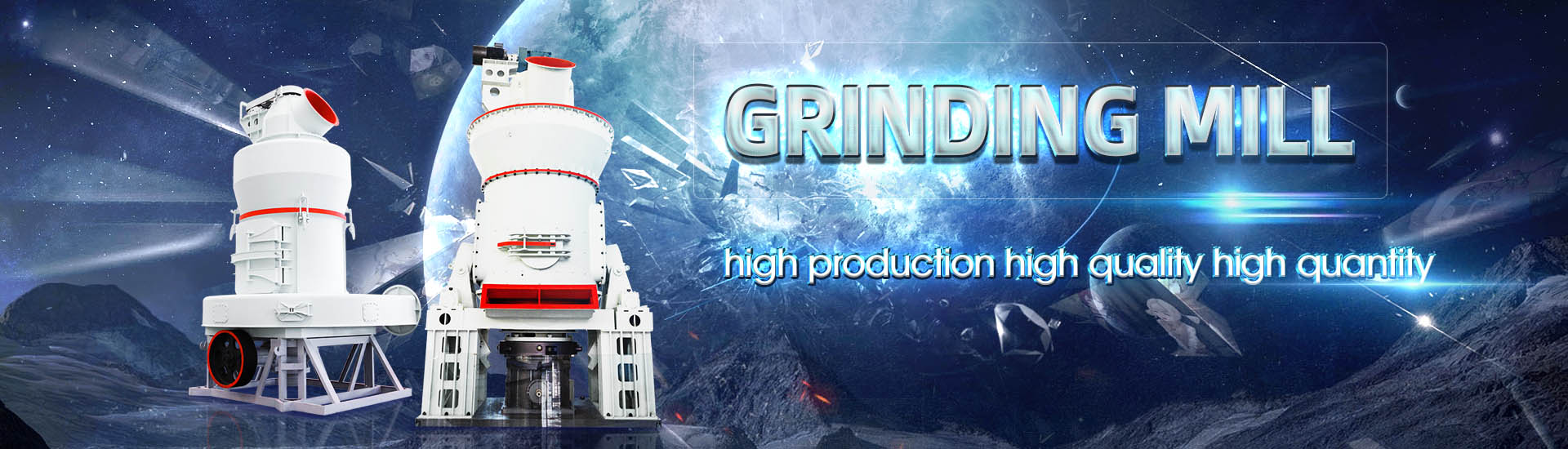
How much can the small discharge port of the 1200x250 ore grinding mill be adjusted
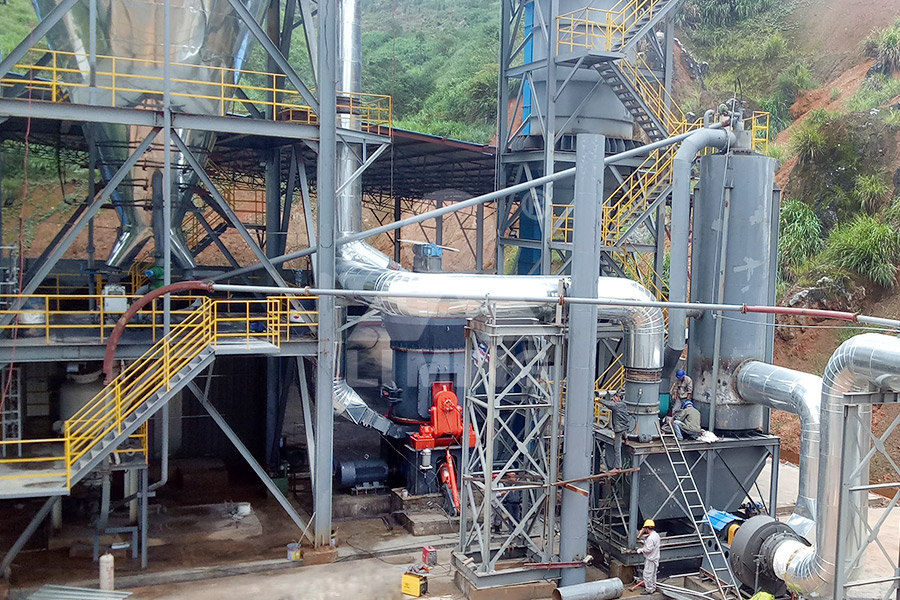
AMIT 135: Lesson 7 Ball Mills Circuits
Size rated as diameter x length Feed System 1 One hopper feed 2 Diameter 40 – 100 cm at 30 ° to 60 ° 3 Top of feed hopper at least 15 meter 展开2015年10月15日 Learn how to calculate the grinding capacity of your ball mill with 911 Metallurgist This guide provides essential formulas, insights, and tips to optimize your milling process and enhance production efficiencyCalculate Ball Mill Grinding Capacity 911Metallurgist2024年11月1日 Inadequate discharge capacity and difficult discharging of small ores can impede and negatively impact the grinding operation of the SAG mill, diminish the crushing Study on the influence of the discharge end cover structure of In ball mills, energy savings vary from 10 per cent to 40 per cent compared to 25 mm media A regrind ball mill with a mix of small grinding media can be as energy effi cient as an Isa Mill ENERGY SAVINGS AND TECHNOLOGY COMPARISON USING
.jpg)
Converting a ball mill from overflow to grate discharge
2020年6月23日 One way of fully utilising the capacity of a ball mill is to convert it from an overflow to a grate discharge This can allow an operation to increase plant throughput or reduce the product size, which can each contribute to 2022年3月30日 HPGR circuits can reduce the hard rock mining industry’s CO 2 emissions by up to 435% compared to SAG/Ball mill circuits Analysis of published data has confirmed that Helping to reduce mining industry carbon emissions: A stepby Grate discharge is not available in Rod Mills Advantages of Stirred Mills (VERTIMILL ®): The main costs for grinding are energy, liners and grinding media They are different for different AMIT 135: Lesson 6 Grinding Circuit – Mining Mill Operator TrainingAccording to the ways by which motion is imparted to the charge, grinding mills are generally classified into two types: tumbling mills and stirred mills In tumbling mills, the mill shell is Grinding Mill an overview ScienceDirect Topics
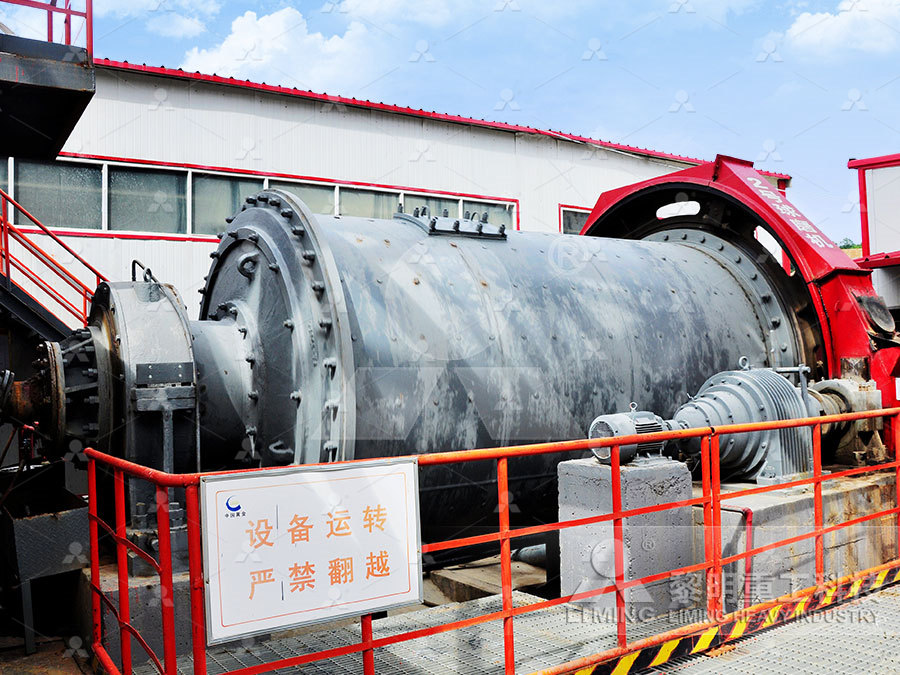
Ore Grinding SpringerLink
2023年7月20日 Moist grinding, a special grinding method, is used to prepare pellets for smelting According to the grinding medium features, ore grinding is mainly classified into ball grinding 2023年10月27日 The ball mill is a rotating cylindrical vessel with grinding media inside, which is responsible for breaking the ore particles Grinding media play an important role in the comminution of mineral ores in these mills This work reviews the application of balls in mineral processing as a function of the materials used to manufacture them and the mass loss, as A Review of the Grinding Media in Ball Mills for Mineral 2023年7月20日 Therefore, the rod mill is mostly used for coarse grinding of the previous period of ball mill, or grinding of brittle materials and materials against overcrushing, such as tungsten and tin ore before gravity separation; and (3) autogenous mill – it refers to the materials which themselves are collided and ground mutually to be crushed when the grinding mill rotates, and Ore Grinding SpringerLink2017年10月26日 The following are factors that have been investigated and applied in conventional ball milling in order to maximize grinding efficiency: a) Mill Geometry and Speed – Bond (1954) observed grinding efficiency to be a Factors Affecting Ball Mill Grinding Efficiency
.jpg)
(PDF) A comprehensive review on the grinding process:
June 2022; ARCHIVE Proceedings of the Institution of Mechanical Engineers Part C Journal of Mechanical Engineering Science 19891996 (vols 203210) 236(2):年5月8日 and ∅11(V) is read from Fig 312 for a trunnion overflow mill or is taken as unity for a batch mill or grate discharge mill The equation (311) has been applied to the computation of the power requirements of large industrial mills, based on the published data given by Taggart, and the results of these calculations are shown in Fig 313Grinding Mill Power 911Metallurgist2014年12月1日 Cleary et al (2010) presented full three dimensional modelling of media flow in a HICOM mill and demonstrated the development of a suitable wear model able to predict the liner life cycleEffect of port configuration on discharge from a HICOM® mill2015年8月6日 What water does is kind of provide a mode of transportation for the ore How Water Impacts Grinding The % solids by volume of the rod mill discharge Rod mill grinding efficiencies have been shown to increase in the range of 5 Ball Rod Mill Density – How Water Impacts Grinding
.jpg)
Simulation of overflow ball mill discharge and trommel flow using
2015年9月1日 The slurry discharge is a much stronger flow than that of the balls and exits the mill with peak speeds of up to 15 m/s As shown in Figure 8, sl urry quic kly flows o ff of the ends of the 2017年1月17日 Other process activities, such as spraying the ore with water for dust control or the fact that runofmine ore moisture is approximately 2%5% are not generally considered (Bleiwas, 2012a)Breaking down energy consumption in industrial grinding mills2017年8月5日 The installed power in the primary mill is generally much greater than in conventional circuits Since the semiautogenous or autogenous mill is dependent at least in part, if not entirely, on the ore to grind itself, a small change in ore grinding characteristics can produce a relatively large change in the grinding capacity of the millHow to Control a SAG Grinding Mill Circuit 911Metallurgist2012年6月1日 As the cylinder starts to rotate, the grinding balls inside the cylinder crush and grind the feed material, generating mechanical energy that aids in breaking bonds, activating the catalyst, and Grinding in Ball Mills: Modeling and Process Control
.jpg)
Understanding the SAG Mill in Copper Ore Mining
The Autogenous Mill, also known as AG Mill, is a type of grinding mill used in the mining industry This machine uses ore and rock itself as grinding media to perform its job Unlike other types of mills that use steel balls or rods for Ball Mill Introduction There are three main stages to mineral processing in the mining industryThese are: Comminution (crushing and grinding); Beneficiation (separation and concentration); Smelting and refining; Ball mills are Ball Mill (Ball Mills Explained) saVRee saVRee2015年7月29日 As you increase the volume of the through put, the time that the ore has to react to the grinding media is lessened As you add ore to the mill you are also adding WATER and changing density which affects the slurry rheology and workings of the grinding action inside that mill This water is one of the main controls that you have over your grindEffect of Water Density on Grinding Mill 911Metallurgist2024年4月26日 These mills utilize the ore itself as the grinding media, reducing the need for additional grinding media AG/SAG mills are typically used for coarse grinding, where large pieces of ore are efficiently broken down The grinding process reduces the ore size, which enhances the efficiency of subsequent beneficiation processes by increasing the Iron Ore Processing: From Extraction to Manufacturing
.jpg)
Ball Mill Grinding Machines: Working Principle, Types, Parts
Advantages of Ball Mill Ball mill grinding machine offer several advantages, including: Versatility: Ball mills can perform various types of grinding, such as dry grinding ball mill or wet grid ball mill, batch or continuous grinding, and fine or ultrafine grinding, making them 2015年6月25日 The above tables list some of the most common Grate Discharge Ball Mill sizes Capacities are based on medium hard ore with mill operating in closed circuit under wet grinding conditions at speeds indicated For dry grinding, speeds are reduced and capacities drop between 30% to 50% Grate Discharge Ball Mill Arrangement DimensionsOverflow VS Grate Discharge Ball or Mill – Why Retrofit2020年7月2日 The ball mill is the key equipment for grinding the minerals after the ore is crushed With the continuous development of the industrial level, the development of ball mills is also moving towards (PDF) Effects of Ball Size Distribution and Mill Speed and Their 1 Ensure material is properly dispersed before adding to the mill This will help to prevent agglomeration and clogging of the discharge screen 2 Don't choke the mill by starting with solids content that's higher than the mill can process A rule of thumb is to start with 50% solids and adjust as neededSolids Choose the Right Grinding Mill Chemical Processing
.jpg)
The Ultimate Guide to Ball Mills Miningpedia
2019年8月14日 When grinding materials with small feed particles, such as sand no 2 slag and coarse fly ash, the cylinder of the mill can be separated into a single silo grinding,and the grinding body can also be steel section • Peripheral ball mill: Grinding Mills Barry A Wills, James A Finch FRSC, FCIM, PEng, in Wills' Mineral Processing Technology (Eighth Edition), 2016 71 Introduction Grinding is the last stage in the comminution process where particles are reduced in size by a combination of impact and abrasion, either dry, or more commonly, in suspension in waterGrinding Mill an overview ScienceDirect Topics3,000 tons of iron ore from a vessel in 24 hours, given ideal conditions But frozen ore in the holds could add days to the process Engineers used small steam donkey engines to hoist ore out of the holds in tubs, which were then emptied into wheelbarrows on the docks In 1880,The Hulett Ore Unloader Port Authority2016年3月21日 F = tonnage of ore to mill; 0 = tonnage of ore in overflow; S = tonnage of sand; M = tonnage of ore in mill discharge; and Ds, Do, and Dm are the liquidtosolid ratios of the sand, overflow, and classifier feed at the points Common Basic Formulas for Mineral Processing
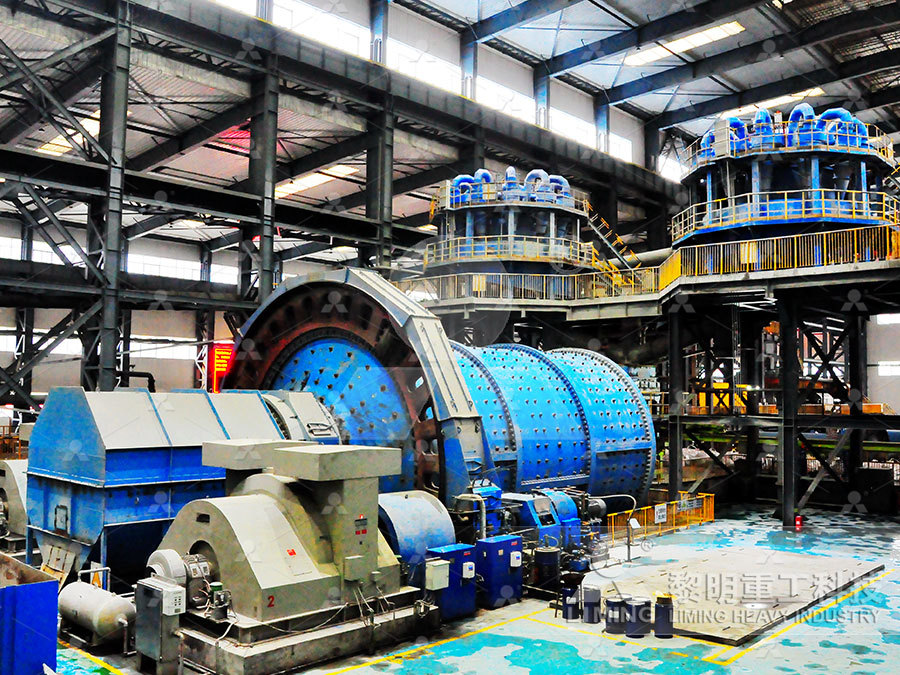
Grinding Mills Common Types 911Metallurgist
2016年11月7日 In Fig 13 is shown a large ball mill, designed for the dry grinding of limestone, dolomite, quartz, refractory and similar materials; this type of mill being made in a series of sizes having diameters ranging from about 26 in to 108 in, with the corresponding lengths of drum ranging from about 15 in to 55 in2019年1月22日 With OD grinding, there are limits on how small a part can be and still be ground this method That is because on parts of 0250” (635 mm) or smaller, it is extremely hard to find the true center In fact, it is the difficulty of finding the center on very small parts that led to the development of centerless grindingFundamentals of OD Grinding Metal Cutting CorporationMill Type Overview Three types of mill design are common The Overflow Discharge mill is best suited for fine grinding to 75 – 106 microns; The Diaphram or Grate Discharge mill keeps coarse particles within the mill for additional grinding and typically used for grinds to 150 – 250 microns; The CenterPeriphery Discharge mill has feed reporting from both ends and the product AMIT 135: Lesson 7 Ball Mills Circuits – Mining Mill Operator 2023年5月3日 Center Periphery Discharging Rod Mill The center periphery discharging rod mill feeds the material through the journals at both ends of the mill, and discharges the grinding products through the circular orifice in the middle of the cylinder (Fig 3)Ore pulp is characterized by short stroke, steep slope, and it can be coarsely ground with fewer fine particles and low Rod Mill SpringerLink

Peripheral Discharge Ball Mills Theory and Practice
2016年3月14日 It is useless to expect a large capacity from a mill operated with balls of a size too small to crush the ore, or when the balls are of a composition that will not withstand the shock of impact and shatter themselves to fragments Hard ores, when fed direct from a crusher, require a proper percentage of 5in steel balls to do effective work2016年6月3日 The absence of impact limits practical feed size to 5mm Because there is greater pressure between media and less production of heat and sound, the device consumes less energy than a tumbling mill to perform the same work The normal top size of balls in a Tower Mill is 25mm For ultrafine grinding, much smaller media can be utilizedTower Mill Operating Work Index 911Metallurgist2023年10月27日 The ball mill is a rotating cylindrical vessel with grinding media inside, which is responsible for breaking the ore particles Grinding media play an important role in the comminution of mineral ores in these mills This work reviews the application of balls in mineral processing as a function of the materials used to manufacture them and the mass loss, as A Review of the Grinding Media in Ball Mills for Mineral 2023年7月20日 Therefore, the rod mill is mostly used for coarse grinding of the previous period of ball mill, or grinding of brittle materials and materials against overcrushing, such as tungsten and tin ore before gravity separation; and (3) autogenous mill – it refers to the materials which themselves are collided and ground mutually to be crushed when the grinding mill rotates, and Ore Grinding SpringerLink
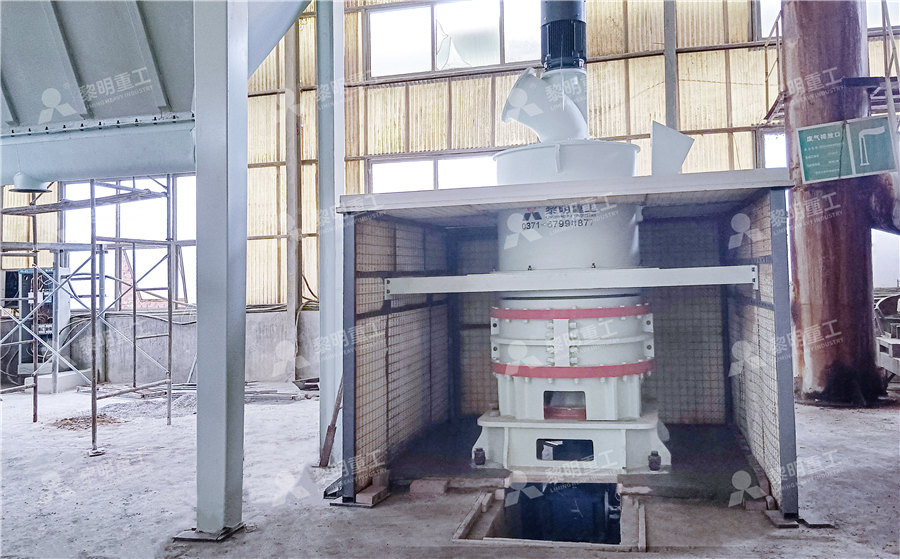
Factors Affecting Ball Mill Grinding Efficiency
2017年10月26日 The following are factors that have been investigated and applied in conventional ball milling in order to maximize grinding efficiency: a) Mill Geometry and Speed – Bond (1954) observed grinding efficiency to be a June 2022; ARCHIVE Proceedings of the Institution of Mechanical Engineers Part C Journal of Mechanical Engineering Science 19891996 (vols 203210) 236(2):1107(PDF) A comprehensive review on the grinding process: 2017年5月8日 and ∅11(V) is read from Fig 312 for a trunnion overflow mill or is taken as unity for a batch mill or grate discharge mill The equation (311) has been applied to the computation of the power requirements of large industrial mills, based on the published data given by Taggart, and the results of these calculations are shown in Fig 313Grinding Mill Power 911Metallurgist2014年12月1日 Cleary et al (2010) presented full three dimensional modelling of media flow in a HICOM mill and demonstrated the development of a suitable wear model able to predict the liner life cycleEffect of port configuration on discharge from a HICOM® mill

Ball Rod Mill Density – How Water Impacts Grinding
2015年8月6日 What water does is kind of provide a mode of transportation for the ore How Water Impacts Grinding The % solids by volume of the rod mill discharge Rod mill grinding efficiencies have been shown to increase in the range of 5 2015年9月1日 The slurry discharge is a much stronger flow than that of the balls and exits the mill with peak speeds of up to 15 m/s As shown in Figure 8, sl urry quic kly flows o ff of the ends of the Simulation of overflow ball mill discharge and trommel flow using 2017年1月17日 Other process activities, such as spraying the ore with water for dust control or the fact that runofmine ore moisture is approximately 2%5% are not generally considered (Bleiwas, 2012a)Breaking down energy consumption in industrial grinding mills2017年8月5日 The installed power in the primary mill is generally much greater than in conventional circuits Since the semiautogenous or autogenous mill is dependent at least in part, if not entirely, on the ore to grind itself, a small change in ore grinding characteristics can produce a relatively large change in the grinding capacity of the millHow to Control a SAG Grinding Mill Circuit 911Metallurgist