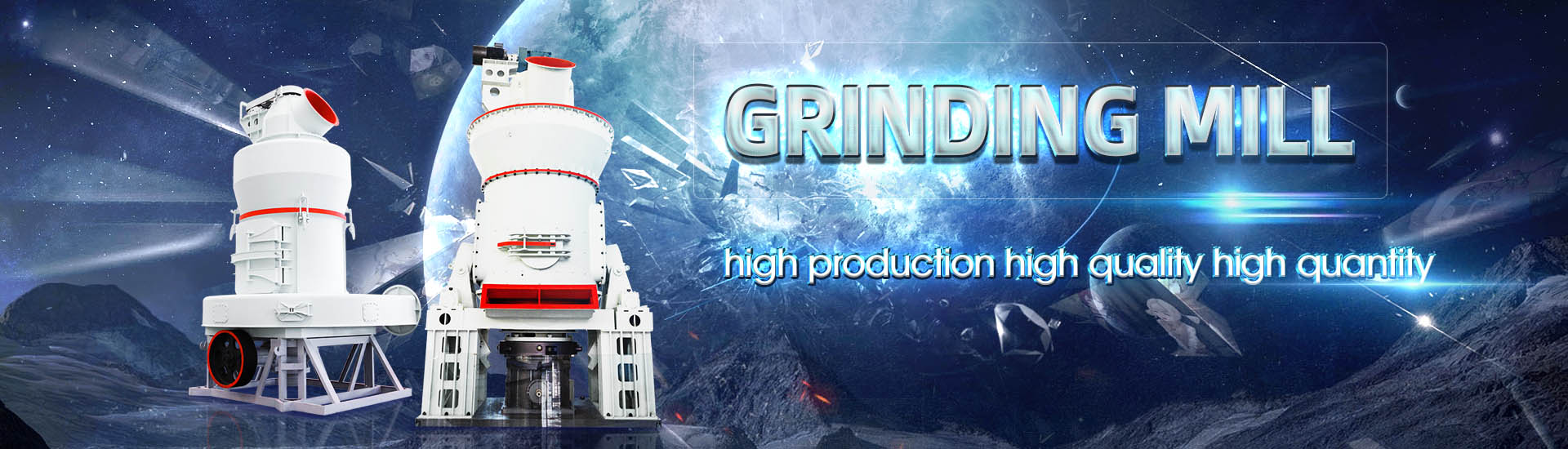
How is the tiger breaking position in the raw material workshop of the cement plant
.jpg)
The Cement Plant Operations Handbook International Cement
Providing a comprehensive guide to the entire cement production process from raw material extraction to the finished product, the industry’s favourite technical reference book is now fully 2015年12月9日 This paper presents an analysis of the cement manufacturing process, an outline of the pollutants generated from cement manufacturing (PDF) Cement Manufacturing ResearchGateTransporting the Raw Materials Workers transport the crushed raw materials to the cement plant, with the process varying significantly based on the proximity of the quarry to the manufacturing StepbyStep Guide to the Manufacturing of Cement PRACTICAL Calcination is the core portion of the process, in which huge rotary kilns come into play Inside, at 1400 degrees C, the raw material is transformed into clinker: small, dark gray nodules 34 Cement Production: How Cement Is Manufactured CEMEX UK
.jpg)
How cement is made Heidelberg Materials
There the rock is broken down to roughly the size used in road metalling The crushed material is transported into the raw material storage of the cement plant by conveyorbelts, cableways or together in a raw mill to a particle size of 90 micrometres, producing “kiln feed” Cement Plant: The Manufacturing Process worldcementassociation 1 Limestone (CaCO3) is taken from a Cement Plant: The Manufacturing Process 4 5 World Cement 1 天前 During this process, these materials partially fuse to form nodular shaped clinker by broking of chemical bonds of the raw materials and recombined into new compounds The Manufacturing of Portland Cement – Process and MaterialsThe cyclone preheating system Phase IV: Calcination The calcination is the core phase of the cement making dry process The calcination of the preheated raw meal takes place in the rotary kiln of the cement plant The rotary kiln is a How Is Cement Produced in Cement Plants Cement
.jpg)
Cement SpringerLink
2021年3月3日 Cement is produced by a hightemperature (about 1500 °C) reaction in a rotary kiln of carefully proportioned and blended ratios of lime (CaO), silica (SiO 2), alumina (Al 2 O 3), and iron oxide (Fe 2 O 3)The production of cement is a chemical process requiring an accurate blend of the previously cited four key organic oxides and the limitation of several undesirable 2020年9月22日 The use of cement and concrete, among the most widely used manmade materials, is under scrutiny Owing to their largescale use, production of cement and concrete results in substantial emission Environmental impacts and decarbonization strategies in the cement The production of raw cement involves the extraction and procurement of raw materials like limestone and clay or iron ore These materials are then crushed and finely ground to form the raw mix The raw mix is then subjected to hightemperature heating in a kiln, reaching temperatures around 1400°C in a process called clinkerExplore Raw Material Used For Cement Production JK Cement2023年11月1日 The development of industrial intelligence represented by Industry 40 provides a more competitive, resilient and sustainable development direction for increasingly complex industrial production processes [[2], [3], [4]]The impacts of Industry 40 on productivity, cost reduction, control over the production process, and customization of production exhibit a The digitization work of cement plant in China ScienceDirect
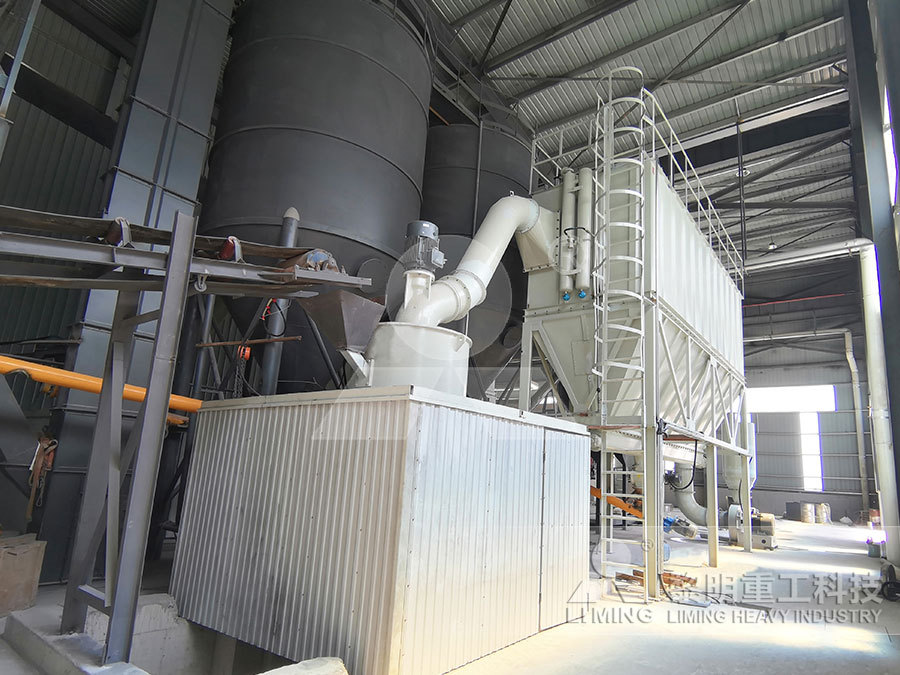
How cement is made Heidelberg Materials
Raw material preparation I: storage and homogenisation The crushed material is transported into the raw material storage of the cement plant by conveyorbelts, cableways or railways and also in exceptional cases with trucks Once there it is stored in blending beds and homogenisedSome cement plant quarries have highly variable raw material deposits Selective mining and preblending may be necessary to produce a chemically uniform kiln feed in these cases Online analyzers are available that can provide real time analyses of the entire raw material streamEverything you need to know about Kiln System Operations in Cement William Aspdin made what could be called ‘mesoPortland cement‘ (a mix of Portland cement and hydraulic lime)Isaac Charles Johnson further refined the production of ‘mesoPortland cement’ (middle stage of development), and claimed to be the real father of Portland cement In 1859, John Grant of the Metropolitan Board of Works, set out requirements for cement to be used in What is the manufacturing process of Portland Cement?as the cement plant machinery mainly includes rotating machines which are very heavy and installed in the open The rotating machinery in cement plants includes raw material crushers, clinker grinders and the kiln which is regarded produce cement The cement thus produced is stored in silos, packed in bags or transportedTHE NEED FOR EFFECTIVE RISK MITIGATION IN CEMENT
.jpg)
Optimizing Material Flow with Belt Conveyor in Cement Plant
2024年5月23日 Key Components of a System in Belt Conveyor in Cement Plant Cement Conveyor Belt: The Importance of Quality and Durability for Efficiency The cement conveyor belt is the backbone of a belt conveyor in cement plant operations It is responsible for the actual transportation of materials from one point to anotherManufacturing of cement involves various raw materials and processes The kiln is supported on the columns of masonry or concrete and rested on roller bearing in slightly inclined position at the gradient of 1 in 25 to 1 in 30 Manufacture of Cement Materials and Manufacturing Nonhydraulic cement sets and becomes adhesive due to carbonation You can use it for various construction projects, except underwater construction projects Hydraulic cement is the most commonly used cement Portland cement is a Cement: What is cement, Types Properties of Google 提供的服務無須支付費用,可讓您即時翻譯英文和超過 100 種其他語言的文字、詞組和網頁。Google 翻譯
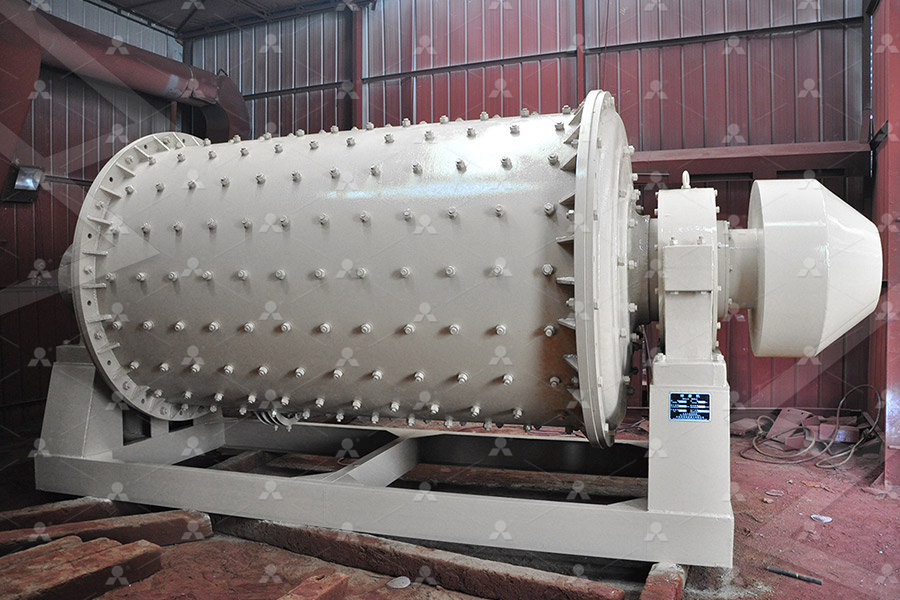
How Cement is Made Portland Cement Association
While each cement plant may differ in layout, equipment, and appearance, the general process of manufacturing portland cement is the same: The finely ground raw material enters the higher end of the kiln—a large cylindrical steel structure lined with special firebrickIn recent years, the tube mill has gradually been replaced by roller mill and other equipment, became the main equipment of cement grinding in cement cement manufacturing plant While in raw meal grinding, with the mature use of vertical mill and roller mill, the power consumption of grinding one ton raw meal has been reduced from 20 to 10 kWh, and even some people claim Raw Material Preparation in Cement Manufacturing Plant AGICOLimestone is the most important raw material in the manufacture of cement as it provides the main ingredient CaO It is blended with other raw materials such as clay, marl, shale to prepare a mix with the four main ingredients, CaO, SiO 2, Al 2O 3 and Fe 2O 3 in the correct proportionHOMOGENIZATION STRATEGY IN THE CEMENT INDUSTRY2019年1月11日 The cement industry is expected to post positive margins on decent price hikes over the months, falling raw material prices and marked drop in overall production costs, said an analysis of Care Ratings Wholesale and retail prices of cement have increased 119% and 124%, respectively, in the current financial yearThe role of gypsum in cement Indian Cement Review
.jpg)
Conveying and Storing in the Cement Industry Aumund
the Cement Industry 6 Clinker Transport 10 Conveying of Raw Meal, Cement and Additives 12 Transport of Raw Material, Clinker, Additives and Cement 14 Hopper Discharge and Crusher Feeding 16 Proportional Feeding, Proportional Discharge 17 Silo and Hopper Discharge 19 DustTight Transport 20 Material Reception and Transfer6 Raw material mill This takes places in vertical steel mill, which grinds the material through the pressure exerted by three conical rollers Which roll over a turning milling table Horizontal mills, inside which the material is pulverized by means of steel balls, are also used in this phaseCement Production: How Cement Is Manufactured CEMEX UKRaw Materials Crushing, Storing and Grinding Clinker calcination is the most crucial part of the whole process of cement manufacturing At this stage, ground raw materials will be sent into the cement kiln and be heated at a high temperature to produce chemical reactions with each other, eventually forming clinker In addition, clinkers that just complete the calcination will have a Cement Clinker Calcination in Cement Production Process AGICO Cement 2022年1月1日 This study uses linear programming to develop a methodology for selecting the best raw material mix in an ASCOM cement plant in Egypt In cement factories, this type adheres to Egyptian chemical LINEAR PROGRAMMING AS A TOOL TO DESIGN THE
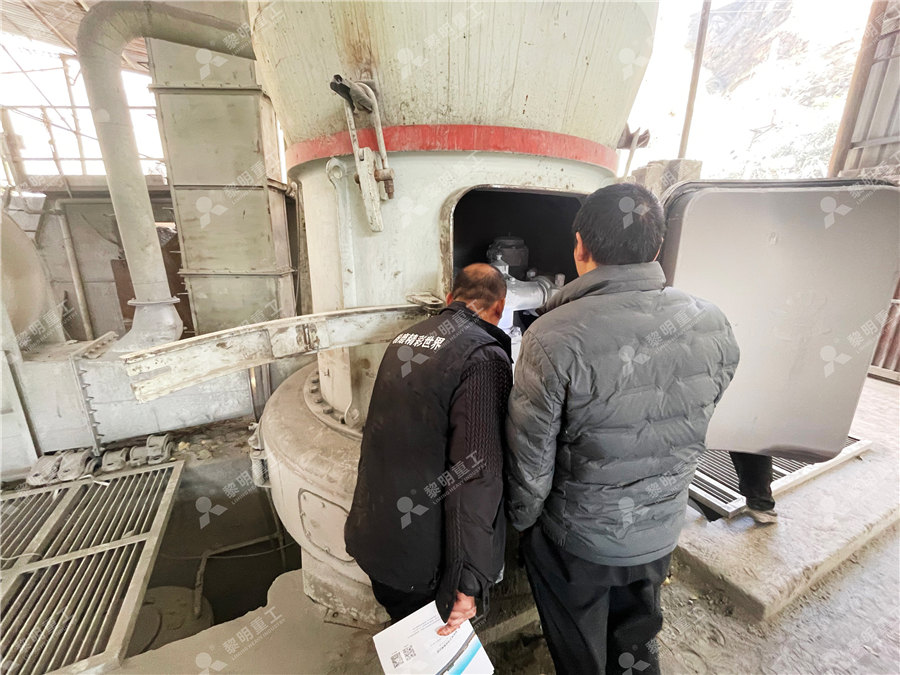
Cement Manufacturing Process: How the Cement is Made?
The preheated raw materials roll down the kiln and get heated to such an extent that the carbon dioxide is driven off with combustion gases The material is then heated to temperature of nearly 1400°C to 1500°C when it gets fused together The fused product is The raw material properties are critical to the performance of the The capital investment in a cement plant is substantial and it is high risk to entrust the performance of this investment to a and the nature of the liquid phase, as Everything you need to know about Kiln Burning SystemsCement conveyor refers to a belt conveyor in cement plant, which is necessary accessory equipment in the cement production line A belt conveyor is a kind of material handling equipment with strong adaptability, applied for conveying bulk density less than 167t / m³, it is mostly used for powder, granular, small lump materials, and bagged materials, such as sand, ore, coal, Cement Conveyor Belt Conveyor In Cement Plant AGICO2019年7月31日 Owing to differences in the raw materials available at each unit, the chemical composition of the produced cement varies significantly from one plant to another (Udara et al, 2019)Environmental Pollution by Cement Industry ResearchGate

Deep decarbonisation of industry: The cement sector Europa
Deep decarbonisation of industry: The cement sector Cement sector overview Cement is the binding agent of concrete, the most widely used construction material in the world The cement sector is a major greenhouse gas emitter, responsible for about 7% of CO 2 emissions globally (1), and about 4% in the EU2022年12月23日 Even if cement is a wellconsolidated material, the chemistry of cement (and the chemistry inside cement) remains very complex and still nonobvious What is sure is that the hydration mechanism plays a pivotal role in the development of cements with specific final chemical compositions, mechanical properties, and porosities This document provides a An Insight into the Chemistry of Cement—A Review MDPI2019年9月27日 There are various types of cement crusher on the market, including jaw crusher, cone crusher, hammer crusher, impact crusher, and etc AGICO Cement can provide all types of cement crusher Our cement crusher can fully crush the raw material, reduce feed size into the mill, and increase the reaction of raw material in the following cement manufacturing process, Cement Euipment Overview Cement Making Machines Cement PlantCement Bonded Board with the use of Tiger Grass as Raw Material were manufactured using 85:15, 90:10 and 95:5 cement: tiger grass proportion with a target board density of 1g/cc The boards were subjected to water absorption test and thickness swelling test for the physical properties; face screw holding test and modulus of rupture test for the mechanical propertiesTiger grass as cement bonded board UTILIZATION OF TIGER GRASS AS RAW
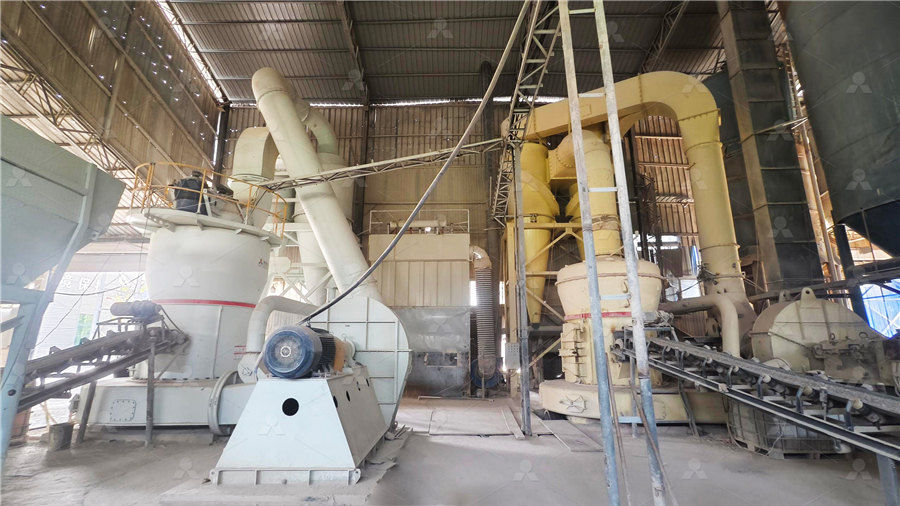
Cement Plant: The Manufacturing Process 4 5 World Cement
ground in a cement mill, which creates cement The cement is then packed and distributed to consumers The kiln feed is blasted in a cement kiln at a temperature of 1450oC, causing clinkering to occur (small balls of up to 25mm diameter) 6 5 Raw mill Preheated tower Cement storage silos Packing warehouse Raw material silos Limestone storageThe cyclone preheating system Phase IV: Calcination The calcination is the core phase of the cement making dry process The calcination of the preheated raw meal takes place in the rotary kiln of the cement plant The rotary kiln is a How Is Cement Produced in Cement Plants Cement 2021年3月3日 Cement is produced by a hightemperature (about 1500 °C) reaction in a rotary kiln of carefully proportioned and blended ratios of lime (CaO), silica (SiO 2), alumina (Al 2 O 3), and iron oxide (Fe 2 O 3)The production of cement is a chemical process requiring an accurate blend of the previously cited four key organic oxides and the limitation of several undesirable Cement SpringerLink2020年9月22日 The use of cement and concrete, among the most widely used manmade materials, is under scrutiny Owing to their largescale use, production of cement and concrete results in substantial emission Environmental impacts and decarbonization strategies in the cement
.jpg)
Explore Raw Material Used For Cement Production JK Cement
The production of raw cement involves the extraction and procurement of raw materials like limestone and clay or iron ore These materials are then crushed and finely ground to form the raw mix The raw mix is then subjected to hightemperature heating in a kiln, reaching temperatures around 1400°C in a process called clinker2023年11月1日 The development of industrial intelligence represented by Industry 40 provides a more competitive, resilient and sustainable development direction for increasingly complex industrial production processes [[2], [3], [4]]The impacts of Industry 40 on productivity, cost reduction, control over the production process, and customization of production exhibit a The digitization work of cement plant in China ScienceDirectRaw material preparation I: storage and homogenisation The crushed material is transported into the raw material storage of the cement plant by conveyorbelts, cableways or railways and also in exceptional cases with trucks Once there it is stored in blending beds and homogenisedHow cement is made Heidelberg MaterialsSome cement plant quarries have highly variable raw material deposits Selective mining and preblending may be necessary to produce a chemically uniform kiln feed in these cases Online analyzers are available that can provide real time analyses of the entire raw material streamEverything you need to know about Kiln System Operations in Cement
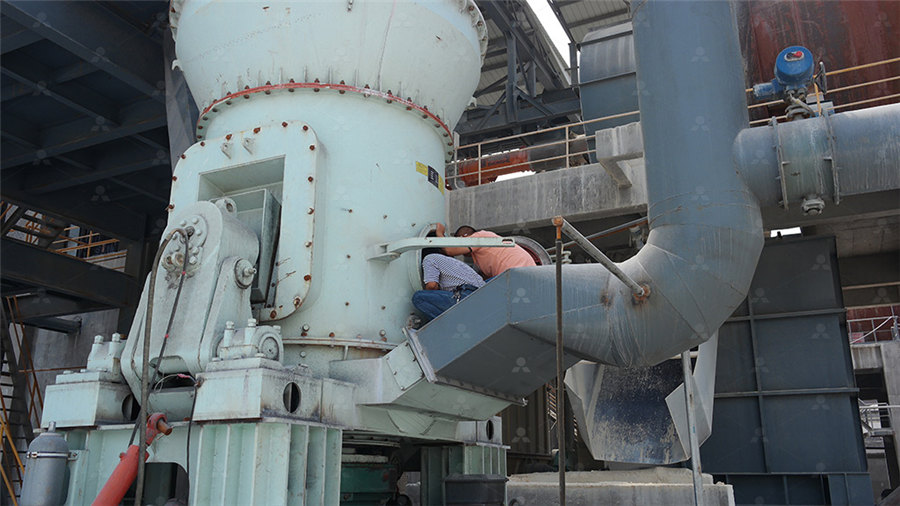
What is the manufacturing process of Portland Cement?
William Aspdin made what could be called ‘mesoPortland cement‘ (a mix of Portland cement and hydraulic lime)Isaac Charles Johnson further refined the production of ‘mesoPortland cement’ (middle stage of development), and claimed to be the real father of Portland cement In 1859, John Grant of the Metropolitan Board of Works, set out requirements for cement to be used in as the cement plant machinery mainly includes rotating machines which are very heavy and installed in the open The rotating machinery in cement plants includes raw material crushers, clinker grinders and the kiln which is regarded produce cement The cement thus produced is stored in silos, packed in bags or transportedTHE NEED FOR EFFECTIVE RISK MITIGATION IN CEMENT 2024年5月23日 Key Components of a System in Belt Conveyor in Cement Plant Cement Conveyor Belt: The Importance of Quality and Durability for Efficiency The cement conveyor belt is the backbone of a belt conveyor in cement plant operations It is responsible for the actual transportation of materials from one point to anotherOptimizing Material Flow with Belt Conveyor in Cement Plant