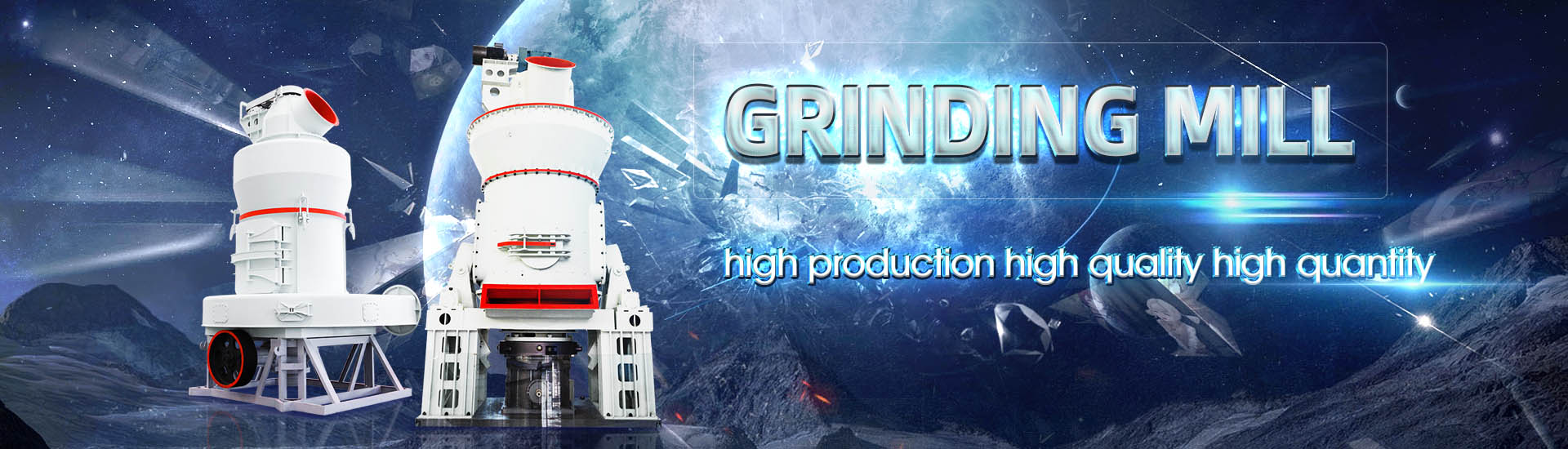
Clinker industrial grinding mill
.jpg)
Industrial versus Laboratory Clinker Processing Using Grinding
2015年12月15日 Unlike industrial mills, laboratory grinding mills operated over given time interval do not account for CL, therefore leading to different cement particle size distribution vertical roller grinding mills for grinding: • Coal • Cement raw material • Clinker / granulated slag • Industrial minerals, and • Ores The core elements of these plants are the Loesche vertical PROCESS OPTIMISATION FOR LOESCHE GRINDING PLANTSGrinding of cement clinker and granulated blast furnace slag in roller grinding mills (vertical airswept grinding mills) is a technology introduced by Loesche The first use of a Loesche mill, 2 µm 5 µm Loesche2012年5月1日 This paper presents an investigation carried out to compare the three clinker grinding systems, namely, the combined grinding (Comflex®) circuit, HPRMonly circuit, and An industrial comparative study of cement clinker grinding
.jpg)
(PDF) A study of different grinding aids for lowenergy
2023年10月23日 In this study we compare the effects of three different grinding aids on clinker grinding using a ball mill A commercial grinding additive, triethanolamine (TEA), and two industrial2023年10月19日 Clinker grinders are an important part of the cement manufacturing process They are used to grind clinker into a fine powder and are typically located at the end of the cooler in a cement plant Clinker is a nodular Clinker Grinding Techniques in Cement Manufacturing2012年11月8日 Raw materials crushing and grinding seeks to reduce materials from roughly one meter cubes of blasted stone to a size where at least 80 percent of the raw material is less Breakthrough in Clinker Grinding Massachusetts Institute of Find your clinker mill easily amongst the 11 products from the leading brands (Retsch, Liming, EIRICH, ) on DirectIndustry, the industry specialist for your professional purchasesClinker mill, Clinker grinding mill All industrial manufacturers
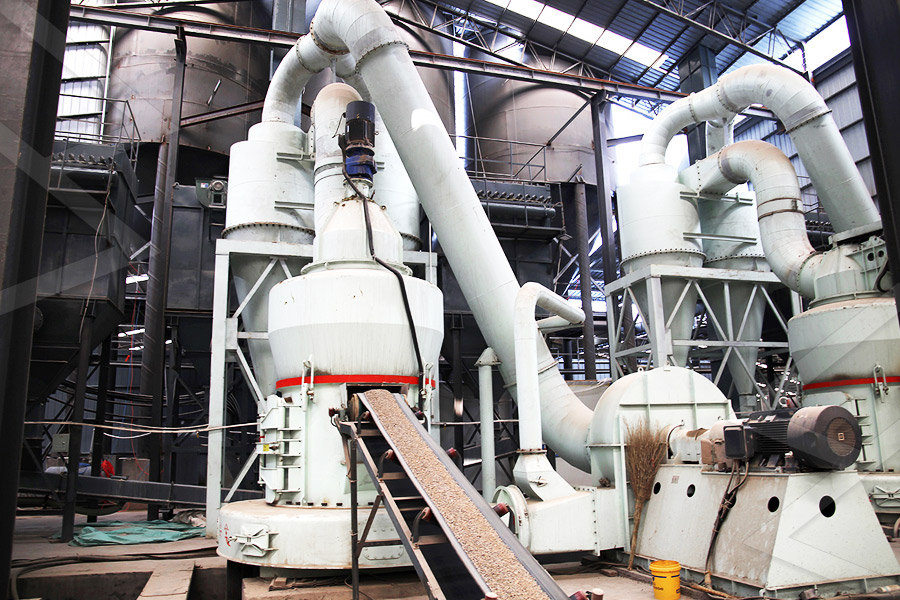
GRINDING ABILITY OF UNPROCESSED AND PROCESSED CLINKER
The grinding of a batch of material (clinker) in the laboratory mill (ball mill type) with a horizontal rotating drum was carried out in two stages: first stage using ball load (see table 1); the Download scientific diagram Various stages during industrial closedcircuit grinding tube mill from publication: Industrial versus Laboratory Clinker Processing Using Grinding Aids (Scale Various stages during industrial closedcircuit Clinker Rejects feed Fresh Ball grinding mill F : Various stages during industrial closedcircuit grinding tube mill T : Design parameters for the tube ball mill and separatorResearch Article Industrial versus Laboratory Clinker Processing The polysius® booster mill, a dry agitated bead mill, has been in development by a cooperation between Netzsch Feinmahltechnik and thyssenkrupp for several years, with the original target application in very fine cement grinding polysius® booster mill
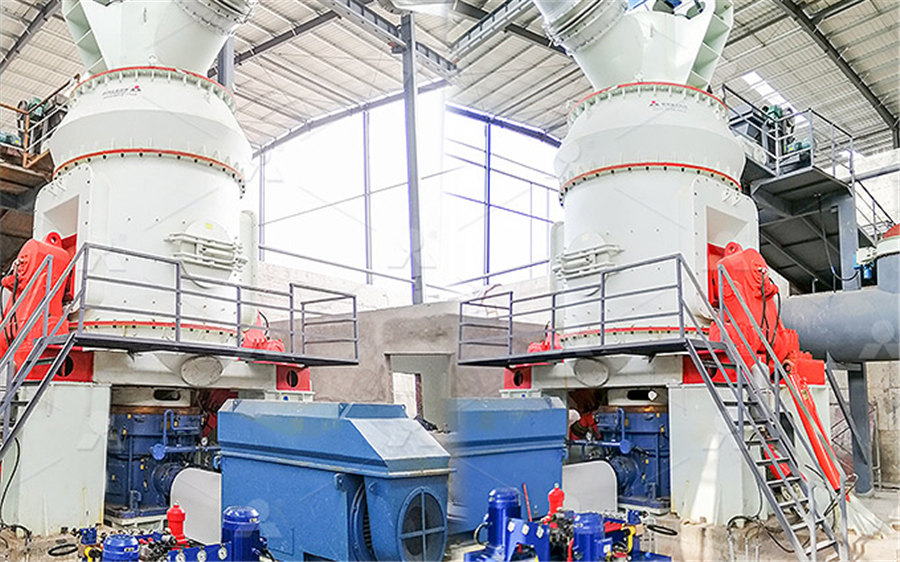
Effects of Mill Speed and Air Classifier Speed on Performance of
2021年6月29日 Five speed levels used in closed cycle grinding mill are 200, 400, 600, 800 and 1000 rpm Industrial versus Laboratory Clinker Processing Using Grinding Aids (Scale Effect)2015年12月15日 Yet, it is important to note that the decrease in Ec due to GA is around twofold higher when grinding was performed in industrial mill, as compared to laboratory mill For example, the decrease in Ec varied from 1792% to 1254% when industrial grinding was realized using the glycol or aminebased GA, respectivelyIndustrial versus Laboratory Clinker Processing Using Grinding Cement grinding unit is also called the cement grinding plant It consists of cement ball mill, dust collector, belt conveyor, bucket elevator, cement silo, powder concentrator, etc AGICO provides highquality clinker grinders and advanced cement grinding technologyCement Grinding Unit Clinker Grinder AGICO CementThe annual cement consumption in the world is around 17 billion tonnes and is increasing by 1% every year []Cement industries consume 5% of the total industrial energy utilised in the world []A total of 40% of the total energy consumption of a cement plant is used in clinker grinding in a ball mill to produce the final cement product [] Predictive Controller Design for a Cement Ball Mill Grinding
.jpg)
Cement Clinker Grinding Plant ball mills supplier
25195tph clinker grinding plant, best option for start up at low cost Cement clinker grinding unit with ball mill, roll press or VRM 24×7 Consulting Support2012年5月1日 This paper is concerned with a comparative analysis of modern cement grinding systems, namely, combined grinding (Comflex®), highpressure roll mill (HPRM) grinding, and horizontal roller mill (Horomill®) grinding Cement production trials were run with these grinding systems in the same cement plant by using the same clinker/gypsum feed to produce cements An industrial comparative study of cement clinker grinding 2024年7月31日 The production of cement, an essential material in civil engineering, requires a substantial energy input, with a significant portion of this energy consumed during the grinding stage This study addresses the gap in the literature concerning the collective impact of key parameters, including ball size, feed rate, and mill speed, on grinding efficiency Nine spherical Effect of Grinding Conditions on Clinker Grinding Efficiency: Ball 2014年2月1日 To investigate the effects of grinding media shapes on the grinding kinetics of ball mill cement clinker, the grinding effects with ϕ20 mm balls and ϕ20 × 20 mm cylinders on six different size Effects of circulating load and grinding feed on the grinding
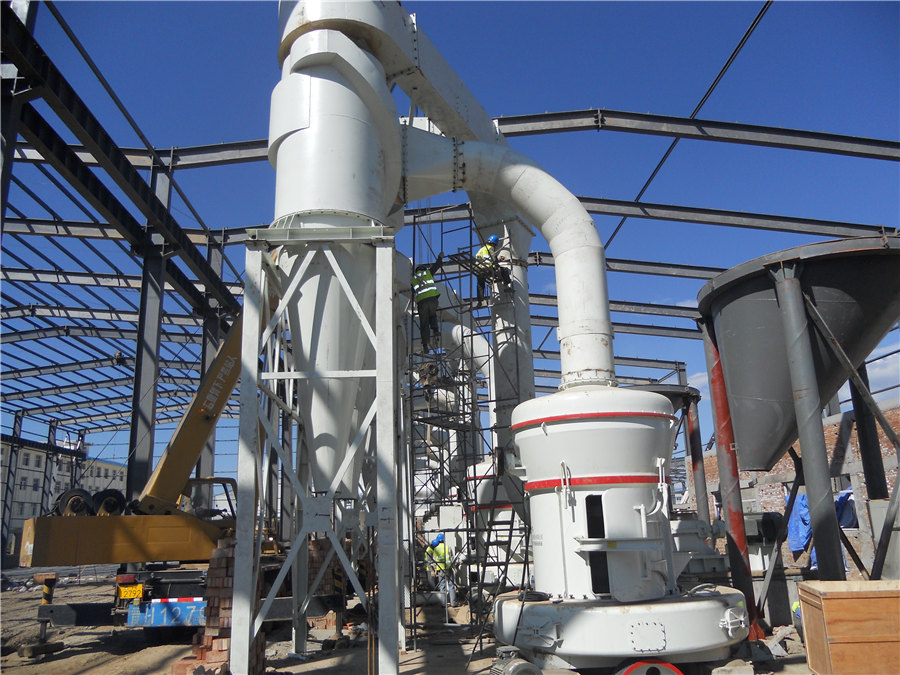
Effects of circulating load and grinding feed on the grinding
2014年2月1日 Samples of the input, output and return material of cement clinker are collected and analyzed from an industrial CKP mill The model of firstorder crushing rate function is established and all the parameters are suitable for physical characterization by using the data of the material size distribution and mass balances The values of three parameters b, μ and γ 2015年10月1日 This research study was initiated following an industrial grinding test undertaken to quantify the effect of a glycolbased GA on mill performance and cement properties The first phase presents the data collected over 2 consecutive days of clinker grinding in a realscale closedcircuit tube mill operating at around 90 ton/hQuantifying the effect of clinker grinding aids under laboratory 2012年11月8日 Current estimates of grinding power requirements used for equipment sizing are indirect indications often based on industrial experience or scaled up from laboratory tests Work indices (Bond, Hardgrove, Kick, Von Rittinger, Hukki, et al) are also indirect and empirical equations that calculate the energy needed toBreakthrough in Clinker Grinding Massachusetts Institute of 2023年4月4日 To reduce the clinker factor of cement produced in its plant of Ouagadougou, Burkina Faso, Ciments d'Afrique (CIMAF) has entrusted thyssenkrupp Industrial Solutions AG, BU Polysius, to install a polysius® booster mill By boosting the fineness and reactivity of the clinker portion, the high energy density mill will enable clinker substitution by local filler while First industrial reference for a polysius® booster mill to reduce
.jpg)
Determination of granulometrical composition of the clinker by grinding
2020年7月24日 This paper presents results regarding the grinding behaviour of two batches of material (clinker) in a ball mill with its own twostep grinding process: the first one with a ball load, the second DOI: 101016/JPOWTEC201311016 Corpus ID: ; Effects of circulating load and grinding feed on the grinding kinetics of cement clinker in an industrial CKP mill @article{Wei2014EffectsOC, title={Effects of circulating load and grinding feed on the grinding kinetics of cement clinker in an industrial CKP mill}, author={Hua Wei and Yaqun He and Effects of circulating load and grinding feed on the grinding The clinker grinding stage accounts for approximately 40% of the electric energy consumed in cement production Because of such a high level of energy demand and the inherent energy inefficiency of conventional ball mill grinding, the cement industry has continually searched for new grinding mill designs and/or grinding system configurations (PDF) An industrial comparative study of cement clinker grinding 2015年1月27日 The use of highpressure grinding rolls (HPGR) prior to ball mills has become a common practice in cement clinker grinding due to significant energy savings in comparison to ball milling aloneBallMill Grinding Kinetics of Cement Clinker Comminuted in the
.jpg)
a) Cement ball mill view, b) Cement mill sketch
Download scientific diagram a) Cement ball mill view, b) Cement mill sketch from publication: Effects of Mill Speed and Air Classifier Speed on Performance of an Industrial Ball Mill Nowadays 2016年10月5日 In this chapter an introduction of widely applied energyefficient grinding technologies in cement grinding and description of the operating principles of the related equipments and comparisons over each other in EnergyEfficient Technologies in Cement GrindingEffect of clinker grinding aids on flow of cementbased materials Materials Industrial clinker used for the production of ASTM C150 Type I cement [4], , odorless, and has a brown color and viscosity of 85 cP 32 Production of Effect of clinker grinding aids on flow of cement 2024年11月19日 Clinker Grinding Mill Manufacturer — With its rich experience of decades, these plants utilize industrial waste from surrounding cities, contributing to energy conservation and emission reduction and bringing monetary benefits Sl No: Qty LIST OF EQUIPMENT: 1: 3: FEED HOPPER: 2: 3: SLIDE GATE: 3: 2: WEIGH BELT FEEDER (for Clinker Grinding Mill Manufacturer Technomart Engineers
.jpg)
GRINDING ABILITY OF UNPROCESSED AND PROCESSED CLINKER
Keywords: cement factory, grinding systems, ball mill, grinding ability, fineness of the material, residue, specific energy, energy efficiency 1 Introduction In the last period, a new concept of clinker grinding has emerged, which achieves a reduction in electricity consumption The process consists of passing theFurthermore, proper grinding of clinker produces fine Blaine at first place and reduces the need for recycling of coarse grains Keywords: Clinker; Cement; Blaine; grinding process; Ball mill speed; Air Classifier speed Research Article Effects of Mill Speed and Air Classifier Speed on Performance of an Industrial Ball Mill Fazeel Ahmad*Effects of Mill Speed and Air Classifier Speed on Performance of Industrial experience has proven that due to the design of grinding parts and the high efficiency separator the OK mill, Figure 3, adequately addresses all the difficult grinding conditions associated with fine grinding of cement clinker and related products, enabling a high grinding efficiency and stable operationCement grinding Vertical roller mills VS ball mills2012年5月1日 Request PDF An industrial comparative study of cement clinker grinding systems regarding the specific energy consumption and cement properties This paper is concerned with a comparative An industrial comparative study of cement clinker grinding
.jpg)
Quantifying the effect of clinker grinding AIDS under laboratory
2015年7月31日 Hence, industrial grinding generated narrow cement PSD curves as a result of enhanced the effect of clinker grinding aids (GAs) on mill performance and cement properties was also studied First industrial referenc e for a polysius® booster mill to reduc e clinker fac tor To reduc e the clinker fac tor of c ement produc ed in its plant of Ouagadougou, Burkina Faso, Ciments d'Afrique (CIMAF) has entrusted thyssenkrupp Industrial Solutions AG, BU Polysius, to First industrial reference for a polysius® booster mill to reduce ISSN 2319 2119 RESEARCH ARTICLE H AAffum et al, The Experiment, 2014, Vol22 (4),15541559 1555 experimentjournal The aim of this study is to determine the hydrodynamic characteristics of an industrial clinker grinding mill and consequently model theCOMPARTMENTAL MODELLING OF FLOW IN A CLINKER GRINDING MILLDownload scientific diagram Various stages during industrial closedcircuit grinding tube mill from publication: Industrial versus Laboratory Clinker Processing Using Grinding Aids (Scale Various stages during industrial closedcircuit
.jpg)
Research Article Industrial versus Laboratory Clinker Processing
Clinker Rejects feed Fresh Ball grinding mill F : Various stages during industrial closedcircuit grinding tube mill T : Design parameters for the tube ball mill and separatorThe polysius® booster mill, a dry agitated bead mill, has been in development by a cooperation between Netzsch Feinmahltechnik and thyssenkrupp for several years, with the original target application in very fine cement grinding polysius® booster mill2021年6月29日 Five speed levels used in closed cycle grinding mill are 200, 400, 600, 800 and 1000 rpm Industrial versus Laboratory Clinker Processing Using Grinding Aids (Scale Effect)Effects of Mill Speed and Air Classifier Speed on Performance of 2015年12月15日 Yet, it is important to note that the decrease in Ec due to GA is around twofold higher when grinding was performed in industrial mill, as compared to laboratory mill For example, the decrease in Ec varied from 1792% to 1254% when industrial grinding was realized using the glycol or aminebased GA, respectivelyIndustrial versus Laboratory Clinker Processing Using Grinding
.jpg)
Cement Grinding Unit Clinker Grinder AGICO Cement
Cement grinding unit is also called the cement grinding plant It consists of cement ball mill, dust collector, belt conveyor, bucket elevator, cement silo, powder concentrator, etc AGICO provides highquality clinker grinders and advanced cement grinding technologyThe annual cement consumption in the world is around 17 billion tonnes and is increasing by 1% every year []Cement industries consume 5% of the total industrial energy utilised in the world []A total of 40% of the total energy consumption of a cement plant is used in clinker grinding in a ball mill to produce the final cement product [] Predictive Controller Design for a Cement Ball Mill Grinding 25195tph clinker grinding plant, best option for start up at low cost Cement clinker grinding unit with ball mill, roll press or VRM 24×7 Consulting SupportCement Clinker Grinding Plant ball mills supplier2012年5月1日 This paper is concerned with a comparative analysis of modern cement grinding systems, namely, combined grinding (Comflex®), highpressure roll mill (HPRM) grinding, and horizontal roller mill (Horomill®) grinding Cement production trials were run with these grinding systems in the same cement plant by using the same clinker/gypsum feed to produce cements An industrial comparative study of cement clinker grinding
.jpg)
Effect of Grinding Conditions on Clinker Grinding Efficiency: Ball
2024年7月31日 The production of cement, an essential material in civil engineering, requires a substantial energy input, with a significant portion of this energy consumed during the grinding stage This study addresses the gap in the literature concerning the collective impact of key parameters, including ball size, feed rate, and mill speed, on grinding efficiency Nine spherical