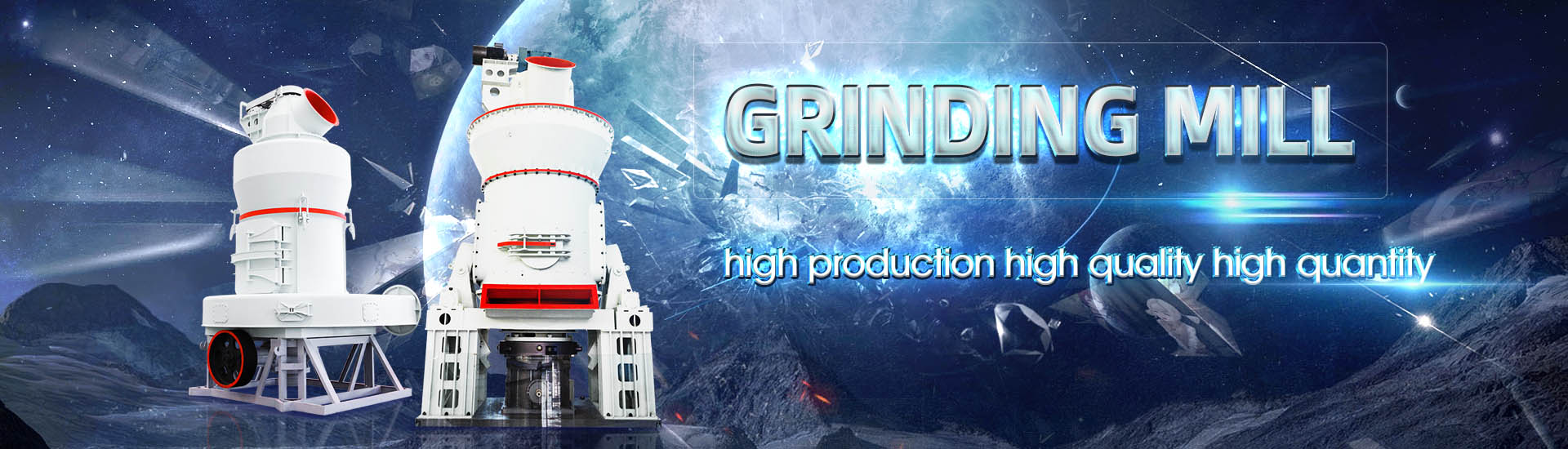
Air swept coal mill central control operator
.jpg)
ATOX COAL MILL
refinement of the ATOX coal mill over the years, today’s leading airswept vertical roller mill is the compact ATOX Offering high reliability, low installation costs and a wide range of sizes, the The airswept coal mill is a critical component in coalfired power plants and industrial furnaces It grinds the coal into a fine powder, facilitating efficient combustion and heat generation With its highspeed airflow and multiple Air Swept Coal Mill Cement Plant Equipment Coal Most commonly used mills for coal grinding in cement plants are closed circuit air swept (Single chamber) ball mills and vertical mills Ball Mill: Single chamber ball mills (with classifying liners Coal Grinding Cement Plant OptimizationBradley Airswept Mills combine the fine grinding action of a pendulum roller mill with air stream classifying and fluid bed drying capabilities to produce precisely sizedAIRSWEPT PENDULUM MILL SYSTEM Bradley Pulverizer
.jpg)
Air swept coal mill Geckointech
Air swept coal mill, or air swept pulverizer, is major grinding equipment for pulverized coal production in power plant, cement plant Hot air stream (heated by air preheater) from primary air fan could take away pulverized coal when Integrated Fan: Facilitates airflow through the mill and collector, enabling efficient product conveying Control Panel: Offers sequential starting and stopping for the milling process Why Rieco? in your process challenges Rieco's air swept Air Swept Mills Rieco2012年5月1日 The paper presents development and validation of a coal mill model to be used for improved mill control, which may lead to a better load following capability of power plants Derivation and validation of a coal mill model for control2009年6月25日 The primary air (PA) flow to the mill is controlled by the hot and cold air dampers operating in parallel In this study, it is envisaged that accurate knowledge of temperatures and Steady state inferential modeling of temperature and pressure in
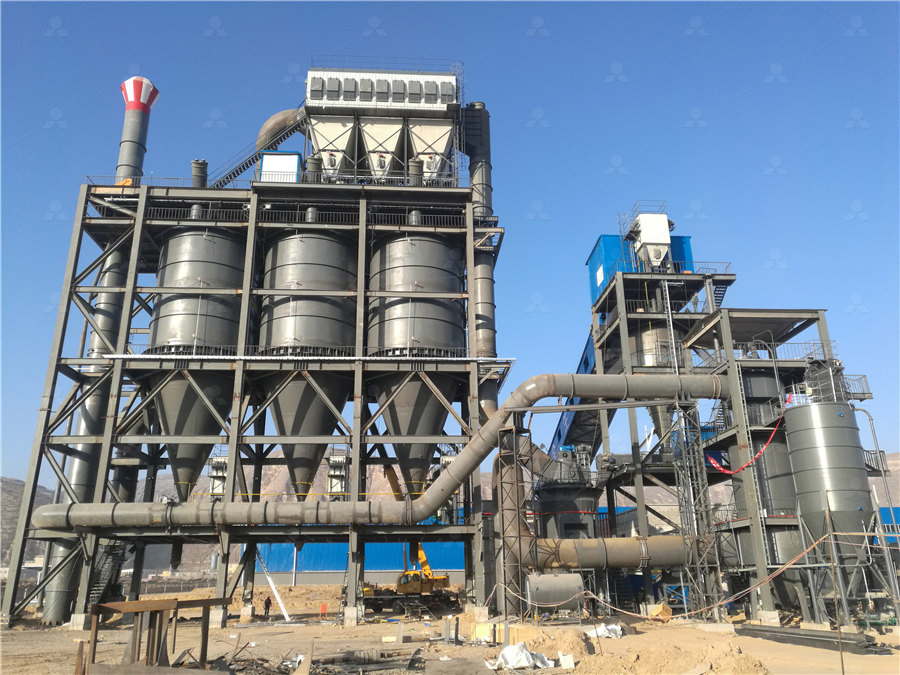
Modelling of vertical spindle mills Part 2: Integrated models for E
2015年3月1日 The pulveriser is airswept in which the coal is fed onto a rotating table through a central pipe The coal is thrown outward by rotation into the grinding race Seated in the race As we have eight numbers (08) of coal mill and each coal mill has four outlet coal pipes, so we have to measure 32 numbers of coal pipe temperature We design and procure 32 numbers of special type surface mounted RTD Fixed the RTD on each and every coal pipe before entering at the burner area 32 numbers of RTD signals are connected to a Measurement and Control of Coal Pipe Temperature of Coal Mills 3 What is the structure of the airswept coal mill? The airswept coal mill is mainly composed of a feeding device, main bearing, rotating part, transmission device, discharge device, highpressure starting device, and lubrication system 31 AirSwept Coal Mill of High Quality Fote MachineryThe air swept coal mill is a coal grinder usually used in the cement production line MFB series air swept coal mills with different capacities and dimensions can be customized by AGICO group Skip to content Blog Contact About Cases Air Swept Coal Mill Coal Mill In Cement Plant
.jpg)
Measurement and Control of Coal Pipe Temperature of Coal Mills
As we have eight numbers (08) of coal mill and each coal mill has four outlet coal pipes, so we have to measure 32 numbers of coal pipe temperature We design and procure 32 numbers of special type surface mounted RTD Fixed the RTD on each and every coal pipe before entering at the burner area 32 numbers of RTD signals are connected to a Material circulation inside the mill FSmidth Cement flsmidthcement 3 ATOX coal mill Proven technology Today the airswept vertical roller mill is the standard solution for coal grinding installations And thanks to our continuous refinement of the ATOX coal mill over the years, today’s leading airswept vertical roller mill is the ATOX COAL MILLIn process terms, the material is swept from the mill Static Grit separators are commonly employed on semi air swept finish mills and on air swept coal mills Some large raw grinding vertical roller mills use them Alpena’s roll press raw grinding circuit uses them as AIR SEPARATORS INFINITY FOR CEMENT EQUIPMENTCONTROL OF COAL MILL In general the control systems, of mills have two components: coal air mixture temperature control and the coal feeder control Control scheme for outlet temperature is essential since improper control may lead to chances of explosion In the thermal power plant, the outlet temperature is maintained at 70 C (PDF) Modeling and Control of Coal Mill Academia
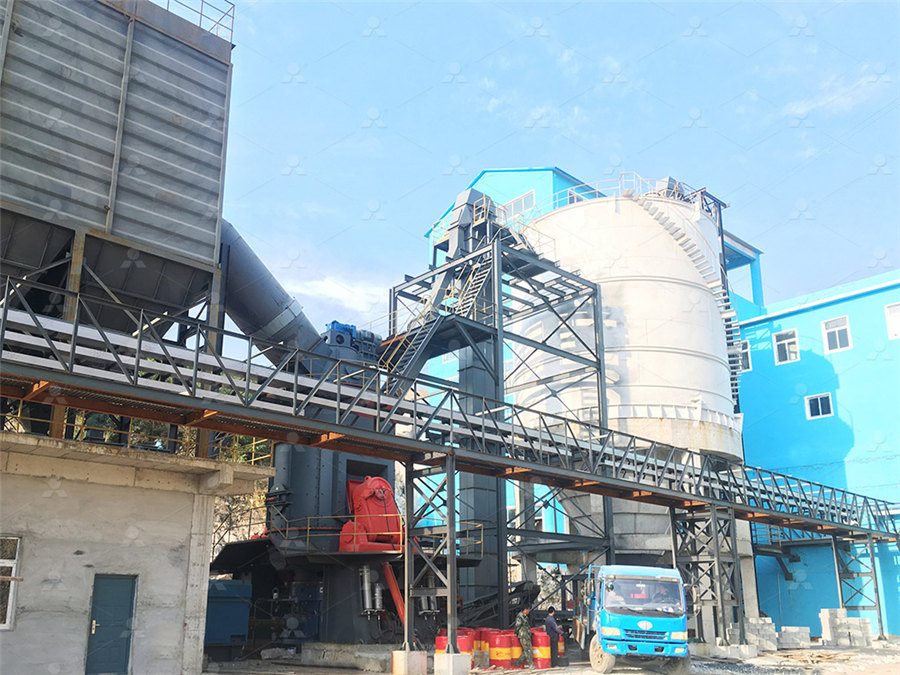
WorldProven Coal Pulverizer Technology Debuts in the US
each gravimetric belt feeder, seal air fan, 1800 rpm primary air fan, and four mill outlets supplying pulverized coal to one of the three horizontal rows of (4) dualfuel burners When operating at boiler MCR, each mill had a coal throughput of approximately 53,000 #ffir Specified product fineness was 70% thru 200 mesh and 98% thru 50 meshCoal Mills are used to pulverize and dry to coal before it is blown into the power plant furnace Operation The coal is feed into the coal mill through a central inlet pipe where gravity is used to lead the coal to the bottom of the mill, where the grinding table and some heavy rollers pulverizes the coal to particlesCoal Mills SolidsWiki2024年3月16日 A vertical coal mill is a type of industrial milling equipment used to crush and grind coal into powder for use in thermal power plants and the cement Air Swept Coal Mill ; Batch Ball Mill ; Cement Ball Mills ; Cement Raw Mill; Ceramic Ball coal fed through a central chute is crushed between the rollers and the grinding table How Does a Vertical Coal Mill WorkFine grinding in an airswept ball mill working in closed circuit with a forced vortex air classifier has been investigated first in continuous laboratory and then in industrial scale Results from the laboratory circuit have shown significant influence of mill load (powder filling) on the capacity of the circuit In laboratory scale the mill load was measured and controlled by a weighing Measurement and Control of the Mill Load in an AirSwept Ball
.jpg)
Coal Mills SolidsWiki
Coal Mills are used to pulverize and dry to coal before it is blown into the power plant furnace Operation The coal is feed into the coal mill through a central inlet pipe where gravity is used to lead the coal to the bottom of the mill, where the grinding table and some heavy rollers pulverizes the coal to particles2012年5月1日 Coal fired power plants are heavily used due to large and long lasting coal resources compared with oil or natural gas An important bottleneck in the operation of this particular kind of plants, however, is the coal pulverization process, which gives rise to slow takeup rates and frequent plant shutdowns (Rees Fan, 2003)In typical coal fired power plants, Derivation and validation of a coal mill model for controlAirswept coal mill is the main equipment of cement plant, also called coal mill in cement plant, used for grinding and drying various hardness of coal, crushing the coal briquette into pulverized coalIt is the important auxiliary equipment of pulverized coal furnace The airswept coal mill runs reliably, can work continuously, also has a large production capacity and less energy Coal Mill In Cement Plant, Airswept Coal Mill Coal MillThe pulverized coal is taken out of the mill by hot air Advantages Compared with the vertical roller mill, the advantages of airswept ball mill are strong adaptability to raw coal quality, simple operation and low investment cost; the disadvantages are high power consumption and high noise Vertical Roller Mill Vertical Roller Coal MillCoal Mill in Cement Plant Vertical Roller Mill AirSwept Ball Mill

Air Swept Mills Rieco
Rieco's Air Swept Mill (ASM) offer an efficient screenless solution for the fine pulverizing of soft to mediumhard materials The unique feature of this system is the adjustable wizards that control product fineness: move them towards the hammers for 2005年2月1日 Request PDF Modeling and simulation of a fully air swept ball mill in a raw material grinding circuit A raw material grinding circuit was modeled using plant data Samples were collected from Modeling and simulation of a fully air swept ball mill in a raw 2017年5月25日 In an airswept mill, the body of which does not differ significantly in general design from a trunnion overflow mill, a powerful stream of air is passed 911 Metallurgist is a trusted resource for practical insights, solutions, and support in mineral processing engineering, helping industry professionals succeed with proven expertise Air Swept MillAir Swept Mill 911MetallurgistAn air swept ball mill also called air swept coal mill is a type of coal mill commonly used in industrial grinding systems for pulverizing coal and other materials This mill uses the flow of air to carry the pulverized coal upward from the grinding zone to the classifier HOME;Air Swept Coal Mill ManufacturerSupplier Tongli Machinery
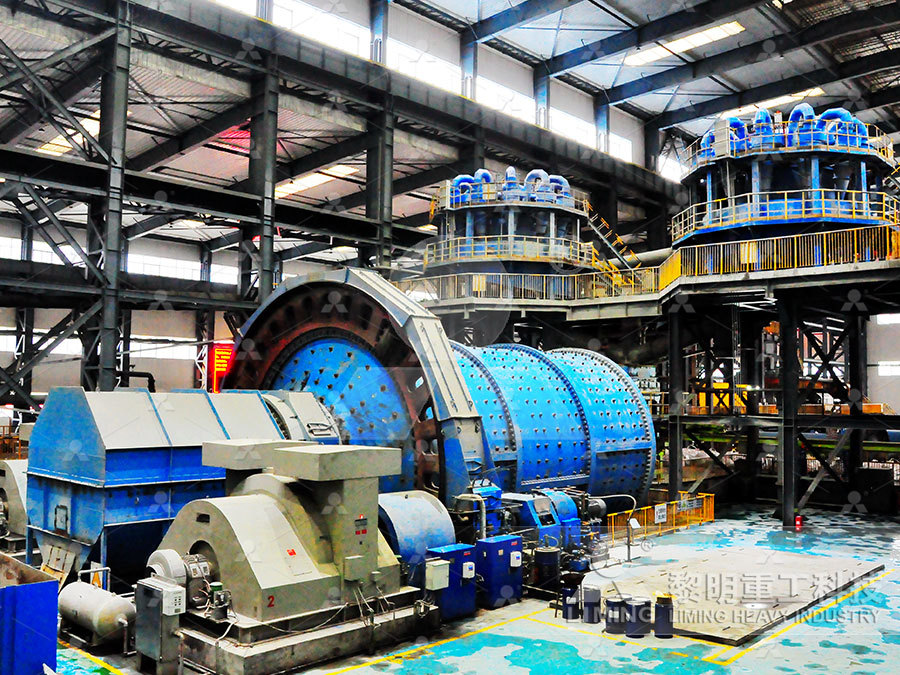
Coal Plant Control Room Operator jobs Indeed
45 Coal Plant Control Room Operator jobs available on Indeed Apply to Plant Operator, Control Room Operator, Senior Production Specialist and more! Skip to main Operate Limestone Mill Air pressure Vent Valve; Monitor for Oil Pump Vibration; Operate BFPT Warm Locate/Operate Manual Sweep Air to Coal Feed Chutes from Fluidizing Air 520 P Niemczyk et al / Control Engineering Practice 20 (2012) 519–530 Nomenclature Dpmill mc mpc mcair mass of unground coal on the table (kg) mass of pulverized coal on the table (kg) mass of pulverized coal carried by Derivation and validation of a coal mill model for Cold Air Locking at Mill Inlet: This is very important for coal mill, as ambient air throttling the drying capacity of mill as well as increases the oxygen content of kiln gases making it riskier Oxygen percentage of more than 1214% is considered catalyst for fire/explosion riskCoal Grinding Cement Plant Optimization520 P Niemczyk et al / Control Engineering Practice 20 (2012) 519–530 Nomenclature Dpmill mc mpc mcair mass of unground coal on the table (kg) mass of pulverized coal on the table (kg) mass of pulverized coal carried by Derivation and validation of a coal mill model for
.jpg)
Steady state inferential modeling of temperature and pressure in an air
2009年6月25日 The plant under study consists of six boilers with five ball mills per boiler, capable of producing a total power output of 3430MW The mill specifications and operational parameters are presented in a caption in Fig 1In each milling circuit, hot and cold air streams are mixed prior to entering the mill to achieve the desired temperature of the mill productAnalysis of Coal Mill Operation Free download as PDF File (pdf), Text File (txt) or read online for free This document analyzes the comilling of coal and wood biomass in a ringball mill It describes tests conducted pulverizing hard coal with additions of 8% and 16% pine sawdust at different moisture contents Key findings include: 1) Biomass has weaker grinding properties Analysis of Coal Mill Operation PDF Mill (Grinding) Scribd3 A 62 m x 20 m mill shell on its way from France to Malaysia With an extensive range of grinding systems, consisting of x tube mills, x rod mills, x autogenous and semiautogenous mills, x AEROFALL mills, x roller mills and x POLYCOM® highpressure grinding rolls including x separators, x cement coolers, x dryers and x expert systems for automatic process control, Tube mills for dry grinding PolysiusMIKRO ACM® AIR CLASSIFYING MILL The Mikro ACM® Air Classifying Mill is an air swept mechanical impact mill with a dynamic air classifier designed to grind an extensive range of materials down to a D97 of 20 microns The Mikro ACM® Air Classifying Mill is available in a range of sizes and can be supplied for laboratory use or large Air Classifying Mill
.jpg)
Instrumentation and control in coalfired power plant ICSC
OPC OLE for process control OT operator terminals PA primary air PLC programmable logic control(ler) pc pulverised coal Instrumentation and control in coalfired power plant 3 Contents 1 Introduction 5 2 Tasks of instrumentation and control 71 Mill control 43 72 Fan control 44 73 Feedwater control 45 74 Valve control 46MPS MILL The MPS mill is classified as an airswept, pressurized, vertical spindle, table/roller mill It contains an integral classifier, a grinding section, a windbox (plenum), and auxiliary components (Figure 1) Frequency converted electric drive Turret Louvre Return hopper Pendulum joints Housing Hot air inlet duct Grinding track carrier MotorCoal Pulverizer Design Upgrades to Meet the Demands of Low Optimization of a Fully Airswept Dry Grinding Cement Raw Meal Ball Mill Closed Circuit Capacity With the Aid Free download as PDF File (pdf), Text File (txt) or read online for free This document discusses optimizing the production capacity of a fully airswept industrial scale twocompartment cement ball mill through simulation The mill has two compartments, with the first Optimization of A Fully AirSwept Dry Grinding Cement Raw Meal As we have eight numbers (08) of coal mill and each coal mill has four outlet coal pipes, so we have to measure 32 numbers of coal pipe temperature We design and procure 32 numbers of special type surface mounted RTD Fixed the RTD on each and every coal pipe before entering at the burner area 32 numbers of RTD signals are connected to a Measurement and Control of Coal Pipe Temperature of Coal Mills
.jpg)
AirSwept Coal Mill of High Quality Fote Machinery
3 What is the structure of the airswept coal mill? The airswept coal mill is mainly composed of a feeding device, main bearing, rotating part, transmission device, discharge device, highpressure starting device, and lubrication system 31 The air swept coal mill is a coal grinder usually used in the cement production line MFB series air swept coal mills with different capacities and dimensions can be customized by AGICO group Skip to content Blog Contact About Cases Air Swept Coal Mill Coal Mill In Cement PlantAs we have eight numbers (08) of coal mill and each coal mill has four outlet coal pipes, so we have to measure 32 numbers of coal pipe temperature We design and procure 32 numbers of special type surface mounted RTD Fixed the RTD on each and every coal pipe before entering at the burner area 32 numbers of RTD signals are connected to a Measurement and Control of Coal Pipe Temperature of Coal Mills Material circulation inside the mill FSmidth Cement flsmidthcement 3 ATOX coal mill Proven technology Today the airswept vertical roller mill is the standard solution for coal grinding installations And thanks to our continuous refinement of the ATOX coal mill over the years, today’s leading airswept vertical roller mill is the ATOX COAL MILL
.jpg)
AIR SEPARATORS INFINITY FOR CEMENT EQUIPMENT
In process terms, the material is swept from the mill Static Grit separators are commonly employed on semi air swept finish mills and on air swept coal mills Some large raw grinding vertical roller mills use them Alpena’s roll press raw grinding circuit uses them as CONTROL OF COAL MILL In general the control systems, of mills have two components: coal air mixture temperature control and the coal feeder control Control scheme for outlet temperature is essential since improper control may lead to chances of explosion In the thermal power plant, the outlet temperature is maintained at 70 C (PDF) Modeling and Control of Coal Mill Academiaeach gravimetric belt feeder, seal air fan, 1800 rpm primary air fan, and four mill outlets supplying pulverized coal to one of the three horizontal rows of (4) dualfuel burners When operating at boiler MCR, each mill had a coal throughput of approximately 53,000 #ffir Specified product fineness was 70% thru 200 mesh and 98% thru 50 meshWorldProven Coal Pulverizer Technology Debuts in the USCoal Mills are used to pulverize and dry to coal before it is blown into the power plant furnace Operation The coal is feed into the coal mill through a central inlet pipe where gravity is used to lead the coal to the bottom of the mill, where the grinding table and some heavy rollers pulverizes the coal to particlesCoal Mills SolidsWiki
.jpg)
How Does a Vertical Coal Mill Work
2024年3月16日 A vertical coal mill is a type of industrial milling equipment used to crush and grind coal into powder for use in thermal power plants and the cement Air Swept Coal Mill ; Batch Ball Mill ; Cement Ball Mills ; Cement Raw Mill; Ceramic Ball coal fed through a central chute is crushed between the rollers and the grinding table