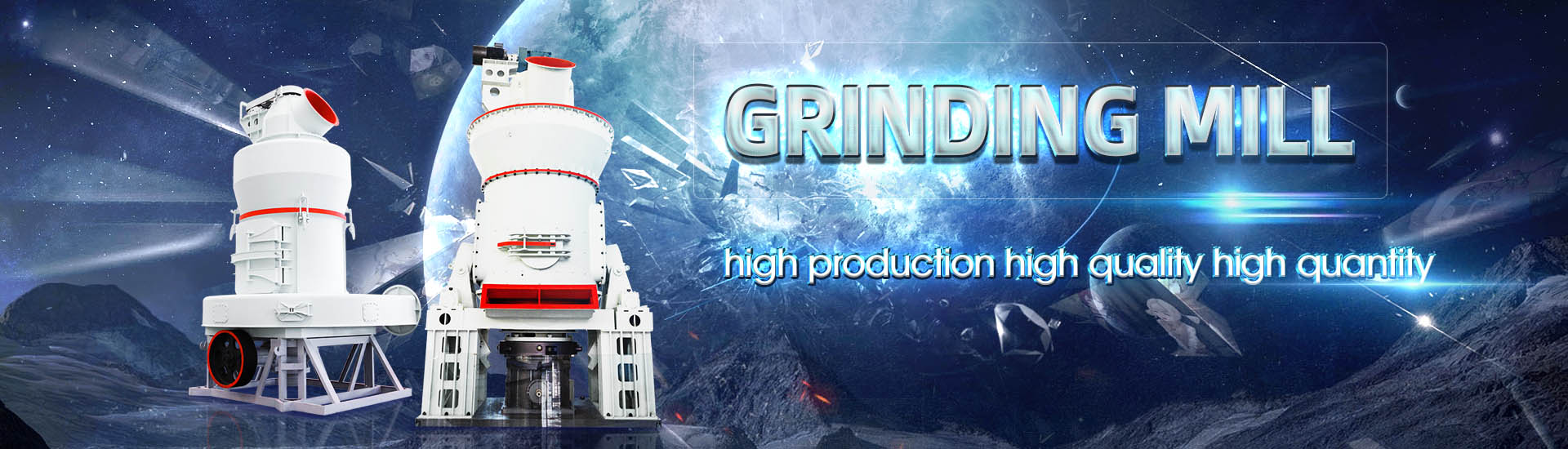
Cement production cement grinding
.jpg)
The Cement Plant Operations Handbook International Cement
The Cement Plant Operations Handbook – Seventh Edition 6 Cement milling Finish milling is the grinding together of clinker with some 35 per cent gypsum, natural or synthetic, for set control, What are the steps involved in manufacturing cement? Cement production involves several key steps, including: Crushing the raw materials Homogenizing the mixture Proportioning the raw materials accurately Grinding the materials StepbyStep Guide to the Manufacturing of CementSome manufacturers grind the raw materials dry, while others use a wetgrinding process involving water Cement manufacturers quarry raw materials including limestone, clay, and sandHow Cement is Made Portland Cement AssociationHighly energy intensive unit operation of size reduction in cement industry is intended to provide a homogeneous and super fine (30004000 Blain) cement Grinding operation is monitored for Cement Grinding Cement Plant Optimization
.jpg)
Grinding in Cement Manufacturing: Key Process, Types of Mills,
Grinding plays a pivotal role in the cement manufacturing process, transforming raw materials into a fine powder suitable for creating cement It’s a crucial step that directly impacts the physical 2015年12月1日 While vertical roller mills (VRMs) are predominantly used for raw material grinding, different types of grinding systems are used for the finish grinding of cement VRMs Process technology for efficient and sustainable cement Grinding with propylene glycol generates approximately 800 Cm 2 /gram cement more surface than grinding without an aid, given the same energy consumption the most popular grinding CEMENT GRINDING SYSTEMS INFINITY FOR CEMENT EQUIPMENT2004年11月1日 There is potential to optimise conventional cement clinker grinding circuits and in the last decade significant progress has been achieved The increasing demand for “finer Cement grinding optimisation ScienceDirect
.jpg)
Cement Grinding Cement Plant Optimization
Grinding Operation Objectives and KPIs Chemical analysis of cement, generally on hourly basis Product fineness, Blain surface and 45micron residue Cement SO3, % Grinding aid usage, grams/tonne Cement moisture, % Production rate, tonnes/hour Operating hours as run factor in % Specific power consumption (SPC) kWh/tonne2019年10月11日 As we all know, the cement production can generally be divided into three processes: raw material preparation, clinker production and finished cement production The cement grinding plant is a vital link of the Cement Grinding Plant Overview Cement Grinding 2023年10月23日 Cement production requires significant energy, and entails high costs and CO2 emissions This is because the clinker requires very fine grindingA study of different grinding aids for lowenergy 2016年10月5日 In this chapter an introduction of widely applied energyefficient grinding technologies in cement grinding and description of the operating principles of the related equip‐ ments and comparisons over each other in terms of grinding efficiency, specific energy consumption, production capacity and cement quality are given A case study per‐ formed on a EnergyEfficient Technologies in Cement Grinding
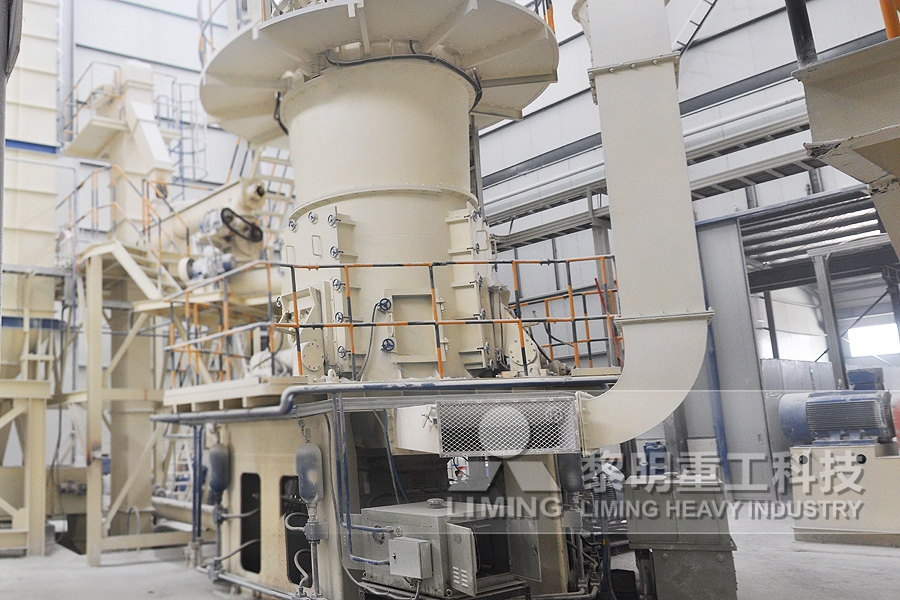
The Cement Plant Operations Handbook International Cement
cement production –10 Regional cement consumption data –11 EU Environmental legislation –12 Ship and truck capacities –13 Cement milling Finish milling is the grinding together of clinker with some 35 per cent gypsum, natural or synthetic, for set control, 300 t/d Cement Production Line 300t/d cement production line designed by Great Wall machinery, fully learns from the lessons and experiences of more than 20 years of NSP production line design, advanced vertical roller mill grinding system and DCS automatic control system; 3000 t/d Cement Production Line Xinxiang Great Wall Machinery provides turnkey basis service Cement Production LineCement Production Seminar: Grinding Understand the fundamentals and gain insights on how to improve the performance and productivity, efficiency, and product quality of your grinding systems This 3day seminar covers ball and vertical mills with a focus oncomminution theory, design basis, operational principles, control and regulation, process troubleshooting, Cement Production Seminar: GrindingCement production involves quarrying limestone and clay, grinding and blending the materials, burning them at high temperatures to form clinker, and finely grinding the clinker to produce cement powder The key steps are: 1) Quarrying limestone and clay and grinding them to powder; 2) Blending the powders in precise proportions; 3) Burning the blend at high heat to form Chapter 1 Introduction To Cement Production PDF Mill (Grinding
.jpg)
Global database of cement production assets and upstream
2023年10月13日 These variables are instrumental in modeling cement production utilization rates, (integrated or grinding), production type (wet or dry), plant capacity and year production first startedAGICO dry process cement production line comprehensively adopts the IT technology, multifunction grinding system, newtype wearresisting and heatresisting materials, mechanical powder conveying device, and some other modern technologies to realize quality cement production It has the characteristic of energy saving, high efficiency, environmental protection, Cement Production Line Cement Manufacturing Plant AGICO Cement 2024年1月17日 According to statistics, the dry cement production line grinding operation consumes Power accounts for more than 60% of the power of the whole plant, of which raw material grinding accounts for more than 30%, coal What Do You Know About Wet Process Of Cement The name Portland was given by the inventor as it resembles a stone quarried on the Isle of Portland The first use of modern day Portland cement was in the tunnel construction in the Thames River in 1828 Manufacture Process of Manufacture of Cement Materials and Manufacturing

A Comprehensive Guide to the Cement Manufacturing
2024年9月5日 This makes it an essential component in building structures like houses, bridges, and roads The cement generally adopted and used widely for building is known as Portland cement The name is so derived because the Cement grinding process mainly includes the mixed materials crushing, material batching, pregrinding, fine grinding, powder classification, dust collecting, automatic control, and other technologies, making cement production high yield and high quality, in line with the requirements of energysaving and emission reductionCement Grinding Unit Clinker Grinder AGICO Cement2016年10月5日 1 Introduction Cement is an energyintensive industry in which the grinding circuits use more than 60 % of the total electrical energy consumed and account for most of the manufacturing cost []The requirements for the cement industry in the future are to reduce the use of energy in grinding and the emission of CO 2 from the kilns In recent years, the production EnergyEfficient Technologies in Cement Grinding IntechOpen2023年8月21日 Tushar Khandhadia, General Manager – Production, Udaipur Cement Works, discusses the role of grinding in ensuring optimised cement production and a high quality end product How does the grinding process contribute to the production of highquality cement?The quality of cement depends on its reactive properties and particle size grinding helps to reduce Grinding process is a critical stage in cement production
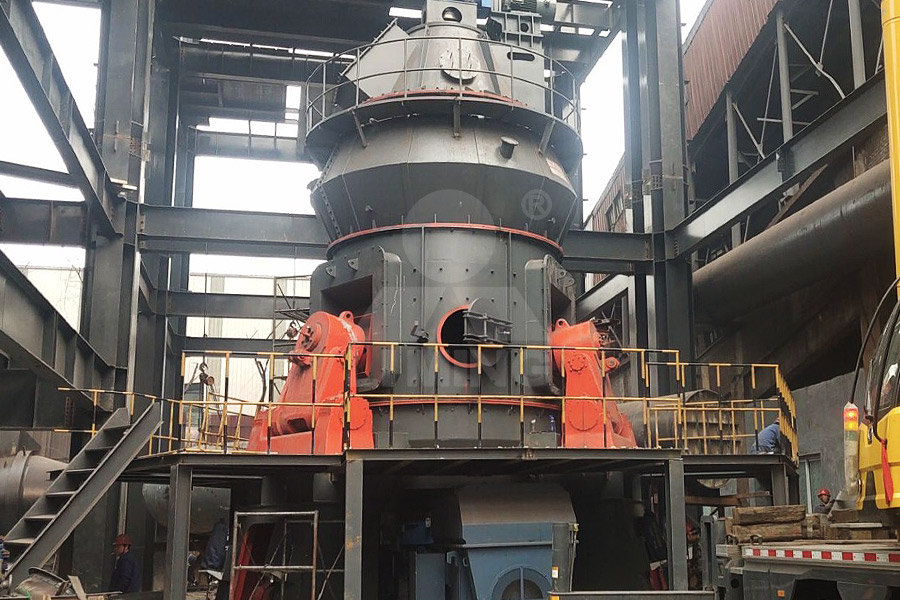
World Cement Grinding Milling QA
2022年2月18日 Sustainability is one of the most important challenges facing cement production, which is responsible for 8% of global carbon emissions – the dependence on fossil fuels must be reduced Depending on the specific customer needs, the cement grinding plant installation comprising a highpressure grinding roll polycom Uses of alternative fuels and raw materials in the cement industry as sustainable waste management options Alfonso Aranda UsónAna M LópezSabirónGermán FerreiraEva Llera Sastresa, in Renewable and Sustainable Energy Reviews, 2013 21 Worldwide production One of the wellknown characteristics of cement production is that cement plants are not uniformly Cement Production an overview ScienceDirect Topics2021年4月19日 Estimating resistance to grinding of cement blends from the mixture’s composition would aid in developing optimization models to reduce energy consumption for cement production However, most studies either focus on determining the overall grindability of the blends or optimizing material composition considering only the final properties of the productResistance to Grinding and Cement Paste Performance of Blends The production of finished cement, on the opposite, must closely follow seasonal and shortterm fluctuations in the delivery of cement from the plants: the storage of the finished cement is expensive, in capital costs and the cement storage life is to a limited extent; in fact, the stocks of finished cement available at any time are rarely more than a week of productionAn Introduction to Clinker Grinding and Cement Storage
.jpg)
Cement TanzaniaInvest
2023年7月24日 Today’s cement industry in Tanzania includes six integrated plants and several grinding facilities with a production capacity of around 11 million tons Tanzania’s cement exports in 2022 increased to 632,726 tons, up 2023年12月20日 Cement manufacturing is a complex process that begins with mining and then grinding raw materials that include limestone and clay, to a fine powder, called raw meal, which is then heated to a sintering temperature as The Cement Manufacturing Process Thermo Fisher 2015年2月9日 It began production in 2010 Today, the Fujairah cement plant has two kilns (both Polysius) and three cement grinding mills: Kiln 1: 4600t/day; Kiln 2: 7500t/day; 3x cement ball mills: 3x100t/hr Fujairah Cement's clinker production capacity is currently estimated at 40Mt/yr, while its cement grinding capacity is around 23Mt/yrThe growing cement industry of the UAE2023年12月26日 As we all know, the dryprocess cement production line is commonly used in the cement industry The new type of dryprocess cement production process includes four main sections: Prehomogenization of raw materials, homogenization of raw materials, clinker firing, cement grinding, etc Raw material conveying system The raw material, including limestone, 6 Cement Equipment For Dryprocess Cement Production Line
.jpg)
OPTIMIZATION OF CEMENT GRINDING OPERATION IN BALL MILLS
consumption and low production The consumption of energy by the cement grinding operation amounts to one third of the total electrical energy used for the production of cement The optimization of this process would yield substantial benefits in terms of energy savings and capacity increase Optimization of the Cement Ball Mill Operation2022年8月15日 Cement Grinding Technology in Cement Production Process English VersionIn this session I will explain about Cement Grinding Technology for cement productioCement Grinding Technology In Cement Production Process The cement grinding process accounts for approx 40% if this energy consumption PRODUCTION – CEMENT TYPES Elements essential for the process are: ¨ Portland cement 2’500 – 6’000 [cm2/g1 ¨ Portland cement with minor additive £ 5 [%] 2’500 – 6’000 [cm2/g ¨ Composite cement CEMENT GRINDING SYSTEMS INFINITY FOR CEMENT EQUIPMENTCement Grinding Menu Toggle Hydraulic Roller Press; High Pressure Grinding Roll; Cement Mill; Vertical Roller Mill; Cement Mill Separator; Steel Balls for Ball Mill; The cement plant designed and built according to the new dry process cement production technology has features of highquality, highyield, energysaving, environmental Cement Plant for Sale Cement Plant Equipment Design AGICO Cement
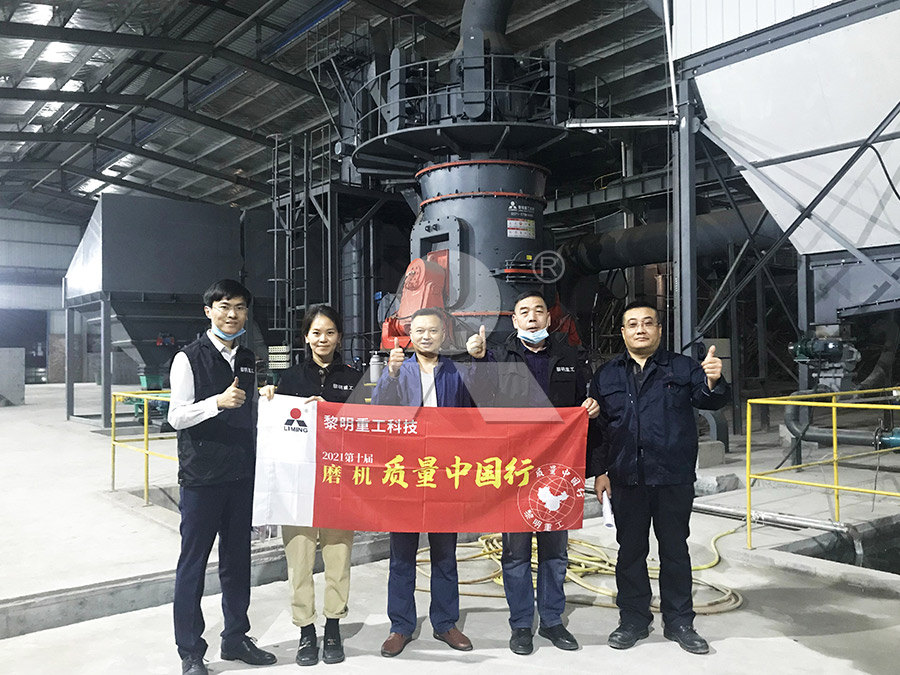
Development Trend Analysis of Cement Production Line
2023年11月21日 Efficient and energysaving new grinding equipment such as vertical cement mills and cement roller presses will become more popular to reduce energy consumption in the grinding process and improve energy efficiency in cement production During the grinding process, imported and exported particle size analysis instruments will be more common to 6 Cement Production Technology –Cement Grinding –Mechanical Design and Function of Separator Separators –General Classification of Separating Principles •according to flow direction relative to particle track •according to kind of separating field separation by gravitational forceCement Grinding myPolysiusServiceGrinding Operation Objectives and KPIs Chemical analysis of cement, generally on hourly basis Product fineness, Blain surface and 45micron residue Cement SO3, % Grinding aid usage, grams/tonne Cement moisture, % Production rate, tonnes/hour Operating hours as run factor in % Specific power consumption (SPC) kWh/tonneCement Grinding Cement Plant Optimization2019年10月11日 As we all know, the cement production can generally be divided into three processes: raw material preparation, clinker production and finished cement production The cement grinding plant is a vital link of the Cement Grinding Plant Overview Cement Grinding
.jpg)
A study of different grinding aids for lowenergy
2023年10月23日 Cement production requires significant energy, and entails high costs and CO2 emissions This is because the clinker requires very fine grinding2016年10月5日 In this chapter an introduction of widely applied energyefficient grinding technologies in cement grinding and description of the operating principles of the related equip‐ ments and comparisons over each other in terms of grinding efficiency, specific energy consumption, production capacity and cement quality are given A case study per‐ formed on a EnergyEfficient Technologies in Cement Grindingcement production –10 Regional cement consumption data –11 EU Environmental legislation –12 Ship and truck capacities –13 Cement milling Finish milling is the grinding together of clinker with some 35 per cent gypsum, natural or synthetic, for set control, The Cement Plant Operations Handbook International Cement 300 t/d Cement Production Line 300t/d cement production line designed by Great Wall machinery, fully learns from the lessons and experiences of more than 20 years of NSP production line design, advanced vertical roller mill grinding system and DCS automatic control system; 3000 t/d Cement Production Line Xinxiang Great Wall Machinery provides turnkey basis service Cement Production Line
.jpg)
Cement Production Seminar: Grinding
Cement Production Seminar: Grinding Understand the fundamentals and gain insights on how to improve the performance and productivity, efficiency, and product quality of your grinding systems This 3day seminar covers ball and vertical mills with a focus oncomminution theory, design basis, operational principles, control and regulation, process troubleshooting, Cement production involves quarrying limestone and clay, grinding and blending the materials, burning them at high temperatures to form clinker, and finely grinding the clinker to produce cement powder The key steps are: 1) Quarrying limestone and clay and grinding them to powder; 2) Blending the powders in precise proportions; 3) Burning the blend at high heat to form Chapter 1 Introduction To Cement Production PDF Mill (Grinding 2023年10月13日 These variables are instrumental in modeling cement production utilization rates, (integrated or grinding), production type (wet or dry), plant capacity and year production first startedGlobal database of cement production assets and upstream AGICO dry process cement production line comprehensively adopts the IT technology, multifunction grinding system, newtype wearresisting and heatresisting materials, mechanical powder conveying device, and some other modern technologies to realize quality cement production It has the characteristic of energy saving, high efficiency, environmental protection, Cement Production Line Cement Manufacturing Plant AGICO Cement