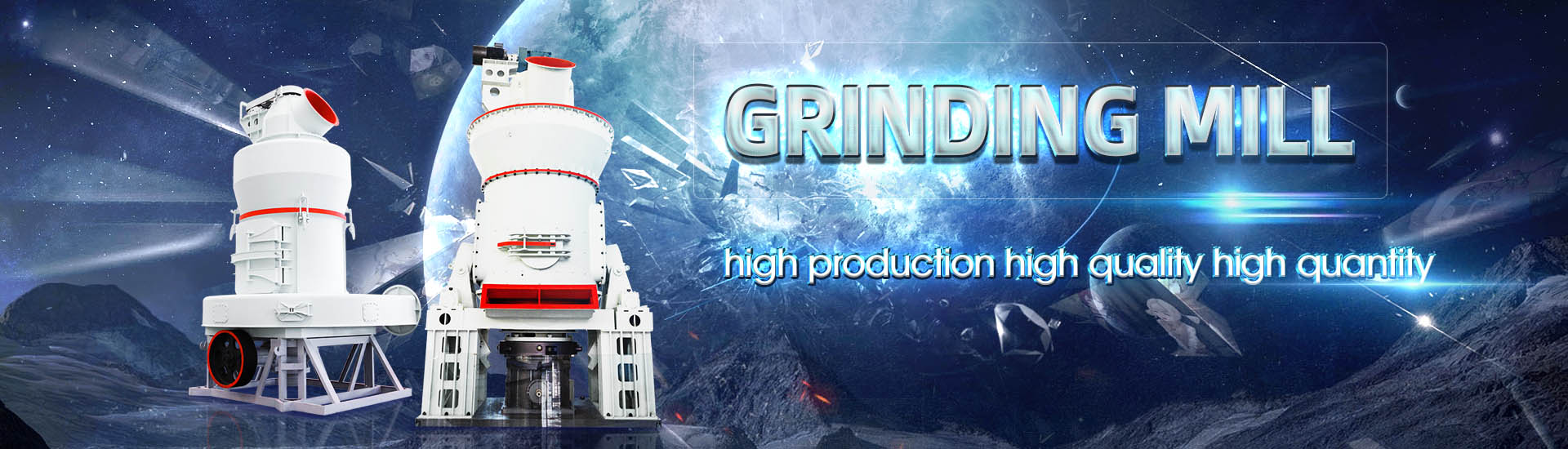
Simple limestone gypsum desulfurization technology plan
.jpg)
环境综合项目工程设计烟气脱硫 百度文库
This design is to introduce the system of dust removal and desulfurization process of each subsystem and equipment layout As for the FGD system,mainly introduces the process and 2022年1月15日 Cui et al proposed a combination of limestonegypsum wet flue gas desulfurization (WFGD) and wet condensation desulfurization technology for enhanced Summary of research progress on industrial flue gas 2009年10月1日 In this study, a desulfurization experiment was performed in a bubbling reactor to investigate the effects of adding organic acids, such as formic, acetic, propionic, lactic, oxalic and adipic New LimestoneGypsum Flue Gas Desulfuization The wet limestonegypsum flue gas desulphurization (FGD) process is the most widely used because of its high desulphurization performance and ease of obtaining aNew LimestoneGypsum Flue Gas Desulfuization Technology
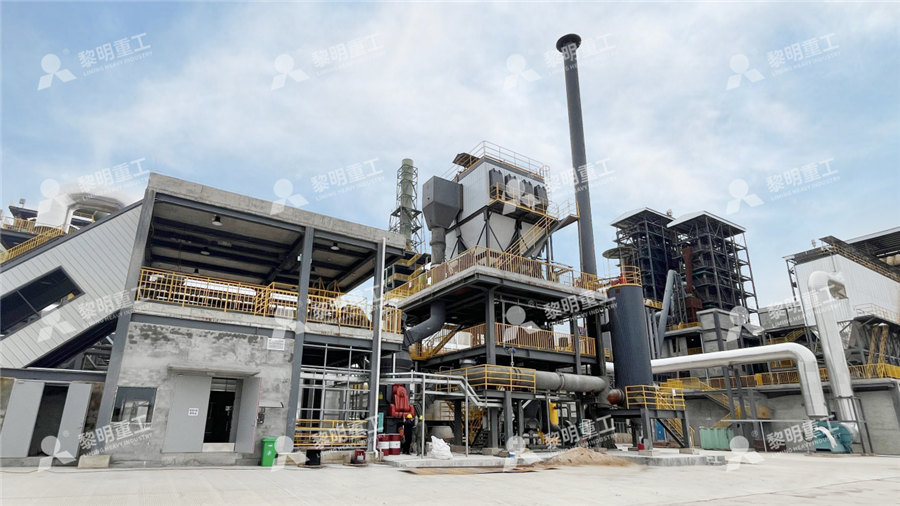
Enhancing the recovery of gypsum in limestonebased wet flue
2017年7月1日 Desulfurization tests show greater performance in terms of gypsum production SO 2 removal efficiency compared to the limestone treated with a traditional mill Multicriteria Wet scrubbers are used in utilities, paper mills, and chemical plants to remove sulfur dioxide (SO 2) and other pollutants from gas streams Undesirable pollutants are removed by contacting Lime / Limestone Wet Scrubbing System for Flue Gas Desulfurization2021年11月1日 This method is the most used desulfurization method because of its high desulfurization efficiency (90%–98%), large capacity, low cost, and easy recovery of by Production and resource utilization of flue gas desulfurized 2020年11月11日 Wet flue gas desulfurization was simulated to improve gypsum production using lowgrade limestone Highgrade limestone with 94 wt% CaCO 3 content is used for Modeling of the wet flue gas desulfurization system to utilize low
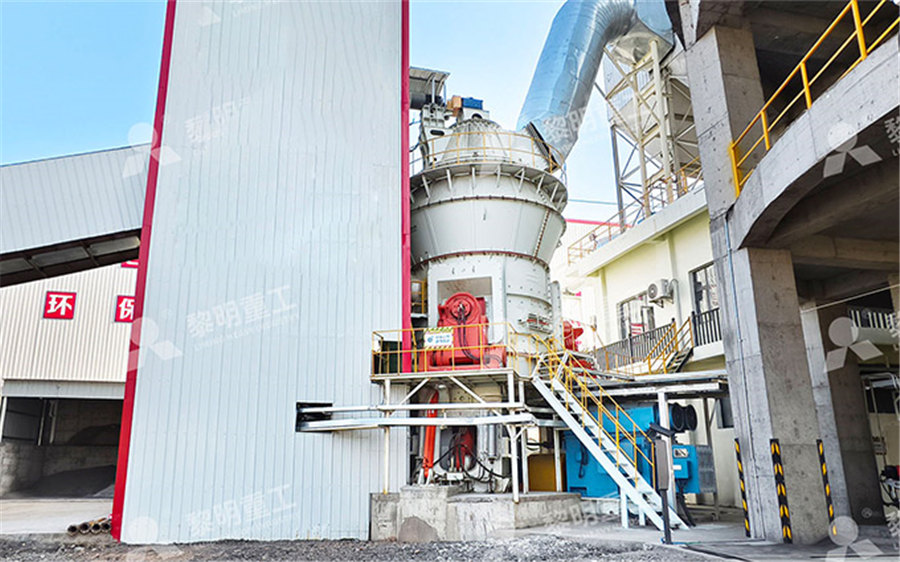
New LimestoneGypsum Flue Gas Desulfuization Technology
Abstract: A new wet FGD processes which SO 2 was absorbed in the spray tower using granular limestone simultaneously adding acetic acid had been proposed The main difference 2021年2月1日 In this study, we show that the current desulfurization technology of wet limestone flue gas desulfurization, which has more than 90% of the market share in China, significantly contributesLimestoneGypsum Wet Flue Gas Desulfurization 2019年3月30日 The maximum efficiency of wet limestonegypsum desulfurization can reach 99%, which basically ensures that the SO 2 concentration in the flue gas can meet the requirements of Chi na Air Pollutant(PDF) Progress of Desulfurization and Denitration Technology of Advances in Engineering Research, volume 112 4th International Conference on Renewable Energy and Environmental Technology (ICREET 2016) Optimization of Limestonegypsum Wet Flue Gas Desulfurization System Jing Han, (PDF) Optimization of Limestonegypsum Wet Flue
.jpg)
Current Status of Zero Liquid Discharge Technology
2024年3月20日 Desulfurization wastewater is industrial wastewater with a high salt content, high metal ions, and high hardness produced by flue gas desulfurization of the limestonegypsum method in coalfired power plants To date, limestonegypsum has been the most widely used sintering flue gas desulfurization technology in China's steel industry In order to demonstrate the application status, this paper stated the current desulfurization situation of Baosteel, Meishan Steel, Xiangtan Steel, Zhang steel Process of limestonegypsum obtained in these steel companies is playing an Study on the LimestoneGypsum Sintering Flue Gas Desulphurization A concise algorithm for calculating absorption height in spray tower for wet limestone–gypsum flue gas desulfurization Jie Zhu, Shichao Ye⁎, Jie Bai, Zhenyuan Wu, Zhenhua Liu, Yunfeng Fuel Processing Technology ResearchGate2022年1月15日 Wet desulfurization technology includes limestonegypsum desulfurization, dualalkali desulfurization, magnesium oxide desulfurization, zinc oxide Prospects Based on the study of dry desulfurization, semidry desulfurization, and wet desulfurization, the research progress of various desulfurization processes, mass transfer mechanisms and process parameters are Summary of research progress on industrial flue gas desulfurization
.jpg)
Enhancing the recovery of gypsum in limestonebased wet flue
2017年7月1日 Among the reasons for the success of the wet FGD system, there is the possibility of recovering a new product to be allocated on the market namely gypsum (He and Lee, 2014)In fact, the synthetic gypsum suitable for several applications such as wallboard manufacturing is the byproduct of the SO 2 scrubbing process for scrubbers using lime or Adding 1030 mmol/L acetic acid, degree of desulphurization was increased to 95% and the limestone utilization was enhanced to 935%, comparison with fine limestone, the desulphurization efficiency and limestone utilization were respective 88% and 929% at the same operating conditions Adding organic acid, buffer capacity of system was enhancedNew LimestoneGypsum Flue Gas Desulfuization Technology2021年3月5日 At present, the continuous accumulation of the flue gas desulfurization (FGD) gypsum in steel plants leads to the serious environmental issues and resource waste To achieve green and sustainable development for the steel industry, it is significant to improve the usage of byproduct gypsum Employing the sintering FGD gypsum, ferric oxide, and graphite carbon Preparation of calcium ferrite by flue gas desulfurization gypsumIn this paper, a concise model for wet limestone–gypsum flue gas desulfurization system with spray tower has been presented, aiming at the prediction of the absorption height in a spray towerSchematic diagram of the limestonegypsum spraying desulfurization
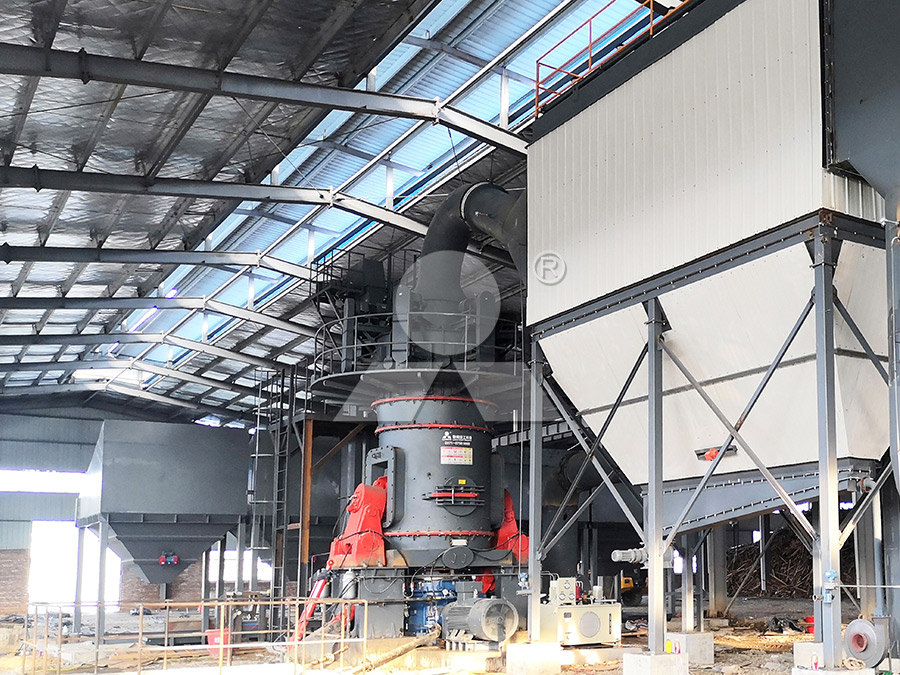
New LimestoneGypsum Flue Gas Desulfuization Technology
The wet limestonegypsum flue gas desulphurization (FGD) process is the most widely used because of its high desulphurization performance and ease of obtaining a2019年8月9日 The limestone gypsum wet flue gas desulfurization technology was currently the m ost widely used in the wo rld with high reliability, high desulfurization efficiency, suitable types of wide Study on Biological Treatment of Limestonegypsum The desulfurization gypsum in thermal power plants is mainly produced by the limestonegypsum wet desulfurization process The method uses limestone as a desulfurizing agent, and sprays the absorbent slurry into the tower to fully Desulfurization gypsum uses and properties take it 2020年8月15日 Since the “Eleventh FiveYear Plan” period, the construction of flue gas desulfurization and denitrification facilities for coalfired power plants have been accelerated to control the emissions of sulfur dioxide (SO 2) and nitrogen oxides (NO X) and thus to address the issue of acid rain in ChinaAccording to the goal of the “Thirteenth FiveYear Plan for Energy Comprehensive evaluation of flue gas desulfurization and
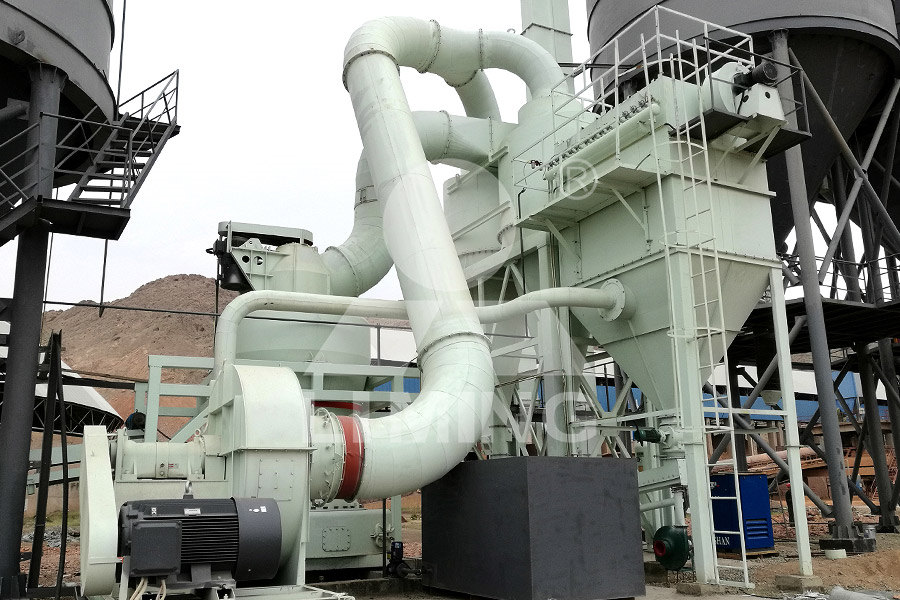
(PDF) A Review of Desulfurization Technology using Limestone in
2015年10月30日 This study investigated that status of domestic and international furnace desulfurization and desulfurization characteristics of limestone for fluidized bed use depending on the technology for 2019年6月1日 Applying the advanced technology of CPS to the (WFGD) system can improve the whole system operation efficiency and reduce energy waste, and has good utilization value for promoting the intelligent upgrade of the factory The limestonegypsum wet flue gas desulfurization system has been widely used due to its remarkable desulfurization effect, but Limestonegypsum wet flue gas desulfurization based on Cyber 2019年12月1日 According to the US Energy Information Administration's statistics, in the 2006–2016 period, approximately 42% of the electricity consumed in the USA was produced by coal combustion (US Energy Information Administration, 2018)The coal combustion process generates various types of residues such as fly ash, bottom ash, boiler slag, flue bed Recent advances in flue gas desulfurization gypsum processes 2013年8月20日 The limestonegypsum wet desulfurization process, the most mature technology, the most applications, the most reliable operation in the world, may have rate of desulfurization of more than 90%Application and Development Trend of Flue Gas Desulfurization
.jpg)
Study on the LimestoneGypsum Sintering Flue Gas
2014年8月1日 To date, limestonegypsum has been the most widely used sintering flue gas desulfurization technology in China's steel industry In order to demonstrate the application status, this paper stated 2010年12月1日 The main task of limestone/gypsum WFGD system is to remove SO 2 from flue gas and to produce gypsum product High efficiency of WFGD system has been achieved through a large amount of studies on A simple realistic modeling of fullscale wet limestone FGD unitshas developed technology for desulfurization of flue gas using a wet lime/limestone gypsum process as a means of reducing sulfur dioxide (SO2) emissions, and has applied it in the treatment of flue gas from thermal power plants ever since 1972 As of July 2004, a total of 167 desulfurization systems using this wet lime/limestone gypsum processAdvanced Technology of Flue Gas Desulfurization (FGD)In the 1990s, the 3rd generation of wetprocess limestone/limegypsum flue gas desulfurization technology took shape, in which such unit was configured to integrate the prescrubber, scrubber and Application and Development Trend of Flue Gas Desulfurization
.jpg)
Basic characteristics and comprehensive utilization of
2020年7月14日 Fluegasdesulfurization gypsum (FGD gypsum) is an industrial b yproduct gypsum obtained by desulfurizing and purifying the f lue gas generated after combus tion of sulfurcontaining fuel (coal, oil,2022年7月9日 Limestonegypsum Wet Desulfurization Wastewater Shanshan Zhang, WU Qiaoling, JIN Yinjia et alImprovement of SalineAlkaline Soil via Flue Gas Desulfurization Gypsum and Safety Analysis of the Associated Heavy Metals Yanrong Fu, Kun He, Chunliang Zhou et alStudy on the Thermal Expansion Performance of Gypsum in the Application of SVXPXVHGDVFHPHQW Limestonegypsum Wet Desulfurization 2020年10月14日 The wet limestone/gypsum flue gas desulfurization (WFGD) technology has been attracting much interest, while handling with wastewater produced in WFGD is indispensable but difficultA novel drying tower technology for zero liquid discharge of 2015年1月31日 In this paper, a concise model for wet limestone–gypsum flue gas desulfurization system with spray tower has been presented, aiming at the prediction of the absorption height in a spray towerA concise algorithm for calculating absorption height in spray
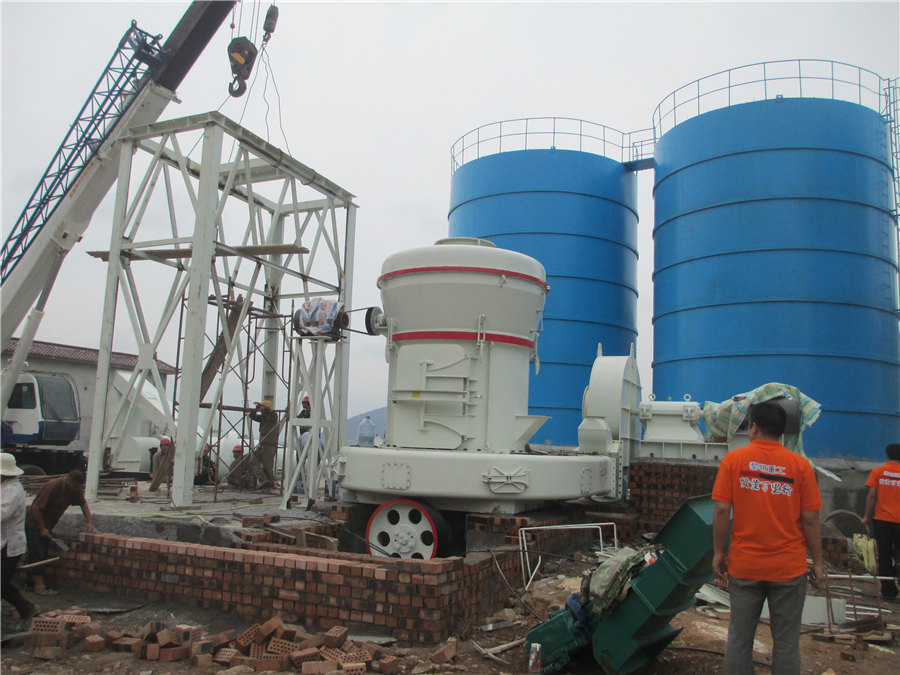
Modeling of the wet flue gas desulfurization system to utilize low
2020年11月11日 Wet flue gas desulfurization was simulated to improve gypsum production using lowgrade limestone Highgrade limestone with 94 wt% CaCO3 content is used for producing gypsum with 93 wt% purity, but owing to the resource depletion of highgrade limestone, lowgrade limestone should be replaced as an alternative However, lowgrade 2014年3月4日 Wet flue gas desulfurization (WFGD) simultaneously removes Hg and SO2 from coalfired power plant flue gas streams Hg0 reemission occurs when the dissolved Hg(II) is converted to a volatile form (PDF) Investigation on Mercury Reemission from LimestoneGypsum Wet Limestone is a key raw material in most FGD systems installed to control sulphur dioxide (SO 2) emissions This report attempts to address the availability of limestone for FGD and also the use of its byproduct, FGD gypsum Limestone is an abundant resource in India with total reserves of 200 billion tonnesFLUE GAS DESULPHURIZATION Centre for Science and In order to investigate the characteristics of fine particles formed during the limestone–gypsum desulfurization process, Qinxia Z, Zhaomei C, Chaojiong Z, Deshi Y (2012) Discussion on wet ESP technology and its application prospect in coalfired power plants Electr Power Environ Prot 28(4):24–26 Google ScholarFine Particle Characteristics from Limestone–Gypsum Desulfurization
.jpg)
(PDF) Progress of Desulfurization and Denitration Technology of
2019年3月30日 The maximum efficiency of wet limestonegypsum desulfurization can reach 99%, which basically ensures that the SO 2 concentration in the flue gas can meet the requirements of Chi na Air PollutantAdvances in Engineering Research, volume 112 4th International Conference on Renewable Energy and Environmental Technology (ICREET 2016) Optimization of Limestonegypsum Wet Flue Gas Desulfurization System Jing Han, (PDF) Optimization of Limestonegypsum Wet Flue 2024年3月20日 Desulfurization wastewater is industrial wastewater with a high salt content, high metal ions, and high hardness produced by flue gas desulfurization of the limestonegypsum method in coalfired power plants Current Status of Zero Liquid Discharge Technology To date, limestonegypsum has been the most widely used sintering flue gas desulfurization technology in China's steel industry In order to demonstrate the application status, this paper stated the current desulfurization situation of Baosteel, Meishan Steel, Xiangtan Steel, Zhang steel Process of limestonegypsum obtained in these steel companies is playing an Study on the LimestoneGypsum Sintering Flue Gas Desulphurization
.jpg)
Fuel Processing Technology ResearchGate
A concise algorithm for calculating absorption height in spray tower for wet limestone–gypsum flue gas desulfurization Jie Zhu, Shichao Ye⁎, Jie Bai, Zhenyuan Wu, Zhenhua Liu, Yunfeng 2022年1月15日 Wet desulfurization technology includes limestonegypsum desulfurization, dualalkali desulfurization, magnesium oxide desulfurization, zinc oxide Prospects Based on the study of dry desulfurization, semidry desulfurization, and wet desulfurization, the research progress of various desulfurization processes, mass transfer mechanisms and process parameters are Summary of research progress on industrial flue gas desulfurization 2017年7月1日 Among the reasons for the success of the wet FGD system, there is the possibility of recovering a new product to be allocated on the market namely gypsum (He and Lee, 2014)In fact, the synthetic gypsum suitable for several applications such as wallboard manufacturing is the byproduct of the SO 2 scrubbing process for scrubbers using lime or Enhancing the recovery of gypsum in limestonebased wet flue Adding 1030 mmol/L acetic acid, degree of desulphurization was increased to 95% and the limestone utilization was enhanced to 935%, comparison with fine limestone, the desulphurization efficiency and limestone utilization were respective 88% and 929% at the same operating conditions Adding organic acid, buffer capacity of system was enhancedNew LimestoneGypsum Flue Gas Desulfuization Technology
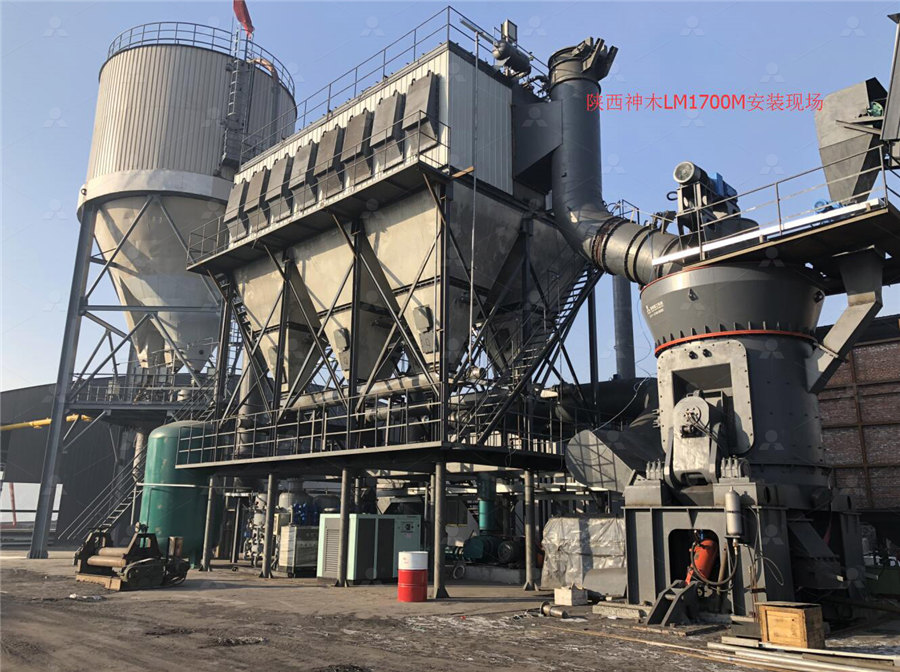
Preparation of calcium ferrite by flue gas desulfurization gypsum
2021年3月5日 At present, the continuous accumulation of the flue gas desulfurization (FGD) gypsum in steel plants leads to the serious environmental issues and resource waste To achieve green and sustainable development for the steel industry, it is significant to improve the usage of byproduct gypsum Employing the sintering FGD gypsum, ferric oxide, and graphite carbon In this paper, a concise model for wet limestone–gypsum flue gas desulfurization system with spray tower has been presented, aiming at the prediction of the absorption height in a spray towerSchematic diagram of the limestonegypsum spraying desulfurization