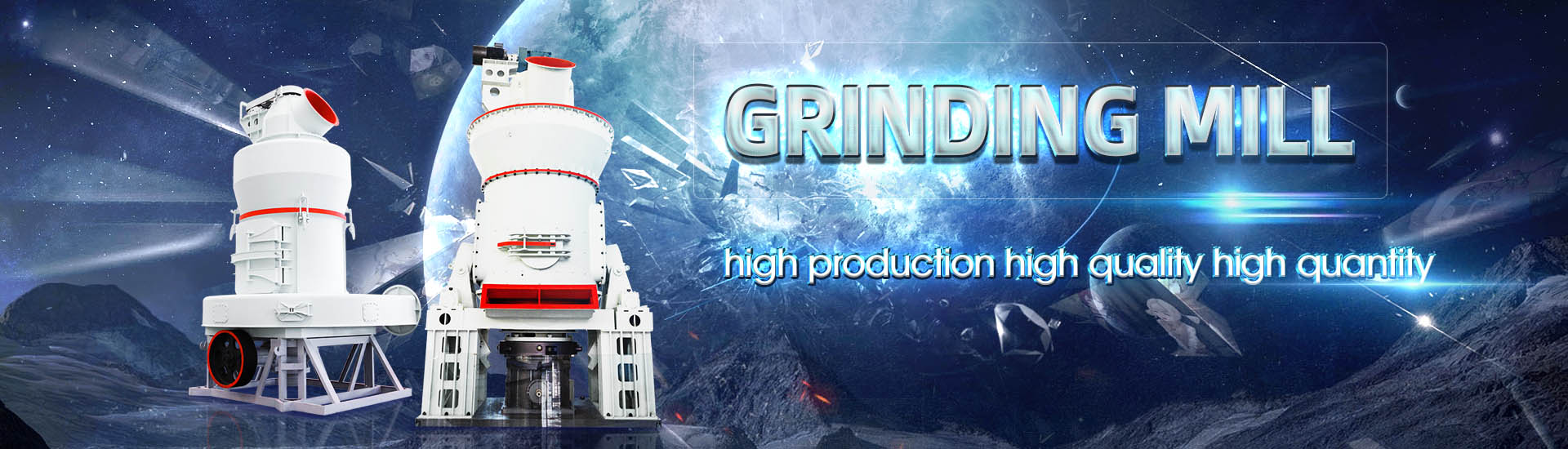
The main cost of hydraulic grinding mill
.png)
A parametric cost model for mineral grinding mills
2014年1月31日 Grinding is one of the most important operations in mineral processing plants and assumes a substantial share of the total milling costs The objective of this work was to develop a set ofThe cost of a grinding mill is influenced by several factors, including the type and size of the mill, material and construction quality, grinding media, drive system and automation, additional The cost of grinding mills: Factors to considerGrinding costs are driven by energy and steel (media, liners, etc) consumption; grinding is the most energyintensive operation in mineral processing On a survey of the energy consumed Grinding Mill an overview ScienceDirect TopicsHydraulic grinding roller swingingout device for easier and quicker changing of grinding components Constant product quality in compliance with specification achieved through static LOESCHEMILLS
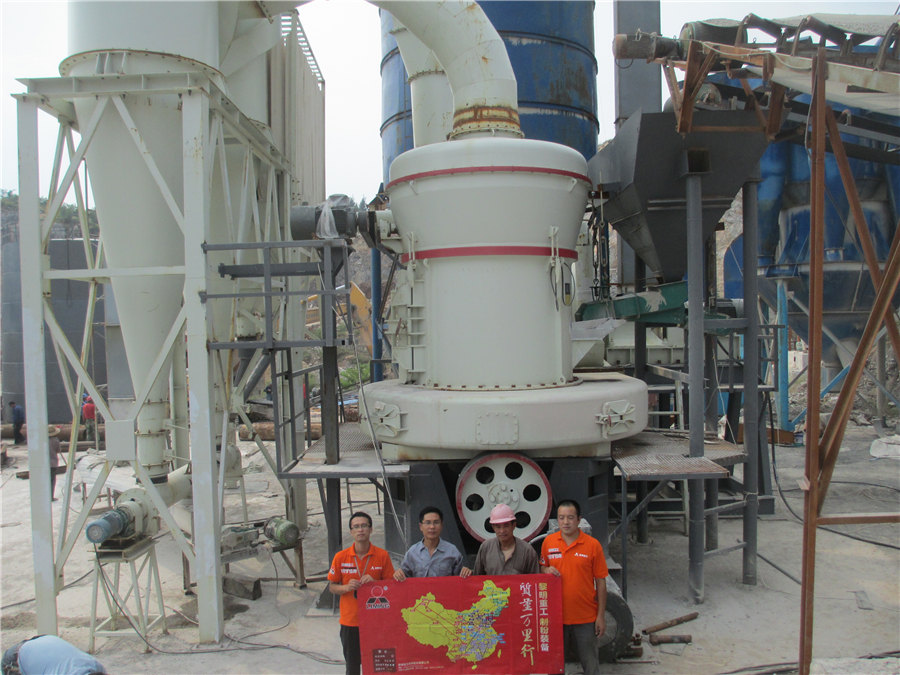
Mine operating costs and the potential impacts of energy and
2014年2月1日 Energy costs typically comprise one of the largest ongoing costs of mining operations, of which 70% is devoted to the comminution of the ore (Norgate and Jahanshahi, efficient grinding plants for its customers Loesche plants are specifically planned for the required process steps and equipped with the associated techno logy This technology comprises: • PROCESS OPTIMISATION FOR LOESCHE GRINDING PLANTSThe mill is driven by an electric motor via a flexible coupling and the mill gearbox via a vertical output flange A segmental thrust bearing at the top of the gearbox absorbs the grinding Loesche Mills for industrial mineralsEvaluation of grinding costs is key to achieving maximum profitability in grinding and it is important that costs are evaluated in a meaningful way Old attitudes of treating abrasive cost, or even Economics of Grinding 16 v2 Handbook of Machining with
.jpg)
Recent developments in grinding machines ScienceDirect
2017年1月1日 In grinding, the total cost of ownership (TCO) includes machinetool acquisition and depreciation, services and support (eg maintenance, training), operating expenses (eg SKF offers solutions for autogenous mills, ball mills, high pressure grinding rolls, rod mills, SAG mils and horizontal grinding mills The solutions are designed to protect pinions and trunnions Grinding mills SKFA vertical roller mill, also known as a vertical grinding mill or vertical mill, is a comprehensive grinding equipment integrating crushing, drying, grinding, grading, and conveying Vertical grinding mills can be widely used in electric power, Energysaving and Efficient Vertical Roller Mill Fote Compression and impact force are the main forces of grinding action and are controlled by hydraulic pressure in the hydropneumatic spring system 2 which helps to refine mill structure and lowers mill weight eventually reduced VRM – AMCL Machinery Limited
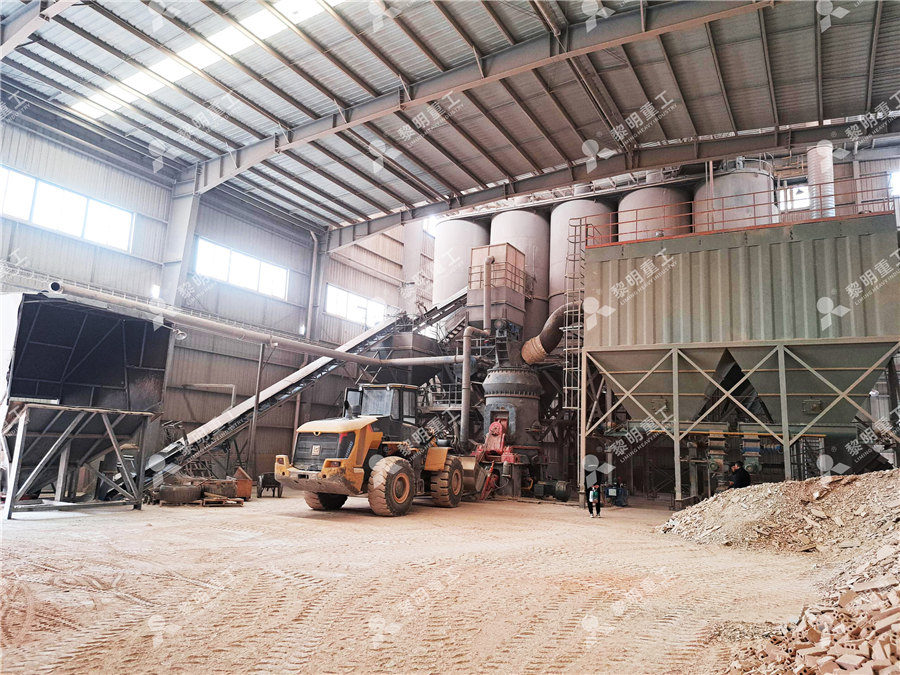
Increase productivity of vertical roller mill using seven
2021年1月29日 High productivity and low power costs can be achieved by increasing output, lowering breakdowns and optimizing the grinding process which eats almost 60% of power costAdopting minerals grinding technology, the hydraulic roller press can be integrated with raw crushing plant, feed material separator, drying device and powder separator to form a grinding system In combination with the ball mill, it can conduct different grinding processes: pregrinding, inter load control of the main drive motor of Hydraulic Roller Press Cement Grinding Equipment PENGFEIIn short, IsaMill™ reduces the energy cost, media cost and capital cost of finegrinding The IsaMill™ is used extensively in base metals, PGM, gold processing and magnetite grinding applications And the power capacity of an IsaMill™ ranges from 75kW to 38mW IsaMill™ is the realworld specification of choice in: mainstream grindingIsaMill™ Glencore TechnologyAs one of the most professional hydraulic lifting basket mill manufacturers and suppliers, we warmly welcome you to wholesale costefficient hydraulic lifting basket mill for sale here from our factory For price consultation, contact usHydraulic Lifting Basket Mill Suppliers, Manufacturers Cost

Opportunities With Underground Grinding and Hydraulic Hoisting
The concept of underground grinding is not new, but to a metallurgist and a mining engineer this could be considered unconventional The idea of pumping a ground slurry several hundred metres from underground in a single lift could also be considered to present a daunting engineering challengex000D Using a practical example of a mine in Australia where the owners have 2021年1月1日 Power cost, fuel cost, Ball mills have been used as the main grinding tool for cement production for over 100 years Insufficient hydraulic pressure for the mill load will result in high circulating load and high pressure loss with potential over filling the mill Review on vertical roller mill in cement industry its performance and not directly related to the mill proper Versatility: Rapid change between feed compositions 3: Mechanical 31: Grinding concept The grinding portion in the OK Mill is significantly different from other cement grinding mills on the market Figure 2: Grinding portion of the OK mill As shown in Figure 2, it consists of aOK Mill: The 3: Mechanical optimized and 31: Grinding concept vertical roller grinding mills for grinding: • Coal • Cement raw material • Clinker / granulated slag • Industrial minerals, and • Ores The core elements of these plants are the Loesche vertical mills for drygrinding the abovementioned grinding stock Loesche has PROCESS OPTIMISATION FOR LOESCHE GRINDING PLANTS
.jpg)
Analysis of vertical roller mill performance with changes in
2022年5月31日 Mineral crushing is the main source of energy consumption in mineral processing According to statistics, this consumption accounts for about 35–50% of the total cost of the mine (Curry et al, 2014), or even higherIt may also account for 18% of the global electrical energy consumption (NapierMunn, 2015)More efficient crushing equipment needs to be 2017年9月11日 All content in this area was uploaded by Deniz Altun on Feb 07, 2019(PDF) Performance Evaluation of Vertical Roller Mill 2020年8月12日 As one of the three major forces of coal mills, the grinding force exerts a significant impact on the working process of coal mills and parameters like mill current and outlet temperatureAn investigation of performance characteristics and FTM Raymond mill, as a kind of grinding mill which is widely used in the field of ore grinding can help users to grind the limestone, marble, calcite, feldspar, and other solid materials into the requested particle size within the range 80325 meshRaymond Mill FTM Mining Machine
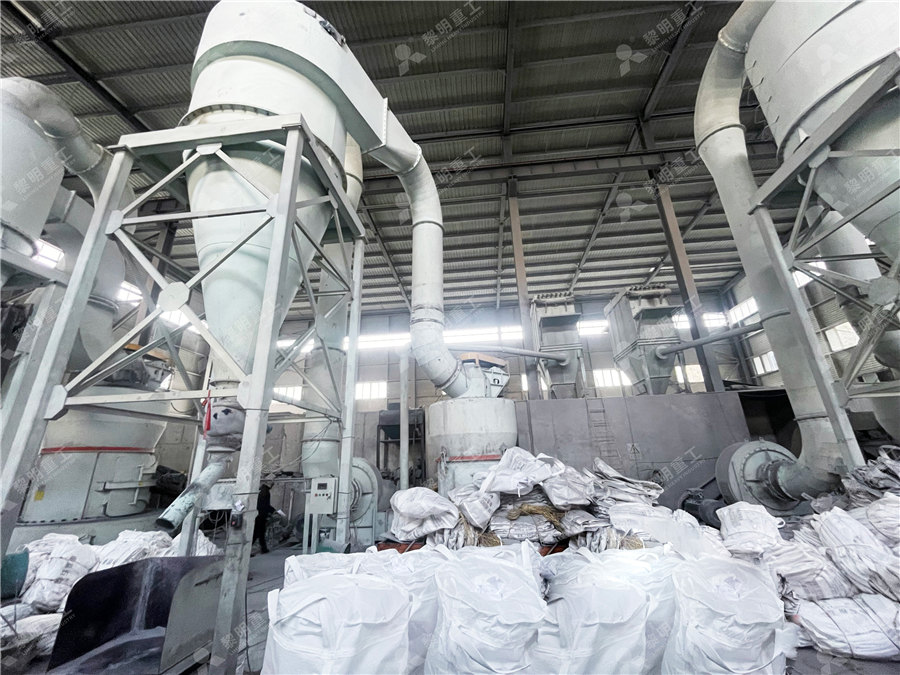
LOESCHEMILLS
1927 First Loesche coal mill delivered for the Klingenberg power station in Berlin 1953 500th coal mill plant sold worldwide 1961 Introduction of hydraulic spring assembly system 1965 Construction of first pressure mill (LM 122 D) 1980 Delivery of first modular coal mill (LM 263 D) 1985 Delivery of first selfinerting coal grinding plant (LM 212 D) for the steel industry (PCI 2023年3月15日 LM Vertical Grinding Mill integrates crushing, drying, grinding, separating and transport The structure is simple while the layout is compact Its occupational area is about 50% of that of the ballmilling system The LM grinding mill can also be arranged outdoors, which greatly reduces the investment costLM Vertical Grinding Mill SBM Mill CrusherR Roller Mill Xiao Xiao1, Huang Lilong2 and Xu Kuangdi3 1Changsha Research Institute of Mining and Metallurgy, Changsha, China 2Changsha Research Institute of Mining and Metallurgy, Changsha, China 3Chinese Academy of Engineering, Beijing, China Roller mill is a type of grinding equipment for crushing materials by pressure between two orRoller Mill Springer2023年2月26日 The main difference between a lathe and mill is that a lathe handles primarily round pieces of material, while a mill shapes them into more complex designs Process of Turning on a Lathe The process of turning on a lathe is a type of machining process that creates objects with symmetrical, round, or tapered profiles by rotating the item held in a chuck or spindle Lathe vs Mill: What’s the Difference and Which is Better?
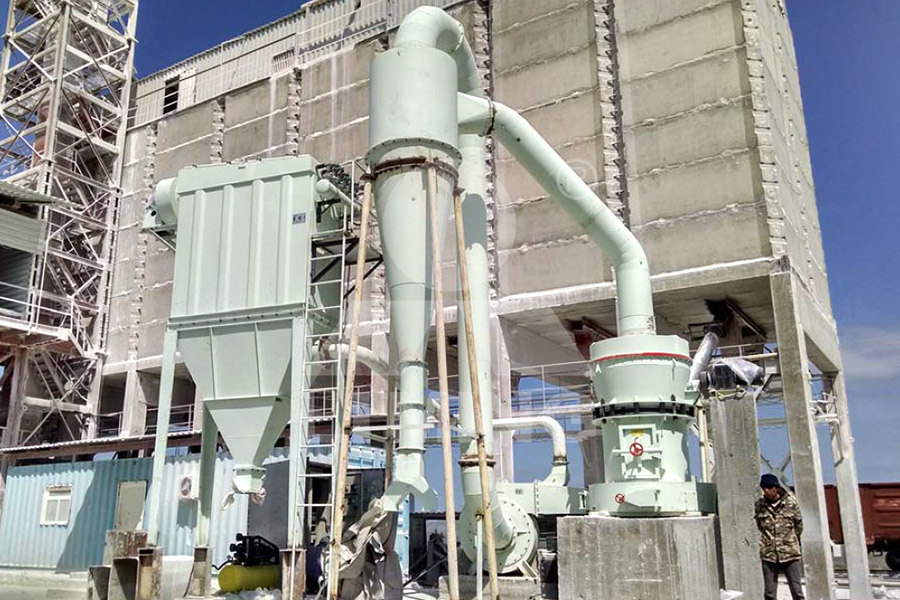
(PDF) The repowering of vertical axis water mills preserving their
2021年8月17日 The main costs related to the repowering and retrofitting of a mill are associated to the were spent to repower a mill for grinding 25 Their hydraulic efficiencies of more than 70%, 2015年3月25日 1 The working principle of the hydraulic system vertical roller mill The hydraulic system ofvertical mill is an important system, the main function ofthe hydraulic system is to break the grinding roller, which is when the internal grinding cavity wear parts wear, can stop open on both sidesofthe grinding roller mill, to replace the inside parts or repairThis type vertical roller Hydraulic system vertical roller mill operation PDF SlideShareThe vertical roller mill (VRM) is a type of grinding machine for raw material processing and cement grinding in the cement manufacturing processIn recent years, the VRM cement mill has been equipped in more and more cement Vertical Roller Mill Operation in Cement Plant2023年5月12日 In position a (Fig 1a) the length l 1 of the lower part of the chamber 1 is minimal, the grinding bodies 2 in it are located at the maximum level h 1Center of masses (CM 1) of grinding bodies (GB) in chamber 1 is located at the minimum distance a 1 from the filling bottom and at the distance b 1 from the crushing cylinder body The length l 2 of the lower part of the Power Calculation of BallTube Mill Drives in the Construction
.jpg)
TwoStage Grinding as the Most CostEffective Option for
2021年7月30日 An ultrafine grinding scheme assessed by the authors as being the most costeffective option for grinding extrahard materials and materials having high su Skip to main content Electrohydraulic grinding is currently in the laboratory research phase Colloidalcavitation wet grinding mill consists of two working rotors 4, 2023年3月15日 Richland Hills, Texas, September 12, 2024 AML, a USbased manufacturer of barcode data collection products, announces the launch of its latest Android ® product, the StrikerX mobile computer StrikerX is the evolution of its predecessor, the Striker, but comes equipped with the most powerful processing architecture available for devices in its class, the The Evolution and Importance of Grinding Mills in Modern Industry2021年8月17日 Hydraulics of the mill (waterwheel + axis) + mill cave + grinding stones + water reservoir (only the crane to lift the upper grinder stone was ok) All: Water wheel dimensions: Diameter: 132 m: Diameter: 132 m: Blade height: 012 m: Blade height: 011 m: Blade number: 32: Blade number: 24: Material: metallic blades, wooden vertical axisThe repowering of vertical axis water mills preserving their cultural As one of the three major forces of coal mills, the grinding force exerts a significant impact on the working process of coal mills and parameters like mill current and outlet temperatureTechnical specifications of vertical roller coal mill
.jpg)
Design of clinker grinding system; mill and separator
Figure 1 presents the design of the clinker grinding system (closed circuit), which consists of a twochamber ball mill and the separator (Plasari and T heraska, 19 81)PDF On May 1, 2017, Caroline Woywadt published Grinding process optimization — Featuring case studies and operating results of the modular vertical roller mill Find, read and cite all the (PDF) Grinding process optimization — Featuring case studies and Our bestinclass OK™ Mill is a globally successful vertical roller mill solution for grinding raw material, cement and slag Its cuttingedge design features consistently deliver the highest quality products with the greatest efficiency It is affordable to install and cost effective to operate over your cement plant’s lifetimeOK™ Raw and Cement MillWhen a drive system is selected for grinding applications, a large number of items need to be checked and many questions must be answered Depending on the mill size and type, the mill can be driven by several configurations of drive systems The main options are single low speed motors connected to a pinion driving a ring gear, two lowTECHNICAL AND COMMERCIAL BENEFITS OF GEARLESS MILL DRIVES FOR GRINDING
.jpg)
Energysaving and Efficient Vertical Roller Mill Fote
A vertical roller mill, also known as a vertical grinding mill or vertical mill, is a comprehensive grinding equipment integrating crushing, drying, grinding, grading, and conveying Vertical grinding mills can be widely used in electric power, Compression and impact force are the main forces of grinding action and are controlled by hydraulic pressure in the hydropneumatic spring system 2 which helps to refine mill structure and lowers mill weight eventually reduced VRM – AMCL Machinery Limited2021年1月29日 High productivity and low power costs can be achieved by increasing output, lowering breakdowns and optimizing the grinding process which eats almost 60% of power costIncrease productivity of vertical roller mill using seven Adopting minerals grinding technology, the hydraulic roller press can be integrated with raw crushing plant, feed material separator, drying device and powder separator to form a grinding system In combination with the ball mill, it can conduct different grinding processes: pregrinding, inter load control of the main drive motor of Hydraulic Roller Press Cement Grinding Equipment PENGFEI
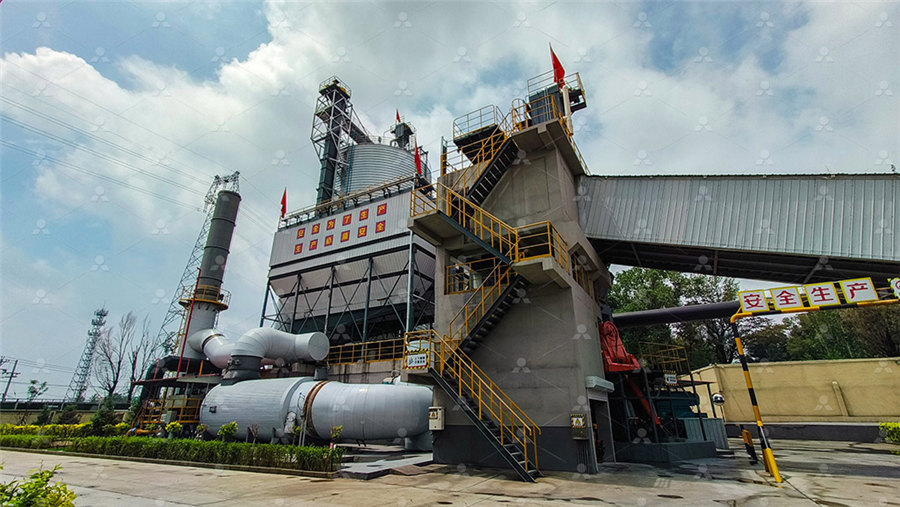
IsaMill™ Glencore Technology
In short, IsaMill™ reduces the energy cost, media cost and capital cost of finegrinding The IsaMill™ is used extensively in base metals, PGM, gold processing and magnetite grinding applications And the power capacity of an IsaMill™ ranges from 75kW to 38mW IsaMill™ is the realworld specification of choice in: mainstream grindingAs one of the most professional hydraulic lifting basket mill manufacturers and suppliers, we warmly welcome you to wholesale costefficient hydraulic lifting basket mill for sale here from our factory For price consultation, contact usHydraulic Lifting Basket Mill Suppliers, Manufacturers Cost The concept of underground grinding is not new, but to a metallurgist and a mining engineer this could be considered unconventional The idea of pumping a ground slurry several hundred metres from underground in a single lift could also be considered to present a daunting engineering challengex000D Using a practical example of a mine in Australia where the owners have Opportunities With Underground Grinding and Hydraulic Hoisting2021年1月1日 Power cost, fuel cost, Ball mills have been used as the main grinding tool for cement production for over 100 years Insufficient hydraulic pressure for the mill load will result in high circulating load and high pressure loss with potential over filling the mill Review on vertical roller mill in cement industry its performance
.jpg)
OK Mill: The 3: Mechanical optimized and 31: Grinding concept
and not directly related to the mill proper Versatility: Rapid change between feed compositions 3: Mechanical 31: Grinding concept The grinding portion in the OK Mill is significantly different from other cement grinding mills on the market Figure 2: Grinding portion of the OK mill As shown in Figure 2, it consists of avertical roller grinding mills for grinding: • Coal • Cement raw material • Clinker / granulated slag • Industrial minerals, and • Ores The core elements of these plants are the Loesche vertical mills for drygrinding the abovementioned grinding stock Loesche has PROCESS OPTIMISATION FOR LOESCHE GRINDING PLANTS