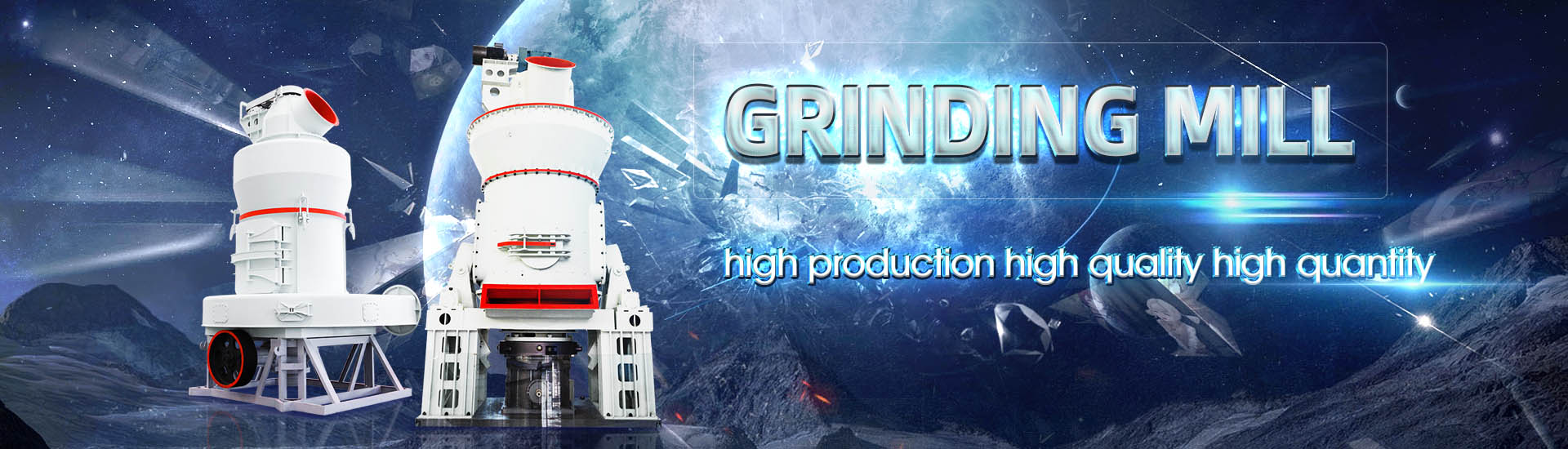
Operation of cement vertical mill
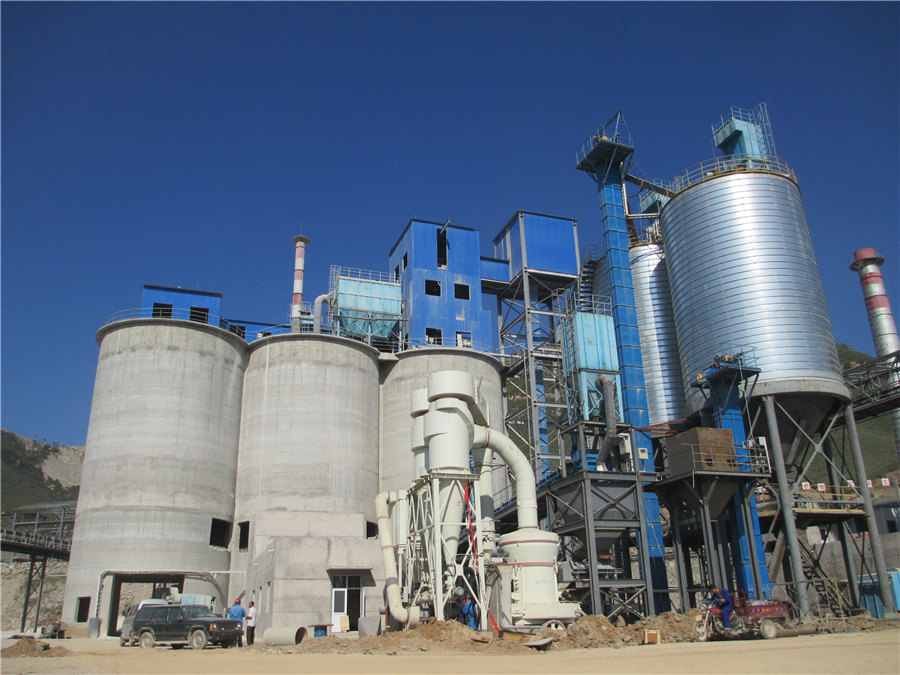
Operational parameters affecting the vertical roller mill
2017年4月1日 Vertical roller mills (VRM) have found applications mostly in cement grinding operations where they were used in raw meal and finish grinding stages and in power plants 2017年9月11日 In this study, an extensive sampling study was carried out at vertical roller mill of ESCH Cement Plant in Luxemburg Samples were collected from mill inside and around the circuit to(PDF) Performance Evaluation of Vertical Roller Mill in 2021年1月1日 For the past three decades the vertical roller mill has emerged to be the preferred choice for grinding raw materials With the grinding capacity of a vertical roller mill and the Review on vertical roller mill in cement industry its performance Vertical roller mills are adopted in 20 cement plants (44 mills) in Japan In the vertical roller mill which is widely used in the raw material grinding process, raw materials input grinding table Vertical roller mill for raw Application p rocess materials
.jpg)
VERTICAL ROLLER MILLS A holistic VRM approach
The quadropol® vertical roller mill by thyssenkrupp Industrial Solutions takes a holistic approach to modern grinding systems in terms of its simple and compatible design Describing the key Roller Mill (VRM) reduces the power consumption for cement grinding approximately 3040% associated with other grinding mills The process variables in cement grinding process using PROCESS CONTROL FOR CEMENT GRINDING IN VERTICAL Vertical roller mills are widely used for especially grinding of coal, cement raw materials, clinker and minerals like bauxite, phosphate, magnesite, etc These machines consist of grindingPerformance Evaluation of Vertical Roller Mill in Cement Grinding: Vertical roller mill is a type of grinder used to grind materials into extremely fine powder for use in mineral dressing processes, paints, pyrotechnics, cements and ceramics It is an energy Vertical roller mill Wikipedia
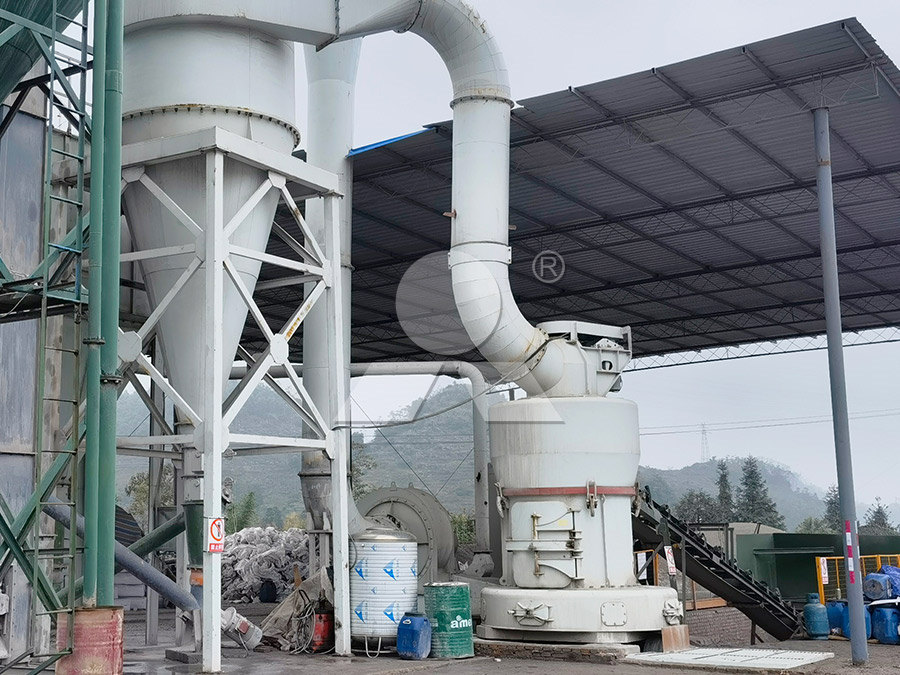
The Cement Plant Operations Handbook International Cement
The Cement Plant Operations Handbook is a concise, practical guide to cement manufacturing and is the standard reference used by plant operations personnel worldwide Providing a 2024年1月23日 vertical cement mill; Cement Manufacturing Plant; Mineral Processing Plant; Cement Grinding Plants; Clinker Grinding Unit; January 23, 2024; The efficient operation of a cement mill is vital for the overall productivity and quality of the cement production processHow To Optimize The Operation Of The Cement Mill2023年12月4日 A vertical roller mill (VRM) is a grinding equipment used for the size reduction of minerals, cement, and ceramics The capacity of the VRM depends not only on the grinding material properties but also on the operational parameters of the VRM This study investigatedNumerical Investigation of Vertical Roller Mill Operation Using In conclusion, the application of vertical roller mill technology in the cement industry has revolutionized the way cement is produced VRMs are more energyefficient, ecofriendly, and produce a more consistent product compared to Application of Vertical Roller Mill in Cement Production
.jpg)
Vertical Mill In Cement Plant Cement Vertical Mill AGICO Cement
Vertical mill merges fine crushing, drying, grinding and powder selecting into a single, which simplifies the production process It has the advantages of high grinding efficiency, low power consumption, large feed particle size, easy adjustment of grinding fineness, simple process, less land occupation, low noise, simple operation and maintenance, low cost and less wear Download scientific diagram Operation of vertical roller mill circuit from publication: An approach to measuring and modelling the residence time distribution of cement clinker in vertical Operation of vertical roller mill circuit ResearchGatevertical roller grinding mills for grinding: • Coal • Cement raw material • Clinker / granulated slag • Industrial minerals, and • Ores The core elements of these plants are the Loesche vertical mills for drygrinding the abovementioned grinding stock Loesche has PROCESS OPTIMISATION FOR LOESCHE GRINDING PLANTS2013年5月15日 Under normal operation by the vertical roller mill feed roller bed thickness after compaction should not be less than 40 ~ 50ram 53 12 Control of grinding pressure: The pressure is affecting the grinding mill output Thank you for your kind attention KPPradeep Kumar Sr GMOperation Karikkali works Chettinad cements LtdVertical raw mill pradeep kumar PPT Free Download SlideShare

Raw mill Cement Plant
After technology modification, the vertical cement mill has obvious advantages compared with the cement ball mill, and it is suitable for the large cement production line Low operation cost: small energy consumption and less damage reduce the running cost Environment protection and clean: small vibration, low noise, Table 1: QMR² performance values of quadropol cement mills during operation, Cementos Progreso, Guatemala Design parameter Nominal Operation QMR2 No 1 (average) Operation QMR2 No 2 (average) downtime of the quadropol® vertical roller mill’ in: Cement International, 17(6), p3639 3 POLYSIUS (2008): ‘Polysius commissions aVERTICAL ROLLER MILLS A holistic VRM approachVertical roller mill manufacturers Vertical roller mill or VRM is a largescale grinding equipment designed for pulverizing cement raw meal, cement clinker, slag, coal, fly ash, limestone, and other hard grinding materialIt integrates grinding, drying, separation, and conveying in one machine The equipment is widely used in many industries such as cement, electric power, metallurgy VRM In Cement Plant Maximize Energy Saving CNBMSINOMAGlobally, cement plants are striving to improve their energy efficiency Therefore, it is critical for cement plant operations to increase the monitoring and control of a vertical raw mill energy process This technology has attracted the interest of the cement industry with its proven benefitAssessment of the thermodynamics efficiency of a cement vertical
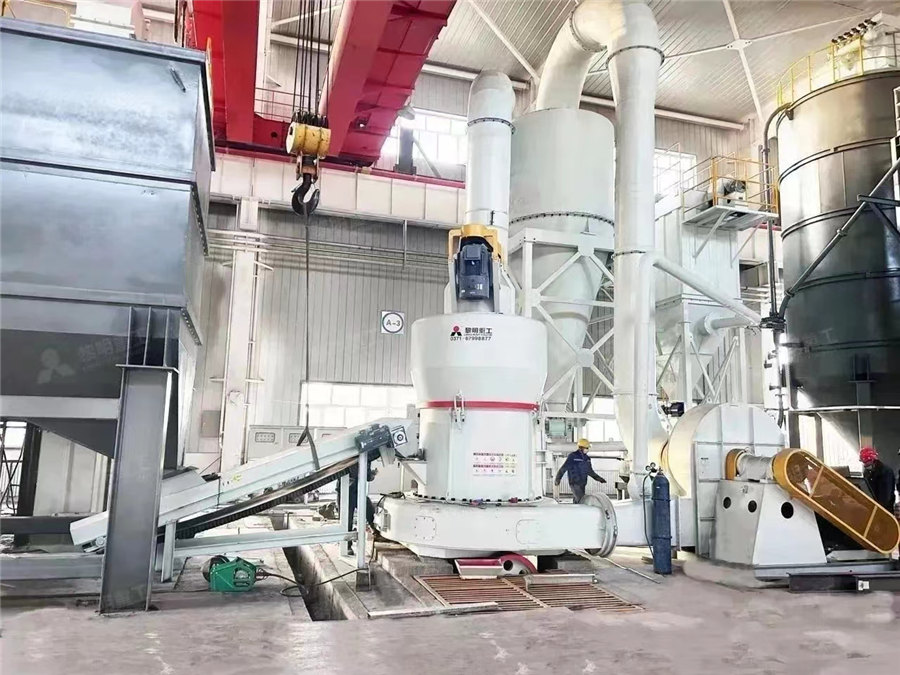
Vertical Cement Mill Magotteaux
At Magotteaux, we have a gamechanger that is likely to impact on vertical cement mill operations for decades In order to make the operation of mills more efficient, more sustainable and less costly, our own design team has come up with an entirely The choice between a vertical roller mill and a ball mill for cement grinding ultimately depends on the specific needs and constraints of the cement plant VRMs offer significant energy savings, finer product control, and reduced maintenance costs, making them an attractive option for modern cement plants focused on efficiency and sustainabilityVertical roller mill vs ball mill for cement grinding: Comparison 2022年1月23日 This work concentrates on the energy consumption and grinding energy efficiency of a laboratory vertical roller mill (VRM) under various operating parameters For design of experiments (DOE), the response surface method (RSM) was employed with the VRM experiments to systematically investigate the influence of operating parameters on the energy Analysis and Optimization of Grinding Performance of Vertical 2021年1月29日 By initiating a CL for an industrial cement vertical roller mill (VRM), this study conducted a novel strategy to explore relationships between VRM monitored operational variables and their Increase productivity of vertical roller mill using seven QC tools
.jpg)
Expert PID Control of Grinding Condition for Cement Vertical Roller Mill
This paper proposed a controller design method based on expert PID to automatically control the load and quality of cement vertical mill This method is applied to a cement plant in Guangxi Province The operation results show that the designed controller can ensure the stability of the system to increase the cement output and reduce energy consumption Therefore, the What Is Cement Vertical Mill The cement vertical mill is a type of grinding equipment that merges fine crushing, drying, grinding, and powder separating into a single, which simplifies the production process and has many irreplaceable advantages, such as high grinding efficiency, large feeding size, low power consumption (2030% less power than a cement ball mill), large Cement Vertical Mill Vertical Grinding Mill Vertical MillVertical raw mill is one kind of raw mill, generally used to grind bulk, granular, and powder raw materials into required cement raw meal in the cement manufacturing plantVertical raw mill is an ideal grinding mill that crushing, drying, grinding, grading transfer set in one It can be widely used in cement, electric power, metallurgy, chemical industry, nonmetallic ore, and other industriesVertical raw mill Cement PlantImportant operation parameters in Vertical mill TO DOWNLOAD THE EXCEL SHEET AND ALL THE OTHER USEFUL BOOKS AND RESOURCES KINDLY CLICK HERE Feed rate to mill, production rate [t/h] Mill differential pressure [mbar] Grinding bed thickness with span [mm] Amount of external material recirculation [t/h, or BE current A] Gas flow through mill [act Important operation parameters in Vertical mill INFINITY FOR CEMENT
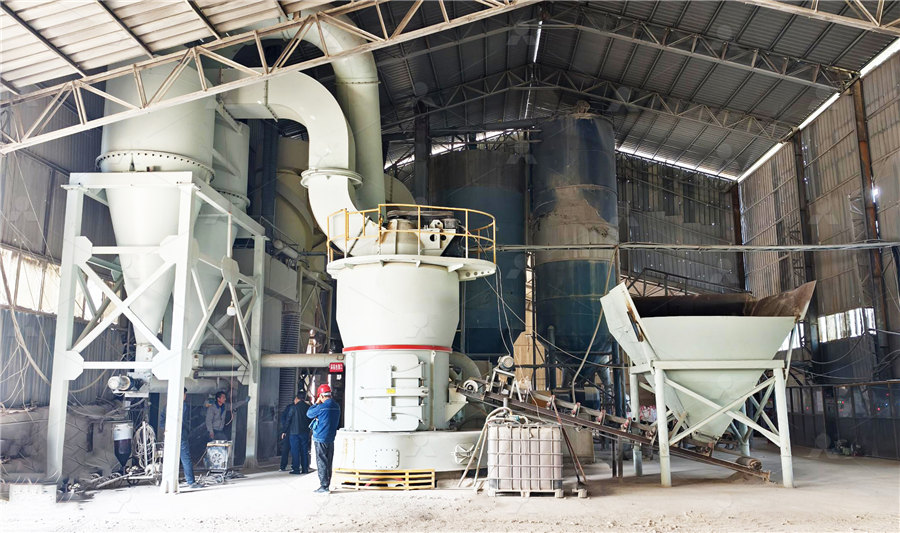
Performance Evaluation of Vertical Roller Mill in Cement
Keywords: Vertical roller mill, cement grinding, performance evaluation INTRODUCTION Broadly, the vertical mill operation is separated into three stages that are; feeding,A 10 MW cement mill, output 270 tonnes per hour A cement mill (or finish mill in North American usage [1]) is the equipment used to grind the hard, nodular clinker from the cement kiln into the fine grey powder that is cementMost cement is currently ground in ball mills and also vertical roller mills which are more effective than ball millsCement mill Wikipediafinish grinding of Portland cement, slag and blended cements The mill consistently uses five to ten percent less power than other cement vertical roller mills, and in comparison with traditional ball mill operations, the energy requirements for the OK cement mill is 3045 percent lower for cement grinding and 4050 percent lower for slag The OK™ CEMENT MILLFor raw materials and cement clinker, the vertical roller mill is an excellent grinding solution because of the relatively lower cost of installation, ease of operation and maintenance, energy efficiency and product quality Further, our Vertical roller mills FLSmidth Cement
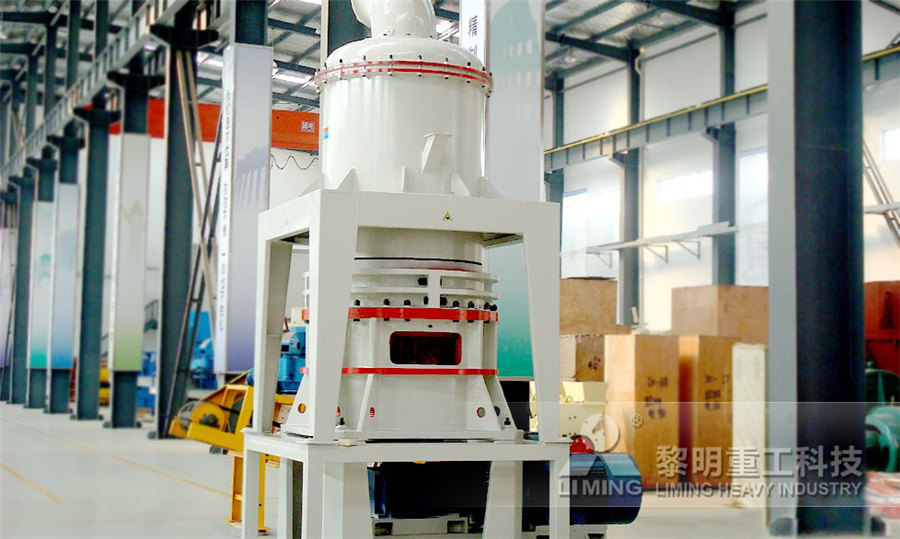
Ok Vertical Mill PDF Mill (Grinding) Cement
The OK vertical roller mill is a compact and energyefficient mill for grinding cement, slag, and blended cements It uses 3050% less energy than ball mill systems and allows for a more simplified plant layout The OK mill combines drying, grinding, and separation into a single unit It provides reliable operation with low noise and vibration The design allows for easy adjustment Improvement of cement performances through the use of grinding aids in vertical roller mill PD’Arcangelo, MMagistri – Mapei SpA, Milan, Italy Abstract Due to the stringent requirement of energy saving, the use of vertical roller mills for cement grinding is now common Even though the reliability and operation stability of modern VRM is veryImprovement of cement performances through the use of While the mill main drive accelerates the operator has to watch the development of the power consumption of the mill main drive and of the differential pressure of the mill When the usual values are reached the start command to the feed group is given During the first 5 to 15 minutes of operation the mill has to be stabilizedPROCESS TRAINING for operators of Vertical RAW MillsVERTICAL ROLLER MILL OPERATION PARAMETERS Advances in Civil Engineering Grinding aids (GAs) are polar chemicals introduced in cement mills in either liquid or powder form to improve on mill grindability efficiency(PDF) CEMENT RAW MATERIAL GRINDING ; VERTICAL ROLLER MILL OPERATION
.jpg)
VERTICAL ROLLER MILLS AMCL
the hot gas which is absorbed by operation of the mill fan Vertical Roller Mill 1 Rotary Lock 2 Separator 3 Chute 4 Roller 5 Swing Lever 6 Table 7 Flow Sheet of Raw Material Grinding Raw Mill Cement/ Slag Mill UM Series A B H UMseries Cement / Slag Mill Models with details of structural dimension, product throughputs and Table 3 Power Consumption Of Roller Press Grinding System Overall, we can conclude the three tables: After the longterm operation, although unit raw material grinding power consumption of the cement roller press grinding system is still low, the indexes of the vertical roller mill grinding system are very close to it, among which the output power of the vertical mill and the roller Comparison Of Vertical Roller Mill And Roller Press MillBy initiating a CL for an industrial cement vertical roller mill (VRM), this study conducted a novel strategy to explore relationships between VRM monitored operational variables and their Schematic operation principle of a verticalrollermill2024年1月23日 vertical cement mill; Cement Manufacturing Plant; Mineral Processing Plant; Cement Grinding Plants; Clinker Grinding Unit; January 23, 2024; The efficient operation of a cement mill is vital for the overall productivity and quality of the cement production processHow To Optimize The Operation Of The Cement Mill
.jpg)
Numerical Investigation of Vertical Roller Mill Operation Using
2023年12月4日 A vertical roller mill (VRM) is a grinding equipment used for the size reduction of minerals, cement, and ceramics The capacity of the VRM depends not only on the grinding material properties but also on the operational parameters of the VRM This study investigatedIn conclusion, the application of vertical roller mill technology in the cement industry has revolutionized the way cement is produced VRMs are more energyefficient, ecofriendly, and produce a more consistent product compared to Application of Vertical Roller Mill in Cement ProductionVertical mill merges fine crushing, drying, grinding and powder selecting into a single, which simplifies the production process It has the advantages of high grinding efficiency, low power consumption, large feed particle size, easy adjustment of grinding fineness, simple process, less land occupation, low noise, simple operation and maintenance, low cost and less wear Vertical Mill In Cement Plant Cement Vertical Mill AGICO CementDownload scientific diagram Operation of vertical roller mill circuit from publication: An approach to measuring and modelling the residence time distribution of cement clinker in vertical Operation of vertical roller mill circuit ResearchGate

PROCESS OPTIMISATION FOR LOESCHE GRINDING PLANTS
vertical roller grinding mills for grinding: • Coal • Cement raw material • Clinker / granulated slag • Industrial minerals, and • Ores The core elements of these plants are the Loesche vertical mills for drygrinding the abovementioned grinding stock Loesche has 2013年5月15日 Under normal operation by the vertical roller mill feed roller bed thickness after compaction should not be less than 40 ~ 50ram 53 12 Control of grinding pressure: The pressure is affecting the grinding mill output Thank you for your kind attention KPPradeep Kumar Sr GMOperation Karikkali works Chettinad cements LtdVertical raw mill pradeep kumar PPT Free Download SlideShareAfter technology modification, the vertical cement mill has obvious advantages compared with the cement ball mill, and it is suitable for the large cement production line Low operation cost: small energy consumption and less damage reduce the running cost Environment protection and clean: small vibration, low noise, Raw mill Cement PlantTable 1: QMR² performance values of quadropol cement mills during operation, Cementos Progreso, Guatemala Design parameter Nominal Operation QMR2 No 1 (average) Operation QMR2 No 2 (average) downtime of the quadropol® vertical roller mill’ in: Cement International, 17(6), p3639 3 POLYSIUS (2008): ‘Polysius commissions aVERTICAL ROLLER MILLS A holistic VRM approach
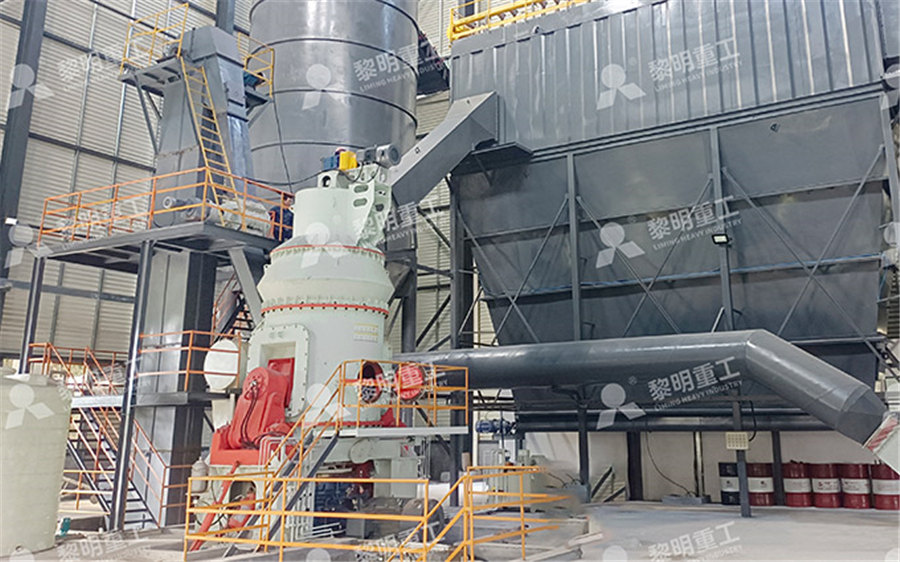
VRM In Cement Plant Maximize Energy Saving CNBMSINOMA
Vertical roller mill manufacturers Vertical roller mill or VRM is a largescale grinding equipment designed for pulverizing cement raw meal, cement clinker, slag, coal, fly ash, limestone, and other hard grinding materialIt integrates grinding, drying, separation, and conveying in one machine The equipment is widely used in many industries such as cement, electric power, metallurgy