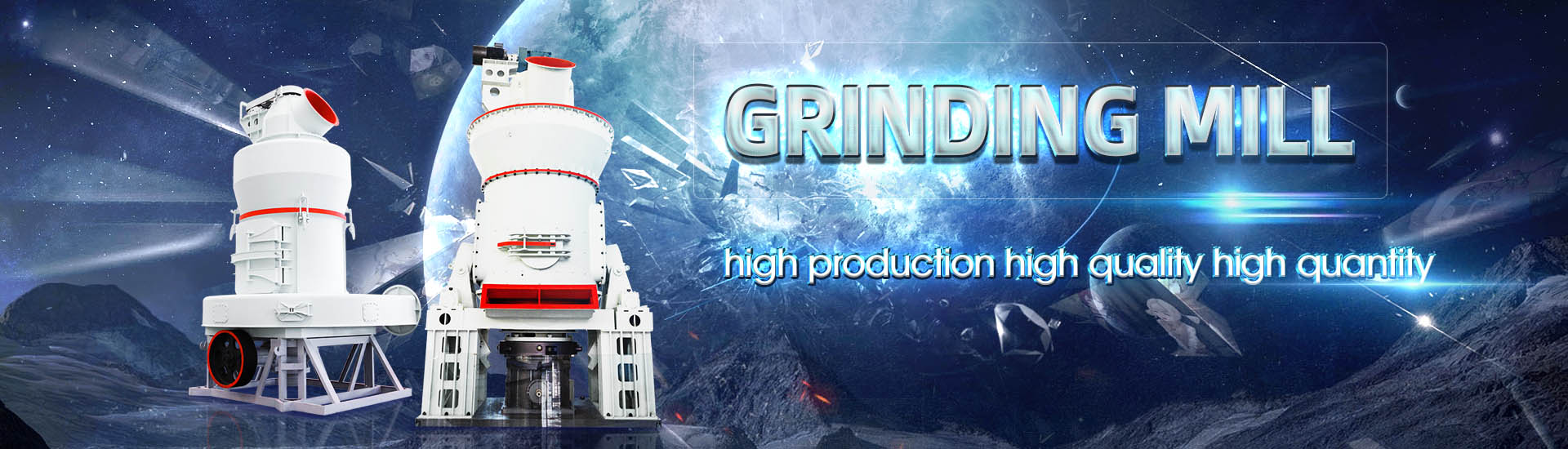
Iron oxide processing machinery
.jpg)
Iron Ore Processing: From Extraction to Manufacturing
2024年4月26日 Iron ore, a naturally occurring mineral composed primarily of iron oxides, is mined and processed to extract iron for various industrial applications This article provides a comprehensive overview of the iron ore 2017年10月17日 The Hismelt process employs a single smelt reduction vessel (SRV) where iron oxide fines are injected deep into hot metal melt, which From Ore to Iron with Smelting and Direct Iron 2017年10月10日 Blast furnacing, smelting and direct iron reduction are the current ironmaking processes Iron is made by reacting iron ore (iron oxide Ironmaking 101 – From Ore to Iron with Blast Furnaces2023年4月5日 Among the reduction methods of iron oxides in ironmaking processes are direct reduction, blast furnace/blast oxygen furnace, and smeltingreduction processRecent Trends in the Technologies of the Direct
.jpg)
Josh Litofsky Iron Ore Analysis Using Portable XRF
One inexpensive way to process and purify iron ores is through the production of direct reduced iron (DRI), also called sponge iron The direct reduction process is a solidstate processing method of reducing various iron oxides to metallic iron India is the largest producer of direct reduction of iron (DRI), popularly known as sponge iron and accounted for about 393% of the global production in 2020 India’s growing economy will ENERGYEFFICIENT TECHNOLOGY OPTIONS FOR DIRECT 2024年2月15日 Coalbased direct reduced iron (DRI) reduces CO 2 emissions by 38 % compared with traditional blast furnace–basic oxygen furnace (BFBOF) ironmaking Using a Direct reduction of iron to facilitate net zero emissions in the steel Iron oxide machines are integral components in the mining industry, designed to facilitate the efficient processing of ores These machines specialize in the reduction of ores into smaller Iron Oxide Machine
.jpg)
Iron Ore Processing an overview ScienceDirect Topics
Resource Recovery and Recycling from Metallurgical Wastes S Ramachandra Rao, in Waste Management Series, 2006 98 Production of Ceramic Tiles from Iron Ore Tailings Current practice of washing iron ore before it is processed for extractive metallurgical operation results in three products, coarse ore lumps with sizes in the range 1080 mm, which are directly charged 2023年4月5日 The blast furnace and direct reduction processes have been the major iron production routes for various iron ores (ie goethite, hematite, magnetite, maghemite, siderite, etc) in the past few decades, but the Recent Trends in the Technologies of the Direct 2017年11月9日 Other iron oxide variants include Goethite, Limonite, and Siderite Each variant contains a known percentage of iron For example, Magnetite ore samples are typically seventythree percent iron, while the rest of the rock contains ironbonded oxygen This is a true Iron Oxide, an iron ore mineral that’s chemically labelled Fe3O4Iron Ore Minerals: How Are They Extracted? Hawk Machinery2020年6月10日 224 Direct Reduction of Iron Oxide by Solid Carbon The direct reduction process of iron oxide by solid carbon is highly endothermic in nature and occurs when the molten slag flows over incandescent coke in the bosh region at a temperature above 1000 °C Therefore, the corresponding reaction can be written as follows:Iron and SteelMaking Process SpringerLink
.jpg)
7 Methods and Equipment for Removing Iron from Quartz Sand
2023年2月15日 FTM MachineryGreen and Intelligent Mining Machinery Manufacturing and Export Base Based on high quality and perfect aftersales service, our products have been exported to more than 120 countries and regions FTM Machinery has become the first choice for over 2,000,000 customers Our customer service team is here to help you 24/7Originally, the iron was collected in pools called pigs, which is the origin of the name pig iron Figure \(\PageIndex{1}\): A Blast Furnace for Converting Iron Oxides to Iron Metal (a) The furnace is charged with alternating layers of iron ore (largely Fe 2 O 3) and a mixture of coke (C) and limestone (CaCO 3)233: Metallurgy of Iron and Steel Chemistry LibreTextsThe direct reduction process is a solidstate processing method of reducing various iron oxides to metallic iron at lower temperatures (well below 1,200 °F) Due to this decreased temperature, steel produced using this technique is more energy efficient than other production techniques4 Determining the concentration of the various phases during DRI processing can improve Josh Litofsky Iron Ore Analysis Using Portable XRF and XRD2017年1月1日 Effective technology for a complex wasteless processing of the iron ores has been designed and includes three main components (plats): comminution plant, briquette plant, pigment plant(PDF) Effective Processing of the Iron Ores ResearchGate

Development of technology for the production of natural red iron oxide
2017年1月1日 The most common inorganic pigment is red iron oxide World production of iron oxide pigments is about 600 thousand tons per year and greatly exceeds the production of other color pigments, with Manganese processing plant includes washing, crushing, gravity separation, flotation and magnetic separation, beneficiation machine's factory price Skip to content JXSC Machinery Us +86 Home; Equipment Gold Mining Equipment It mainly separates the manganese iron oxide Manganese minerals are attracted to magnetic Manganese Ore processing JXSC Machinery2018年5月17日 Properties In the Earth's crust iron is found mainly as minerals of iron oxide such as hematite, magnetite, goethite and limonite The minerals that are mostly used as ore for making iron are hematite (Fe 2 O 3) and Iron Geoscience Australia2023年2月15日 Hematite, also spelled haematite, is a weakly magnetic iron ore with better floatability than magnetite and wide distributionIt is one of the most important raw materials for the extraction of iron Its composition is complex How to Extract Iron from Hematite: Methods and Plants

From Ore to Iron with Smelting and Direct Iron
2017年10月17日 Figure 1: Steelmaking byproducts for blast furnace (BF), basic oxygen furnace (BOF) and electric arc furnace (EAF) processes Source: World Steel Association (worldsteel) The first step in the production of steel or cast Iron oxide masks are glass substrates coated with a thin iron oxide film and AZ1350J photoresist They are developed and stripped in APT chrome developer machine, but manually etched 30; Scope When you have completed your Iron Oxide mask processing, run rinse program 93, then disable the APT chrome on the wandIron Oxide Mask Processing University of California, Berkeley2023年3月13日 FTM MachineryGreen and Intelligent Mining Machinery Manufacturing and Export BaseBased on high quality and perfect aftersales service, our products have been exported to more than 120 countries and regions FTM Machinery has become the first choice for over 2,000,000 customersHow to Process Copper Ore: Beneficiation Methods and Equipment2016年6月15日 21 Preparation of Iron Foams Using FreezeCasting Iron oxide (Fe 2 O 3) powder (mean particle size 99 pct, SigmaAldrich, Co, USA) were used to make a slurry The slurry was prepared by mixing 10 ml deionized water with 4 wt pct binderProcessing, Microstructure, and Oxidation Behavior of Iron Foams
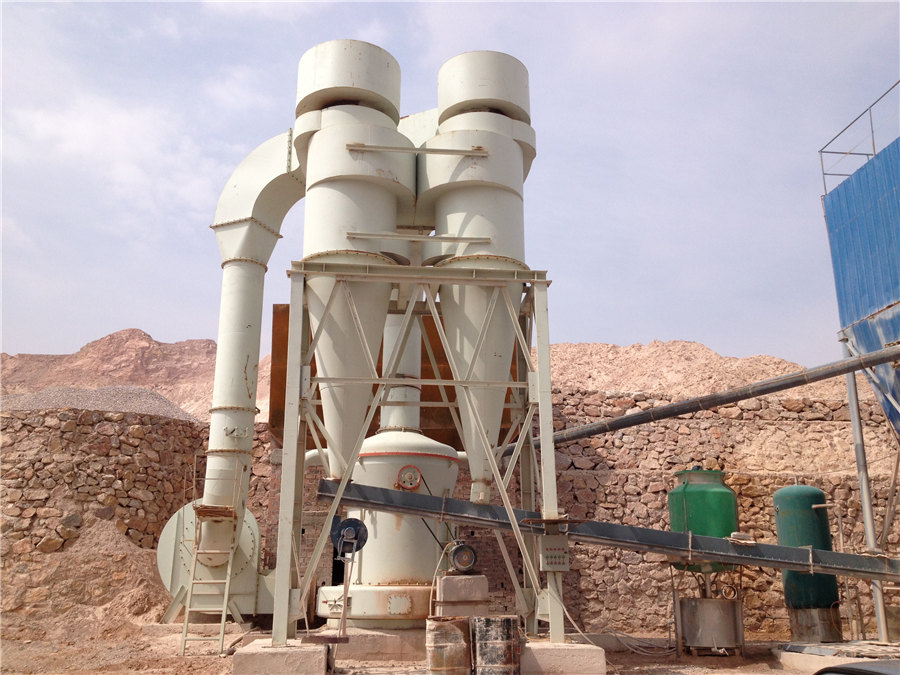
Iron Oxide Machine
Iron oxide machines are integral components in the mining industry, designed to facilitate the efficient processing of ores These machines specialize in the reduction of ores into smaller fragments, Choosing the appropriate iron oxide machine for mining operations is crucialIron processing Ores, Smelting, Refining: Iron ores occur in igneous, metamorphic (transformed), or sedimentary rocks in a variety of geologic environments Most are sedimentary, but many have been changed by weathering, and so their precise origin is difficult to determine The most widely distributed ironbearing minerals are oxides, and iron ores consist mainly of Iron processing Ores, Smelting, Refining Britannica2023年4月25日 The iron minerals’ colors vary and are caused by a high concentration of iron oxides The most important iron deposits are found in sedimentary rocks There are more than 300 types of iron ore, but only 20 types are used, mainly in four types : magnetite (Fe 3 O 4 ), hematite (Fe 2 O 3 ), limonite (2Fe 2 O 3 3H 2 O), and siderite (FeCO 3 )Iron Ore: The Backbone of World Industry Fote MachineryCopper processing is a complicated process that begins with mining of the ore (less than 1% copper) and ends with sheets of 9999% pure copper called cathodes, which will ultimately be made into products for everyday useThe most common types of ore, copper oxide and copper sulfide, undergo two different processes, hydrometallurgy and pyrometallurgy, respectively, Copper Mining and Processing: Processing Copper Ores
.jpg)
Iron Oxide Chapter 1 TheEnigmaMachine Archive of Our Own
Two, solid, yellow rectangles appeared on the front segment of machine's screen Two arms, adorned with claws, unfolded from the side of the egg, filling the forest with the sound of screeching metal While he used all of his processing power to analyze the robot, he felt something pull against the Emerald in his handCopper oxide requires gravity separation after the crushing stage, which our line of machinery can handle with swift efficiency For iron recovery, we apply magnetic separators to remove iron before gravity separationCopper Processing Plant JXSC2024年8月21日 Moreira et al developed an iron oxide/graphenic carbon hybrid photocatalyst for the decomposition of PFAS contaminants, under UV light Their method offers a cheap and efficient alternative that Hybrid graphenic and iron oxide photocatalysts for 2023年4月7日 Magnetite is an iron oxide ore, which belongs to the equiaxed crystal system, and its chemical formula is Fe 3 O 4 The Mohs hardness of magnetite is 55~65 Like hematite , it has strong magnetismHow to Recover Iron from Magnetite: 4 Methods and Stages
.jpg)
Iron Ore Processing, General SpringerLink
2022年10月20日 Iron ore handling, which may account for 20–50% of the total delivered cost of raw materials, covers the processes of transportation, storage, feeding, and washing of the ore en route to or during its various stages of treatment in the mill Since the physical state of iron ores in situ may range from friable, or even sandy materials, to monolithic deposits with hardness of Finished products: 2020% of copper concentrate grade and 9362% of copper recovery rate 6385% of iron concentrate grade and 3214% of iron recovery rate Chemical Processing Method Applicable copper ores: The ore that copper is difficult to float in the form of chrysocolla, cuprite and copper ore impregnated by iron hydroxide and manganese aluminosilicate or in the form Copper Ore Processing Plant Fote Machinery2024年11月21日 1 Magnetic separation methods Magnetic separation is the primary physical iron removal methodIron mineral impurities in kaolin usually have weak magnetic properties and can be removed by magnetic separationThe effect of removing iron by ordinary magnetic separation is remarkable for magnetic solid minerals such as magnetite and ilmenitePurifying Kaolin: Removing Iron Impurities Made Easy2017年6月28日 Iron ore processing calls up a whole proprietary range of extractive gear That primary crusher now has a secondary stage The ore is recycled and crushed again, then it’s passed forward to a grinding station, so the iron ore is HOW DOES MINING EQUIPMENT WORK IN IRON ORE MINING Hawk Machinery
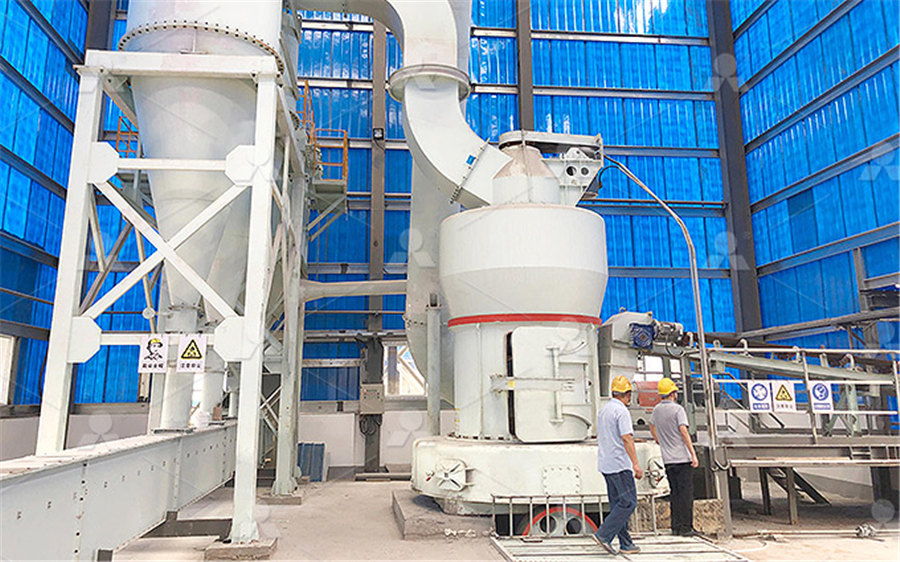
Black Phosphate vs Black Oxide: The Ultimate Guide to Conversion
2024年11月20日 Black Oxide Coating: This process encompasses the conversion of, amongst others, iron (II) phosphide into iron (II, III) oxide by an alkaline solution especially sodium hydroxide Process Temperature: Black Phosphate: Carried out at relatively low temperatures, generally between 20100 Degree C, depending on the specific type of phosphate used2024年8月14日 A wide range of applications using functionalized magnetic nanoparticles (MNPs) in biomedical applications, such as in biomedicine as well as in biotechnology, have been extensively expanding over the last years Their potential is tremendous in delivery and targeting systems due to their advantages in biosubstance binding By applying magnetic materials Multifunctional Iron Oxide Nanoparticles as Promising Magnetic Resource Recovery and Recycling from Metallurgical Wastes S Ramachandra Rao, in Waste Management Series, 2006 98 Production of Ceramic Tiles from Iron Ore Tailings Current practice of washing iron ore before it is processed for extractive metallurgical operation results in three products, coarse ore lumps with sizes in the range 1080 mm, which are directly charged Iron Ore Processing an overview ScienceDirect Topics2023年4月5日 The blast furnace and direct reduction processes have been the major iron production routes for various iron ores (ie goethite, hematite, magnetite, maghemite, siderite, etc) in the past few decades, but the Recent Trends in the Technologies of the Direct
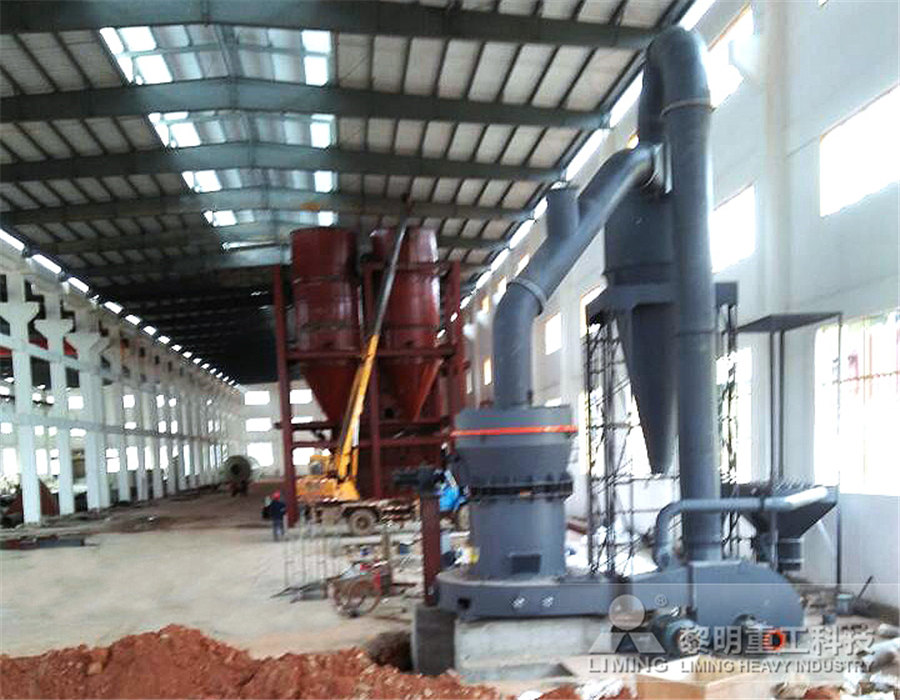
Iron Ore Minerals: How Are They Extracted? Hawk Machinery
2017年11月9日 Other iron oxide variants include Goethite, Limonite, and Siderite Each variant contains a known percentage of iron For example, Magnetite ore samples are typically seventythree percent iron, while the rest of the rock contains ironbonded oxygen This is a true Iron Oxide, an iron ore mineral that’s chemically labelled Fe3O42020年6月10日 224 Direct Reduction of Iron Oxide by Solid Carbon The direct reduction process of iron oxide by solid carbon is highly endothermic in nature and occurs when the molten slag flows over incandescent coke in the bosh region at a temperature above 1000 °C Therefore, the corresponding reaction can be written as follows:Iron and SteelMaking Process SpringerLink2023年2月15日 FTM MachineryGreen and Intelligent Mining Machinery Manufacturing and Export Base Based on high quality and perfect aftersales service, our products have been exported to more than 120 countries and regions FTM Machinery has become the first choice for over 2,000,000 customers Our customer service team is here to help you 24/77 Methods and Equipment for Removing Iron from Quartz SandOriginally, the iron was collected in pools called pigs, which is the origin of the name pig iron Figure \(\PageIndex{1}\): A Blast Furnace for Converting Iron Oxides to Iron Metal (a) The furnace is charged with alternating layers of iron ore (largely Fe 2 O 3) and a mixture of coke (C) and limestone (CaCO 3)233: Metallurgy of Iron and Steel Chemistry LibreTexts
.jpg)
Josh Litofsky Iron Ore Analysis Using Portable XRF and XRD
The direct reduction process is a solidstate processing method of reducing various iron oxides to metallic iron at lower temperatures (well below 1,200 °F) Due to this decreased temperature, steel produced using this technique is more energy efficient than other production techniques4 Determining the concentration of the various phases during DRI processing can improve 2017年1月1日 Effective technology for a complex wasteless processing of the iron ores has been designed and includes three main components (plats): comminution plant, briquette plant, pigment plant(PDF) Effective Processing of the Iron Ores ResearchGate2017年1月1日 The most common inorganic pigment is red iron oxide World production of iron oxide pigments is about 600 thousand tons per year and greatly exceeds the production of other color pigments, with Development of technology for the production of natural red iron oxide Manganese processing plant includes washing, crushing, gravity separation, flotation and magnetic separation, beneficiation machine's factory price Skip to content JXSC Machinery Us +86 Home; Equipment Gold Mining Equipment It mainly separates the manganese iron oxide Manganese minerals are attracted to magnetic Manganese Ore processing JXSC Machinery