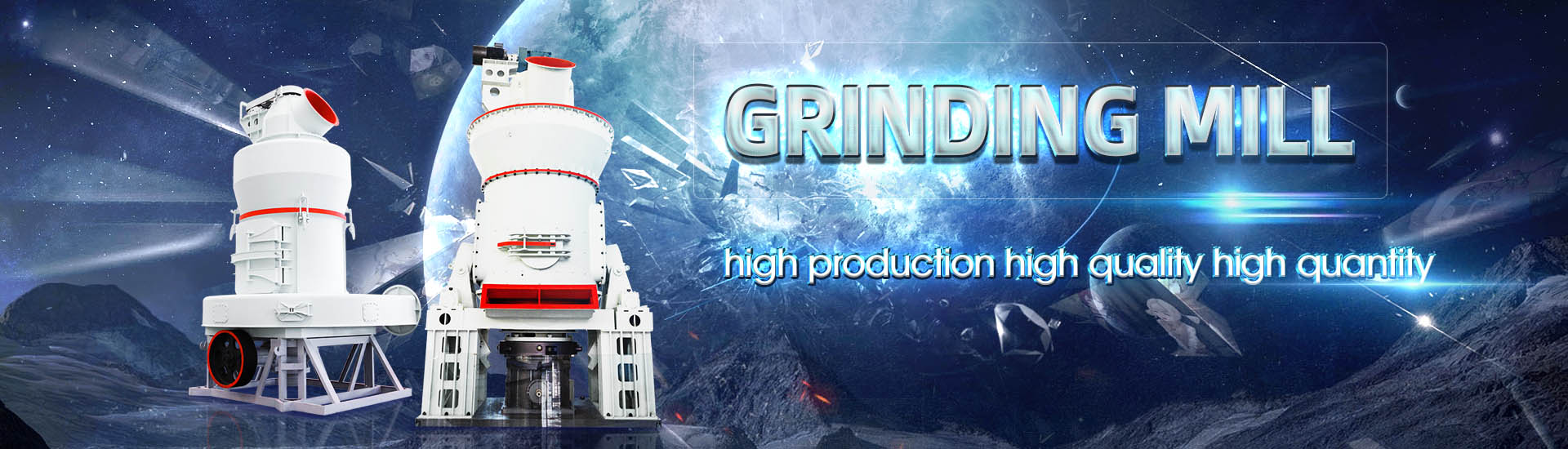
Electrolytic aluminum waste slag mill calcium carbonate crushing station
.jpg)
The recycling of carbonrich solid wastes from aluminum
2024年5月23日 Here, we review carbonrich solid wastes with focus on sources and hazards, detoxification, separation, recovery, recycling and disposal Treatment techniques include Clean process for selective recovery of lithium carbonate from waste lithiumbearing aluminum electrolyte slag Ind Eng Chem Res , 62 ( 2023 ) , pp 14537 14547 , Clean and efficient lithium recovery from waste electrolytes via an 2023年9月1日 This study employed hydrometallurgical processes to selectively leach lithium from Licontaining aluminum electrolyte slag, using sodium carbonate solution as the leaching 从废弃含锂铝电解渣中选择性回收碳酸锂的清洁工艺 2023年4月25日 As the main solid waste of the electrolytic aluminum industry, overhaul slag contains a large amount of hazardous substances, and how to treat it harmlessly and efficiently recover the valuable substances in it has become an urgent problem in the aluminum industry in recent years This article analyzes and summarizes the composition and hazards of the Research Progress of Electrolytic Aluminum Overhaul Slag
.jpg)
Research on the Coprocessing of Mixed Electrolytic Aluminum Waste
Research on the Coprocessing of Mixed Electrolytic Aluminum Waste in Circulating Fluidized Bed Boiler Lei Shi1, grinding the materials with an electric mill, 50 grams of electrolytic aluminum waste samples were sieved to 0075 mm Blending ratio Calcium carbonate/g Condition 1 5:5 0 Condition 2 7:3 0 Condition 3 :7 02022年10月10日 One of the main electrolytic aluminum production costs is the consumption of carbon anodes, and carbon anode slag is a common hazardous waste in the aluminum industryRecovery of carbon and cryolite from spent carbon 2021年10月1日 Aluminum electrolysis of China, solid waste, such as waste aluminum electrolyte, has been largely idled and caused serious environmental pollution In this paper, a novel approach is developed for achieving the separation/recovery of lithium from spent lithiumcontaining aluminum electrolyte by a sodium carbonate roasting–acid leaching processA novel approach for lithium recovery from waste lithium 2022年2月19日 Recycling waste containing rare earth has always been a research hotspot The molten salt electrolysis process of rareearth metals and alloys generates a large amount of waste slag, which contains high rareearth content and, thus, has very considerable recovery value However, the high content of fluorine in rareearth molten salt slag brings challenges to the Recovery of RareEarth Elements from Molten Salt Electrolytic Slag
.jpg)
Efficient lithium recovery from electrolytic aluminum slag via an
2024年2月1日 The electrolytic aluminum industry generates a large amount lithium (Li)containing electrolytic aluminum slag (EAS) annually, and this can result in severe environmental pollution and wasting of Li resources This paper proposes a method for recovering Li from the slag using AlCl 3 as the leaching agent The effects of the leaching temperature, AlCl 3 2023年10月1日 The main components of waste aluminum cryolite electrolyte are cryolite (Na 3 AlF 6), potassium cryolite (K 2 NaAlF 6), lithium cryolite (Na 2 LiAlF 6), fluorite (CaF 2), and approximately 2% carbon black (Wang et al, 2019)The main treatment methods of waste aluminum cryolite electrolyte can be divided into two categories: combined thermalwet Efficient extraction and recovery of lithium from waste aluminum 2024年5月26日 Mineral carbonation is one of the known methods for carbon capture, utilization, and storage (CCUS) Slag from the steel industry is studied as a common source of CaCO3 via mineral carbonation owing to its high Ca content Despite numerous preliminary studies, the optimal factors governing the mineral carbonation of steelmaking slag, such as extraction and Experimental study on indirect mineral carbonation using five 2023年9月1日 Lithium (Li)bearing aluminum electrolyte slag is an inevitable byproduct of the aluminum industry, and improper disposal or stacking it may lead to potential environmental hazards This study employed hydrometallurgical processes to selectively leach lithium from Licontaining aluminum electrolyte slag, using sodium carbonate solution as the leaching agent Clean Process for Selective Recovery of Lithium Carbonate from Waste

Comprehensive performance study of aluminum ash and calcium
2022年12月12日 Based on the research on bulk solid waste contact molding technology by our team [49], the comprehensive performance of pressed bricks with different ratios of aluminum ash and calcium carbide slag was investigated, the ratios of aluminum ash and calcium carbide slag are 9:1 ∼ 1:9 and pure aluminum ash and calcium carbide slag, the pressing pressure is 300 2020年12月1日 The rapid development of the electrolytic aluminum industry in China and the increasing demand for aluminum products have led to the development of many lowgrade bauxite mines with an average Li 2 O content of at least 058% (Wang et al, 2013)Due to the use of this lowgrade bauxite in the electrolytic aluminum process, the content of lithium in the Novel process for the extraction of lithium carbonate from spent 2012年12月31日 The main mineral components of waste cathode carbon include sodium fluoride, cryolite, calcium fluoride, silicate minerals and so on, therein the fluorine content is about 986%, and the content Study on Harmless and Resources Recovery 2022年5月1日 Most widely used acidic agents could react with these carbonates and release CO2 before they were recarbonated After the leaching step, alkaline reagents (eg, NH4OH, NaOH) are introduced to Preparation of calcium carbonate nanoparticles from waste carbide slag
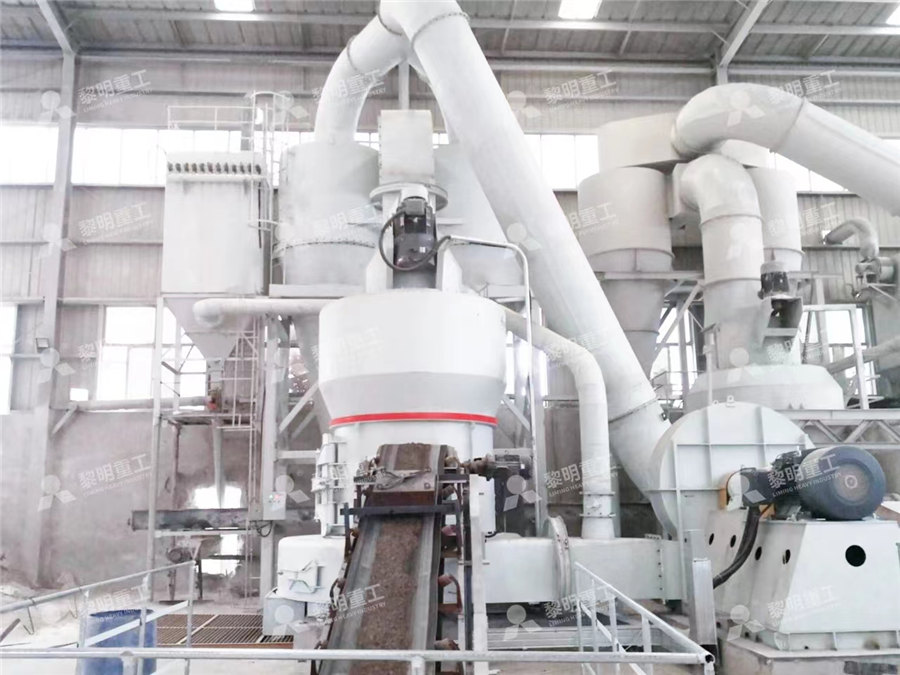
Research on the Coprocessing of Mixed Electrolytic Aluminum Waste
Research on the Coprocessing of Mixed Electrolytic Aluminum Waste in Circulating Fluidized Bed Boiler Lei Shi1, grinding the materials with an electric mill, 50 grams of electrolytic aluminum waste samples were sieved to 0075 mm Blending ratio Calcium carbonate/g Condition 1 5:5 0 Condition 2 7:3 0 Condition 3 :7 02021年10月6日 Secondary aluminum dross is a byproduct of the electrolytic aluminum industry, whose main components are Al2O3, AlN and Na3AlF6 Secondary aluminum dross is a type of hazardous waste, with a Research on the Preparation Parameters and Basic Properties of 2021年10月23日 Three different sources of calcium oxide were used, namely oyster shells, mussel shells and commercial calcium carbonate All these materials were ball milled in water prior to calcination at 500 °C (decomposition of CaCO 3 to CaO) after which the repeated milling in dry environment for 1 min was conductedShells and Other Calcium CarbonateBased Waste2022年2月19日 Recycling waste containing rare earth has always been a research hotspot The molten salt electrolysis process of rareearth metals and alloys generates a large amount of waste slag, which Recovery of RareEarth Elements from Molten Salt Electrolytic Slag
.jpg)
Research on the Preparation Parameters and Basic Properties of
calcium aluminate hydrate, calcium carbonate and hydroxide Mailar et al [20] tried to replace some sintering raw materials with secondary aluminum dross to make refractory2020年1月2日 The invention discloses a fluorineretaining agent for overhaul slag of an aluminum electrolytic cell The fluorineretaining agent comprises the following components of, by mass, 80100 parts of calcium sulfate, 6080 parts of calcium oxide, 5070 parts of calcium hydroxide and 3060 parts of calcium chloride The invention further discloses a method for Fluorineretaining agent for overhaul slag of aluminum electrolytic 2024年6月29日 Aluminum electrolyte is a necessity for aluminum reduction cells; however, its stock is rising every year due to several factors, resulting in the accumulation of solid waste Currently, it has become a favorable material for the resources of lithium, potassium, and fluoride In this study, the calcification roasting–twostage leaching process was introduced to extract Stepwise extraction of lithium and potassium and recovery of Raymond Grinding Precipitated Calcium Carbonate Limestone Machine Price for Sale, Find Details and Price about Mining Machine Grinding Mill from Raymond Grinding Precipitated kaolin, bentonite, flint clay, fluorite, wollastoniteore, Raymond Grinding Precipitated Calcium Carbonate
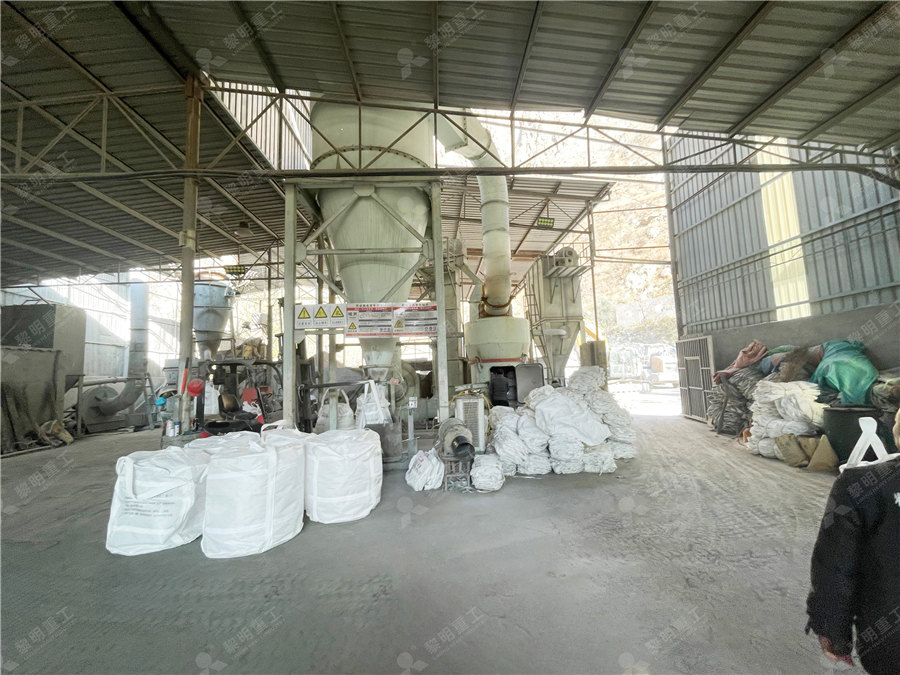
Novel process for the extraction of lithium carbonate from spent
2020年12月1日 The rapid development of the electrolytic aluminum industry in China and the increasing demand for aluminum products have led to the development of many lowgrade bauxite mines with an average Li 2 O content of at least 058% (Wang et al, 2013) Due to the use of this lowgrade bauxite in the electrolytic aluminum process, the content of lithium in the When a jaw crusher is equipped with the ASC system, the crushing forces are carried by massive hydraulic cylinders mounted into the rear header casting If an uncrushable object enters the crusher cavity and crushing forces reach the Slag crushing Metso2023年12月1日 Based on these considerations, the idea of using vegetable waste through natural fermentation to produce organic acids as a substitute for traditional industrial acids, and using them to soak and treat blast furnace slag, is proposed by our team, while the generated WCS would be employed as the Ca source for the synthesis of valueadded amorphous Producing amorphous calcium carbonate using waste Carich 2024年6月1日 Calcinating the slag with calcium oxide and aluminum sulfate at 1173 K achieved fluorine fixation to form rare earth oxides by 69, 70 recovery of waste sulfur slag, 71, 72 recovery of aluminum electrolytic waste residue, 73 Rare earth recovery from fluoride moltensalt electrolytic slag by sodium carbonate roasting REEs recovery from molten salt electrolytic slag: Challenges and

Recovery of carbon and cryolite from spent carbon anode slag of
2022年10月9日 1 Department of Mining Engineering, Shanxi Institute of Technology, Yangquan, China; 2 Department of Mining Engineering, Balochistan University of Information Technology, Engineering and Management Sciences (BUITEMS), Quetta, Pakistan; One of the main electrolytic aluminum production costs is the consumption of carbon anodes, and carbon 2021年5月6日 Every year a million tonnes of calcium rich agro and industrial waste are generated around the whole globe These calcium rich waste like finger citron, shells of cockle, mussel, oysters etc, and egg shell are biological sources which have various organic compounds The inorganic calcium rich waste includes gypsum, dolomite, sludge etc, which are produced The Processing of Calcium Rich Agricultural and Industrial Waste 2024年5月1日 Selective preparation of lithium carbonate from overhaul slag by high temperature sulfuric and plays a theoretical and technological foundation for the recovery of electrolytic aluminum hazardous waste in the future 2 and more than 80% of the grain size of −0074 mm could be obtained without crushing in the leaching Selective preparation of lithium carbonate from overhaul slag by 2024年2月1日 Overhaul slag, as one of the main hazardous solid wastes generated in the electrolytic aluminum, has high research value [12]The electrolytic cell lining is eroded by continuous chemical corrosion of hightemperature molten metal and salt, resulting in expansion and peeling off, leading to low production efficiency and degradation of performance [13]A novel approach for extracting lithium from overhaul slag by low
.jpg)
Sustainable Approaches for LD Slag Waste Management in Steel
2016年5月16日 Reduce, reuse, and recycle are important techniques for waste management These become significant for improving environmental and economic condition of industries Integrated steel industries are generating huge amounts of steel slag as waste through the blast furnace and Linz–Donawitz (LD) process Presently, these wastes are disposed by dumping in 2023年4月25日 As the main solid waste of the electrolytic aluminum industry, overhaul slag contains a large amount of hazardous substances, and how to treat it harmlessly and efficiently recover the valuable substances in it has become an urgent problem in the aluminum industry in recent years This article analyzes and summarizes the composition and hazards of the Research Progress of Electrolytic Aluminum Overhaul Slag Research on the Coprocessing of Mixed Electrolytic Aluminum Waste in Circulating Fluidized Bed Boiler Lei Shi1, grinding the materials with an electric mill, 50 grams of electrolytic aluminum waste samples were sieved to 0075 mm Blending ratio Calcium carbonate/g Condition 1 5:5 0 Condition 2 7:3 0 Condition 3 :7 0Research on the Coprocessing of Mixed Electrolytic Aluminum Waste 2022年10月10日 One of the main electrolytic aluminum production costs is the consumption of carbon anodes, and carbon anode slag is a common hazardous waste in the aluminum industryRecovery of carbon and cryolite from spent carbon
.jpg)
A novel approach for lithium recovery from waste lithium
2021年10月1日 Aluminum electrolysis of China, solid waste, such as waste aluminum electrolyte, has been largely idled and caused serious environmental pollution In this paper, a novel approach is developed for achieving the separation/recovery of lithium from spent lithiumcontaining aluminum electrolyte by a sodium carbonate roasting–acid leaching process2022年2月19日 Recycling waste containing rare earth has always been a research hotspot The molten salt electrolysis process of rareearth metals and alloys generates a large amount of waste slag, which contains high rareearth content and, thus, has very considerable recovery value However, the high content of fluorine in rareearth molten salt slag brings challenges to the Recovery of RareEarth Elements from Molten Salt Electrolytic Slag 2024年2月1日 The electrolytic aluminum industry generates a large amount lithium (Li)containing electrolytic aluminum slag (EAS) annually, and this can result in severe environmental pollution and wasting of Li resources This paper proposes a method for recovering Li from the slag using AlCl 3 as the leaching agent The effects of the leaching temperature, AlCl 3 Efficient lithium recovery from electrolytic aluminum slag via an 2023年10月1日 The main components of waste aluminum cryolite electrolyte are cryolite (Na 3 AlF 6), potassium cryolite (K 2 NaAlF 6), lithium cryolite (Na 2 LiAlF 6), fluorite (CaF 2), and approximately 2% carbon black (Wang et al, 2019)The main treatment methods of waste aluminum cryolite electrolyte can be divided into two categories: combined thermalwet Efficient extraction and recovery of lithium from waste aluminum
.jpg)
Experimental study on indirect mineral carbonation using five
2024年5月26日 Mineral carbonation is one of the known methods for carbon capture, utilization, and storage (CCUS) Slag from the steel industry is studied as a common source of CaCO3 via mineral carbonation owing to its high Ca content Despite numerous preliminary studies, the optimal factors governing the mineral carbonation of steelmaking slag, such as extraction and 2023年9月1日 Lithium (Li)bearing aluminum electrolyte slag is an inevitable byproduct of the aluminum industry, and improper disposal or stacking it may lead to potential environmental hazards This study employed hydrometallurgical processes to selectively leach lithium from Licontaining aluminum electrolyte slag, using sodium carbonate solution as the leaching agent Clean Process for Selective Recovery of Lithium Carbonate from Waste 2022年12月12日 Based on the research on bulk solid waste contact molding technology by our team [49], the comprehensive performance of pressed bricks with different ratios of aluminum ash and calcium carbide slag was investigated, the ratios of aluminum ash and calcium carbide slag are 9:1 ∼ 1:9 and pure aluminum ash and calcium carbide slag, the pressing pressure is 300 Comprehensive performance study of aluminum ash and calcium