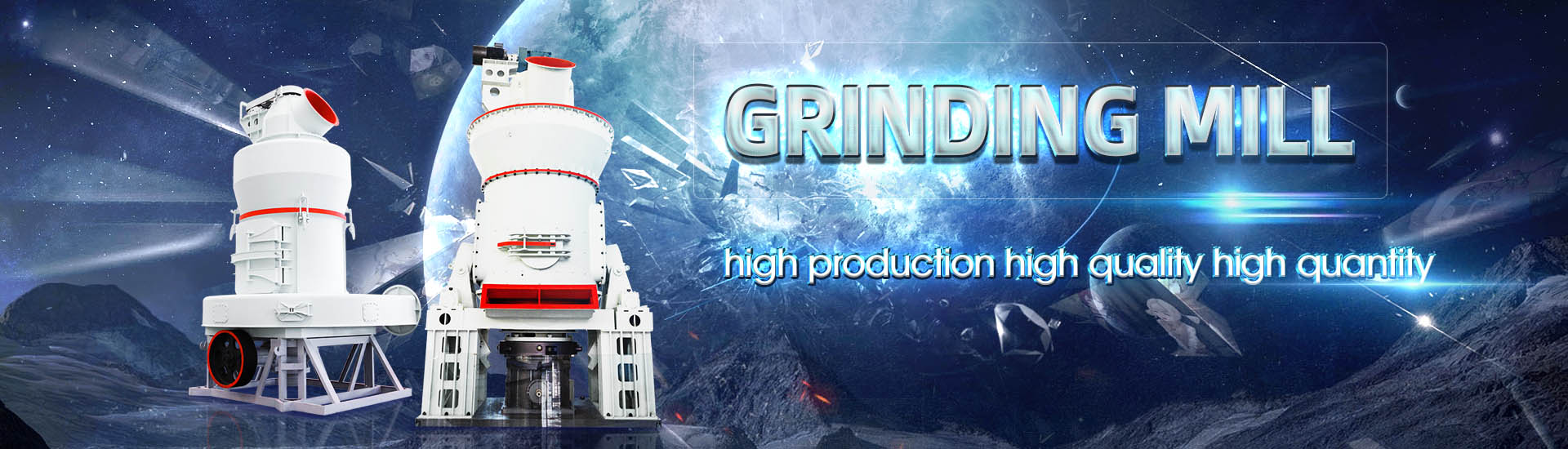
Coal Mill Roller Wear Coal Mill Roller Wear Coal Mill Roller Wear

A Wear Condition Monitoring Model of Coal Mill Grinding Roller
2020年12月21日 In order to realize the monitoring of grinding roller wear state of coal mill in power plant as well as improve the reliability and safety of equipment, it is essential to build a Abstract: In order to solve the problem to directly measure the wear of roller of HP coal mill in thermal power plant, this paper proposes a new design scheme of wear monitoring and Design Scheme of Fault Diagnosis System for Rollers of Coal Mills2020年10月14日 Based on the extracted root mean square and kurtosis features, the tool wear monitoring is realized by MSPCA and PCA respectively The analysis and comparison results A Wear Condition Monitoring Model of Coal Mill Grinding Roller 1996年3月1日 This paper reports on the contribution of a number of material coal properties and machine operating parameters to the wear of vertical spindle mill components This assists in Component wear in vertical spindle mills grinding coal
.jpg)
The wear mechanism of mill beaters for coal grinding madeup
2022年12月1日 Determination of the causeandeffect relationship regarding the wear of the lining (beater) of a coal beater mill is presented The type and state of the material used for the To realize the wear condition of grinding roller of coal mill in power plant and improve the reliability of the equipment, it is essential to build a monitoring model with high accuracy for grinding A State Monitoring Method for Coal Mill Grinding Roller Base On 2011年9月1日 This study is aimed at identifying the most common degradation mechanisms occurring in closed circuit high stress comminution equipment such as vertical roller mills Both Wear mechanism of abrasion resistant wear parts in raw material Abstract: In order to monitor the wear condition of grinding roller of coal mill in power plant and improve the reliability of production equipment, it is necessary to establish a state monitoring Monitoring Model of Coal Mill in Power Plant Based on Big Data
.jpg)
A Wear Condition Monitoring Model of Coal Mill Grinding Roller
2020年10月14日 In order to realize the monitoring of grinding roller wear state of coal mill in power plant as well as improve the reliability and safety of equipment, it is essential to build a This article, based on the abrasion condition of the rollers on the working field, analyzes the movement characteristics of the material layer of the vertical roller mills from several aspects, Wear mechanism of the rollers of MPS vertical roller millVertical coal grinding mill integrates crushing, drying, grinding, powder selection and conveying; It has simple system and compact structure Vertical coal mill covers an floor area about 50% of the coal ball mill with the same Vertical Coal Mill for Coal Grinding in Cement Plant2013年2月1日 Wear mechanisms in a coal pulveriser Compression, abrasion and impact are the three wear mechanisms that act upon the grinding elements and the pulveriser internals Compression is a wear component that results Coal pulverisation with vertical roller mills
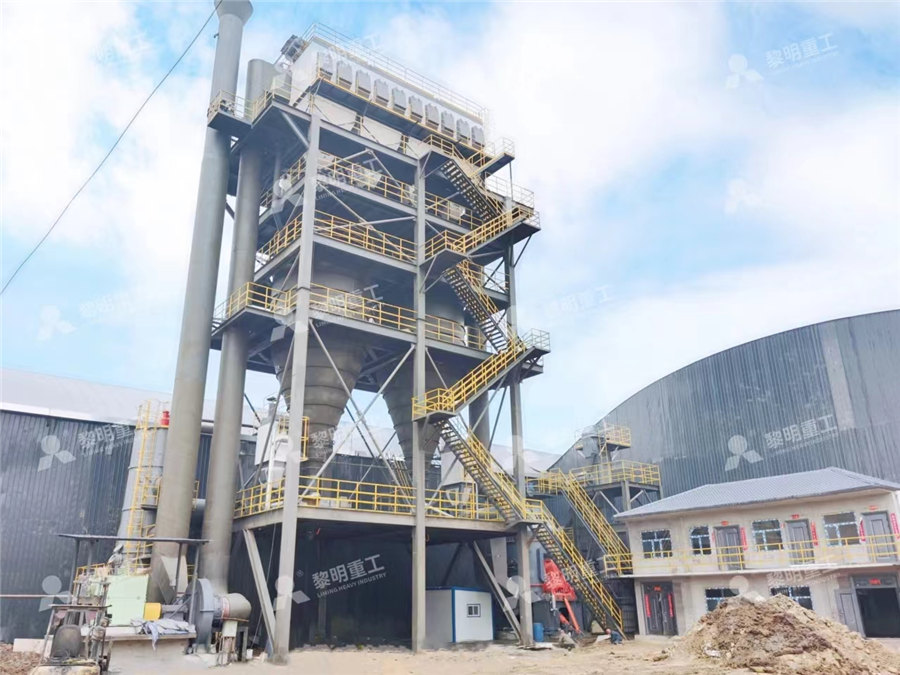
Technical specifications of vertical roller coal mill
This study shows the performance of a currently running vertical roller coal mill (VRM) in an existing coalfired power plant In a power plant, the coal mill is the critical equipment, whose and power plants Gebr Pfeiffer SE (GPSE) describes its vertical roller mills for coal grinding and provides a case study of an MPS225BK installed at CBR’s Lixhe cement works in Belgium COAL GRINDING Figure 1: MPS coal grinding mill with SLS highefficiency classifier Figure 2: MPS series for coal grinding millsCOAL GRINDING IMPS: more than meets the eye Gebr Pfeiffer• Grinding roller wear • Fineness (Blaine) or residue (VOA) • Mill motor speed • Mill air flow/mill differential pressure • Temperature after the mill • Pressure before the mill • Grinding stock feed • Classifier speed • Mill fan speed • Water spraying • Hot gas • Fresh air Manipulated variables Disturbance variable PROCESS OPTIMISATION FOR LOESCHE GRINDING PLANTS2012年11月17日 20 131Fineness Fineness is an indicator of the quality of the pulverizer action Specifically, fineness is a measurement of the percentage of a coal sample that passes through a set of test sieves usually designated at 50, 100, and 200 mesh A 70% coal sample passing through a 200 mesh screen indicates optimum mill performance The mill wear and Coal mill pulverizer in thermal power plants PPT SlideShare

A Study on 500 MW Coal Fired Boiler Unit’s Bowl Mill
hour data pulverized coal fineness report, coal data, grinding roll wear depth, preventive maintenance data etc, from the plant, are collected The service checks, overhaul and necessary checks of the operating conditions of certain important components of the mill listed below are undertaken, to ensure the Figure 2 Section of coal bowl mill DOI: 101145/ Corpus ID: ; A Wear Condition Monitoring Model of Coal Mill Grinding Roller Based on LSTM @article{Li2020AWC, title={A Wear Condition Monitoring Model of Coal Mill Grinding Roller Based on LSTM}, author={Yanping Li and Liang Tian and Yongping Li and Yaokui Gao}, journal={Proceedings of the 2020 International A Wear Condition Monitoring Model of Coal Mill Grinding Roller 2020年8月12日 To understand the performance of a vertical roller coal mill, the real operational tests have been performed considering three different coal sources Obtained results indicate that grinding pressure, primary air (PA) temperature and mill motor current have a tendency to rise by increasing coal feeding mass flow rates for all used coalAn investigation of performance characteristics and energetic A vertical roller mill is an energysaving mill that meets market demand 3 sets of HLM1900M coal vertical mill Auxiliary equipment: Jaw crusher, conveyor belt, it will be more difficult to grind the powder, which will easily cause wear and tear on the equipment b The temperature of the material entering the millEnergysaving and Efficient Vertical Roller Mill Fote Machinery
.jpg)
Industrial Roller Mills Williams Crusher
As the acknowledged leader in fluid bed roller mill design, Williams Roller Mills provide years of reliable, consistent, and efficient operation However, what truly sets our equipment apart is their ease of use and maintenance Learn more The document provides installation and operation instructions for the HRM1700M Vertical Roller Coal Mill It describes the mill's technical parameters, components, structure, working principles, and installation process Key aspects include grinding rollers that can be removed for maintenance, a hydraulic system that controls grinding pressure, and a separator that Operation Manual: HRM1700M Vertical Roller Coal MillCompared with the vertical roller mill, the advantages of airswept ball mill are strong adaptability to raw coal quality, simple operation and low investment cost; the disadvantages are high power consumption and high noise Vertical Roller Coal Mill in Cement Plant Vertical Roller Mill Air 2023年7月4日 Roller mill is a type of grinding equipment for crushing blast furnace slag, and coal The highpressure roller mill mainly consists of the feeding system and damage of parts caused by the impact between the roller and the liner are avoided In addition, the roller and the liner are made of wearresistant steel to Roller Mill SpringerLink

Reprint from ZKG 3 Gebr Pfeiffer
In most areas of industrial grinding of bulk solids material, vertical roller mills (VRM) have prevailed Compared with ball mills, the ratio is about 90 to 10 This relationship also exists in coal grinding applications in the cement industry, where normally a twomillsystem is used 1 Introduction Two mill systems are employed for most coalThe raw material of coal powder is coal with various hardness, and it drying in the coal mill grinding process to obtain finished coal powder which can be efficiently burned Coal ball mills are widely used in the cement industry and thermal power generation industry, and are also suitable for metallurgical industry, chemical industry, sugar industry and other fieldsCoal Ball Mill Grinding for Different Kinds of Pulverized CoalCoal vertical mills also called coal mills, which are specialized in superfine grinding of raw coal and bituminous coal materials in cement plant, power plants, steel mills and other fields Capacity :570 t/h fineness :80 mu;mR 3% Power :1822 kWh/t Application :Power plant, cement plant, lime Roller mill GMRC Series coal mill Xinxiang Great Wall The coal vertical roller mill has less dust, low noise, high efficiency granular composition, and excellent combustion performance due to its special design and structure Chaeng(Great wall machinery) Vertical Roller Mill has simple process, compact structure, product fineness of 80μmR 3%, with steady and average product finenessVertical Coal Mill Great Wall
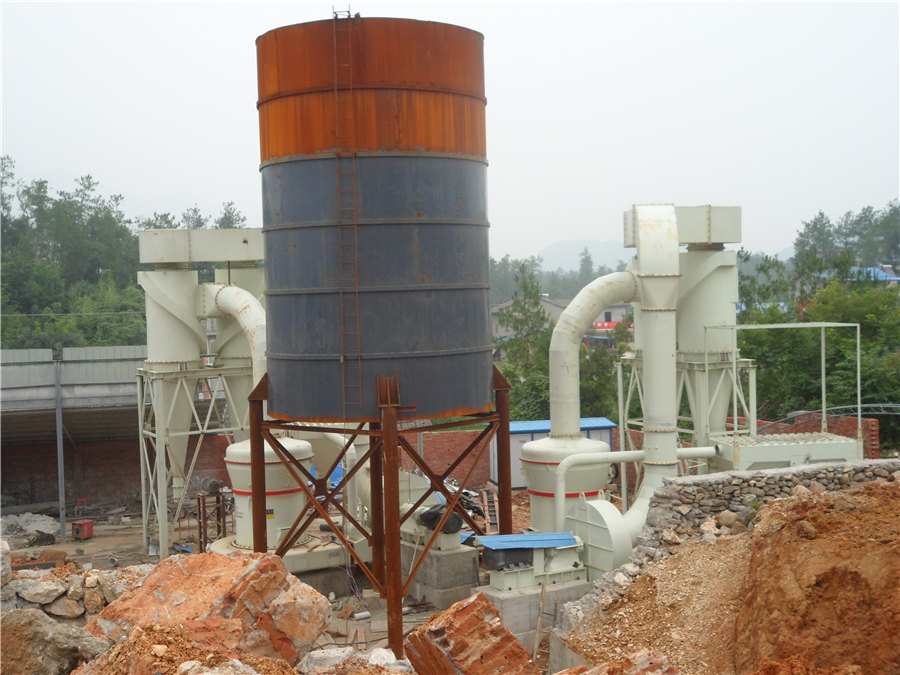
Pulveriser in Thermal Power Plant Bowl Mill Ball Mill
2021年8月5日 Larger pieces of coal are broken by impact and the fine grinding is done by attrition and crushing as the balls roll and slide within the charge Hot air flow is induced through the mill in order to dry the coal and remove the fines from balls themselves wear and are continuously replaced by new ones RELATED SEARCHES: Mill 2011年9月1日 Key word: Coal mill roller, Abrasive wear, Fluxcored wire, Resurfacing welding View Show abstract Comparison of a newly developed compressiontwist abrasive wear test with the ASTM G65 test Wear mechanism of abrasion resistant wear parts in raw 2014年1月1日 Two mill systems are employed for most coal grinding applications in the cement industry These are, on the one hand, vertical roller mills (VRM) that have achieved a share of almost 90% and, on (PDF) MPS mills for coal grinding ResearchGateHiChrome Wear Segments offer a longlasting, flexible, and environmentallyfriendly wear solution for our vertical roller mills Learn more ATOX ® Coal Mill Our ATOX® Coal Mill has large rollers with great grinding capability of virtually Vertical roller mills FLSmidth Cement

COAL PULVERIZER DESIGN UPGRADES TO MEET THE DEMANDS
emissions in coalfired power plants, Riley Power Inc (RPI), a Babcock Power Inc (BPI) company has been actively developing mill system technology to achieve better coal fineness, increased capacity, greater reliability, and longer wear life The effort has improved the design of low, medium, and highemissions in coalfired power plants, Riley Power Inc (RPI), a Babcock Power Inc (BPI) company has been actively developing mill system technology to achieve better coal fineness, increased capacity, greater reliability, and longer wear life The effort has improved the design of low, medium, and highCoal Pulverizer Design Upgrades to Meet the Demands of Low 1990 Central coal grinding plant (LM 263 D) for gas and steam power station (coal gasification) 1992 Central coal grinding plant (LM 263 D) for the production of lignite (brown) coal dust 2002 Coal grinding plant (LM 232 D) for grinding wood pellets for power stations 2005 First 4roller pressure mill (LM 434 D) becomes availableLOESCHEMILLSCrack repair of Ball Mill Crusher with PTA wear facing Onsite repair of Roller Press Our applications Based upon hundreds of successful applications approved by our clients across the globe, Castolin Eutectic can provide optimized solutions with a wide range of products and technologies to combat wear in VRM (Vertical Roller Mill) and many moreKey Industry Program Castolin Eutectic

Review on vertical roller mill in cement industry its
2021年1月1日 Grinding Mill Vertical Roller Mill or Ball Mill: The reclaimed raw mix fed to Raw Mills, for drying and fine grinding of Raw meal for kiln feed: 4: Coal Grinding: Grinding Mill Vertical Roller Mill or Ball Mill: Coal is ground in Coal mill, which is a fuel for use in Kiln firing: 5: Pyro Section, Clikerization: In line calciner six stage Roller Tire and Table Segment for Roller Mill; Wear and Heatresistant Castings for Bellless Type Blast Furnace; Valve untuk keperluan industri Hammer Crusher for Coal; Roll Grizzly/ Roller Screen; Impact Crusher; Dryers, Calciners/Kiln Indirect Heating Dryer KID Dryer;Vertical Super Fine Grinding Mill (Vertical Roller Mill) VX Mill Roller Mill Xiao Xiao1, Huang Lilong2 and Xu Kuangdi3 Raymond mill is mainly used to grind coal, nonmetallic ore, glass, ceramics, cement, gypsum, avoided In addition, the roller and the liner are made of wearresistant steel to minimize the wear of damageable partsRoller Mill SpringerQ1: Why are there so many cracks? A1 Due to the cooling rates of dissimilar metals Our hard facing plate for coal chute liner is manufactured by weld ing which results in high temperatures During the cooling, the plate goes through a stress relieving which is a natural process and does not effect the performance of the plate The stress relief cracks should be between 3/4" 2" apartHard Plate Coal Mill Grinding Roller Repair Welding Plate Wear
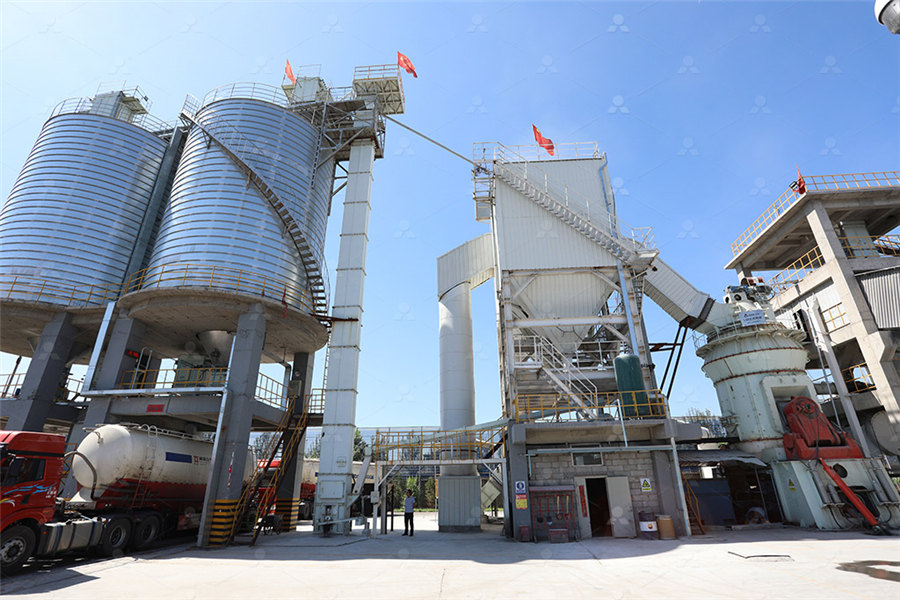
Vertical Coal Mill for Coal Grinding in Cement Plant
Vertical coal grinding mill integrates crushing, drying, grinding, powder selection and conveying; It has simple system and compact structure Vertical coal mill covers an floor area about 50% of the coal ball mill with the same 2013年2月1日 Wear mechanisms in a coal pulveriser Compression, abrasion and impact are the three wear mechanisms that act upon the grinding elements and the pulveriser internals Compression is a wear component that results Coal pulverisation with vertical roller millsThis study shows the performance of a currently running vertical roller coal mill (VRM) in an existing coalfired power plant In a power plant, the coal mill is the critical equipment, whose Technical specifications of vertical roller coal milland power plants Gebr Pfeiffer SE (GPSE) describes its vertical roller mills for coal grinding and provides a case study of an MPS225BK installed at CBR’s Lixhe cement works in Belgium COAL GRINDING Figure 1: MPS coal grinding mill with SLS highefficiency classifier Figure 2: MPS series for coal grinding millsCOAL GRINDING IMPS: more than meets the eye Gebr Pfeiffer
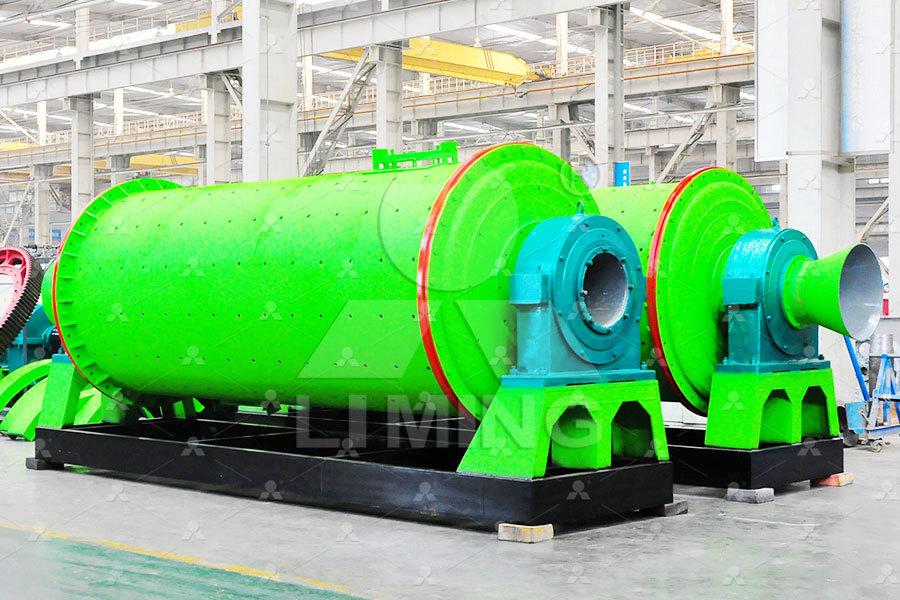
PROCESS OPTIMISATION FOR LOESCHE GRINDING PLANTS
• Grinding roller wear • Fineness (Blaine) or residue (VOA) • Mill motor speed • Mill air flow/mill differential pressure • Temperature after the mill • Pressure before the mill • Grinding stock feed • Classifier speed • Mill fan speed • Water spraying • Hot gas • Fresh air Manipulated variables Disturbance variable 2012年11月17日 20 131Fineness Fineness is an indicator of the quality of the pulverizer action Specifically, fineness is a measurement of the percentage of a coal sample that passes through a set of test sieves usually designated at 50, 100, and 200 mesh A 70% coal sample passing through a 200 mesh screen indicates optimum mill performance The mill wear and Coal mill pulverizer in thermal power plants PPT SlideSharehour data pulverized coal fineness report, coal data, grinding roll wear depth, preventive maintenance data etc, from the plant, are collected The service checks, overhaul and necessary checks of the operating conditions of certain important components of the mill listed below are undertaken, to ensure the Figure 2 Section of coal bowl mill A Study on 500 MW Coal Fired Boiler Unit’s Bowl Mill DOI: 101145/ Corpus ID: ; A Wear Condition Monitoring Model of Coal Mill Grinding Roller Based on LSTM @article{Li2020AWC, title={A Wear Condition Monitoring Model of Coal Mill Grinding Roller Based on LSTM}, author={Yanping Li and Liang Tian and Yongping Li and Yaokui Gao}, journal={Proceedings of the 2020 International A Wear Condition Monitoring Model of Coal Mill Grinding Roller
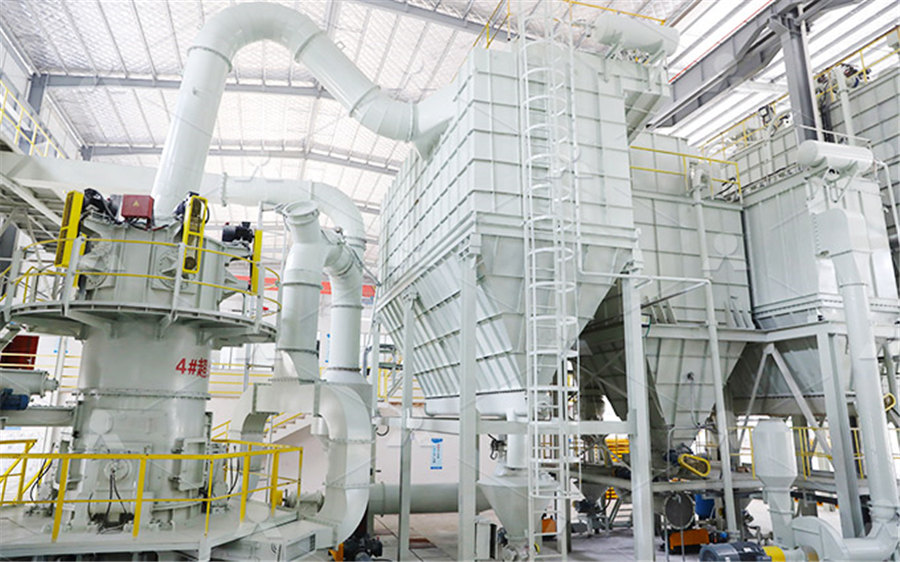
An investigation of performance characteristics and energetic
2020年8月12日 To understand the performance of a vertical roller coal mill, the real operational tests have been performed considering three different coal sources Obtained results indicate that grinding pressure, primary air (PA) temperature and mill motor current have a tendency to rise by increasing coal feeding mass flow rates for all used coalA vertical roller mill is an energysaving mill that meets market demand 3 sets of HLM1900M coal vertical mill Auxiliary equipment: Jaw crusher, conveyor belt, it will be more difficult to grind the powder, which will easily cause wear and tear on the equipment b The temperature of the material entering the millEnergysaving and Efficient Vertical Roller Mill Fote Machinery