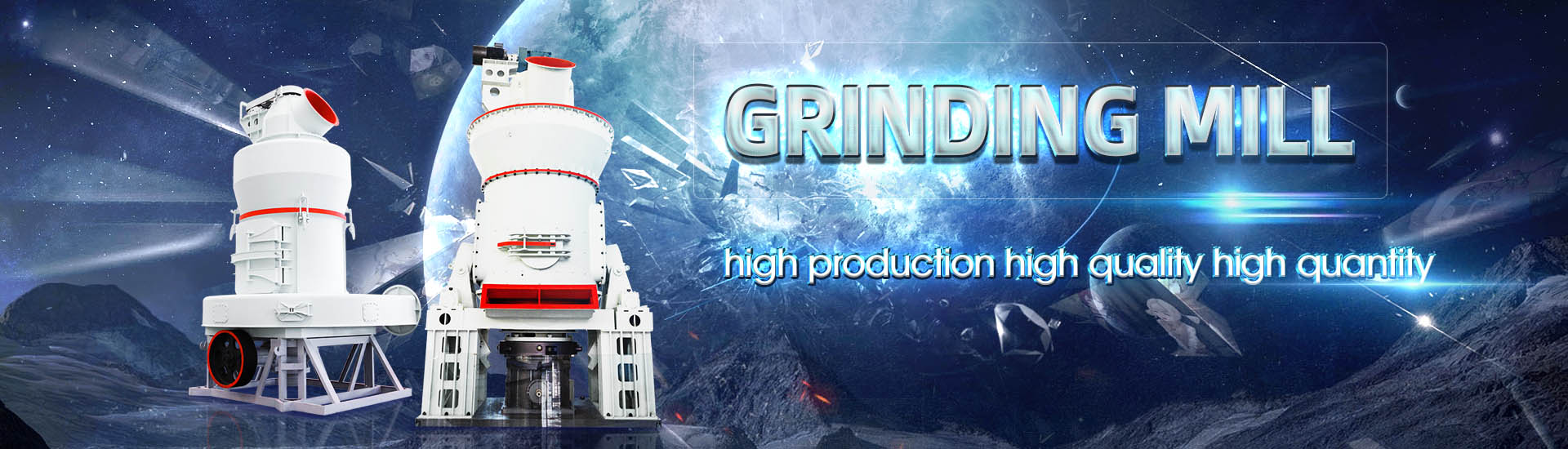
Ball mill quicklime solution 2*13 meters
.jpg)
COMPLETE PLANT CAPABILITY LIME SYSTEMS LTD
Lime Systems manufactures a range of packaged roller mounted ball mills suitable for quicklime slaking and regrind applications The mills range from 600mm diameter for laboratory batch HighEfficiency Ball Mill for Quicklime and Fly Ash Processing, Find Details and Price about Industrial Ball Mill High Efficiency Grinding Mill from HighEfficiency Ball Mill for Quicklime and HighEfficiency Ball Mill for Quicklime and Fly Ash Processing2015年6月19日 The basic parameters used in ball mill design (power calculations), rod mill or any tumbling mill sizing are; material to be ground, characteristics, Bond Work Index, bulk density, specific density, desired mill Ball Mill Design/Power Calculation 911MetallurgistTongli Heavy Machinery It was first established in 1958 After working hard for more than 65 years, Tongli has owned the firstclass science and technology development centers and craftsmen team with much experience and skilled technology, especially in manufacturing series of cement production equipment such as rotary kiln, ball mill, vertical roller mill, etcABOUTTongli Machinery
.jpg)
Ball Mill Liner Design 911Metallurgist
2016年1月5日 For 60 mm (25″) and smaller top size balls for cast metal liners use double wave liners with the number of lifters to the circle approximately 131 D in meters (for D in feet, divide 131 D by 33)Cement Ball Mill Structure When Ball Mill is working, raw material enters the mill cylinder through the hollow shaft of the feed The inside of the cylinder is filled with grinding media of various diameters (steel balls, steel segments, etc); when the cylinder rotates around the horizontal axis at a certain speed, Under the action of centrifugal force and friction force, the medium and the Ball Mill for Cement Grinding Process2017年10月26日 The following are factors that have been investigated and applied in conventional ball milling in order to maximize grinding efficiency: a) Mill Geometry and Speed – Bond (1954) observed grinding efficiency to be a function of ball mill diameter, and established empirical relationships for recommended media size and mill speed that take this factor into Factors Affecting Ball Mill Grinding EfficiencyA survey of Australian processing plants revealed a maximum ball mill diameter of 524 meters and length of 884 meters (Morrell, 1996) Autogenous mills range up to 12 meters in diameter The lengthtodiameter ratios in the previous table are for normal applicationsAMIT 135: Lesson 7 Ball Mills Circuits – Mining Mill Operator
.jpg)
Ball Mills Lime Systems
We provide rollermounted ball mills designed to cater to various grinding applications and accommodate a range of grinding media Our ball mills are capable of handling tonnages exceeding 20TPH of dry feed per train, contingent upon the specific attributes of the feed materialMill Shell:The foundation of the Slag ball mill, the mill shell, is a cylindrical structure made of premiumgrade steelTongli heavy machinery is equipped with a large annealing furnace of 65x65x20m and a 65x65x20m large sandblasting room, which can conduct overall heat treatment and sandblasting on the ball mill to ensure the service life and appearance of the slag grinding ball mill Manufacturer Tongli Machinery2012年6月1日 solution to the batch grinding equation and can be found in ball mill, sump and classifier [10, 13, 33, 39] efficiency of the ball mill and the economic assessment of the process controlGrinding in Ball Mills: Modeling and Process ControlMill Shell: The foundation of the large ball mill, the mill shell, is a cylindrical structure made of premiumgrade steel Tongli heavy machinery is equipped with a large annealing furnace of 65x65x20m and a 65x65x20m large sandblasting room, which can conduct overall heat treatment and sandblasting on the ball mill to ensure the service life and appearance of the Large Ball Mill For Sale Manufacturer Tongli Machinery
.jpg)
Understanding Ball Mill Parts: Essential Components for Effective
2024年5月17日 A ball mill is a type of grinder used to grind and blend materials for use in various industrial applications It operates on the principle of impact and attrition, where the grinding media (usually steel balls) are used to break down the materialMill Shell: The foundation of the conical ball mill, the mill shell, is a cylindrical structure made of premiumgrade steel Tongli heavy machinery is equipped with a large annealing furnace of 65x65x20m and a 65x65x20m large sandblasting room, which can conduct overall heat treatment and sandblasting on the ball mill to ensure the service life and appearance of the Conical Ball Mill And Design Manufacturer Tongli MachineryTurnkey solutions for lime calcination High active Vertical Roller Mill Final Grinding Plant; Ball Mill Roller Press Combined Grinding Plant; VRM Ball Mill Combined Grinding System; Cement and carbon dioxide The calcination temperature is about 900℃1100℃ The chemical reaction: CaCO3(Limestone)→CaO (quicklime)+CO2(carbon Lime Calcination Plant Solution 2001000tpd Quicklime CNBM The vertical mill, also known as the vertical roller mill, has emerged as a leading piece of equipment for the production of quicklime due to its advanced technology and operational excellence 2 Features of the Vertical Mill Grinding Principle The vertical mill operates based on the principle of material bed grindingVertical mill: The preferred equipment for quicklime production
.jpg)
17 Signs of Problems with Ball Mills: Quickly Remove Hidden Troubles
2023年2月15日 What should we do to solve those problems? 1 First of all, it is necessary to do analyses including changes of nature of the ore, whether the amount of ore, water, sand and overflow size are normal Then do the measures to deal with them 2 Reduce the amount of feed to the mill until the working state of the ball mill returns to normal; 3 Appropriately reduce the Ball mill girth gear Rotary kiln thrust roller Ball mill trunnion Rotary kiln pinion Ball mill head Rotary kiln roller shaft Ball mill bearing bush Rotary kiln bearing housing Ball mill bearing housing ManufacturerFactory Rotary kiln spring plate ManufacturerFactory Ball mill transmission connection ManufacturerFactoryBall Mill Rotary Kiln Vertical Roller Mill Manufacturer Tongli The proven classical option for cement grinding Whether employed as a twocompartment separator mill in an independent grinding system, or in combination with a high pressure grinding roll, the Ball Mill is a robust and reliable alternative for cement and granulated blast furnace slag grinding Used in combination with the sepol® highefficiency separator, ball mills can reliably Ball Mill thyssenkrupp PolysiusSolutions offers solutions to suit your every need The ball mill that best suits your respective application depends on many factors, including feed grain size, grindability, moisture and drying properties In conjunction with our customers, we analyze the requirements and together develop the optimum plant configuration 2Industrial Solutions polysius ball mills ThyssenKrupp
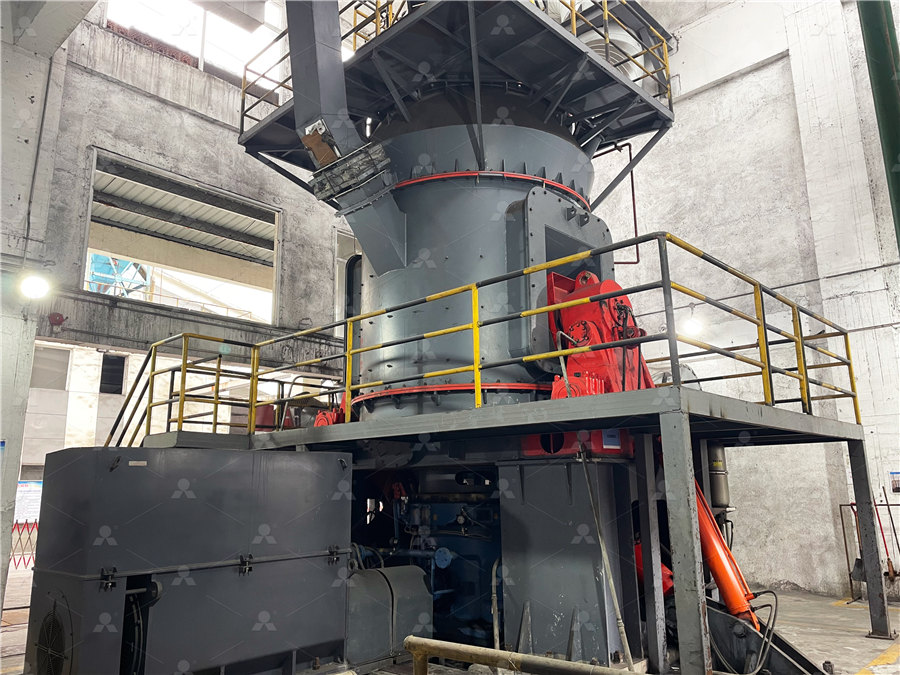
Technical specifications and selection guide for ball mills
2 Selection Guide: When selecting a ball mill, several factors should be taken into consideration to ensure the appropriate mill for the desired application: Application: Consider the type of materials to be processed and the desired particle size Different ball mills may be more suitable for certain materials and particle size requirementsTongli is a professional manufacturer and supplier of ball mills We provide highquality service and aftersales support We offer ball mills in different sizes and specifications to meet the diverse needs of our customers Whether you require bulk purchases or customized production, we can provide the best solutions Our products undergo strict quality control to ensure excellent Ball Mill For Sale Manufacturer Supplier Factory Tongli MachinerySQM2 is a compact highspeed ball mill with the 3D movement for making the small quantity of samples at easy and fast It has higher impact energy created by rotation, vibration, and oscillation with frequency up to 1000RPM with a two Highspeed Vibration Ball Mill SQM2 Chuanghe Lab2016年10月20日 Concrete may be made up in different mixtures having different proportions of sand and aggregate These are expressed in parts – for example a 1:2:4 mixture indicates one bag of cement, 2 cubic feet of sand, and 4 cubic Ball Mill Maintenance Installation Procedure
.jpg)
Ball mill Wikipedia
A section cutthrough of ball mills A ball mill is a type of grinder filled with grinding balls, used to grind or blend materials for use in mineral dressing processes, paints, pyrotechnics, ceramics, and selective laser sinteringIt works on the principle of impact and attrition: size reduction is done by impact as the balls drop from near the top of the shellCement mills are the milling machines used in cement plants to grind hard clinker into fine cement powders Cement ball mill and vertical roller mill are two most widely used cement mills in today’s cement grinding plants and are also the main types of cement mill we produce As a professional cement equipment manufacturer, AGICO has rich experience in the designing and Cement Mill for Sale Buy Cement Ball Mill Vertical Roller Mill 2020年10月1日 Kajian Produksi Ball Mill Dalam Menentukan Efektivitas Penggerusan Bijih Timah Primer Di CV Persada Tambang Intitama TK 4218 Paku Kabupaten Bangka Selatan October 2020 MINERAL 5(2):16(PDF) Kajian Produksi Ball Mill Dalam Menentukan Efektivitas Vertical roller mill: The cement vertical roller mill has become a popular choice for grinding raw materials in the cement industry due to its significant advantages over traditional ball mill systems, compare to the traditional cement ball mill, it is more energyefficient and can be exposed outsideThe main components of the cement vertical roller mill include the grinding table, Close circuit Cement grinding plantSOLUTIONTongli Machinery
.jpg)
Rotary Kiln High Quality Manufacturers Tongli Machinery
Rotary kiln is widely used in the manufacturing processes of industries such as cement, metallurgy, and chemical We offer a wide range of specifications and models of rotary kilns to meet the diverse needs of our customers We support OEM/ODM production and have experienced manufacturing and aftersales teams We are currently selling multiple models of 2008年10月22日 Request PDF Ball MillAssisted Dechlorination of Flexible and Rigid Poly(vinyl chloride) in NaOH/EG Solution [13], and with organic NaOH solutions under atmospheric pressure Ball MillAssisted Dechlorination of Flexible and Rigid Poly(vinyl A ball is thrown from an initial height of 2 meters with an initial upward velocity of 15 m/s The ball's height h (in meters) after t seconds is given by the following h=2+15t512 Find all values of t for which the ball's height is 10 meters Round your answer(s) to the nearest hundredthSolved A ball is thrown from an initial height of 2 meters Chegg2015年6月19日 The basic parameters used in ball mill design (power calculations), rod mill or any tumbling mill sizing are; material to be ground, characteristics, Bond Work Index, bulk density, specific density, desired mill Ball Mill Design/Power Calculation 911Metallurgist
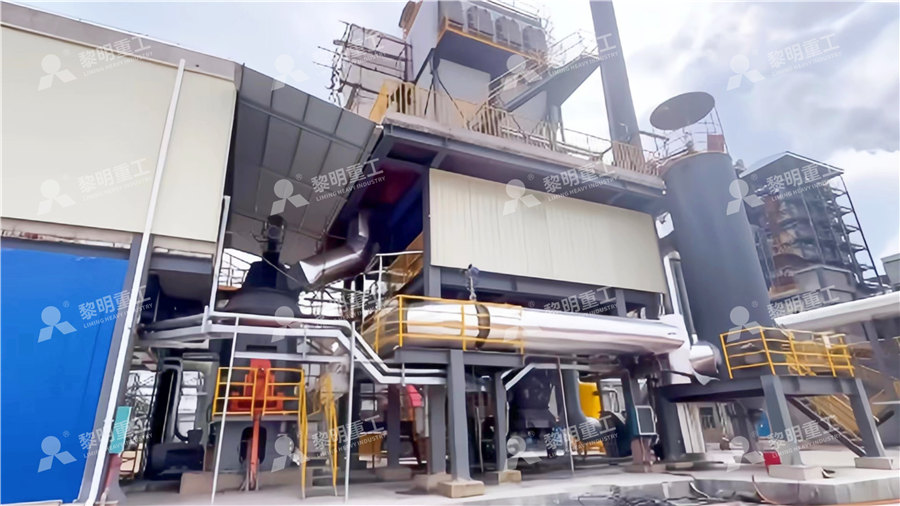
ABOUTTongli Machinery
Tongli Heavy Machinery It was first established in 1958 After working hard for more than 65 years, Tongli has owned the firstclass science and technology development centers and craftsmen team with much experience and skilled technology, especially in manufacturing series of cement production equipment such as rotary kiln, ball mill, vertical roller mill, etc2016年1月5日 For 60 mm (25″) and smaller top size balls for cast metal liners use double wave liners with the number of lifters to the circle approximately 131 D in meters (for D in feet, divide 131 D by 33)Ball Mill Liner Design 911MetallurgistCement Ball Mill Structure When Ball Mill is working, raw material enters the mill cylinder through the hollow shaft of the feed The inside of the cylinder is filled with grinding media of various diameters (steel balls, steel segments, etc); when the cylinder rotates around the horizontal axis at a certain speed, Under the action of centrifugal force and friction force, the medium and the Ball Mill for Cement Grinding Process2017年10月26日 The following are factors that have been investigated and applied in conventional ball milling in order to maximize grinding efficiency: a) Mill Geometry and Speed – Bond (1954) observed grinding efficiency to be a function of ball mill diameter, and established empirical relationships for recommended media size and mill speed that take this factor into Factors Affecting Ball Mill Grinding Efficiency
.jpg)
AMIT 135: Lesson 7 Ball Mills Circuits – Mining Mill Operator
A survey of Australian processing plants revealed a maximum ball mill diameter of 524 meters and length of 884 meters (Morrell, 1996) Autogenous mills range up to 12 meters in diameter The lengthtodiameter ratios in the previous table are for normal applicationsWe provide rollermounted ball mills designed to cater to various grinding applications and accommodate a range of grinding media Our ball mills are capable of handling tonnages exceeding 20TPH of dry feed per train, contingent upon the specific attributes of the feed materialBall Mills Lime SystemsMill Shell:The foundation of the Slag ball mill, the mill shell, is a cylindrical structure made of premiumgrade steelTongli heavy machinery is equipped with a large annealing furnace of 65x65x20m and a 65x65x20m large sandblasting room, which can conduct overall heat treatment and sandblasting on the ball mill to ensure the service life and appearance of the slag grinding ball mill Manufacturer Tongli Machinery2012年6月1日 solution to the batch grinding equation and can be found in ball mill, sump and classifier [10, 13, 33, 39] efficiency of the ball mill and the economic assessment of the process controlGrinding in Ball Mills: Modeling and Process Control