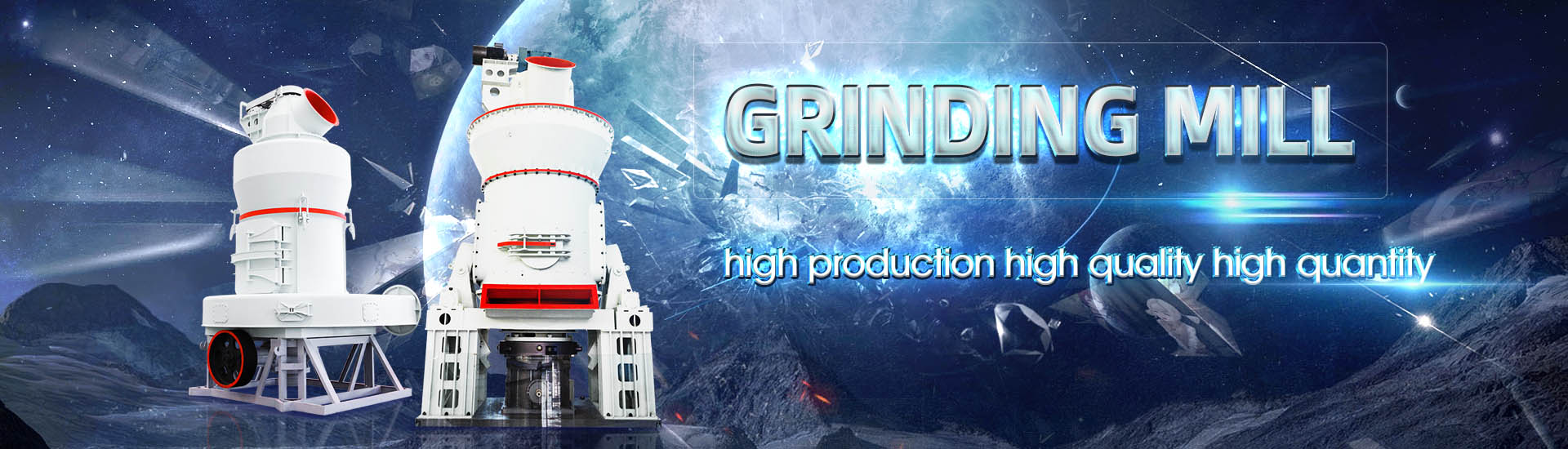
Technical parameters of prsd1608 white carbon black ore mill
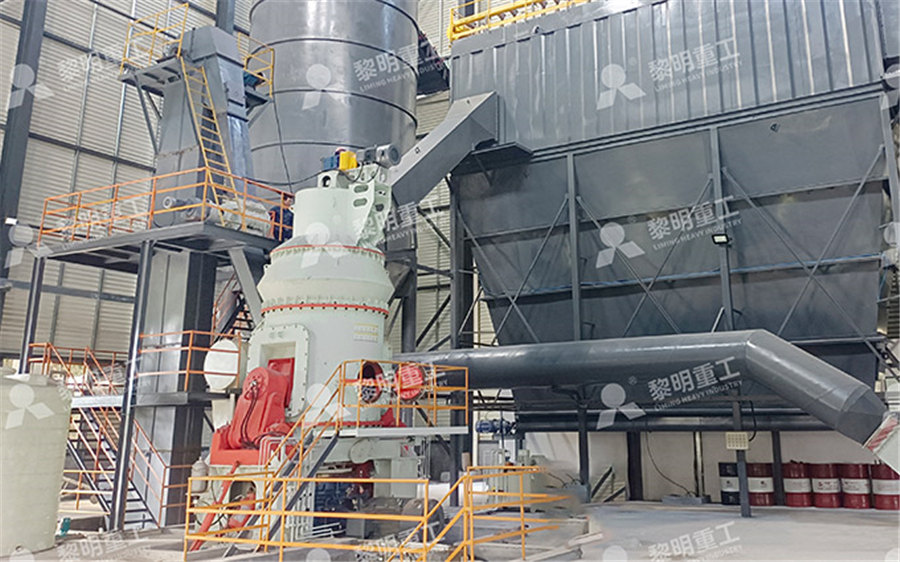
Optimisation and analysis of bead milling process for preparation
The optimum milling process parameters, ie, the milling time and the milling speed, to prepare pigment dispersion depends on a number of factors including the pigment hardness, the 2018年6月1日 We have devised a method to establish the optimum milling parameters for a particular type of pigmentdispersion system In addition, a method is proposed to ascertain Optimisation and analysis of bead milling process for preparation ENERGYEFFICIENT RECOVERED CARBON BLACK FINISHING PRECISE CONTROL OF THE QUALITY AND TARGET FINENESS OF THE END PRODUCT HIGH PROCESS AND RECOVERED CARBON BLACK Hosokawa AlpineThis paper discusses the product development methodology of a unique carbon black dispersion technology, from conception of the idea to the development of a production proven process Process Development and Process Control Methodology of a
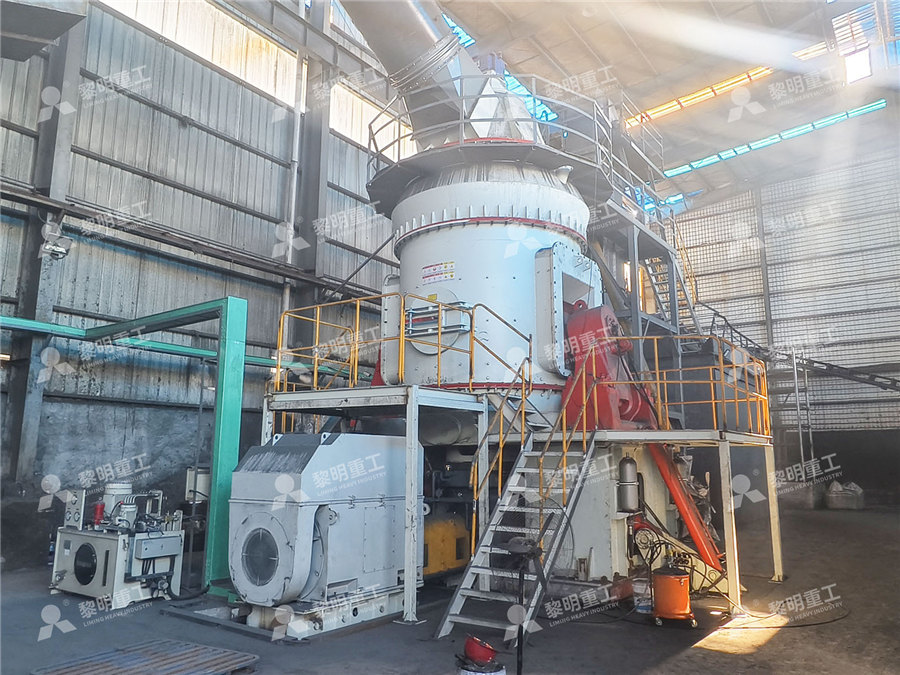
A Review of the Grinding Media in Ball Mills for Mineral Processing
2023年10月27日 These parameters are the fractional ball filling (J), the fraction of critical speed (fc), the fraction of the mill volume filled by powder (fc), powder filling (U), solids concentration, 2023年11月24日 These parameters are the fractional ball filling (J), the fraction of critical speed (fc), the fraction of the mill volume filled by powder (fc), powder filling (U), solids concentration, Grinding Media in Ball Mills for Mineral ProcessingThis paper presents the structure of the latest version of the JKTech autogenous and semiautogenous (AG/SAG) mill specific energy model, which is an adaptation of that previously SAG Mill Design and Benchmarking Using Trends in the JKTech 2021年10月21日 For the MA hydrometallurgical process, the key parameters for the mechanical device are the rotating speed \ (\left (\omega \right)\); diameter \ (\left (d\right)\) of the Effect of Ball Mill Parameters’ Variation on the Particles of a

Mill, material, and process parameters – A mechanistic model for
2019年8月1日 Introduction of mill, material and formulation parameters to stress model Prediction of optimum operation conditions, grinding times or specific energies Model is for determining applicationrelated technical warranty parameters The following mechanical and thermal process technology operations can be carried out on a production and on a Classifier Mill Hosokawa Micron Ltd2021年10月21日 The economic and technical values of the hydrometallurgical or leaching processing are a function of its reaction rates and these reaction rates are enhanced by mechanical activation (MA) in hydrometallurgical processing This study presents a novel derived theoretical model for MAassisted leaching in investigating the effects of ball mill parameters Effect of Ball Mill Parameters’ Variation on the Particles of a 2020年10月9日 In order to obtain the optimal operation parameters of a SAG mill, in this paper, the discrete element method (DEM) is used to simulate the breakage process of the particles by controlling three Operation Analysis of a SAG Mill under Different
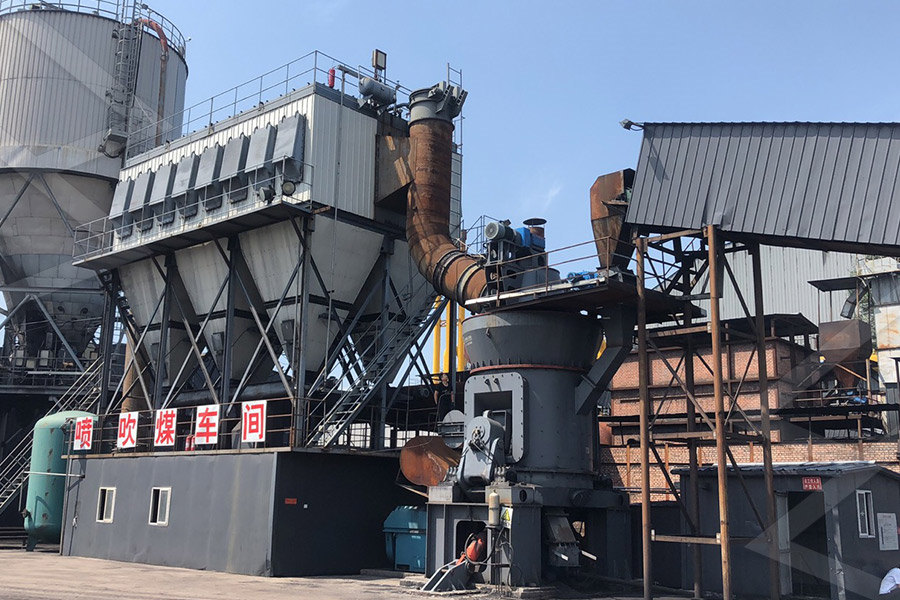
(PDF) Control of ball mill operation depending on ball
2023年12月12日 In addition, the ore properties are one of the important parameters for the optimal utilizing of the ball mill Ore can have various properties, such as hardness, density, moisture content, etc High energy utilization rate, low operating cost, grinding particle size range D50: 0510μm The revolution of dry milling technology, the milled particle size can reach submicron or nanometer level, which greatly improves the energy utilization efficiency and realizes low carbon, energy saving, environmental protection and resource recycling by supersonic steam jet millSupersonic Steam Jet Mill ALPA Powder Equipment2017年3月20日 Ball mill process parameters for five ground samples with ball load J = 050, particle filling U = 053, mill speed N c = 71% and mill factor F c = 069 Shape and size factors equation and Physicochemical Problems of Mineral Processing Investigation 2019年12月18日 In this paper, rice husk (RH) was used as raw material to prepare white carbon black, and the key technological parameters of preparing white carbon black from RH were studied through single Preparing high purity white carbon black from rice husk
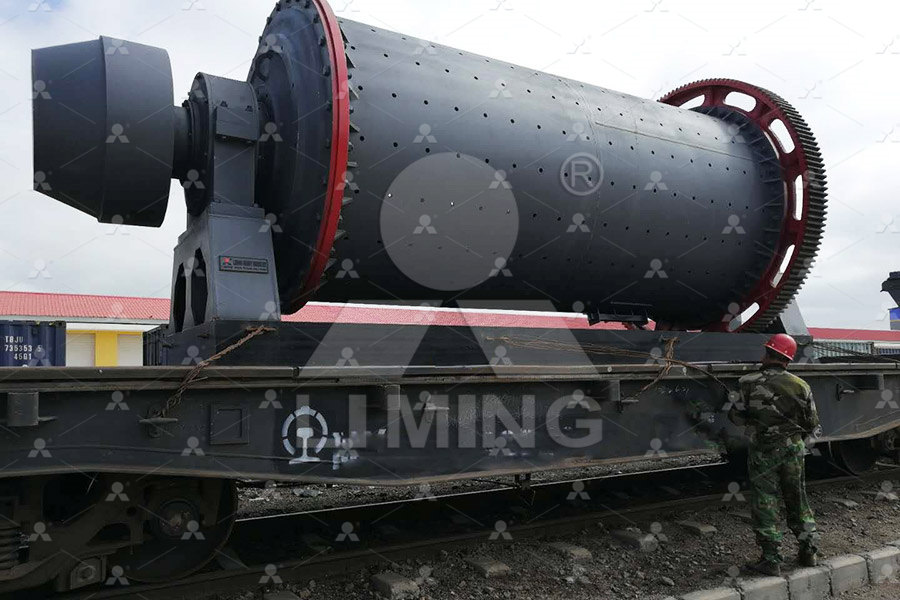
Research of iron ore grinding in a verticalrollermill
Request PDF On Mar 15, 2015, Mathis Reichert and others published Research of iron ore grinding in a verticalrollermill Find, read and cite all the research you need on ResearchGate2009年8月1日 Mill scale is an iron oxide waste generated during steelmaking, casting and rolling Total generation of mill scale at JSWSL is around 150 t/day and contains 60–70%FeO and 30–35%Fe2O3Recycling of steel plant mill scale via iron ore ResearchGate2017年4月14日 The use of acid in large doses and complex processes hindered their application yet More methods were reported to promote the quality as well as reduce the cost in the past years, including Preparation and Characterization of White Carbon Black From Blast furnace slag (BFS), a waste product of the iron manufacture process, contains a mass of silica obtained from gangue of the iron ores and ash content in fuels and fluxes In recent years, large amounts of BFS have not been fully utilized, leading to the surrounding environmental pollution and the additional administration costs for steel enterprises in China A simple Synthesis Method of White Carbon Black Utilizing Water
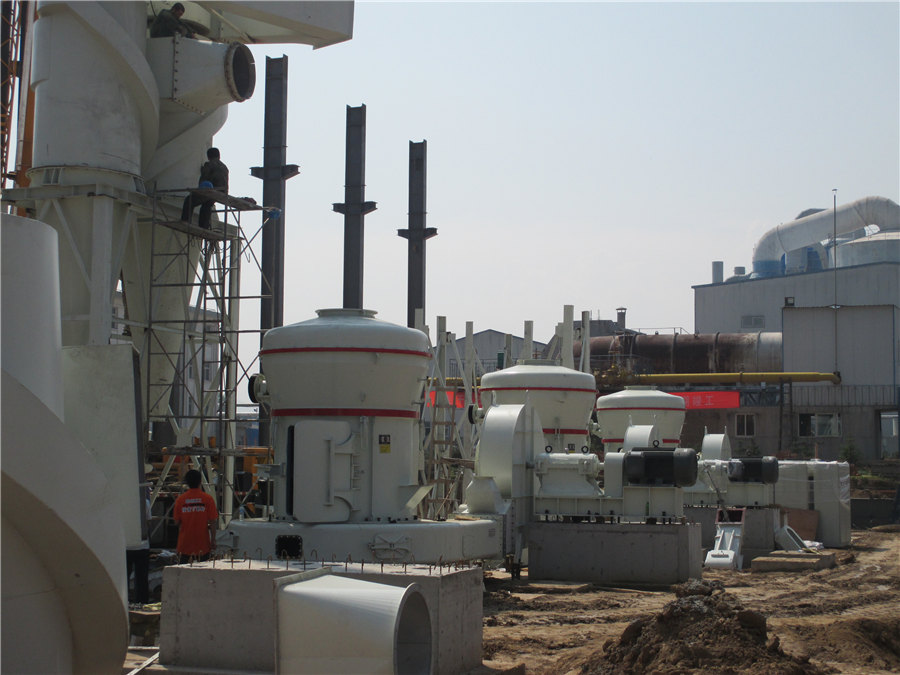
(PDF) Grinding Media in Ball MillsA Review
2023年4月23日 Comminution is a very important and resultdetermining step in mineral processing This is because further downstream processes in the beneficiation chain depend entirely on itWhere does a Hot Strip Mill fit in the flatroll production process? Making, Shaping and Treating of Steel: 101 3 4 11/2/2020 3 Making, Shaping and Treating of Steel: 101 • Required Geometric Parameters: Thickness Width Flatness Straightness (Camber) Profile (Crown / Edge Drop) 7 8 11/2/2020 5 Making, Shaping and Treating of Steel: 101Principles of Hot Rolling AIST2012年4月1日 Despite the simplicity of the simultaneous state and parameter estimation method it is known to suffer from several limitations For example, the authors in [17] showed that the simultaneous Dual particle filters for state and parameter estimation with 2019年10月1日 Firstly, the conventional ball mill parameters such as mill speed (% of critical speed), material filling ratio (Jb), ball filling ratio (fc), ball size distribution (10203040 mm, %), grinding Wet and dry grinding of coal in a laboratoryscale ball mill: Particle
.jpg)
New life for old tiresCarbon black powder mill SBM Ultrafine
2023年7月17日 1 Refined carbon black is reused to make car tires, fan belts and printer toner 2 Regenerated carbon black can be refined into nanoscale quality to replace expensive primary carbon black, enabling manufacturers to provide cheaper substitutes and replacement products Project story Getting to know SBM for the first time2020年11月22日 Pulp and paper mills generate huge amount of wastewater depending on the type of processes used in the plant whose unsafe disposal can be very hazardous to environment and human health(PDF) Characteristics and Treatment of Pulp and Paper Mill 2016年1月1日 Basic oxygen furnace slag (BOF slag) contains high amount of useful oxides such as CaO, MgO, SiO 2 , etc, therefore, a solution of the slag recycling would be used as a flux in pelletizing process(PDF) Improving reducibility of iron ore pellets by optimization of 2020年1月3日 The stateoftheart of both technology and operational practice of a hot rolling mill are discussed The focus is first on the control of entry temperature in the finish mill2020 Technology and Operation of a Hot Rolling Mill
.jpg)
(PDF) Mill scale as a potential additive to improve the quality
2017年12月21日 (a) Acidic iron ore pellet without mill scale (b) Acidic iron ore pellet with 15% mill scale Figure 6 Effect of mill scale on apparent porosity in acidic pellet2232 Investigation of parameter for pelletizing and briquetting at pilot scale (Task 32) 25 2233 Discussion of results and transfer 28 224 Thermal Evaluation of PreTreated ACASOS 30 2241 Thermal lab scale tests 30 2242 Technical scale tests using ACASOS for evaluating sinter parameter and quality 33Alternate carbon sources for sintering of iron ore2020年8月12日 VRM has been widely researched in processing of cement (Ito et al 1997;Jorgensen 2005;Wang et al 2009, Ghalandari et al 2021), coal (Tontu 2020), iron ore (Reichert et al 2015), zinc ore (van An investigation of performance characteristics and This continuous powder surface coating system is designed on the base of German know how with Chinese equipment, and can be used for coating of various powders like calcium carbonate (GCC, PCC), kaolin, talc, mica, ThreeRoller Coating Machine EPIC Powder
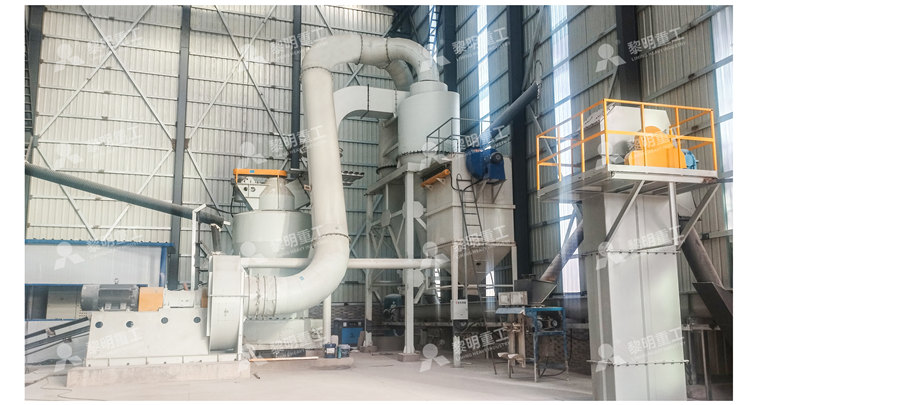
Grinding in Ball Mills: Modeling and Process Control
2012年6月1日 PDF The paper presents an overview of the current methodology and practice in modeling and control of the grinding process in industrial ball mills Find, read and cite all the research you 2021年2月19日 The ball mill process parameters discussed in this study are ball to powder weight ratio, ball mill working capacity and ball mill speed As Taguchi array, also known as orthogonal array design, adds a new dimension to conventional experimental design, therefore, Orthogonal array (L9) was carefully chosen for experimental design to understand the effects Comparative Study on Improving the Ball Mill Process Parameters 2017年1月1日 An increase of over 10% in mill throughput was achieved by removing the ball scats from a single stage SAG mill These scats are non spherical ball fragments resulting from uneven wear of balls (PDF) Performance optimization of an industrial ball mill for 2020年7月23日 Optimization of stirred mill parameters for fine grinding of PGE bearing chromite ore, Particulate Science and Technology, DOI: 101080/2020 To link to this article: https://doi Optimization of stirred mill parameters for fine grinding of PGE
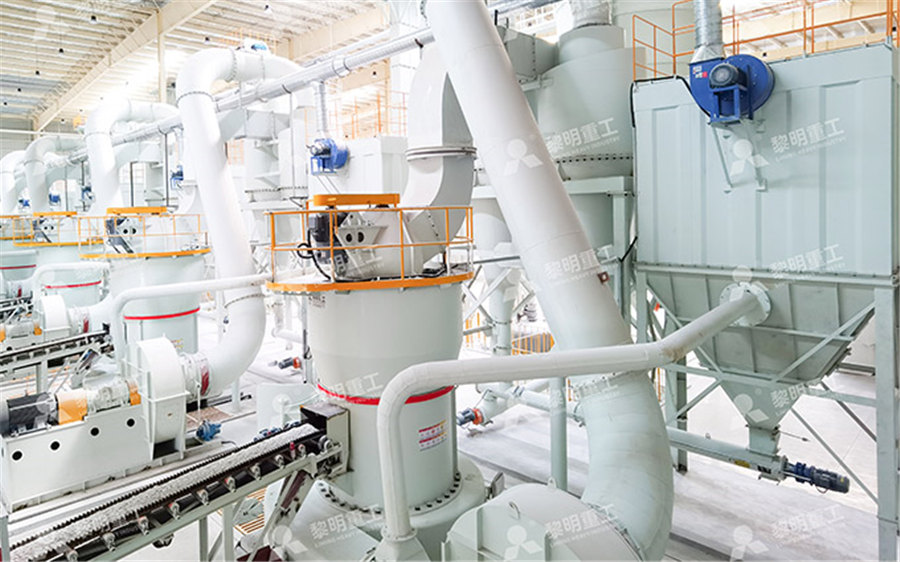
STUDY OF IRON EXTRACTION FROM MILL SCALE ResearchGate
2020年6月1日 Mill scale is bluishblack in color It is usually less than 01 mm (00039 in) thick, and initially adheres to the steel surface and protects it from atmospheric corrosion provided no break 2018年2月1日 In another study to investigate ball size distribution on ball mill efficiency by Hlabangana et al [50] using the attainable region technique on a silica ore by dry milling, a threeball mix of Effect of ball and feed particle size distribution on the milling (SAG) mill with each hour costing between 30,000 to 200,000 USD and such maintenance can occur every six to nine months [1] SAG mills are the technology of choice for reducing primary hardrock ore to feed size for use in a secondary crusher In these mills, cascading ore undergoesPREDICTIVE OPTIMIZATION OF SAG MILL WEAR USING ROCKY2022年1月15日 The optimization process is applied to the machining operations in order to provide continual improvement in accuracy and quality of produced parts(PDF) A Review of the Recent Development in Machining Parameter
.jpg)
Effect of Ball Mill Parameters’ Variation on the Particles of a
2021年10月21日 The economic and technical values of the hydrometallurgical or leaching processing are a function of its reaction rates and these reaction rates are enhanced by mechanical activation (MA) in hydrometallurgical processing This study presents a novel derived theoretical model for MAassisted leaching in investigating the effects of ball mill parameters 2020年10月9日 In order to obtain the optimal operation parameters of a SAG mill, in this paper, the discrete element method (DEM) is used to simulate the breakage process of the particles by controlling three Operation Analysis of a SAG Mill under Different 2023年12月12日 In addition, the ore properties are one of the important parameters for the optimal utilizing of the ball mill Ore can have various properties, such as hardness, density, moisture content, etc (PDF) Control of ball mill operation depending on ball High energy utilization rate, low operating cost, grinding particle size range D50: 0510μm The revolution of dry milling technology, the milled particle size can reach submicron or nanometer level, which greatly improves the energy utilization efficiency and realizes low carbon, energy saving, environmental protection and resource recycling by supersonic steam jet millSupersonic Steam Jet Mill ALPA Powder Equipment
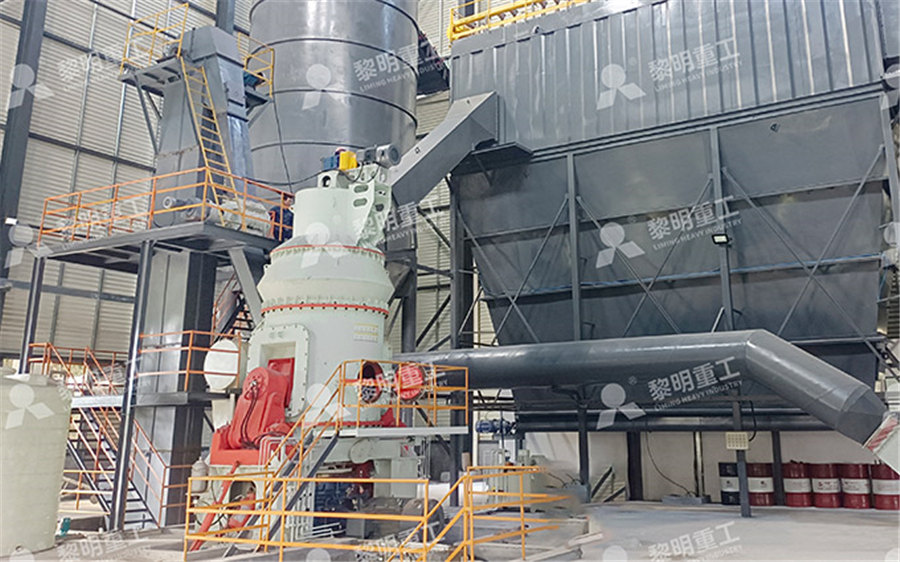
Physicochemical Problems of Mineral Processing Investigation
2017年3月20日 Ball mill process parameters for five ground samples with ball load J = 050, particle filling U = 053, mill speed N c = 71% and mill factor F c = 069 Shape and size factors equation and 2019年12月18日 In this paper, rice husk (RH) was used as raw material to prepare white carbon black, and the key technological parameters of preparing white carbon black from RH were studied through single Preparing high purity white carbon black from rice huskRequest PDF On Mar 15, 2015, Mathis Reichert and others published Research of iron ore grinding in a verticalrollermill Find, read and cite all the research you need on ResearchGateResearch of iron ore grinding in a verticalrollermill2009年8月1日 Mill scale is an iron oxide waste generated during steelmaking, casting and rolling Total generation of mill scale at JSWSL is around 150 t/day and contains 60–70%FeO and 30–35%Fe2O3Recycling of steel plant mill scale via iron ore ResearchGate

Preparation and Characterization of White Carbon Black From
2017年4月14日 The use of acid in large doses and complex processes hindered their application yet More methods were reported to promote the quality as well as reduce the cost in the past years, including Blast furnace slag (BFS), a waste product of the iron manufacture process, contains a mass of silica obtained from gangue of the iron ores and ash content in fuels and fluxes In recent years, large amounts of BFS have not been fully utilized, leading to the surrounding environmental pollution and the additional administration costs for steel enterprises in China A simple Synthesis Method of White Carbon Black Utilizing Water