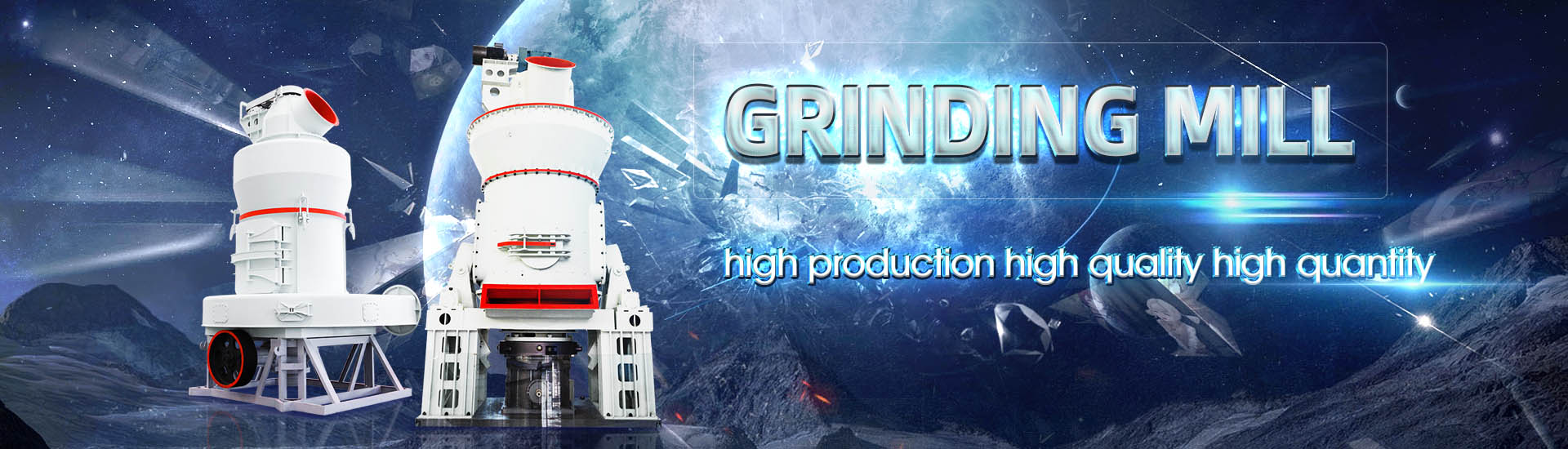
Ore grinding mill speed probe
.jpg)
(PDF) Optimization of mill performance by using online
2010年3月10日 It can provide online and accurate measurements of the degree of grinding ball fill and pulp position for timely decision making and actions 2023年10月27日 Grinding media play an important role in the comminution of mineral ores in these mills This work reviews the application of balls in mineral processing as a function of the A Review of the Grinding Media in Ball Mills for Mineral Processing 2021年1月1日 In this study the controller searches along the grind curves to either optimize the mill throughput or grind by means of the mill feed or rotational speed The proposed controller Optimizing grinding mill performance using extremum seeking 2023年1月1日 Optimization analysis of grinding mill for low grade PGE bearing chromite ore About 40% of energy can be saved using stirred mill than the ball mill In the present study, Size reduction performance evaluation of HPGR/ball mill and
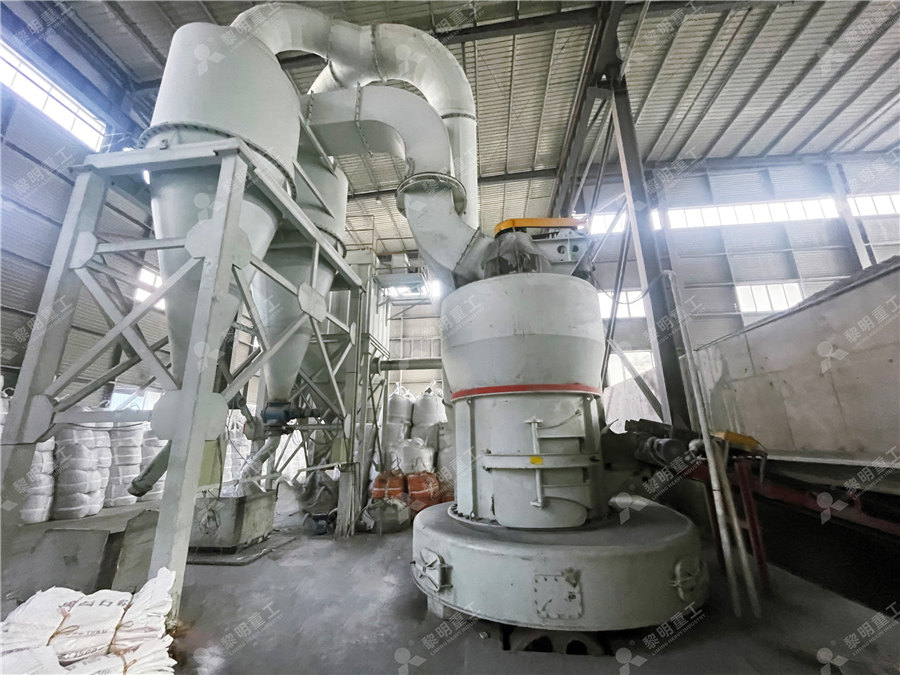
Rethinking Grinding Efficiency in Ball Mills
• Increases shear energy dissipation / power drawn by the mill for equivalent mass of media • Higher shear energy dissipation is achieved for wearing lifters (change in face angle) • Ball mill/tumbling mill is used to grind ores and minerals during beneficiation processes It is used for size reduction in minerals in a grinding circuit Ball mills are huge drumlike structure inside Monitoring the fill level of a ball mill using vibration sensing and 2015年4月9日 Grinding Mills and Their Types satyendra; April 9, 2015; 12 Comments ; autogenous grinding, ball mill, grinding mills, hammer mill, rod mill, roller mill, SAG,; Grinding Mills and Their Types In various fields of the Grinding Mills and Their Types IspatGuru2023年4月23日 Comminution includes the blasting, crushing, and grinding of ore to liberate valuable mineral particles mill speed, mill filling and grinding media properties[14](PDF) Grinding Media in Ball MillsA Review
.jpg)
Monitoring the fill level of a ball mill using vibration sensing and
2019年10月19日 Ball mills are extensively used in the size reduction process of different ores and minerals The fill level inside a ball mill is a crucial parameter which needs to be monitored regularly for optimal operation of the ball mill In this paper, a vibration monitoringbased method is proposed and tested for estimating the fill level inside a laboratoryscale ball mill A vibration Spherical grinding media are predominantly used in final stages of ore grinding The spherical balls change shape through breakage and wear shapes were studied in a pilot laboratory mill An inductive proximity probe, light emitting diode, Figure 511 Power variation with mill speed for different media shapes (J=15%) EFFECTS OF GRINDING MEDIA SHAPES ON BALL MILL 2023年10月27日 The ball mill is a rotating cylindrical vessel with grinding media inside, which is responsible for breaking the ore particles Grinding media play an important role in the comminution of mineral ores in these mills This work reviews the application of balls in mineral processing as a function of the materials used to manufacture them and the mass loss, as A Review of the Grinding Media in Ball Mills for Mineral flow inside the mill, showed that the collision energy of grinding media increased with mill speed from 22 to 45rpm giving more undersized product of 152mm, 112mm and 86mm and suddenly dropped Grinding Media in Ball MillsA Review ResearchGate
.jpg)
EFFECTS OF MILL ROTATIONAL SPEED ON THE BATCH GRINDING KINETICS OF
EFFECTS OF MILL ROTATIONAL SPEED ON THE BATCH GRINDING KINETICS OF A UG2 PLATINUM ORE By DINEO MOKGANYETJI MAKGOALE Submitted in accordance with the requirements for the degree of MAGISTER TECHNOLOGIAE in the subject ENGINEERING: CHEMICAL at the UNIVERSITY OF SOUTH AFRICA SUPERVISOR: Prof FRANCOIS 2023年10月17日 Ultrafine powder mill (threering / fourring mediumspeed micropowder mill) feed particle size ≤25 mm, production capacity 0545 t/h, production fineness 1503500 mesh,it is a highefficiency and lowconsumption ultrafine powder processing equipment that successfully replaces the traditional jet mill and complex process ball mill grinding and powder selection, How to choose a suitable ore powder grinding mill?2017年9月1日 Wet grinding was beneficial for the energy efficiency for both ores and promoted the selectivity of flotation particularly with sulphidic ore The wear of the mill and grinding media seemed more Fine grinding: How mill type affects particle shape ResearchGatethe mill speed, and mill load [11] Different types of multivariate methods such as partial least square (PLS) and radial basis function–PLS (RBFPLS) have been used in [12] to predict the variations in the slurry density and ball volume inside a laboratoryscale ball mill The ore grinding ability of a SAG mill wasMonitoring the fill level of a ball mill using vibration sensing and
.jpg)
Grinding Media in Ball MillsA Review Preprints
2023年4月24日 grinding media During the interaction of ore and grinding media, a complex physical and chemical system is formed, causing changes in particle size, pulp chemistry, surface chemistry, and crystal structure of minerals [13] The movement of grinding media which results in collisions is affected by mill design, mill speed, mill filling and 2024年8月8日 Unlock the secrets to ball mill efficiency with our comprehensive guide on choosing the right grinding media Learn Additionally, evaluate the milling conditions, including the type of mill, speed, duration, and whether the Ball Mill Success: A StepbyStep Guide to Choosing HGM ultrafine grinding mill can process nonmetallic ores with Mohs hardness less than 7 The equipment has stable operation, simple operation, long service life, low carbon and environmental protection There are 5 models of HGM SBM Ore Ultrafine Grinding Mill2024年2月27日 A grinding mill, semiautogenous (SAG) or autogenous (AG), is one of the most critical ore processing plants in the entire mineral processing circuit As shown in Fig 1 , a grinding mill requires shell liners to provide lifting to the ore and media, after which the collisional contacts induces ore breakage mechanism from which grinding product is generatedDevelopment of a Wear Sensor for Monitoring Grinding Mill Shell
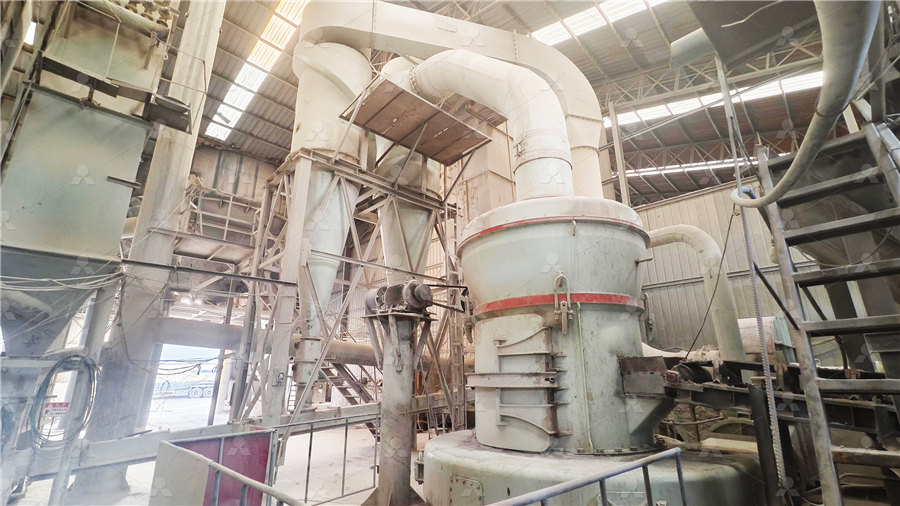
EFFECTS OF MILL ROTATIONAL SPEED ON THE BATCH GRINDING
critical speed below 50% was due to the need of lower energy consumption in milling processes The selection and breakage function parameters were determined and compared for fractions of critical speed First the grinding kinetics of the ore was determined and it was found that the material breaks in nonfirst order mannerSpherical grinding media are predominantly used in final stages of ore grinding The spherical balls change shape through breakage and wear shapes were studied in a pilot laboratory mill An inductive proximity probe, light emitting diode, Figure 511 Power variation with mill speed for different media shapes (J=15%) EFFECTS OF GRINDING MEDIA SHAPES ON BALL MILL 1 Grindability: The grindability of the ore affects the efficiency of the grinding mill Harder ores require more energy and longer grinding times, which can impact the mill's performance and operational costs 2 Media andliner Wear: The condition of the grinding media and liners affects the mill's efficiencyUnderstanding the operation of grinding mills in the mining and The dynamics of the ball load within a wetgrinding mill are examined, using measurements of torque and load t Group Leader: Precious Metals, Oredressing Division, Council for Mineral Technology, Private Bag X30l5, Randburg, Transvaal 2125, mill speed A conductivity probe mounted in the mill shellThe effects of mill speed and filling on the behaviour of the load
CFB石灰石脱硫剂制备96.jpg)
Population balance model approach to ball mill optimization in iron ore
1 Population balance model approach to ball mill optimization in iron ore grinding Patricia M C Faria1,2, Luís Marcelo Tavares2 and Raj K Rajamani3 1 Vale SA, Brazil 2 Department of operation (1) Structure parameters of grinding mill, including its specifications, model, aspect ratio, ore discharging method, and liner form (2) Various working parameters of grinding mill, including fraction of critical speed for grinding mill, filling rate for grinding mill, grinding concentration,grindingcycleload,etc(3)AndgrindOre Grinding Methods and Process of Ore GrindingComminution is an important process in mineral processing, power plants, cement production and pharmaceutical industries It is costly and an inefficient process in terms of energy requirements and steel consumption related to grinding media and liners Spherical grinding media are predominantly used in final stages of ore grinding The spherical balls change shape through Effects of grinding media shapes on ball mill performance2022年5月23日 Grinding experiments were conducted in a laboratoryscale stirred mill on a lowgrade PGE bearing chromite ore HighPressure Grinding Rolls (HPGR) product of −1 mm was used as feed material to Modeling and application of stirred mill for the coarse grinding

Grinding Modeling and Energy Efficiency in Ore/Raw
2022年8月31日 The grinding speed of ore and its component minerals decreased exponentially with the grinding time, and the instantaneous grinding speed of 0 min was negatively correlated with the feed sizes The rapidly out of the mill depends on the following main factors: properties of ores in the mill (mass, size, hardness, density and granulometric composition of particles): characteristics of grinding agents (mass, density, size and distribution of balls); rotation speed of the mill; density of straw during wet grinding [5]Control of ball mill operation depending on ball load and ore 2014年2月1日 Besides, the impact force on the lifter was affected by mill speed, grinding media filling, lifter height and iron ore particle The maximum percent of the impact force between 600 and 1400 N is Effects of slurry filling and mill speed on the net power draw of a A Review of the Grinding Media in Ball Mills for Mineral Processing, 2023 The ball mill is a rotating cylindrical vessel with grinding media inside, which is responsible for breaking the ore particles Grinding media play an important role in the comminution of mineral ores in these millsEffects of Grinding Media Shapes on Ball Mill Performance
.jpg)
(PDF) Reducing Grinding Energy and Cost Magnetite Iron Ore
The results of the analyses clearly shows that using a sieve of +180µm and its bottom 180µm, the best time for grinding 05kg of Itakpe iron ore with 3kg of grinding media and a mill speed of 92 rpm is 8 minutes, yielding 1710% fines and 8290% coarse, 08 mill critical speed measured 1520% fines and 8480% coarse2017年10月26日 The following are factors that have been investigated and applied in conventional ball milling in order to maximize grinding efficiency: a) Mill Geometry and Speed – Bond (1954) observed grinding efficiency to be a function of ball mill diameter, and established empirical relationships for recommended media size and mill speed that take this factor into Factors Affecting Ball Mill Grinding Efficiency2017年7月3日 Critical Speed Power Speed Curves Critical speed has been defined and dealt with by many writers It is the speed at which the centrifugal and centripetal forces, acting on an infinitely small particle traveling on and with the breast of the mill, are equal Then the particle will not leave its position It becomes part of a “flywheel”Variables Affecting Grinding Mill Power 911Metallurgistcritical speed below 50% was due to the need of lower energy consumption in milling processes The selection and breakage function parameters were determined and compared for fractions of critical speed First the grinding kinetics of the ore was determined and it was found that the material breaks in nonfirst order mannerEFFECTS OF MILL ROTATIONAL SPEED ON THE BATCH GRINDING
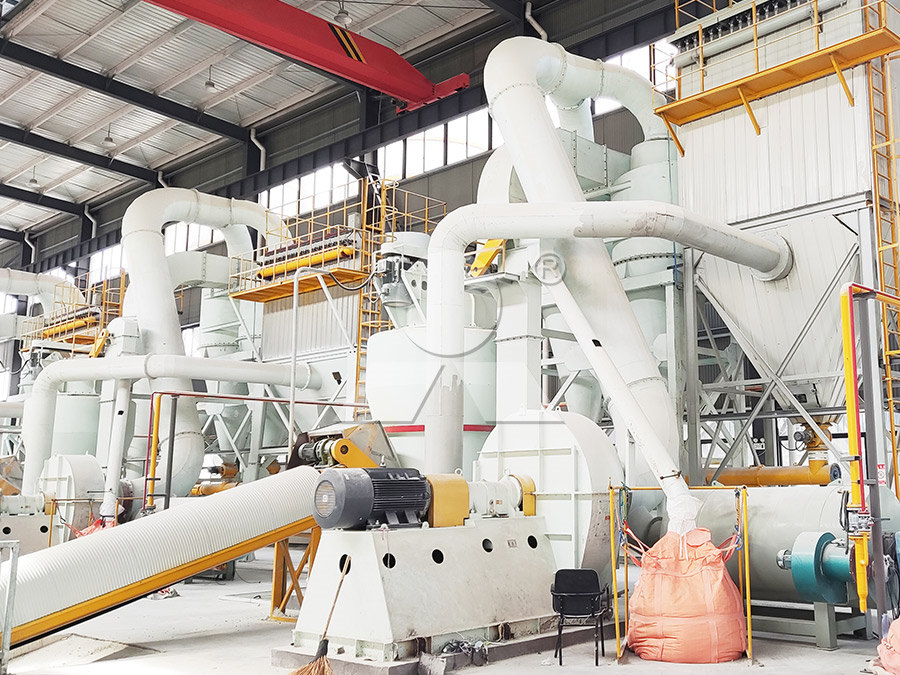
Grinding Mills and Their Types IspatGuru
2015年4月9日 Grinding Mills and Their Types satyendra; April 9, 2015; 12 Comments ; autogenous grinding, ball mill, grinding mills, hammer mill, rod mill, roller mill, SAG,; Grinding Mills and Their Types In various fields of the 2023年4月23日 Comminution includes the blasting, crushing, and grinding of ore to liberate valuable mineral particles mill speed, mill filling and grinding media properties[14](PDF) Grinding Media in Ball MillsA Review2019年10月19日 Ball mills are extensively used in the size reduction process of different ores and minerals The fill level inside a ball mill is a crucial parameter which needs to be monitored regularly for optimal operation of the ball mill In this paper, a vibration monitoringbased method is proposed and tested for estimating the fill level inside a laboratoryscale ball mill A vibration Monitoring the fill level of a ball mill using vibration sensing and Spherical grinding media are predominantly used in final stages of ore grinding The spherical balls change shape through breakage and wear shapes were studied in a pilot laboratory mill An inductive proximity probe, light emitting diode, Figure 511 Power variation with mill speed for different media shapes (J=15%) EFFECTS OF GRINDING MEDIA SHAPES ON BALL MILL
.jpg)
A Review of the Grinding Media in Ball Mills for Mineral
2023年10月27日 The ball mill is a rotating cylindrical vessel with grinding media inside, which is responsible for breaking the ore particles Grinding media play an important role in the comminution of mineral ores in these mills This work reviews the application of balls in mineral processing as a function of the materials used to manufacture them and the mass loss, as flow inside the mill, showed that the collision energy of grinding media increased with mill speed from 22 to 45rpm giving more undersized product of 152mm, 112mm and 86mm and suddenly dropped Grinding Media in Ball MillsA Review ResearchGateEFFECTS OF MILL ROTATIONAL SPEED ON THE BATCH GRINDING KINETICS OF A UG2 PLATINUM ORE By DINEO MOKGANYETJI MAKGOALE Submitted in accordance with the requirements for the degree of MAGISTER TECHNOLOGIAE in the subject ENGINEERING: CHEMICAL at the UNIVERSITY OF SOUTH AFRICA SUPERVISOR: Prof FRANCOIS EFFECTS OF MILL ROTATIONAL SPEED ON THE BATCH GRINDING KINETICS OF 2023年10月17日 Ultrafine powder mill (threering / fourring mediumspeed micropowder mill) feed particle size ≤25 mm, production capacity 0545 t/h, production fineness 1503500 mesh,it is a highefficiency and lowconsumption ultrafine powder processing equipment that successfully replaces the traditional jet mill and complex process ball mill grinding and powder selection, How to choose a suitable ore powder grinding mill?
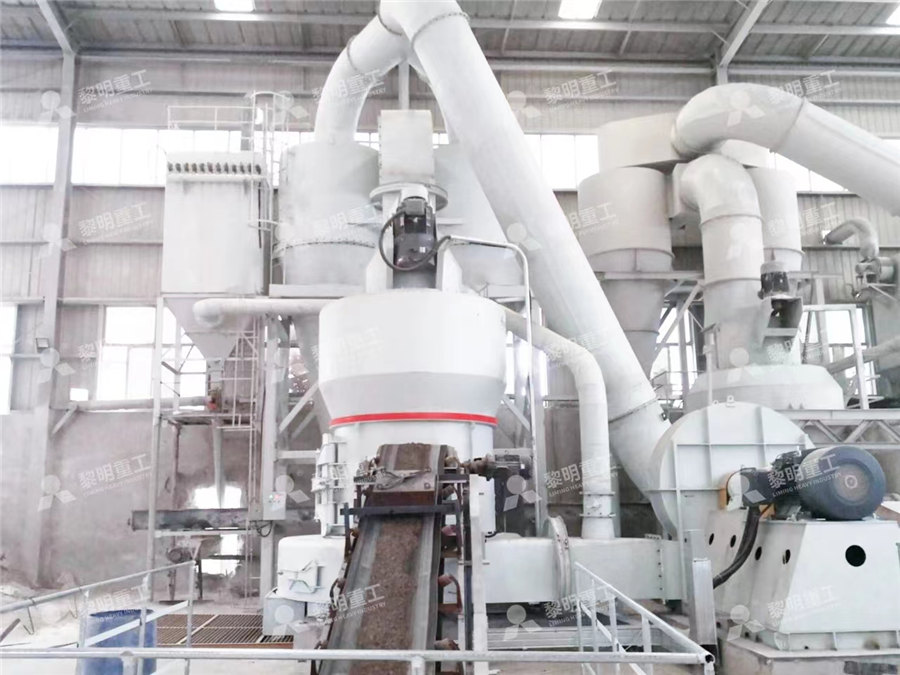
Fine grinding: How mill type affects particle shape ResearchGate
2017年9月1日 Wet grinding was beneficial for the energy efficiency for both ores and promoted the selectivity of flotation particularly with sulphidic ore The wear of the mill and grinding media seemed more the mill speed, and mill load [11] Different types of multivariate methods such as partial least square (PLS) and radial basis function–PLS (RBFPLS) have been used in [12] to predict the variations in the slurry density and ball volume inside a laboratoryscale ball mill The ore grinding ability of a SAG mill wasMonitoring the fill level of a ball mill using vibration sensing and