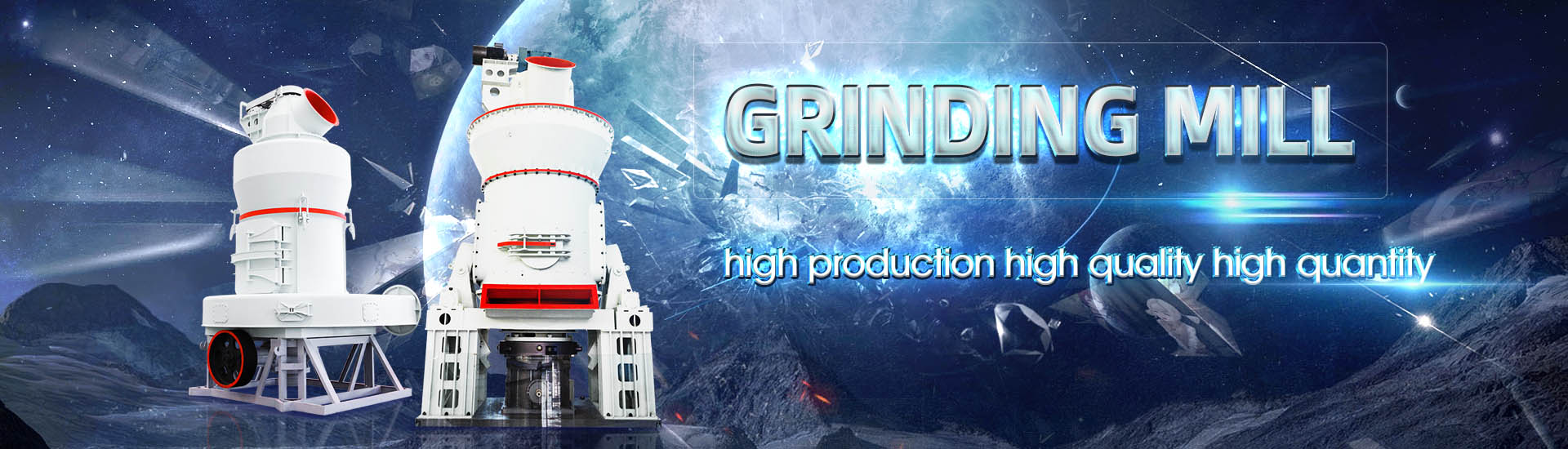
Cement plant feed rate
.jpg)
Kiln Feeding Cement Plant Optimization
In volumetric systems of metering, feed rate is assessed by volume of raw meal delivered than its actual weight For example, screw conveyors and rotary vane feeders with close tolerances between casing and screw with rpm control by variable speed drive (s)O2 and CO must be considered first before increasing fuel rate Feed Rate is generally maintained in a stable kiln operation When the control actions, like Clinkerization Cement Plant Optimization2022年10月20日 Cement production plants are one of the extremest CO2 emissions, and the rotary kiln is a cement plant’s most energyconsuming and energywasting unit Thus, enhancing its operation assessments (PDF) Modeling operational cement rotary kiln 2023年11月1日 Thus [[55], [56], [57]], the overall CO 2 capture rate is limited to around 60 % of the plant's total direct CO 2 emissions (for this share, the capture rate can reach up to 95 %) (for 20 % of total kiln feed) will be commissioned in a cement plant in Hannover, Germany to increase the TRL to 8 and prove longterm stabilityThe cement plant of tomorrow ScienceDirect
.jpg)
Cement Mill Feeding Cement Plant Optimization
Feed rate is generally controlled with the speed of weigh feeder belt, which is driven by a variable speed drive Feed rate is monitored and controlled by a control panel generally supplied with weigh feeder Provisions for drop test for calibration of weigh feeders are commonly available in cement plants to validate production figuresIn indirect metering system feed rate is determined by measuring cross section of material and rate at which it flows and taking into account bulk density of material Calibration and Drop Test Facilities Provisions for drop test for calibration of weigh feeders are commonly available in cement plants to validate production figuresRaw Mill Feeding Cement Plant OptimizationThe Cement Plant Operations Handbook is a concise, Kiln feed 4 Flames and fuels 38 1 Chemistry of combustion – 2 Fuels – 3 Physics of combustion – 4 Burner design – 5 Cement kiln burners – 6 Heat transfer – 7 Pollutant formation – 8 ModellingThe Cement Plant Operations Handbook International Cement Case Study: Consistency Improvements at a European Cement Plant A cement plant in Europe faced challenges with fluctuating kiln feed quality, leading to unstable kiln operations and high fuel consumption By implementing a realtime online analyzer combined with automated feed control systems, the plant reduced variability in feed composition Raw Mill and Kiln Feed Consistency: Key to Efficient Cement
.jpg)
Everything you need to know about Kiln System Operations in Cement
However, some cement plants in the past have suffered fires or explosions in cement kiln air pollution control devices (APCDs) Dobson (1974), with Factory Mutual Research, stated that between 1971 and the date of the article (1974) damage had been reported to nine ESPs in cement plants insured by Factory Mutualplant P roBlem: Modern cement producers utilize the dry process, where the raw materials (limestone, shale, etc) are finely ground and dried into the raw meal, which is then preheated to 900ºC prior to entering the cement kiln The feed rate of the raw meal must be closely linked with the kiln CEMENT KILN FEED CONTROL Rev 1CEMENT KILN FEED CONTROL REXA, Inc Electraulic™ Actuation2019年2月14日 The maximum sewage sludge feed rate should not be more than 5% of the clinker production capacity of the cement plant The wet sewage sludge is better for blending into wet process slurries and use in wet process kilns In the dry cement process, the sludge must be dried to reduce the moisture content below 1% before firingAlternative Fuels from Waste Products in Cement IndustryCement kiln dust was used successfully as a cover material instead of clay at a sanitary landfill located at a Californian cement plant (Crosby and others, 2000) In the early 1900s, cement plant employees began disposing of household waste at the company’s onsite landfillEverything you need to know about Cement Kiln Dust Generation
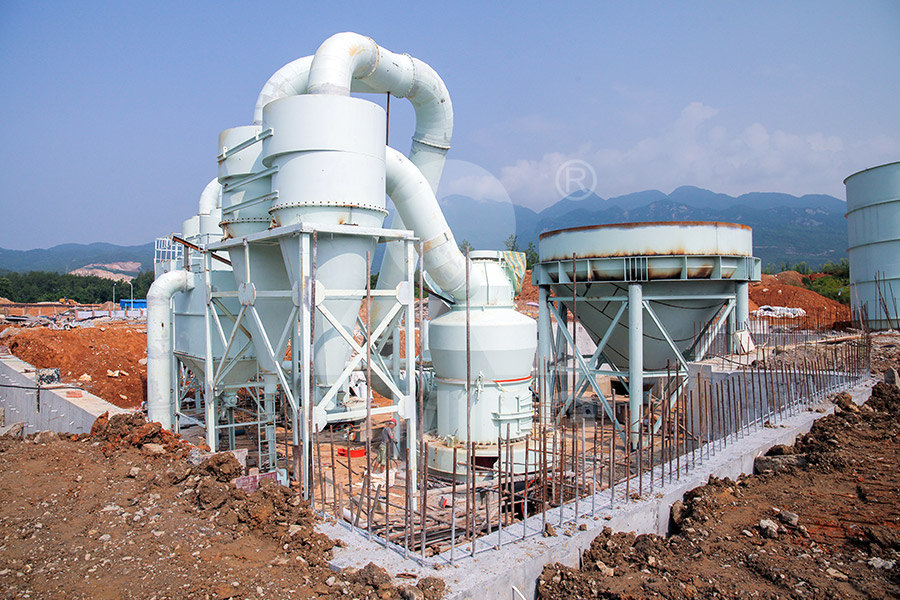
Modeling operational cement rotary kiln variables with
2022年10月20日 21 Dataset For exploring the relationships between kiln feed rate, and ID fan speed, and other operating variables, a dataset was collected from one of the preheater and rotary kiln (Clinker Baking unit) circuits (line 1) in the Ilam cement plant (Figure 1)The Ilam plant has two lines for cement production (5,300 t/d)Bucket elevator in cement plant, also called cement bucket elevator, is mechanical conveying equipment, mainly apply for the vertical lift of powder, particles like limestone, coal, gypsum, clinker, clay, raw meal, cement, TGD And Chain Type Bucket Elevator Cement Plant2024年6月3日 Uncertainties in feed flow rate, kiln air flow rate, tertiary air flow rate, and coal flow rate in the combustion sections of the plant are the subject of the study Initially, an Aspen Plus model of the kiln and calciner units of the cement plant was developed and converted into a dynamic mode to generate 700 data samples with 10% uncertaintyPrediction and optimization of emissions in cement manufacturing plant Chemical analysis of cement, generally on hourly basis Product fineness, Blain surface and 45micron residue Cement SO3, % Grinding aid usage, grams/tonne Cement moisture, % Production rate, tonnes/hour Operating hours as run factor in % Specific power consumption (SPC) kWh/tonne Specific Wear rate, g/t (checked during maintenance of mills)Cement Grinding Cement Plant Optimization

Clinkerization Cement Plant Optimization
Kiln feed rate fluctuations and composition inconsistency makes difficult to control free lime in clinker Five stagecyclones are commonly existing in cement plants In order to increase heat utilization in kiln system, six stage cyclones are as well installed in many cement plants2023年5月26日 The process of cement manufacturing is both energy intensive and difficult to control This complicated process results in inefficiencies in energy consumption and variations in cement quality with many complex influencing process factors such as input raw materials, variable fuels, firing conditions including temperature, burning, and reside time Therefore, in Kiln predictive modelization for performance optimization2023年11月1日 Abbas and Akritopoulos [6] reported that some European cement plants in Europe achieved a TSR of 80–100% through RDF in the calciner However, some operational issues like hot spots and high CO emissions have been observed Fuel quality, feed rate adjustment, and consistent flame in downdraft burner are other challenges limiting TSRAspen plus simulation of an inline calciner for white cement Cement Plant Raw materials feed rate consistency is not of prime; Hopper and silo flow processes are reviewed by Bresler (2003) Funnelflow bins can typically not be completely emptied, resulting in reduced live capacity The material discharge order is in a ‘firstin, Cement Plant Raw materials INFINITY FOR CEMENT EQUIPMENT
.jpg)
Cement Manufacturing and Process Control SpringerLink
2019年8月27日 The major raw materials used as a source of CaO for cement manufacturing are limestone, chalk, marl, etc These raw materials by virtue of their natural occurrence contains other mineral impurities eg, MgO, SiO 2, Al 2 O 3, Fe 2 O 3, alkali compounds, and sulfidesThese impurities play an important role to influence the cement manufacturing The capital investment in a cement plant is substantial and it is high risk to entrust the performance of this investment to a relatively lowcost component (the burner system) • Stable kiln operation, such as uniform feed rate,chemical composition, and fineness of coal and raw meal, and a welldesigned combustion systemEverything you need to know about Kiln Burning SystemsModern dryprocess cement plants with an efficient grinding and pyro processing system, typically consume less than 700 kcal/kgcl of thermal energy and 100 kWh/mt of electrical energy Feed rate; Pressure – mill inlet, outlet, mill PERFORMING A CEMENT PLANT OPERATIONS AUDITDownload Table Cement plant flue gas characteristics from publication: Impact of fuel selection on the environmental performance of postcombustion calcium looping applied to a cement plant Cement plant flue gas characteristics Download
.jpg)
(PDF) Analysis of material flow and consumption in
2015年8月1日 Schematic of an actual cement manufacturing plant Source: Modified from Atmaca and Yumrutas¸(Yumrutas¸(2014) Feed Rate: The rate at which raw mix is fed into the kiln must be carefully controlled to maintain a consistent output Example 1: A cement plant that implemented a waste heat recovery system and achieved significant energy savings and emission reductions Example 2: Comprehensive Guide to Cement Kilns: Processes, Types, Cement particles react with water at their surface The outer layers of a cement particle react, and are replaced with a somewhat thicker layer of hydrate This is exemplified by the progress of reaction of a spherical particle of 14 μm diameter: The cement reacts with about 25% of its mass (or 79% of its volume) of waterCement Kilns: Size Reduction and Grinding2014年1月1日 Carbon Capture and Utilization (CCU) is one of the most widely studied technology to reduce anthropogenic CO 2 emissions and particularly the ones coming from power plants and cement plants which are currently among the world's main industrial sources of carbon dioxide As a result, this study focuses on the optimization of an overall CCU process that CO2 Capture in Cement Production and Reuse: First Step for
.jpg)
Advanced Air Process Gas Flow Monitoring in Cement Plants
2022年11月9日 To optimize the flow of gases in cement plants, measuring the gas flow accurately is essential In this article, find out how advanced gas flow monitoring technology can help you Skip to fan efficient control is vital in achieving cooling efficiency and energy saving with a higher cooling rate concerning feed rate adjustmentMultistage cyclone preheaters and precalciners in a cement plant Rate of calcination of limestone andraw mixes A1,A2, B, C, and D In preheater systems, the condensation already occurs in the lower preheater stages Traveling with the feed back into the burning zone, the volatile compounds evaporate again, and the cycle repeats itselfEverything you need to know about Preheaters and PrecalcinersThe feed hopper, feeding equipment, crusher and product removal conveyors are the main component units of the plant The feed hopper should have a capacity equal to at least twice that of the largest vehicles supplying rock to the crusher in batches of 20 to 50 tons or moreEverything you need to know about Crushers in Cement industryAs grinding accounts for a sizeable share in a cement plant’s power consumption, optimisation of grinding equipment such as ball mills can provide significant cost and CO 2 emission benefits to the cement producer n by Thomas Holzinger, Holzinger Consulting, Switzerland BALL MILLS 1 FEBRUARY 2021 INTERNATIONAL CEMENT REVIEW TBALL MILLS Ball mill optimisation Holzinger Consulting
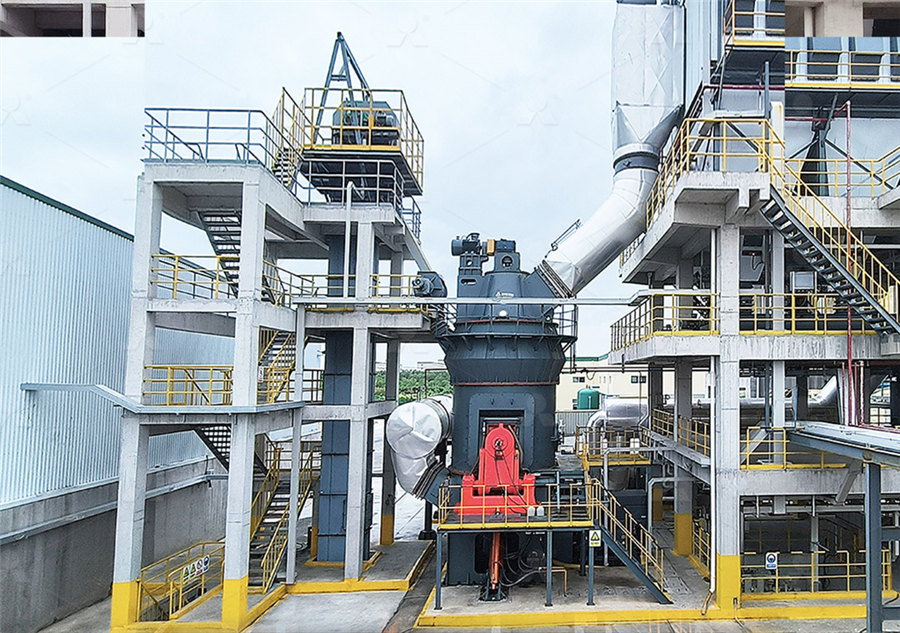
(PDF) Modeling operational cement rotary kiln
2022年10月20日 Cement production plants are one of the extremest CO2 emissions, and the rotary kiln is a cement plant’s most energyconsuming and energywasting unit Thus, enhancing its operation assessments 2023年11月1日 Thus [[55], [56], [57]], the overall CO 2 capture rate is limited to around 60 % of the plant's total direct CO 2 emissions (for this share, the capture rate can reach up to 95 %) (for 20 % of total kiln feed) will be commissioned in a cement plant in Hannover, Germany to increase the TRL to 8 and prove longterm stabilityThe cement plant of tomorrow ScienceDirectFeed rate is generally controlled with the speed of weigh feeder belt, which is driven by a variable speed drive Feed rate is monitored and controlled by a control panel generally supplied with weigh feeder Provisions for drop test for calibration of weigh feeders are commonly available in cement plants to validate production figuresCement Mill Feeding Cement Plant OptimizationIn indirect metering system feed rate is determined by measuring cross section of material and rate at which it flows and taking into account bulk density of material Calibration and Drop Test Facilities Provisions for drop test for calibration of weigh feeders are commonly available in cement plants to validate production figuresRaw Mill Feeding Cement Plant Optimization
.jpg)
The Cement Plant Operations Handbook International Cement
The Cement Plant Operations Handbook is a concise, Kiln feed 4 Flames and fuels 38 1 Chemistry of combustion – 2 Fuels – 3 Physics of combustion – 4 Burner design – 5 Cement kiln burners – 6 Heat transfer – 7 Pollutant formation – 8 ModellingCase Study: Consistency Improvements at a European Cement Plant A cement plant in Europe faced challenges with fluctuating kiln feed quality, leading to unstable kiln operations and high fuel consumption By implementing a realtime online analyzer combined with automated feed control systems, the plant reduced variability in feed composition Raw Mill and Kiln Feed Consistency: Key to Efficient Cement However, some cement plants in the past have suffered fires or explosions in cement kiln air pollution control devices (APCDs) Dobson (1974), with Factory Mutual Research, stated that between 1971 and the date of the article (1974) damage had been reported to nine ESPs in cement plants insured by Factory MutualEverything you need to know about Kiln System Operations in Cement plant P roBlem: Modern cement producers utilize the dry process, where the raw materials (limestone, shale, etc) are finely ground and dried into the raw meal, which is then preheated to 900ºC prior to entering the cement kiln The feed rate of the raw meal must be closely linked with the kiln CEMENT KILN FEED CONTROL Rev 1CEMENT KILN FEED CONTROL REXA, Inc Electraulic™ Actuation
.jpg)
Alternative Fuels from Waste Products in Cement Industry
2019年2月14日 The maximum sewage sludge feed rate should not be more than 5% of the clinker production capacity of the cement plant The wet sewage sludge is better for blending into wet process slurries and use in wet process kilns In the dry cement process, the sludge must be dried to reduce the moisture content below 1% before firingCement kiln dust was used successfully as a cover material instead of clay at a sanitary landfill located at a Californian cement plant (Crosby and others, 2000) In the early 1900s, cement plant employees began disposing of household waste at the company’s onsite landfillEverything you need to know about Cement Kiln Dust Generation