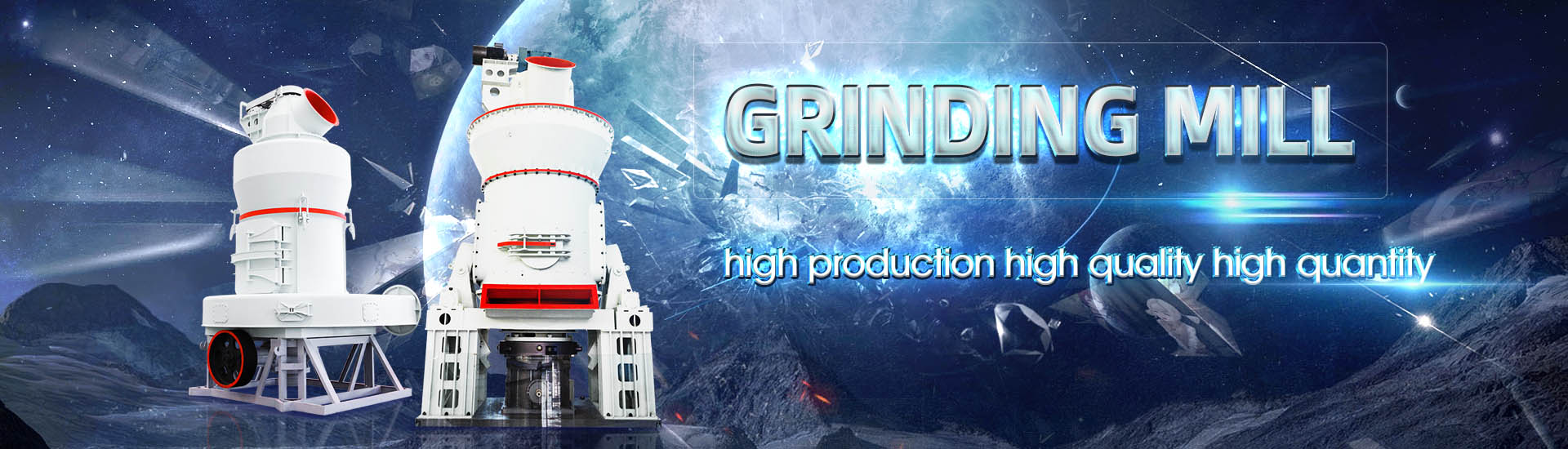
How much is the total investment required for cement grinding station
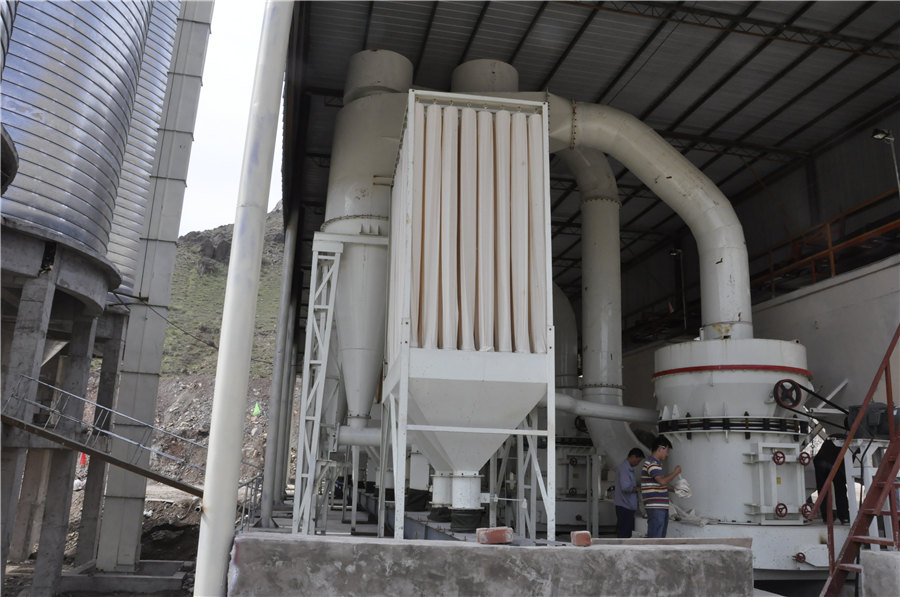
How much dose it cost to start a cement grinding plant?
2024年5月31日 For small and mediumsized cement grinding stations with an annual output of 100,000 to 1 million tons, the total investment is about 64 million to 129 million yuan The specific equipment model and price will vary depending on the supplier, technical specifications, According to the data we know, the total cost of a cement plant is estimated to be US$ 17,00How Much Does It Cost To Start A Cement Plant?What are the operating costs for setting up a cement manufacturing plant? What should be the pricing mechanism of the final product? What will be the income and expenditures for a Cement Manufacturing Plant Report 2024: Setup and Cost2024年4月4日 The cost of building a cement plant per million tonnes of annual capacity is a crucial factor that determines the total investment required for the project Detailed Unveiling Cement Manufacturing Plant Costs Osum
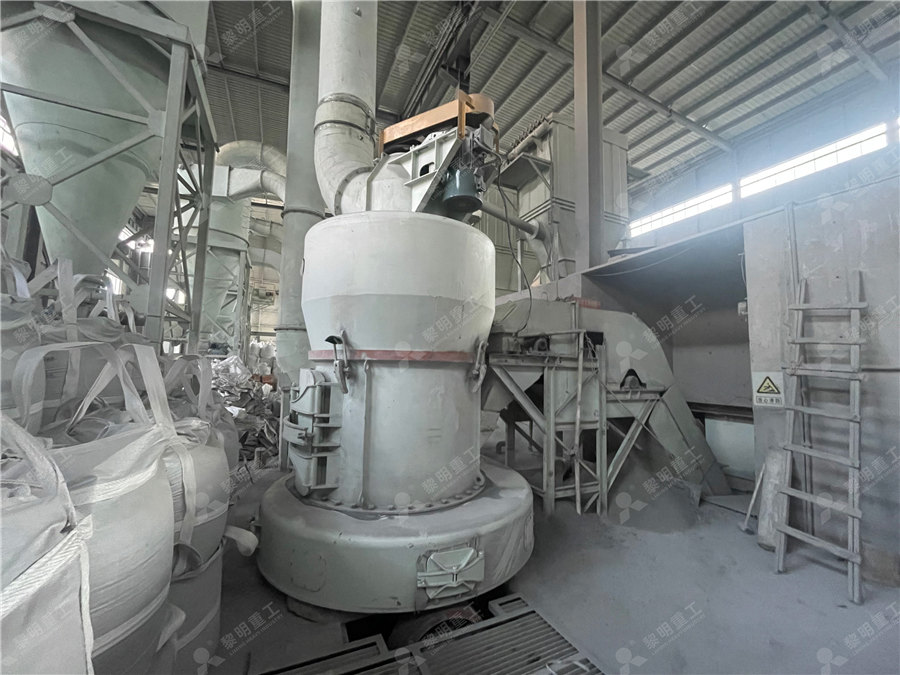
How to Start a Cement Factory
To answer these questions, investors must consider the local cement market size, cement prices, and their own investment capacity The larger the production scale of a cement factory, the higher the construction cost and production costAGICO Cement can supply cement grinding unit with features of simple process, easy operation, less equipment and low investment, energy saving and environmental protectionCement Grinding Unit Cement Grinding Plant2004年4月30日 Past comparisons of total installation costs for a ball mill with high efficiency separator versus a VRM have indicated the higher equipment costs associated with the roller Installed cost comparison for cement grinding systems2022年8月10日 Optimum fineness needs to be found for the type of raw materials, coal, and clinker to avoid overgrinding, which comes with ‘excess energy’ consumption and has a negative impact on quality and cost The Efficient grinding unit selection impacts profitability
.jpg)
Cement Grinding Cement Plant Optimization
Highly energy intensive unit operation of size reduction in cement industry is intended to provide a homogeneous and super fine (30004000 Blain) cement Grinding operation is monitored for 2022年2月18日 For reference, the grinding process represents a significant part of a cement plant’s electrical demand, in the range of 50 – 70% of the total integrated plant’s needs Therefore, limiting grinding power demand is a major World Cement Grinding Milling QAThe final manufacturing stage at a cement plant is the grinding of cement clinker from the kiln, mixed with 45% gypsum and possible additives, into the final product, cement In a modern cement plant the total consumption of electrical energy is about 100 kWh/t The cement grinding process accounts for approx 40% if this energy consumptionCEMENT GRINDING SYSTEMS INFINITY FOR CEMENT EQUIPMENT2024年4月4日 These expenses typically account for approximately 1520% of the total cost of sales (Cement Equipment) Careful management and optimization of these expenses are crucial for cost control Considering and analyzing these factors is vital for estimating the total investment required to start a cement manufacturing plantUnveiling Cement Manufacturing Plant Costs Osum
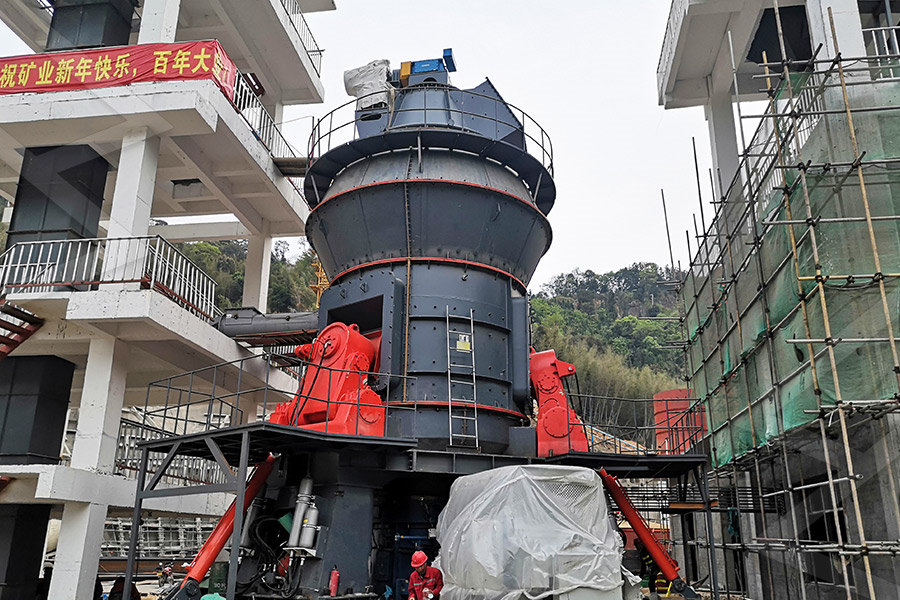
Key factors in setting up a cement plant Indian
2020年1月3日 According to Cement Manufacturers Association, India accounts for over 8% of the overall global installed capacity Regionwise, the southern region comprises 35% of the total cement capacity, followed by the northern, 2019年1月3日 Clinker grinding technology is the most energyintensive process in cement manufacturing Traditionally, it was treated as "low on technology" and "high on energy" as grinding circuits use more than 60 per cent of total energy consumed and account for most of the manufacturing cost Since the increasing energy cost started burning the benefits significantly, Clinker grinding technology in cement manufacturingThe production capacity of cement factories also varies greatly, ranging from 50 TPD to 10,000 TPD What kind of cement does the cement factory produce? What is the production scale? To answer these questions, investors must consider the local cement market size, cement prices, and their own investment capacityHow to Start a Cement Factory2022年8月10日 Therefore, producing cement with less energy is becoming a key element of profitability: as the grinding process consumes about 60 per cent of the total plant electrical energy demand and about 20 per cent of cement production variable costEfficient grinding unit selection impacts profitability Indian Cement

Global Projects: Cement capacity expansion to 2025
2021年12月21日 Joe Harder of OneStone Consulting looks at how the cement industry is expanding its cement and clinker capacities, despite the Covid19 pandemic and overcapacities in many countries, drawing on the findings of OneStone’s new multiclient market report Cement Projects Focus 2025 The global cement industry is investing in new, modern and efficient Advantages : It can make 1,000 tons to 6,000 tons of cement per day It can finish the jobs of grinding and packaging cement Case Description: Cement grinding station is one production unit of cement finished products, which doesn't include the last finished stage of the cement production processCement Grinding Station FTM Machinery2024年11月23日 Cement Extraction, Processing, Manufacturing: Raw materials employed in the manufacture of cement are extracted by quarrying in the case of hard rocks such as limestones, slates, and some shales, with the aid of blasting when necessary Some deposits are mined by underground methods Softer rocks such as chalk and clay can be dug directly by Cement Extraction, Processing, Manufacturing Britannica2024年11月22日 Startup Cost Average Amount Range (USD) Land and property acquisition: $1,000,000 $5,000,000: Equipment and machinery installation: $5,000,000 $20,000,000Cost Efficiency: How To Estimate Expenses For A Cement Plant
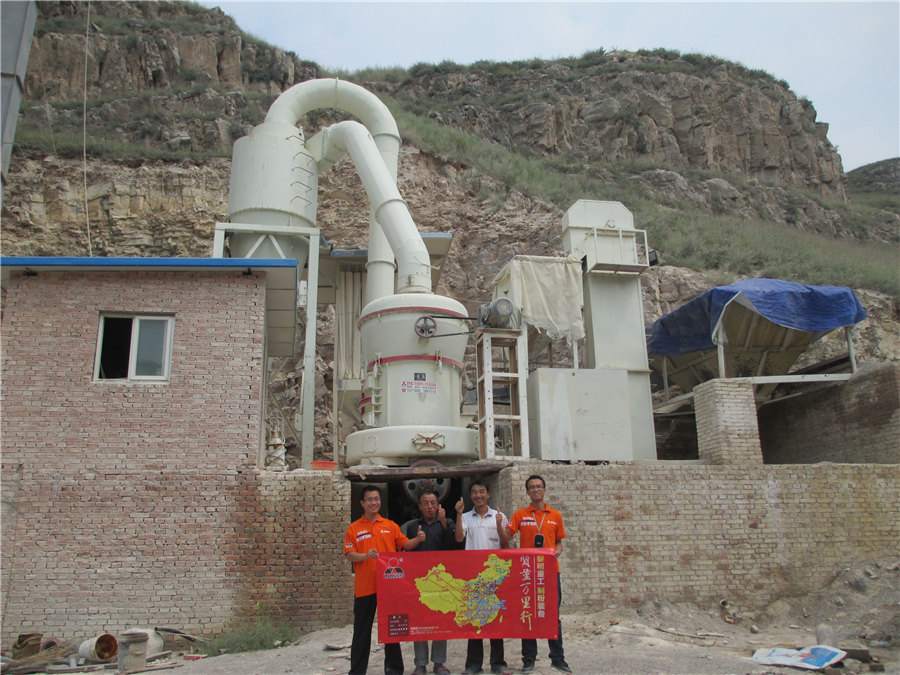
Cement Manufacturing Plant Report 2024: Setup and Cost
Report Overview: IMARC Group’s report titled “Cement Manufacturing Plant Project Report 2024: Industry Trends, Plant Setup, Machinery, Raw Materials, Investment Opportunities, Cost and Revenue” provides a complete roadmap for setting up a cement manufacturing plant It covers a comprehensive market overview to microlevel information such as unit operations involved, 2023年4月13日 Although here at A1 we usually don’t recommend concrete grinding as the first choice for concrete repair, we want to make sure you have as much information as possible about all available options in order to make the Concrete Grinding: Everything You Need to Know2020年8月25日 The Portland cement manufacturing process is representative of all types of cement limestone and clay are the main raw materials of cement making, the cement raw materials will be processed into a raw meal by Cement Production Process Cement Manufacturing The investment required to start a cement dealership business mainly varies depending on the size of your shop, It has a production capacity of over 35 MTPA and a network of over 170 cement plants and grinding stations across India Read more about ACC Cement Dealership 4How to start a Cement Business in India?
.jpg)
POWERING THE CEMENT INDUSTRY CEMBUREAU
CEMENT SECTOR POWERING THE CEMENT INDUSTRY Cement is an energyintensive industry, but currently, electricity accounts for circa 12% within the energy mix, while the rest is various fuels Total electricity consumption in a dry process is split into equal parts between raw material preparation and clinker production (25% each), then 43% for2016年3月1日 By combining the estimate for cement consumption in 2050 and the above anticipated improvements for alternative fuel use, clinker factor and efficiency, we can calculate the likely amount of coal required by the cement sector in 2050 2050 cement demand estimate = 57Bnt 2050 cement sector coal requirement* = 475 540Mt Value taken forward = 510MtCoal for cement: Present and future trends2015年1月31日 From hubandspoke model to split grinding; from singlegrinding solution to a combination of system solutions; and from energyintensive traditional ball mill to upgraded versions and use of pregrinders, the cement industry is shifting towards more energyefficient grinding solutions ICR trains its spotlight on the current technology trends The cement Grinding Solutions Indian Cement ReviewQuick return with minimal capital investment FREE To Ask! Skip to content +86 s about blog contact EN ES Menu Menu To meet the small and mediumsized clinker grinding demand of cement producers, process of the modular grinding station Need To Know: Modular Mobile Grinding Plant, Portable Grinding Plant Cement

(PDF) A study of different grinding aids for lowenergy cement
October 2023; Journal of the Southern African Institute of Mining and Metallurgy 123(9):471478Reducing CO2 emissions while producing enough cement to meet demand is a global challenge, especially since demand growth is expected to resume as the slowdown in Chinese activity is offset by expansion in other marketsCement IEA International Energy Agency2018年4月16日 Step 2: Calculate the grinding time by subtracting any stoppage time from the total shift time Step 3: Divide the square feet ground by the total grinding time So, if you grind 5,000 square feet in 7 hours, you would have a production rate of 714 square feet per hourConcrete Grinding Tools 101 Concrete Construction MagazineVertical roller mills and ball mills represent two clearly distinct technologies However, with proper adjustments to the operational parameters of the vertical roller mill almost identical cement properties can be achieved by the two mills Cement grinding Vertical roller mills VS ball mills
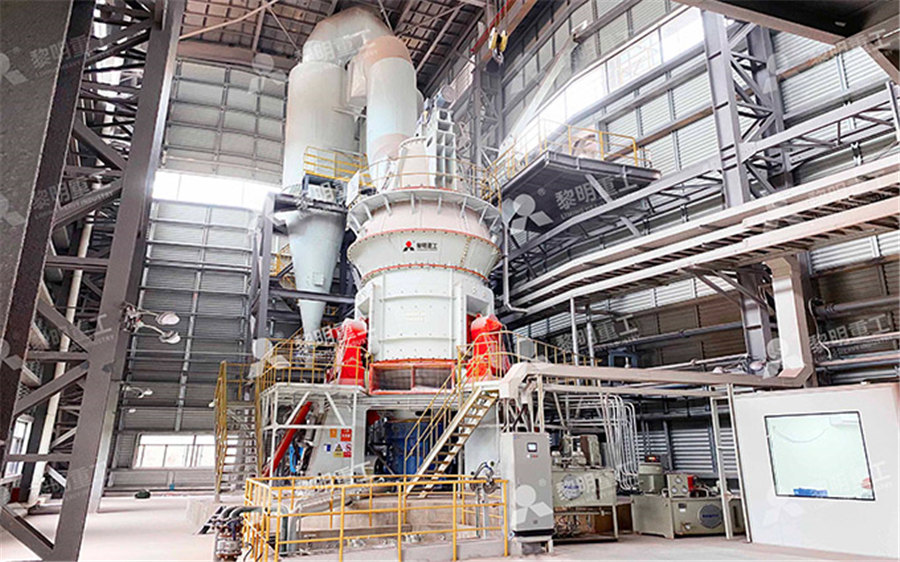
How much does it cost to start a cement factory?
2024年11月5日 In total, the cement factory investment requirements can exceed $2 million for smaller operations, while largerscale factories may require upwards of $10 million It's essential to create a detailed cement factory business plan to 2023年8月21日 ICR looks at the inner workings of grinding mills in the cement industry to understand the technological advancements that are reshaping the landscape against the foreground of sustainability Innovations to enhance the grinding processes are aimed at minimising their environmental footprint while increasing efficiency and performance In CuttingEdge Grinding Solutions Indian Cement Review2004年11月1日 Grinding occurs at the beginning and the end of the cement making process Approximately 15 tonnes of raw materials are required to produce 1 tonne of finished cementThe electrical energy consumed in the cement making process is in order of 110 kWh/tonne and about 30% of which is used for the raw materials preparation and about 40% for the final cement Cement grinding optimisation ScienceDirectPEC Consulting Group LLC 10123 Corporate Square Dr, St Louis, MO 63132 +1 314 8780123 peccgOPTIMIZATION OF CEMENT GRINDING OPERATION IN BALL MILLS
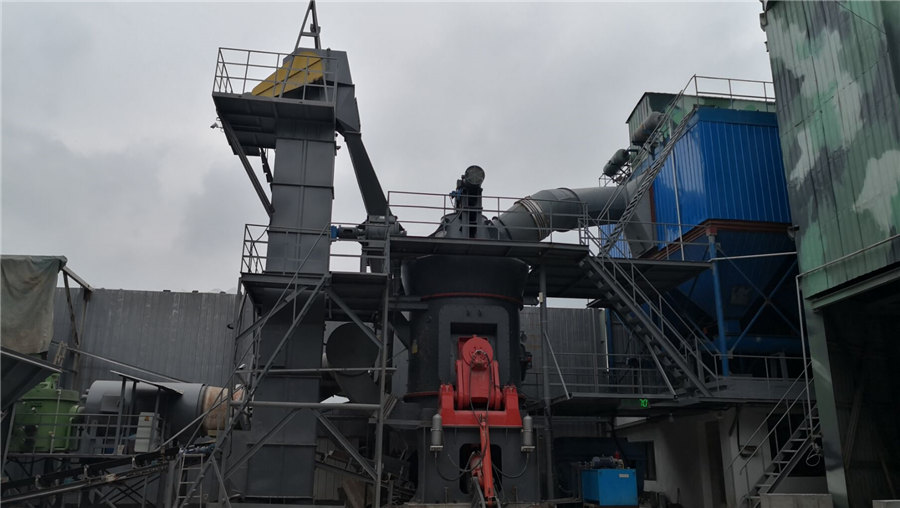
Energy Efficiency Improvement and Cost Saving Opportunities for Cement
About 97% of the cement produced in the US in 2010 was Portland cement, while masonry cement accounted for 3% of US cement output (USGS, 2012a) Cement plants are typically constructed in areas with substantial raw materials deposits (eg 50 years or longer) There were 110 operating cement plants in the US in 2010,2023年11月6日 The influence of the GAs incorporation in cement grinding on properties such as workability and setting times of the placed concrete and/or mortar has been covered in this review(PDF) Review of the Effect of Grinding Aids and Admixtures on the 25195tph clinker grinding plant, best option for start up at low cost Cement clinker grinding unit with ball mill, roll press or VRM 24×7 Consulting SupportClinker Grinding Unit for Sale, Buy Cement Grinding Station at 2022年6月30日 The cement is pumped pneumatically to storage silos Another station is designated for cement packing in paper bags and bulk dispatch Cement is usually packed in 20 – 50kg bags A bulk quantity of cement is transported via trucks, trains, or ships Emission of Dust During the Manufacturing of CementThe Manufacturing Process of Cement in Factory
46.jpg)
CEMENT GRINDING SYSTEMS INFINITY FOR CEMENT EQUIPMENT
The final manufacturing stage at a cement plant is the grinding of cement clinker from the kiln, mixed with 45% gypsum and possible additives, into the final product, cement In a modern cement plant the total consumption of electrical energy is about 100 kWh/t The cement grinding process accounts for approx 40% if this energy consumption2024年4月4日 These expenses typically account for approximately 1520% of the total cost of sales (Cement Equipment) Careful management and optimization of these expenses are crucial for cost control Considering and analyzing these factors is vital for estimating the total investment required to start a cement manufacturing plantUnveiling Cement Manufacturing Plant Costs Osum2020年1月3日 According to Cement Manufacturers Association, India accounts for over 8% of the overall global installed capacity Regionwise, the southern region comprises 35% of the total cement capacity, followed by the northern, Key factors in setting up a cement plant Indian 2019年1月3日 Clinker grinding technology is the most energyintensive process in cement manufacturing Traditionally, it was treated as "low on technology" and "high on energy" as grinding circuits use more than 60 per cent of total energy consumed and account for most of the manufacturing cost Since the increasing energy cost started burning the benefits significantly, Clinker grinding technology in cement manufacturing
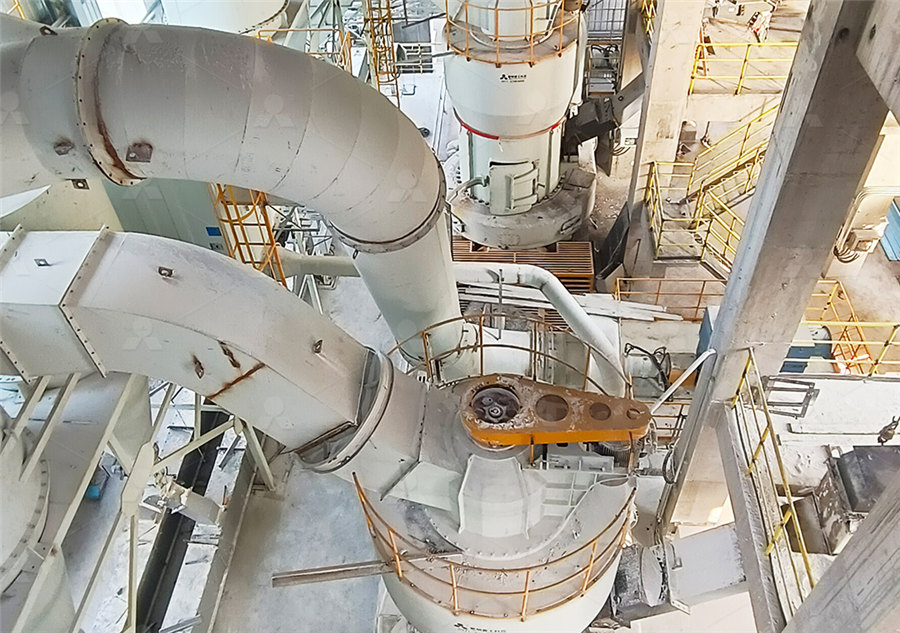
How to Start a Cement Factory
The production capacity of cement factories also varies greatly, ranging from 50 TPD to 10,000 TPD What kind of cement does the cement factory produce? What is the production scale? To answer these questions, investors must consider the local cement market size, cement prices, and their own investment capacity2022年8月10日 Therefore, producing cement with less energy is becoming a key element of profitability: as the grinding process consumes about 60 per cent of the total plant electrical energy demand and about 20 per cent of cement production variable costEfficient grinding unit selection impacts profitability Indian Cement 2021年12月21日 Joe Harder of OneStone Consulting looks at how the cement industry is expanding its cement and clinker capacities, despite the Covid19 pandemic and overcapacities in many countries, drawing on the findings of OneStone’s new multiclient market report Cement Projects Focus 2025 The global cement industry is investing in new, modern and efficient Global Projects: Cement capacity expansion to 2025Advantages : It can make 1,000 tons to 6,000 tons of cement per day It can finish the jobs of grinding and packaging cement Case Description: Cement grinding station is one production unit of cement finished products, which doesn't include the last finished stage of the cement production processCement Grinding Station FTM Machinery
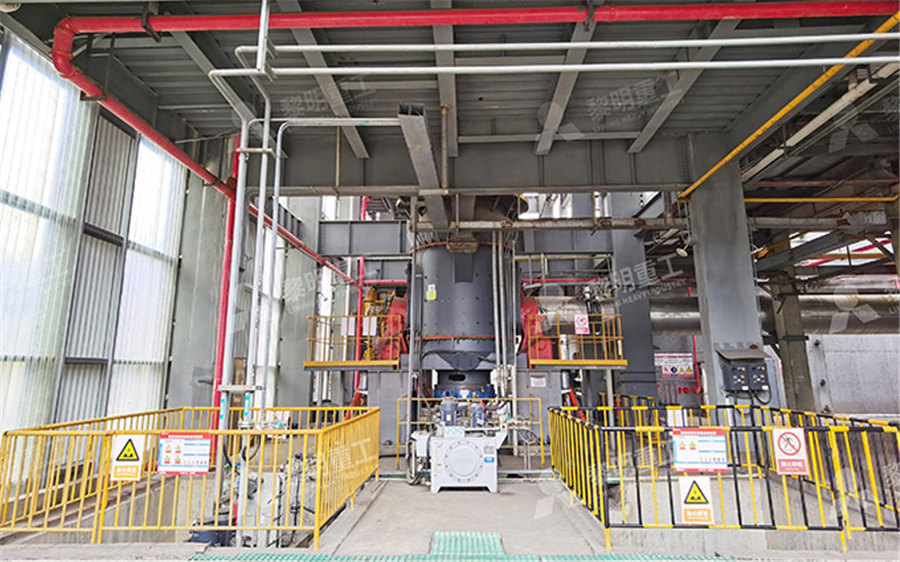
Cement Extraction, Processing, Manufacturing Britannica
2024年11月23日 Cement Extraction, Processing, Manufacturing: Raw materials employed in the manufacture of cement are extracted by quarrying in the case of hard rocks such as limestones, slates, and some shales, with the aid of blasting when necessary Some deposits are mined by underground methods Softer rocks such as chalk and clay can be dug directly by 2024年11月22日 Startup Cost Average Amount Range (USD) Land and property acquisition: $1,000,000 $5,000,000: Equipment and machinery installation: $5,000,000 $20,000,000Cost Efficiency: How To Estimate Expenses For A Cement Plant