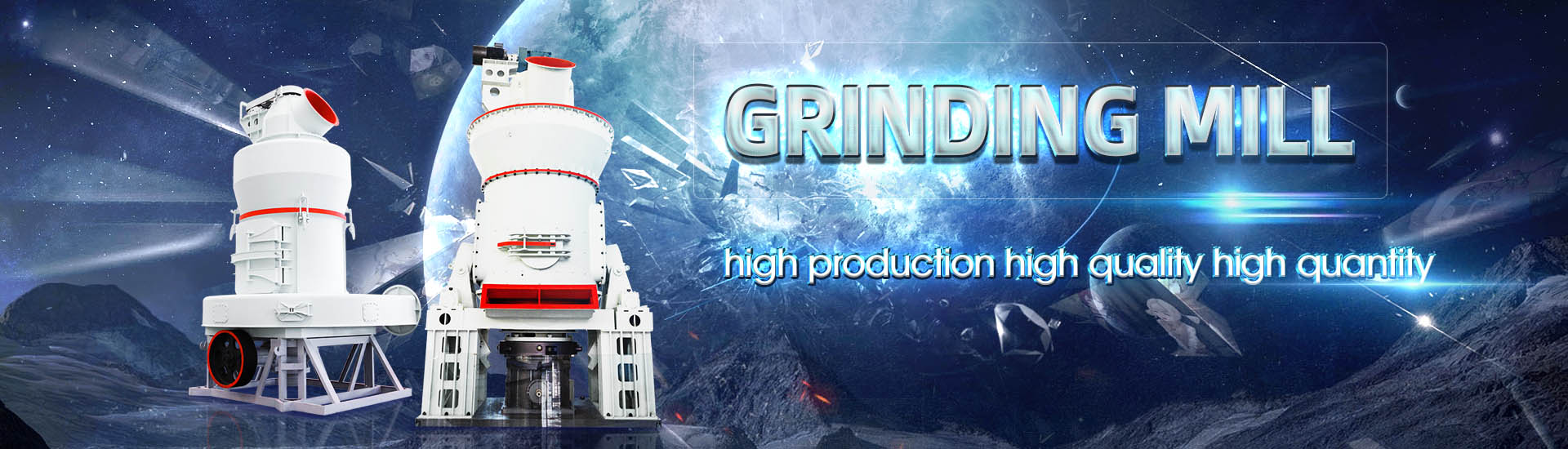
Coal mill schematic diagram High speed coal mill
.jpg)
Modeling and Control of Coal Mill
A simplified design schematic of a vertical spindle mill is shown in Figure 1 Raw coal is transported on a conveyor belt and dropped into the mill through the chute The coal falls into Coal mill is an important component of the thermal power plant It is used to grind and dry the moisturized raw coal and transport the pulverized coal – air mixture to the boiler Poor dynamic (PDF) Modeling and Control of Coal Mill AcademiaMedium speed mills are widely used in largescale thermal power plants, which run at a setting speed of 50∼300 r/min, owing to their efficiency The schematic of a medium speed coal mill isSchematic of medium speed coal mill [5] ResearchGateAiming at the typical faults in the coal mills operation process, the kernel extreme learning machine diagnosis model based on variational model feature extraction and kernel principalSchematic diagram of the working principle of MPS
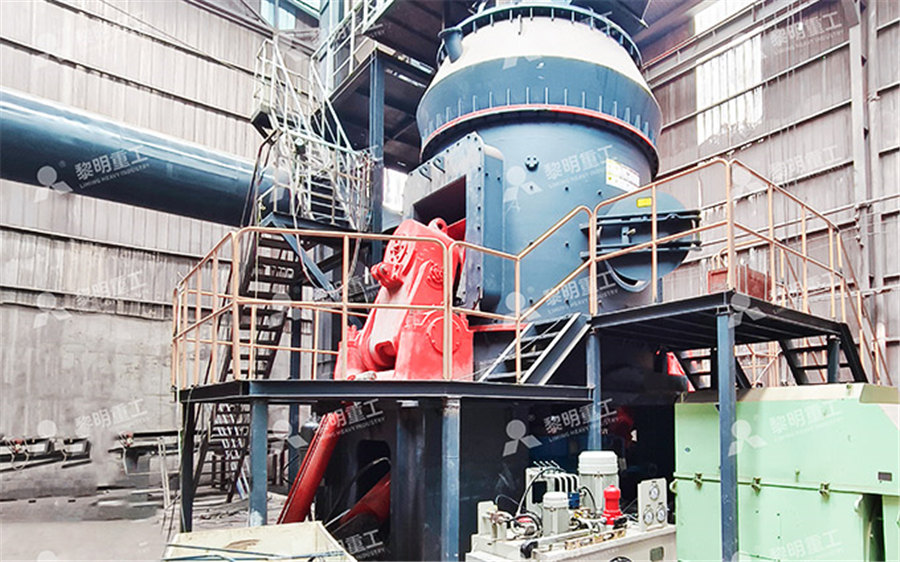
Schematic structure of the MPS mediumspeed mill
In this paper, the diagnosis model based on three typical abnormities in the process of coal mill is firstly established A new realtime updating strategy for the Bayesian network (BN) model2017年8月1日 This paper is organized as follows: section one opens with a brief introduction of coal mills; section two deduces and establishes the nonlinear differential equations of coal Modeling of a medium speed coal mill ScienceDirectsbm diagram for zgm113n coal millzgm95 type roller mill size Beijing Power Plant Vertical Mill DescriptionAtox coal mill 200 300 1500 3000 100 200 45 60 ms small size big energy savings sbm/sbm diagram for zgm113n coal millmd at main dihog/sbm2012年5月1日 The paper presents development and validation of a coal mill model to be used for improved mill control, which may lead to a better load following capability of power plants Derivation and validation of a coal mill model for control

A Comparison of Three Types of Coal Pulverizers Babcock Power
This paper presents a comparison of the Riley Vertical Roller Mill with Riley's two other pulverizer designs— a lowspeed ball tube mill and a highspeed attrition pulverizer Specific topics 2015年11月1日 Coal mills are bottleneck in coal–fired power generation process due to difficulty in developing efficient controls and faults occurring inside the mills In this paper, a dynamic A unified thermomechanical model for coal mill operation2012年11月17日 20 131Fineness Fineness is an indicator of the quality of the pulverizer action Specifically, fineness is a measurement of the percentage of a coal sample that passes through a set of test sieves usually designated at 50, Coal mill pulverizer in thermal power plants PPTThe system is based on a monochrome CCD (Charged Couple Device) camera of highspeed frame rate (120 frames per second) Processing stage comprises the digital analysis in the spatial and spectral Schematic diagram of the pulverized coal
.jpg)
Schematic diagram of the working principle of MPS
Download scientific diagram Schematic diagram of the working principle of MPS medium speed coal mill [1] from publication: Fault Diagnosis of Coal Mill Based on Kernel Extreme Learning Machine Erosive Wear Analysis of Mnsteels Hammers due to Coal Impact in a HighSpeed Pulverising Mill II Abstract The coal pulverisation process plays a significant role in thermal power plants to generate electricity Largesize coal lumps drop onto the Erosive Wear Analysis of MnSteels Hammers due to Coal Impact in a High Download scientific diagram Schematic diagram of coal mill layout from publication: Combined operation mode of subcritical Wflame boiler and coal mill optimized numerical simulation The Schematic diagram of coal mill layout ResearchGate2015年11月1日 As presented by Andersen et al (2009) and Odgaard, Stoustrup, and Mataji (2007), coal moisture imposes limit on the maximum load at which a coal mill can be operated and the load gradient (how fast the mill may change its operating point), if it is desired that the pulverized coal entering the furnace has moisture content less than or equal to a certain value A unified thermomechanical model for coal mill operation

Dual fault warning method for coal mill based on ScienceDirect
2024年5月1日 The coal mill is a machine that breaks and grinds coal into pulverized coal It is the core equipment of pulverizing system Coal mills are categorized according to speed as low, medium and high speed mills The low and mediumspeed coal mills are the most popular due to their economy [25] The modeling object is ZGM type mediumspeed roller Equipped with the highefficiency RAKM dynamic separator, the ATOX coal mill will grind any type of coal to the required fineness at the highest efficiency When provided with a variable speed mill motor, the ATOX will also grind petcoke and anthracite down to a fineness below 5% +90 μm Furthermore, it is designed toATOX COAL MILL2012年5月1日 A simplified design schematic of a socalled roll mill is presented in Fig 2 Raw coal is transported on a conveyor belt and dropped into the mill, where it falls onto a grinding table and is crushed by rollers Primary air, blown from the bottom of the mill, picks up fine coal particles and transports them into the classifier sectionDerivation and validation of a coal mill model for controlThe standard mill capacity for twenty (20) different mill sizes ranges from 10 tph to 190 tph (Figure 3) 4 Figure 2 First Generation MPS Mill with spring grinding force loading systemCOAL PULVERIZER DESIGN UPGRADES TO MEET THE DEMANDS
.jpg)
Sectional view of MBF coal mill Download Scientific
A control oriented model was then developed by Fan (1994) and Fan and Rees (1994) In 2009, coal flow and outlet temperature of mill were modelled using mass and heat balance equations for startup Download scientific diagram Schematic structure of the MPS mediumspeed mill from publication: Application of ModelBased Deep Learning Algorithm in Fault Diagnosis of Coal Mills The coal Schematic structure of the MPS mediumspeed millFigure 7) with sufficient coal/air mill exit temperature (14009, was expected to eliminate a number of past fuel system deficiencies such as: Low mill product fineness Little mill turndown capability Utilization of maximum available primary air at all mill loads (to avoid mill roller skidding) Abnormally high coal pipe (excessive coal pipe wearWorldProven Coal Pulverizer Technology Debuts in the USThe coal ou tput then moves towards the throat of the mill where it mixes with high speed hot primary air The heavier Schematic diagram of coal mill The mass of coal to be pulverised depends on the mass flow of the raw coal, , the return flow of the particles rejectedModeling and Control of Coal Mill
.jpg)
Modeling of a medium speed coal mill ResearchGate
2017年5月1日 Download Citation Modeling of a medium speed coal mill This paper presents a coal mill model that considers the effect of coal moisture on its accuracy This mathematical model is derived 2017年8月1日 Simulation results indicate that the model effectively represents the midhigh process of coal mill dynamics and can be used to estimate the key parameters in coal mills, which are difficult to measure or cannot be measured In this study, MPS180HPII medium speed coal mill is used as the research objectModeling of a medium speed coal mill ScienceDirectFigure 1 shows a typical mill system schematic including fuel bunker, feeder, mill, primary air system medium and high speed to process a variety of coals, from bituminous, subbituminous to lignite coals These machines include Ball Tube Mills (BTM), vertical roller mills and Atrita ® (highspeed attrition mills) During operation,Mill Steam Inerting System Review and Performance Validation2020年8月12日 This study shows the performance of a currently running vertical roller coal mill (VRM) in an existing coalfired power plant In a power plant, the coal mill is the critical equipment, whose An investigation of performance characteristics and energetic
.jpg)
Schematic diagram of a coalfired steam power plant [11]
Download scientific diagram Schematic diagram of a coalfired steam power plant [11] from publication: Hot Corrosion Erosion Problems in Coal Based Power Plants in India and Possible 2009年9月20日 A control oriented model was then developed by Fan (1994) and Fan and Rees (1994) In 2009, coal flow and outlet temperature of mill were modelled using mass and heat balance equations for startup Modeling and Parameter Identification of Coal MillThe Functionality of a Ball Mill Diagram A ball mill is a crucial equipment used for grinding materials into fine powders in various industries It operates on the principles of impact and attrition, where the grinding media are balls to be fed The Ultimate Guide to Understanding Ball Mill 2021年8月5日 High speed impact mill; The slow speed and medium speed mills are selected for coals ranging from subbituminous to anthracite In bowl mill pulveriser raw coal coming from feeder gets ground between the grinding rolls Pulveriser in Thermal Power Plant Bowl Mill Ball Mill

Diagram of electricity generation from coal (World Coal
Download scientific diagram Diagram of electricity generation from coal (World Coal Institute, 2010) from publication: A Review on Technologies for Reducing CO2 Emission from Coal Fired Power Coal Injection) 1990 Central coal grinding plant (LM 263 D) for gas and steam power station (coal gasification) 1992 Central coal grinding plant (LM 263 D) for the production of lignite (brown) coal dust 2002 Coal grinding plant (LM 232 D) for grinding wood pellets for power stations 2005 First 4roller pressure mill (LM 434 D) becomesLOESCHEMILLS2021年11月4日 Test methods for grindability and abrasion testing: Full scale ring and ball mill, Hardgrove mill [30,31], BCURAroll mill, Rotating electrode ball wear tester [32], Dropweight test machine [28 Technique to Investigate Pulverizing and Abrasive Performance of Coals It contains coal feeder, coal mill, rotary separator, raw coal hopper and stone coal scuttle, as depicted in Fig 2 The coal pulverizing system grinds the raw coal into pulverized coal with Schematic diagram of the coal pulverizing system
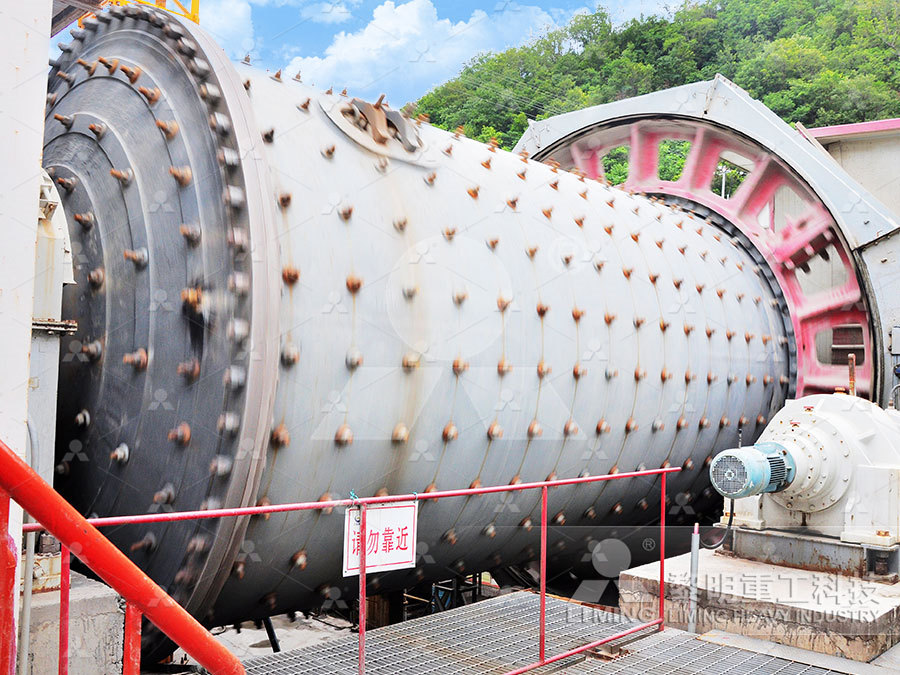
Review of control and fault diagnosis methods applied to coal
2015年8月1日 The diagrams are developed The SAMA nomenclature is detailed in Fig 5 Download: Download fullsize image; Fig 4 Schematic of mill control for (a) low speed mills and (b) medium speed mills If the value of the mill differential pressure rises too high, then the coal feeder speed is reduced to a minimum value for HRM1700MVRM Free download as PDF File (pdf), Text File (txt) or read online for free The document provides installation and operation instructions for the HRM1700M Vertical Roller Coal Mill It describes the mill's technical parameters, components, structure, working principles, and installation process Key aspects include grinding rollers that can be removed for Operation Manual: HRM1700M Vertical Roller Coal Mill2022年2月24日 Curves of mill productivity, power consumed, specific surface of coal dust in terms of the relative rotational speed of the ball drum mill Composition of the balls loading the mill with a standard Improving the efficiency of the coal grinding process in ball drum Download scientific diagram (a) Schematic diagram of a four high rolling mill, (b) coordinate system, and (c) equivalent springmass system from publication: Nonlinear Dynamic Analysis of a (a) Schematic diagram of a four high rolling mill, (b) coordinate
.jpg)
Coal mill pulverizer in thermal power plants PPT
2012年11月17日 20 131Fineness Fineness is an indicator of the quality of the pulverizer action Specifically, fineness is a measurement of the percentage of a coal sample that passes through a set of test sieves usually designated at 50, The system is based on a monochrome CCD (Charged Couple Device) camera of highspeed frame rate (120 frames per second) Processing stage comprises the digital analysis in the spatial and spectral Schematic diagram of the pulverized coal Download scientific diagram Schematic diagram of the working principle of MPS medium speed coal mill [1] from publication: Fault Diagnosis of Coal Mill Based on Kernel Extreme Learning Machine Schematic diagram of the working principle of MPS Erosive Wear Analysis of Mnsteels Hammers due to Coal Impact in a HighSpeed Pulverising Mill II Abstract The coal pulverisation process plays a significant role in thermal power plants to generate electricity Largesize coal lumps drop onto the Erosive Wear Analysis of MnSteels Hammers due to Coal Impact in a High
.jpg)
Schematic diagram of coal mill layout ResearchGate
Download scientific diagram Schematic diagram of coal mill layout from publication: Combined operation mode of subcritical Wflame boiler and coal mill optimized numerical simulation The 2015年11月1日 As presented by Andersen et al (2009) and Odgaard, Stoustrup, and Mataji (2007), coal moisture imposes limit on the maximum load at which a coal mill can be operated and the load gradient (how fast the mill may change its operating point), if it is desired that the pulverized coal entering the furnace has moisture content less than or equal to a certain value A unified thermomechanical model for coal mill operation2024年5月1日 The coal mill is a machine that breaks and grinds coal into pulverized coal It is the core equipment of pulverizing system Coal mills are categorized according to speed as low, medium and high speed mills The low and mediumspeed coal mills are the most popular due to their economy [25] The modeling object is ZGM type mediumspeed roller Dual fault warning method for coal mill based on ScienceDirectEquipped with the highefficiency RAKM dynamic separator, the ATOX coal mill will grind any type of coal to the required fineness at the highest efficiency When provided with a variable speed mill motor, the ATOX will also grind petcoke and anthracite down to a fineness below 5% +90 μm Furthermore, it is designed toATOX COAL MILL
.jpg)
Derivation and validation of a coal mill model for control
2012年5月1日 A simplified design schematic of a socalled roll mill is presented in Fig 2 Raw coal is transported on a conveyor belt and dropped into the mill, where it falls onto a grinding table and is crushed by rollers Primary air, blown from the bottom of the mill, picks up fine coal particles and transports them into the classifier sectionThe standard mill capacity for twenty (20) different mill sizes ranges from 10 tph to 190 tph (Figure 3) 4 Figure 2 First Generation MPS Mill with spring grinding force loading systemCOAL PULVERIZER DESIGN UPGRADES TO MEET THE DEMANDS