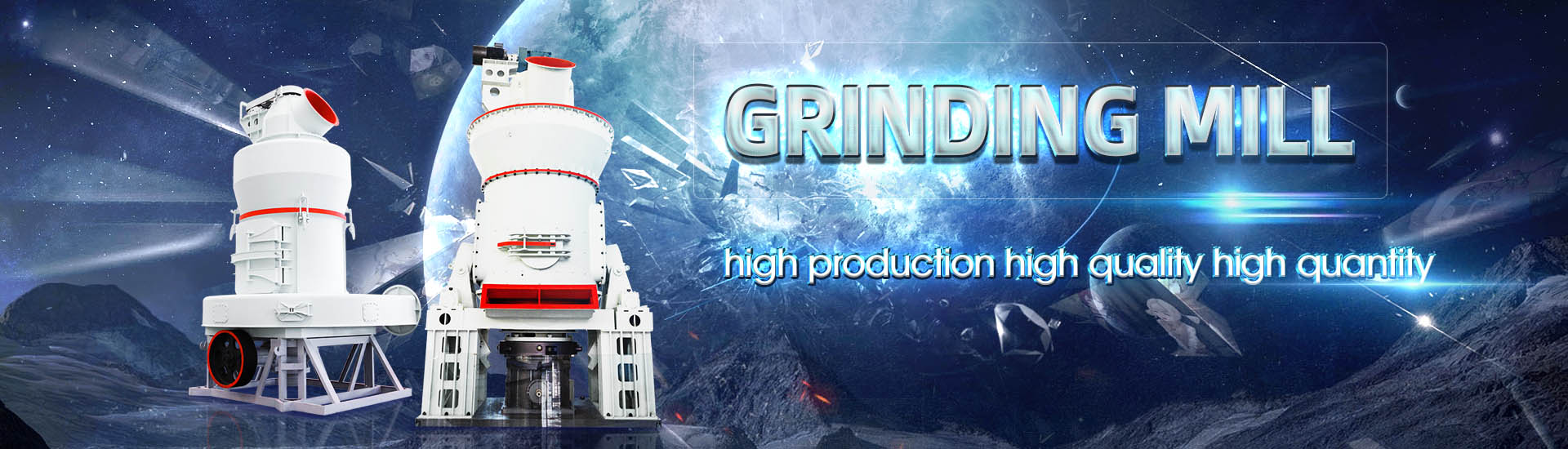
How to reduce the sintering cost of laterite nickel ore
.jpg)
Selective Reduction of Laterite Nickel Ore JSTAGE
23 Direct reduction of laterite nickel ore in industrial scale Most laterite nickel ore processing is carried out using Elkem process The Elkem process uses Rotary Kiln and Electric Furnace (RKEF) to reduce and smelt laterite nickel ore Commercialization of Elkem process itself 2024年11月1日 A large number of sintering tests and industrial production of nickel laterite ore have shown that its high crystal water content and smelting composition lead to poor sintering Review on comprehensive utilization of nickel laterite ore2023年11月24日 Researchers have been exploring methods to improve the magnetic separation process of laterite nickel ore roasting, one of which is to use different reducing agents The commonly used types of reducing agents Study on the MediumTemperature Reduction Therefore, a novel method to process laterite nickel ore using lower energy is needed The novel method is done via direct reduction and magnetic separation In laterite nickel processing by Selective Reduction of Laterite Nickel Ore JSTAGE
.jpg)
(PDF) Nickel Laterite Smelting Processes and Some ResearchGate
2019年9月3日 Industrially, the pyrometallurgical treatment of laterites is mostly accomplished with a wellestablished method, namely, the rotary kiln–electric arc furnace (RKEF) process, 2023年1月19日 Several plants have tried to improve the production process to reduce energy consumption and cost based on the experience, such as controlling the MgO/SiO 2 mass ratio of feeds to reduce the smelting An Overview of Nickel Utilization from Laterite Ore2012年5月20日 The processing of nickel laterite ore to produce ferronickel is energy intensive, especially when low nickel content ores are processed The selective reduction–beneficiation Upgrading low nickel content laterite ores using selective 2024年5月20日 For the better sinter consolidation characteristics of limonitic nickel laterite, the hybrid sintering technology was applied and a lowmelting additive was added in the sintering Improving Sinter Consolidation Characteristics of Nickel Laterite by

Improving Sinter Consolidation Characteristics of Nickel Laterite by
2024年5月20日 For the better sinter consolidation characteristics of limonitic nickel laterite, the hybrid sintering technology was applied and a lowmelting additive was added in the sintering2014年1月1日 Sintering at high NLOs proportion can not only decrease the cost of molten iron, but also improve the value of the steel This paper introduced the general situation of the NLOs, discussedThe application of nickel lateritic ores in sinteringcrease if the nickel laterite ores are hydrated and sintered by means of traditional sintering, and if the nickel lateritic sinters are then reduced in the shaft furnace To facilitate this process, a comparative study on sintering behaviors of nickel laterite from the Philippines and Indonesia was carried out in this paper 2 ExperimentalMineral Change of Philippine and Indonesia Nickel Lateritic Ore Pressure acid leaching has been applied to the Caron process to reduce highenergy consuming phases in direct ore leaching Direct leaching eliminates the need for drying and reduction steps, which then leads to energy savings (Buyukakinci, 2008)The acceptable nickel content in this method is 1–5% (Dalvi et al, 2004)Also, the crushed ore is dissolved directly with sulfuric acid Bioleaching of Lateritic Nickel Ores SpringerLink
.jpg)
Selective Reduction of Laterite Nickel Ore JSTAGE
23 Direct reduction of laterite nickel ore in industrial scale Most laterite nickel ore processing is carried out using Elkem process The Elkem process uses Rotary Kiln and Electric Furnace (RKEF) to reduce and smelt laterite nickel ore Commercialization of Elkem process itself began with the development of a pilot plant in 1953–19542023年3月28日 In this paper, lowgrade limonitic nickel laterite and chromite were synergistically utilized via the hybrid sintering process (ie, pelletsintering process) for highquality Ni–Cr sinter preparation and great carbon emission reduction Under the optimum process conditions, Ni–Cr sinter indices were substantially improved in the pelletsintering process Tumble index and Reduction of Carbon Footprint Through Hybrid Sintering of Low The second principle of ferronickel smelting is that laterite ores cannot be smelted to nickel metal alone, ie, separately from iron This is because (1) garnierite concentrates always contain 5–10 times more Fe than Ni and (2) oxygen is only slightly more strongly bonded to Fe than to Ni—ie, FeO in calcined concentrate is almost as easy to reduce as NiOLaterite Ore an overview ScienceDirect Topics2021年3月29日 Nickel can be found in laterite ores, sulfide ore, in secondary resources, and nonland resources like sea nodules[6,7] However, only 40 pct of nickel scrap can be recovered as secondary sources, nonland resources require high investment and operational costs, thus, sulfides and lateritic ores are the most important nickel sources[6,8,9,10,11,12] The identified Roasting and Leaching Behavior of Nickel Laterite Ore
.jpg)
Nickel Laterites: The World’s Largest Source of Nickel
2013年6月25日 The Goro Nickel Mine is one of the world’s largest Nickel Laterite Mines The project is owned by Vale (69%), a joint venture company composed of Sumic Nickel Netherlands, Sumitomo Metal Mining and Mitsui (21%) and the remaining 2024年3月13日 The leaching behavior of nickel and iron in limonitetype laterite nickel ore was studied through ammonium hydrogen sulfate atmospheric leaching The leaching temperature, ammonium bisulfate concentration, reaction time, and acid excess rate during the nickel dissolution process were optimized using the response surface methodology (RSM) Leaching Kinetics of LimoniteType Laterite Nickel Ore from 2014年1月1日 The sintering experiment of laterite with different carbon content were carried out, and the effect of carbon content on sintering velocity, agglomeration ratio, mass loss, temperatures of off gas The application of nickel lateritic ores in sintering ResearchGateThe results showed that the adding proportion of laterite nickel ores should be less than 15% when the high temperature properties of the mixing ores were well Increasing the mixing ration of laterite nickel ores in the sintering blending would play an Sintering Characteristics of Iron Ores with Addition of Laterite Nickel
.jpg)
Nickel Laterite Metallurgy SpringerLink
2023年5月28日 The nickel laterite in upper layer of the ore deposit, with higher content of iron (Fe) and lower content of silica (SiO 2) and magnesium (Mg) in general, belongs to the limonite type, and usually contains lower nickel of about 1%, but a certain amount of cobalt (Co), while the nickel laterite in lower layer of the ore deposit, with higher content of silica (SiO 2) and 2022年5月15日 For nickel laterite ores, similarly to copper ores, a presintering operation is required, for which sulfuric acid is added to the base ore, and the ore is sintered in rotating drums But the practice has shown , that the introduction of the sintering operation with sulfuric acid is not enough for successful implementation of the oxidized nickel ores heap leaching processProcessing of oxidized nickel ores using sintering, roasting and 2022年3月4日 To improve sintering performance and reduce carbon emissions, limonitic nickel laterite sintering was strengthened via the pelletsintering process and the relevant mechanism was revealed by chemistry and mineralogy analyses of product sinter Sintering performance in the pelletsintering process was significantly improved with tumble index and productivity Improving Sintering Performance of Limonitic Nickel Laterite and 2022年4月12日 One main source of nickel besides nickel sulfide ore is laterite nickel ore Laterite ore is more sustainable and has abundant reserves Nowadays, nickel demands are increasingly needed either for the manufacture of stainless steel or nickelbased batteries This study aims to study the smelting process of limonitic laterite nickel ore The smelting process Smelting and Selective Reduction of Limonitic Laterite Ore in Mini
.jpg)
Carbothermic Reduction of Nickeliferous Laterite Ores for Nickel
while the proportion was only 8% in 2001 It shows that China’s nickel consumption had experienced a substantial increase in the first decade of the2020年7月22日 Laterite ores are becoming the most important global source of nickel and cobalt Pyrometallurgical processing of the laterites is still a dominant technology, but the share of nickel and cobalt Review of the past, present, and future of the hydrometallurgical 31 MATERIALS RESEARCH COMMUNICATIONS 1(1) (2020) 2633 Fakhreza et al Based on the peak contained in the XRD results in Fig 6, the sintered results of sintering of laterite nickel ore with air air flow rate of 545 m3/min revealed the major phase of sintered namely Pyroxene (CaFeSi2O4) and Olivine ((Fe,Mg)2SiO4) and several phases minor from sintered are Nickel The Effect of Air Flow Rate on Sinter Yield, Sinter Strength and Ni 2022年1月1日 1 Introduction With the overexploitation of highgrade nickel sulfide and increasingly mature smelting process of lowgrade nickel laterite, the production of nickel products from nickel laterite ores has become the focus [[1], [2], [3]]Pyrometallurgical smelting processes are regarded as the mainstream methods to treat limonitic laterite, in which sinteringblast Mineralization mechanism of limonitic laterite sinter under different
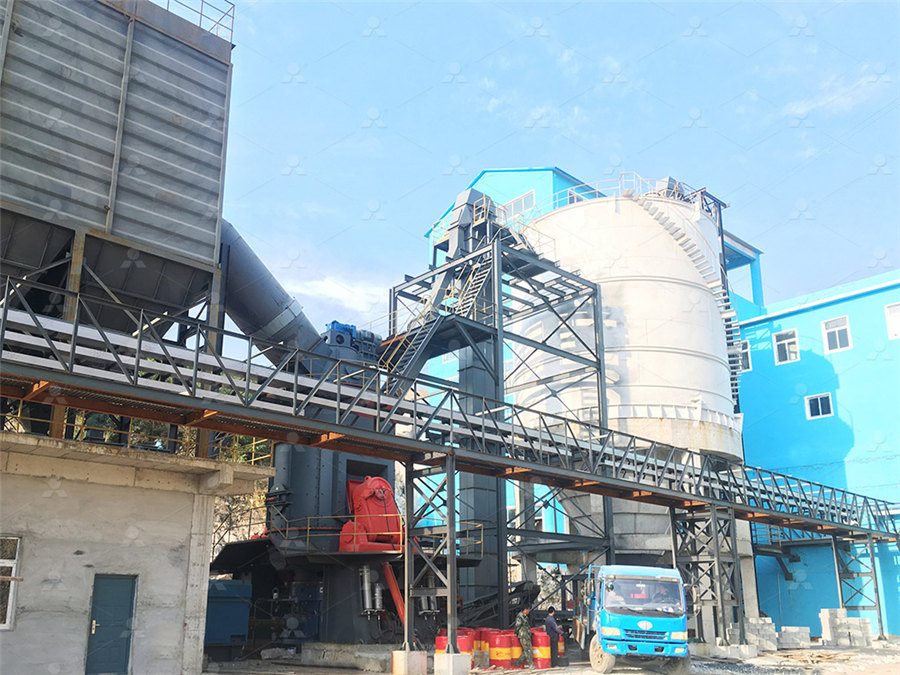
An investigation into the cosintering process of limonitic nickel
2021年5月1日 Table 1 shows the chemical compositions of raw materials used in the sinter pot tests The adopted iron ores include nickel laterite and chromite ores imported from Philippines and South Africa, respectively The former contains 4509% total iron, 109% NiO and 345% Cr 2 O 3 and simultaneously possesses high LOI (Loss on ignition) of 1249% and rich gangue 2022年8月22日 The stainlesssteel industry is the primary driver of nickel demand and uses both class 1 and 2 (lower purity) nickel Class 2 nickel from nickel laterite ores can be converted to nickel sulfate; however, it requires highpressure acid leaching Much of the laterite ore comes from the Philippines, Indonesia, and New CaledoniaRecent Progress in Hydrometallurgical Processing of Nickel Lateritic Orethe water content of the limonitic laterite ore sintering mixture is much higher than that of an ordinary iron ore sintering mixture, usually reaching 17–20% However, the high water content of the mixture will have an adverse effect on the sintering process18,19 On the one hand, the removal of a large amount of water will consume a lot of Mineralization Behavior and Strengthening Mechanism of 2024年5月20日 In recent years, the major nickel source of stainless steel has been converted from nickel sulfide ore into nickel laterite ore due to the massive consumption of the former [1, 2]In addition, limonitic nickel laterite accounts for about 60% of the total nickel laterite resources []The abundant nickel laterite ore is generally used for ferronickel preparation through Improving Sinter Consolidation Characteristics of Nickel Laterite
.jpg)
(PDF) Nickel Sulfide Versus Laterite: The Hard
2009年9月1日 There are widespread nickel resources around the world, but divided principally between nickel sulfide or laterite (oxide) resources Historically production has been dominated by sulfide ores but Nickel processing Extraction, Refining, Alloying: The extraction of nickel from ore follows much the same route as copper, and indeed, in a number of cases, similar processes and equipment are used The major differences in equipment are the use of highertemperature refractories and the increased cooling required to accommodate the higher operating temperatures in nickel Nickel processing Extraction, Refining, Alloying Britannica2020年10月1日 The depletion of sulfide nickel ore and the growing of stainless steel demand each year cause the use of lowgrade laterite nickel ore continues to increaseAnalysis the Effect of Charcoal Mass Variation to Ni Content, Sinter 2020年5月1日 1 Introduction Due to the worldwide strong demand for stainless steel products and dramatic depletion of nickel sulfide resources, mining of nickel laterite with basic reserve of 444 billion tons, has become extremely attractive in recent years [1, 2]Limonitic nickel laterite, an ironrich nickel ore [3, 4], possesses rich reserves accounting for 60% of total lateritic nickel An investigation into the distinctive sintering performance and
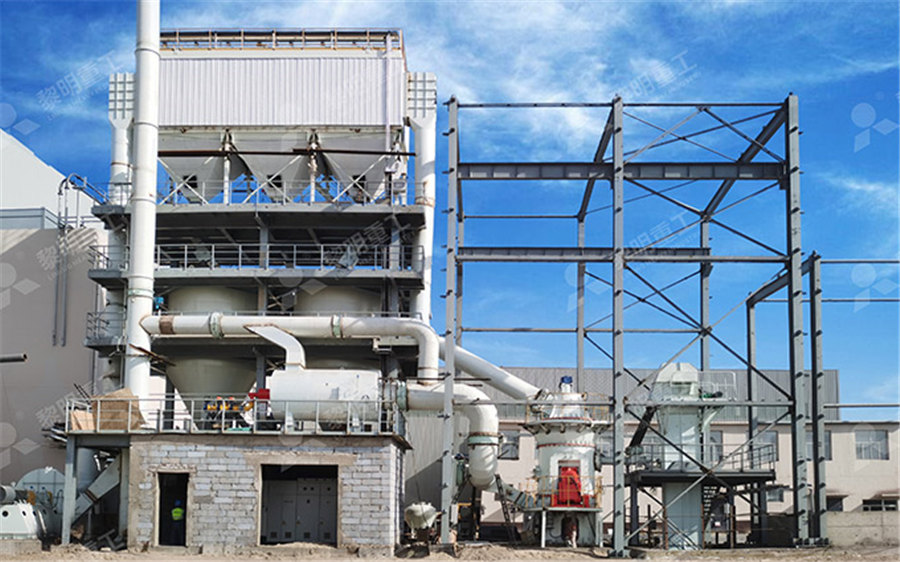
An investigation into the distinctive sintering performance and
2020年4月1日 With the type of limonitic nickel laterite transformed from highgangue to lowgangue nickel ore, tumble index and productivity are improved from 4587% and 097 t m−2 h−1 to 5016% and 105 t 2011年1月1日 The research of smelting low ferronickel from preconcentrate nickeliron ore with 276 % Ni and 3800 % Fetotal was carried out to find an effective way for stainless steel enterprises to use the Dehydrating and sintering of Philippine nickel laterite3 Dry, M Technical Cost Comparison of Laterite Treatment Processes Part 3 ALTA 2015 Proceedings, Perth, Australia pp 2447 4 Dry, M Technical Cost Comparison of Laterite Treatment Processes Part 4 – Hydroxide to Metal ALTA 2016 Proceedings, Perth, Australia pp 8197 Technical Cost Comparison of Laterite Treatment Processes 1Technical Cost Comparison of Laterite Treatment Processescrease if the nickel laterite ores are hydrated and sintered by means of traditional sintering, and if the nickel lateritic sinters are then reduced in the shaft furnace To facilitate this process, a comparative study on sintering behaviors of nickel laterite from the Philippines and Indonesia was carried out in this paper 2 ExperimentalMineral Change of Philippine and Indonesia Nickel Lateritic Ore
.jpg)
Bioleaching of Lateritic Nickel Ores SpringerLink
Pressure acid leaching has been applied to the Caron process to reduce highenergy consuming phases in direct ore leaching Direct leaching eliminates the need for drying and reduction steps, which then leads to energy savings (Buyukakinci, 2008)The acceptable nickel content in this method is 1–5% (Dalvi et al, 2004)Also, the crushed ore is dissolved directly with sulfuric acid 23 Direct reduction of laterite nickel ore in industrial scale Most laterite nickel ore processing is carried out using Elkem process The Elkem process uses Rotary Kiln and Electric Furnace (RKEF) to reduce and smelt laterite nickel ore Commercialization of Elkem process itself began with the development of a pilot plant in 1953–1954Selective Reduction of Laterite Nickel Ore JSTAGE2023年3月28日 In this paper, lowgrade limonitic nickel laterite and chromite were synergistically utilized via the hybrid sintering process (ie, pelletsintering process) for highquality Ni–Cr sinter preparation and great carbon emission reduction Under the optimum process conditions, Ni–Cr sinter indices were substantially improved in the pelletsintering process Tumble index and Reduction of Carbon Footprint Through Hybrid Sintering of Low The second principle of ferronickel smelting is that laterite ores cannot be smelted to nickel metal alone, ie, separately from iron This is because (1) garnierite concentrates always contain 5–10 times more Fe than Ni and (2) oxygen is only slightly more strongly bonded to Fe than to Ni—ie, FeO in calcined concentrate is almost as easy to reduce as NiOLaterite Ore an overview ScienceDirect Topics
.jpg)
Roasting and Leaching Behavior of Nickel Laterite Ore
2021年3月29日 Nickel can be found in laterite ores, sulfide ore, in secondary resources, and nonland resources like sea nodules[6,7] However, only 40 pct of nickel scrap can be recovered as secondary sources, nonland resources require high investment and operational costs, thus, sulfides and lateritic ores are the most important nickel sources[6,8,9,10,11,12] The identified 2013年6月25日 The Goro Nickel Mine is one of the world’s largest Nickel Laterite Mines The project is owned by Vale (69%), a joint venture company composed of Sumic Nickel Netherlands, Sumitomo Metal Mining and Mitsui (21%) and the remaining Nickel Laterites: The World’s Largest Source of Nickel2024年3月13日 The leaching behavior of nickel and iron in limonitetype laterite nickel ore was studied through ammonium hydrogen sulfate atmospheric leaching The leaching temperature, ammonium bisulfate concentration, reaction time, and acid excess rate during the nickel dissolution process were optimized using the response surface methodology (RSM) Leaching Kinetics of LimoniteType Laterite Nickel Ore from 2014年1月1日 The sintering experiment of laterite with different carbon content were carried out, and the effect of carbon content on sintering velocity, agglomeration ratio, mass loss, temperatures of off gas The application of nickel lateritic ores in sintering ResearchGate
.jpg)
Sintering Characteristics of Iron Ores with Addition of Laterite Nickel
The results showed that the adding proportion of laterite nickel ores should be less than 15% when the high temperature properties of the mixing ores were well Increasing the mixing ration of laterite nickel ores in the sintering blending would play an