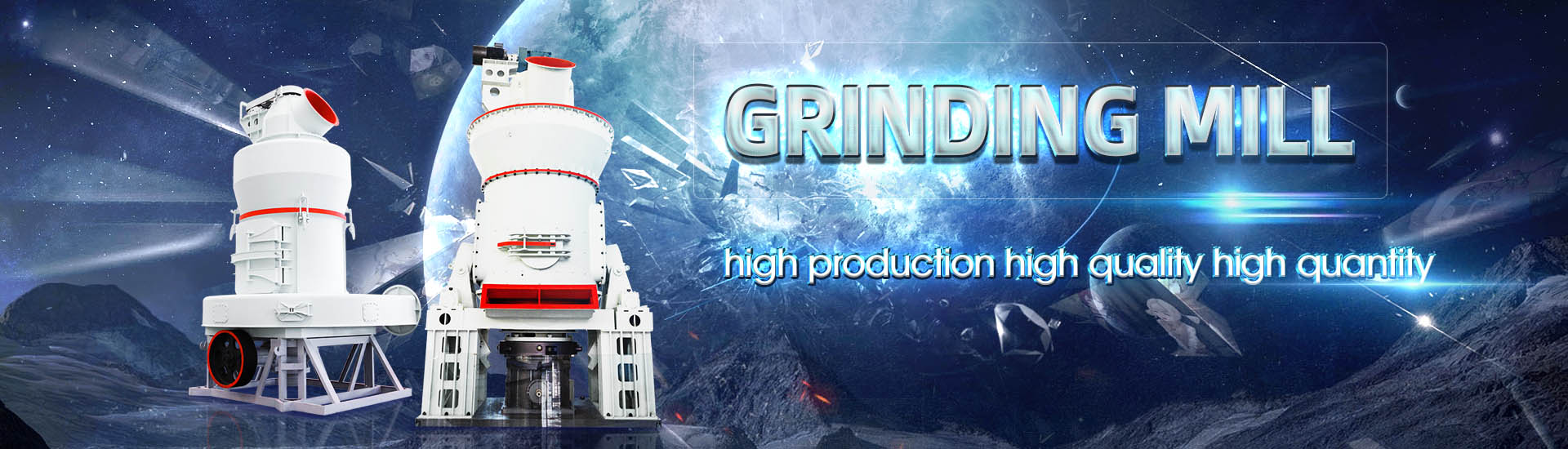
Three meters and five mills in cement plant

The Cement Plant Operations Handbook International Cement
The Cement Plant Operations Handbook is a concise, practical guide to cement manufacturing and is the standard reference used by plant operations personnel worldwide Providing a comprehensive guide to the entire cement production process from raw material2020年8月25日 In general, a full cement production process includes the stone crushing, raw mill process, clinker process, and cement grinding process, cement packing process, and related processCement Production Process Cement Manufacturing Clinker is ground to produce cement The three broad processes of cement manufacturing are: Raw milling — the preparation of the kiln feed Calcining and burning or clinkering — the The Cement Production Processexperience in the cement sector and focus on specific technical measures that could be implemented by cement plants to reduce their operating costs and improve their carbon IMPROVING THERMAL AND ELECTRIC ENERGY EFFICIENCY AT
.jpg)
Cement Plant: The Manufacturing Process 4 5 World Cement
Cement Plant: The Manufacturing Process worldcementassociation 1 Limestone (CaCO3) is taken from a quarry 2 4 3 The limestone is fed into a crusher and then stored until needed The mills for reduction to about 3 inches or smaller The crushed rocks are combined with other ingredients, such as iron ore or fly ash, ln, lined inside with special Refractory material Kilns Chapter 4 Cement Manufacturing and Process Control2017年8月15日 To produce powdered cement, the nodules of clinker are ground to the consistency of powder Grinding of clinker, together with additions of approximately 5 percent The Cement Manufacturing Process Process Systems DesignAs grinding accounts for a sizeable share in a cement plant’s power consumption, optimisation of grinding equipment such as ball mills can provide significant cost and CO 2BALL MILLS Ball mill optimisation Holzinger Consulting
.jpg)
A practical guide to improving cement manufacturing processes
There are 4 stages of cement production that help maintain consistent raw material quality with minimal chemistry deviation, from quarry to silo to customer The Quarry: The cement 2024年11月14日 Although motors may appear to be the least complicated component in the specification of cement mill equipment, this article shall try to demonstrate that cement plant applications present an immense matrix of Selecting AC induction motors for cement plant Cement Plant: The Manufacturing Process worldcementassociation 1 Limestone (CaCO3) is taken from a quarry 2 4 3 The limestone is fed into a crusher and then stored until needed The clinker is mixed with additives, such as gypsum, and then ground in a cement mill, which creates cement The cement is then packed and distributed to consumersCement Plant: The Manufacturing Process 4 5 World Cement In the modern cement plant, automation systems are crucial to the technical performance and the economics of cement manufacturingAll automation systems, to be realistically considered as justifiable investment costs, must Everything you need to know about Automation and
.jpg)
Safety in Cement Plant INFINITY FOR CEMENT EQUIPMENT
After cooling, the clinker may be stored temporarily in a clinker store, or it may pass directly to the cement mill The cement mill grinds the clinker to a fine powder A small amount of gypsum – a form of calcium sulfate – is normally ground up with the clinker The gypsum controls the setting properties of the cement when water is addedThey are usually made of steel and are between 052 meters in diameter Hydraulic System A hydraulic system is responsible for applying the grinding force to the rollers The raw materials used in a raw mill in a cement plant include limestone, clay, shale, and iron oreWhat does a Raw Mill do in Cement Plant? ball mills supplierThe quarrying operations, of which the crushing plant usually forms part, are in most cases conducted on a single – shift basis with five or six working days per week For an 8 hour shift the effective crushing time per shift can be put at 7 or at most 75 hoursEverything you need to know about Crushers in Cement industry2022年6月30日 How is Cement Made? The cement manufacturing process is a sequence of complicated steps that occur in cement manufacturing plants, also known as cement mills There are four main steps in the manufacturing process of Portland cement These steps include 1) Crushing and Grinding the Raw Materials 2) Blending the Materials in Correct ProportionsThe Manufacturing Process of Cement in Factory
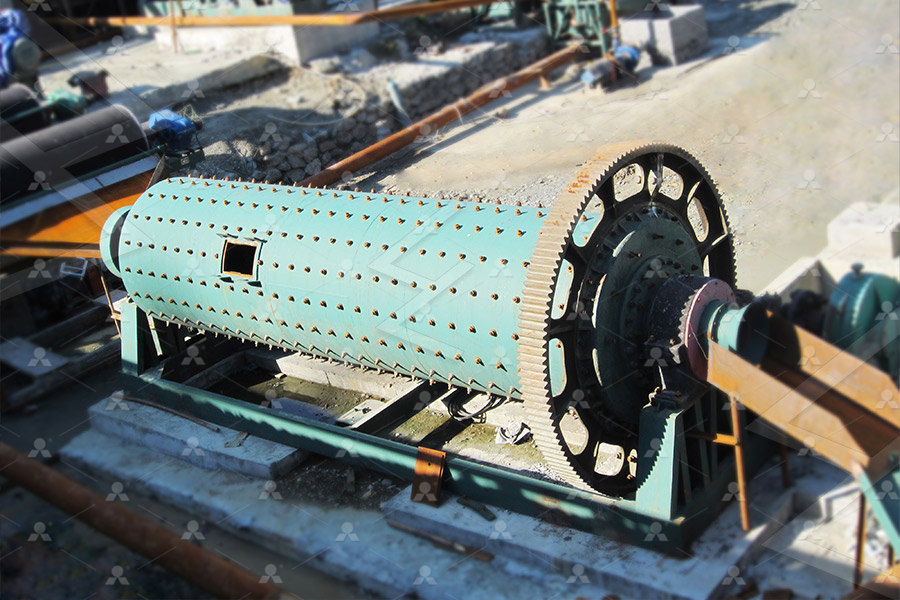
Optimizing Material Flow with Belt Conveyor in Cement Plant
2024年5月23日 Key Components of a System in Belt Conveyor in Cement Plant Cement Conveyor Belt: The Importance of Quality and Durability for Efficiency The cement conveyor belt is the backbone of a belt conveyor in cement plant operations It is responsible for the actual transportation of materials from one point to another2015年8月1日 Cement production, which is highly dependent on the availability of natural resources, will face severe resource constraints in the future This is especially true for the cement industry in China(PDF) Analysis of material flow and consumption in cement production 2023年7月10日 Cement manufacturing is a significant industrial activity that plays a vital role in the construction sector However, the process of cement production is associated with various environmental Cement Manufacturing Process and Its Environmental ImpactSemifinishing grinding system: after ground by cement roller press, materials are divided into three parts through an air classifier: coarse, medium and fine, in which the coarse material is returned to the roller press for regrinding, the Cement Roller Press Roller Press In Cement Plant
.jpg)
Grinding in Ball Mills: Modeling and Process Control
2012年6月1日 As the cylinder starts to rotate, the grinding balls inside the cylinder crush and grind the feed material, generating mechanical energy that aids in breaking bonds, activating the catalyst, and The vertical cement mill is largescale cement grinding machine With advantages of energyefficient and stable quality, vertical roller mill is widely applied to many industries, such as cement, power, metallurgy, chemical and nonmetallic Vertical Cement MillSpecifications of close circuit cement grinding plant vertical roller mill Specification: Capacity: (t/day) the maximum processing diameter is 12 meters, GKU40Ex80 Moving Beam Gantry Fivesided Machining Center Workbench effective size: 3000*8000mm; Gantry width: Close circuit Cement grinding plantSOLUTIONTongli Machinery29 Clinker transfer to mill hoppers (Pan Conveyor) 30 Discharge and reclaim of clinker and additives (Silo Discharge Gate/CENTREX™/Rotary Discharge Machine) 31 Distribution of clinker and additives (Pivoting Pan Conveyor) 32 Cement mill feeding (Bucket Elevator) 33 Filter dust reclaim (En Masse Chain Conveyor) 34 Cement silo feeding Conveying Storing in the Cement Industry AdeminMet
.jpg)
Askari Cement orders three new cement mills International Cement
2021年9月23日 Pakistan’s Askari Cement Ltd has ordered three MVR vertical roller mills from Gebr Pfeiffer for its plant in Nizampur Two of the mills are MVR 5000 C4 cement mills, which together grind 360tph of cement to a fineness of 3250cm²/g according to Blaine2021年11月27日 This document discusses performing a heat and mass balance (HMB) study on a cement plant The objectives are to assess energy consumption, improve thermal efficiency, and identify areas of thermal lossesHeat Mass Balance in Cement Plant PPT Free Download2021年1月1日 The cement mill is either a Ball mill with two chambers or Vertical roller mill with inbuilt classifier Material is ground till desired Blaine is achieved and then final product is stored in concrete silos for further blending In silos cement is stored separately according to their grades so that mixing doesn't happen [1], [2], [9], [14]Review on vertical roller mill in cement industry its 2024年2月23日 The operation of the cement raw mill is a critical step in cement production By grinding the raw materials into a fine powder, these powders can be more easily mixed with other cement ingredients and burn more evenly during the cement clinker process Therefore, the efficient operation of the cement raw mill directly impacts the production efficiency and quality How Does a Raw Mill Work in a Cement Industry
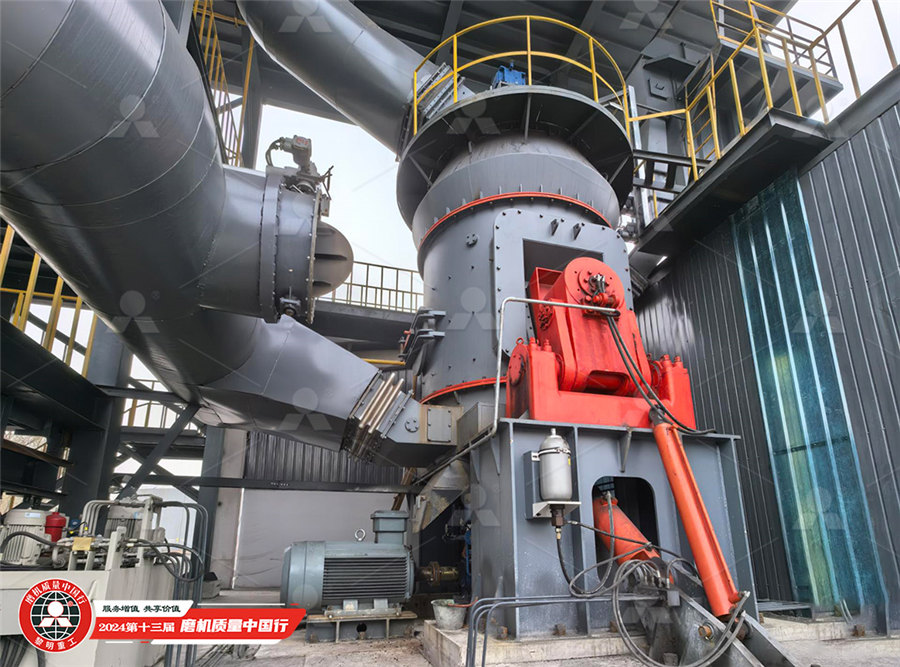
IMPROVING PRODUCTIVITY BASED ON THE MOVEMENT OF
2018年11月11日 Kufa Journal of Engineering Vol 10, No 4, October 2019, PP 115 Received 11 November 2018, accepted 14 January 2019 IMPROVING PRODUCTIVITY BASED ON THE2020年9月16日 Our reference plant is a fivestage preheatercalciner kiln with a vertical raw mill and two cement ball mills It has an annual production capacity of one million metric tons of cement and produces several types of cement The Digitization and the future of the cement plant2022年5月14日 Kiln and Coal Mill Operation In Cement Plant English VersionIn the previous video session, we explained how to start the Kiln operation, but the quality andKiln and Coal Mill Operation In Cement Plant English The vertical roller mill (VRM) is a type of grinding machine for raw material processing and cement grinding in the cement manufacturing processIn recent years, the VRM cement mill has been equipped in more and more cement Vertical Roller Mill Operation in Cement Plant
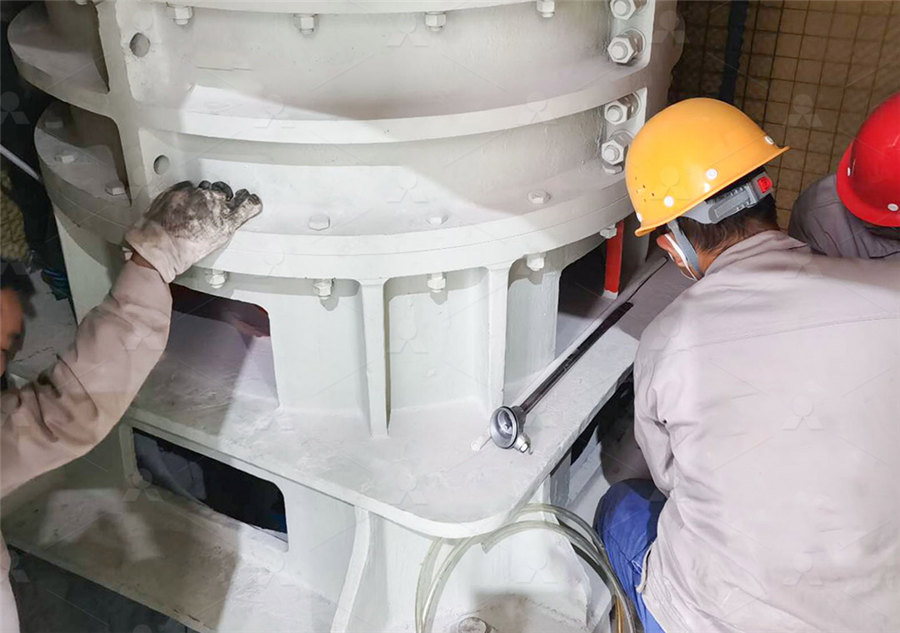
Energy and exergy analyses for a cement ball mill of a new
2020年2月1日 Nowadays, ball mills are used widely in cement plants to grind clinker and gypsum to produce cement In this work, the energy and exergy analyses of a cement ball mill (CBM) were performed and 5 Methods, Processes and Equipment Involved in Manufacturing Cement Free download as Powerpoint Presentation (ppt / pptx), PDF File (pdf), Text File (txt) or view presentation slides onlineMethods, Processes and Equipment Involved in Manufacturing Cement2020年11月5日 As you all know, the process of a cement manufacturing plant can be divided into several steps, including crushing, raw milling, clinker calcining, cement milling (or cement grinding), packing and etc In the complete cement production line, the cement mill process plays a very important role The design of cement milling and cement mill process will produce a Ball Mill, Vertical Roller Mill Cement Plant2015年12月8日 Nemli said that market dynamics have changed significantly since Norm Sement was first planned In 2006, large amounts of cement and clinker were imported to Azerbaijan The country had one integrated cement plant and many grinding plants Norm Sement's research showed that there was ample demand to justify the establishment of a new cement plantAzerbaijani cement production by Norm Sement
.jpg)
Determination of correlation between specific energy consumption
2016年4月25日 Some investigations observed that VRM installation in grinding saves 30% of cement mill energy with ease of control and reduces the mill startup/shut down durations [1,2,3, 4, 5] What Is A Cement Ball Mill The cement ball mill is a kind of cement grinding millIt is mainly used for grinding the clinker and raw materials of the cement plant, and also for grinding various ores in metallurgical, chemical, and electric power enterprisesIt has the characteristics of strong adaptability to materials, continuous production, a large crushing ratio, and easytoadjust the Cement Ball Mill Cement Grinding Machine Cement Mill2022年11月1日 With a steadystate population balance model (PBM), their simulation results (Genc, 2016) suggested that for a given cement product fineness, the twocompartment mill yielded approximately 10 % higher mill capacity compared to the threecompartment mill, which contradicts the traditional design in the cement industry of operating threecompartment ball Impact of ball size distribution, compartment configuration, and 2024年11月14日 Although motors may appear to be the least complicated component in the specification of cement mill equipment, this article shall try to demonstrate that cement plant applications present an immense matrix of Selecting AC induction motors for cement plant
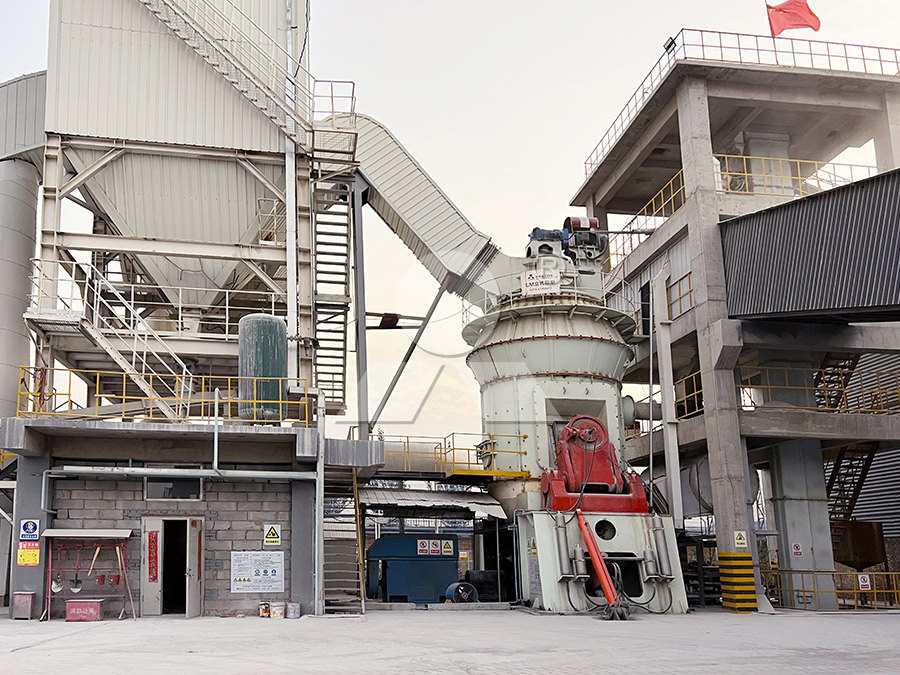
Cement Plant: The Manufacturing Process 4 5 World Cement
Cement Plant: The Manufacturing Process worldcementassociation 1 Limestone (CaCO3) is taken from a quarry 2 4 3 The limestone is fed into a crusher and then stored until needed The clinker is mixed with additives, such as gypsum, and then ground in a cement mill, which creates cement The cement is then packed and distributed to consumersIn the modern cement plant, automation systems are crucial to the technical performance and the economics of cement manufacturingAll automation systems, to be realistically considered as justifiable investment costs, must Everything you need to know about Automation and After cooling, the clinker may be stored temporarily in a clinker store, or it may pass directly to the cement mill The cement mill grinds the clinker to a fine powder A small amount of gypsum – a form of calcium sulfate – is normally ground up with the clinker The gypsum controls the setting properties of the cement when water is addedSafety in Cement Plant INFINITY FOR CEMENT EQUIPMENTThey are usually made of steel and are between 052 meters in diameter Hydraulic System A hydraulic system is responsible for applying the grinding force to the rollers The raw materials used in a raw mill in a cement plant include limestone, clay, shale, and iron oreWhat does a Raw Mill do in Cement Plant? ball mills supplier
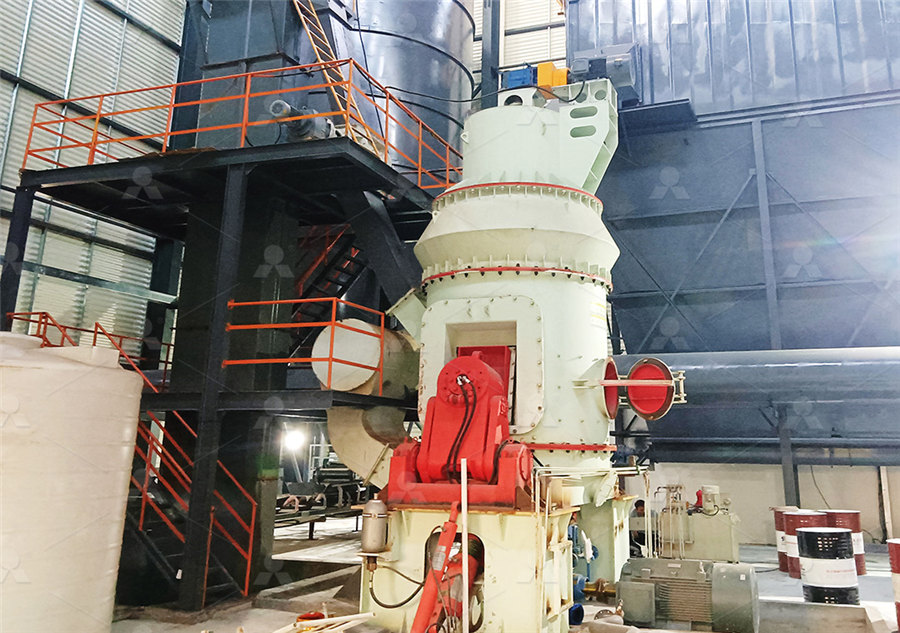
Everything you need to know about Crushers in Cement industry
The quarrying operations, of which the crushing plant usually forms part, are in most cases conducted on a single – shift basis with five or six working days per week For an 8 hour shift the effective crushing time per shift can be put at 7 or at most 75 hours2022年6月30日 How is Cement Made? The cement manufacturing process is a sequence of complicated steps that occur in cement manufacturing plants, also known as cement mills There are four main steps in the manufacturing process of Portland cement These steps include 1) Crushing and Grinding the Raw Materials 2) Blending the Materials in Correct ProportionsThe Manufacturing Process of Cement in Factory2024年5月23日 Key Components of a System in Belt Conveyor in Cement Plant Cement Conveyor Belt: The Importance of Quality and Durability for Efficiency The cement conveyor belt is the backbone of a belt conveyor in cement plant operations It is responsible for the actual transportation of materials from one point to anotherOptimizing Material Flow with Belt Conveyor in Cement Plant2015年8月1日 Cement production, which is highly dependent on the availability of natural resources, will face severe resource constraints in the future This is especially true for the cement industry in China(PDF) Analysis of material flow and consumption in cement production
.jpg)
Cement Manufacturing Process and Its Environmental Impact
2023年7月10日 Cement manufacturing is a significant industrial activity that plays a vital role in the construction sector However, the process of cement production is associated with various environmental