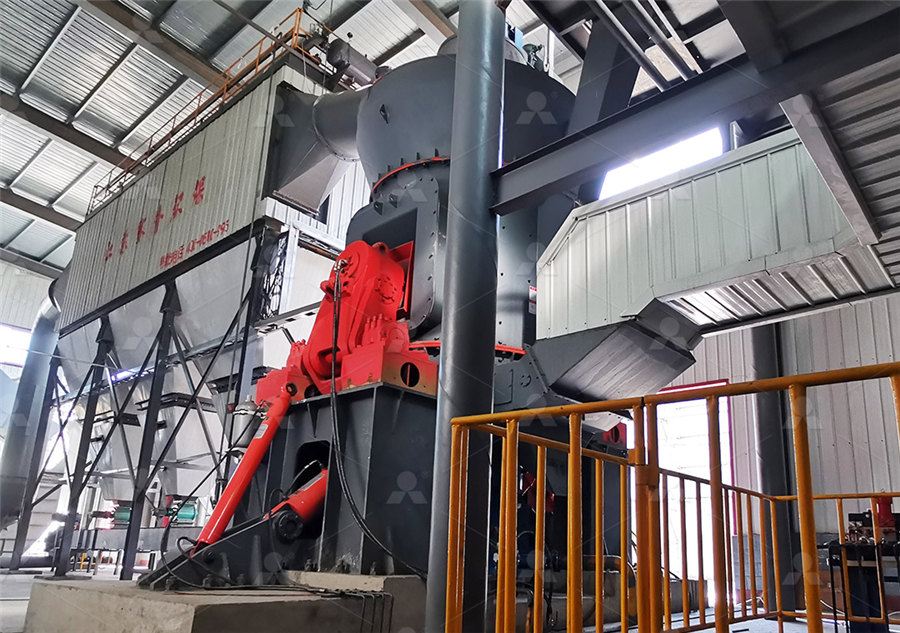
Abrasive Water Jet Machining process: A state of art of review
2020年1月1日 In AWJ machining, the material is removed by the erosion process, wherein hard abrasive particles are suspended in a high velocity of the water jet stream, which, in turn, increases the acceleration of the abrasive particles, and their kinetic energy impingement towards the target material, causing material removal [3]Fig1 (c) shows the basic layout of injection 2021年2月23日 In an open coat abrasive, 50% or 75% of the cover is coated with abrasive grain These grains incorporate materials such as corundum, garnet, silicon carbide, light brownish aluminum oxide, heat handled aluminum oxide, zirconia alumina, and ceramic alumina Abrasive Backing Types Abrasive backing varieties are paper, fabric, film, or fiberAbrasive: Material Types Industrial ApplicationsABRASIVE POWDERS: INFO, DETAILS Particle Size: 1 to 500 microns Options for the WIDEST Range of Applications; SDS for ABRASIVE POWDERS; ABRASIVE LAB; ABRASIVES: CONTROL YOUR PROCESS; MICRO ABRASIVE PROCESSING 101 SWAM ® Micro Sandblasting: Technology, Options, Precise Control, Flexibility; R D: PROCESS Crystal Mark: Abrasive Powders Crystal Mark Micro Abrasive pipe Abrasive particles can be used as unbonded, loosely bonded or bonded Bonded magnetic abrasive particles are prepared by sintering of ferromagnetic powder (iron) and abrasive powder at a very high pressure and manufacturing process employed determines surface finish level Some processes are inherently capable ofMAGNETIC ABRASIVE FINISHING Zenodo
.jpg)
Lapping Process: Definition, Working Principle, Types, Material
2022年5月21日 Abrasive particles often reduce or flatten the tops and ridges found on the surface of the work Characteristics/ Signs of the Lapping process: The following features of the Lapping Process are: The size of the Abrasive grit used in the lapping process varies from 120 to 1200 mesh depending on the smoothness of the surface you preferSalmon, Stuart C Modern Grinding Process Technology McGrawHill, 1992 Periodicals Murray, Charles J "Retainer System I would like to know the technology and which material is used for making of abrasive wheels please send me the names of materials for the purpose of mineHow grinding wheel is made material, history, used, parts, If the diamond abrasive powder crystal form is flake particles, it is easy to cause scratches and wear marks to the polishing ceramic or stone after being made into a resin diamond abrasive tool; If the crystal form of synthetic diamond powder particles is round, then the holding force between the diamond particles and resin bonds is not strong enoughSynthetic Diamond Powder for Making Resin Bond Diamond 2017年8月28日 Production of spherical Ti powder Making spherical powder is not a specific processing technique However, it is singled out here because it is in high demand for AM using selective laser sintering or electron beam sintering techniques Titanium alloy, Ti–6Al–4V in particular, is one of the prime examples of AM metalsPowder metallurgy of titanium – past, present, and future
.jpg)
Micron Diamond Powders Exceptional Cutting
Diamond is one of the hardest known materials, making it ideal for grinding hard and brittle materials such as ceramics, glass, and metals In addition, Micron diamond powders are often used as an abrasive material in grinding and 514 Effect of abrasive powder The effect of abrasive powders (nonmagnetic particles) is much less than the other parameters and is negligible However, as shown in Figure 9, alumina powder (Al 2 O 3) has a slightly better effect on surface finishing Effect of abrasive particle morphology along with other 23 Nonmagnetic abrasive particle (Abrasive powders) As mentioned in the introduction, abrasive particles include ferromagnetic particles and fine abrasive powders There are different types of abrasive powders used for finishing process including silicon carbide (SiC), aluminum oxide (Al 2O 3), Cubic boron nitride(CBN), Diamond powder Effect of abrasive particle morphology along with other Based on tribological considerations and comparing behavior of workmaterials from the three main groups (Table 163) during abrasive processing, it is possible to reach the following general conclusions:Owing to high values of density and surface energy, as well as susceptibility to tribochemical attack, metals are beginning to be replaced by other materials for many Abrasive Processing an overview ScienceDirect Topics
.jpg)
Study on Polysaccharide Bonded Abrasive Tool Using
2023年11月13日 Aiming to green machining of single crystal sapphire, polysaccharidebonded soft abrasive tool using hydrothermal gelatinisation method was proposed Mechanical properties of prepared polysaccharide films show that when the weight ratio of natural polysaccharide to crosslinked polysaccharide is 1:1, the tensile strength and extension rate of the film are containing the abrasive powder and vibrating at 50 c/s, entrains the abrasive particle and is the passed into a connecting hose This abrasive and gas mixture emerges from a small nozzle at high velocity A pressure regulator controls the gas flow and pressureThe nozzle is mounted on a fixture The work piece is placed in frontSynthesis And Analysis Of Abrasive Jet Machine For Brittle 2019年12月1日 In this work, the atomization process was utilized in order to fabricate significantly high content of diamond powders on the surface of spherical magnetic abrasive powder (MAP)Preparation and characterization of spherical diamond magnetic abrasive 2024年5月13日 Abrasive Tool Design: The shape, bond, and structure of the abrasive tool can influence the cutting action and the type of finish that can be achieved Pros and Cons of Abrasive Machining Like any manufacturing process, abrasive machining presents its own set of advantages and limitations: Pros:Abrasive Machining: What it is, Its Types and Applications LEADRP

MICRO MACHINING PROCESSES IIT Kanpur
hard abrasive particles, constant powder feeding devices andmaskingtechnology Introduction 5 Micropattern making process for the AJMM Park et al (2004) Microgrooving of glass using microabrasive jet machining, Journal of Materials Processing Technology 146 (2004) 234–2402020年1月2日 During magnetic abrasive finishing process, finishing powder, which is responsible for the se vere deterioration of surface finish Kim and Kwak [34] enhanced the performance of the MAF (PDF) Magnetic Abrasive Finishing Process ResearchGatehard abrasive particles, constant powder feeding devices andmaskingtechnology Introduction 5 Micropattern making process for the AJMM Park et al (2004) Microgrooving of glass using microabrasive jet machining, Journal of Materials Processing Technology 146 (2004) 234–240MICRO MACHINING PROCESSESFormulas for MRR in abrasive jet machining process Establish analytical formula for MRR (Modeling) Condition for equal MRR in ductile and brittle materials in AJM How material removal rate can be increased? Process capability of Abrasive Jet Machining – Process, Parameters,
.jpg)
Abrasive Wikipedia
An abrasive is a material, often a mineral, that is used to shape or finish a workpiece through rubbing [1] which leads to part of the workpiece being worn away by frictionWhile finishing a material often means polishing it to gain a smooth, reflective surface, the process can also involve roughening as in satin, matte or beaded finishes In short, the ceramics which are used to cut, 1 Steel: Steel structures are one of the most popular substrates for powder coating It's durable, strong, and versatile, making it a prime choice for various industries Powdercoated steel is commonly seen in automotive parts, appliances, outdoor furniture, and industrial equipmentPowder Coating Process Explained – A Detailed BreakdownAbrasives Powder Diamond and cubic boron nitride (CBN) abrasives for grinding wheels and dicing blades, and micron powders for polishing and lapping applications Hyperion Materials Technologies manufactures a full line of diamond and cubic boron nitride (cBN) mesh and powders for all of your abrasives needsAbrasive Powder Diamond CBN Abrasives for Polishing and The Lapping Powder The abrasive powder for lapping comes in the form of silicon carbide, aluminum oxide, boron carbide, diamond powders (also see Page 38 “Lapping with Diamond”), or similar products In addition, the quality criteria are the particle size, size distribution, hardness, shape, and number of edgesAbrasive Powder for Lapping Abrasive Powder Types Stahli USA

Abrasive Types, Grades, Uses Applications Britannica
Abrasive, sharp, hard material used to wear away the surface of softer, less resistant materials Included within the term are both natural and synthetic substances, ranging from the relatively soft particles used in household cleansers and jeweler’s polish to the hardest known material, theSilicon Carbide Grinding Powders for fine grinding or rough polishing of semiconductors, ceramics and ferrous materials Softer than diamond but harder than aluminum oxide Normally used as a slurry Silicon Carbide Powder (or SiC) is designed for grinding and lapping operations where high precision finishes are required and processing costs are importantSilicon Carbide Powder is Abrasive Polishing Powders Grinding Polishing Powders 11312 Process Description17 The process description is broken into three distinct segments discussed in the following sections: production of the abrasive grains, production of bonded abrasive products, and production of coated abrasive products Abrasive Grain Manufacturing 1131 Abrasives Manufacturing US EPA2020年7月1日 Both types of MAPs can polish various shapes of workpieces due to their selfadaptability and selfsharpening Lin et al [12] studied the freeform surface of SS304 material using sintered alumina MAPs They studied the machining efficiency of this magnetic abrasive tool, and obtained the optimal parametric condition in the MAF processModeling of material removal in magnetic abrasive finishing process