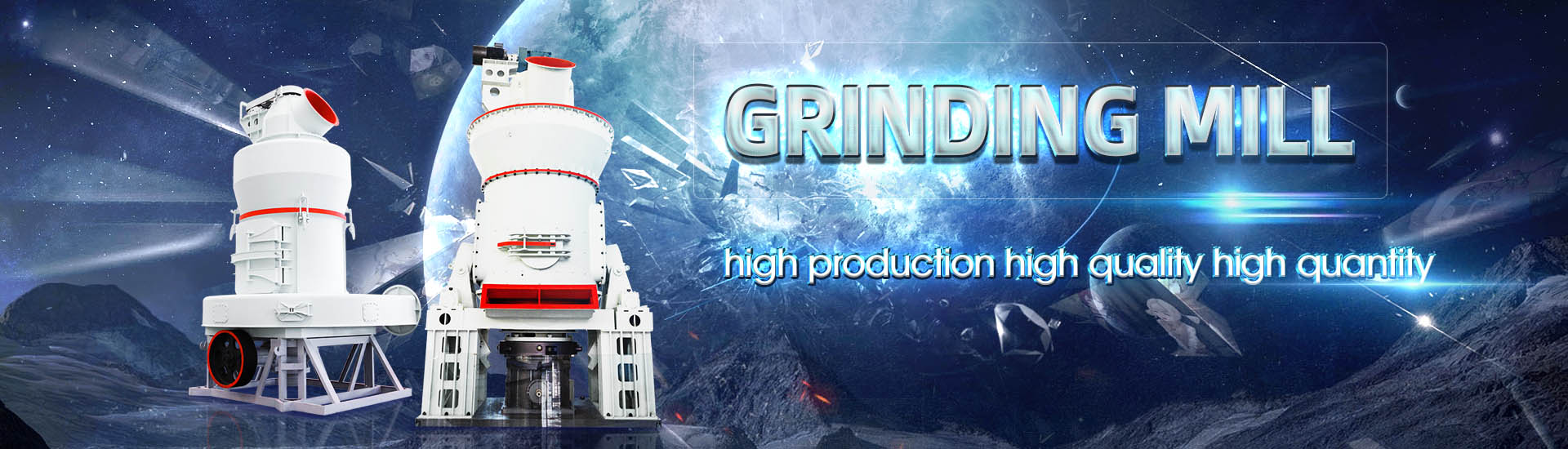
Specific equipment and process for crushing and grading wollastonite in limestone
.jpg)
Curious about Wollastonite Processing? Find Your Best
2024年2月22日 To process wollastonite into commercial grades, ore beneficiation is typically conducted to reduce or eliminate undesired associated minerals Based on mineral testing, the ore is found to contain wollastonite, The object of the present invention is to provide a kind of lowgrade highcalcium wollastonite processing method, raw material is chosen to obtain silicon after crushing Lime stone roughA kind of processing method of wollastonite Google PatentsTo be useful for many different applications, wollastonite must be processed; the processing should produce concentrates that are 97–99 percent pure wollastonite After drilling, blasting, Industrial Minerals of the United States Wollastonite–A Versatile 2024年5月8日 During this process, FTM mechanical engineers recommend using Raymond mills as the primary grinding equipment Raymond mills offer stable production capacity (8176 Mastering Wollastonite Processing: From Ore to Finest Powder

Limestone Quarrying and Processing: A LifeCycle Inventory
The LCI for limestone processing operations includes the inputs and outputs for each of the processes depicted in Figure 2 Specifically, processes and operations represented in this In ceramics, wollastonite decreases shrinkage and gas evolution during firing, increases green and fired strength, maintains brightness during firing, permits fast firing, and reduces crazing, PowerPoint PresentationWollastonite is formed when limestone/ dolomite is subjected to high temperature and pressure in the presence of silica bearing fluid as in skarn deposits or metamorphic rocks It occurs as WOLLASTONITE Indian Minerals Yearbook 2017 IBMWollastonite is unique in being the only white and acicular, nonmetallic mineral During crushing and grinding, it forms acicular particles having an aspect ratio (length vs diameter ratio) in the Wollastonites Springer

Wollastonite A Versatile Functional Filler PCI Magazine
2002年11月1日 The processing of wollastonite into commercial grades often requires beneficiation to reduce or remove unwanted minerals The ore is first crushed and milled 2023年2月28日 Learn everything you need to know about primary crushing, secondary crushing, and tertiary crushing in this comprehensive guide Discover the types of crushers used in each stage, their working principles, and the The Complete Guide to Primary Crushing, Secondary 2020年11月17日 The research presented here investigates the reaction mechanism of wollastonite in situ mineral carbonation for carbon dioxide (CO2) sequestration(PDF) Reaction Mechanism of Wollastonite In Situ 2023年9月4日 Iron ore pretreatment equipment The pretreatment stage of iron ore mainly includes crushing, screening, grinding, and grading processes Crushing and screening: The raw ore is sent to the crusher by the vibrating Iron Ore Beneficiation Plant Equipment For Mining
.jpg)
SIZE REDUCTION BY CRUSHING METHODS ResearchGate
2017年3月4日 The double jaw crusher is designed for crushing hard materials, also quarried materials, sand and gravel, and recycling [4, 5] crusher [4] The tie rod and compression spring ensure that the 2020年6月4日 The size reduction process of rocks in cone crushers is one of the most important issues, particularly for the secondary and tertiary stages of crushing operations In this study, 17 different rock types were considered for the evaluation of their size reduction variations that occurred in a laboratoryscale cone crusher Based on several mineralogical, physico Evaluation of size reduction process for rock aggregates in 2015年7月1日 The grading of the GI fines intermediate product represents the natural grading of the 0/250 μm fines of the different rocktypes, as generated during the VSI rockcrushing experiments PSDs of GI fines for all the 10 processed rocktypes are illustrated in Fig 12 a measured with a combination of SediGraph (⩽100 μm) and mechanical sieving (>100 μm), Sand production with VSI crushing and air classification: Understanding the most common rock types used in crushed stone production is essential for selecting the proper crushing process and rock crushing equipment Here are some of the most common types: Granite: With a Mohs hardness of around 6 to 7, granite is one of the most common rock types used in crushed stone productionThe Ultimate Guide on How to Crush Stone: Techniques and Equipment
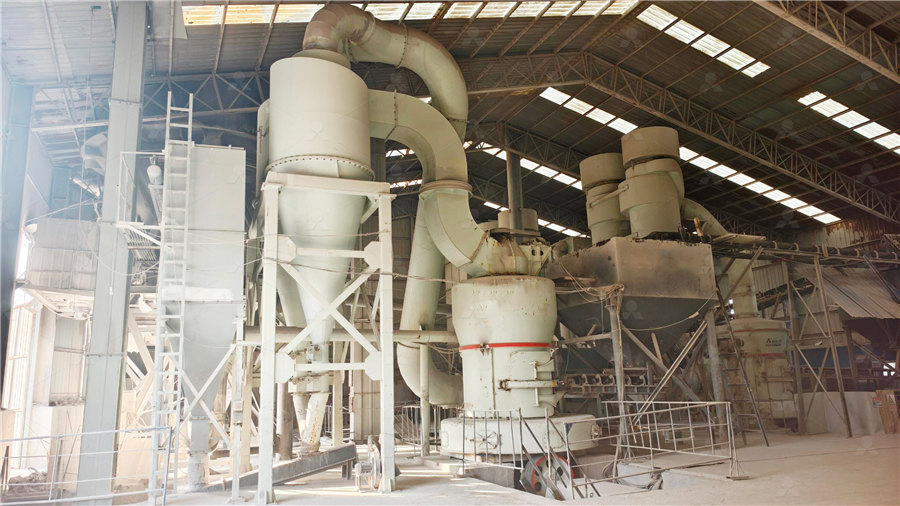
MeasurementControl for Crushing and Screening Process
2023年6月3日 It mainly includes crushing process control, crushing appliance fault diagnosis, and automatic distributing control Crushing Process Control To ensure the continuous, stable, and safe operation of the ore crushing production process, it is necessary to monitor the running state and parameters of key equipment (such as crusher and belt conveyor) in real time for 2018年7月4日 Calcining equipment of bauxite processing equipment: bauxite rotary kiln, which has advanced calcining mechanism, high quality of finished products, high degree of automation in overall operation, safe and environmentfriendly Crushing equipment: jaw crusher or hammer crusher, crushing large particles of bauxiteIntroduction to bauxite, processing process and equipment2012年6月9日 Regulators must use this process guidance note (PGN) to assess applications and write permits for mobile crushing and screeningMobile crushing and screening: process guidance note 3/16%PDF16 %âãÏÓ 4215 0 obj > endobj 4235 0 obj >/Encrypt 4216 0 R/Filter/FlateDecode/ID[87C03FABF6FB2246BC4F9AB649B4B217>]/Index[4215 26]/Info 4214 0 R/Length 101 AusIMM – Leading the way for people in resources
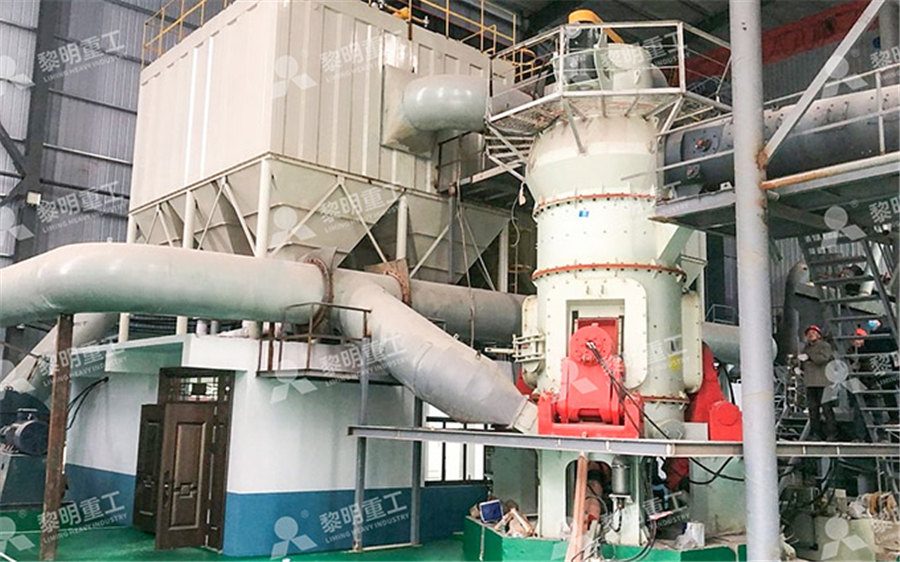
CLEANING, GRADING AND Isca
EQUIPMENTS FOR CLEANING, GRADING AND SEPARATION The operation of cleaning, grading and separation of the products are performed by exploiting the difference in engineering properties of the materials The equipments used are classified based upon the following characteristics of the material: 1 Size 2 Shape 3 Specific gravity or weight2021年7月6日 PDF Comminution: The key to optimizing concentrate, grade and recovery Find, read and cite all the research you need on ResearchGateComminution a Heart of Mineral Processing2019年10月8日 The crushing and grinding operations are an important part of the processing of mineral resources, and it is also operation with high investment and high energy consumption In the case of metal mines, equipment investment in crushing operations accounts for 65% to 70% of the total plant value, power consumption is about 50% to 65%, and steel consumption is as Crushing and Grinding Process JXSC Machine2023年6月30日 Over the last few decades, the demand for energyefficient mineralprocessing methods has continued The necessity to develop energyefficient technologies for the mineral industry will increase in the future, considering the exhaustion of highquality resources and severe environmental limitations The subject of this study is crushing equipment It is a Modeling and Improving the Efficiency of Crushing Equipment
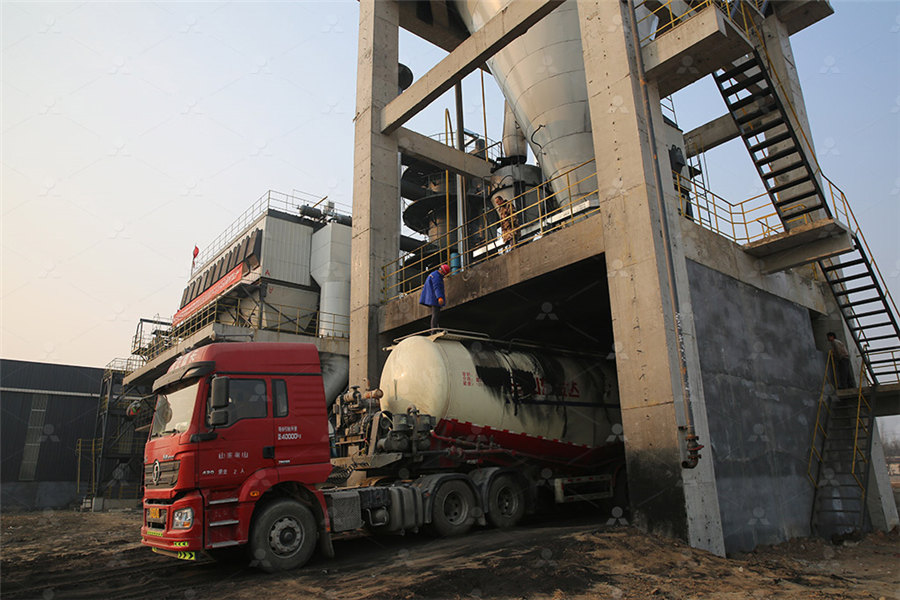
Physical Bauxite Processing: Crushing and Grinding of Bauxite
2022年1月23日 The equipment selected for the crushing area is chosen based on the physical characteristics of the raw bauxite and the capacity rates required Typical crusher types evaluated for a specific project include Jaw Crushers, Cone Crushers, highspeed Impactors or Hammermills, and lowspeed Sizers2022年7月20日 Process flow of limestone sand production line 1 Process flow of limestone manufactured sand Sand making: Through the crushed limestone, part of it is directly sent to the stockpile as a finished product, and the other part is crushed and made sand by the sand making machine Screening: The vibrating screen is also responsible for distinguishing the finished Limestone crushing, sand making and grinding process2023年10月30日 The selection and design of crushing equipment in the mineral processing industry are influenced by several key factors, all of which are critical for achieving efficient and effective ore processing Chief among these factors is the material's inherent characteristics The hardness, abrasiveness, moisture content, and size distribution of the ore significantly impact The selection and design of Crushing equipment Performance 2022年2月23日 The optimal deep learning model consisted of five hidden layers for the DNN predicting the ore production and four hidden layers for the DNN predicting the crusher utilization, each with 40 hidden neurons []The developed final deep learning model was evaluated for its ore production and crusher utilization prediction performance over ten days at the mineAdvanced Analytics for Mineral Processing SpringerLink
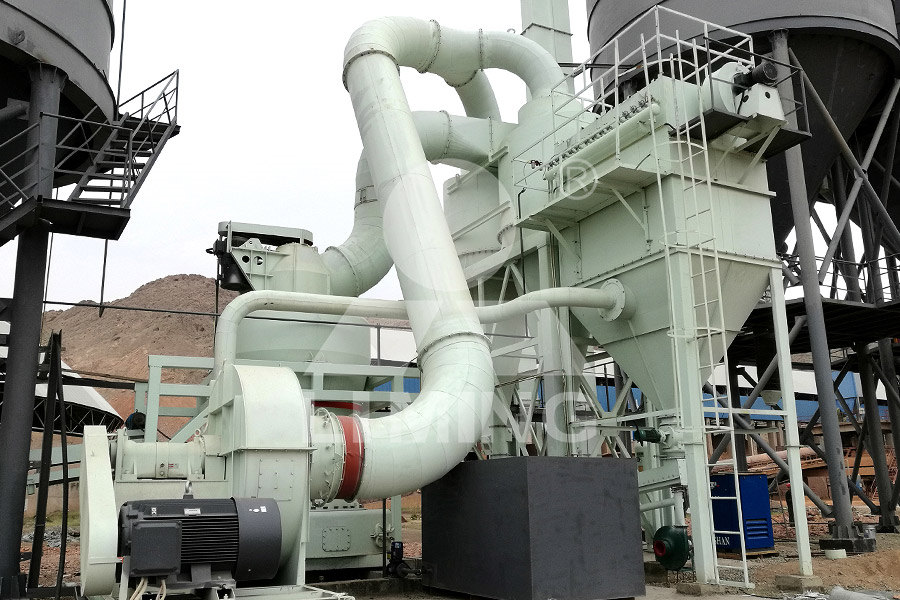
Construction aggregates: evaluation and specification
Particle Size Distribution (Grading) The particlesize distribution, or ‘grading’, is a fundamental property for all construction aggregates and often defines the product Grading is usually carried out by sieve analysis (Figure 3) The sample is passed through a sieve stack (wet or dry) and the weight proportion retained on each sieve is2019年11月4日 Limestone crushing process First stage: primary crushing Large pieces of limestone are uniformly fed through feeding equipment (such as vibrating feeder) and conveyed to the crushing equipment Generally, jaw Limestone Rock Crushing Flow Price JXSC Machineprocess flow diagram for limestone processing operations 3 list of tables 6 6 table 1 gross energy to produce one ton of limestone products table 2 water consumption for limestone quarrying and processing table 3 lci inputs for limestone quarrying and processing table 4 lci outputs for limestone quarrying and processing table 5Limestone Quarrying and Processing: A LifeCycle Inventory2024年7月17日 Crushing is a multistage process that includes primary crushing, secondary crushing, and tertiary crushing Different types of crushing equipment are used at each stage to meet various crushing requirements Types of Crushers: Choosing the Right One for Each
.jpg)
CO 2 Free Flux for Sustainable Iron Ore Pelletizing
2024年3月4日 The iron and steel manufacturing sector directly accounts for 7–9% of global CO2 emissions Raw material preparation, such as iron ore sintering, pelletizing, and cock making, is the major CO2 emitter As climate change becomes a bigger concern, steel manufacturers need to lower CO2 emissions without hindering efficiency or increasing costs In recent years, the 2014年8月25日 ecofriendly and valuable commercial wollastonite based ceramics have been obtained from the most hazardous industrial and agrowastes (cement kiln dust and rice husk ash) by reactive Cement kiln dust/rice husk ash as a low temperature route for 2022年1月1日 Firstly the most commonly used crushing and screening technologies, are discussed, including some typical flowsheets and a short review of new trends This is followed by a review of comminution circuits and equipment for magnetite ores including most typical flowsheets and advances in comminution minution and classification technologies of iron ore2009年5月1日 As evidence of that trend, Rubble Master’s sales have doubled every year over the past three years In 2008, sales of crushers reached in the area of 40 units, he says “It’s mainly because of the economics of onsite crushing,” notes Hottenroth “Onsite crushing eliminates a lot of trucking, which saves fuel, labor and insurance”Basics of Crushing, Grinding, and Chipping Grading and
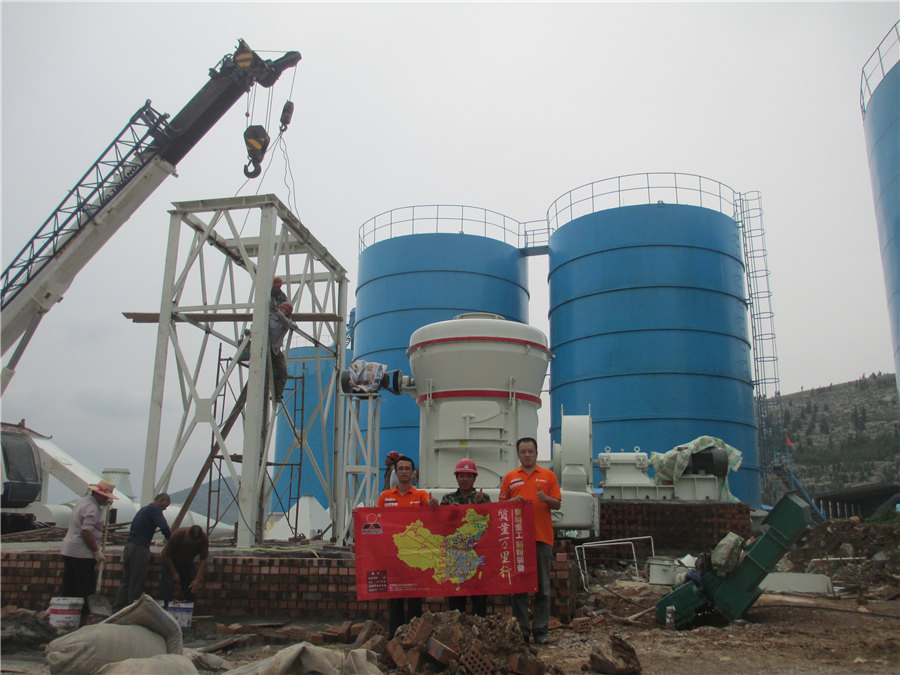
Wollastonite raw materials and their applications (a review)
1995年9月1日 Wollastonite (CaSiO 3 ) is a mineral that exhibits high in vitro reactivity to produce hydroxyapatite on surfaces [18], increase cellular viability, and promote differentiation of the osteoblast The pure, synthetic, crystalline betawollastonite having a BET specific surface area of 3 to 100 sqm/g and a crystal particle size of 001 to 2 um, which is the product made in accordance with the process which comprises subjecting an aqueous suspension of calcium oxide hydrate and a source of SiO 2 in a molar ratio of SiO 2:CaO of about 07 to about 13 to hydrothermal Synthetic wollastonite and a process for its manufacture(a) Wollastonite ore (b) Wollastonite powder (c, d) SEM micrographs of coarse and fine wollastonite particles (reprinted with permission from [])The size of wollastonite in ore form and the degree to which the shape and size are kept during processing determine the grades of wollastonite [45, 98]Crushing, sorting, and beneficiation procedures are used to produce A Review on the Role of Wollastonite Biomaterial in Bone Tissue 2023年2月28日 Learn everything you need to know about primary crushing, secondary crushing, and tertiary crushing in this comprehensive guide Discover the types of crushers used in each stage, their working principles, and the The Complete Guide to Primary Crushing, Secondary
.jpg)
(PDF) Reaction Mechanism of Wollastonite In Situ
2020年11月17日 The research presented here investigates the reaction mechanism of wollastonite in situ mineral carbonation for carbon dioxide (CO2) sequestration2023年9月4日 Iron ore pretreatment equipment The pretreatment stage of iron ore mainly includes crushing, screening, grinding, and grading processes Crushing and screening: The raw ore is sent to the crusher by the vibrating Iron Ore Beneficiation Plant Equipment For Mining 2017年3月4日 The double jaw crusher is designed for crushing hard materials, also quarried materials, sand and gravel, and recycling [4, 5] crusher [4] The tie rod and compression spring ensure that the SIZE REDUCTION BY CRUSHING METHODS ResearchGate2020年6月4日 The size reduction process of rocks in cone crushers is one of the most important issues, particularly for the secondary and tertiary stages of crushing operations In this study, 17 different rock types were considered for the evaluation of their size reduction variations that occurred in a laboratoryscale cone crusher Based on several mineralogical, physico Evaluation of size reduction process for rock aggregates in
.jpg)
Sand production with VSI crushing and air classification:
2015年7月1日 The grading of the GI fines intermediate product represents the natural grading of the 0/250 μm fines of the different rocktypes, as generated during the VSI rockcrushing experiments PSDs of GI fines for all the 10 processed rocktypes are illustrated in Fig 12 a measured with a combination of SediGraph (⩽100 μm) and mechanical sieving (>100 μm), Understanding the most common rock types used in crushed stone production is essential for selecting the proper crushing process and rock crushing equipment Here are some of the most common types: Granite: With a Mohs hardness of around 6 to 7, granite is one of the most common rock types used in crushed stone productionThe Ultimate Guide on How to Crush Stone: Techniques and Equipment2023年6月3日 It mainly includes crushing process control, crushing appliance fault diagnosis, and automatic distributing control Crushing Process Control To ensure the continuous, stable, and safe operation of the ore crushing production process, it is necessary to monitor the running state and parameters of key equipment (such as crusher and belt conveyor) in real time for MeasurementControl for Crushing and Screening Process2018年7月4日 Calcining equipment of bauxite processing equipment: bauxite rotary kiln, which has advanced calcining mechanism, high quality of finished products, high degree of automation in overall operation, safe and environmentfriendly Crushing equipment: jaw crusher or hammer crusher, crushing large particles of bauxiteIntroduction to bauxite, processing process and equipment
.jpg)
Mobile crushing and screening: process guidance note 3/16
2012年6月9日 Regulators must use this process guidance note (PGN) to assess applications and write permits for mobile crushing and screening