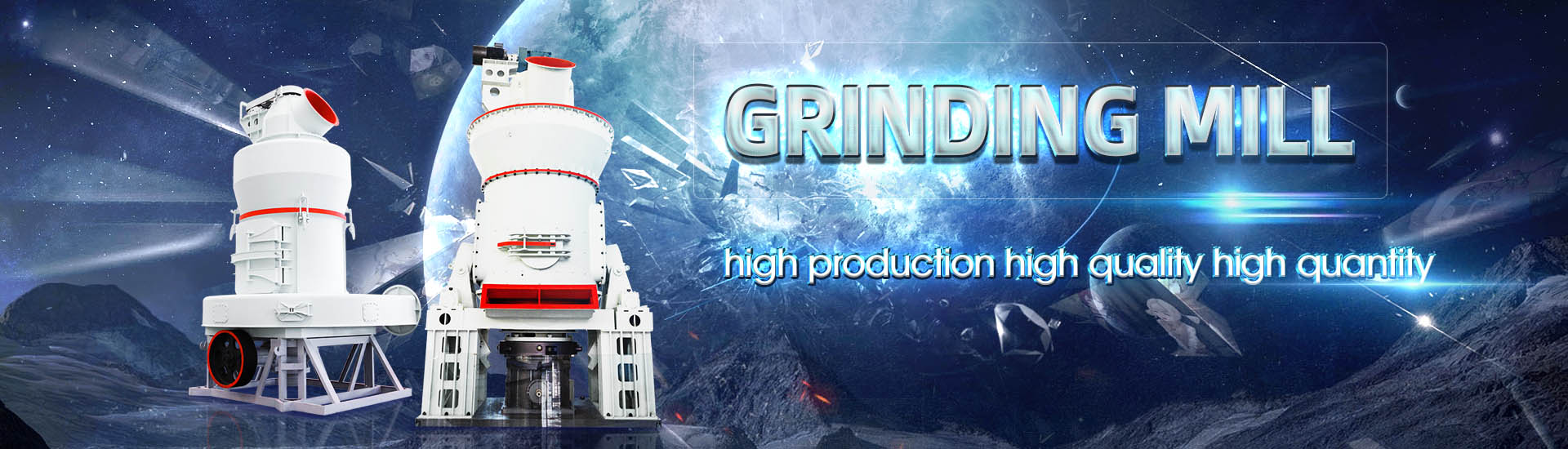
HOME→Calculation formula for cement mill steel ball quicklime cement mill steel ball quicklime Calculation formula for cement grinding steel ball quicklime
Calculation formula for cement mill steel ball quicklime cement mill steel ball quicklime Calculation formula for cement grinding steel ball quicklime

Ball Mill Calculations PDF Mill (Grinding) Industrial
The document contains formulas and examples for calculating key performance metrics for ball mills used in cement production It includes formulas to calculate power consumption, production rate, specific power, circulation factor, online live calculators for grinding calculations, Ball mill, tube mill, critical speed, Degree of filling balls, Arm of gravity, mill net and gross powerball mill calculations, grinding media filling degree, ball size, mill ball mill performance efficiency formulas if you work in a cement plant and you need courses and manuals like this manual and books and excel sheets and Ball Mill Performance Efficiency Formulas INFINITY 13 Ball Mill Study Data 105 14 Ball Mill Formulas 111 15 BIS Specification of Additives 113 16 Cement Testing 115 17 BIS Specifications for various Cements 120 18 Thermo Physical CEMENT FORMULAE HANDBOOK Green Business Centre
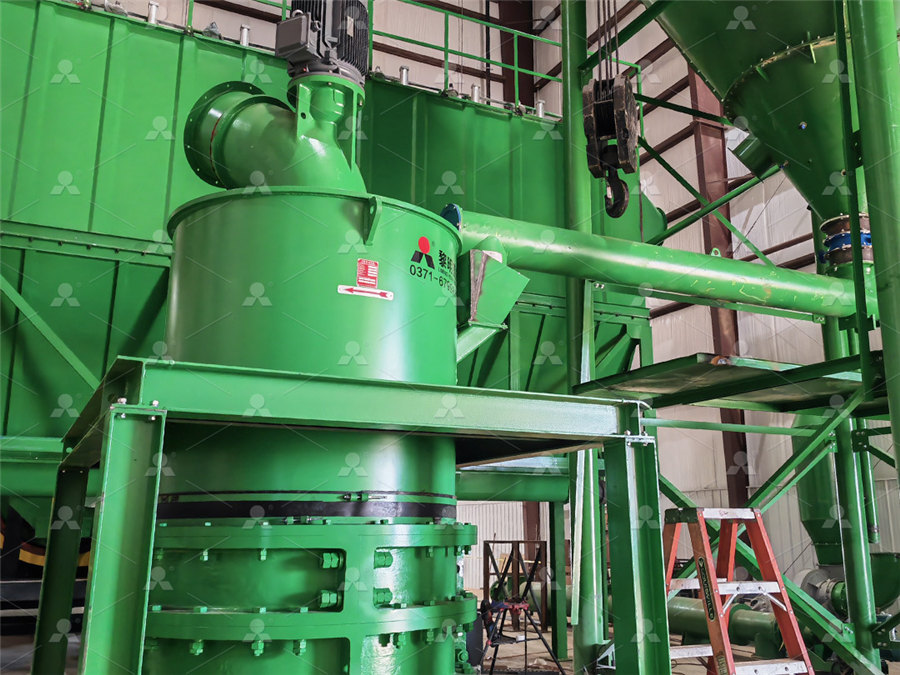
Cement ball mill process calculation pdf PPT
2024年1月5日 The document discusses the movement of grinding media in ball mills, optimal ball charge and filling levels, key components like linings, diaphragms, drives and bearings, and factors that influence mill operation This document provides information on performance metrics and formulas for evaluating ball mill efficiency at Ambuja Cement Rajasthan Limited It includes definitions and calculations for key parameters like arm of gravity, torque Ball Mill Calculations PDF Mill (Grinding) Industrial All Ball mill or tube mill calculation, Critical speed, Ball Size calculations, Separator efficiency, Mill power cnsumption calculation, production at blain Optimization; Online Training; Process and Ball mill calculations, tube mill calculations, separator efficiency This document provides guidance on ball mill grinding processes It covers topics such as ball mill design including length to diameter ratios, percent loading, critical speed, and internals evaluation Methods for assessing ball charge, Ball Mill Grinding Process Handbook
.jpg)
BALL MILLS Ball mill optimisation Holzinger Consulting
Ball mill optimisation As grinding accounts for a sizeable share in a cement plant’s power consumption, optimisation of grinding equipment such as ball mills can provide significant cost Find: required maximum ball size – F80 – Maximum ball size (mm) Mill performance test Steps 1 Recording of related operational data 2 Air flow measurement 3 Crash stop and visual inspection in mill 4 Sampling in mill 5 Cement Separator Ball Mill OptimizationAn inefficient ball mill is a major expense and could even cost you product quality The best ball mills enable you to achieve the desired fineness quickly and efficiently, with minimum energy expenditure and low maintenance With more Ball mill for cement grindingVertical roller mills and ball mills represent two clearly distinct technologies However, with proper adjustments to the operational parameters of the vertical roller mill almost identical cement properties can be achieved by the two mills Cement grinding Vertical roller mills VS ball mills
.jpg)
Ball charge optimization INFINITY FOR CEMENT EQUIPMENT
Previous Post Next Post Contents1 Ball charge optimization2 1 How to use the BP21 2 Description of the main indicators used in this BP2101 The residue on 2mm/4mm before partition wall2102 Material filling level and ball charge expansion211 Cement mill specific power 1st compartment 212 Raw mill specific power 1st compartment Ball charge Grinding Steel Ball Applicable Materials: Cement, silicate, newtype building material, refractory material, ferrous metal and nonferrous metal, glass ceramics, etc Under normal circumstances, it is not necessary to add small steel grinding balls When the ball mill is operating normally, friction will occur between the ball and ball, Choose the Best Grinding Steel Balls for Your Ball Mill Fote Mill performance is based on mill diameter and length only increases or decreases capacity The Slice Mill is simply a mill of the same diameter as the production mill but much shorter A Slice Mill of 72” diameter by 12” wide would replicate the result of Variables in Ball Mill Operation Paul O Abbe2024年1月5日 Ball mills are tube mills used for grinding materials like cement and involve several components The document discusses the movement of grinding media in ball mills, optimal ball charge and filling levels, key components like linings, diaphragms, drives and bearings, and factors that influence mill operation such as ventilation, water injection and Cement ball mill process calculation pdf PPT SlideShare
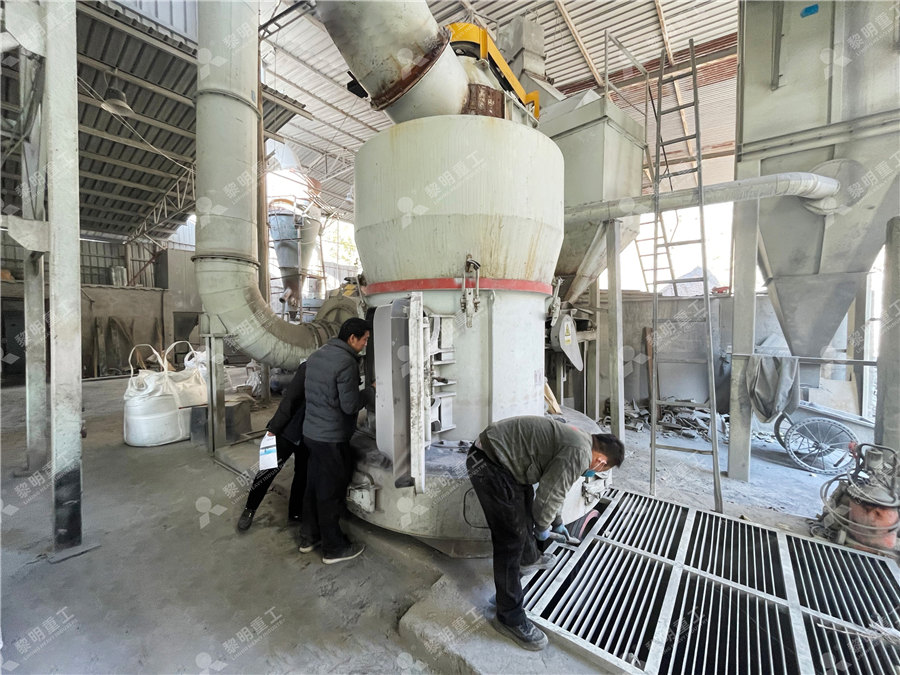
Cement Ball Mill Cost Effective Cement Grinding Mill from
The installation of liners Length Diameter Ratio The lengthdiameter ratio of the cement ball mill is relatively large For mills of opencircuit grinding system, the lengthdiameter ratio is usually between 35 and 6 to ensure that the product fineness is qualified through single grinding; For ball mills in closedcircuit grind system, in order to increase the material flow rate, the length 2019年8月30日 1 Calculation of ball mill capacity The production capacity of the ball mill is determined by the amount of material required to be ground, and it must have a certain margin when designing and selecting There are many Ball Mill Parameter Selection – Power, Rotate Speed, Cement mills are the milling machines used in cement plants to grind hard clinker into fine cement powders Cement ball mill and vertical roller mill are two most widely used cement mills in today’s cement grinding plants and are also the Cement Mill for Sale Buy Cement Ball Mill Vertical 2015年9月6日 Although it was developed nearly 50 years ago, Bond‘s method is still useful for calculating necessary mill sizes and power consumption for ball and rod mills This paper discusses the basic development of the Bond method, Calculate Top Ball Size of Grinding Media FRED C
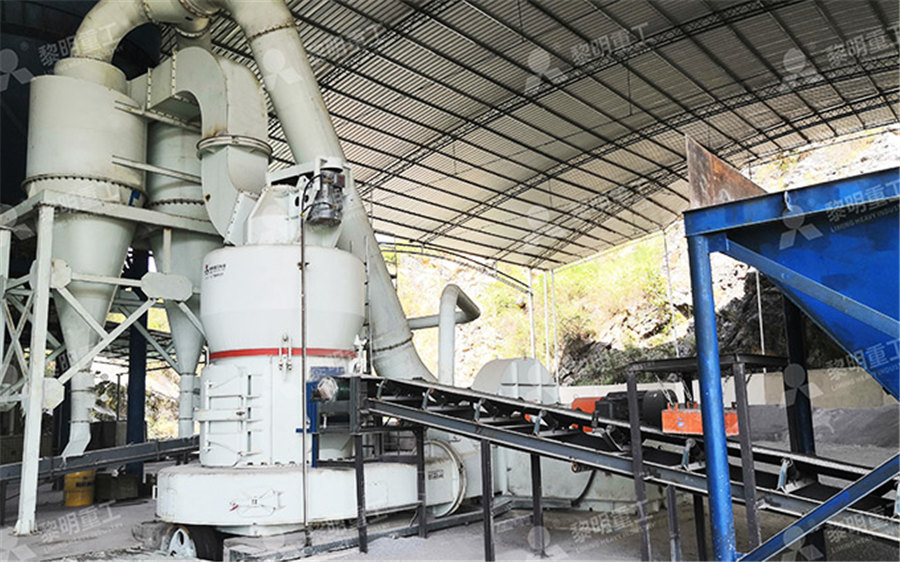
Ball Mill for Cement Grinding Process
Cement Ball Mill Structure When Ball Mill is working, raw material enters the mill cylinder through the hollow shaft of the feed The inside of the cylinder is filled with grinding media of various diameters (steel balls, steel segments, etc); when the cylinder rotates around the horizontal axis at a certain speed, Under the action of centrifugal force and friction force, the medium and the 2012年6月1日 is lined with mill liners protecting the steel body of the mill and incorporating mill lifters which help to raise the content of the mill to greater heights before it drops and cascades down [36]Grinding in Ball Mills: Modeling and Process Control2015年6月19日 While the mill is stopped, the charge volume can be gotten by measuring the diameter inside the liners and the distance from the top of the charge to the top of the mill The % loading or change volume can then be read off the graph below or approximated from the equation and calculation: % Steel Charge Loading in Mill = 113 – 126 H/ D Ball Mill Steel Charge Volume Calculation 911Metallurgist2024年2月27日 Due to the broken material, the steel ball needs good wear resistance and enough toughness, usually with alloy steel, high manganese steel, cast iron and chromium iron and other materials with forging or casting method molding, with the corresponding heat treatment process is more economical, ball mill steel ball according to the process and material can be How To Choose Steel Balls For Ball Mill? Grinding Balls Cement
.jpg)
Cement Mill Optimization: Practical Strategies for Enhanced
Adjusting mill parameters: Finetuning mill parameters such as mill speed, ball charge, filling ratio, and grinding media size can have a substantial impact on the grinding efficiency of the mill For example, a 10% increase in mill speed can result in up to 10% higher production rate, while optimizing the ball charge can lead to a 510% reduction in energy consumptionBALL MILL OPERATION Ball mills for finish grinding cement usually consist of two compartments An intermediate diaphragm separates both compartments from each other The 1 compartment is filled with coarser balls and lifting liners and is supposed to pre Process Training Ball Mill INFINITY FOR CEMENT EQUIPMENTThe choice between a vertical roller mill and a ball mill for cement grinding ultimately depends on the specific needs and constraints of the cement plant VRMs offer significant energy savings, finer product control, and reduced maintenance costs, making them an attractive option for modern cement plants focused on efficiency and sustainabilityVertical roller mill vs ball mill for cement grinding: Comparison 2023年2月15日 Example of steel grinding ball proportioning A beneficiation plant in Singapore loads balls into a ϕ 1500mm×3000mm wet grid type ball mill, determines the filling rate ϕ = 50%, and selects cast steel grinding balls δ = Method of Steel Grinding Ball Proportioning and
.jpg)
Ball Mill Critical Speed 911Metallurgist
2015年6月20日 A Ball Mill Critical Speed (actually ball, rod, AG or SAG) is the speed at which the centrifugal forces equal gravitational forces at the mill shell’s inside surface and no balls will fall from its position onto the shell The imagery below helps explain what goes on inside a mill as speed varies Use our online formula The mill speed is typically defined as the percent of the Ball Mill Performance Efficiency: S Description: Symbol: Formula: Example: No 1: Arm of gravity: a: 0666 * ( 1 – 4 * R 2) 15: h: 0583 – TAN1 [ 05 / R * (1 – 4*R 2) 05] – [ 2*R * (1 – 4*R 2) 05]: Deff: 418: h: Centre Distance (from mill Ball Mill Performance Efficiency Formulas2024年1月26日 Approximately 65–75 % of the total power consumption is used in grinding process Generally, ball mills are utilized for grinding the raw material into finished product (cement) in grinding unit of cement plants As the cement manufacturing is the continuous process, it is necessary to properly maintain the ball mill for the efficient putation of charging media for a double compartment cement ball mill All Ball mill or tube mill calculation, Critical speed, Ball Size calculations, Separator efficiency, Mill power cnsumption calculation, production at blain Optimization; Online Training; Process and Energy Audit; Online Calculations; Knowledge Base; Contact Us; Grinding Calculations Critical Speed (nc) Mill Speed (n) Degree of Filling (%DF Ball mill calculations, tube mill calculations, separator efficiency
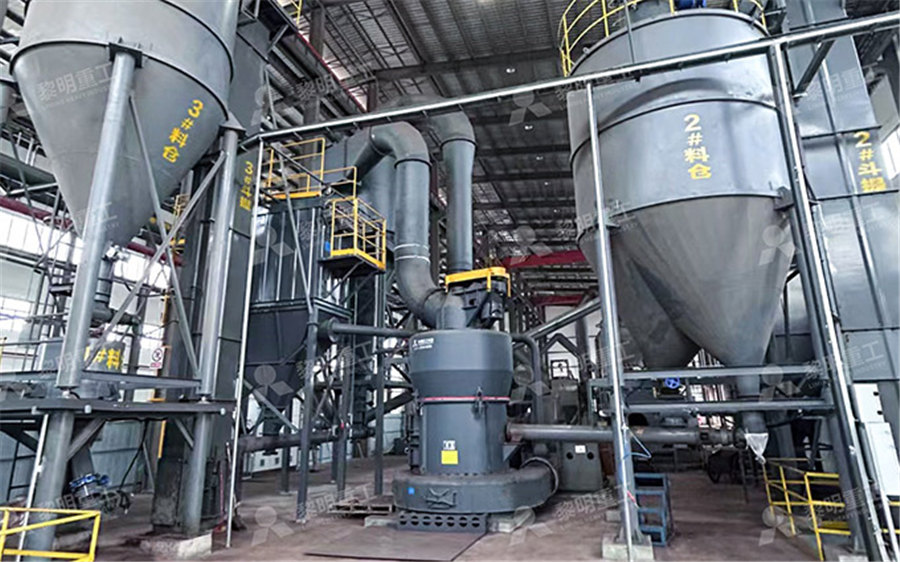
Ball Mill Grinding Process Handbook
Ball Mill Grinding Process Handbook Free download as PDF File (pdf), Text File (txt) or read online for free This document provides guidance on ball mill grinding processes It covers topics such as ball mill design including length to diameter ratios, percent loading, critical speed, and internals evaluation Methods for assessing ball charge, wear rates, and liner management are 2016年1月1日 One of the most popular milling machines is the cement mill, which is used to crush raw materials such as lime, silicate, alumina and iron oxide using grinding balls [3]A comparison of wear rates of ball mill grinding mediaFor the ball mill efficient operation, it is necessary to constantly maintain the required loading level by the grinding media It is very important to correctly and accurately measure the grinding media quantity in the mill Measurements provided in the workedout mill (without crushed material) by measuring the following parameters (measurements provided at three points – mill power Calculation of the filling degree the ball mill with grinding media2016年10月5日 1 Introduction Cement is an energyintensive industry in which the grinding circuits use more than 60 % of the total electrical energy consumed and account for most of the manufacturing cost []The requirements for the cement industry in the future are to reduce the use of energy in grinding and the emission of CO 2 from the kilns In recent years, the production EnergyEfficient Technologies in Cement Grinding IntechOpen
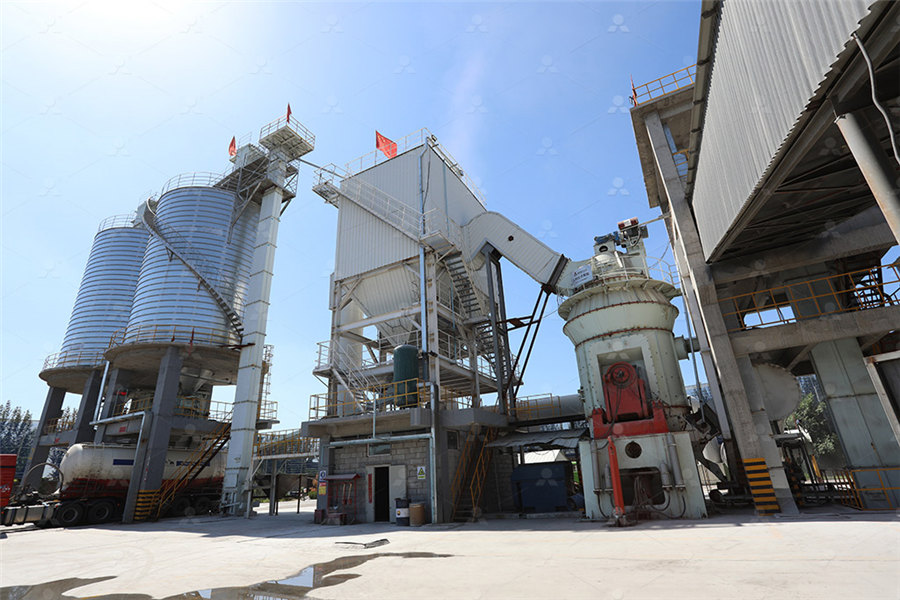
Cement Separator Ball Mill Optimization
Find: required maximum ball size – F80 – Maximum ball size (mm) Mill performance test Steps 1 Recording of related operational data 2 Air flow measurement 3 Crash stop and visual inspection in mill 4 Sampling in mill 5 An inefficient ball mill is a major expense and could even cost you product quality The best ball mills enable you to achieve the desired fineness quickly and efficiently, with minimum energy expenditure and low maintenance With more Ball mill for cement grindingVertical roller mills and ball mills represent two clearly distinct technologies However, with proper adjustments to the operational parameters of the vertical roller mill almost identical cement properties can be achieved by the two mills Cement grinding Vertical roller mills VS ball millsPrevious Post Next Post Contents1 Ball charge optimization2 1 How to use the BP21 2 Description of the main indicators used in this BP2101 The residue on 2mm/4mm before partition wall2102 Material filling level and ball charge expansion211 Cement mill specific power 1st compartment 212 Raw mill specific power 1st compartment Ball charge Ball charge optimization INFINITY FOR CEMENT EQUIPMENT
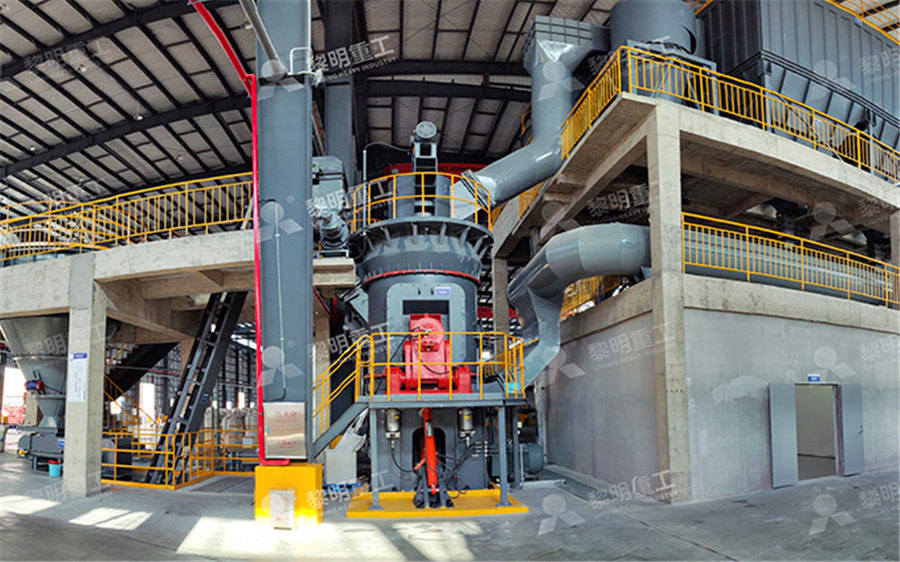
Choose the Best Grinding Steel Balls for Your Ball Mill Fote
Grinding Steel Ball Applicable Materials: Cement, silicate, newtype building material, refractory material, ferrous metal and nonferrous metal, glass ceramics, etc Under normal circumstances, it is not necessary to add small steel grinding balls When the ball mill is operating normally, friction will occur between the ball and ball, Mill performance is based on mill diameter and length only increases or decreases capacity The Slice Mill is simply a mill of the same diameter as the production mill but much shorter A Slice Mill of 72” diameter by 12” wide would replicate the result of Variables in Ball Mill Operation Paul O Abbe2024年1月5日 Ball mills are tube mills used for grinding materials like cement and involve several components The document discusses the movement of grinding media in ball mills, optimal ball charge and filling levels, key components like linings, diaphragms, drives and bearings, and factors that influence mill operation such as ventilation, water injection and Cement ball mill process calculation pdf PPT SlideShareThe installation of liners Length Diameter Ratio The lengthdiameter ratio of the cement ball mill is relatively large For mills of opencircuit grinding system, the lengthdiameter ratio is usually between 35 and 6 to ensure that the product fineness is qualified through single grinding; For ball mills in closedcircuit grind system, in order to increase the material flow rate, the length Cement Ball Mill Cost Effective Cement Grinding Mill from