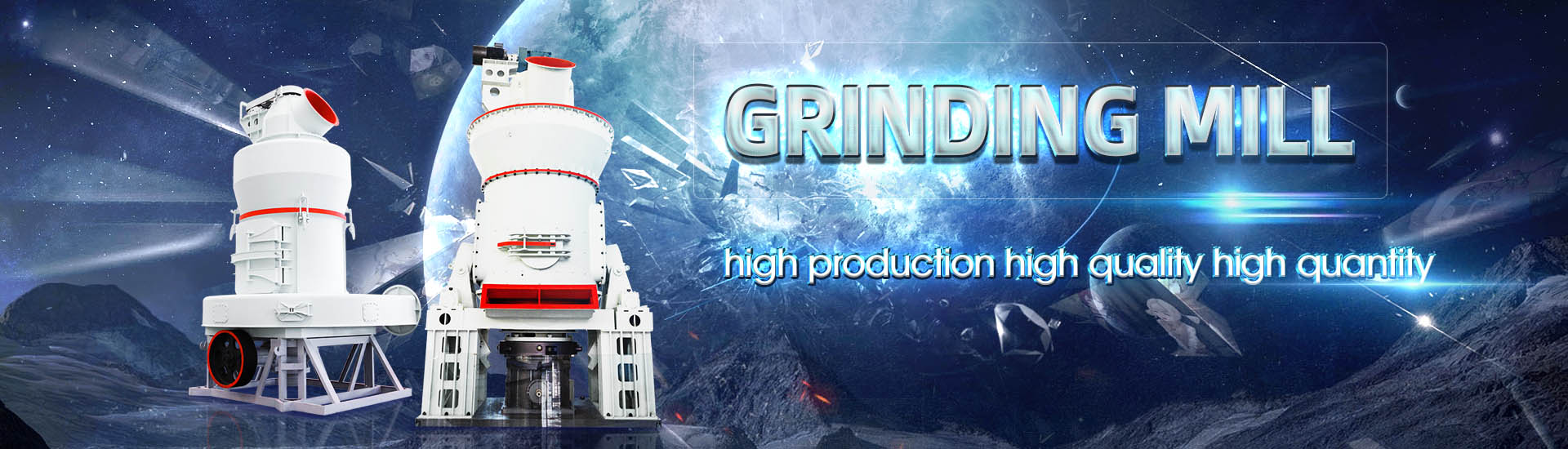
Selection of ore grinding mill
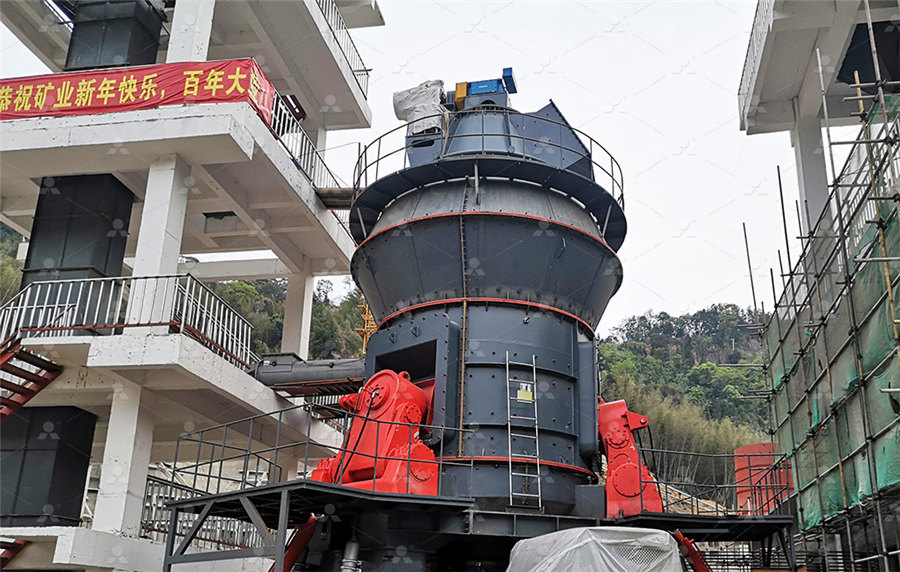
A Review of the Grinding Media in Ball Mills for Mineral Processing
2023年10月27日 Grinding media play an important role in the comminution of mineral ores in these mills This work reviews the application of balls in mineral processing as a function of the materials used to manufacture them and the mass loss, as influenced by three basic wear 2017年9月1日 The objective of this work is to assess the influence of fine grinding in ball mills and stirred mills on valuable mineral liberation and particle shape characteristics of UG2 ore, a Fine grinding: How mill type affects particle shape characteristics 2023年4月23日 One of the most used tumbling mills is the ball mill This paper reviews different types of grinding media that have been developed and improved over the years and their properties Also(PDF) Grinding Media in Ball MillsA ReviewThe relative importance of these three main grinding actions and their mutual balance resulting in a continuous uniform operation of the mill depend to a very large extent on the nature of the Primary Grinding Mills: Selection, Sizing And Current Practices
.jpg)
How to Choose the Correct GRINDING MEDIA PCI Mag
Acceptable Way: measure the initial media level with a stick or mark somewhere visible Check the level periodically and fill when needed Alternative Way: passive maintenance: wait until 2007年1月1日 The fine grinding mills are classified often into five major groups (i) impact mills, (ii) ball media mills, (iii) air jet mills, (iv) roller mills, and (v) shearing attrition mills from the Chapter 10 Selection of Fine Grinding Mills ScienceDirect2012年6月1日 The paper presents an overview of the current methodology and practice in modeling and control of the grinding process in industrial ball mills Basic kinetic and energy Grinding in Ball Mills: Modeling and Process Control ResearchGateGrinding media can be the ore itself (autogenous grinding primary and secondary), natural or manufactured nonmetallic media (pebble milling) or manufactured metallic media steel Selection Of Rod Mills, Ball Mills, Pebble Mills And Regrind Mills
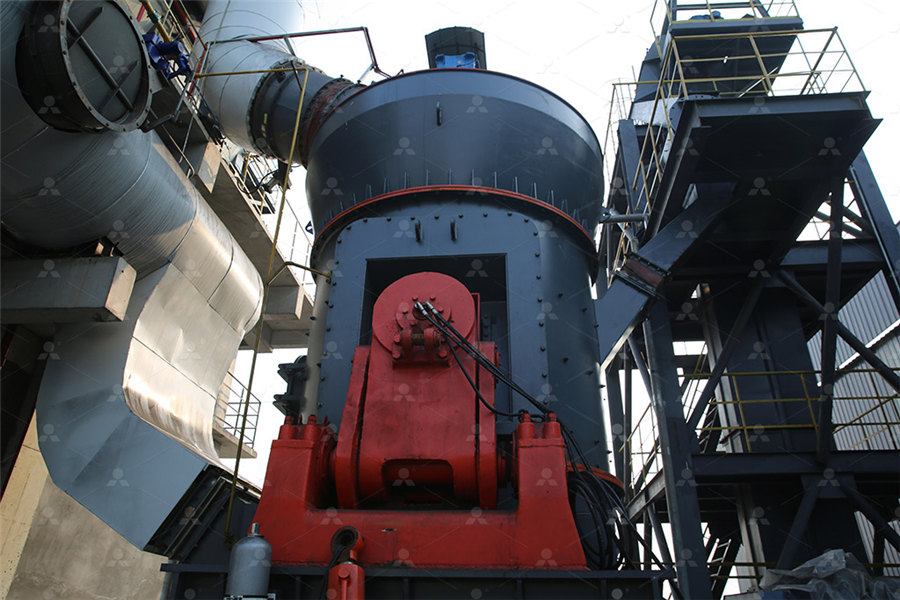
Modeling of Bauxite Ore Wet Milling for the Improvement of
2021年9月5日 This study aimed to model bauxite grinding and assess the optimum material filling volume in a laboratory ball mill in order to improve mill and overall process efficiency Stirred milling technologies have firmly established themselves in concentrator circuits as energyefficient alternatives to tumbling ball mills High and continued increases in electricity costs, TECHNOLOGY SELECTION OF STIRRED MILLS FOR ENERGY Combining impact and shearing actions enhances mill efficiency Proper selection of media milling equipment is vital for success in all three areas There are many different types of grinding mills (Table 1) Some devices, such as ball mills, Solids Choose the Right Grinding Mill Chemical Video credit: shsbjq / CC BYSA 40 Specifications Important specifications when selecting grinding mills and pulverizers include, The size of the mill can range from pilot/lab to production, eg, 35 to 1600 cu ft; Feed size, material, and Grinding Mills and Pulverizers Selection Guide:
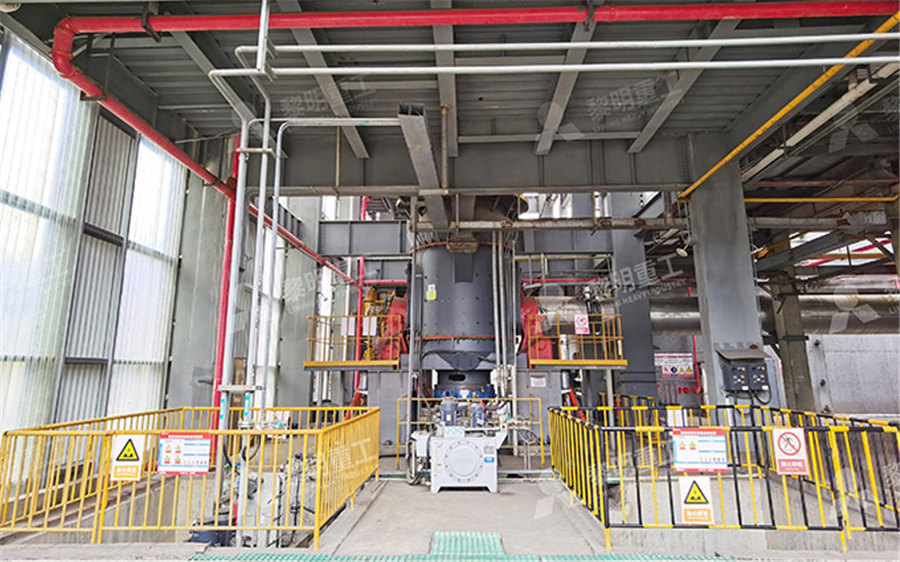
Helping to reduce mining industry carbon emissions: A stepby
2022年3月30日 Currently Autogenous (AG)/SemiAutogenous (SAG)/Ball mill technology dominates comminution circuit design where grinding to relatively fine sizes is required, eg the gold, copper, nickel, platinum, silver, lead, zinc and low grade iron ore sectors High Pressure Grinding Rolls (HPGR) have been found to be more energy efficient than tumbling 2023年10月17日 4 Ultrafine Vertical Grinding Mill Ultrafine vertical grinding mill feed particle size ≤ 20mm, production capacity 120 t/h, production fineness 1503000 mesh CLUMUltrafine vertical grinding mill is a new type of milling equipment that includes grinding, grading, conveying, secondary powder selection, and finished product packagingHow to choose a suitable ore powder grinding mill?HGM ultrafine grinding mill can process nonmetallic ores with Mohs hardness less than 7 The equipment has stable operation, simple operation, long service life, low carbon and environmental protection There are 5 models of HGM ultrafine grinding mill, SBM Ore Ultrafine Grinding Millthe mill, uncouples the breakage rate and selection functions and introduces time as a variable The ki is the rate ofbreakage of particle size i in the mill, while the bij are the breakage selection functions for the breakage of particles from class j into class i The dynamic conservation of mass equations describing the Grinding • 10 mm Assessment of the Functionality of Selection and Breakage Rate
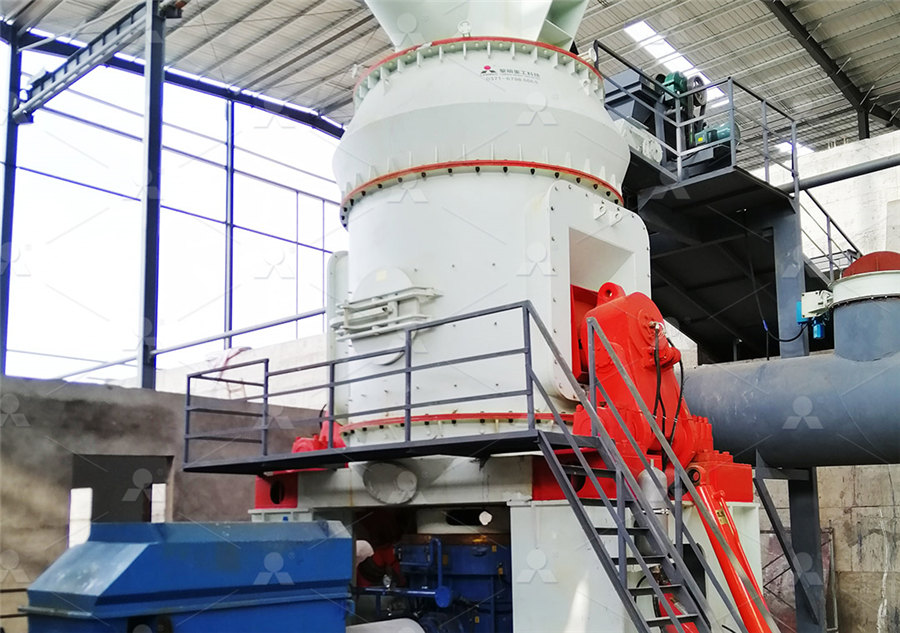
Grinding Mills for reliable size reduction tasks RETSCH
After the grinding, the state of the solid is changed: the grain size, the grain size disposition, and the grain shape There are essentially five different grinding mechanisms, and Retsch offers seven different types of mills that can be utilized The grinding balls perform for longer hours, it is advisable to subject these types of ores to grinding balls, which can withstand the higher energy that the ores possess (Yusupov et al, cations: 2007) interaction between grinding media and mineral in Selection of Grinding Media for Use in the Gold Processing 2016年6月6日 One of the most important was the severe stressing which took place at the connection of the mill shell and the trunnion bearing end plates, which is further aggravated by the considerable distortion of the shell and the bearing journals due to the dynamic load effect of the rotating mill with a heavy mass of ore and pulp being lifted and dropped as the grinding SAG Mill Grinding Circuit Design 911MetallurgistThe second primary function of a liner is to transfer rotary motion of the mill to the grinding media and charge After all, it is the interface between the mill and the grinding charge Although work on the grinding action in mills was published 100 years ago (White 1905 and Davis 1919), the firstThe Selection and Design of Mill Liners 911 Metallurgist
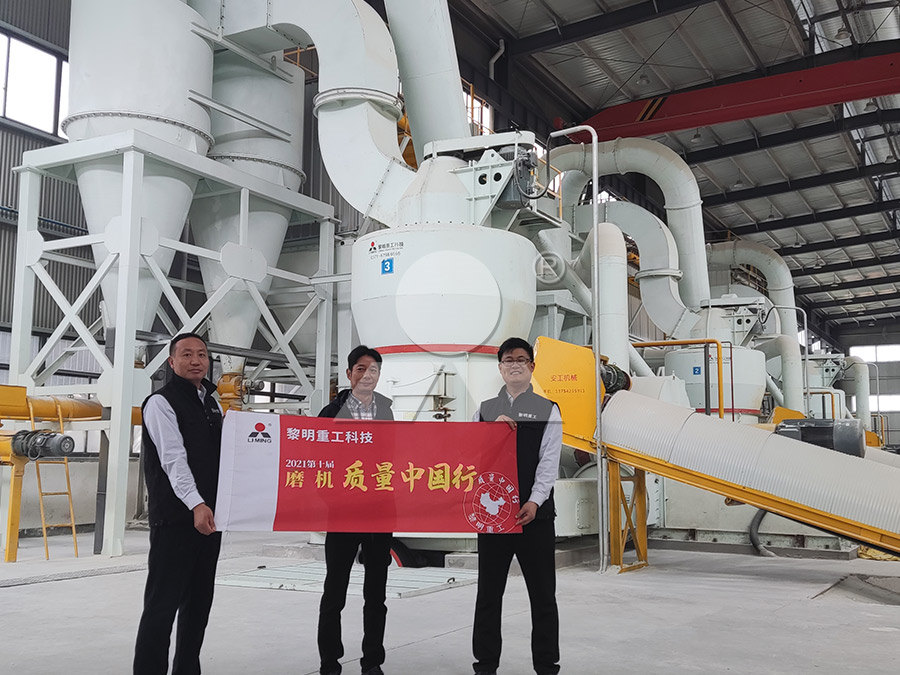
Comparison of Ore Hardness Measurements for Grinding Mill
2021年1月14日 was surprising that the Bond Rod Mill Wi average was 113 kWh/t Since the ore is unusually soft, the Rod Mill Wi is probably irrelevant in determining required power for the SAG mill Drop Weight Tests Drop Weight tests were done at Hazen and analyzed by Contract Support Services, Inc Table 4: Summary of 6 JKTech Drop Weight Tests2007年1月1日 When the finest grinding is required by dry grinding, the jet milling or the attrition milling with a roller mill, a ball media mill or a powderbed attrition mill would be useful Figure 10 shows a comparison of grinding performance between the powderbed attritiontype mill and an air jet mill as well as impact mills equipped with attrition mechanismChapter 10 Selection of Fine Grinding Mills ScienceDirect2017年11月6日 Grinding mill operation should be done only with an adequate “cushion” of coarse ore in mills to prevent ballon ball impacts that occur during low feed rate operation or grind outs Ballonball impacts develop subsurface Grinding Ball Design 911Metallurgistfrom the ores The grinding of ore is a highly energyintensive process [1–4] In this process, the size of the particle obtained depends on the energy consumption of the ball mill The major challenge encountered in the process of iron ore grinding is to maintain the desired product particle size distribution (PSD) with sufficientEstimation of Grinding Time for Desired Particle Size Distribution
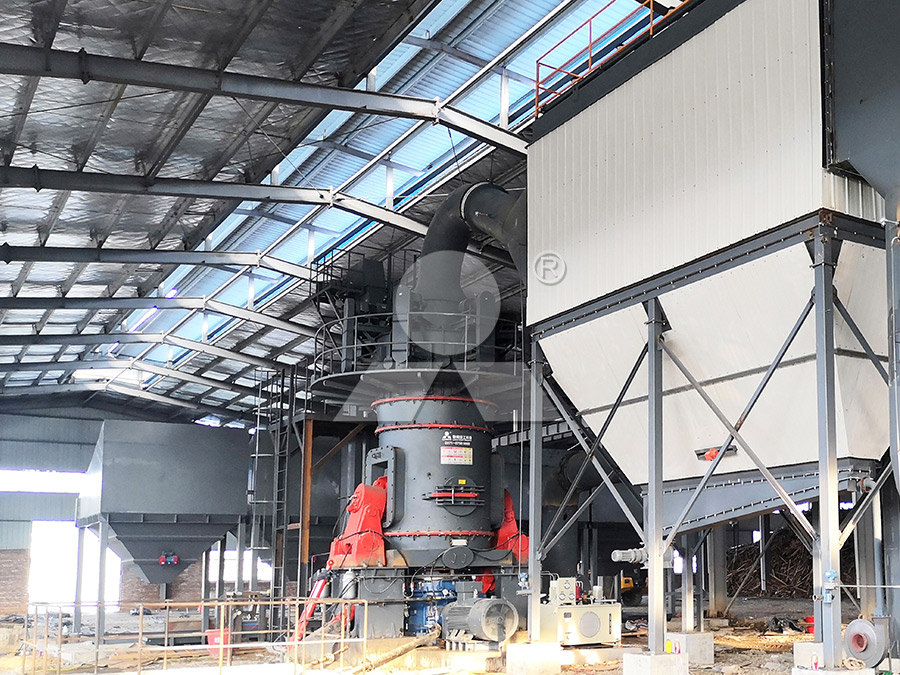
Grinding mills for mining and minerals processing Metso
Horizontal Mill Plant Units offer complete support in grinding circuit selection, as well as execution, service and operation Read more Grinding parts and services Our grinding mill inspection packages can help you save thousands of Euros per day Gear and pinion services A complete range of gear and pinion sets, inspections, A crushing plant delivered ore to a wet grinding mill for further size reduction The size of crushed ore (F 80) was 40 mm and the SG 28 t/m 3 The work index of the ore was determined as 122 kWh/t A wet ball mill 1 m × 1 m was chosen to grind the ore down to 200 micronsGrinding Mill an overview ScienceDirect Topics2024年1月10日 When gravity or magnetic separation of metal ores (such as tungsten tin ore and rare metal ores), rod mills are often used to prevent overcrushing; it is also suitable for brittle materials, such as coal; in the secondstage grinding process; generally, a rod mill is used as the primary grinding equipment, which has larger production capacity and higher efficiencyBall Mill VS Rod Mill: Difference Selection JXSC Machine2015年4月15日 Bond rod mill grindability tests at 10 or 14 mesh for Work Index For each ball mill grinding step, a Bond ball mill grindability test for Work Index at one mesh size coarser than the desired 80% passing size and at the mesh size of or just finer than the 80% passing sizeWhat Ore Testing is Required For Mill Selection
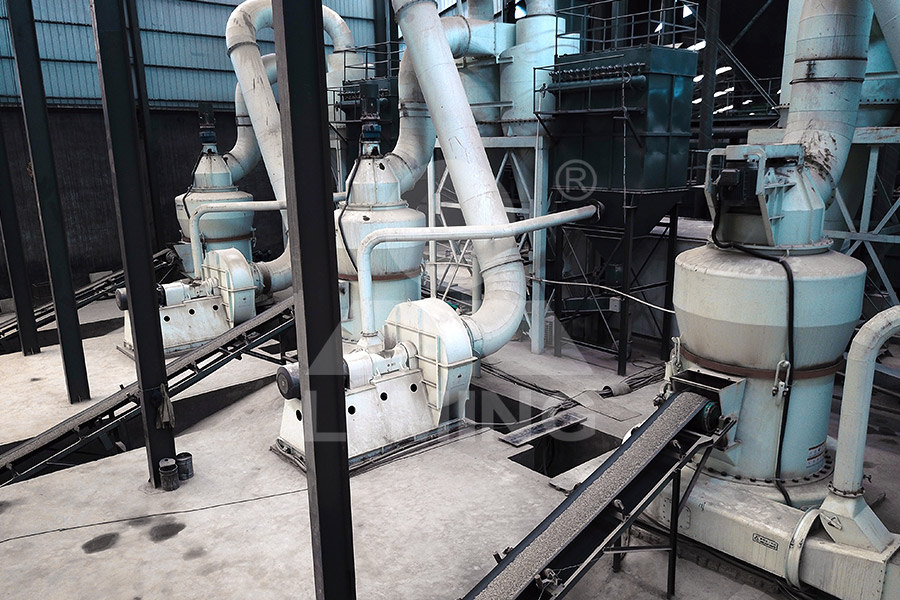
Fine grinding: How mill type affects particle shape characteristics
2017年9月1日 With the continual depletion of high grade simple ore bodies, more complex, finely disseminated ore bodies are being processed, which has led to an increase in the prevalence of fine grinding (Sinnott et al, 2006)This has been evident in the platinum group element (PGE) industry in South Africa, where the Bushveld Complex hosts 70% of global 2017年6月2日 Selection of the proper crusher, grinding mill or pulverizer is dependent on the material to be processed and the requirements of the end product Additional factors to consider are the feed size and hardness, whether the feed is wet, dry or both and whether the equipment needs to be operating continuously or in batchesHow it Works: Crushers, Grinding Mills and Pulverizers2014年1月1日 An analysis of the kinetics of dolomite grinding in a dry ball mill reveals that the following approximations apply for the parameters of the batch grinding model: the size discretized selection Population balance model approach to ball mill INTRODUCTION Primary grinding mills as defined in this paper, are autogenous or semiautogenous rotating, tumbling mills having a coarse feed with a top size usually varying from 150 to 300 mm (6 to 12 inches) Most frequently, the feed to these mills is the product of primary crushing plants but in some cases run of mine ore is used as feed such as at Benguet, Primary Grinding Mills: Selection, Sizing And Current Practices
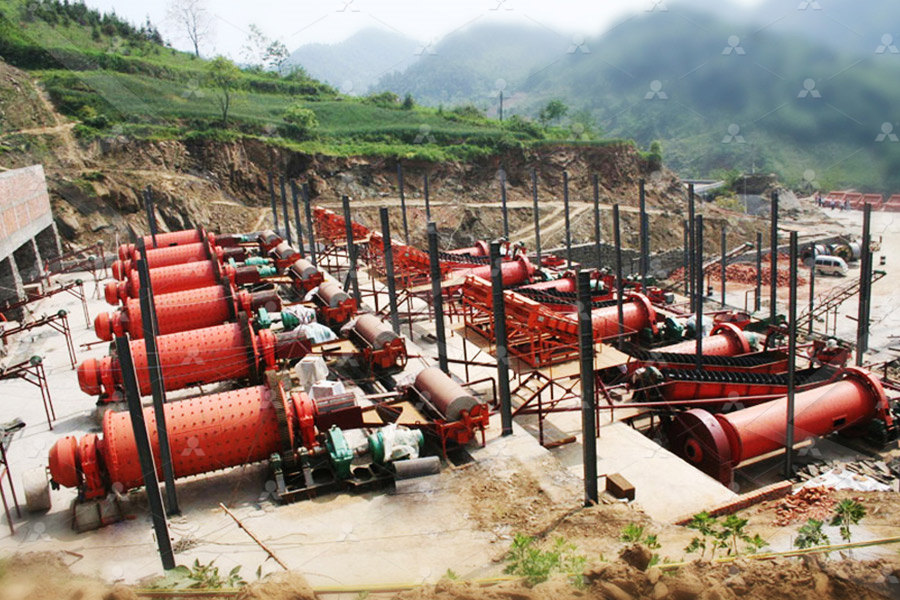
CLUM Ultrafine Vertical Grinding Mill
CLUM series of ultrafine gypsum powder vertical grinding mills are a new type of ultrafine industrial ore grinding equipment that specific surface area 21000cm 2 /g, the main machine powder can reach D97=85um for two times The 2023年10月27日 The ball mill is a rotating cylindrical vessel with grinding media inside, which is responsible for breaking the ore particles Grinding media play an important role in the comminution of mineral A Review of the Grinding Media in Ball Mills for Mineral Processing2018年8月8日 One of the most effective methods of grinding Portland cement is the use of an electromagnetic mill, which has proven its advantage in creating clinkerless binders [2], regulating the kinetics of (PDF) Grinding Kinetics Adjustment of Copper Ore Grinding in Effect of mill type on ore grinding performance Ball mills are widely used in the mining and metallurgical industries for the grinding of ores and other materials There are a wide variety of mill types available, each with its own advantages and disadvantages The Factors affecting ores grinding performance in ball mills
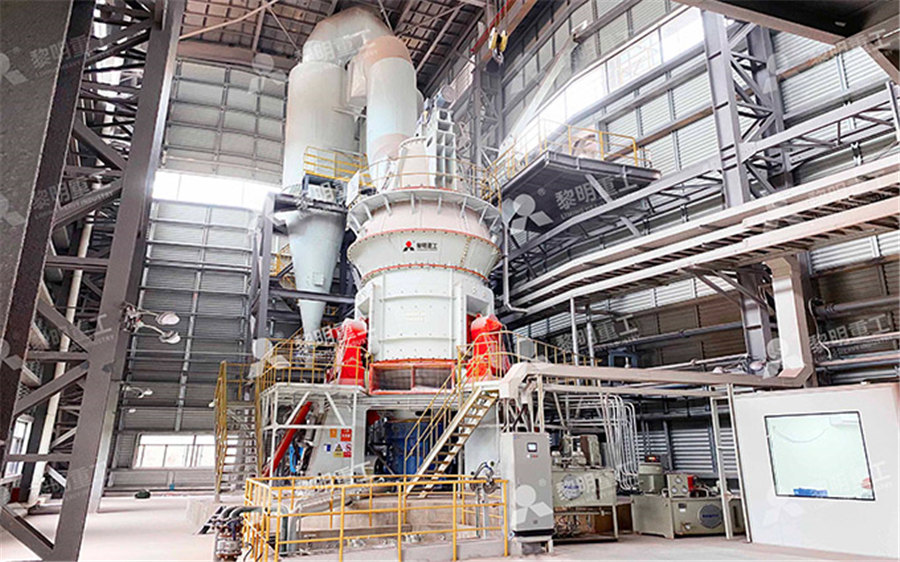
The Selection Design and Application of Mill Liners for Large
The history of mill liners has evolved over time and this paper tracks the changes and development of liner technology It provides an overview of the primary types of liners, the design and the materials of construction The design of a mill liner is driven by application, materials of construction, casting technology and handling issues The choice of solid steel, grid liners, 2016年7月8日 In the same way Fig 3 indicates that an 800hp motor and a 101/214 or 105′ by 14′ Ball Mill is required Following is a condensed tabulation of the above selections Sizing a Ball or Rod Mill Sizing a Crusher using >1200 Wi of Ores from Database For your convenience, this manual lists over 1200 work indexesEquipment Sizing: Crusher or Grinding Mill 911MetallurgistThe operators need to also be acutely aware of the risk that they expose the liner and mill to if they allow the mill charge to run down Strict lower limits must be placed on mill load, and the mill must be stopped if feed rate or ore incompetence lead to the mill charge grinding out and exposing the liners to direct impactThe selection and design of mill liners AcademiaThis review serves to highlight problems of mill liner designs and how they can be tackled in a logical and often inexpensive manner by considering charge trajectories and liner spacing criteria, in conjunction with liner wear monitoring Dramatic shortcomings of mill liner designs, especially of large SAG mills, such as rapid failure and even mill shell damage arising from impacting of the [PDF] The selection and design of mill liners Semantic Scholar
.jpg)
Solids Choose the Right Grinding Mill Chemical
Combining impact and shearing actions enhances mill efficiency Proper selection of media milling equipment is vital for success in all three areas There are many different types of grinding mills (Table 1) Some devices, such as ball mills, Video credit: shsbjq / CC BYSA 40 Specifications Important specifications when selecting grinding mills and pulverizers include, The size of the mill can range from pilot/lab to production, eg, 35 to 1600 cu ft; Feed size, material, and Grinding Mills and Pulverizers Selection Guide: 2022年3月30日 Currently Autogenous (AG)/SemiAutogenous (SAG)/Ball mill technology dominates comminution circuit design where grinding to relatively fine sizes is required, eg the gold, copper, nickel, platinum, silver, lead, zinc and low grade iron ore sectors High Pressure Grinding Rolls (HPGR) have been found to be more energy efficient than tumbling Helping to reduce mining industry carbon emissions: A stepby 2023年10月17日 4 Ultrafine Vertical Grinding Mill Ultrafine vertical grinding mill feed particle size ≤ 20mm, production capacity 120 t/h, production fineness 1503000 mesh CLUMUltrafine vertical grinding mill is a new type of milling equipment that includes grinding, grading, conveying, secondary powder selection, and finished product packagingHow to choose a suitable ore powder grinding mill?

SBM Ore Ultrafine Grinding Mill
HGM ultrafine grinding mill can process nonmetallic ores with Mohs hardness less than 7 The equipment has stable operation, simple operation, long service life, low carbon and environmental protection There are 5 models of HGM ultrafine grinding mill, the mill, uncouples the breakage rate and selection functions and introduces time as a variable The ki is the rate ofbreakage of particle size i in the mill, while the bij are the breakage selection functions for the breakage of particles from class j into class i The dynamic conservation of mass equations describing the Grinding • 10 mm Assessment of the Functionality of Selection and Breakage Rate After the grinding, the state of the solid is changed: the grain size, the grain size disposition, and the grain shape There are essentially five different grinding mechanisms, and Retsch offers seven different types of mills that can be utilized The Grinding Mills for reliable size reduction tasks RETSCHgrinding balls perform for longer hours, it is advisable to subject these types of ores to grinding balls, which can withstand the higher energy that the ores possess (Yusupov et al, cations: 2007) interaction between grinding media and mineral in Selection of Grinding Media for Use in the Gold Processing
.jpg)
SAG Mill Grinding Circuit Design 911Metallurgist
2016年6月6日 One of the most important was the severe stressing which took place at the connection of the mill shell and the trunnion bearing end plates, which is further aggravated by the considerable distortion of the shell and the bearing journals due to the dynamic load effect of the rotating mill with a heavy mass of ore and pulp being lifted and dropped as the grinding The second primary function of a liner is to transfer rotary motion of the mill to the grinding media and charge After all, it is the interface between the mill and the grinding charge Although work on the grinding action in mills was published 100 years ago (White 1905 and Davis 1919), the firstThe Selection and Design of Mill Liners 911 Metallurgist