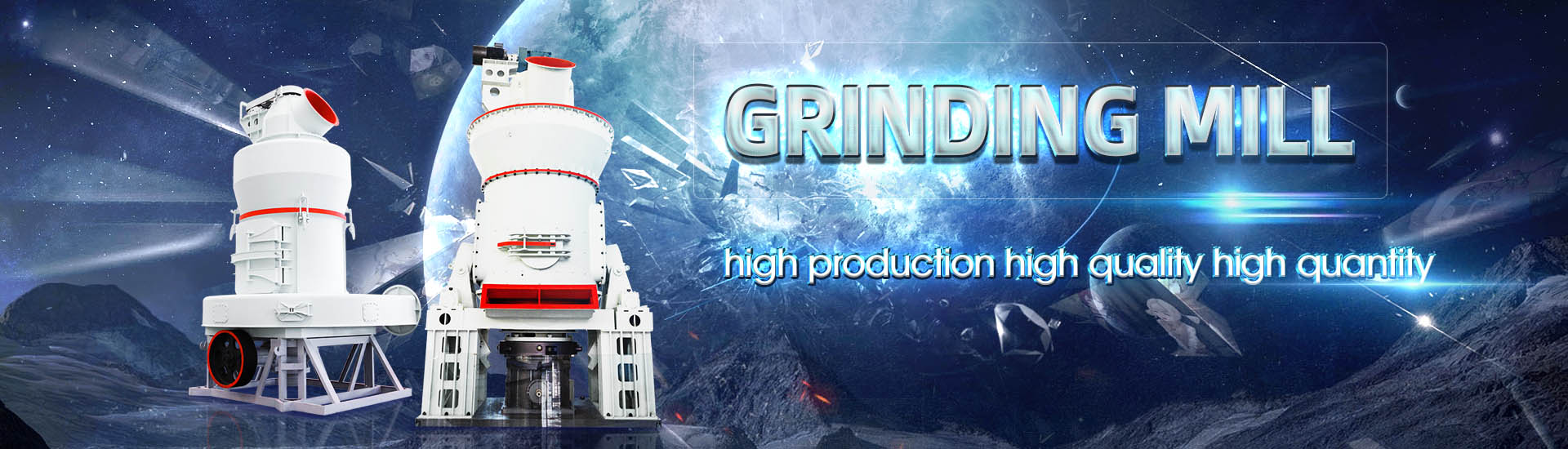
Calculation of ironmaking furnace process coefficient
.jpg)
Optimization of Raceway Parameters in Iron Making Blast Furnace
Reduction of fuel consumption, increase of the blast furnace capacity and productivity are the main factors, which determine the development of the iron making industry The decrease of 2022年9月1日 Hydrogen use in the blast furnace (BF) ironmaking process promises to mitigate the carbon footprint substantially This paper presents a numerical study on the effects of Numerical modeling and analysis of hydrogen blast furnace 2014年1月1日 As shown in Figure 13, an optimization model for a blast furnace was established based on nonlinear programming theory [54, 55] This model was based on the material Utilization coefficient optimization model for blast furnace iron 2023年7月18日 At present, the prediction model of a BF FR mainly focuses on the prediction of the coke ratio The methods used are mainly divided into traditional ironmaking mechanism Predictive Modeling and Control Analysis of Fuel Ratio in Blast
.jpg)
Consistent Optimization of Blast Furnace Ironmaking
2022年5月18日 To address this problem, a consistency optimization framework based on controllability assurance soft sensor modeling is proposed The method achieves the information extraction of uncontrollable variables in a process Optimization of ironmaking blast furnaces (BFs) must consider bottom and top operations This is done by a recently developed integrated BF model covering the BF below the burden surface Key operating parameters are focused, viz Optimization of Ironmaking Blast Furnace Operations 2021年7月25日 Optimization techniques are applied widely in iron and steel making process to solve complicated processrelated problems These methods and the models created through DataDriven Optimization of Blast Furnace Iron Making Process Optimization of ironmaking blast furnaces (BFs) must consider bottom and top operations This is done by a recently developed integrated BF model covering the BF below the burden surface Optimization of Ironmaking Blast Furnace Operations Using an
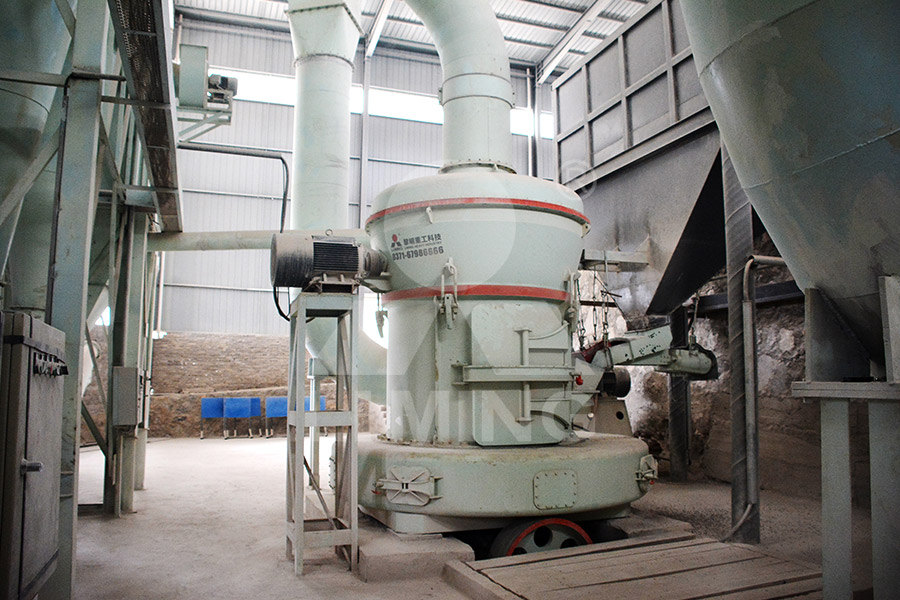
Comprehensive Numerical Modeling of the Blast
2016年4月8日 Blast furnaces are countercurrent chemical reactors, widely utilized in the ironmaking industry Hot reduction gases injected from lower regions of the furnace ascend, reacting with the descending burden Through Ironmaking Session 9 2 Düsseldorf, 27 June – 1 July 2011 2 tuyere conditions It can give recommendations to improve the performance of the blast furnaceNUMERICAL SIMULATION OF BLAST FURNACE SHAFT PROCESS2016年8月15日 Feng et al [69], [70], [71] applied constructal theory to the iron and steel production process, and conducted constructal optimizations for the insulation layer of steel rolling reheating furnace wall [69], the secondary cooling process of slab continuous casting [70], and the sinter cooling process based on exergy output maximization [71], respectivelyConstructal design of a blast furnace ironmaking process based However, the relative process calculation model is absent, which makes it difficult to determine the coke saving potential quantitatively and supply substantial guidance for practical production In this paper, a new process calculation model is established to study the influences of charging high reactivity coke in the blast furnace on theCALCULATION MODEL OF NEW BLAST FURNACE IRONMAKING PROCESS

Mathematical Modeling of the Blast Furnace Process
Dmitriev, A N Mathematical Modeling of the Blast Furnace Process Ekaterinburg: IMET UB RAS, 2019 On the basis of modern concepts, the results of many years of research on the mathematical modeling of the blast furnace process are presented A complex of mathematical models is described, including two2020年7月15日 Currently, approximately 95% of hot metal is produced by the blast furnace ironmaking process, which is also predicted to be the largest single ironmaking process until 2050 because of its advantages in production cost and efficiency Therefore, replacing fossilbased fuels with H 2 as the reductant is expected to relieve environmental concerns and, Blast Furnace Ironmaking an overview ScienceDirect TopicsCALCULATION MODEL OF NEW BLAST FURNACE IRONMAKING PROCESS BY USING HIGH REACTIVITY COKE1 Ying Sun2 Shengli Wu2 Lihua Zhang2 Yu Zhou2 Wei Shen2 Biyang Tuo2 Abstract The technology of using high reactivity coke in the blast furnace ironmaking process is proved to promote iron ore reduction in lump zone by both theoretical analysis andCALCULATION MODEL OF NEW BLAST FURNACE IRONMAKING PROCESS FIG 2 Blast furnace smelting process of VTM And a large steel production base was built in Panzhihua The content of TiO 2 can be stably produced for a long time under the condition of 25%, which Review and Thermodynamic Calculation of Gasbased Shaft Furnace
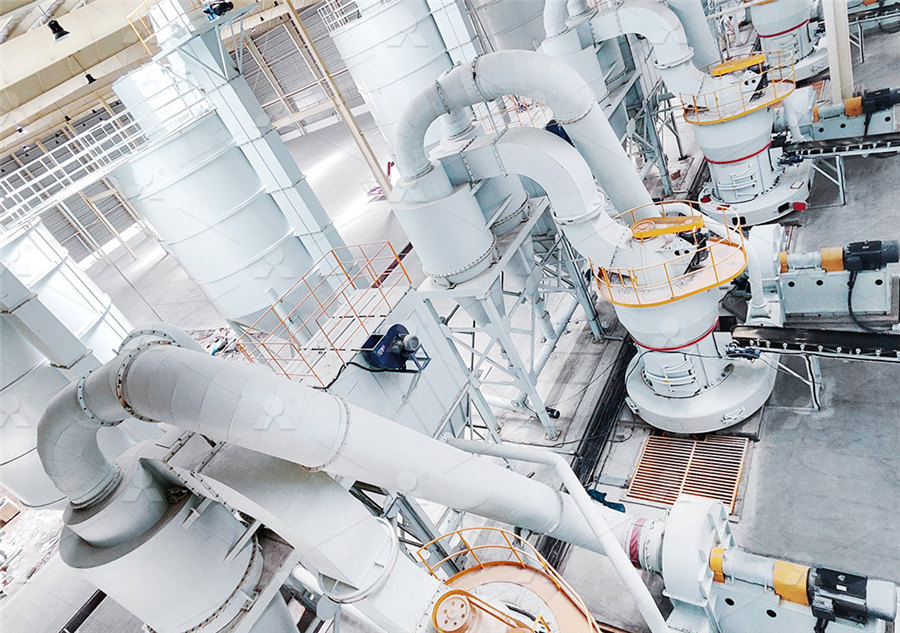
Numerical Investigation of Particle Size on the Performance of
2024年7月2日 Coke and ore sizes are important to the efficiency and stability of blast furnace (BF) operation in practice However, their selection is usually determined by experience and there is no systematic study on the effects of ore and coke sizes on BF operation This paper presents a numerical study on the multiphase flow and thermochemical behaviors inside the BF with 2022年2月10日 In the field of ironmaking, it is crucial to predict the gas utilization rate (GUR), which is strongly related to the product quality and the smooth operation of a blast furnace (BF) The present work proposes a model based on the multilayer perceptron (MLP) algorithm and datadriven to predict GUR after 1 h, 2 h, and 3 h, respectively First, the collected data are Machine Learning Modeling of Gas Utilization Rate in Blast Furnace2024年10月3日 Comparative calculations indicate that this process, relative to the conventional blast furnace ironmaking process, can diminish CO 2 emissions per ton of iron by 44–69% [12,13,14] It is expected to emerge as a viable technological alternative for the steel industry to implement the ‘dual carbon’ development strategyNumerical Simulation of the Inner Characteristics in a Hydrogen 2022年11月27日 Advanced manufacturing is a new trend for sustainable industrial development, and digital twin is a new technology that has attracted attention Blast furnace smelting is an effective method in the manufacturing of A Digital Twin Model of ThreeDimensional Shading
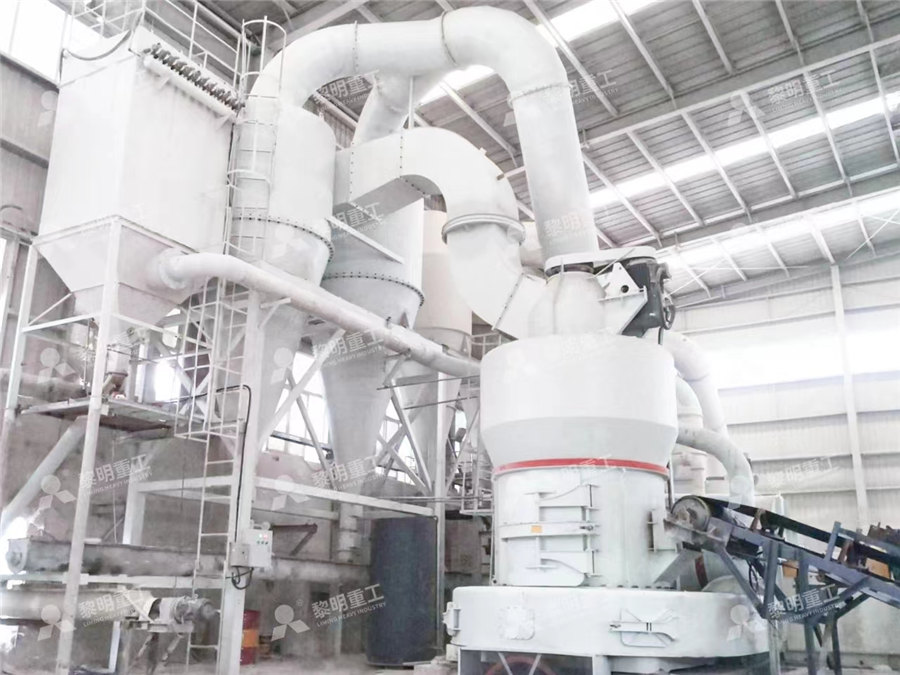
Parts of an ironmaking blast furnace plant
Download scientific diagram Parts of an ironmaking blast furnace plant from publication: Prediction and Explanation Models for Hot Metal Temperature, Silicon Concentration and Cooling Capacity 2023年11月23日 This paper develops a processlevel carbon emission calculation model for iron and steel enterprises through the carbon emission mechanism of the whole production process The relationship between material, energy and carbon flows is considered and combined The carbon emissions of enterprises are divided into industrial emissions and combustion CO2 emission accounting and emission reduction analysis of the 2023年7月18日 Blast Furnace Ironmaking Process Furnace charges (sinter, pellet, and lump) and coke fall into a BF from the throat, and the coke and charge alternately fill the BF shaft, as shown in Fig 1There are several tuyeres in the lower part of a BF belly, and hot blast (compressed preheated air) and pulverized coal are blown into a BF through themPredictive Modeling and Control Analysis of Fuel Ratio in Blast Furnace Blast furnace (BF) ironmaking is the most important technology by which iron is reduced from ore rapidly and efficiently It is currently the dominant process for producing iron in the steel industry that accounts for 7–9 % of CO 2 emissions from the global use of fossil fuels 1Optimization of Ironmaking Blast Furnace Operations Using an
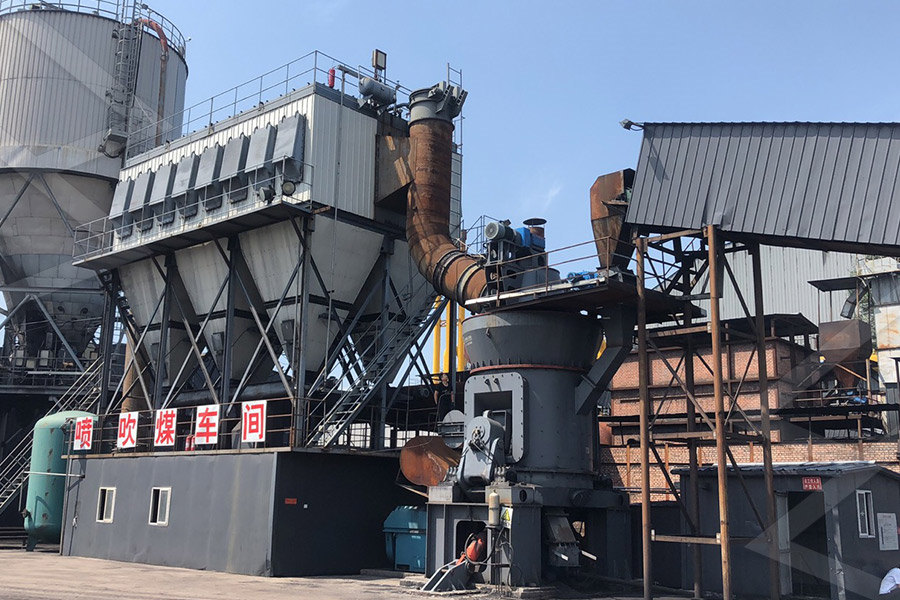
Development and Problems of Fluidized Bed Ironmaking Process:
2023年10月9日 Comprehensive control of greenhouse gas emissions and response to climate change are concerns of countries around the world to protect living homes The steel industry is responsible for over 10% of global CO2 emissions, with approximately 80% of these emissions coming from the ironmaking process Great efforts have been made in both blast furnace (BF) 2019年12月12日 A threedimensional (3D) parallel process model simulating ironmaking blast furnaces (BFs) has been developed using computational fluid dynamics (CFD) It explicitly describes the layered burden and cohesive zone (CZ), gas and liquid redistribution near raceways, trickling liquid flow in the CZ and dripping zone, and stockline variation The ThreeDimensional Modeling of an Ironmaking Blast Furnace Review and Thermodynamic Calculation of Gasbased Shaft Furnace Direct Reduction Ironmaking Weiming Luo1 1Energy and Power Engineering, Xi'an Jiaotong University, , China Abstract Different techniques have been used to study the reduction process of Review and Thermodynamic Calculation of Gasbased Shaft Furnace 2015年12月7日 A Novel Discrete Particle Model of Blast Furnace Ironmaking Process December 2015; w here h is heat transfer coefficient; V models for the calculation of the particle–particle and A Novel Discrete Particle Model of Blast Furnace Ironmaking Process
.jpg)
Research on Mathematical Model and Process Parameter
2024年7月24日 Production practices show that the energy consumption of the RHF direct reduction process is about 210 kgce/t, which is lower than 39531 kgce/t of the blast furnace ironmaking process [] RHF itself is the main equipment of RHF direct reduction process involving pellet reduction, gas combustion, heat transfer, and atmosphere control, [] therefore forming a Numerical calculations of the cohesive zone situation are based on the horizontal below burden probe measures, Table 4 shows the K 2 coefficient values radial distribution, Okosun T, Silaen A, Wu B Comprehensive Numerical Modeling of the Blast Furnace Ironmaking Process JOM 2016;68:1353–1362 doi: 101007/s1183701618914 Calculation of Coke Layers Situation in the Cohesive Zone of Blast Furnace2018年11月23日 MultiObjective Optimization of Cost Saving and Emission Reduction in Blast Furnace Ironmaking Process November 2018; Metals 8(12):979; DOI the blast furnace carbon loss calculation model is (PDF) MultiObjective Optimization of Cost Saving and 2020年12月11日 Studies have shown that the reduction of wustite is the limiting factor in the ironmaking process, whether in hydrogenbased shaft furnaces, hydrogenrich blast furnaces or smelting reduction vessels(PDF) Review and Thermodynamic Calculation of Gas

This is an electronic reprint of the original article This reprint may
researchers are working on adapting the existing blast furnace process to meet the new challenges Modeling has played a crucial role in new adaptations of the process The present review has been dedicated to historical developments of blast furnace modeling, which is a reason for the success and competitiveness of the blast furnace process2019年10月8日 Improving the burdening practice by optimization of raw flux calculation in blast furnace burden, Ironmaking Steelmaking, DOI: 101080/2019 To link to this article: https://doi Improving the burdening practice by optimization of raw flux 2004年5月17日 The aim of a burden calculation in the blast furnace process is to compute the amounts of burden materials to be charged for obtaining desired hot‐metal and slag composition Both the yield factor and distribution coefficient values were generally good and showed stable behaviour for repeated periods under similar operational Use of an optimisation model for the burden calculation for the b = / = / = ThreeDimensional Modeling of an Ironmaking Blast Furnace

Numerical Simulation of the 3D Asymmetric Inner States of an Ironmaking
2023年2月14日 The blast furnace (BF) still maintains its dominant role in the ironmaking process because of its high efficiency So far, this process occupies around 63 percent of the total hot metal (HM) production for steelmaking in the world [] In the operation of modern ironmaking BFs, the hot blast, usually oxygen enriched, is injected into the furnace at a high speed of over 200 2021年1月3日 The paper shows the use of novel modelling techniques adapted from ironmaking in the pyrometallurgical process of zinc production Firstly, regarding the purpose to determine the boundary Calculation of Coke Layers Situation in the Cohesive Zone of Blast Furnace2017年8月1日 The burden distribution process is an important and efficient measure to maintain the stable operation of the blast furnace An accurate burden distribution model will reveal the impact on the Development of Blast Furnace Burden Distribution Process Modeling Ironmaking Session 9 2 Düsseldorf, 27 June – 1 July 2011 2 tuyere conditions It can give recommendations to improve the performance of the blast furnaceNUMERICAL SIMULATION OF BLAST FURNACE SHAFT PROCESS
.jpg)
Constructal design of a blast furnace ironmaking process based
2016年8月15日 Feng et al [69], [70], [71] applied constructal theory to the iron and steel production process, and conducted constructal optimizations for the insulation layer of steel rolling reheating furnace wall [69], the secondary cooling process of slab continuous casting [70], and the sinter cooling process based on exergy output maximization [71], respectivelyHowever, the relative process calculation model is absent, which makes it difficult to determine the coke saving potential quantitatively and supply substantial guidance for practical production In this paper, a new process calculation model is established to study the influences of charging high reactivity coke in the blast furnace on theCALCULATION MODEL OF NEW BLAST FURNACE IRONMAKING PROCESS Dmitriev, A N Mathematical Modeling of the Blast Furnace Process Ekaterinburg: IMET UB RAS, 2019 On the basis of modern concepts, the results of many years of research on the mathematical modeling of the blast furnace process are presented A complex of mathematical models is described, including twoMathematical Modeling of the Blast Furnace Process2020年7月15日 Currently, approximately 95% of hot metal is produced by the blast furnace ironmaking process, which is also predicted to be the largest single ironmaking process until 2050 because of its advantages in production cost and efficiency Therefore, replacing fossilbased fuels with H 2 as the reductant is expected to relieve environmental concerns and, Blast Furnace Ironmaking an overview ScienceDirect Topics
.jpg)
CALCULATION MODEL OF NEW BLAST FURNACE IRONMAKING PROCESS
CALCULATION MODEL OF NEW BLAST FURNACE IRONMAKING PROCESS BY USING HIGH REACTIVITY COKE1 Ying Sun2 Shengli Wu2 Lihua Zhang2 Yu Zhou2 Wei Shen2 Biyang Tuo2 Abstract The technology of using high reactivity coke in the blast furnace ironmaking process is proved to promote iron ore reduction in lump zone by both theoretical analysis andFIG 2 Blast furnace smelting process of VTM And a large steel production base was built in Panzhihua The content of TiO 2 can be stably produced for a long time under the condition of 25%, which Review and Thermodynamic Calculation of Gasbased Shaft Furnace 2024年7月2日 Coke and ore sizes are important to the efficiency and stability of blast furnace (BF) operation in practice However, their selection is usually determined by experience and there is no systematic study on the effects of ore and coke sizes on BF operation This paper presents a numerical study on the multiphase flow and thermochemical behaviors inside the BF with Numerical Investigation of Particle Size on the Performance of 2022年2月10日 In the field of ironmaking, it is crucial to predict the gas utilization rate (GUR), which is strongly related to the product quality and the smooth operation of a blast furnace (BF) The present work proposes a model based on the multilayer perceptron (MLP) algorithm and datadriven to predict GUR after 1 h, 2 h, and 3 h, respectively First, the collected data are Machine Learning Modeling of Gas Utilization Rate in Blast Furnace
.jpg)
Numerical Simulation of the Inner Characteristics in a Hydrogen
2024年10月3日 Comparative calculations indicate that this process, relative to the conventional blast furnace ironmaking process, can diminish CO 2 emissions per ton of iron by 44–69% [12,13,14] It is expected to emerge as a viable technological alternative for the steel industry to implement the ‘dual carbon’ development strategy