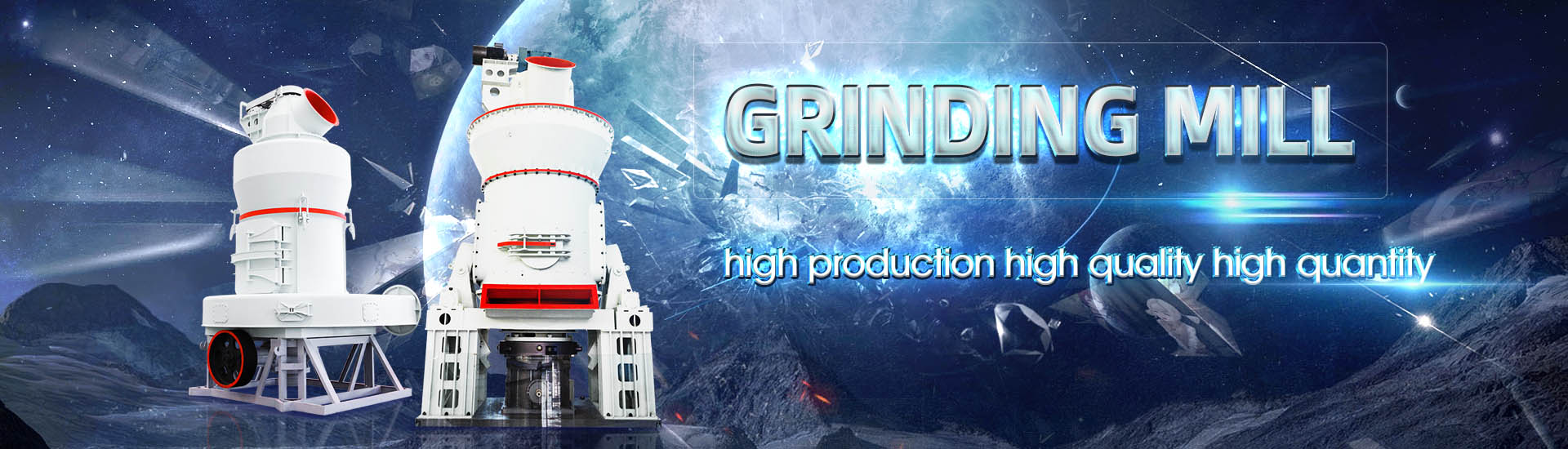
Grinding mill, selection principle, Seconds
.jpg)
Chapter 10 Selection of Fine Grinding Mills ScienceDirect
2007年1月1日 The fine grinding mills are classified often into five major groups (i) impact mills, (ii) ball media mills, (iii) air jet mills, (iv) roller mills, and (v) shearing attrition mills from the viewpoints of grinding machinesThis document provides guidance on ball mill grinding processes It covers topics such as ball mill design including length to diameter ratios, percent loading, critical speed, and internals evaluation Methods for assessing ball charge, Ball Mill Grinding Process Handbook2020年9月22日 The processing capacity of ball mills and rod mills is usually calculated by volumetric method or power consumption method, and the selection of ore mill should meet the following requirements: 1) Rod mills are mostly Grinding Machines: Types and Selection PrinciplesIn this presentation we will discuss the principle of the Attritor and its applications The Attritor is a grinding mill containing internally agitated media It has been generically referred to as a ATTRITORS AND BALL MILLS HOW THEY WORK Union Process

Principles of Modern Grinding Technology
2013年1月1日 Principles of Modern Grinding Technology explains the principles that led to rapid improvements in modern grinding technology over recent decades Removal rates and quality standardsThis paper will focus on the ball mill grinding process, its tools and optimisation possibilities (see Figure 1) The ball mill comminution process has a high electrical energy consumption, BALL MILLS Ball mill optimisation Holzinger ConsultingGrinding is divided into three basic applications: • Precision grinding (die grinders) • Rough grinding and cutting off • Surface grinding (sanders and polishers) With this division, Pocket Guide to Grinding Technique Atlas Copco2004年12月10日 Presently, the description, selection and design of comminution and dispersion processes are based mainly on practical experience and empirical relations For the Mill selection and process optimization using a physical grinding
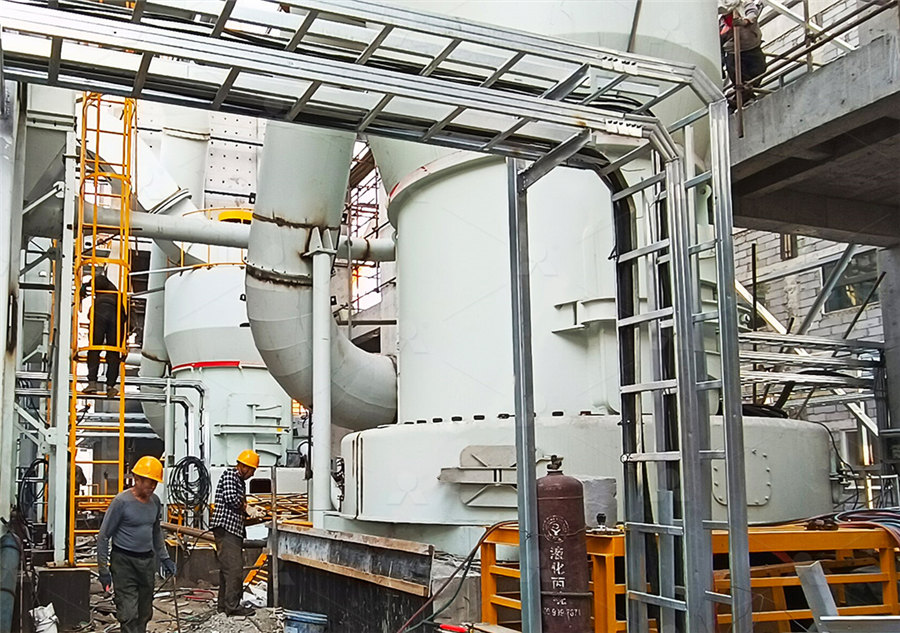
Selection Tips for Grinding Mills Union Process
Selecting the right grinding mills for your operation requires the serious consideration of a variety of factors, far beyond “what do I want to grind?” and “How fine do I want it?” A starter list of The bead mill is an apparatus that agitates grinding media (beads) in a cylindrical vessel to grind or disperse minute particles in slurry The rotor of the mill generates bead motion, which induces intense shear force and impact on the Bead Mill, Principle and Applications / Apex Mill series Grinding Mills: Ball Mill Rod Mill Design PartsCommon types of grinding mills include Ball Mills and Rod Mills This includes all rotating mills with heavy grinding media loads This article focuses on ball and rod mills excluding SAG and AG Grinding Mills 911Metallurgist2020年7月24日 Cryomilling is a ball mill micronization process that is carried out at a low temperature (RETSCH, 2021) The grinding jar is cooled to ca −196°C by liquid nitrogen supplied continuously (PDF) A Review on Cryogenic Grinding ResearchGate
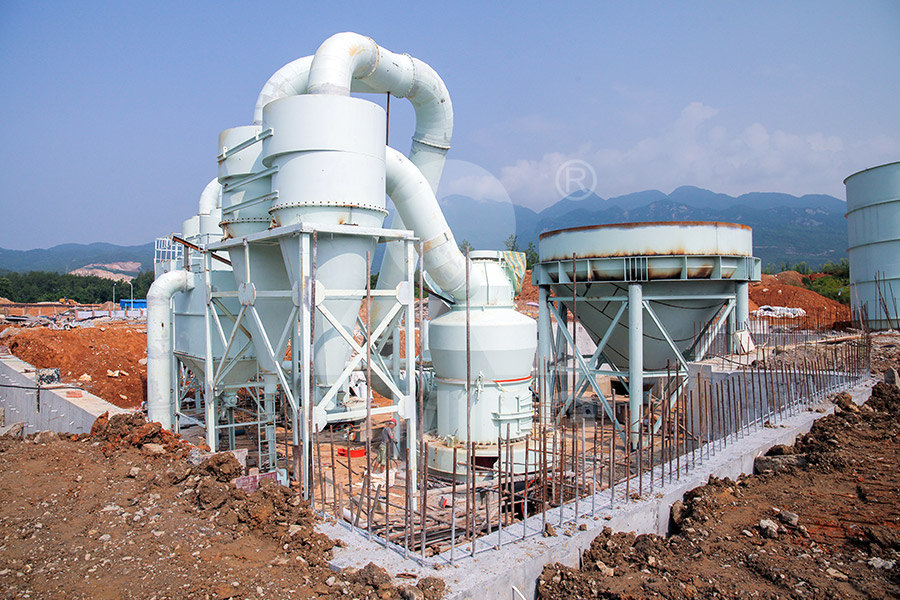
Chapter 10 Selection of Fine Grinding Mills ScienceDirect
2007年1月1日 The subject of selection of grinding machines here is limited to the fine grinding mills, which in principle produce fine and ultrafine particles 2 As for the selection of fine grinding mills, each mill has its own advantageous particle size range for 2009年10月1日 The principle was tested on the planetary ball mill and the horizontal laboratory ball mill, and according to the results obtained, it can be concluded that the proposed methodology can be useful Batch Grinding in Laboratory Ball Mills: Selection FunctionATTRITOR GRINDING MILLS AND NEW DEVELOPMENTS I INTRODUCTION AND PRINCIPLES In this presentation we will discuss the principle of the Attritor and its applications The Attritor is a grinding mill containing internally agitated media It has been generically referred to as a “stirred ball mill”We will discuss the principle of the Attritor and its applications2018年8月17日 Extreme temperatures, impact velocity, mill load, grinding media, ore types, and applications are some of the factors to be considered while installing new linersGrinding Mills — Types, Working Principle Applications
.jpg)
TECHNOLOGY SELECTION OF STIRRED MILLS FOR ENERGY
strategies will focus specifically on the two major stirred mill machine types; namely, gravityinduced (VERTIMILL™ grinding mill and NippionEirich tower mill) and fluidized (SMD, Isamill™, KnelsonDeswik mill, etc ) Finally, case studies from circuits across industry and laboratory tests will be used to illustrate2017年7月17日 A threeroll mill is used mostly for dispersion, but does some grinding as well It uses three rollers of different speeds and directions to cause the sheer force between them to disperse and grind particles The threeroll mill is used to disperse material within a media, which is usually some type of semiviscous material such as creamThreeroll mill selection tips Processing Magazinenormal time to prepare samples is from two to ten seconds A safety switch located in the lid prevents accidental operation of the mill with the lid removed The KN 295 Knifetec™ is equipped with a grinding chamber cooling feature which enables it to be connected to a cold water tap or other laboratory chilling devicesMill Collection fossanalytics2013年1月1日 Bond, 1952, Bond, 1960 formulated the earliest scaleup model for prediction and design of the performance of an industrialscale ball mill This procedure evolved from the classical energysize reduction principle (Austin, 1973)Although the Bond model has since been used to characterize the grinding of carrots (Chakkaravarthi et al, 1993), Gum karaya (Walde Grinding for food powder production ScienceDirect
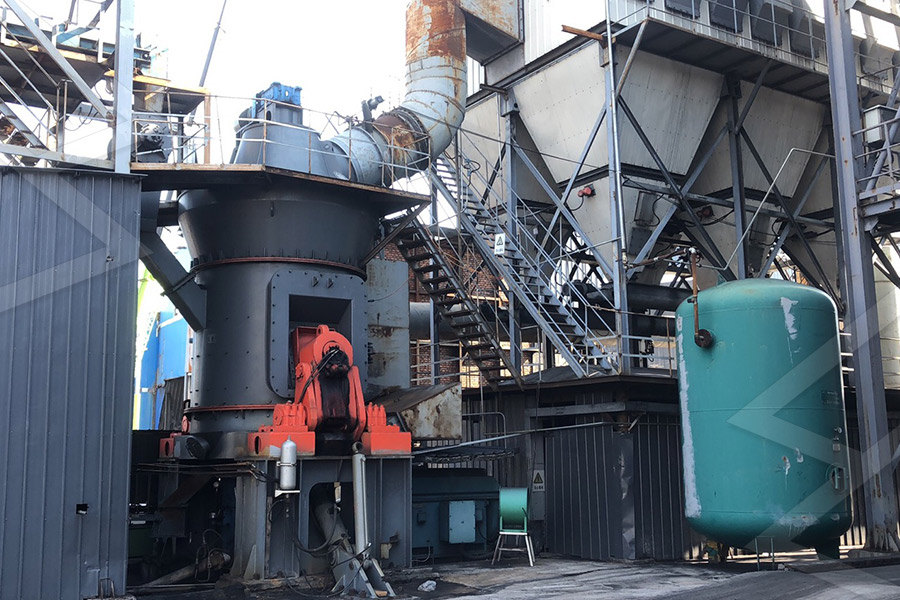
Ball Mill VS Rod Mill: Difference Selection JXSC
2024年1月10日 The two are similar in appearance and grinding principle, but there are differences in structure, performance, use, etc Home » News » Ball Mill VS Rod Mill: Difference Selection Contact Now +86 Attrition Mill Grinding of Refractories John E Becker UNION PROCESS, INC Akron, Ohio Ceram Eng Sci Proc, 16[1] 11526 (1995) The principles and applications of wet and dry grinding refractory materials in the Attritor, a highenergy stirred ball mill, Grinding media selection is based upon several interrelated factors:Attrition Mill Grinding of Refractories Union ProcessDuring frictional grinding, heat development should be considered because a significant part of the energy is lost as heat Equipment such as ball mills and disc mills use this grinding principle, where the action of the surfaces moving against each other results in size reduction through frictional forcesGrinding Mills for reliable size reduction tasks RETSCHIntroduction The LM Vertical Grinding Mill , launched by SMMVIK Machinery, integrates five functions of crushing, grinding, powder selection, drying and material conveyingIt is characterized by centralized technological process, small occupational area, low investment, high efficiency, energy conservation and environment protectionLM Vertical Grinding Mill SMMVIK Machinery

Grinding Mills and Pulverizers Selection Guide: Types, Features
Video credit: shsbjq / CC BYSA 40 Specifications Important specifications when selecting grinding mills and pulverizers include, The size of the mill can range from pilot/lab to production, eg, 35 to 1600 cu ft; Feed size, material, and hardness of feed must be considered; Output size ranges; Mills can handle dry or wet input, or both; Mills operate in batches or continuouslyGrinding Mills Barry A Wills, James A Finch FRSC, FCIM, PEng, in Wills' Mineral Processing Technology (Eighth Edition), 2016 71 Introduction Grinding is the last stage in the comminution process where particles are reduced in size by a combination of impact and abrasion, either dry, or more commonly, in suspension in waterGrinding Mill an overview ScienceDirect Topics302 Principles of comminution Comminution is a generic term for size reduction; In the mill the grinding chamber is an oval loop of pipe 25 to 200 mm in diameter and 12 to 24 m high Feed enters through a venturi injector which is situated near the bottom of the loopSize Reduction1: Grinding – Unit Operations in Food Processing2006年1月1日 An overview of the selection and design of mill liners was published by Powell et al (2006), providing a reference source on mill liners, however no comprehensive technical manual or training is (PDF) Selection and design of mill liners ResearchGate

Ball Mill Grinding Process Handbook
Ball Mill Grinding Process Handbook Free download as PDF File (pdf), Text File (txt) or read online for free This document provides guidance on ball mill grinding processes It covers topics such as ball mill design including length to diameter ratios, percent loading, critical speed, and internals evaluation Methods for assessing ball charge, wear rates, and liner management are 2017年10月26日 The following are factors that have been investigated and applied in conventional ball milling in order to maximize grinding efficiency: a) Mill Geometry and Speed – Bond (1954) observed grinding efficiency to be a Factors Affecting Ball Mill Grinding Efficiency2016年6月6日 Sufficient capacity (primarily a concern of large circuits where multiple pebble crushers are required to serve one grinding line); Design for bypassing crushers during maintenance, and; Evaluation of the where to SAG Mill Grinding Circuit Design 911MetallurgistSIZE of grinding media is one of the principal factors affecting efficiency and capacity of tumblingtype grinding mills It is best determined for any particular installation by lengthy plant tests with carefully kept records However, a method of calculating the proper sizes, based on correct theoretical principles and tested by experience, can be very helpful, both for new installations Grinding Ball Size Selection OneMine

6 Aspects For You to Understand Raymond Mill
2023年6月12日 Overview of Raymond Mill Raymond mill is one the most commonly used grinding mill in China's grinding industry It has been widely used in the milling and processing fields of more than 280 kinds of materials in the industries of nonflammable and nonexplosive minerals, chemicals, construction, etc, such as barite, calcite, potash feldspar, talc, marble, SIZE of grinding media is one of the principal factors affecting efficiency and capacity of tumblingtype grinding mills It is best determined for any particular installation by lengthy plant tests with carefully kept records However, a method of calculating the proper sizes, based on correct theoretical principles and tested by experience, can be very helpful, both for new installations OneMine Minerals Beneficiation Grinding Ball Size SelectionMill Selection and Arrival: Before installation, carefully select the appropriate grinding mill based on your specific application and requirements Once the mill is delivered to the site, inspect it for any damage that may have occurred during transportationA guide to grinding mill installation: Ensuring efficient and 2017年10月3日 Share with Facebook; Share with Twitter; Share with Google+; Share with LinkedIn; Posted: October 3, 2017 Grinding Mills Types, Working Principle Applications The purpose of this article is to explain the usage of grinding mills in a mineral processing operation and to enable buyers to understand the best suitable grinding mill as per their specific needsGrinding Mill Types, Working Principle Applications
.jpg)
Grinding Ball Size Selection PDF Mill (Grinding) Minerals
Grinding Ball Size Selection Free download as PDF File (pdf), Text File (txt) or read online for free The document discusses methods for selecting the proper size of grinding balls used in tumblingtype grinding mills It begins by explaining that the size of grinding balls impacts grinding efficiency and capacity It then presents an empirical equation previously developed by the Selecting the right grinding mills for your operation requires the serious consideration of a variety of factors, far beyond “what do I want to grind?” and “How fine do I want it?” A starter list of questions would include: Do you need lab grinding mills or production sized mills? Do you need to perform wet or dry milling?Selection Tips for Grinding Mills Union ProcessGrinding Mills: Ball Mill Rod Mill Design PartsCommon types of grinding mills include Ball Mills and Rod Mills This includes all rotating mills with heavy grinding media loads This article focuses on ball and rod mills excluding SAG and AG Grinding Mills 911Metallurgist2020年7月24日 Cryomilling is a ball mill micronization process that is carried out at a low temperature (RETSCH, 2021) The grinding jar is cooled to ca −196°C by liquid nitrogen supplied continuously (PDF) A Review on Cryogenic Grinding ResearchGate
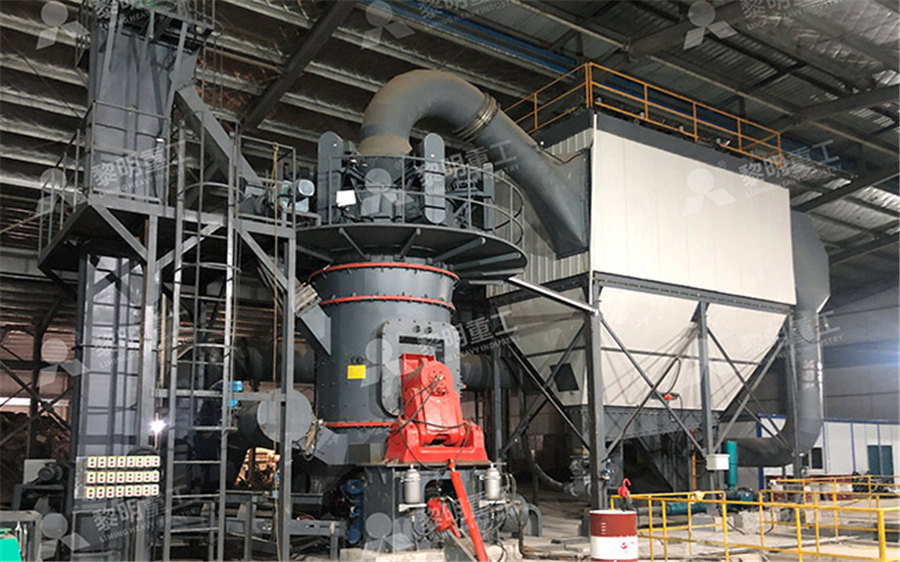
Chapter 10 Selection of Fine Grinding Mills ScienceDirect
2007年1月1日 The subject of selection of grinding machines here is limited to the fine grinding mills, which in principle produce fine and ultrafine particles 2 As for the selection of fine grinding mills, each mill has its own advantageous particle size range for 2009年10月1日 The principle was tested on the planetary ball mill and the horizontal laboratory ball mill, and according to the results obtained, it can be concluded that the proposed methodology can be useful Batch Grinding in Laboratory Ball Mills: Selection FunctionATTRITOR GRINDING MILLS AND NEW DEVELOPMENTS I INTRODUCTION AND PRINCIPLES In this presentation we will discuss the principle of the Attritor and its applications The Attritor is a grinding mill containing internally agitated media It has been generically referred to as a “stirred ball mill”We will discuss the principle of the Attritor and its applications2018年8月17日 Extreme temperatures, impact velocity, mill load, grinding media, ore types, and applications are some of the factors to be considered while installing new linersGrinding Mills — Types, Working Principle Applications
.jpg)
TECHNOLOGY SELECTION OF STIRRED MILLS FOR ENERGY
strategies will focus specifically on the two major stirred mill machine types; namely, gravityinduced (VERTIMILL™ grinding mill and NippionEirich tower mill) and fluidized (SMD, Isamill™, KnelsonDeswik mill, etc ) Finally, case studies from circuits across industry and laboratory tests will be used to illustrate2017年7月17日 A threeroll mill is used mostly for dispersion, but does some grinding as well It uses three rollers of different speeds and directions to cause the sheer force between them to disperse and grind particles The threeroll mill is used to disperse material within a media, which is usually some type of semiviscous material such as creamThreeroll mill selection tips Processing Magazinenormal time to prepare samples is from two to ten seconds A safety switch located in the lid prevents accidental operation of the mill with the lid removed The KN 295 Knifetec™ is equipped with a grinding chamber cooling feature which enables it to be connected to a cold water tap or other laboratory chilling devicesMill Collection fossanalytics