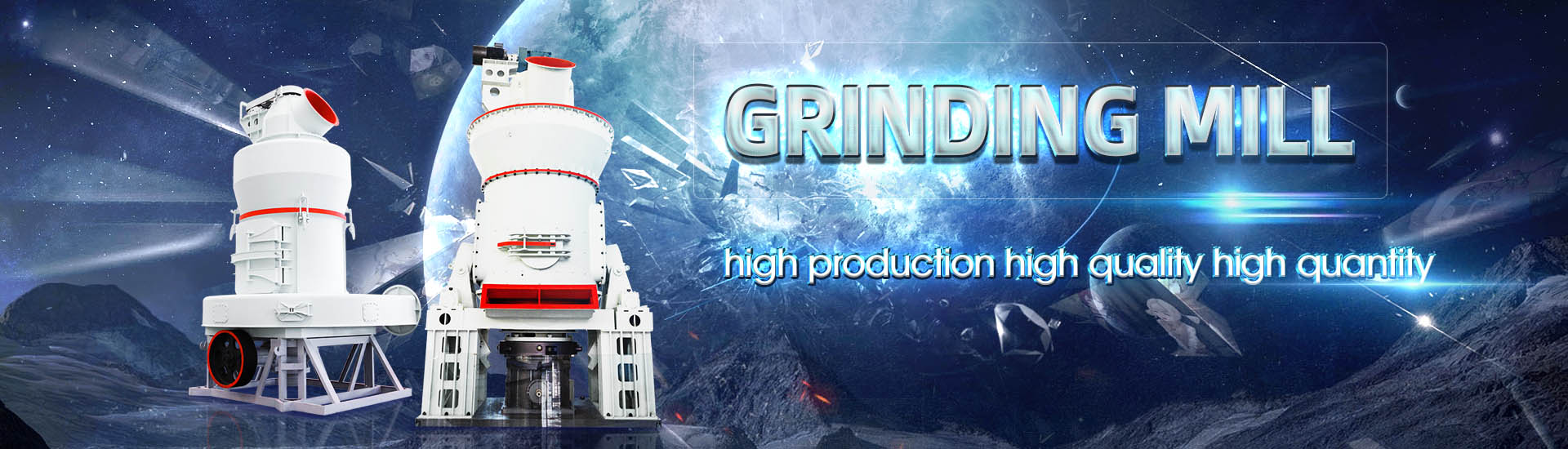
Ore powder making plant license application process
.jpg)
Licenses and Rights Application Guidelines and Assessment
APPLICATION GUIDELINES AND ASSESSMENT PROCEDURES 1 PURPOSE This document is an initiative of the Ministry of Mines and Energy aimed at explaining the types of licences and permits administered and issued by the Ministry and the application and evaluation processes Guidelines for mineral process plant development studies P R Whincup* This paper presents guidelines for studies required for the development of mineral processing facilities from initial Guidelines for mineral process plant development studies AusIMM2021年3月15日 This part describes the history, goals of pelletization, and provides a framework so that the chemical factors leading into an effective pelletizing process can be understood Iron Ore Pelletization: Part I Fundamentals: Mineral Processing 2017年2月16日 Sintering is a thermal agglomeration process that is applied to a mixture of iron ore fines, recycled ironmaking products, fluxes, slagforming agents, and solid fuel (coke) The (PDF) Iron Ore Sintering: Process ResearchGate
.jpg)
From Ore to Iron with Smelting and Direct Iron Reduction
2017年10月17日 In the smelting reduction process, pelletized iron oxide ore or fine ore powders are prereduced in a fluidized bed or reduction shaft The reduced iron along with coal and PDF On Jul 11, 2018, Sandra Lúcia de Moraes and others published Iron Ore Pelletizing Process: An Overview Find, read and cite all the research you need on ResearchGateIron Ore Pelletizing Process: An Overview ResearchGate2018年8月9日 This study focussed on flowsheet simulation for mineralogicalbased approach to geometallurgy of iron ores Process unit models used were selected based on their Process simulations in mineralogybased geometallurgy of iron oresIron ore powder agglomeration is the basis for blast furnace ironmaking and is the processing work in between ore crushing, ore grinding separation, and steelmaking Its purpose is to Agglomeration of Iron Ores SpringerLink
.jpg)
Study on the Basic Characteristics of Iron Ore Powder with
2022年7月30日 Study on the Basic Characteristics of Iron Ore Powder with Different Particle Sizes Zezheng Li 1,2,3,4,5, Yifan Li 1,2,3 2 Hebei Key Laboratory of Data Science and Application, North China University of Science and Technology, Tangshan and guide the sintering performance plant to choose the best ore allocation method, The iron ore production has significantly expanded in recent years, owing to increasing steel demands in developing countries However, the content of iron in ore deposits has deteriorated and lowgrade iron ore has been processed Iron Ore Pelletizing Process: An Overview IntechOpen2020年4月1日 On the other hand, since most plants are optimized for a specific size fraction (≥ 75 µm) and the tailings of chromite plants are generally characterized by fine particles, a recurring problem Process optimization of a chrome ore gravity The invention discloses a sintering process of manganese ore powder The process comprises the following steps of: adding water to mix manganese ore powder, a binding agent, fuel, a fluxing agent and return ore as mixed ore, wherein the binding agent is formed by mixing manganese salt and organic matter and counts for 0630% of mass of the mixed ore, the fuel counts for 30 Sintering process of manganese ore powder Google Patents
.jpg)
Application of deep learning in iron ore sintering process: a review
sintered ore were also appreciated by the ironmaking process Therefore, the sintering process eventually became the preferred choice for the briquetting of pulverised materials [34] 21 Sintering process and its chemical reactions The significance of sintering is that the lumping of pulverised ore from the mining process can be used to obtain2009年8月1日 Request PDF Recycling of steel plant mill scale via iron ore pelletisation process Mill scale is an iron oxide waste generated during steelmaking, casting and rolling Total generation of mill Recycling of steel plant mill scale via iron ore pelletisation process 2013年4月24日 1 Talcum Powder Manufacturing Process Within the talcum powder manufacturing process, crusher, grinding mill are utilized as talc powder making machine for powder production Most talc deposits are open pit mine Talc rock is found by giant spades Different ore types are sorted because they are removed in the seamTalcum powder manufacturing process PDF Free DownloadThis process helps to increase the surface area of the ore, making it more accessible for subsequent grinding Grinding, on the other hand, involves further reducing the size of the crushed ore into a fine powder The crushed ore is transferred to a grinding mill, which contains heavyduty steel balls or rodsGold Refinery Process: From Raw Material to Pure Gold
.jpg)
Iron Ore Pelletizing Process: An Overview Semantic Scholar
2018年7月11日 The iron ore production has significantly expanded in recent years, owing to increasing steel demands in developing countries However, the content of iron in ore deposits has deteriorated and lowgrade iron ore has been processed The fines resulting from the concentration process must be agglomerated for use in iron and steelmaking This chapter 2016年1月8日 The first commercial production of phosphate rock began in England in 1847 A wide variety of techniques and equipment is used to mine and process phosphate rocks in order to beneficiate lowgrade ores and remove impurities The eighth chapter of this book deals with mining and beneficiation of phosphate ore The principle and operating conditions of important Mining and Beneficiation of Phosphate Ore IntechOpen2022年7月15日 Iron ore sintering is an agglomeration process of iron or e fines, fluxes, fossil fuel (coke and coal), and some ironbearing waste materials in the ironmaking and steelmaking industry [Influence of Sinter Parameters on CO Emission in Iron 2013年2月23日 Fig 2 Flowsheet of straight travelling grate process Grate kiln process The grate kiln process was developed by former Allis Chalmer and the first plant on this technology was constructed in 1960 In the grate kiln process Introduction to Iron ore Pellets and Pelletizing
.jpg)
Applications of Iron Ore Pellets Sree Metaliks
2023年12月1日 How Are Iron Ore Pellets Made? Here’s a quick introduction for you on how Pellets are made Usually, Iron Ore is manufactured and converted into Pellets These are oval lumps of iron ore that are hardened using fuel This process of converting iron ore into pellets is known as Pelletization Iron Ore Pellets are then used in the production of 2020年11月1日 Process water collected from the iron ore beneficiation plant was treated by electrocoagulation (EC) process to make it suitable for reuse or safe for dischargeTreatment of iron ore beneficiation plant process water by 2020年2月15日 The proposed intelligent decisionmaking strategy can effectively improve abnormal operating mode, which has a good application prospect in the iron ore sintering process View Show abstractAn Intelligent Control Strategy for Iron Ore Sintering Ignition Process To know about details of fee (application, inspection annual license fee) Product specific Marking Fees can be also be searched from the URL : View: 8: The applications are accepted only through online mode including all payments To submit your application, please visit our online portal, manakonline: 9Apply For License Bureau of Indian Standards
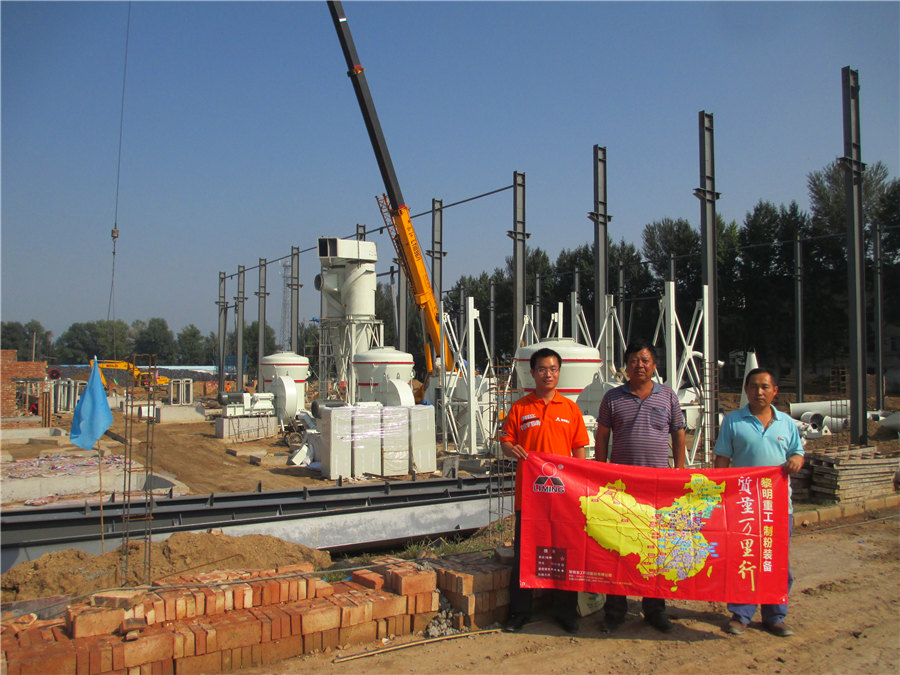
Hazard Identification, Risk Assessment, and Control Measures as
2017年5月1日 General India has the fourth largest iron ore reserves in the world after Russia, Brazil, and Australia[] As per the survey conducted by the Indian Bureau of Mines (IBM) in April 2000, India had 9919 million tonnes of recoverable reserves of haematite and 3546 million tonnes of magnetite[]As good quality iron ore deposits are depleting very fast, beneficiation 2023年5月6日 In the flotation process of copper ore processing, the collector adsorbed on the surface of the target mineral, which increases the hydrophobicity difference between valuable and gangue mineralsThen the mineral particles with high content of beneficial minerals are adsorbed on the surface of the bubbles, and finally, the air bubbles float upCopper Ore Production Process JXSC Mineralore pelletizing plant The idea of rolling moist fine ore in a drum to form balls and then drying and firing it was first patented by A G Andersson in Sweden in 1912 Further development was performed to bring the idea to reality In 1943, E W Davies and coworkers demonstrated the process using an experimental shaft furnaceIron Ore Pelletizing Process: An Overview IntechOpen2024年1月11日 The limestone sandmaking plant process mainly includes three stages: coarse crushing, fine crushing, and sand making The finished sand and gravel aggregate made of limestone can provide industrial raw materials for industries such as airport construction, water conservancy power stations, tall buildings, concrete mixing plants, etcLimestone Crushing And SandMaking Plant Eastman Rock
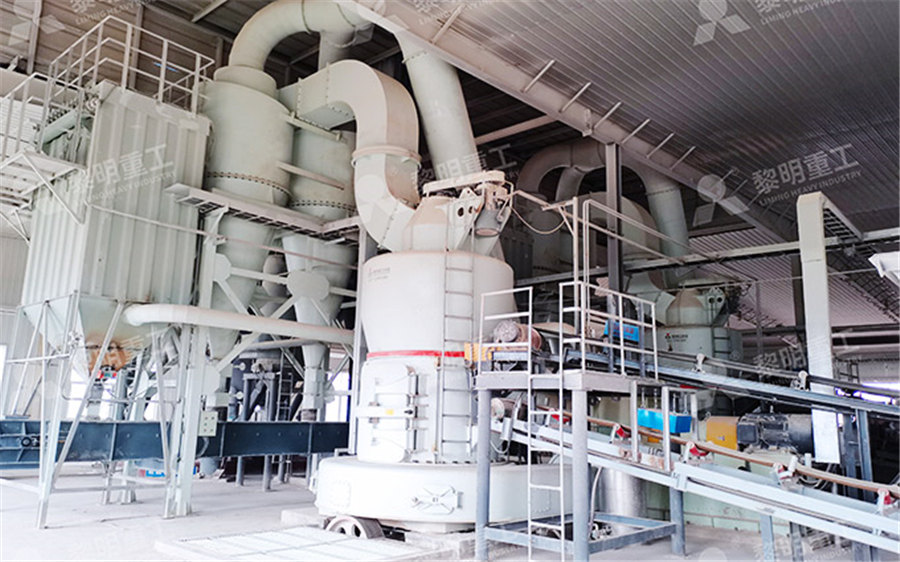
The Process of Making Copper From Ore to Product
2024年7月30日 The smaller pieces are ground into a fine powder in a ball or rod mill This process increases the surface area of the ore, allowing for better copper extraction The grinding mills use steel balls or rods to crush the ore into a fine consistency, similar to 2024年1月23日 Gypsum powder is formed by a series of treatments on a large bulk of gypsum, with a finished particle size usually around 80325 mesh In terms of the entire production process of gypsum grinding, the equipment required Gypsum Powder Grinding And Processing Plant 2021年1月1日 Currently, approximately 14 billion tons per year of iron ore tailing wastes (IOT) are generated, mainly in Australia, Brazil, and China This work describes the characterization and application Iron Ore Tailings: Characterization and ApplicationsCopper processing is a complicated process that begins with mining of the ore (less than 1% copper) and ends with sheets of 9999% pure copper called cathodes, which will ultimately be made into products for everyday useThe most common types of ore, copper oxide and copper sulfide, undergo two different processes, hydrometallurgy and pyrometallurgy, respectively, Copper Mining and Processing: Processing Copper Ores
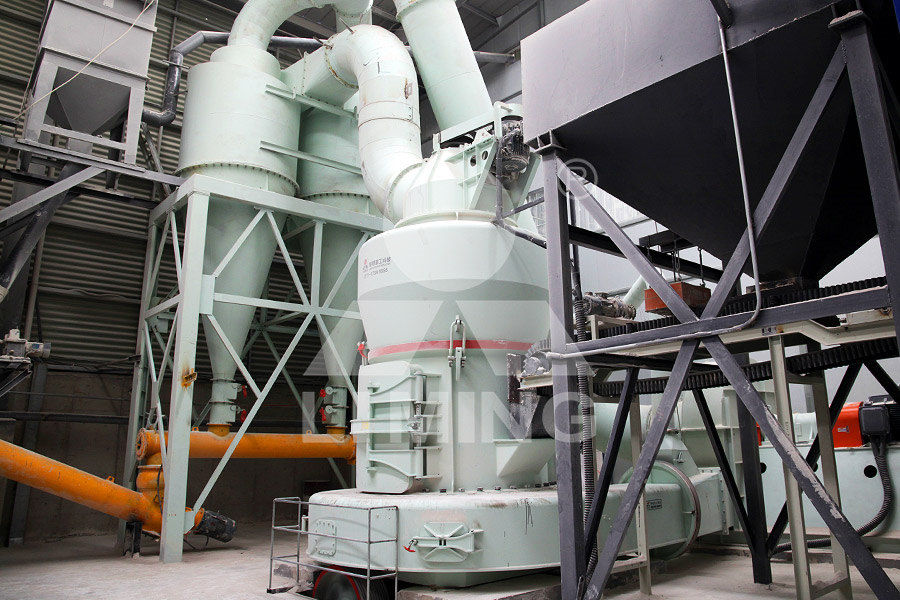
How to Process Copper Ore: Beneficiation Methods and Equipment
2023年3月13日 The oxidized ore is vulcanized by adding vulcanizing agent and then the flotation is carried out with the ordinary reagents of copper sulphide flotation Scope of application: mainly malachite, azurite and atacamite Process flow: Yellowcake, chemically U 3 O 8, is a uranium concentrate powder recovered from leach solutions Yellowcake is an intermediate step in processing uranium ores and nuclear fuel production Typically, yellowcake can be obtained through the conventional milling and chemical processing of uranium ore, forming a coarse powderYellowcake U3O8 Description Production nuclearpower2023年2月15日 Hematite, also spelled haematite, is a weakly magnetic iron ore with better floatability than magnetite and wide distributionIt is one of the most important raw materials for the extraction of iron Its composition is complex In addition to containing a small amount of magnetite, the impurity embedding of haematite has uneven particle size and high content of How to Extract Iron from Hematite: Methods and Plants2024年8月15日 A typical mineral processing plant is able to process various types of ores and mineral materials, including metal ores, nonmetallic ores, clay minerals, building materials and energy minerals Metallic ores: Gold ore, silver ore, copper ore , Mineral Processing Plants: What You Need to Know
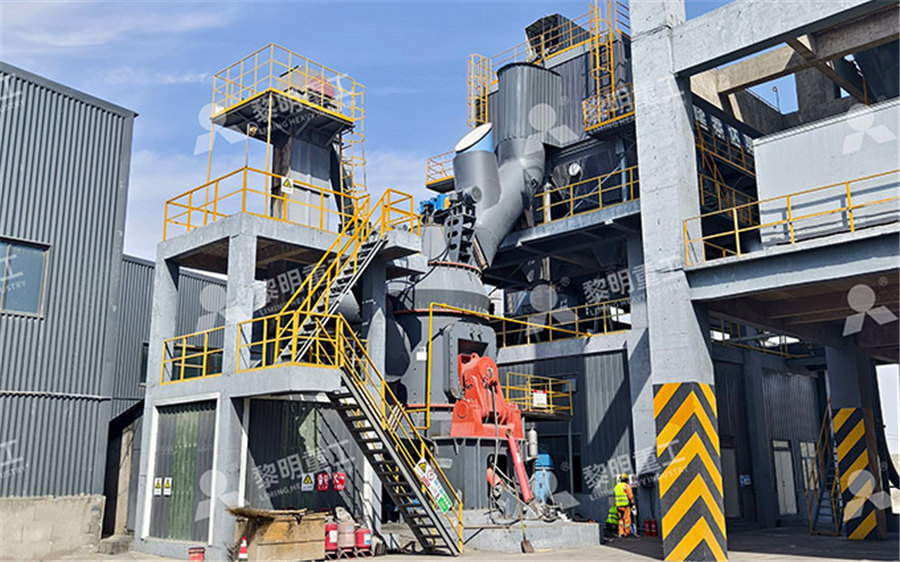
(PDF) Iron Ore Granulation for Sinter Production: Developments
2022年12月29日 The roles of iron ore, fuel, fluxes, and moisture in sintering granulation are also analyzed, and finally advanced granulation equipment and processes for industrial production, as well as their 2021年12月16日 applications, and give titanium products of the carbothermal reduction of titanium ore such as ilmenite expensive than the use of Mg However, the Hunter process can also produce T i powderTitanium: An Overview of Resources and Production Methods2022年7月30日 Study on the Basic Characteristics of Iron Ore Powder with Different Particle Sizes Zezheng Li 1,2,3,4,5, Yifan Li 1,2,3 2 Hebei Key Laboratory of Data Science and Application, North China University of Science and Technology, Tangshan and guide the sintering performance plant to choose the best ore allocation method, Study on the Basic Characteristics of Iron Ore Powder with The iron ore production has significantly expanded in recent years, owing to increasing steel demands in developing countries However, the content of iron in ore deposits has deteriorated and lowgrade iron ore has been processed Iron Ore Pelletizing Process: An Overview IntechOpen
.jpg)
Process optimization of a chrome ore gravity
2020年4月1日 On the other hand, since most plants are optimized for a specific size fraction (≥ 75 µm) and the tailings of chromite plants are generally characterized by fine particles, a recurring problem The invention discloses a sintering process of manganese ore powder The process comprises the following steps of: adding water to mix manganese ore powder, a binding agent, fuel, a fluxing agent and return ore as mixed ore, wherein the binding agent is formed by mixing manganese salt and organic matter and counts for 0630% of mass of the mixed ore, the fuel counts for 30 Sintering process of manganese ore powder Google Patentssintered ore were also appreciated by the ironmaking process Therefore, the sintering process eventually became the preferred choice for the briquetting of pulverised materials [34] 21 Sintering process and its chemical reactions The significance of sintering is that the lumping of pulverised ore from the mining process can be used to obtainApplication of deep learning in iron ore sintering process: a review2009年8月1日 Request PDF Recycling of steel plant mill scale via iron ore pelletisation process Mill scale is an iron oxide waste generated during steelmaking, casting and rolling Total generation of mill Recycling of steel plant mill scale via iron ore pelletisation process

Talcum powder manufacturing process PDF Free Download
2013年4月24日 1 Talcum Powder Manufacturing Process Within the talcum powder manufacturing process, crusher, grinding mill are utilized as talc powder making machine for powder production Most talc deposits are open pit mine Talc rock is found by giant spades Different ore types are sorted because they are removed in the seamThis process helps to increase the surface area of the ore, making it more accessible for subsequent grinding Grinding, on the other hand, involves further reducing the size of the crushed ore into a fine powder The crushed ore is transferred to a grinding mill, which contains heavyduty steel balls or rodsGold Refinery Process: From Raw Material to Pure Gold2018年7月11日 The iron ore production has significantly expanded in recent years, owing to increasing steel demands in developing countries However, the content of iron in ore deposits has deteriorated and lowgrade iron ore has been processed The fines resulting from the concentration process must be agglomerated for use in iron and steelmaking This chapter Iron Ore Pelletizing Process: An Overview Semantic Scholar2016年1月8日 The first commercial production of phosphate rock began in England in 1847 A wide variety of techniques and equipment is used to mine and process phosphate rocks in order to beneficiate lowgrade ores and remove impurities The eighth chapter of this book deals with mining and beneficiation of phosphate ore The principle and operating conditions of important Mining and Beneficiation of Phosphate Ore IntechOpen