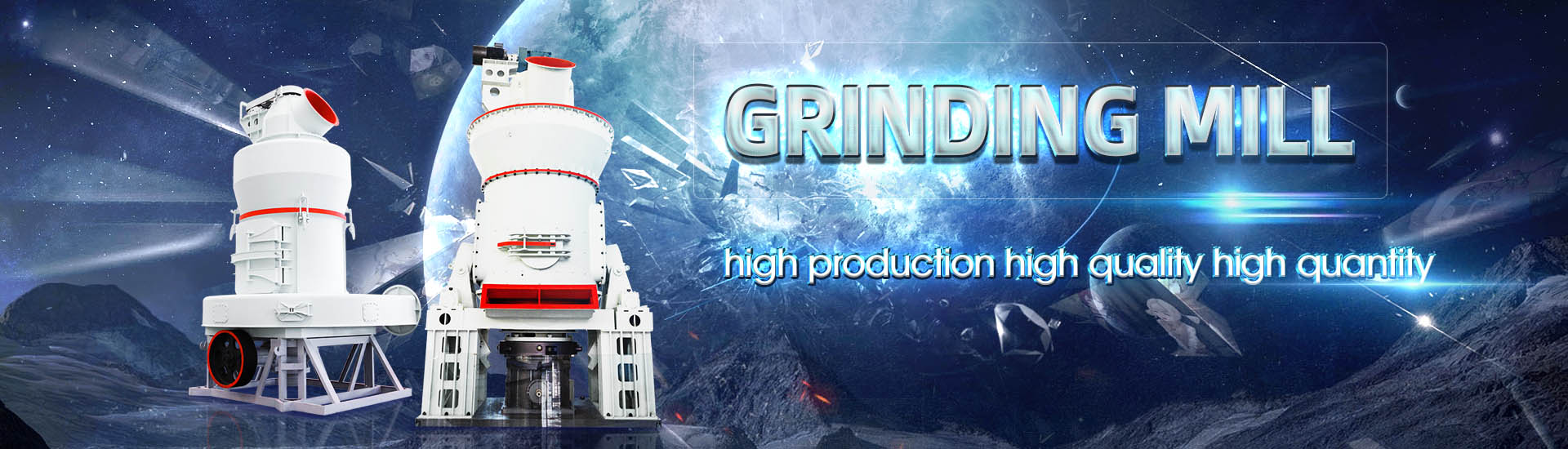
Ore mill quicklime iron mixture
.jpg)
Effect of Oxygen Enrichment on Top Layer Sinter Properties J
Sintering is a process in which iron ore fines along with limestone, dolomite, coke fines, quicklime GCP dust, flue dust, mill scale and return sinter are mixed with water to form nodules and then 2022年12月31日 This paper aims to study the melt and flow characteristics of iron ore and analyze the variation law of pore structure with fluidity of iron ore during sintering First, the Experimental study on melt and flow characteristics and pore 2021年10月1日 The addition of iron ore in the form of concentrate and micropellets to the sinter mixture enhances the mean sphericity of the granules while decreasing the sinter bed voidage Influence of quick lime on pore characteristics of hightemperature 2011年5月29日 High reactive quicklime should be used as much as possible in the sintering mixture It reached better sintering results while quicklime was used instead of limestone and Sintering characteristics of fluxes and their structure optimization

Importance of intensive mixing on sintering with finegrained iron
2020年11月1日 The flux (quicklime) is evenly distributed, and it can also optimize the mineralization process because iron oxides can easily contact CaO and generate calcium 2023年1月19日 In this study, we present a method to determine the optimum water content using the agitation torque of wet ore powder blended with quicklime First, we investigated the Optimum Water Content Estimation for Wet Granulation of Iron In this study, we present a method to determine the optimum water content using the agitation torque of wet ore powder blended with quicklime First, we investigated the agitation torque for Optimum Water Content Estimation for Wet Granulation of Iron 2022年11月25日 Quicklime was selected as the best conditioning agent through conditioningdewatering experiments because it could effectively reduce the viscosity of oily CRM sludge and improve theEnhancing the Dewaterability of Oily Cold Rolling Mill
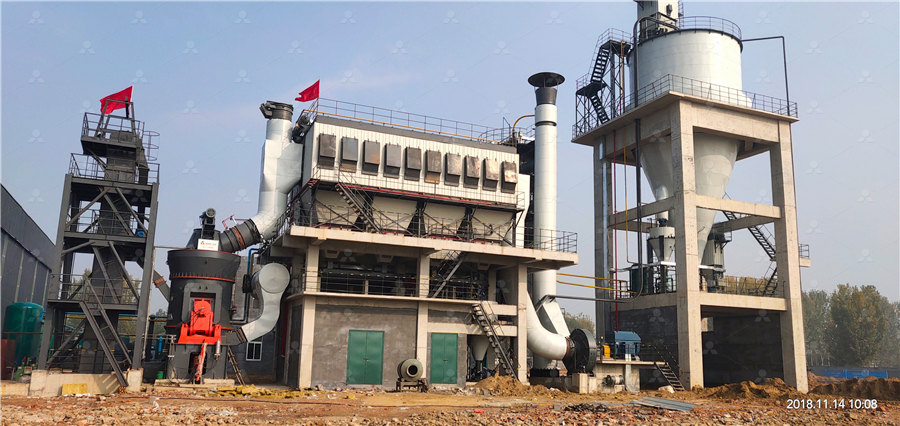
Milled Quicklime for Hot Metal Desulphurization
In the hot metal desulphurization process, Carmeuse offers fluid milled lime or blends to be injected into the hot metal through an immersed lance using an inert carrier gas such as argon or nitrogen2022年7月15日 For wet granulation of iron ore powders, for the first time, the use of agitation torque has been proposed in our previous study 23) Our previous study demonstrated that the optimum water Determining Optimum Water Content for Iron Ore Blending ratio of sinter mixture used in the experiments Material Iron ore Coke Return Sinter Limestone Dolomite Quick lime Mill scale Flue dust GCP dust Mass (%) 5525 5 24 625 5 15 1 1 1 Fig 2 Schematic diagram of sinter pot (Online version in color)Effect of Oxygen Enrichment on Top Layer Sinter Properties J 2016年10月28日 dusts and mill scale, Eisele and Kawatra, 2003), Granulation consists of the homogenization of iron ore mixture in a rotation drum with 78% water for a few minutes with the finalityIron Ore Sintering: Raw Materials and Granulation
.jpg)
A Case Study of Sintering with Low Silica Iron Ore
The reference ratio of blended ore is 8% A, 13% B, 15% C, 6% D, 12% E, 37% F, and 9% G In order to obtain a suitable SiO 2 content, the proportion of E ore in blended ore was reduced and the proportion of other iron ores in blended ore was fixed In other words, the proportion of other ores increases proportionally2022年7月15日 Carbon monoxide is the major hazardous component in flue gas exhausting from the iron ore sintering This study aims to reduce the CO emission by changing the sinter parameters by sintering pot (PDF) Influence of Sinter Parameters on CO Emission in Iron Ore 2023年3月23日 Hydrogenbased direct reduced iron (H2DRI) is an alternative pathway for lowcarbon steel production Yet, the lack of established process and business models defining “green steel” make it Green steel: design and cost analysis of hydrogenbased direct iron 2022年11月25日 Enhancing the Dewaterability of Oily Cold Rolling Mill Sludge Using Quicklime as a Conditioning Agent November 2022; ACS Omega 7 as well as iron ore was 2:1, and the mixture was stirred Enhancing the Dewaterability of Oily Cold Rolling Mill Sludge
.jpg)
123: Metals and Ores Chemistry LibreTexts
Iron ore is reduced with coke in a blast furnace (Figure \(\PageIndex{1}\)) The blast furnace is loaded with iron ores, usually hematite Fe 2 O 3 or magnetite Fe 3 O 4, together with coke (coal that has been separately baked to remove volatile components) Air preheated to 900 °C is blown through the mixture, in sufficient amount to turn the 2023年8月1日 The iron and steel metallurgy industry faces the question of how to replace carbon in iron ore reduction to reduce CO 2 emission in basic industries and achieve the expectation of "double carbon" This study investigates the reduction swelling of individual iron ore pellet under mixed H 2CO atmospheres and at temperatures of 800–1000 ℃ by insitu Direct reduction of iron ore pellets by H2CO mixture: An insitu 2022年12月31日 The raw materials used are five kinds of iron ores and quicklime Table 1 shows different iron ores’ size distribution and bulk density (Zhou et al, 2020a) The five iron ores used in this study came from Australia and Brazil and had a wide size distribution ranging from 0 to 10 mm Table 2 showsExperimental study on melt and flow characteristics and pore Xiaoxian HUANG Cited by 289 of Central South University, Changsha (CSU) Read 41 publications Contact Xiaoxian HUANGXiaoxian HUANG Doctor of Engineering Central
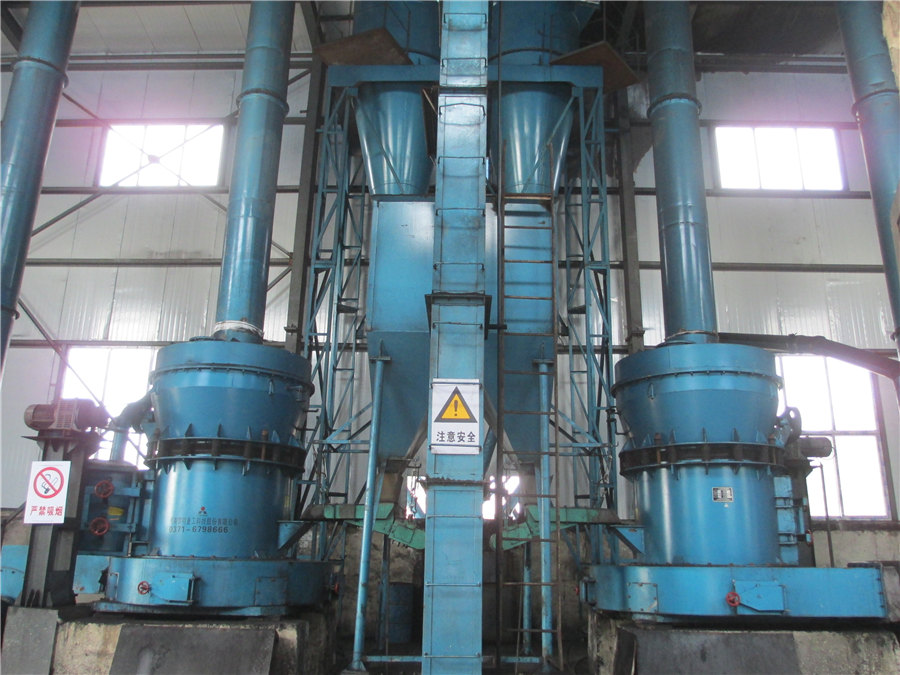
Evaluation of Quality Parameters and Mineralogy of Iron Ore
2024年9月26日 The present article focuses on incorporating mill scale, a steel plant solid waste, into the iron ore pelletization process The characterization results indicated that the mill scale contained about 71% of Fe and predominantly consists of magnetite and wustite mineral phases A detailed pelletization study is conducted using the mill scale at different proportions (0%, 2022年4月8日 NO and SO2 are representative harmful gases generated in steel works, and iron ore sintering process accounts for more than 50 pct of total generation The current study investigated the effects of adding CaO and FeO, which are the components contained in raw materials to sinter mix on the formation of NO and SO2 The addition of CaO to sinter mix Effects of Adding Calcined Dolomite and Mill Scale to Sinter Mix 2023年7月20日 Dewatering is critical to oily cold rolling mill (CRM) sludge treatment Therefore, finding an efficient, energysaving, and applicable dewatering technology for oily CRM sludge is still urgent This study investigated the performance of quicklime as a conditioning agent for oily CRM sludge conditioning and dewatering The interactive effects of quicklime dosage, Oily cold rolling mill sludge conditioned by quicklime to improve 2020年11月1日 This investigation mainly focused on revealing the importance and function mechanism of intensive mixer on sintering performance with 100% finegrained iron ore materials (the proportion of −0 Importance of intensive mixing on sintering with finegrained iron ore
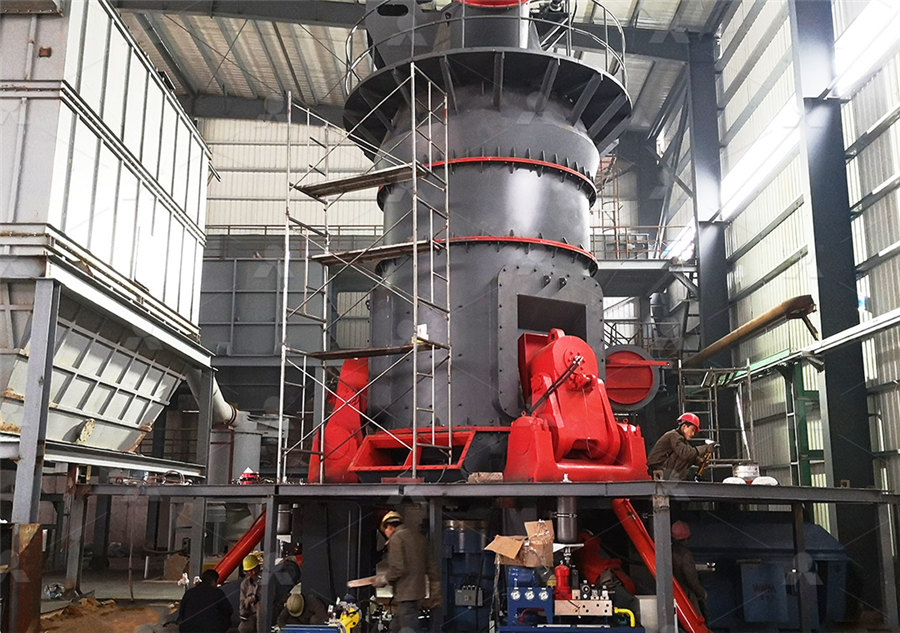
Sintering characteristics of fluxes and their structure optimization
2011年5月29日 Sintering characteristics of common fluxes and sintering blending ores, such as mineralization capacity, liquid generation capacity, consolidation strength, were examined to master the behavior and effect of fluxes in sintering Based on fundamental studies, sinter pot tests were carried out to obtain the principles of optimizing the sinter flux structure The results 2018年7月11日 The iron concentrate is a product of the hydrometallurgical processing of uranium ore As it contains up to 65% of iron, it can be used as a raw material for ferrous metallurgy (Fernández Iron Ore Agglomeration Technologies Provisional chapter Iron Ore and OreC were Brazilian hematite iron ores with TFe > 6400%, while OreD to OreG were four Australian limonite ores with LOI (Loss of ignition) > 500% The OrePIB (the proportionfixed ironbearing blend) was a mixture of 4 kinds of recycling iron bearing materials and 4 kinds of undersized iron ore fines (sinters, pellets and lump ores)Interpretation on Iron Ore Granulation Process Based on Particle2021年10月1日 At present around 6–7% of iron ore slimes, out of total production, are being generated and accumulated at iron ore mine sites of National Mineral Development Corporation Limited, IndiaInfluence of quick lime on pore characteristics of high
.jpg)
IRON AND STEEL chemguide
The common ores of iron are both iron oxides, and these can be reduced to iron by heating them with carbon in the form of coke Coke is produced by heating coal in the absence of air Coke is cheap and provides both the reducing 2021年2月21日 Methods Experimental Procedure The reference ratio of blended ore is 8% A, 13% B, 15% C, 6% D, 12% E, 37% F, and 9% G In order to obtain a suitable SiO 2 content, the proportion of E ore in blended ore was reduced and the proportion of other iron ores in blended ore was fixed In other words, the proportion of other ores increases proportionallyA Case Study of Sintering with Low Silica Iron Ore2022年12月12日 Phase Transformation and Enhanced Zn Removal Technology During the Iron Ore Sintering Process Quicklime 020 390 7962 128 099 In this study, 21 kg of the mixture of ore, dust,Phase Transformation and Enhanced Zn Removal Sintering is a process by which a mixture of iron ores, feed 11 Sinter feed 12 Sinter feed 14 Sinter feed 15 Sinter feed 16 Pellet fines 1 Pellet feed 5 Dolomitic limestone Quicklime Area cleaning material Mill scale from operations Steel sludge Slag of KR process Lump and sinter fines Carbonaceous dust of coke plant Steel slag Thin Characterization and mass balance of trace elements in an iron ore
.jpg)
Direct Alloying Steel with Chromium by Briquettes Made from
Direct Alloying Steel with Chromium by Briquettes Made from Chromite Ore, Mill Scale, and Petroleum Coke Xianfeng Hu, Lena Sundqvist €Okvist, Johan Eriksson, Qixing Yang, and Bo Björkman2023年9月24日 where Q is the flow rate of gas through the bed, m 3 /min; A is the crosssectional area of the bed, m 2; h is the height of the bed, m; and ΔP is the pressure drop of the bed, mm water column The sintering mixture was composed of iron ores, coke breeze and fluxes (dolomite, limestone and quicklime) with different proportions, in which the quicklime was 3%, Prediction of suitable water content in granulation of sintering 2017年1月1日 Finally, the magnetic component of the roasted ore can be recovered by magnetic separation after being liberated from gangue minerals Many pilotscale suspension magnetizing roasting and magnetic Recovery and separation of iron from iron ore using innovative 2020年11月12日 Iron ore sintering is an important process capable of absorbing and treating various types of industrial solid waste, and there has been a great deal of research pointing to the effective (PDF) Comprehensive Technologies for Iron Ore Sintering with a
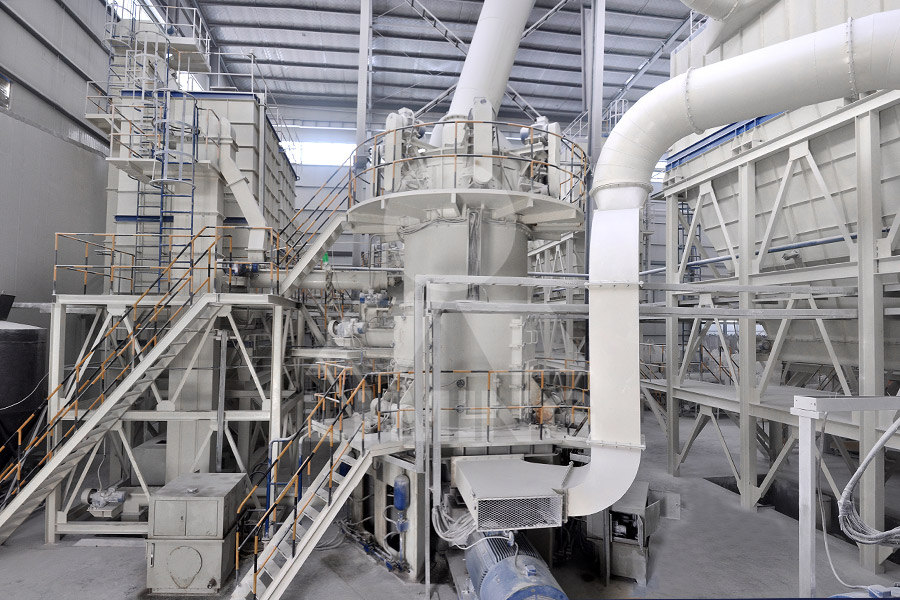
Lesson Explainer: Extracting Iron Nagwa
In this explainer, we will learn how to describe the extraction of iron from its ore in the blast furnace Sign Up; Sign In; English The mixture of iron ore, coke, and limestone is known as charge This charge travels on conveyor belts to the top of the blast furnace2022年7月15日 For wet granulation of iron ore powders, for the first time, the use of agitation torque has been proposed in our previous study 23) Our previous study demonstrated that the optimum water Determining Optimum Water Content for Iron Ore Blending ratio of sinter mixture used in the experiments Material Iron ore Coke Return Sinter Limestone Dolomite Quick lime Mill scale Flue dust GCP dust Mass (%) 5525 5 24 625 5 15 1 1 1 Fig 2 Schematic diagram of sinter pot (Online version in color)Effect of Oxygen Enrichment on Top Layer Sinter Properties J 2016年10月28日 dusts and mill scale, Eisele and Kawatra, 2003), Granulation consists of the homogenization of iron ore mixture in a rotation drum with 78% water for a few minutes with the finalityIron Ore Sintering: Raw Materials and Granulation
.jpg)
A Case Study of Sintering with Low Silica Iron Ore
The reference ratio of blended ore is 8% A, 13% B, 15% C, 6% D, 12% E, 37% F, and 9% G In order to obtain a suitable SiO 2 content, the proportion of E ore in blended ore was reduced and the proportion of other iron ores in blended ore was fixed In other words, the proportion of other ores increases proportionally2022年7月15日 Carbon monoxide is the major hazardous component in flue gas exhausting from the iron ore sintering This study aims to reduce the CO emission by changing the sinter parameters by sintering pot (PDF) Influence of Sinter Parameters on CO Emission in Iron Ore 2023年3月23日 Hydrogenbased direct reduced iron (H2DRI) is an alternative pathway for lowcarbon steel production Yet, the lack of established process and business models defining “green steel” make it Green steel: design and cost analysis of hydrogenbased direct iron 2022年11月25日 Enhancing the Dewaterability of Oily Cold Rolling Mill Sludge Using Quicklime as a Conditioning Agent November 2022; ACS Omega 7 as well as iron ore was 2:1, and the mixture was stirred Enhancing the Dewaterability of Oily Cold Rolling Mill Sludge
.jpg)
123: Metals and Ores Chemistry LibreTexts
Iron ore is reduced with coke in a blast furnace (Figure \(\PageIndex{1}\)) The blast furnace is loaded with iron ores, usually hematite Fe 2 O 3 or magnetite Fe 3 O 4, together with coke (coal that has been separately baked to remove volatile components) Air preheated to 900 °C is blown through the mixture, in sufficient amount to turn the 2023年8月1日 The iron and steel metallurgy industry faces the question of how to replace carbon in iron ore reduction to reduce CO 2 emission in basic industries and achieve the expectation of "double carbon" This study investigates the reduction swelling of individual iron ore pellet under mixed H 2CO atmospheres and at temperatures of 800–1000 ℃ by insitu Direct reduction of iron ore pellets by H2CO mixture: An insitu 2022年12月31日 The raw materials used are five kinds of iron ores and quicklime Table 1 shows different iron ores’ size distribution and bulk density (Zhou et al, 2020a) The five iron ores used in this study came from Australia and Brazil and had a wide size distribution ranging from 0 to 10 mm Table 2 showsExperimental study on melt and flow characteristics and pore