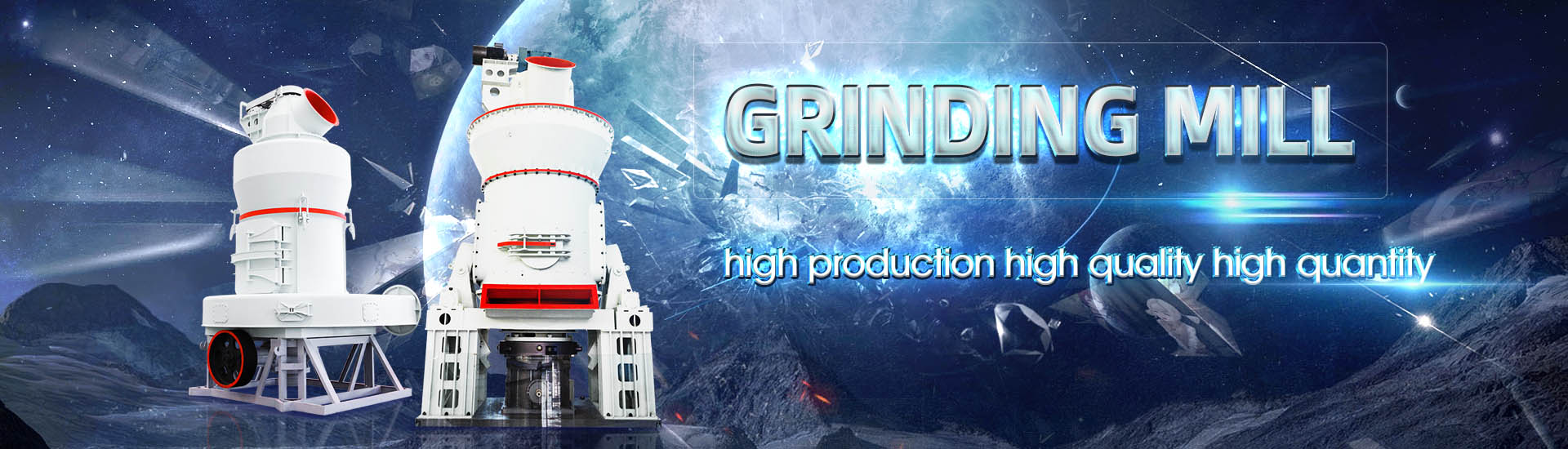
Talc powder grinding production line particle size
.jpg)
Particle size distribution, chemical and mineralogical
The efficiency of talc mechanical activation by means of two different mechanoactivators centrifugal and attrition mill is investigated in this study and the comparative analysis of theHosokawa Alpine sets new standards with this system: achievable fineness values with the dry grinding of powders down to d97 = 1μm At the same time, the particle shape remains intact – ULTRAFINE GRINDING Hosokawa Alpine2019年10月31日 In this study, we investigate the effect of the ball size in a highenergy ball mill on the comminution rate and particle size reduction Highenergy ball milling at 2000 rpm producesEffects of Ball Size on the Grinding Behavior of Talc 1998年8月1日 Room temperature grinding of talc powder was conducted by a planetary ball mill using media balls of different sizes The grinding behavior of the talc sample was investigated Correlation of powder characteristics of talc during Planetary Ball
.jpg)
Mechanochemical effects on talc during fine grinding process in a
2009年7月1日 Talc showed minimum particle size when the value of P/N 2 was 60 × 10 − 9 bar/rpm 2 This value was obtained when the jet mill was operated at a classifier rotational We present a study of talc grinding in an Alpine 100 AFG opposed air jet mill with an inline laser granulometer The conditions for steady state operation have been determined from Talc grinding in an opposed air jet mill: startup, product quality 2002年12月18日 The particle size distribution measured by the Insitec inline laser granulometer in continuous grinding experiments gives a measurement of the median size of the talc Talc grinding in an opposed air jet mill: startup, product quality 2020年8月12日 Within the scope of the research, the effects of operating parameters including media filling ratio, solid mass fraction, grinding media size, and grinding time were studied Impact of Operating Parameters on the Breakage Process of Talc
CFB石灰石脱硫剂制备——磨机公众号12.8 推送案例(8)51.jpg)
Effect of Hydrophobicity on Talc Grinding in Attritor Mill
2024年3月10日 The change in talc particle size in dry and wet grinding modes was recorded along with monitoring the structural change by Xray diffraction (XRD) and scanning electron 2020年10月1日 Several comminution laws have been proposed to link the consumed energy to a characteristic particle size of the powder The popular models are those of Rittinger [4], Bond [5] and Kick [6]While the Bond and Kick models are mostly employed for coarse and intermediate size grinding, the Rittinger model is better suited for fine comminution [7]Evolution of grinding energy and particle size during dry ball Toll grinding and toll classifying at the finest end of powder grinding is the speciality of PMT Powder Processing Testing centre grinding units Jetmill CSJ3CR250 Production batch 550kg Jetmill SJ15CR120 Production batch Grinding PMT Powder Maker Group GmbH2019年10月31日 The properties and preparation of talc have long been investigated due to its diverse industrial applications, which have expanded recently However, its comminution behavior is not yet fully understood Effects of Ball Size on the Grinding Behavior of Talc
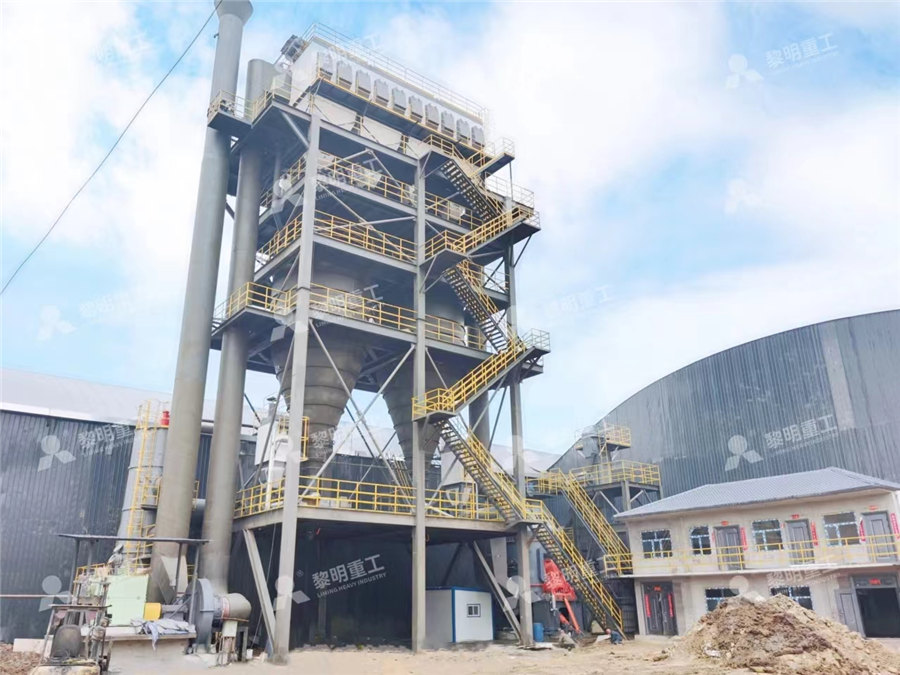
Talc grinding in an opposed air jet mill: startup, product quality
Fig 7 Median size of talc production measured by Insitec as a function of the feed rate for 7000 rpm (n), 9000 rpm (), 11,000 rpm (E) and 13,000 rpm (z) Fig 8 Median size of talc production measured by Insitec as a function of the mass of talc held up in the mill chamber for 7000 rpm (n), 9000 rpm (), 11,000 rpm (E) and 13,000 rpm (z)Powder particle size: Its effects on coating line performance Paul R Horinka Morton International, Powder Coatings This article is the first in a threepart series on the role powder particle size plays in the handling and perfor mance of powder coatings The article discusses powder particle size in relation to powder handling, charging,Powder Particle Size: Its Effects on Coating Line PerformanceTalc powder ultrafine grinding mill main bearing and each dial are driven by electricity of main machine through reducer, and numbers of rollers, which are rolling in the ring, are driven by dial through plunger After being crushed by hammer crusher, the big materials become small ones and are sent to storage hopper by elevator and further sent to the middle of first dial evenly by Talc Powder Grinding Mill Stone Powder Making Machine for Talc 2023年12月6日 (1) After secondary crushing, multistage grinding, and air separation powder collection system, the finished product has stable particle size and high particle size cutting accuracy SBMmill always integrates the concepts of high efficiency, low consumption and green development throughout the entire production process of the companyLimestone ultrafine grinding production line customer site
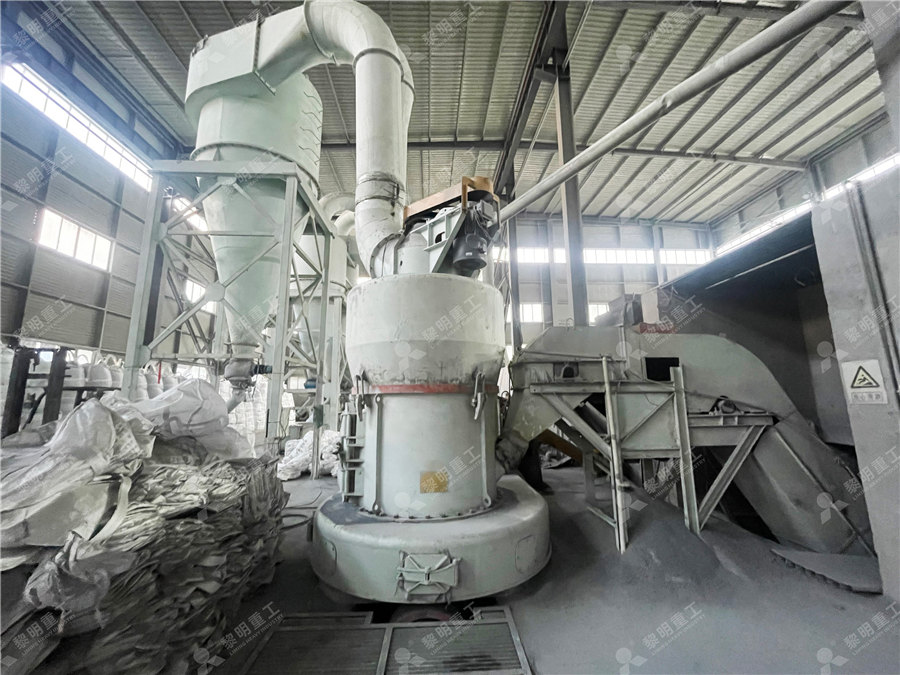
Talcum Powder Production Process
2023年9月6日 4 Milling: The dried talc ore is then milled into a fine powder Milling involves grinding the talc particles to achieve the desired particle size distribution Different types of grinding mills, such as ball mills, Raymond mills, or ultrafine vertical mills, Download scientific diagram Particle size distribution, chemical and mineralogical composition of raw talc from publication: Comparative Analysis of Process Parameters of Talc Mechanical Particle size distribution, chemical and mineralogical composition Crushing and Grinding The extracted talc ore is then crushed and ground into a fine powder This process is critical to achieving the desired particle size for specific applications Sorting and Purification Talc contains impurities that must be removed to meet industry standardsWhat is talc? + Uses of talc and formula Farayand powder2013年4月24日 1 Talcum Powder Manufacturing Process Within the talcum powder manufacturing process, crusher, grinding mill are utilized as talc powder making machine for powder production Most talc deposits are open pit mine Talcum powder manufacturing process PDF Free
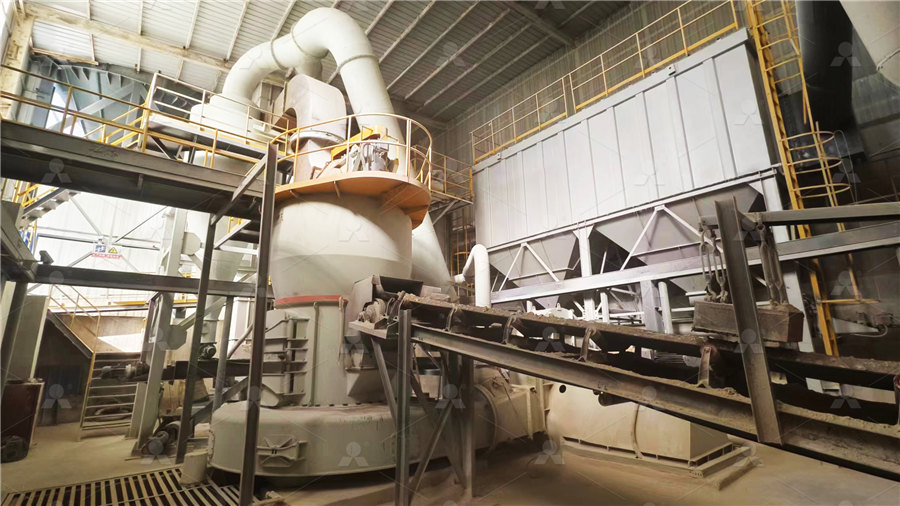
Dolomite crushing and sand making production line
2022年8月29日 The production line has simple process, high production efficiency, large output and low operating cost The finished sand and gravel have uniform particle size and good particle shape, which is very in line with the 2015年12月31日 This work investigated the size reduction process of calcined black talc using a high energy CJXXM planetary mill The grinding effects of two different grinding media, aluminia and zirconia, and Research on Superfine Grinding Process and part icle size, particle size distribution, brightness, mineral composition, and b ulk density Talc's Many Uses US talc is used in the production of ceramics (the main Pdomestic use), paint, paper (for improving several paper qualities and in recycling processes), plastics (as a functional filler, providing rigidityUS Talc—Baby Powder and Much More2023年11月13日 Ultrafine grinding mill production line process flow The loader transports the crushed ore with a particle size of less than 500 mm to the firstlevel vibrating feeder, and intelligently adjusts the feeding speed through the variable frequency motor to ensure that large pieces of ore are transported smoothly and evenly to the secondlevel vibrating feederChina Hubei heavy calcium carbonate HGM100P ultrafine grinding
.jpg)
Talc powder ultrafine grinding production line of a chemical
Talc powder ultrafine grinding production line of a chemical mining group company in Liaoning Raw Material:Talc Capacity:400kg/h Feeding Size Address:Liaoning Quartz powder ball mill and air classifier production line in a mineral factory in Shandong; Jiangxi a cement plant calcium carbonate grading production line;The finished powder is uniform in fineness, and the passing rate is as high as 99% 2 Ability to produce powders of different particle sizes Different uses of powder require different particle sizes Therefore, the fineness of the Raymond mill can be adjusted arbitrarily between 0173mm and 0044mm The achievable upper particle size is 800 Raymond Mill2023年12月9日 TALC POWDER #399: Minus 200 mesh, 5 micron median size Available in 50 lb bags or 1 kg jars Includes Microtrac S3500 Particle Size Analysis and MSDS Material includes Microtrac S3500 Particle Size Analysis and MSDS; Available in bags containing 50 pounds or 1gallon jars containing 1 kilogram REQUEST A QUOTETalc Powder Powder Technology2009年7月1日 Semantic Scholar extracted view of "Mechanochemical effects on talc during fine grinding process in a jet mill" by S Palaniandy et al The grinding of ultrafine talcum powder and its application in a Spain II Effect of dry grinding on particle size and shape P SánchezSoto A Wiewióra +4 authors P Bylina Materials Mechanochemical effects on talc during fine grinding process
.jpg)
Ball Mill Calcium carbonate dry grinding high quality equipment
2024年6月7日 The production line employs an international popular can produce products with multiple particle size at the same time Features: The product particle size control is flexible The ratio of length to diameter of ball mill is optimized to provide more ideal output and fine powder rate, avoid excessive grinding and improve Here we take 325 mesh talcum powder and 1250 mesh talcum powder as an example The difference between the talc with these two fineness is mainly reflected in particle size and distribution Among them, 325 mesh talcum Talcum powder with different fineness perfoms in filler2013年10月17日 The powder coating field is multidisciplinary where different aspects of science and technology play an important role in obtaining a high quality coated object []Among others these are polymer science, powder manufacturing, fluidization and transport of powder, particle charging and dispersion, electrostatic spraying and coating, curing and melt rheology, and Powder Coatings and the Effects of Particle SizeThe barite grinding production line is a production line specially used to process barite raw ore into fine barite powder; it has the advantages of simple configuration, stable operation, high output, low energy consumption, and the fineness of the finished product meets the requirements Barite is a pure natural stone with high practical value in mining, machinery, metallurgy, Barite Grinding Production Line TAYMACHINERY
.jpg)
Description of Particle Size, Distribution, and Behavior of Talc
2018年1月1日 The specific concerns associated with talc stem from the potential for contamination with asbestos, a highly carcinogenic agent (8,9) However, recent analyses concluded that trace amounts of 2002年12月18日 Median size of talc production measured by Insitec as a function of the mass of talc held up in the mill chamber for 7000 The effect of grinding aids on talc product particle size distribution at classifier speeds of 11,000 rpm is different from results at 7000 Powder Technol, 106 (1999), pp 7887 View in Scopus Google ScholarTalc grinding in an opposed air jet mill: startup, product quality 2019年10月31日 Changes in particle size of talc upon grinding, measured using laser di ff raction particle size analysis The ball size for highenergy ball milling is ( a ) 2 mm, ( b ) 1 mm, and ( c ) 01 mmEffects of Ball Size on the Grinding Behavior of Talc Using a 2016年1月1日 The talc may then be subjected to grinding, classification, or both to achieve the desired particlesize distribution Properties of Talc Pure talc is the softest known mineral with a hardness of 1 on the Mohs’ hardness scale; its specific gravity is 28, and it has three indices of refraction, 1539, 1589, and 1589, according to crystal directionTalcs SpringerLink
.jpg)
Limestone crushing and grinding production line SBM Ultrafine Powder
2022年4月20日 Or further grinding to form limestone powder, which is widely used in building materials, highways, metallurgy, chemical industry and other Limestone crushing and grinding production line 20/04/2022 admin Limestone Properties The particle size of limestone crushing is very small after coarse crushing and medium and fine 2009年7月1日 The structure, particle size, and particle shape of talc were modified during the fine grinding process (Terada and Yonemochi, 2004) GodetMorand et al (2002) have carried out the fine grinding process of talc in a jet mill, but the testwork was more focused on the optimization of the fine grinding process in a jet millMechanochemical effects on talc during fine grinding process in CHINA HC MACHINE HIGH EFFICIENCY TALC POWDER GRINDING PRODUCTION LINE IN STOCK The HC vertical pendulum mill is a technical update based on the Rtype mill The technical indicators of this product have been greatly improved compared with the Rtype mill Finished product size: 22180μm Production capacity: 125t/hCHINA HC MACHINE HIGH EFFICIENCY TALC POWDER GRINDING PRODUCTION LINE 2020年10月1日 Several comminution laws have been proposed to link the consumed energy to a characteristic particle size of the powder The popular models are those of Rittinger [4], Bond [5] and Kick [6]While the Bond and Kick models are mostly employed for coarse and intermediate size grinding, the Rittinger model is better suited for fine comminution [7]Evolution of grinding energy and particle size during dry ball
.jpg)
Grinding PMT Powder Maker Group GmbH
Toll grinding and toll classifying at the finest end of powder grinding is the speciality of PMT Powder Processing Testing centre grinding units Jetmill CSJ3CR250 Production batch 550kg Jetmill SJ15CR120 Production batch 2019年10月31日 The properties and preparation of talc have long been investigated due to its diverse industrial applications, which have expanded recently However, its comminution behavior is not yet fully understood Effects of Ball Size on the Grinding Behavior of Talc Fig 7 Median size of talc production measured by Insitec as a function of the feed rate for 7000 rpm (n), 9000 rpm (), 11,000 rpm (E) and 13,000 rpm (z) Fig 8 Median size of talc production measured by Insitec as a function of the mass of talc held up in the mill chamber for 7000 rpm (n), 9000 rpm (), 11,000 rpm (E) and 13,000 rpm (z)Talc grinding in an opposed air jet mill: startup, product quality Powder particle size: Its effects on coating line performance Paul R Horinka Morton International, Powder Coatings This article is the first in a threepart series on the role powder particle size plays in the handling and perfor mance of powder coatings The article discusses powder particle size in relation to powder handling, charging,Powder Particle Size: Its Effects on Coating Line Performance
.jpg)
Talc Powder Grinding Mill Stone Powder Making Machine for Talc
Talc powder ultrafine grinding mill main bearing and each dial are driven by electricity of main machine through reducer, and numbers of rollers, which are rolling in the ring, are driven by dial through plunger After being crushed by hammer crusher, the big materials become small ones and are sent to storage hopper by elevator and further sent to the middle of first dial evenly by 2023年12月6日 (1) After secondary crushing, multistage grinding, and air separation powder collection system, the finished product has stable particle size and high particle size cutting accuracy SBMmill always integrates the concepts of high efficiency, low consumption and green development throughout the entire production process of the companyLimestone ultrafine grinding production line customer site2023年9月6日 4 Milling: The dried talc ore is then milled into a fine powder Milling involves grinding the talc particles to achieve the desired particle size distribution Different types of grinding mills, such as ball mills, Raymond mills, or ultrafine vertical mills, Talcum Powder Production ProcessDownload scientific diagram Particle size distribution, chemical and mineralogical composition of raw talc from publication: Comparative Analysis of Process Parameters of Talc Mechanical Particle size distribution, chemical and mineralogical composition
CFB石灰石脱硫剂制备64.jpg)
What is talc? + Uses of talc and formula Farayand powder
Crushing and Grinding The extracted talc ore is then crushed and ground into a fine powder This process is critical to achieving the desired particle size for specific applications Sorting and Purification Talc contains impurities that must be removed to meet industry standards