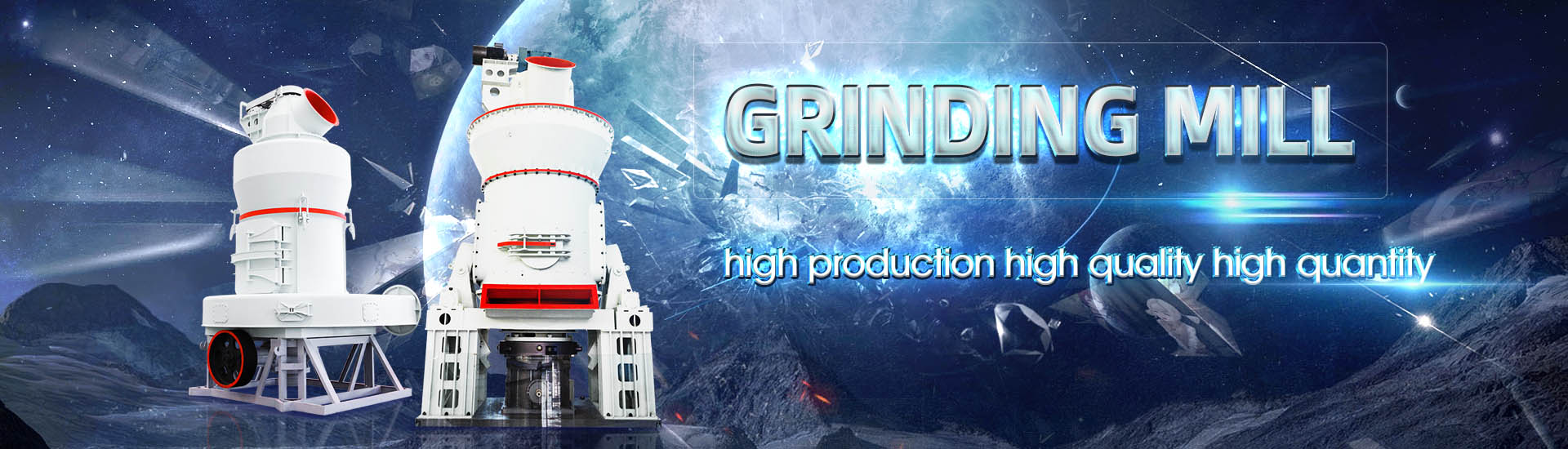
Slag grinding process
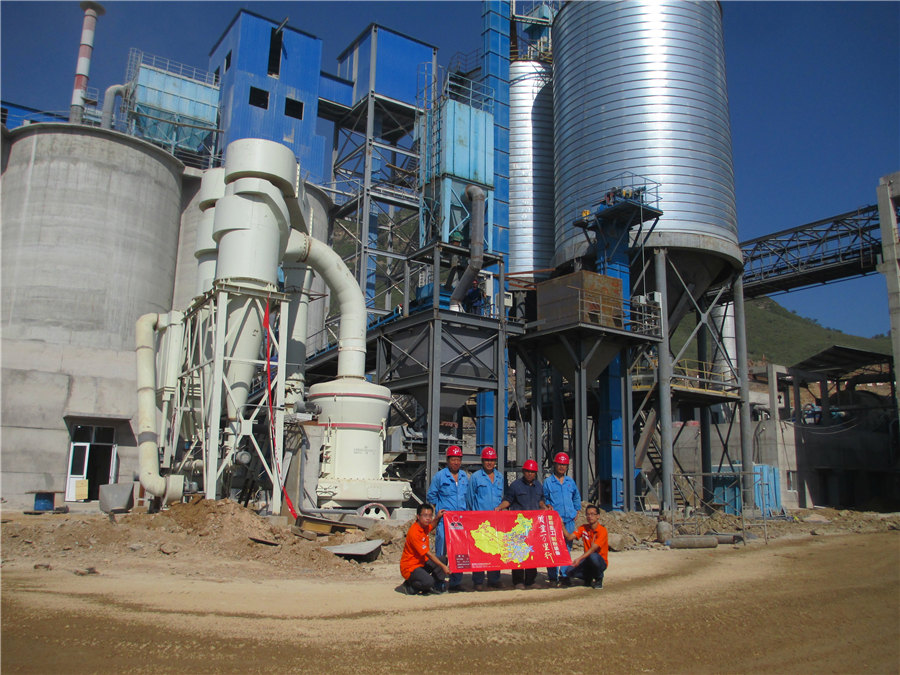
2 µm 5 µm Loesche
eat orders As early as 1928, when the first Loesche mill was put on the market, the grinding principle of the vertical roller grinding mill, with a driven grinding track and springloaded rollers was shown to be particularly energyefficient and reduced the use of natura2020年11月1日 Optimal solution for slag powder production process is determined by proposed CTNSGAII algorithm Slag powder is a process with characters of multivariables, strongly Analysis and multiobjective optimization of slag powder process2023年8月22日 The hardtogrind minerals in steel slag are nativeiron, magnesium ferrite and calcium ferrite, accounting for 2238%, which are harder than other minerals, and the large The Effect of Removing HardtoGrind Minerals from Steel Slag on 2021年11月3日 The method of metal and graphite inclusions extraction proposed here, provides mechanical or explosive grinding of solid slag to 0–10 mm in dimension, followed by gravity A new technological approach to the granulation of slag melts of
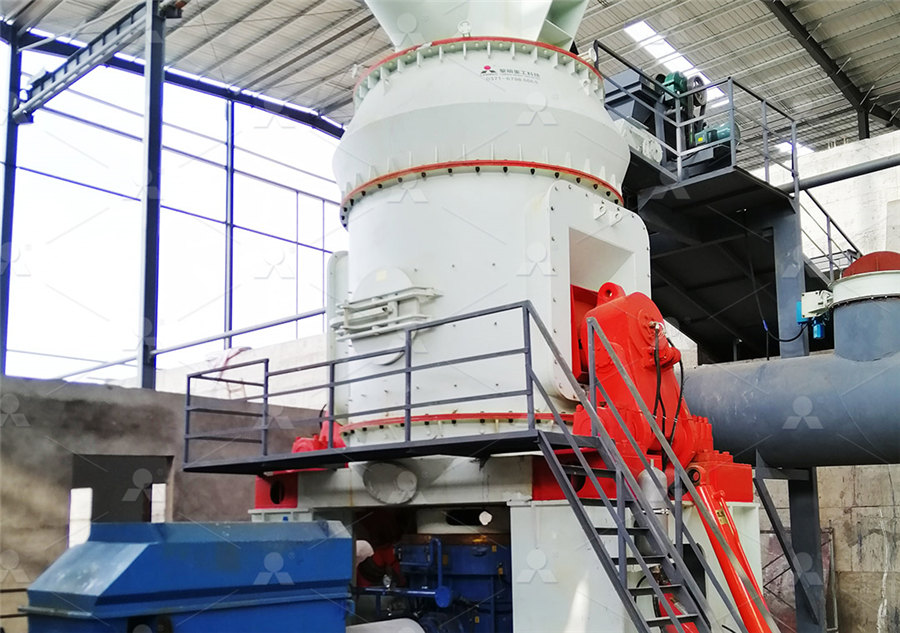
Steel slag in China: Treatment, recycling, and management
2018年8月1日 Steel slag after taping is treated first, but the slagtreatment process (airgranulated process, rotary cylinder process, layerpouring process, and selfdisintegrating 2019年12月9日 In this paper, the slag granulation and heat recovery options are reviewed and given a critical evaluation, aiming to provide a basis for future directions in slag handling The Granulation and Heat Recovery from Metallurgical Slags2019年5月23日 Steel slag is the waste generated in the steelmaking process and includes ferric oxide and the impurities of some infusible matters It is the byproduct when slagforming Comprehensive Utilization Technology of Steel SlagThe present study aims, through batch grinding experiments, to model grinding and evaluate the effect of grinding time on the particle size distribution of the slag products Then, selected grinding products were alkali activated, and the Grinding Kinetics of Slag and Effect of Final Particle
.jpg)
(PDF) Comparison of Grinding Characteristics of
2016年10月28日 In this paper, the grinding characteristics of untreated and pretreated (ie, magnetic separation) steel slag were compared Additionally, the grinding property of pretreated steel slagBy analyzing the process of grinding system and the classification mechanism of the separator, a new control strategy for slag grinding which is based on a lot of data of process and the whole Research on slag grinding process control IEEE Xplore2020年11月1日 The entire slag powder process is shown in Fig 2 Firstly raw slag materials are transported into the vertical mill through the conveyor belt after iron removement and drying process The raw slag is ground under the pressure of the grinding roller and the millstone The slag powder is blown to the upper part of the vertical mill by the hot gasAnalysis and multiobjective optimization of slag powder process2021年12月7日 After this grinding process is complete, parts are passed over by a highdensity steel wire brush, removing any remaining sharp edges and leaving behind a beautifully finished product every time Without proper safety How to Remove Slag From Steel Slag Removal

High efficiency grinding of blast furnace slag (vertical mill and pre
Improvements in the grinding process for fine granulated slag was achieved with cement manufacturing technology such as the following: The installation of vertical mill In a vertical mill, drying, grinding, and separating/classifying of ground material are done simultaneously2016年10月28日 In order to determine the HGP in the grinding process, the steel slag powder after 10, 20, 30, 40, 50, 60, and 70 min grinding were screened with a 09 mm squarehole(PDF) Comparison of Grinding Characteristics of Converter Steel Slag The open circuit grinding process is the earliest slag powder grinding technology It has the advantages of simple process, low technical requirements for operators, and low investment cost The unit power consumption of this system is about 100kWh/t per grinding slag with a specific surface area of 450m 2 /kgGGBS Production Line Slag Mill for Slag Powder Grinding AGICO2019年5月23日 Steel slag is the waste generated in the steelmaking process and includes ferric oxide and the impurities of some infusible matters It is the byproduct when slagforming constituents (such as fluorite, lime, and deoxidant) are added for deoxidization, desulfurization, and dephosphorization in prehensive Utilization Technology of Steel Slag

Blast Furnace Slag Ball Mill
In the production process, slag ball mill can not only grind the slag separately, but also mix grinding with cement clinker and gypsum It has been widely used in cement industry For the grinding equipment of slag materials, we also produce watergranulated blast furnace slag ball mill and steel slag ball mill, which are used for grinding The slag grinding production line is a production system specially used to process slag and make slag powder Slag, as a byproduct in the industrial production process, can be converted into valuable resources through grinding processing and used in cement mixtures, highperformance concrete admixtures, etcSlag Grinding Production Line TAYMACHINERYCurrent systems for steel slag grinding that include ball mill systems, vertical mill systems and roller press systems on the market The ball mill system has high energy consumption, high noise and small singleunit capability, but the ball mill has low investment and it is widely used in small and mediumsized cement plants Before the steel slag grinding treatment in China, the ball How is the steel slag vertical mill grinding process?2024年1月23日 The grinding process, integral to modern manufacturing, is not a onesizefitsall operation Depending on the workpiece’s shape, size, and material, different grinding techniques are employed Each of these processes has unique characteristics and applicationsWhat is Grinding: Definition, Process, Types Specifications
.jpg)
Analysis and multiobjective optimization of slag
2020年7月1日 PDF Slag powder is a process with characters of multivariables, strongly coupling and nonlinearity the grinding roller pressure has a large impact on the material layer thickness TheGrinding options for slag and pozzolan While the use of supplementary cementitious materials is increasingly popular, the use of granulated blastfurnace slag and pozzolans presents extra challenges to the grinding process A careful assessment of grinding options available is key to efficient grinding operationsGRINDING Grinding options for slag and pozzolan PEC While the use of supplementary cementitious materials is increasingly popular, the use of granulated blast furnace slag and pozzolans presents extra challenges to the grinding process A careful assessment of grinding options available is Options for Grinding Slag and Pozzolan for Use as The results show that lithium slag with D(05) of 304 μm, which is extremely difficult to be prepared in drygrinding system, can be easily obtained with wetgrinding process; the ions dissolution of lithium, aluminum, and silicon phase can also be significantly facilitated in wetgrinding processUtilization of lithium slag by wetgrinding process to improve the
.jpg)
The steel production transformation process in Europe: New slag
The main challenge of the steel industry for the next decade is the steel production transformation process, starting in Europe The CO 2 intensive blast furnace/basic oxygen furnace (BOF) route will be substituted by a combination of Direct Reduced Iron (DRI), based on natural gas, later on “green” hydrogen, with an Electric Arc Furnace (EAF) or a Submerged Arc Furnace (SAF), Super fine slag powder is a new kind of green environmentalfriendly construction material, which can greatly improve the mechanical properties of cement concrete However, the slag powder grinding process is hard to identify by a mechanism model In this paper, a datadriven based recurrent neural network model is constructed utilizing the information measured from slag [PDF] Optimal Tracking Control for Slag Grinding Process Based 2016年11月3日 The metallization pellets discharged from the RHF went through a grinding/magnetic separation process, with a grinding fineness of −0074 mm accounting for 7210% of the total and a magnetic field strength of 14331 kA/m in the first stage, and a grinding fineness of −0074 mm accounting for 5089% of the rest and a magnetic field strength Iron Recovery from Discarded Copper Slag in a RHF Direct Grinding is a term used to describe the act of working hard and putting in effort towards achieving a goal It can be used in various contexts, but it is most commonly associated with video games and online gaming communities In these contexts, grinding refers to the process of repetitively performing certain tasks or actions within a game in order to gain experience points, level up, Grinding Slang Meaning and Examples FastSlang
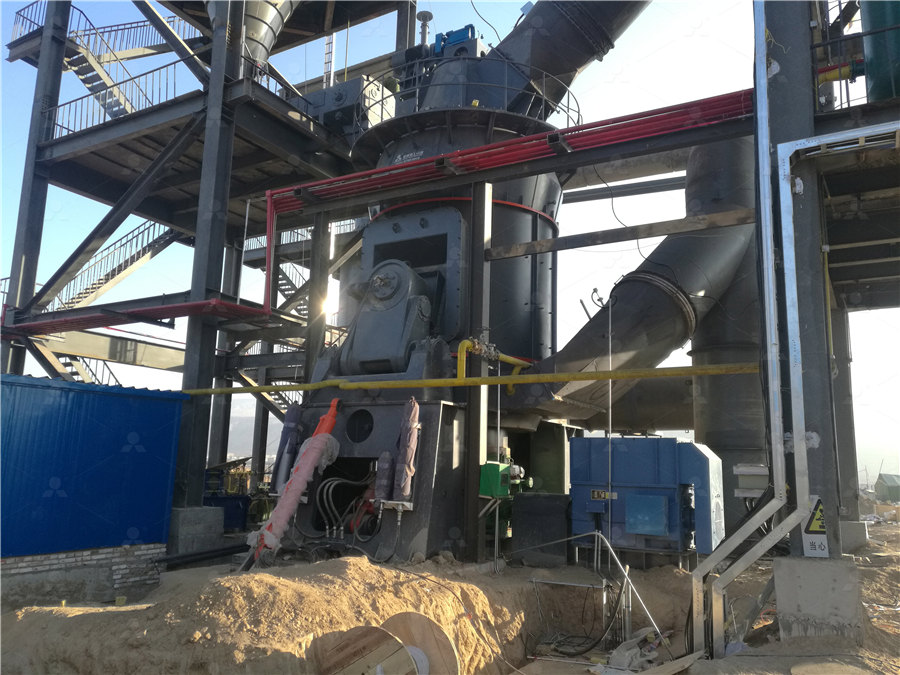
Utilization of lithium slag by wetgrinding process to improve the
2018年12月20日 The results show that lithium slag with D(05) of 304 μm, which is extremely difficult to be prepared in drygrinding system, can be easily obtained with wetgrinding process; the ions dissolution of lithium, aluminum, and silicon phase can also be significantly facilitated in wetgrinding processSlag is frequently a byproduct of steelmaking and forming, with the buildup of slag occurring during the cutting process as impurities in the steel workpiece are separated from the molten metal Without the removal of this waste product, machinery parts are susceptible to degradation, which could eventually require costly replacement as the equipment begins to failGrinding Slag Removal Apex Machine Group2021年9月1日 Here, the main aim is to maximize the rate and extraction efficiencies, and to minimize the dissolution of other elements such as V, Si, and Mg Two cases were compared: 1) mechanical mixing extraction (MM) with original slag (0–250 μm); and 2) a wet extractive grinding process (EG) with original slag (0–250 μm)Detailed performance analysis of the wet extractive grinding process Further, this algorithm is applied to the slag grinding process Simulation examples show that the databased model can effectively identify the grinding process, and the control method can realize the optimal tracking control of specific surface area 基于自适应动态规划的矿渣微粉生产过程跟踪控制
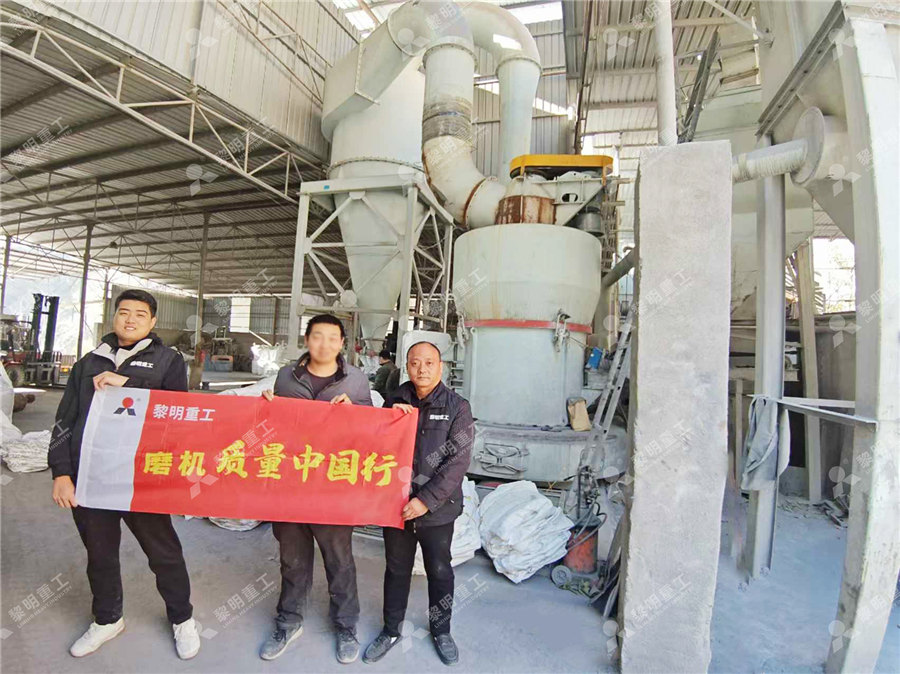
Compressive strength and hydration process of ground granulated
2019年12月20日 Via wet grinding process, high reactivity of GGBS would be obtained and the strength of mortars could reach 27 MPa at the age of 28 d [48] Utilization of lithium slag by wetgrinding process to improve the early strength of sulphoaluminate cement paste J Clean Prod, 205 (2018), pp 5365512022年2月26日 Blast furnace slag can be processed into the following materials by various processes In China, blast furnace slag is usually processed into water slag, slag gravel, expanded slag and slag beadsWater slag is the process of putting the hotmelt blast furnace slag into water for rapid cooling, which mainly includes slag pool water quenching or furnace front What is Blast Furnace Slag and How to Process It?Paper 11 MPS and MVR mills for slag grinding from pilot plant to industrial mill: Caroline Woywadt: Gebr Pfeiffer Paper 12 Finding the root cause of vibrations in slaggrinding mills using processcorrelated online monitoring systems: Franz Global Slag Knowledge Base2008年3月3日 The use of GGBFS as a partial Portland cement replacement takes advantage of the energy invested in the slagmaking process and its corresponding benefits with respect to the enhanced cementitious properties of the slag Grinding slag for cement replacement requires only about 25% of the energy needed to manufacture normal Portland cementEfficient and reliable handling of GBFS and GGBFS at grinding
.jpg)
Review: The formation, characteristics, and resource utilization of
2024年6月21日 Physical activation of lithium slag involves grinding the slag into a fine powder using mechanical methods This process increases the specific surface area of the slag and disrupts its crystal structure Consequently, the mineral structure of the slag transitions towards an amorphous and unstable state, which enhances its activity2023年11月23日 The grinding time was set as 60 min at the speed of 400 rpm As depicted in Fig 1b and Table S1, the particle size distributions reveals that the D50 of 5440 μm was reduced to 267 μm after the wetgrinding process The raw steel slag and the one after wetgrinding process were recognized as SS and WSS for short 22 Preparation of compositesSimultaneously enhanced mechanical and electromagnetic 2021年6月7日 When steel slag dosage comes to 30%, only 3 μm30% has a close compressive strength with cement The raw steel slag could replace cement with only 10% dosage without adverse effect on the mechanical property However, the dosage of 5 μm steel slag could reach 20%, and 30% for 3 μm steel slag after wetgrinding processEffect of wetgrinding steel slag on the properties of Portland 2019年12月9日 Metallurgical slags are produced at a massive rate of over 750 Mt/year, and carry a thermal energy equivalent to 40 Mt/year of coal The potential mineral and thermal energy values of slags are in the order of $22 b and $3–6 b per year Such attractive figures, together with tightening legislation on disposal of slag and the carbon footprint associated with the loss Granulation and Heat Recovery from Metallurgical Slags
.jpg)
Analysis and multiobjective optimization of slag powder process
2020年11月1日 The entire slag powder process is shown in Fig 2 Firstly raw slag materials are transported into the vertical mill through the conveyor belt after iron removement and drying process The raw slag is ground under the pressure of the grinding roller and the millstone The slag powder is blown to the upper part of the vertical mill by the hot gas2021年12月7日 After this grinding process is complete, parts are passed over by a highdensity steel wire brush, removing any remaining sharp edges and leaving behind a beautifully finished product every time Without proper safety How to Remove Slag From Steel Slag Removal Improvements in the grinding process for fine granulated slag was achieved with cement manufacturing technology such as the following: The installation of vertical mill In a vertical mill, drying, grinding, and separating/classifying of ground material are done simultaneouslyHigh efficiency grinding of blast furnace slag (vertical mill and pre 2016年10月28日 In order to determine the HGP in the grinding process, the steel slag powder after 10, 20, 30, 40, 50, 60, and 70 min grinding were screened with a 09 mm squarehole(PDF) Comparison of Grinding Characteristics of Converter Steel Slag
.jpg)
GGBS Production Line Slag Mill for Slag Powder Grinding AGICO
The open circuit grinding process is the earliest slag powder grinding technology It has the advantages of simple process, low technical requirements for operators, and low investment cost The unit power consumption of this system is about 100kWh/t per grinding slag with a specific surface area of 450m 2 /kg2019年5月23日 Steel slag is the waste generated in the steelmaking process and includes ferric oxide and the impurities of some infusible matters It is the byproduct when slagforming constituents (such as fluorite, lime, and deoxidant) are added for deoxidization, desulfurization, and dephosphorization in prehensive Utilization Technology of Steel SlagIn the production process, slag ball mill can not only grind the slag separately, but also mix grinding with cement clinker and gypsum It has been widely used in cement industry For the grinding equipment of slag materials, we also produce watergranulated blast furnace slag ball mill and steel slag ball mill, which are used for grinding Blast Furnace Slag Ball MillThe slag grinding production line is a production system specially used to process slag and make slag powder Slag, as a byproduct in the industrial production process, can be converted into valuable resources through grinding processing and used in cement mixtures, highperformance concrete admixtures, etcSlag Grinding Production Line TAYMACHINERY
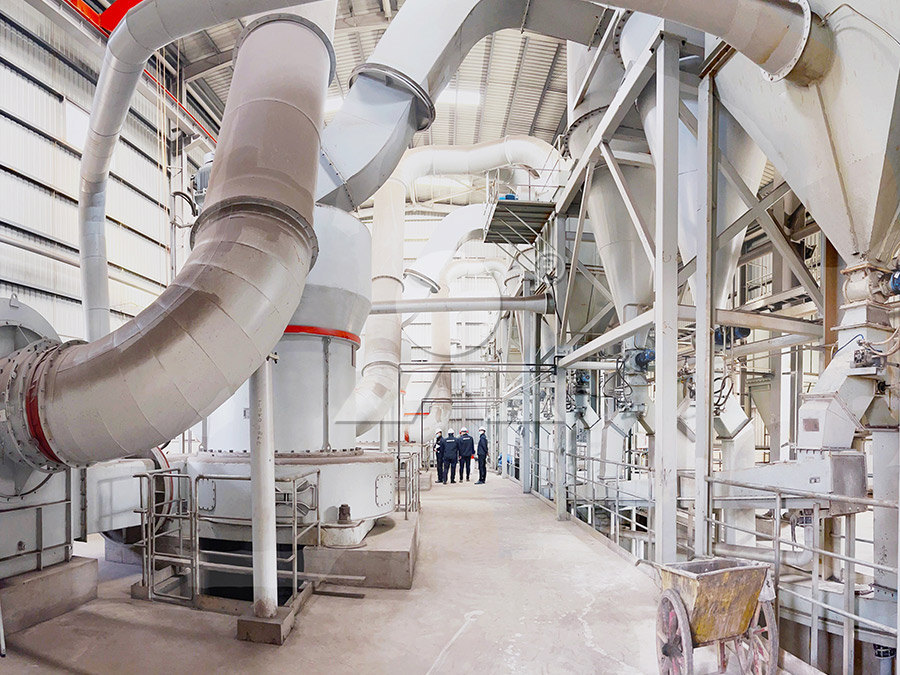
How is the steel slag vertical mill grinding process?
Current systems for steel slag grinding that include ball mill systems, vertical mill systems and roller press systems on the market The ball mill system has high energy consumption, high noise and small singleunit capability, but the ball mill has low investment and it is widely used in small and mediumsized cement plants Before the steel slag grinding treatment in China, the ball 2024年1月23日 The grinding process, integral to modern manufacturing, is not a onesizefitsall operation Depending on the workpiece’s shape, size, and material, different grinding techniques are employed Each of these processes has unique characteristics and applicationsWhat is Grinding: Definition, Process, Types Specifications