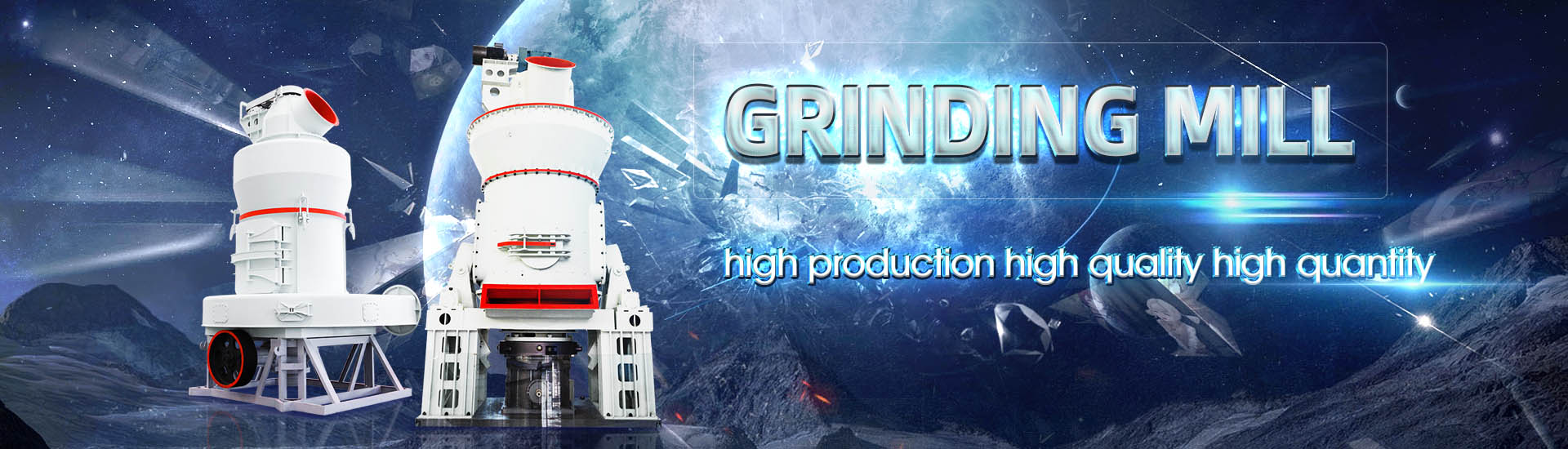
Vertical ore grinding machine discharge particle size mathematical model
.jpg)
PREDICTING THE PRODUCT PARTICLE SIZE DISTRIBUTION FROM
laboratory vertical stirred mill The grinding results show that changes in the feed size, stirring speed, and grinding media size are the primary parameters affecting the particle breakage 2020年1月16日 In this article, we propose a new modeling framework where a discretized distributed parameter macroscale model and a mesoscale kinetic model are combined to Mesoscale Particle Size Predictive Model for Operational Optimal A new modeling framework is proposed where a discretized macroscale model and a mesoscale kinetic model are combined to predict the grinding product particle size The key idea is to A Mesoscale Endpoint Predictive Model of Ore Grinding Particle Size2024年8月7日 Abstract: This article presents a case study on predicting the particle size of copper ore grinding with stochastic configuration networks (SCNs) A set of temporal data was Predicting Particle Size of Copper Ore Grinding With Stochastic
.jpg)
Research on prediction model of ore grinding particle
2019年3月28日 The prediction of grinding particle size is an effective measure to optimize the grinding process Cassiterite polymetallic sulfide ore and leadzinc ore, as the research object in this paper, their particle size prediction 2020年9月1日 Good agreement between experimental and simulated particle size distribution for grinding of a copper ore and a limestone Vertical stirred mills are now widely used in the Mechanistic modeling and simulation of a batch vertical stirred 2021年9月1日 Feed size, product size and energy data from pilot scale grinding tests were evaluated with material characterization tests Based on energysize reduction models Predicting the grinding energy of vrm depending on material 2019年3月28日 The results show that particle size distribution of crushing products under different crushing energies and ore particle sizes is obtained by drop weight test, and the Research on prediction model of ore grinding particle size
.jpg)
MATHEMATICAL MODELS OF PARTICLE SIZE DISTRIBUTION IN
In the paper author presents the method of modeling of HPGR products' particle size distribution by using suitable mathematical models A basis of the HPGR perfor mance assessment and 2018年12月1日 The results show the applicability of using population balance modeling in estimating the product particle size distribution from a laboratory vertical stirred mill The use Predicting the product particle size distribution from a laboratory The highpressure grinding roll (HPGR) technology is currently one of the most efficient methods of hard ore comminution from the scope of the energy consumption Throughput and energetic models of performance are quite well developed, but technological models predicting the comminution effects still needs an indepth research In the paper author presents the method MATHEMATICAL MODELS OF PARTICLE SIZE DISTRIBUTION IN CLUM series of ultrafine gypsum powder vertical grinding mills are a new type of ultrafine industrial ore grinding equipment that integrates grinding, grading, CLUM Ultrafine Vertical Grinding Mill Discharge fineness: 1503000 mesh CLUM Ultrafine Vertical Grinding Mill
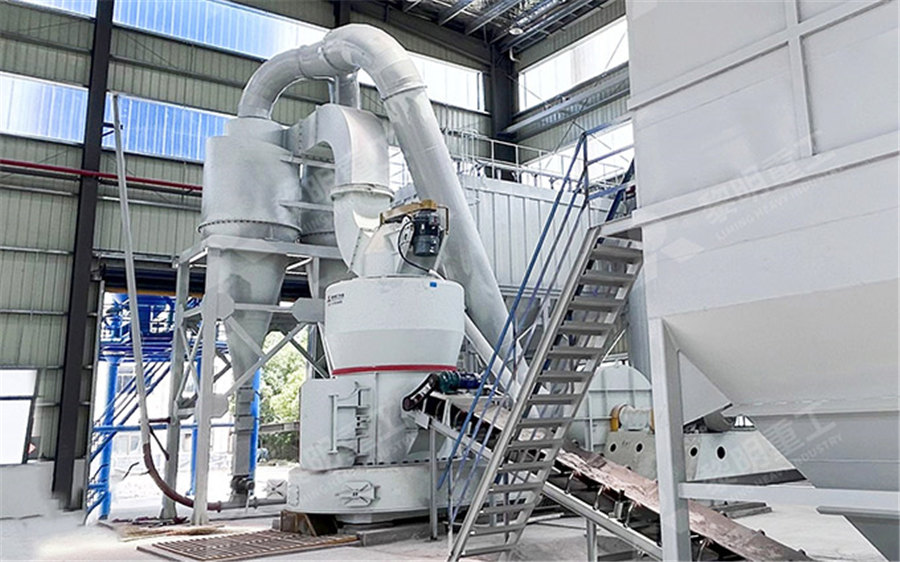
MATHEMATICAL MODELS OF PARTICLE SIZE DISTRIBUTION IN
Mathematical models of particle size distribution in simulation analysis 125 The operating pressure (P) has the most significant importance on the roller press operating efficiency The 2015年3月10日 Vertical roller mills (VRM) have been used extensively for comminuting both cement raw materials and minerals like limestone, clinker, phosphate, manganese, magnesite, feldspar and titanium These mills combine crushing, grinding, classification and drying operations in one unit and have advantages over conventional machines and literature reports that 15% Copper ore grinding in a mobile vertical roller mill pilot plantMathematical models of particle size distribution (PSD) are necessary in the modelling and simulation of comminution circuits In order to evaluate the application of the Swebrec PSD model (SWEF) in the grinding circuit at the Punta Gorda NiCo plant, a sampling campaign was carried out with variations in the operating parameters Subsequently, the fitting of the data to the Use of the Swebrec Function to Model Particle Size Distribution 2017年9月1日 Cassiterite polymetallic sulfide ore and leadzinc ore, as the research object in this paper, their particle size prediction mechanism are studied based on the drop weight test, batch grinding Mathematical modeling of a vertical shaft impact crusher using

Mathematical modeling of a vertical shaft impact crusher using
2017年9月1日 Mathematical modeling of a vertical shaft impact crusher using the Whiten model They demonstrated that the VSI could be a suitable machine for producing highquality crushed aggregate with highgrade cubicity and a low amount of fine aggregate Research on prediction model of ore grinding particle size distribution2022年10月26日 The particle size composition of grinding products will significantly affect the technical and economic indexes of subsequent separation operations The polymetallic complex ores from Tongkeng and Gaofeng are selected as the research object in this paper Through the JK dropweight test, the batch grinding test, and the populationbalance kinetic model of Research on Grinding Characteristics and Comparison of ParticleSize 2022年6月30日 The raw ore exploited from the mining site for the mineral processing plant is a loose particle group with a maximum particle size of 1500 ∼ 1000 mm (openpit mining) or 600 ∼ 400 mm (underground mining), while the separation particle size of the concentrator is usually 02 ∼ 01 mm or finer [Yu et al, 2021; Guo et al, 2021], which suggests that the particle size of Characterization of chalcopyrite ore under high voltage pulse discharge 2015年9月1日 Many attempts have been made to characterize particle size distribution (PSD) curves using different mathematical models, which are primarily used as a basis for estimating soil hydraulic propertiesParticle size distribution models, their characteristics and
.jpg)
Vertical mill simulation applied to iron ores
2014年11月1日 The model previously implemented in Modsim™ has been successfully applied to represent the vertical mill operated with different ores The simulations produced particle size distributions that 2020年8月14日 DEM Simulation of LaboratoryScale Jaw Crushing of a GoldBearing Ore Using a Particle Replacement ModelDEM Simulation of LaboratoryScale Jaw Crushing of a GoldBearing Ore Figure 51 Breakage function from grinding in a laboratory vertical stirred mill 85 Figure 52 Specific selection function from grinding in a laboratory vertical stirred mill 86 Figure 53 Measured (points) and predicted (dotted lines) product particle size distributionPREDICTING THE PRODUCT PARTICLE SIZE DISTRIBUTION FROM A VERTICAL 2014年10月20日 The model previously implemented in Modsim™ has been successfully applied to represent the vertical mill operated with different ores The simulations produced particle size distributions that Population balance model approach to ball mill optimization in iron ore
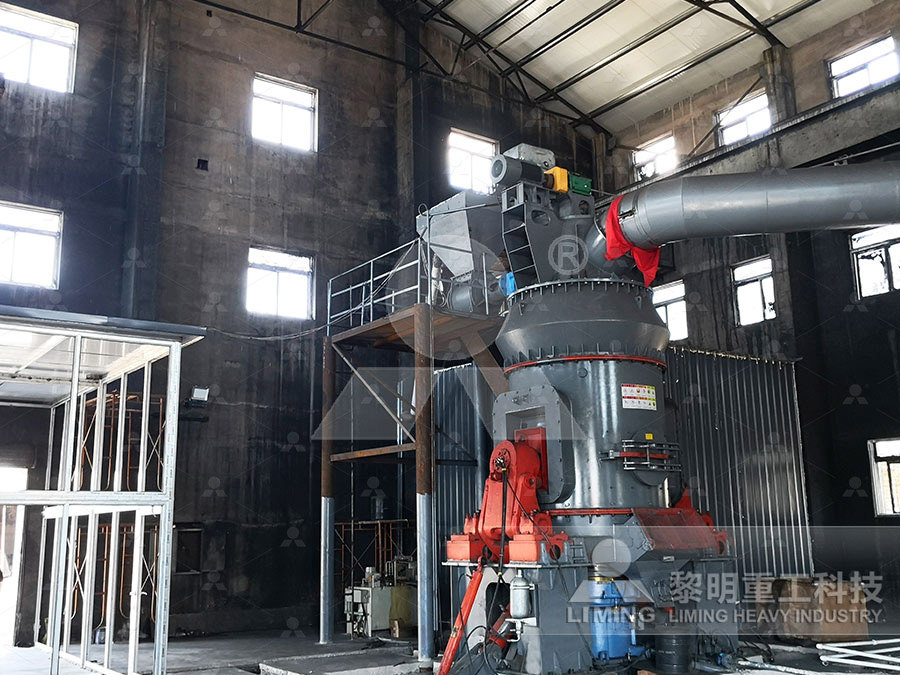
Mathematical vs machine learning models for particle size
2024年6月6日 Purpose Particle size distribution (PSD) assessment, which affects all physical, chemical, biological, mineralogical, and geological properties of soil, is crucial for maintaining soil sustainability It plays a vital role in ensuring appropriate land use, fertilizer management, crop selection, and conservation practices, especially in fragile soils such as those of the North 2017年9月30日 The ore particle size distribution is an important basis for the evaluation of crushing effect The particle size parameters mainly include the particle area, perimeter, equivalent diameter, shape factor and so on In order to obtain the ore particle size distribution, we mainly study the following aspects: (1)Research of Ore Particle Size Detection Based on Image Processing2020年8月14日 The Discrete Element Method (DEM) is a numerical method that is able to simulate the mechanical behavior of bulk solids flow using spheres or polyhedral elements, offering a powerful tool for equipment design and optimization through modeling and simulation The present work uses a Particle Replacement Model (PRM) embedded in the software DEM Simulation of LaboratoryScale Jaw Crushing of a GoldBearing Ore 2020年1月16日 Request PDF Mesoscale Particle Size Predictive Model for Operational Optimal Control of Bauxite Ore Grinding Process This study investigates the use of a mesoscale kinetic model to cooperate Mesoscale Particle Size Predictive Model for Operational Optimal
.jpg)
Performance Evaluation of Vertical Roller Mill in Cement Grinding
Particle size distributions of collected samples were determined by the combination of dry sieving and laser scattering method down to 500 µm Data obtained from two surveys were used to obtain 2024年11月1日 When constructing an ore model using filled spherical particles, the porosity within the model is often much greater than that of the actual ore Smaller radius spherical particles can be arranged more closely together, which reduces the porosity of the ore model (Brouwers, 2006, Cho et al, 2007, Groot and Stoyanov, 2011)A Krigingbased method for calibrating the bondedparticle model PDF On Jan 1, 2009, Mohammad Reza Khalesi and others published A grindingliberation model for the size reduction of gold ores Find, read and cite all the research you need on ResearchGateA grindingliberation model for the size reduction of Request PDF On Mar 15, 2015, Mathis Reichert and others published Research of iron ore grinding in a verticalrollermill Find, read and cite all the research you need on ResearchGateResearch of iron ore grinding in a verticalrollermill
.jpg)
Analysis and validation of a runofmine ore grinding mill circuit
2013年4月1日 However, a lot of academic applications have been developed using Matlab/Simulink R le Roux et al (2013) proposed and validated a novel and simple nonlinear model, Sbárbaro (2010), Liu and 2024年10月24日 The crushed particles arrive at the crushing product collection box through the discharge Tavares LM (2017) Mathematical modeling of a vertical shaft impact crusher using the Whiten model Miner Eng Li Y, Yang J, Ma S, Sun Y (2019) Research on prediction model of ore grinding particle size distribution J Disper Sci Experimental Study of the Crushing Characteristics of Single Particle (2) are related to grinding operation as follows: A = f (mill conditions, eg, media size, solids concentration, mill speed, mill filling) α = f (ore hardness, mineralogy, specific gravity, etc Particle size distribution of pilot grinding circuit feeds2013年11月26日 The RosinRammler Bennet (RRB) model fitted well the particle size distribution data over the entire range of the size distribution for grinding in both hammer mill and pin mill with high Grinding Studies of Mango Ginger: Mathematical Modelling of Particle
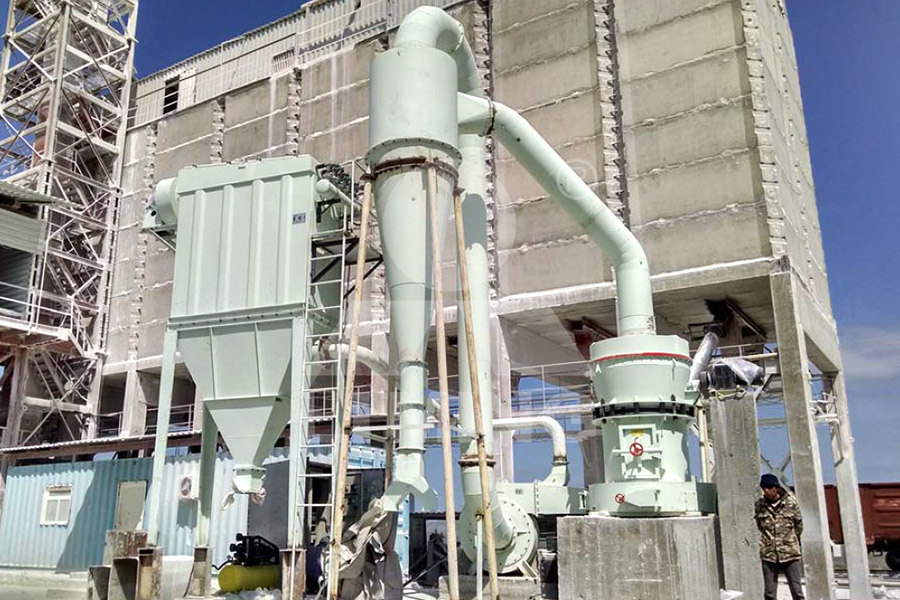
(PDF) Application of perfect mixing model for simulation of vertical
2017年5月26日 Vertical roller mills (VRMs) are wellestablished grinding equipment for various tasks in the coal and cement industry There are few studies on simulation of VRMs2017年9月1日 Several mathematical models for the VSI crusher have been proposed in the The researcher also established a minimum particle size below which the probability of particles being classified Carvalho, RM, Tavares, LM, 2014 A predictive model of the Vertical Shaft Impact (VSI) Crusher In: Comminution ’14 Cape Town, pp 1 Mathematical modeling of a vertical shaft impact crusher using 2022年10月26日 Through the JK dropweight test, the batch grinding test, and the populationbalance kinetic model of grinding with the Simulink platform, the grinding characteristics of the two types of ores and Research on Grinding Characteristics and Comparison of ParticleSize Vertical roller mills, (VRM), are widely used for grinding raw materials in factories engaged in the extraction and processing of minerals Any machine used for grinding or crushing consumes around 30 to 40% of the energy of a factory The loading Parameters for the Grinding Process in Vertical Mills Using
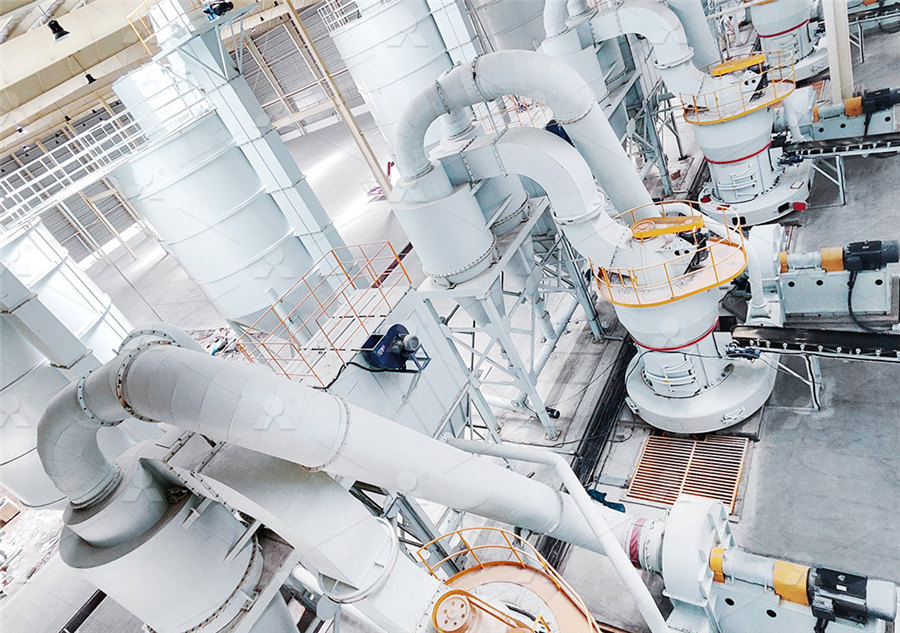
MATHEMATICAL MODELS OF PARTICLE SIZE DISTRIBUTION IN
The highpressure grinding roll (HPGR) technology is currently one of the most efficient methods of hard ore comminution from the scope of the energy consumption Throughput and energetic models of performance are quite well developed, but technological models predicting the comminution effects still needs an indepth research In the paper author presents the method CLUM series of ultrafine gypsum powder vertical grinding mills are a new type of ultrafine industrial ore grinding equipment that integrates grinding, grading, CLUM Ultrafine Vertical Grinding Mill Discharge fineness: 1503000 mesh CLUM Ultrafine Vertical Grinding MillMathematical models of particle size distribution in simulation analysis 125 The operating pressure (P) has the most significant importance on the roller press operating efficiency The MATHEMATICAL MODELS OF PARTICLE SIZE DISTRIBUTION IN 2015年3月10日 Vertical roller mills (VRM) have been used extensively for comminuting both cement raw materials and minerals like limestone, clinker, phosphate, manganese, magnesite, feldspar and titanium These mills combine crushing, grinding, classification and drying operations in one unit and have advantages over conventional machines and literature reports that 15% Copper ore grinding in a mobile vertical roller mill pilot plant
.jpg)
Use of the Swebrec Function to Model Particle Size Distribution
Mathematical models of particle size distribution (PSD) are necessary in the modelling and simulation of comminution circuits In order to evaluate the application of the Swebrec PSD model (SWEF) in the grinding circuit at the Punta Gorda NiCo plant, a sampling campaign was carried out with variations in the operating parameters Subsequently, the fitting of the data to the 2017年9月1日 Cassiterite polymetallic sulfide ore and leadzinc ore, as the research object in this paper, their particle size prediction mechanism are studied based on the drop weight test, batch grinding Mathematical modeling of a vertical shaft impact crusher using 2017年9月1日 Mathematical modeling of a vertical shaft impact crusher using the Whiten model They demonstrated that the VSI could be a suitable machine for producing highquality crushed aggregate with highgrade cubicity and a low amount of fine aggregate Research on prediction model of ore grinding particle size distributionMathematical modeling of a vertical shaft impact crusher using 2022年10月26日 The particle size composition of grinding products will significantly affect the technical and economic indexes of subsequent separation operations The polymetallic complex ores from Tongkeng and Gaofeng are selected as the research object in this paper Through the JK dropweight test, the batch grinding test, and the populationbalance kinetic model of Research on Grinding Characteristics and Comparison of ParticleSize

Characterization of chalcopyrite ore under high voltage pulse discharge
2022年6月30日 The raw ore exploited from the mining site for the mineral processing plant is a loose particle group with a maximum particle size of 1500 ∼ 1000 mm (openpit mining) or 600 ∼ 400 mm (underground mining), while the separation particle size of the concentrator is usually 02 ∼ 01 mm or finer [Yu et al, 2021; Guo et al, 2021], which suggests that the particle size of 2015年9月1日 Many attempts have been made to characterize particle size distribution (PSD) curves using different mathematical models, which are primarily used as a basis for estimating soil hydraulic propertiesParticle size distribution models, their characteristics and