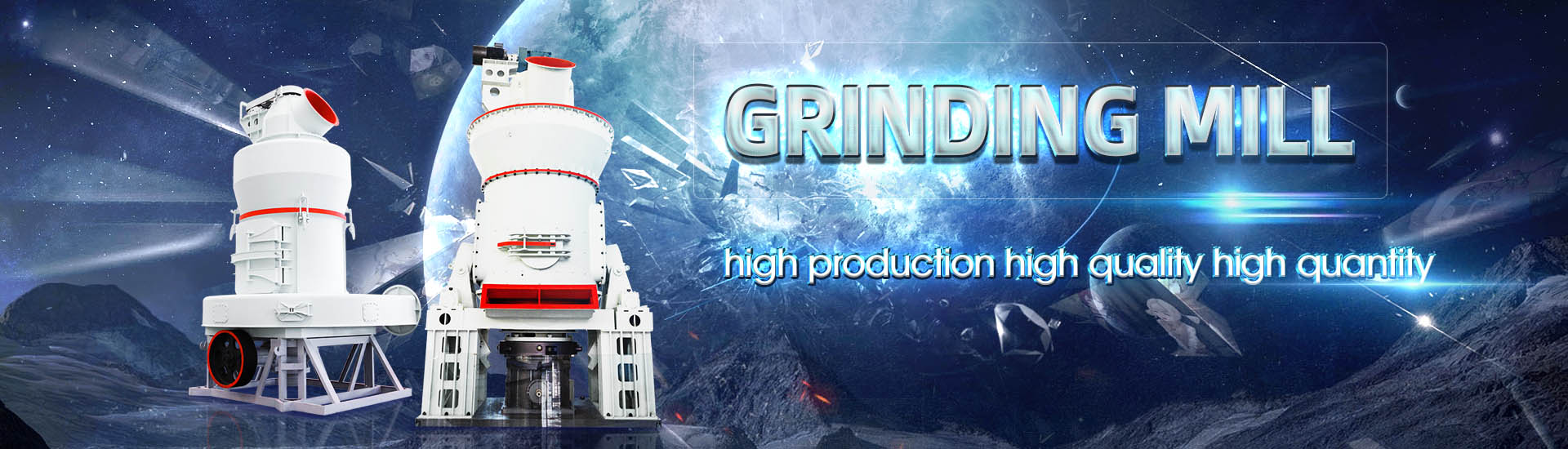
Wuan Guzhen grinding calcite ore magnetic ore powder processing plant
.jpg)
Application of premagnetic separation to address grinding
Adding a premagnetic separation process to the ore beneficiation process separates magnetic and nonmagnetic minerals with significant differences in performance before grinding, 2015年1月1日 In this section, several cases of magnetic techniques for the treatment of typically magnetic ores are introduced, and they are magnetite, hematite, ilmenite, limonite, and Magnetic Techniques for Mineral Processing ScienceDirectEffective role of grinding aids in the dry grinding performance of calcite Powder Technology 2023, 426 , https://doi/101016/jpowtec2023 Vitalis Chipakwe, Christopher Chemical Grinding Aids for Increasing Throughput in the Wet 2024年5月31日 This paper presents an industrial verification test, adding a high pressure grinding roll and magnetic separation operation after the thirdstage fine crushing operation to High Pressure Grinding Roll and Magnetic Separation for Energy
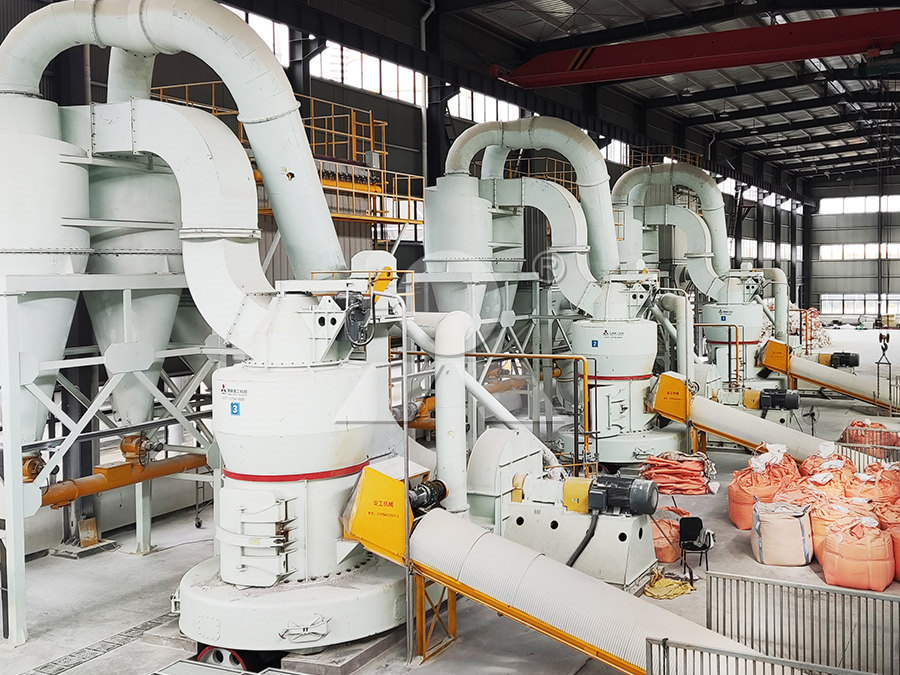
Magnetic Separation Technology for Mineral
2024年5月9日 Magnetic separation technology plays a pivotal role in mineral processing, offering efficient and versatile solutions for separating valuable minerals from gangue materials By harnessing the magnetic properties of 2009年1月1日 The iron ore beneficiation plants normally include a series stages of size reduction (in order to achieve the desired liberation degree), increasing iron ore grade (magnetic separation), and Processing of Magnetite Iron Ores–Comparing PDF On Oct 19, 2016, Serkan Inal and others published PRODUCTION OF CHROMITE CONCENTRATE FROM MAGNETIC WASTES OF ORE PROCESSING PLANT Find, read and cite all the research you need on PRODUCTION OF CHROMITE CONCENTRATE FROM 2021年3月24日 Mineral and Technological Features of Magnetite–Hematite Ores and Their Influence on the Choice of Processing TechnologyMineral and Technological Features of Magnetite–Hematite Ores
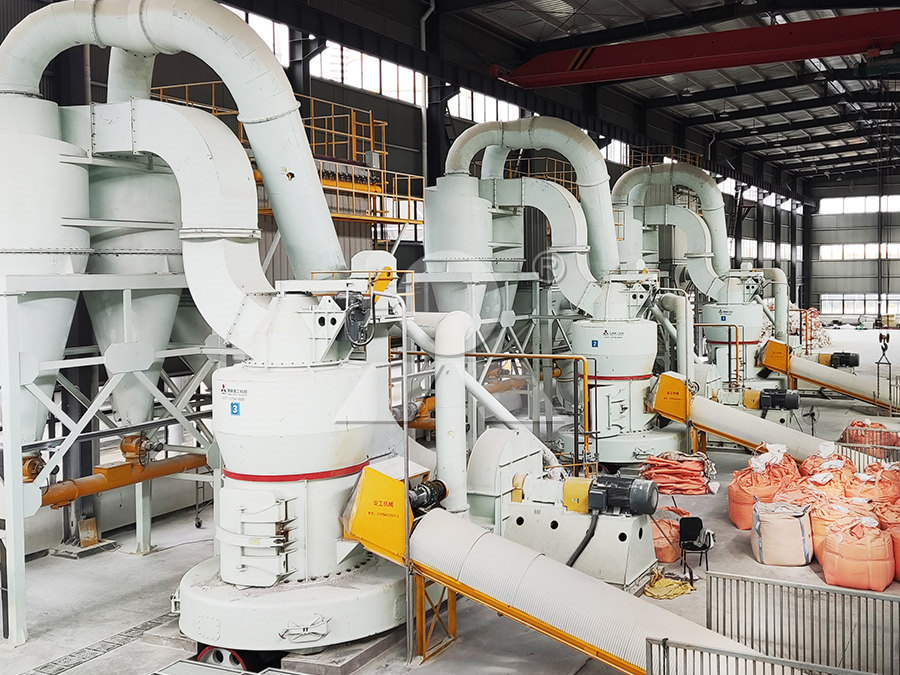
Beach Magnetic Iron Ore Beneficiation Equipment Sand Processing Plant
Beach Magnetic Iron Ore Beneficiation Equipment Sand Processing Plant 1Description Spiral separator for Zircon Ore Concentrating are gravity concentrators and separate minerals of different specific gravity according to their relative movement in response to gravity, centrifugal force and other forces in the fluid mediumto note that much of the pioneer work in magnetic processing of ores was done on dry material In spite of the disadvantages of dusty, uncomfortable plants, the dry method has produced acceptable concen trates in most cases No definite date can be given for the change in emphasis from dry to wet processing of iron ore,ADVANCES IN MAGNETIC SEPARATION OF ORES 911 2020年4月1日 On the other hand, since most plants are optimized for a specific size fraction (≥ 75 µm) and the tailings of chromite plants are generally characterized by fine particles, a recurring problem Process optimization of a chrome ore gravity concentration plant 2012年1月1日 Effect of feed size fraction on the concentrate assay and metal recovery using high intensity magnetic separator The size labels are: 1 for 500+20 μm, 2 for 350+20 μm, and 3 for 150+20 μmEffective processing of lowgrade iron ore through gravity and magnetic
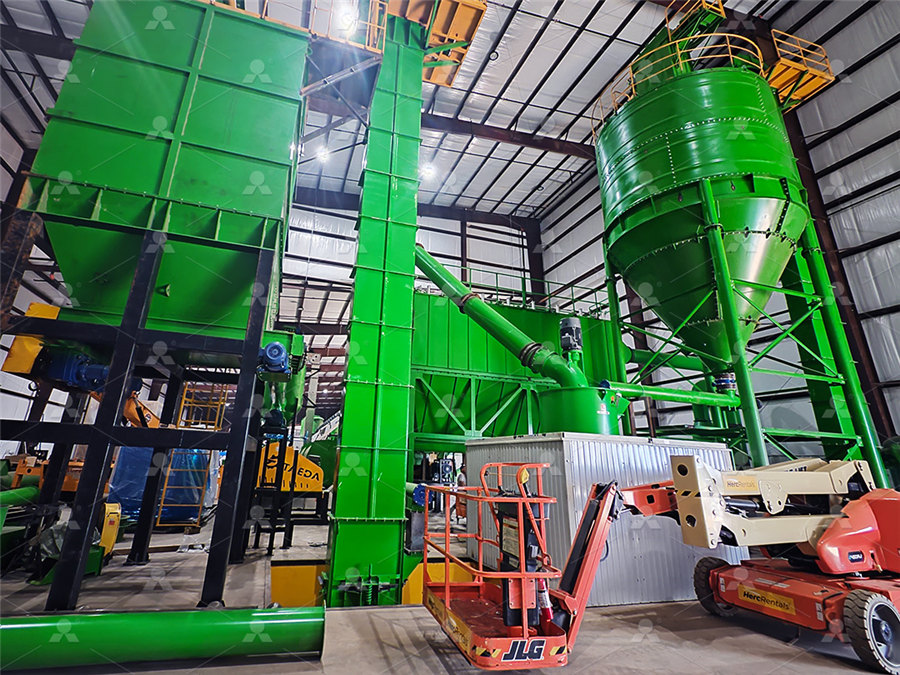
Mineral Processing Plant Beneficiation Solutions JXSC
Ore processing is the process of separating valuable minerals from its ores by ore beneficiation equipment Mineral processing plant is recovers or extracts minerals through a range of ore dressing solutions, including washing, crushing, grinding, gravity concentration, flotation magnetic separation, electrostatic separation and more JXSC provide full mining process Copper processing is a complicated process that begins with mining of the ore (less than 1% copper) and ends with sheets of 9999% pure copper called cathodes, which will ultimately be made into products for everyday useThe most common types of ore, copper oxide and copper sulfide, undergo two different processes, hydrometallurgy and pyrometallurgy, respectively, Copper Mining and Processing: Processing Copper Oresmineral processing, art of treating crude ores and mineral products in order to separate the valuable minerals from the waste rock, or gangue It is the first process that most ores undergo after mining in order to provide a more Mineral processing Metallurgy, Crushing Grinding 2021年3月18日 CIP gold processing plants mostly use a closedcircuit grinding process with inspection and classification and two processes that combine one closedcircuit, preinspection and classification #5 CIP extraction After How Does A CIP Gold Processing Plant Work?
.jpg)
Introduction to Mineral Processing or Beneficiation
Within an ore body, valuable minerals are surrounded by gangue and it is the primary function of mineral processing, to liberate and concentrate those valuable minerals 13 RunOfMine Material and Minerals Generally, mineral 2021年3月24日 Analysis of the current technical solutions for the processing of iron ores showed that the highgrade ores are directly exposed to metallurgical processing; by comparison, lowgrade ores, depending on the mineralogical and material composition, are directed to beneficiation including gravitational, magnetic, and flotation processes or their combination Mineral and Technological Features of Magnetite–Hematite Ores When iron ore is extracted from a mine, it must undergo several processing stages Six steps to process iron ore 1 Screening We recommend that you begin by screening the iron ore to separate fine particles below the crusher’s CSS before the crushing stageThe six main steps of iron ore processing MultotecReducing Grinding Energy and Cost Magnetite Iron Ore Design Case Study A Jankovic and W Valery Metso Process Technology Innovation, PO Box 1028, Eagle Farm Qld, 4009, AustraliaReducing Grinding Energy and Cost Magnetite Iron Ore
.jpg)
Lithium Processing Plant, Equipment JXSC Machinery
Lithium processing plant malinly includs crushing, grinding, gravity separation, flotation, magnetic separation or combined beneficiation process Skip to content JXSC Machinery it is necessary to refer to the particle size of the raw ore and equip a reasonable lithium ore crushing process Grinding Classifying: Tin(Cassiterite) ore processing refers to the process of extracting tin from ore Gravity separation, magnetic separation and flotation are mainly used to grade tin concentrate and remove other impurities In order to achieve high efficient, lowcost beneficiation flow, JXSC will custom process and equipment according to ore characteristicsTin Ore Processing Plant JXSC MachineryA summary of the resultant unit circuit energy for each option is shown in Figure 7 Perth, WA, 27 29 July 2009 3 B McNAB et al FIG 3 Option 1 flow sheet FIG 4 Option 2 flow sheet 4 Perth, WA, 27 29 July 2009 Iron Ore Conference PROCESSING OF MAGNETITE IRON ORES – COMPARING GRINDING OPTIONS FIG 5 Option 3 flow sheetProcessing of Magnetite Iron Ores–Comparing Grinding OptionsThis setup is a 510tph vein gold ore crushing plant, main equipment and flow details as follows: 1 The trough feeder it can feed evenly to the crusher 2 The jaw crusher preliminary crushing of large rocks can also be made mobile type as requested 3 The hammer crusher output size is adjustable like 10mm,5mm, etc For this project it’s grind materials to 02mm, it also can be Hard Rock Gold Processing Plant JXSC Machinery
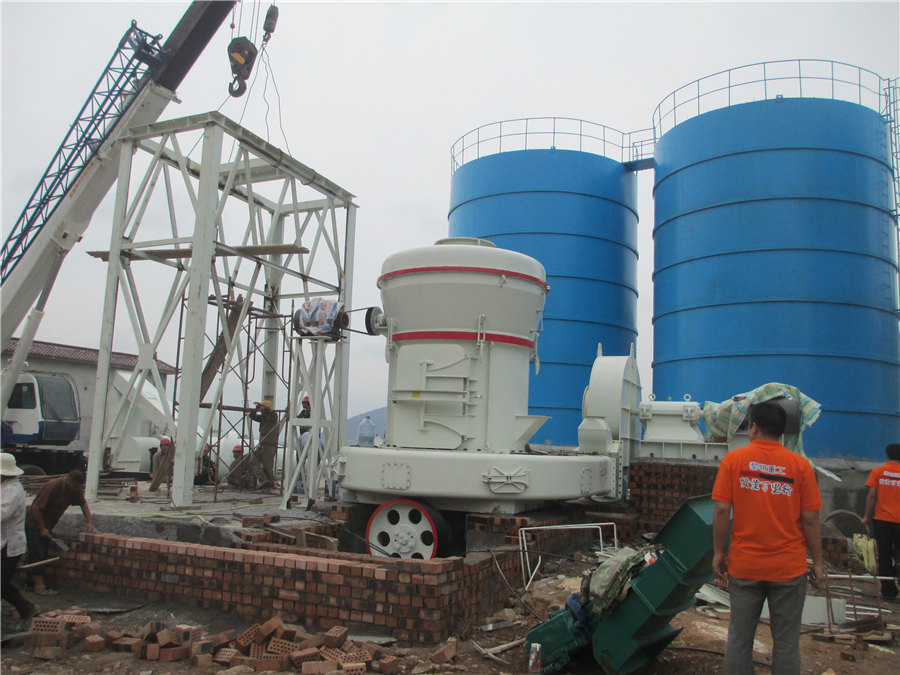
Iron Ore Processing, General SpringerLink
2022年10月20日 Iron ore handling, which may account for 20–50% of the total delivered cost of raw materials, covers the processes of transportation, storage, feeding, and washing of the ore en route to or during its various stages of treatment in the mill Since the physical state of iron ores in situ may range from friable, or even sandy materials, to monolithic deposits with hardness of 2013年9月16日 The major benefit of fully autogenous grinding is the elimination of steel grinding media costs and the need to discriminate between steel and magnetite in coarse magnetic separationEcoEfficient and CostEffective Process Design for 2016年4月27日 The slime fraction of the ore overflowed by the hydraulic classifier and by the rodmill spiral classifier is thickened in a Spiral Rake Tray Thickener for treatment by flotation The flotation circuit is designed to treat Manganese Ore Processing 911Metallurgist2023年3月24日 A 50 TPH tungstenmolybdenum ore processing plant in South Korea is located in Sangdong, which is considered to be the largest tungsten mine in the world The raw ore is a finegrained tungstenmolybdenum ore with a grade of 013% Mo, 035% WO 3 , and 004% molybdenum disulfide (MoS 2 )Tungsten Processing 4 Successful Processing Plants
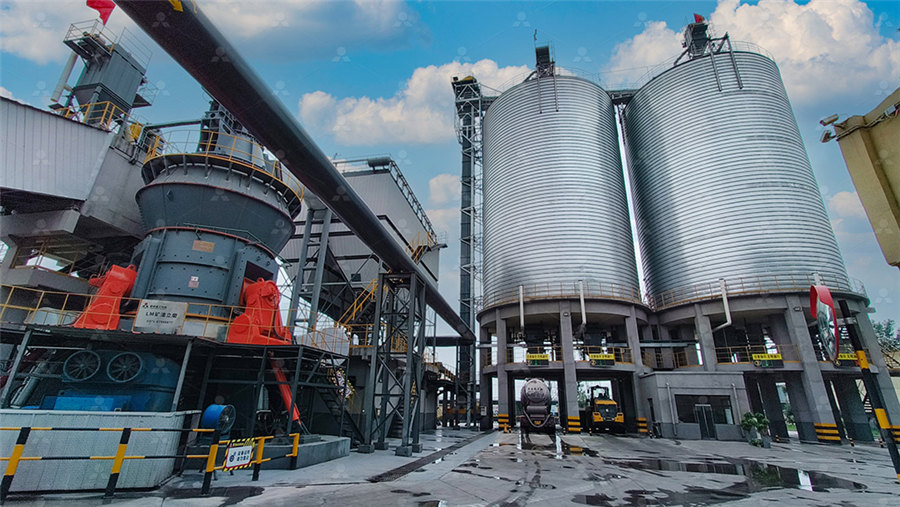
Ecoefficient and costeffective process design for magnetite iron ore
Various magnetite ore grinding flowsheets have been implemented in the past, including: Conventional three A study into the options for a 10 Mtpa ore processing plant for a hard, finegrained, Option 2 has an additional grinding and magnetic separation stage compared to Option 1 and is considered to be simple for design and operation2017年1月1日 Finally, the magnetic component of the roasted ore can be recovered by magnetic separation after being liberated from gangue minerals Many pilotscale suspension magnetizing roasting and magnetic Recovery and separation of iron from iron ore using innovative PDF On Jul 11, 2018, Sandra Lúcia de Moraes and others published Iron Ore Pelletizing Process: An Overview Find, read and cite all the research you need on ResearchGateIron Ore Pelletizing Process: An Overview ResearchGate2021年2月2日 If the ore is igneous carbonatitic alkaline or ultra basic phosphate deposit, crushing, grinding, scrubbing, and flotation associated with other steps such as magnetic and or gravity separation is (PDF) ENRICHMENT OF APATITEBEARING IRON ORE BY MAGNETIC
.jpg)
Manganese ore processing plant Hengcheng Mining Equipment Co,ltd
At Hengcheng, we provide not only gold gravity separation machines, but also flotation, magnetic separation machines Currently we are good at alluvial/deluvial gold ore, hardrock gold ore, manganese ore, tin ore, copper ore, tantalumniobium(coltan) ore processing, and we have gained lots of project running experiences till nowThe iron ore production has significantly expanded in recent years, owing to increasing steel demands in developing countries However, the content of iron in ore deposits has deteriorated and lowgrade iron ore has been processed The fines resulting from the concentration process must be agglomerated for use in iron and steelmaking This chapter shows the status of the Iron Ore Pelletizing Process: An Overview IntechOpen2024年5月9日 Magnetic separation technology plays a pivotal role in mineral processing, offering efficient and versatile solutions for separating valuable minerals from gangue materials By harnessing the magnetic properties of Magnetic Separation Technology for Mineral 2009年1月1日 The iron ore beneficiation plants normally include a series stages of size reduction (in order to achieve the desired liberation degree), increasing iron ore grade (magnetic separation), and Processing of Magnetite Iron Ores–Comparing
.jpg)
PRODUCTION OF CHROMITE CONCENTRATE FROM
PDF On Oct 19, 2016, Serkan Inal and others published PRODUCTION OF CHROMITE CONCENTRATE FROM MAGNETIC WASTES OF ORE PROCESSING PLANT Find, read and cite all the research you need on 2021年3月24日 Mineral and Technological Features of Magnetite–Hematite Ores and Their Influence on the Choice of Processing TechnologyMineral and Technological Features of Magnetite–Hematite Ores Beach Magnetic Iron Ore Beneficiation Equipment Sand Processing Plant 1Description Spiral separator for Zircon Ore Concentrating are gravity concentrators and separate minerals of different specific gravity according to their relative movement in response to gravity, centrifugal force and other forces in the fluid mediumBeach Magnetic Iron Ore Beneficiation Equipment Sand Processing Plant to note that much of the pioneer work in magnetic processing of ores was done on dry material In spite of the disadvantages of dusty, uncomfortable plants, the dry method has produced acceptable concen trates in most cases No definite date can be given for the change in emphasis from dry to wet processing of iron ore,ADVANCES IN MAGNETIC SEPARATION OF ORES 911
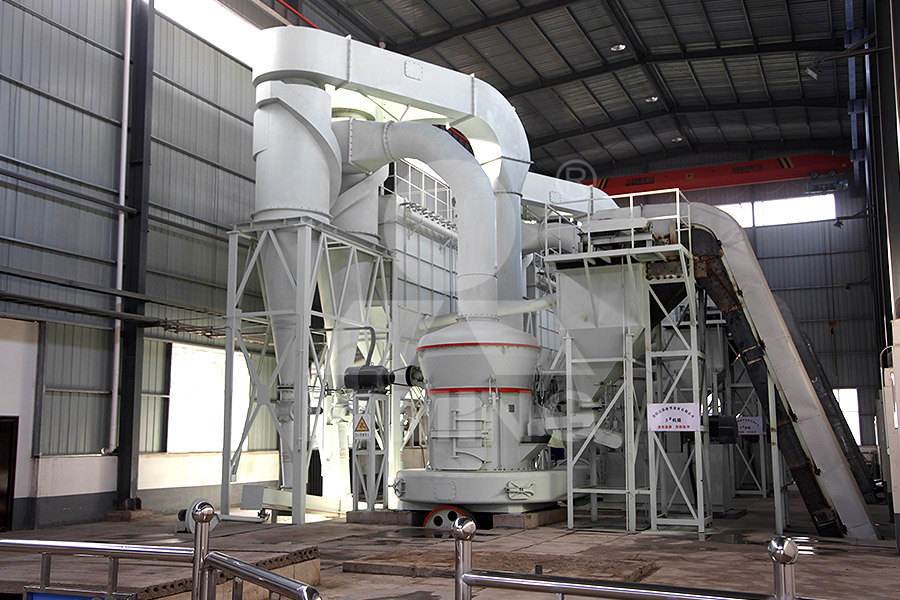
Process optimization of a chrome ore gravity concentration plant
2020年4月1日 On the other hand, since most plants are optimized for a specific size fraction (≥ 75 µm) and the tailings of chromite plants are generally characterized by fine particles, a recurring problem 2012年1月1日 Effect of feed size fraction on the concentrate assay and metal recovery using high intensity magnetic separator The size labels are: 1 for 500+20 μm, 2 for 350+20 μm, and 3 for 150+20 μmEffective processing of lowgrade iron ore through gravity and magnetic Ore processing is the process of separating valuable minerals from its ores by ore beneficiation equipment Mineral processing plant is recovers or extracts minerals through a range of ore dressing solutions, including washing, crushing, grinding, gravity concentration, flotation magnetic separation, electrostatic separation and more JXSC provide full mining process Mineral Processing Plant Beneficiation Solutions JXSC Copper processing is a complicated process that begins with mining of the ore (less than 1% copper) and ends with sheets of 9999% pure copper called cathodes, which will ultimately be made into products for everyday useThe most common types of ore, copper oxide and copper sulfide, undergo two different processes, hydrometallurgy and pyrometallurgy, respectively, Copper Mining and Processing: Processing Copper Ores