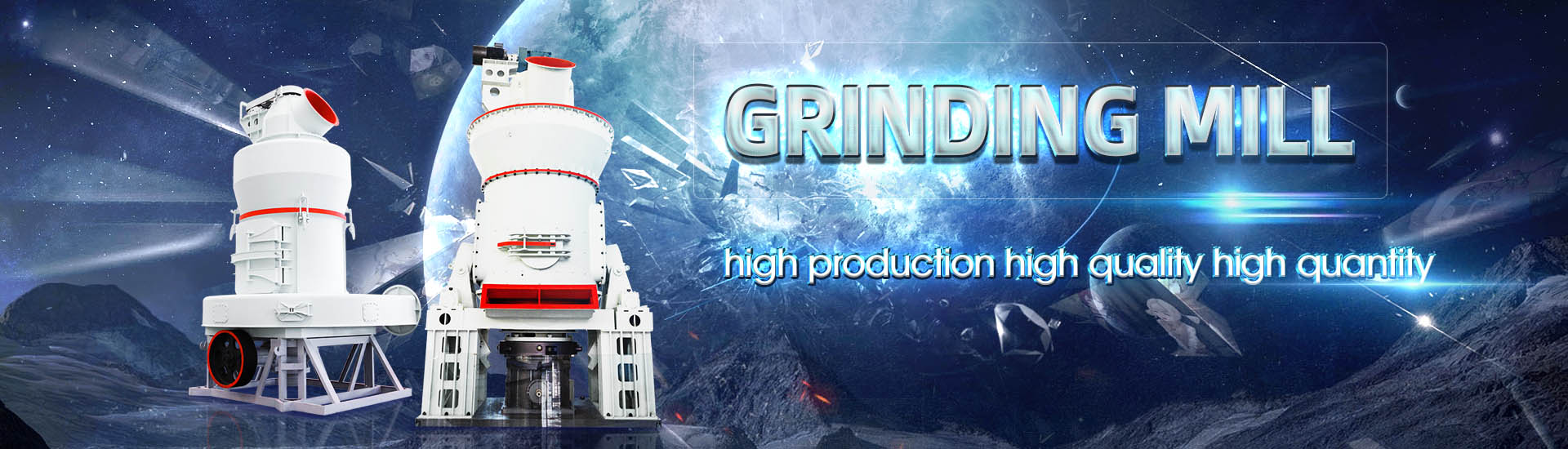
What is the pressure at which cement production coal enters the coal mill
.jpg)
Coal Mill – Coal Mill In Cement Plant AGICO Cement
The coal mill grinding system is an important part of the dry process cement manufacturing In cement plants, we usually adopt the air swept coal mill system or vertical mill system as the pulverized coal preparation system, which is Fine coal leaves the mill with the gas stream, the coal fineness is adjusted by altering the angle of the separator vanes, or the rotor speed Coal drying is ensured by controlling the coal mill inlet COAL PREPARATION AND FIRING INFINITY FOR CEMENT The most used coal mills in cement plants are airswept ball mills and vertical roller mills At present, most cement plants use coal as the main fuel in the clinker production process The standard coal consumed by the new dry process for Coal Mill in Cement Plant Vertical Roller Mill Air 2016年3月1日 Coal provides around 90% of the energy consumed by cement plants around the world, despite the environmental harm caused by its combustion It takes 200 450kg of coal Coal for cement: Present and future trends
.jpg)
Coal Mill an overview ScienceDirect Topics
Coal mills or pulverizers play a very essential part in the coalfired power production system Coal mills grind the coal into fine powder, and the primary air entering the mill dries and drives the The continued application of pressure causes a sequence of reactions referred to as “coalification”, and the degree to which this process takes place defines the nature of the coal The degree of alteration is referred to as “rank”, highrank Cement Plants: CoalMost commonly used mills for coal grinding in cement plants are closed circuit air swept (Single chamber) ball mills and vertical mills Ball Mill: Single chamber ball mills (with classifying liners Coal Grinding Cement Plant OptimizationAirswept coal mill is the main equipment of cement plant, also called coal mill in cement plant, used for grinding and drying various hardness of coal, crushing the coal briquette into pulverized coal It is the important auxiliary equipment of Coal Mill In Cement Plant, Airswept Coal Mill Coal Mill
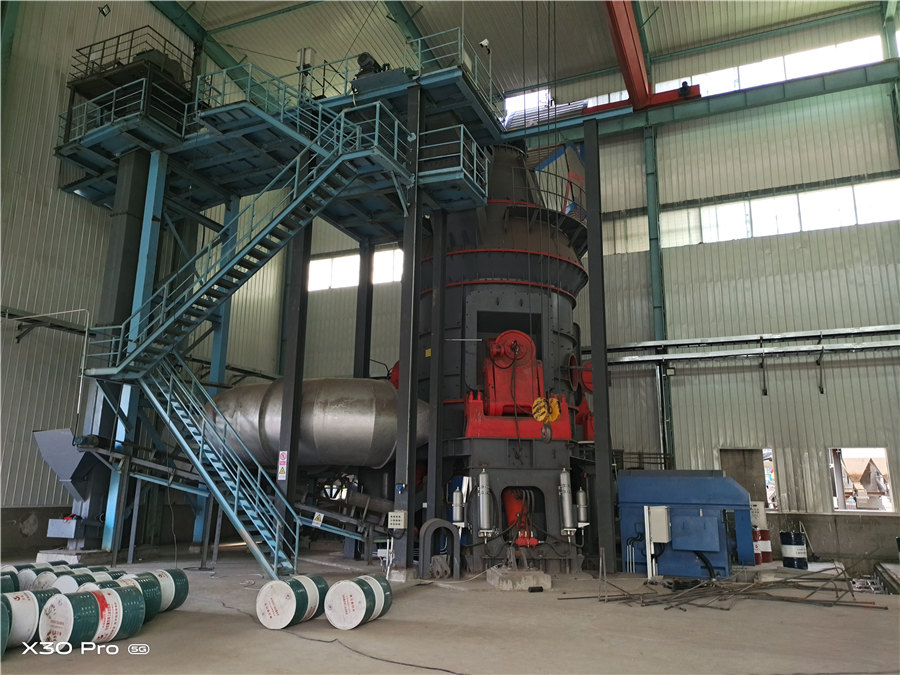
cement, concrete World Coal Association EnergyBC
What is Cement? Cement is made from a mixture of calcium carbonate (generally in the form of limestone), silica, iron oxide and alumina A hightemperature kiln, often fuelled by coal, heats A coal mill is also called a coal pulverizer or coal grinder It is a mechanical device used to grind raw coal into pulverized coal powders The most used coal mills in cement plants are airswept ball mills and vertical roller mills At present, most Coal Mill in Cement Plant Vertical Roller Mill Air Coal Mill Safety In Cement Production Industries It may come as a surprise, The risk of explosions is more or less reduced to an explosion inside the mill, which therefore needs to be explosion, pressure, and shockresistant NFPA Coal Mill Safety In Cement Production IndustriesAirswept coal mill is the main equipment of cement plant, also called coal mill in cement plant, used for grinding and drying various hardness of coal, crushing the coal briquette into pulverized coalIt is the important auxiliary equipment of Coal Mill In Cement Plant, Airswept Coal Mill Coal
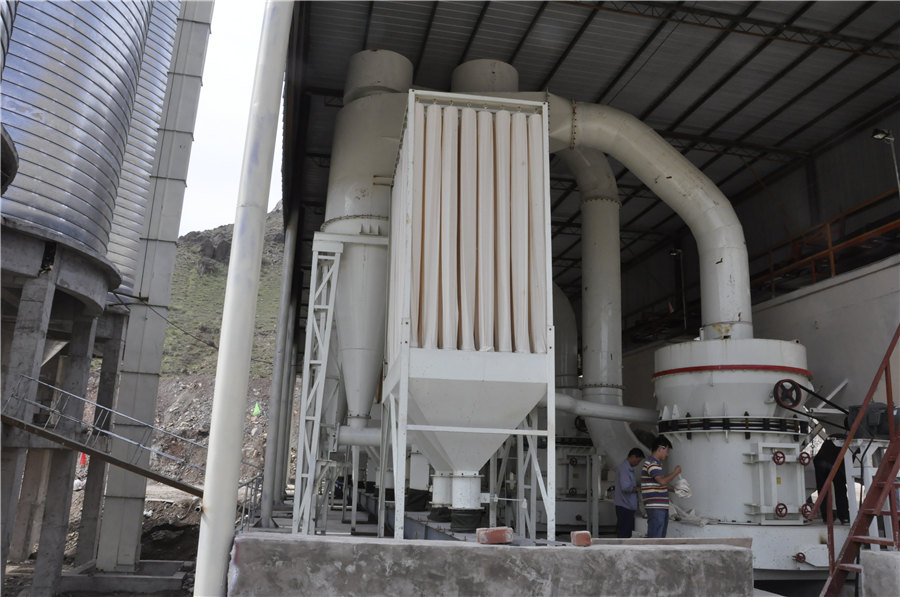
Coal and its application in the cement production process
2021年8月29日 A year, factories usually have to produce about 800,000 tons of clinker, if in the past they had to use more than 136,000 tons of 4A bran coal, now thanks to the application of the solution of using coal oxide in the production of rotary kiln cement clinker, it only takes about approx 120,000 tons of 4A coal bran, the numbers themselves have shown the effectiveness 2024年8月31日 In the realm of cement production, understanding the role of coal is crucial for assessing its impact on both the environment and production efficiencyCement, an essential construction material, is traditionally produced using a combination of raw materials, energy sources, and processing techniquesThis article provides an indepth exploration of whether Is Coal Needed for Cement Production? A Comprehensive AnalysisClinker production is the most energyintensive stage in cement production, accounting for over 90% of total industry energy use Clinker is produced by pyroprocessing in kilns These kiln systems evaporate the free water in the meal in preheater cyclone, calcite the carbonate constituents (calcination) in calciner, and form Portland cement minerals (clinkerization) in Cement Manufacturing Process INFINITY FOR CEMENT EQUIPMENT2024年6月1日 Over the past few decades, cement production has witnessed significant growth due to increasing urbanization, population growth and infrastructure development in many regions The global cement production worldwide from 1995 to 2022 is shown in Fig 2Decarbonising cement and concrete production: Strategies,
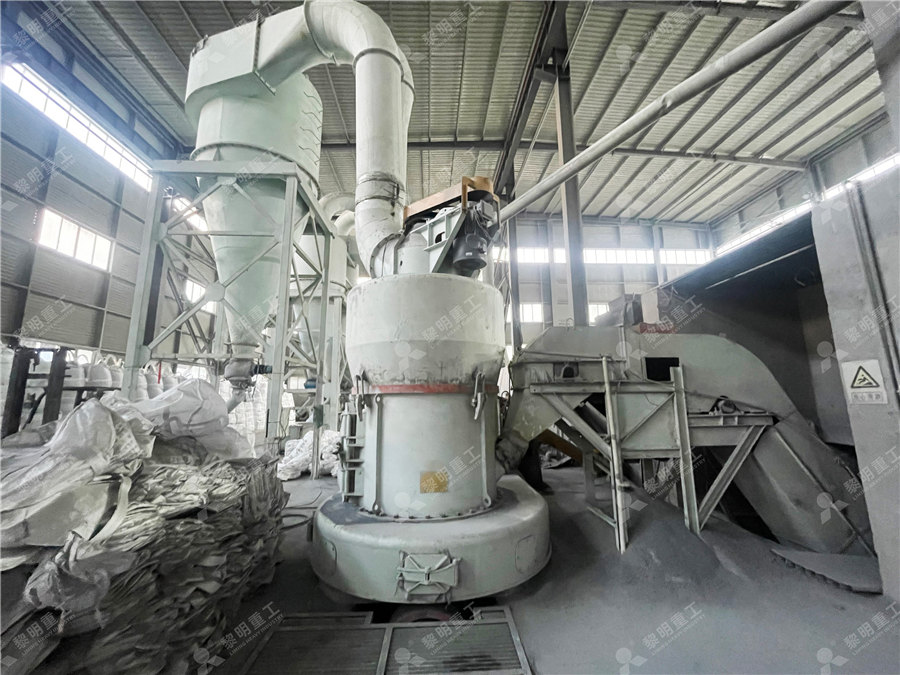
Cement Plants: Coal
London coal gas production began in 1813 and by 1842 was producing 300,000 tons of coke a year, so coke was also readily available, and, being essentially a waste product, was cheaper than coal Early cement plants used coal for drying slurry and for 343 Cement production Cement production is one of the largest CO 2emitting industries globally, with the US contributing 643 MMT of CO 2 in 2014 [38] In 2014, the US produced 826 MMT of cement while the world produced a total of 4180 MMT China accounts for the majority of production, claiming 596% of global cement productionCement Production an overview ScienceDirect TopicsPortland cement clinker was first made (in 1825) in a modified form of the traditional static lime kiln [2] [3] [4] The basic, eggcup shaped lime kiln was provided with a conical or beehive shaped extension to increase draught and thus obtain the higher temperature needed to make cement clinkerFor nearly half a century, this design, and minor modifications, remained the only Cement kiln WikipediaREFORMS ACHIEVEMENTS OF MINISTRY OF COAL SINCE 2014 COAL PRODUCTION Through sustained programme of investment and greater thrust on application of modern technologies, it has been possible to raise the All India production of coal at 89319 million tonnes in 202223The all India Production of coal during 202324 was 99783 MT with a positive Ministry of Coal, Government of India
.jpg)
Raw mill Cement Plant
Raw mill is generally called cement raw mill, raw mill in cement plant, it refers to a common type of cement equipment in the cement plantIn the cement manufacturing process, raw mill in cement plant grind cement raw materials Coalfired power generation plants are most commonly based on pulverised coal combustion (PCC) systems, in which heat from combustion of the coal is used to raise high pressure superheated steam that drives a steam turbine generator Steam turbine plants have been in use for over a hundred years, and have reached supercritical conditions withUnderstanding coalfired power plant cycles ICSCsharp decline in cement production over the last 15 years, from a peak of 262Mt in 2007 to 168Mt in 2017, equivalent to a reduction in cement per capita from 05 to 03 tonnes per person (3) The CO 2 intensity of cement production over that period has improved by about 7% (06t of CO 2 emitted per tonne of cement in 2017) (2)Deep decarbonisation of industry: The cement sector EuropaCoal Mill Safety parameters: Position of Explosion vents Operational readiness of quick shutoff dampers Inertization section readiness (N2, CO2 pressure in bars) Mill Inlet Temperature (0 C) Mill Outlet, bag filter Provisions for drop test for calibration of weigh feeders are commonly available in cement plants to validate production Coal Grinding Cement Plant Optimization
.jpg)
Coal: Past, Present, and Future Sustainable Use ScienceDirect
2020年1月1日 Coal is mainly used for the electricity generation and commercial heating—in 2016, this took up 653% of the primary coal usage globally Other sectors of usage for coal include iron and steel production, cement manufacturing, and as a feedstock for liquid fuel2019年4月18日 This chapter describes the process of coalification, which gradually turns plant debris into coal, involving heat, pressure and the effects of time coke production) In coal, many constituting compounds can be recognized, which are similar to minerals in a rock These constituents are called macerals The Origin and Classification of Coal SpringerLink2020年6月16日 Prediction of the Cement Grate Cooler Pressure in the Cooling Process Based on a MultiModel Fusion Neural Network(PDF) Prediction of the Cement Grate Cooler Pressure in the For a cement mill: intermediate or outlet diaphragm For the case of; cement mills with a drying chamber see raw mills Mill working conditions: ventilation air speed through the mill Bigger or smaller than 12 [m/s] Material abrasivity The [%] of slag or pouzzolana content on the fresh mill feed for cement grindingEverything you need to know about clinker/cement Grinding
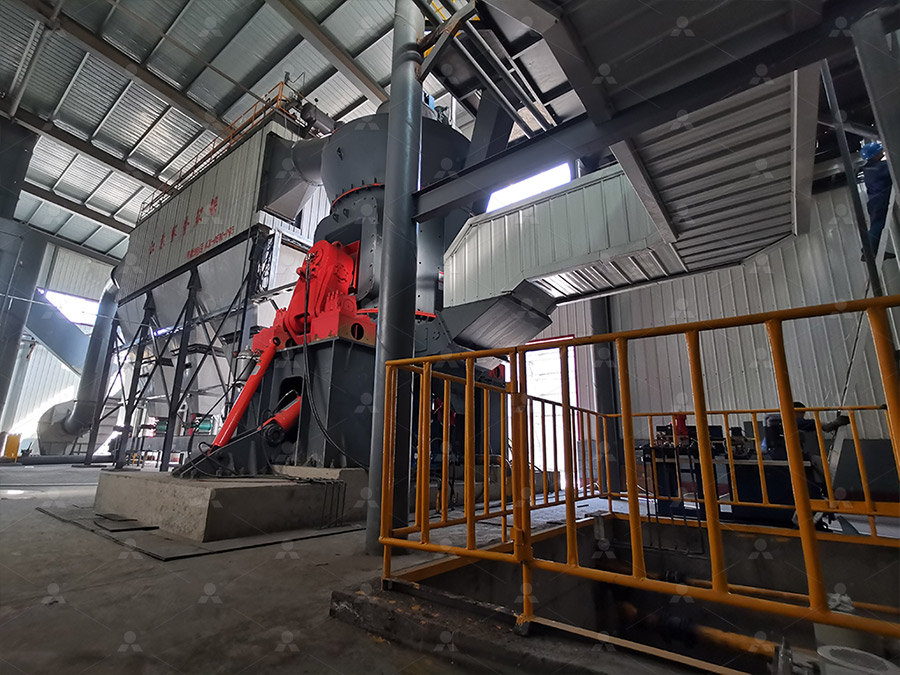
HOW ELECTRICITY IS PRODUCED AT A COALFIRED POWER
and then to the power station site The purpose of the coal stockyard is to ensure that there is sufficient coal reserves available to keep the power station in operation should the mine experience production problems Inside the power station, the coal is pulverised to a fine powder in giant grinding mills This isIn the current practice, onestring preheaters are usually proposed for a production rate of up to 50006000 ton/day A twostring preheater is recommended for production rates higher than 6000 ton/day For production Everything you need to know about Preheaters and 2014年6月9日 Many cement kilns in Russia have yet to be modernised, but the fuel balance will remain in favour of coal once modernisation is completed 2 Historically, Latin America, unlike North America, has not been at the forefront Coal and cement – an intricate relationship World Bituminous coals are dense black solids, frequently containing bands with a brilliant lustre The carbon content of these coals ranges from 78 to 91 percent and the water content from 15 to 7 percent Noncoking bituminous coals are used for power generation, cement making and to provide heat and steam in industryTHE FORMATION OF COAL Eskom
.jpg)
The Cement Manufacturing Process Thermo Fisher Scientific
2023年12月20日 The result is called clinker, which are rounded nodules between 1mm and 25mm across The clinker is ground to a fine powder in a cement mill and mixed with gypsum to create cement The powdered cement is then mixed with water and aggregates to form concrete that is used in constructionIn this episode of the DustSafetyScience Podcast, we interview Vincent Grosskopf, founder of Coal Mill SafetyHe has over 40 years of experience in bulk material handling industries, 25 of which were spent in dust explosion protection through Thorwesten Vent based in Germany He’s been semiretired since 2011 and now does tactical consulting, specifically working with DSS055: Coal Mill Safety In Cement Production Dust Safety 2018年10月10日 1 Introduction Nowadays, cement manufacturing is an energyintensive industry The energy costs of cement industry are about 40% of the product cost that indicates that this sector is one of the biggest CO 2 emitter The global anthropogenic CO 2 emission of cement industry is approximately 5% []The International Energy Agency reported in 2011 that Heat Integration in a Cement Production IntechOpen2023年8月23日 The production process of a cement ball mill involves raw material preparation, grinding, linearization, clinker grinding, and the eventual storage and distribution of the finished cement product This process is integral to the production of cement, a vital building material that plays a central role in construction and infrastructure development around the worldWhat Are the Parts of a Cement Mills? Cement Ball Mill Production
.jpg)
Coal's Importance to the World Society for Mining, Metallurgy
The primary source of this carbon is coking coal 17 Cement – Coal provides around 90% of the energy consumed by cement plants around the world It takes 200 450kg of coal to produce 1 ton of cement The cement industry consumes around 4% of global coal production, around 330Mt/yr 18 Cement is an important commodity for building wind turbines2016年10月5日 1 Introduction Cement is an energyintensive industry in which the grinding circuits use more than 60 % of the total electrical energy consumed and account for most of the manufacturing cost []The requirements for the cement industry in the future are to reduce the use of energy in grinding and the emission of CO 2 from the kilns In recent years, the production EnergyEfficient Technologies in Cement Grinding IntechOpenAdvantages of air swept coal mill The feeding device of the airswept coal mill adopts a louvertype structure with oblique air intake, which enhances the heat exchange capacity of the mill and can effectively prevent material blocking at the entrance of the coal mill; optimize the support system, improve the lubrication structure, and reduce system resistanceAir Swept Coal Mill Cement Plant MachineryA coal mill is also called a coal pulverizer or coal grinder It is a mechanical device used to grind raw coal into pulverized coal powders The most used coal mills in cement plants are airswept ball mills and vertical roller mills At present, most Coal Mill in Cement Plant Vertical Roller Mill Air
.jpg)
Coal Mill Safety In Cement Production Industries
Coal Mill Safety In Cement Production Industries It may come as a surprise, The risk of explosions is more or less reduced to an explosion inside the mill, which therefore needs to be explosion, pressure, and shockresistant NFPA Airswept coal mill is the main equipment of cement plant, also called coal mill in cement plant, used for grinding and drying various hardness of coal, crushing the coal briquette into pulverized coalIt is the important auxiliary equipment of Coal Mill In Cement Plant, Airswept Coal Mill Coal 2021年8月29日 A year, factories usually have to produce about 800,000 tons of clinker, if in the past they had to use more than 136,000 tons of 4A bran coal, now thanks to the application of the solution of using coal oxide in the production of rotary kiln cement clinker, it only takes about approx 120,000 tons of 4A coal bran, the numbers themselves have shown the effectiveness Coal and its application in the cement production process2024年8月31日 In the realm of cement production, understanding the role of coal is crucial for assessing its impact on both the environment and production efficiencyCement, an essential construction material, is traditionally produced using a combination of raw materials, energy sources, and processing techniquesThis article provides an indepth exploration of whether Is Coal Needed for Cement Production? A Comprehensive Analysis
.jpg)
Cement Manufacturing Process INFINITY FOR CEMENT EQUIPMENT
Clinker production is the most energyintensive stage in cement production, accounting for over 90% of total industry energy use Clinker is produced by pyroprocessing in kilns These kiln systems evaporate the free water in the meal in preheater cyclone, calcite the carbonate constituents (calcination) in calciner, and form Portland cement minerals (clinkerization) in 2024年6月1日 Over the past few decades, cement production has witnessed significant growth due to increasing urbanization, population growth and infrastructure development in many regions The global cement production worldwide from 1995 to 2022 is shown in Fig 2Decarbonising cement and concrete production: Strategies, London coal gas production began in 1813 and by 1842 was producing 300,000 tons of coke a year, so coke was also readily available, and, being essentially a waste product, was cheaper than coal Early cement plants used coal for drying slurry and for Cement Plants: Coal343 Cement production Cement production is one of the largest CO 2emitting industries globally, with the US contributing 643 MMT of CO 2 in 2014 [38] In 2014, the US produced 826 MMT of cement while the world produced a total of 4180 MMT China accounts for the majority of production, claiming 596% of global cement productionCement Production an overview ScienceDirect Topics
.jpg)
Cement kiln Wikipedia
Portland cement clinker was first made (in 1825) in a modified form of the traditional static lime kiln [2] [3] [4] The basic, eggcup shaped lime kiln was provided with a conical or beehive shaped extension to increase draught and thus obtain the higher temperature needed to make cement clinkerFor nearly half a century, this design, and minor modifications, remained the only