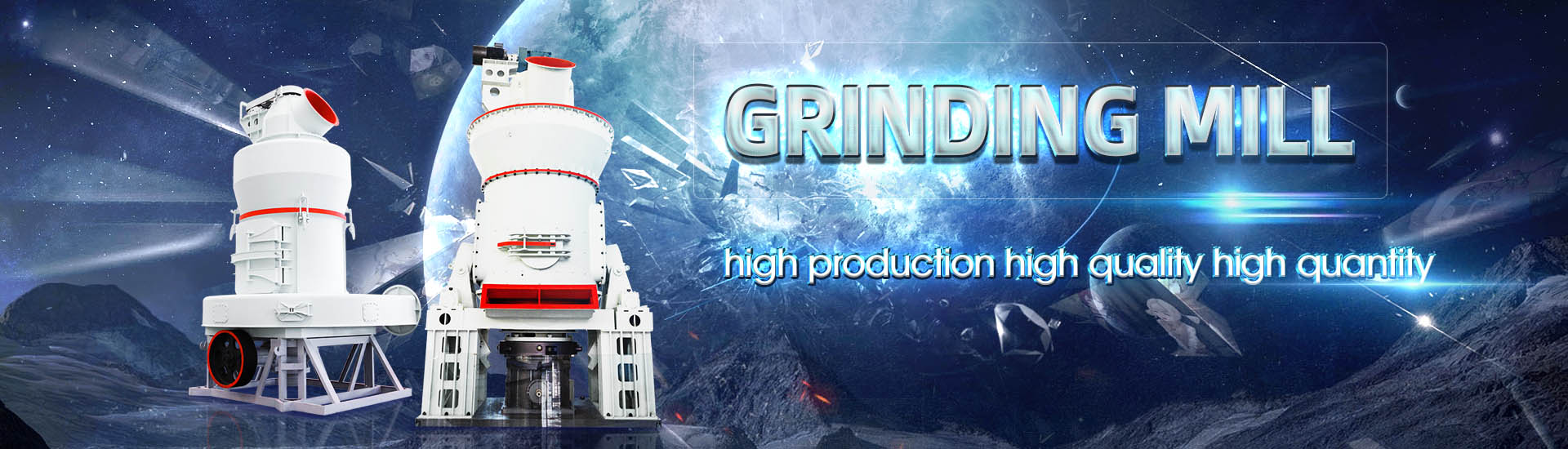
Cement grinding ball consumption
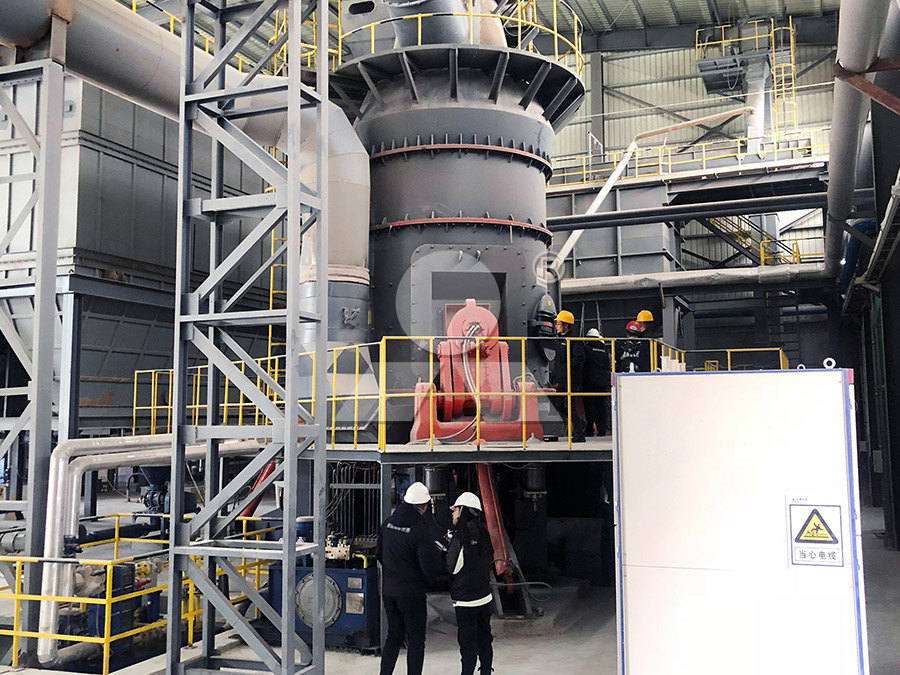
OPTIMIZATION OF CEMENT GRINDING OPERATION IN BALL MILLS
consumption and low production The consumption of energy by the cement grinding operation amounts to one third of the total electrical energy used for the production of cement The optimization of this process would yield substantial benefits in terms of energy savings and The consumption of energy by the cement grinding operation amounts to one third of the total electrical energy used for the production of cement The optimization of this process would yield substantial benefits in terms of energy Optimization of Cement Grinding Operation in Ball As grinding accounts for a sizeable share in a cement plant’s power consumption, optimisation of grinding equipment such as ball mills can provide significant cost and CO 2BALL MILLS Ball mill optimisation Holzinger ConsultingBall mills with high efficiency separators have been used for cement grinding in cement plants all these years Ball mill is a cylinder rotating at about 7080% of critical speed on two trunnions in Cement Grinding Cement Plant Optimization
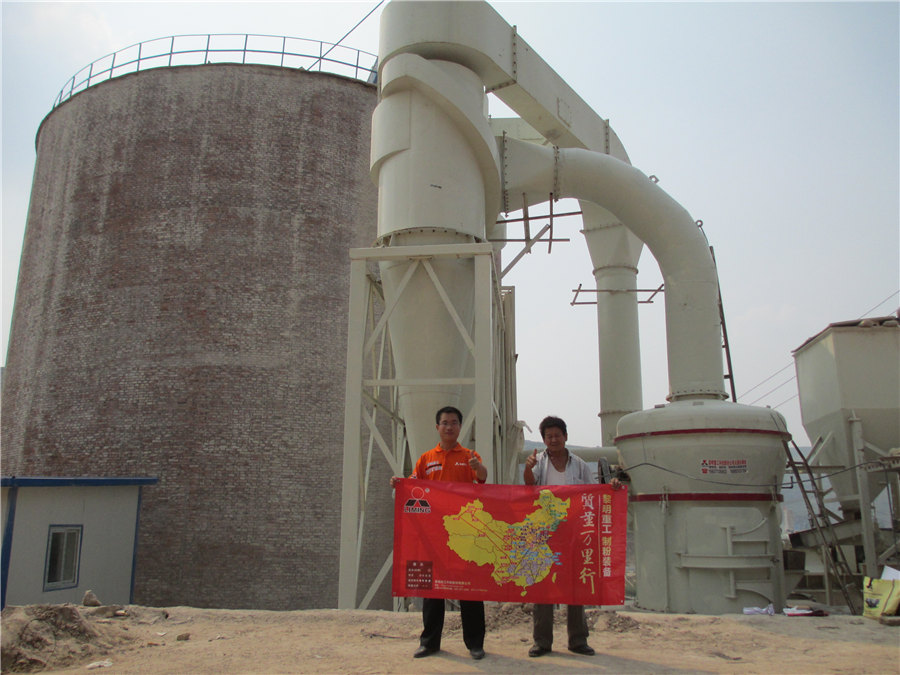
A critical review on energy use and savings in the cement industries
2011年5月1日 Increases in the ball charge distribution and surface hardness of grinding media and wear resistant mill linings have shown a potential for reducing wear as well as energy Ball mills meanwhile, due to low electrical energy efficiency and limitations on drying capacity, play a minor role in new installations Cement grinding In Table 1, three common cement Thomas Holzinger, Holzinger Consulting, grinding system 2016年4月25日 In this study, certain measures are implemented in an existing raw mill in a cement factory and the specific energy consumption of the unit is calculated to be 2552 kWh/ton farine The effectsDetermination of correlation between specific energy 2020年2月1日 Electricity consumption is a major energy efficiency indicator in cement raw materials grinding system Advance prediction of electricity consumption provides the basis for Energy and exergy analyses for a cement ball mill of a new
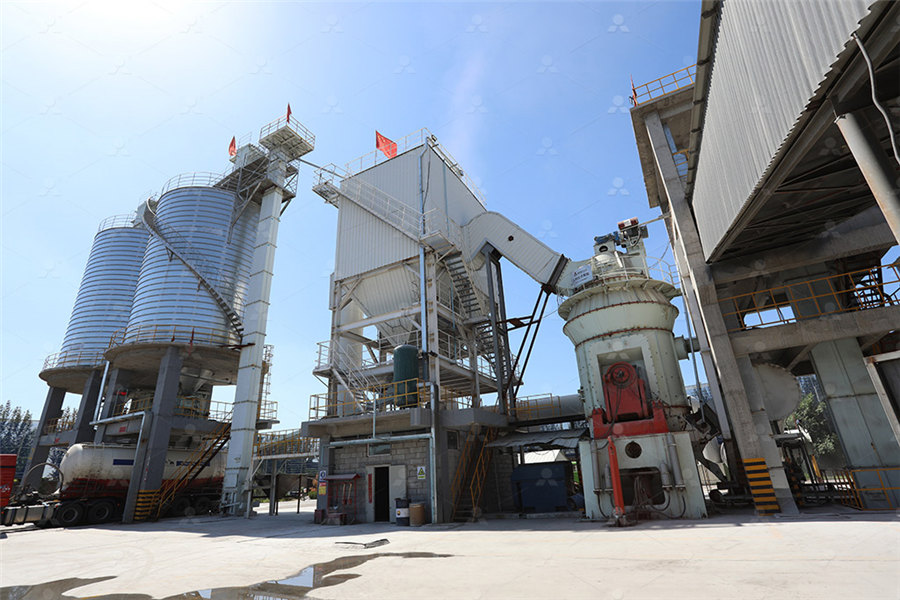
Determining cement ball mill dosage by artificial intelligence tools
2013年12月1日 This paper proposes modelling ball mill consumption as used in the cement industry from field variables The regression model was based on artificial neural networks forSummary of Grinding in Cement Manufacturing Purpose of Grinding Essential for creating a fine powder from raw materials Prepares material for the next steps in cement production Types of Mills Ball Mills Use steel balls to grind material Higher energy consumption Vertical Roller Mills Use cylindrical rollers for grindingGrinding in Cement Manufacturing: Key Process, Types of Mills, 1 Of the 4 main mill systems in use for cement grinding, ball mills are by far the predominant, despite a higher energy consumption compared with a standalone Vertical Roller Mill or Roller Press; 2Improvements in New Existing Cement Grinding Nowadays, in the field of cement grinding system of the world cement industry, the major cement grinding equipments include loop flow ball mill, roller press, ball mill semifinishing system, and vertical mill system, in which ball mill and Power Consumption of Cement Manufacturing Plant
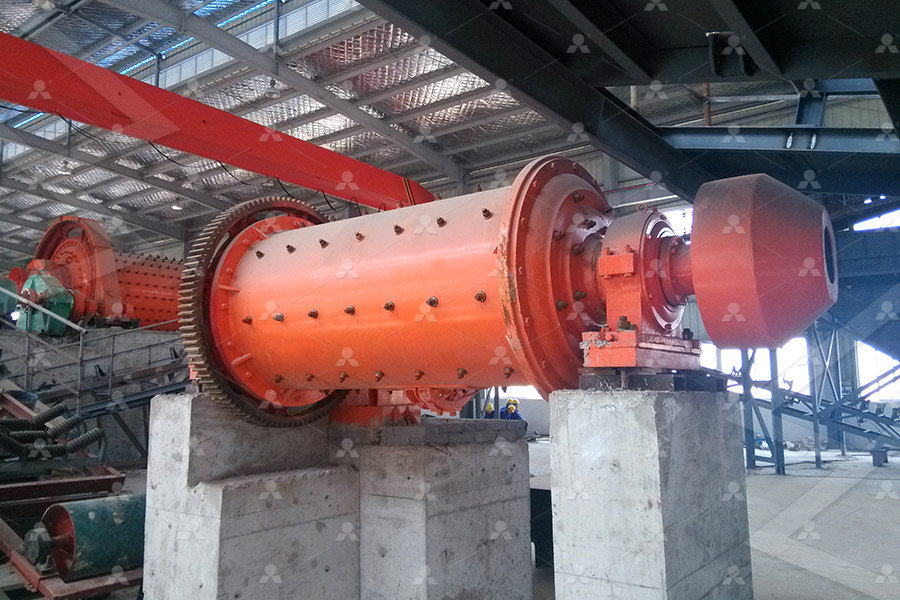
polysius® booster mill thyssenkrupp Polysius
Advantages at a glance: Modular design and small footprint enable integration in existing grinding plants Production increase in range of 1020 %, depending on the fineness, especially for smaller ball mill systems up to 100 tph Quality improvement by use of the additional grinding stage, for example to improve the early strength while maintaining the original production rate2023年4月23日 A comparison of the grinding media is given together with the knowledge gaps that still need to be bridged to improve the quality and performance of grinding media used in ball mills(PDF) Grinding Media in Ball MillsA Review ResearchGateIn the cement industry, the choice between a vertical roller mill (VRM) and a ball mill for cement grinding is a crucial decision These two types of mills have unique advantages and disadvantages that can significantly impact the efficiency, energy consumption, and overall performance of a cement plantVertical roller mill vs ball mill for cement grinding: Comparison 2013年2月26日 This is an abridgedversion of the full article, which appeared in the March 2013 issue of World Cement Subscribers can view the full article by logging in Introduction Vertical roller mills (VRM) have become the standard for grinding raw materials in the cement manufacturing paring ball mills and VRMS for cement grinding
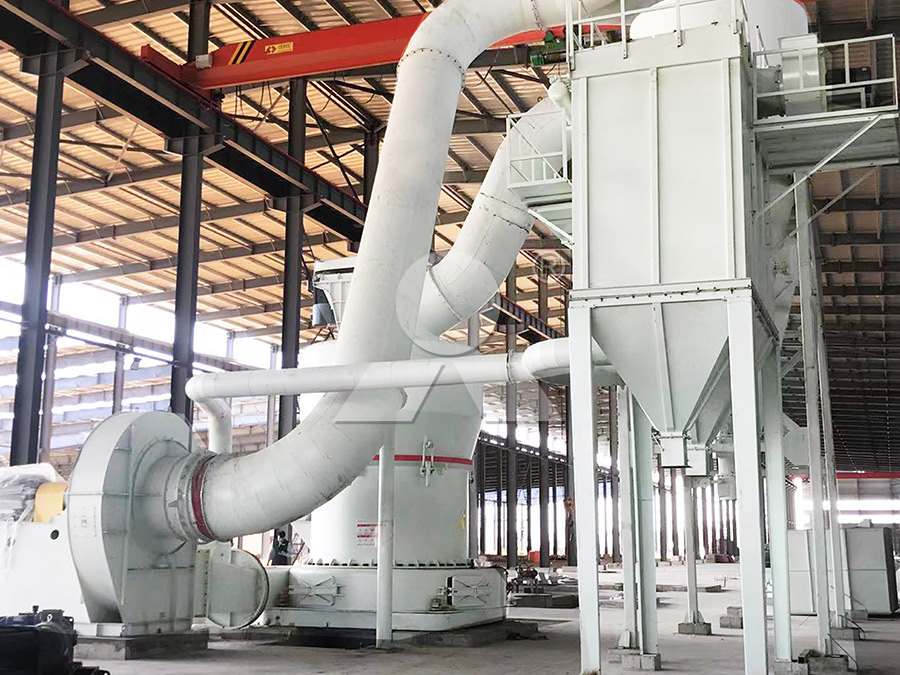
Ball Mill For Cement Grinding – Cement Ball Mill Ball Mill
Ball mill for cement grinding is a kind of important cement equipment in cement plants According to statistics, the power consumption per ton of cement production is no less than 70 kW / h, but the effective utilization rate of this part of electric energy is very lowenergy is used for many operations like Crushing,Grinding,Rolling etc, The present paper deals with the methods and technologies that can be adopted in cement process plants to optimize Electrical energy consumption to conserve energy Index Terms Cement industry, Energy conservation, Electrical Energy, OptimizationOptimizing Electrical Energy Consumption In Cement Process Comparison of cement grinding systems for ordinary portland cement at 3500 Blaine, 4% limestone Ball mill Combi grinding system Finish grinding Ball mill with cage rotor separator Roller press in semifinish mode and ball mill VRM Roller press Specel Energy consumption mill motors kWh/t 30 25 17 17 % at mill motor (ball mill 100%) % 100 83 57 57Thomas Holzinger, Holzinger Consulting, grinding system 2023年8月21日 Energy consumption in cement grinding is a significant aspect of cement production and constitutes a substantial portion of the overall energy consumption in cement manufacturing The grinding process is energy CuttingEdge Grinding Solutions Indian Cement
.jpg)
Predictive Controller Design for a Cement Ball Mill
The annual cement consumption in the world is around 17 billion tonnes and is increasing by 1% every year []Cement industries consume 5% of the total industrial energy utilised in the world []A total of 40% of the total energy online live calculators for grinding calculations, Ball mill, tube mill, critical speed, Degree of filling balls, Arm of gravity, mill net and gross powerball mill calculations, grinding media filling degree, ball size, mill Size of the grinding media typically varies in a range of 48 mm The grinding tools reach a tip speed of 5 times the critical speed, rather creating a constant cloud of grinding media than a revolving mass of rolling and falling balls inside the rotating shell of a ball mill, at a maximum of 07 times the critical speed onlyLet’s talk: polysius® booster mill – the next level in cement The grinding ball, is also known as grinding media or ball mill ball is the medium used to grind the material in the ball mill In actual use, the steel ball, the material, and the cylinder wall constantly collide and friction, and the steel ball itself will also produce consumptionGrinding Ball Ball Mill Balls For Sale Ball Mill Media Cement

BALL MILL FLSmidth Cement
This reduces the energy consumption of the mill ventilation fan and keeps your energy costs down Cement grinding – taking on the tough tasks This table shows the range of FLSmidth ball mills for cement grinding, with capacities up to ~10 000 kW in This review paper is mainly going to focus on the effect of grinding media on ball mill performance Grinding media directly affects energy consumption, product size and consequently the grinding Grinding Media in Ball MillsA Review ResearchGateTraditional cement grinding technology The cement mill has low output, high energy consumption, low quality of finished cement, and high production costs It is necessary to strengthen the upgrading and upgrading of the cement grinding processDifference Between Cement Vertical Mill and Ball MillA 10 MW cement mill, output 270 tonnes per hour A cement mill (or finish mill in North American usage [1]) is the equipment used to grind the hard, nodular clinker from the cement kiln into the fine grey powder that is cementMost cement is currently ground in ball mills and also vertical roller mills which are more effective than ball millsCement mill Wikipedia
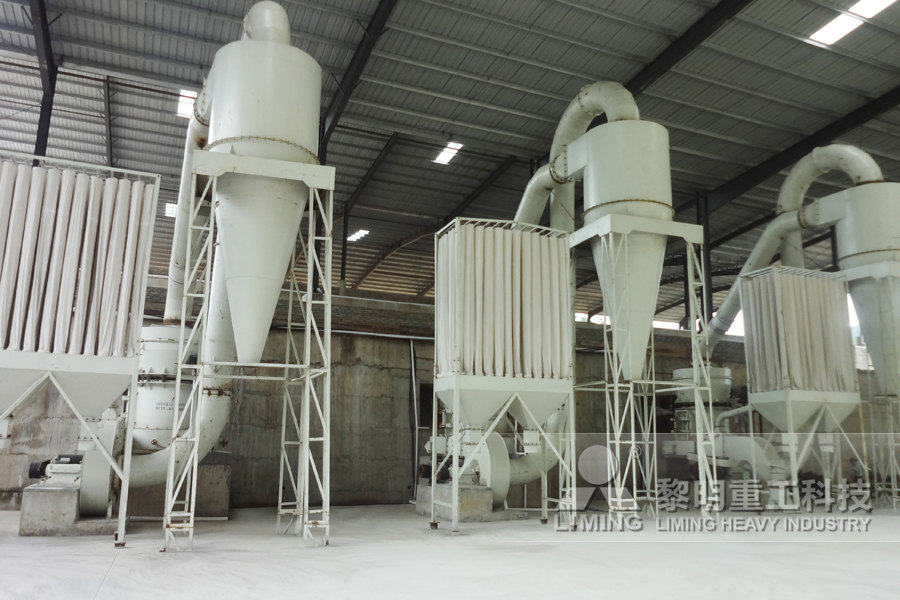
`Grinding Aid Effectiveness in Cement Ball Mill Academia
Grinding Aid Effectiveness in Cement Ball Mill Web: bulawali : bulawali@gmail, ali@bulawali LinkedIn: Ali Bulawali The introduction of the grinding aid (GA) has been started more than 50 year ago, to facilitate clinker grinding in cement mills improve mill output despite of the above features, the wear of mill interior parts well be increaseCement Grinding Unit EPC Solution With a strong RD team, experienced engineers, and firstclass technical services, we aim to provide users with the most advanced and optimized cement production solutions The main task of Cement Grinding Plant Expert Cement Grinding 2022年8月10日 Grinding might be an individual step in the cement production line but it is a crucial one, given the energy consumption and impact on the quality of output that it gives ICR explores how grinding methods have evolved with Grinding: Smarter Solutions Indian Cement Review2019年10月11日 Cement grinding machine selection will directly decide the quality and cost of whole cement grinding unknit According to the real cement projects, there are three common solutions for cement grinding plant Cement Cement Grinding Plant Overview Cement Grinding
.jpg)
Ball charge optimization INFINITY FOR CEMENT EQUIPMENT
Previous Post Next Post Contents1 Ball charge optimization2 1 How to use the BP21 2 Description of the main indicators used in this BP2101 The residue on 2mm/4mm before partition wall2102 Material filling level and ball charge expansion211 Cement mill specific power 1st compartment 212 Raw mill specific power 1st compartment Ball charge 2016年4月25日 The proposed model correlates the specific grinding energy, the clinker work index and the specific surface (Blaine) of a cement produced through finegrinding in ball millsDetermination of correlation between specific energy consumption 2024年1月5日 Closedcircuit ball mill grinding plant Advantage: Lower power consumption than an open circuit ball mill High cement fineness achievable Cement fineness can be controlled with separator adjustment Disadvantage: Closedcircuit mills are more sophisticated and can have more technical problems Larger space requirement Higher investment cost (+ 25 Cement ball mill process calculation pdf PPT SlideSharearticle Ball mill upgrade cuts energy consumption by 25% Upgrading an existing ball mill circuit with hydraulic roller presses and TRIBOMAX® wear surfaces achieved a 127% increase in production, at the same time as lowering power consumption by Ball mill upgrade cuts energy consumption by 25% FLSmidth Cement
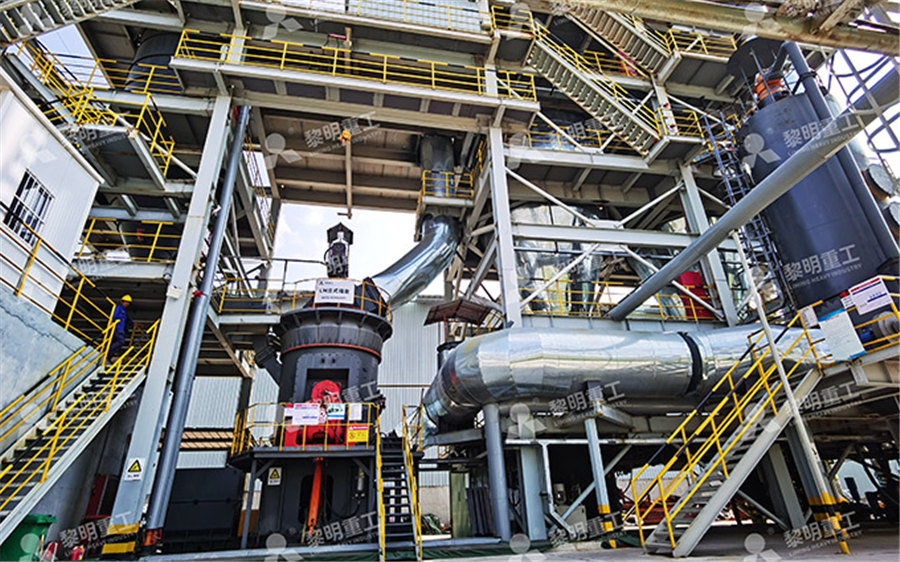
Energy and cement quality optimization of a cement grinding circuit
2018年7月1日 Among the industries, the nonmetallic industry was reported as the third largest energy user and accounted for about 12% of the global energy use [1]Within this portion, cement industry had the majority of the utilization with 85–12% [1], [2]US Energy Information Administration (EIA) [7] named cement industry as the most energy intensive among the 2021年1月25日 Choice and consumption of grinding media is related primarily to the volume and charecteristics of the ore Detour Gold GRINDING BALL USAGE: MEDIA APPLICATION SUITABILITY: Tower Mills: 05”15” grinding balls are recommended The normal top size of They are recommended for cement grinding and ultrafine wet regrinding Grinding Balls and Other Grinding Media: Key consumables2023年10月27日 The ball mill is a rotating cylindrical vessel with grinding media inside, which is responsible for breaking the ore particles Grinding media play an important role in the comminution of mineral ores in these mills This work reviews the application of balls in mineral processing as a function of the materials used to manufacture them and the mass loss, as A Review of the Grinding Media in Ball Mills for Mineral Summary of Grinding in Cement Manufacturing Purpose of Grinding Essential for creating a fine powder from raw materials Prepares material for the next steps in cement production Types of Mills Ball Mills Use steel balls to grind material Higher energy consumption Vertical Roller Mills Use cylindrical rollers for grindingGrinding in Cement Manufacturing: Key Process, Types of Mills,
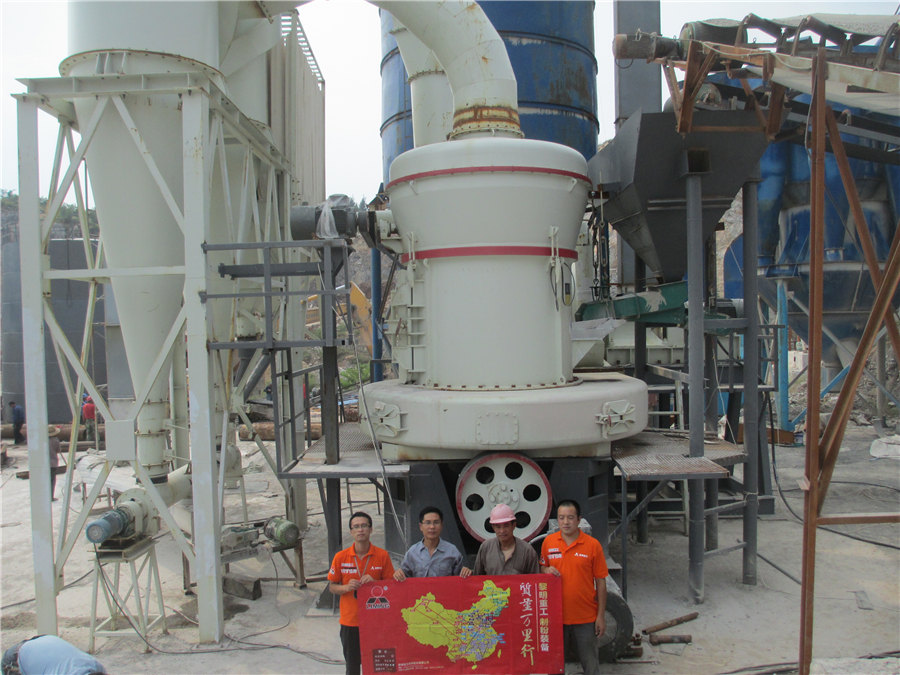
Improvements in New Existing Cement Grinding
1 Of the 4 main mill systems in use for cement grinding, ball mills are by far the predominant, despite a higher energy consumption compared with a standalone Vertical Roller Mill or Roller Press; 2Nowadays, in the field of cement grinding system of the world cement industry, the major cement grinding equipments include loop flow ball mill, roller press, ball mill semifinishing system, and vertical mill system, in which ball mill and Power Consumption of Cement Manufacturing PlantAdvantages at a glance: Modular design and small footprint enable integration in existing grinding plants Production increase in range of 1020 %, depending on the fineness, especially for smaller ball mill systems up to 100 tph Quality improvement by use of the additional grinding stage, for example to improve the early strength while maintaining the original production ratepolysius® booster mill thyssenkrupp Polysius2023年4月23日 A comparison of the grinding media is given together with the knowledge gaps that still need to be bridged to improve the quality and performance of grinding media used in ball mills(PDF) Grinding Media in Ball MillsA Review ResearchGate
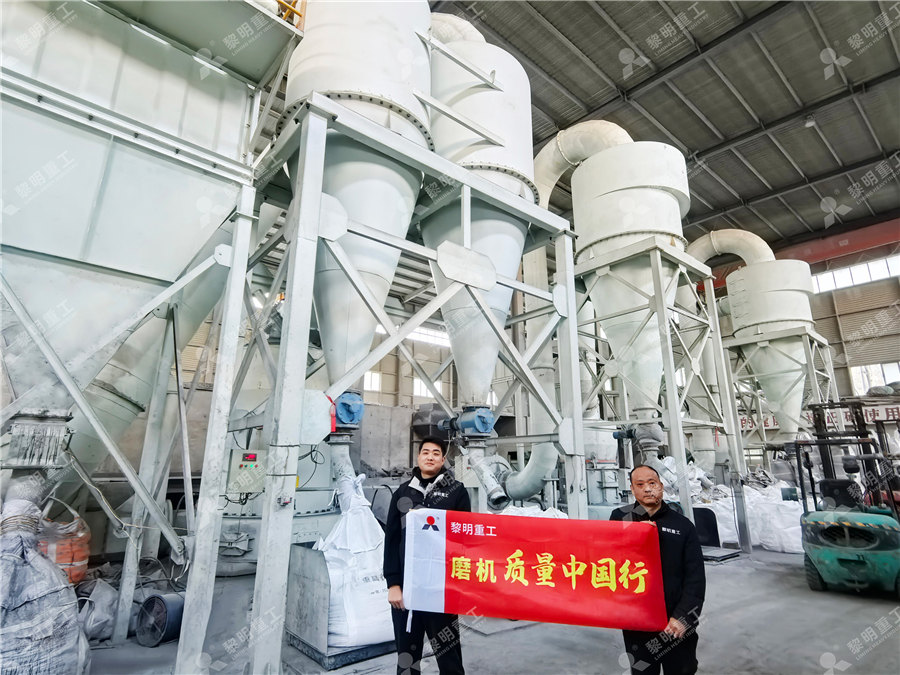
Vertical roller mill vs ball mill for cement grinding: Comparison
In the cement industry, the choice between a vertical roller mill (VRM) and a ball mill for cement grinding is a crucial decision These two types of mills have unique advantages and disadvantages that can significantly impact the efficiency, energy consumption, and overall performance of a cement plant2013年2月26日 This is an abridgedversion of the full article, which appeared in the March 2013 issue of World Cement Subscribers can view the full article by logging in Introduction Vertical roller mills (VRM) have become the standard for grinding raw materials in the cement manufacturing paring ball mills and VRMS for cement grindingBall mill for cement grinding is a kind of important cement equipment in cement plants According to statistics, the power consumption per ton of cement production is no less than 70 kW / h, but the effective utilization rate of this part of electric energy is very lowBall Mill For Cement Grinding – Cement Ball Mill Ball Mill energy is used for many operations like Crushing,Grinding,Rolling etc, The present paper deals with the methods and technologies that can be adopted in cement process plants to optimize Electrical energy consumption to conserve energy Index Terms Cement industry, Energy conservation, Electrical Energy, OptimizationOptimizing Electrical Energy Consumption In Cement Process
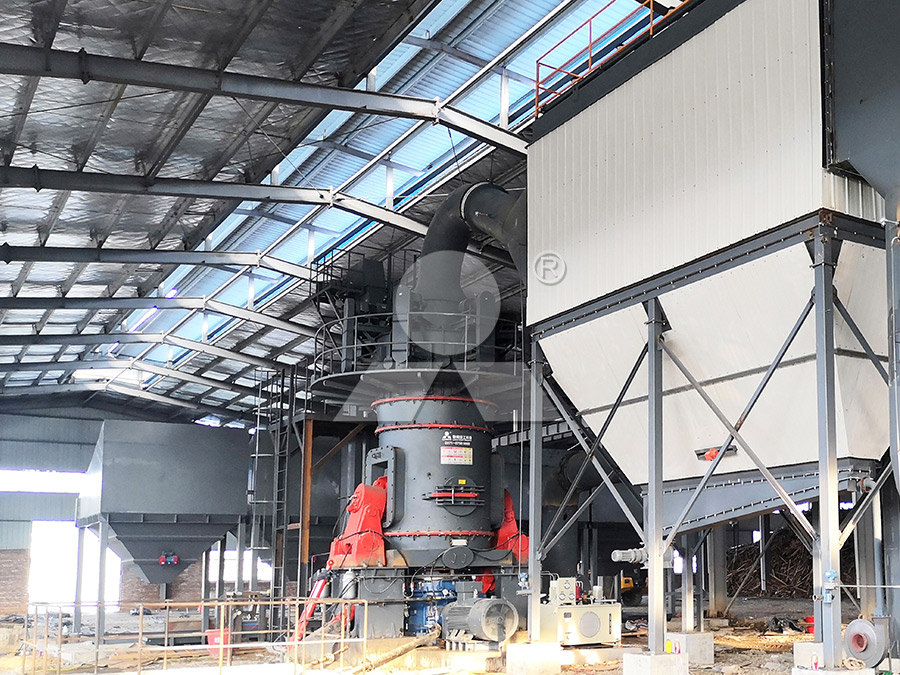
Thomas Holzinger, Holzinger Consulting, grinding system
Comparison of cement grinding systems for ordinary portland cement at 3500 Blaine, 4% limestone Ball mill Combi grinding system Finish grinding Ball mill with cage rotor separator Roller press in semifinish mode and ball mill VRM Roller press Specel Energy consumption mill motors kWh/t 30 25 17 17 % at mill motor (ball mill 100%) % 100 83 57 57