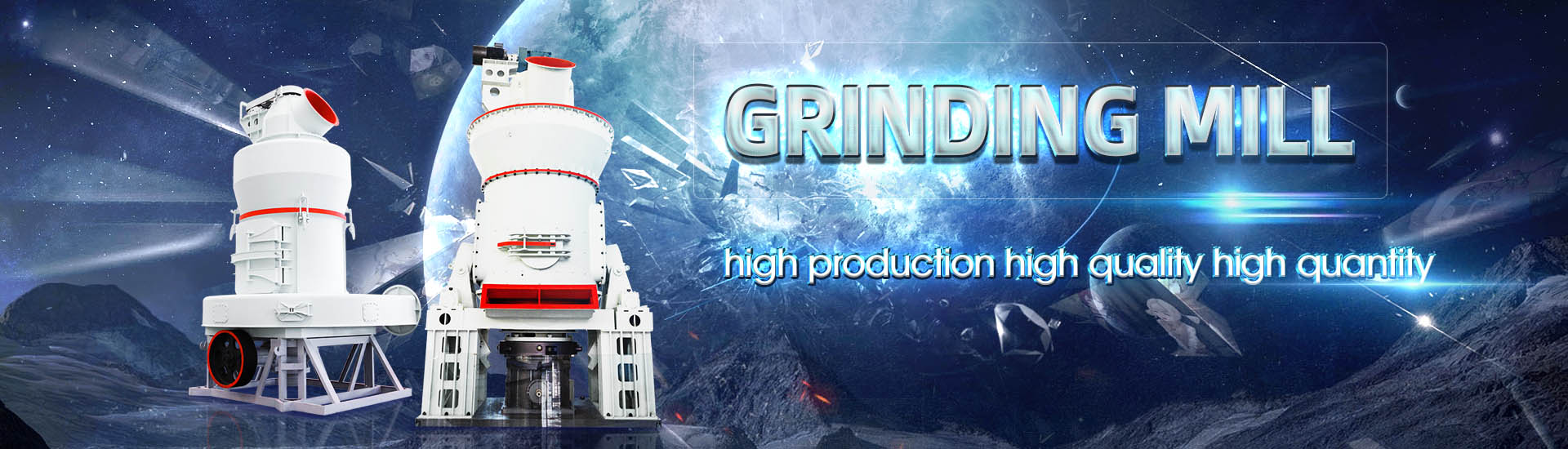
Vertical grinding ore grinding machine feed particle size

RECENT DEVELOPMENTS IN COARSE GRINDING USING VERTICAL
The feed size was approximately 70um and both the laboratory ball mill and laboratory vertical mill utilized 5mm steel shots as the grinding media The energy efficiency benefit to the vertical mill When combined with coarseparticle flotation technology, which allows improved metal recoveries at a coarser flotation feed size, the combination of using more powerefficient grinding Flowsheet of the Future: HighPressure Grinding Rolls, Vertical 2018年6月1日 In this article the effect of grinding media size distribution and feed material particle size distribution (PSD) on the product fineness requirements were investigated A Effect of ball and feed particle size distribution on the milling The FLS Tower Mill (FTM) reduces energy and media consumption, while minimising water usage in secondary and tertiary wet grinding of minerals The tower mill is a robust, proven FLS Tower Mill A vertical leap in fine grinding
.jpg)
Stirred media mills in the mining industry: Material grindability
2020年6月1日 Stirred media mills are used by the mining industry for ultrafine grinding to enhance liberation, and to decrease particle sizes of industrial minerals to tailor functional 2021年9月1日 Feed size, product size and energy data from pilot scale grinding tests were evaluated with material characterization tests Based on energysize reduction models Predicting the grinding energy of vrm depending on material 2022年10月26日 Through the JK dropweight test, the batch grinding test, and the populationbalance kinetic model of grinding with the Simulink platform, the grinding characteristics of the two types of ores and the particlesize Research on Grinding Characteristics and Comparison 2019年4月16日 Conference: Applying a Successful Technology from the Cement Industry: Advantages of Grinding Ore in a VerticalRollerMill; At: Antalya, Türkey(PDF) LEARNING FROM OTHER INDUSTRIES; WHY THE
.jpg)
Flowsheet of the Future: HighPressure Grinding Rolls, Vertical
Flowsheet of the Future: HighPressure Grinding Rolls, Vertical Stirred Mill, Coarse Particle Flotation, Vertical Stirred Regrind Mill *M van de Vijfeijken1, B Dierx2, E Wasmund3, J Concha4, J Hernandez5, M Sherman6 1Swiss Tower Mills Minerals AG Haselstrasse 1, 5400 Baden, Switzerland 2Weir Minerals2019年10月11日 The d 50 value is the average particle size of this particle size distribution This means that 50% of the particles are finer and 50% are coarser than d 50 (see figure 1, marked with a red line) Bulk materials with the same d 50 value Grinding: benefits of particle size modification Feed Strategy2018年2月1日 Feed size was divided into two fractions of (+238 −4) and (+2 −238) millimeters, from which different feeds with different weight and size percent values were fed to mill at three feeds of Effect of ball and feed particle size distribution on the milling Ore grinding machines can be divided into many types according to different Vertical Shaft Compound Crusher; Ball Mills; Batch Small Ball Mill; Generally, when the feed particle size is below 30mm and the product particle size is not less than 1mm, the rod mill is more efficient Grinding media material When selecting media Ore Grinding Machines: Ball Mill, Rod Mil Grinding Media
.jpg)
Estimation of Grinding Time for Desired Particle Size Distribution
2020年1月3日 Iron ores obtained from different sources differ in their chemical and physical properties These variations make the process of grinding a difficult task The work carried out in this context focuses on three different samples of iron ore, viz, high silica high alumina, low silica high alumina, and low silica low alumina The grinding process for all the three iron ores is 2020年5月28日 The feed samples of X, Y, and Z iron ores were ground in the BBM (ball mill refers to a BBM of size 300 mm × 300 mm with smooth liners) to identify the PSD, BWI, and RT of each ore Grinding experiments were conducted according to Bond’s standard test procedure []For each iron ore sample, the RT taken to produce 250% circulating load in the BBM was Investigation on Iron Ore Grinding based on Particle Size Distribution 2019年3月28日 The feedparticle size and the hardness of the mineral sample affect the grinding behavior The product particle size is mainly 071 times the feedparticle size, and the other fine particle sizes Research on prediction model of ore grinding particle size distribution2022年2月28日 An investigation conducted on magnetite ore grinding with a dry HPGR machine to reduce the particle size from 50 mm to 90 µm has revealed that using two stages HPGR closed circuit with an air classifier can reduce energy consumption by 46% compared to a circuit in which there is a tertiary crushing with a wet ball millGrinding SpringerLink

Estimation of Grinding Time for Desired Particle Size Distribution
Estimation of Grinding Time for Desired Particle Size Distribution crushing machine, all the three iron ore samples were crushed to −3 mm and analyzed for the desired P 80 passing (−150 μm) and percentage of hematite liberated in the three feed iron ore samples The – 150μm feed size fractions were selected to determine the nominal2023年7月10日 principal grinding methods used in mineral ore processing, reducing the particle size from 500 mm to sub15 µ m through ultrafine grinding [ 23 ] Energies 2023 , 16 , x FO R P EER RE VIEW 5 of 41(PDF) EnergyEfficient Advanced Ultrafine Grinding of 2022年3月9日 In this article we focused on the ways how to optimize the particle size in the grinding process of the feed mill However, there is still much to learn in order to understand the animal biology and the effect of particle size on its Importance and optimization of particle size in animal 2017年11月1日 Besides feed composition, as the most important factor that determines the efficiency of feed utilization by pigs, feed structure (particle size) and feed form (mash, pellets) are also important for the optimal nutrient utilization (Wondra et al, 1995a, Choct et al, 2004, Thorsten, 2011, Ball et al, 2015)Importance of feed structure (particle size) and feed form
.jpg)
(PDF) Grinding Media in Ball MillsA Review ResearchGate
2023年4月23日 observed that 30mm diameter balls were better than 10 and 20mm diameter balls in grinding a quartzite ore of feed size 8 to +56mm However, there was an increa se in efficiency when the feed Download scientific diagram Particle size distribution (PSD) of feed and ground samples from publication: Influence of dry grinding on physicochemical and surface properties of talc In this Particle size distribution (PSD) of feed and ground samples2012年6月1日 The feed material is typically composed of the BFRs and the catalyst, both in powder form As the cylinder starts to rotate, the grinding balls inside the cylinder crush and grind the feed Grinding in Ball Mills: Modeling and Process Control2017年3月4日 Comminution is particle size reduction of m aterials Ball mills are used for wet grinding iron ore, g old/copper ore, These vertical grinding mills are wide ly used in SIZE REDUCTION BY GRINDING METHODS ResearchGate
.jpg)
FLS Tower Mill A vertical leap in fine grinding
A vertical leap in fine grinding M 0124 100016ENG V2 Introducing our newest agitated steel media mill for fine grinding Particle size Recovery The double helix screw provides efficient energy transfer to Energyefficient wet grinding of metallic ores and minerals from a feed particle size 80%passing (F80) Download scientific diagram Particle size distribution of pilot grinding circuit feeds from publication: Vertical mill simulation applied to iron ores The application of vertical mills in Particle size distribution of pilot grinding circuit feeds5 Ball mills are used for wet grinding iron ore, gold/copper ore, nickel ore and other ores, as well as lime/limestone for flue gas desulphurisation systems, coal and other raw materialsSIZE REDUCTION BY GRINDING METHODS By ResearchGate2024年6月11日 In this study, the evolution behavior of the particle size distribution during the grinding process was examined with fractal theory According to the distribution index k of the Rosin–Rammler–Benne model, the Effect of Solid Concentration on Particle Size
.jpg)
Evolution of grinding energy and particle size during dry ball
2020年10月1日 Several comminution laws have been proposed to link the consumed energy to a characteristic particle size of the powder The popular models are those of Rittinger [4], Bond [5] and Kick [6]While the Bond and Kick models are mostly employed for coarse and intermediate size grinding, the Rittinger model is better suited for fine comminution [7]31 Particle size distribution of ground products from different feed sizes In the lowspeed grinding test, the particle size distribution results and abrasion behavior characteristics of the ground products were investigated by changing the influence factors such as the feed size, sample type and grinding timeResearch on the characteristics of particles size for grinding 2023年7月20日 Except those that process some placers, almost all mineral processing plants have grinding operations, in which materials are crushed by the impact and abrasive action of grinding medium (steel rod, steel ball, gravel, or ore block itself) to meet the requirements of separation operation, and the particle size of the product is generally less than 5 mm Based Ore Grinding SpringerLink3Into the grinding particle size, generally up to 5% of the diameter of the grinding rollers, large grinding feed size up to 150 ~~ 200mm, the superior performance of equipment and technology, single output, the high rate of operation of equipment, metal wear than a ball millVertical stone milling machine
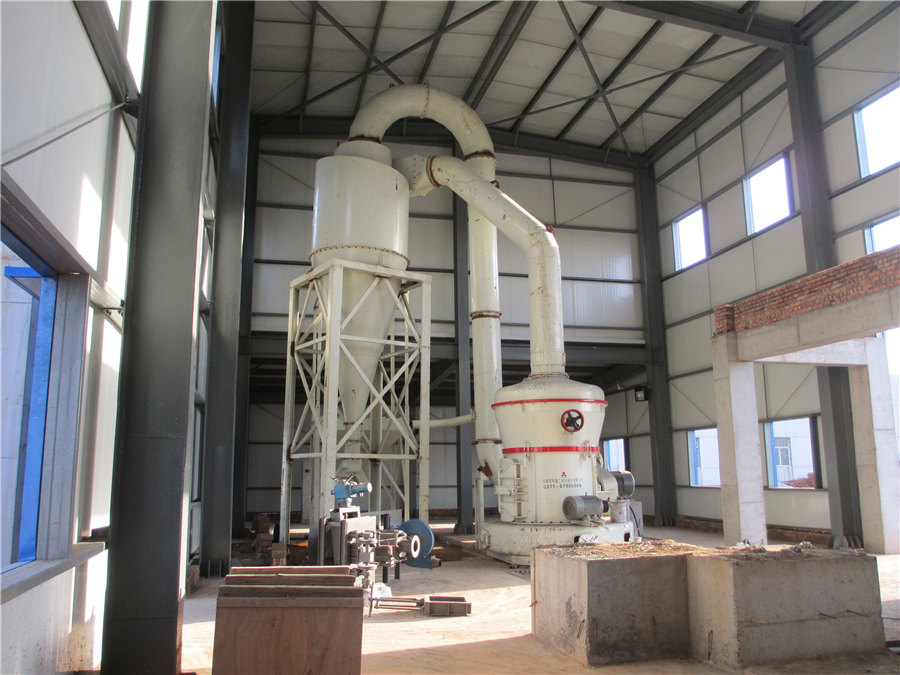
PREDICTING THE PRODUCT PARTICLE SIZE DISTRIBUTION FROM A VERTICAL
laboratory vertical stirred mill The grinding results show that changes in the feed size, stirring speed, and grinding media size are the primary parameters affecting the particle breakage rate The test data also show that a finer product size is obtained when the mill operates at higher stirring speeds while using smaller grinding media2015年3月15日 For the grinding tests, a Loesche mill LM45 (table diameter 045 m) is used (Fig 2a) This pilot scale mill is a special development for ore grinding, which is reflected by several features The mill has four rollers, which are able to stress the particle bed with grinding pressures of up to 5000 kN/m 2Research of iron ore grinding in a verticalrollermillselect the appropriate size of the grinding media in order to obtain optimum technological results in the fine particles yield and the obtained fineness in grinding products for variable particle size distribution of the feed 4 Results of investigations The obtained particle size of the ore from the electromagnetic mill milling products is Analysis of a grinding efficiency in the electromagnetic mill for 2018年10月8日 Particle shape also has a significant effect on the fracture characteristics of the material (Pourghahramani and Forssberg 2005;Tavares 2007) Although researches in this regard have shown that (PDF) Iron Ore Concentrate Particle Size Controlling Through

(PDF) LEARNING FROM OTHER INDUSTRIES; WHY THE
2019年4月16日 Conference: Applying a Successful Technology from the Cement Industry: Advantages of Grinding Ore in a VerticalRollerMill; At: Antalya, TürkeyFlowsheet of the Future: HighPressure Grinding Rolls, Vertical Stirred Mill, Coarse Particle Flotation, Vertical Stirred Regrind Mill *M van de Vijfeijken1, B Dierx2, E Wasmund3, J Concha4, J Hernandez5, M Sherman6 1Swiss Tower Mills Minerals AG Haselstrasse 1, 5400 Baden, Switzerland 2Weir MineralsFlowsheet of the Future: HighPressure Grinding Rolls, Vertical 2019年10月11日 The d 50 value is the average particle size of this particle size distribution This means that 50% of the particles are finer and 50% are coarser than d 50 (see figure 1, marked with a red line) Bulk materials with the same d 50 value Grinding: benefits of particle size modification Feed Strategy2018年2月1日 Feed size was divided into two fractions of (+238 −4) and (+2 −238) millimeters, from which different feeds with different weight and size percent values were fed to mill at three feeds of Effect of ball and feed particle size distribution on the milling
.jpg)
Ore Grinding Machines: Ball Mill, Rod Mil Grinding Media
Ore grinding machines can be divided into many types according to different Vertical Shaft Compound Crusher; Ball Mills; Batch Small Ball Mill; Generally, when the feed particle size is below 30mm and the product particle size is not less than 1mm, the rod mill is more efficient Grinding media material When selecting media 2020年1月3日 Iron ores obtained from different sources differ in their chemical and physical properties These variations make the process of grinding a difficult task The work carried out in this context focuses on three different samples of iron ore, viz, high silica high alumina, low silica high alumina, and low silica low alumina The grinding process for all the three iron ores is Estimation of Grinding Time for Desired Particle Size Distribution 2020年5月28日 The feed samples of X, Y, and Z iron ores were ground in the BBM (ball mill refers to a BBM of size 300 mm × 300 mm with smooth liners) to identify the PSD, BWI, and RT of each ore Grinding experiments were conducted according to Bond’s standard test procedure []For each iron ore sample, the RT taken to produce 250% circulating load in the BBM was Investigation on Iron Ore Grinding based on Particle Size Distribution 2019年3月28日 The feedparticle size and the hardness of the mineral sample affect the grinding behavior The product particle size is mainly 071 times the feedparticle size, and the other fine particle sizes Research on prediction model of ore grinding particle size distribution
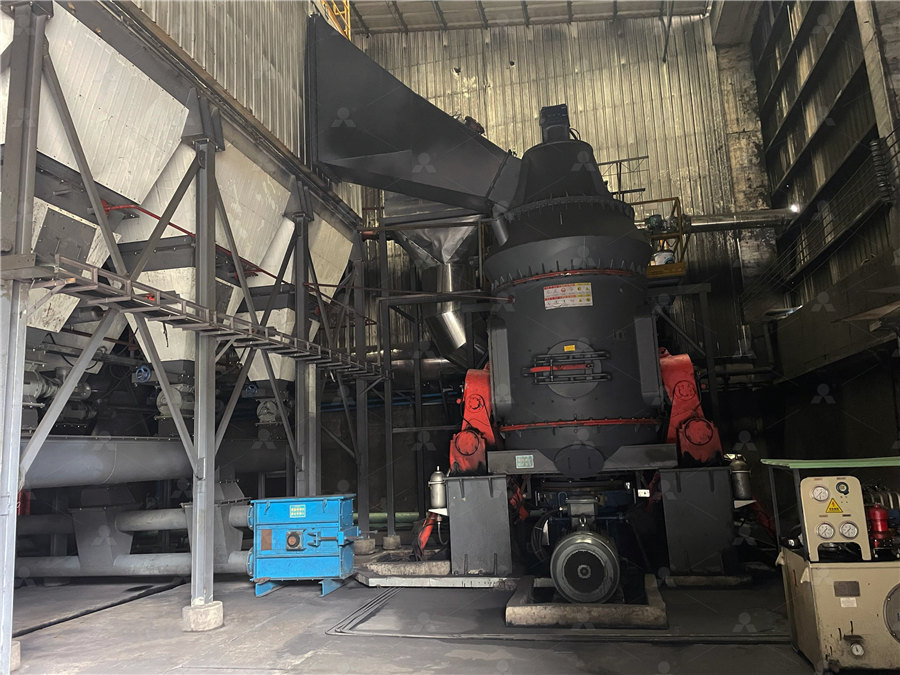
Grinding SpringerLink
2022年2月28日 An investigation conducted on magnetite ore grinding with a dry HPGR machine to reduce the particle size from 50 mm to 90 µm has revealed that using two stages HPGR closed circuit with an air classifier can reduce energy consumption by 46% compared to a circuit in which there is a tertiary crushing with a wet ball millEstimation of Grinding Time for Desired Particle Size Distribution crushing machine, all the three iron ore samples were crushed to −3 mm and analyzed for the desired P 80 passing (−150 μm) and percentage of hematite liberated in the three feed iron ore samples The – 150μm feed size fractions were selected to determine the nominalEstimation of Grinding Time for Desired Particle Size Distribution