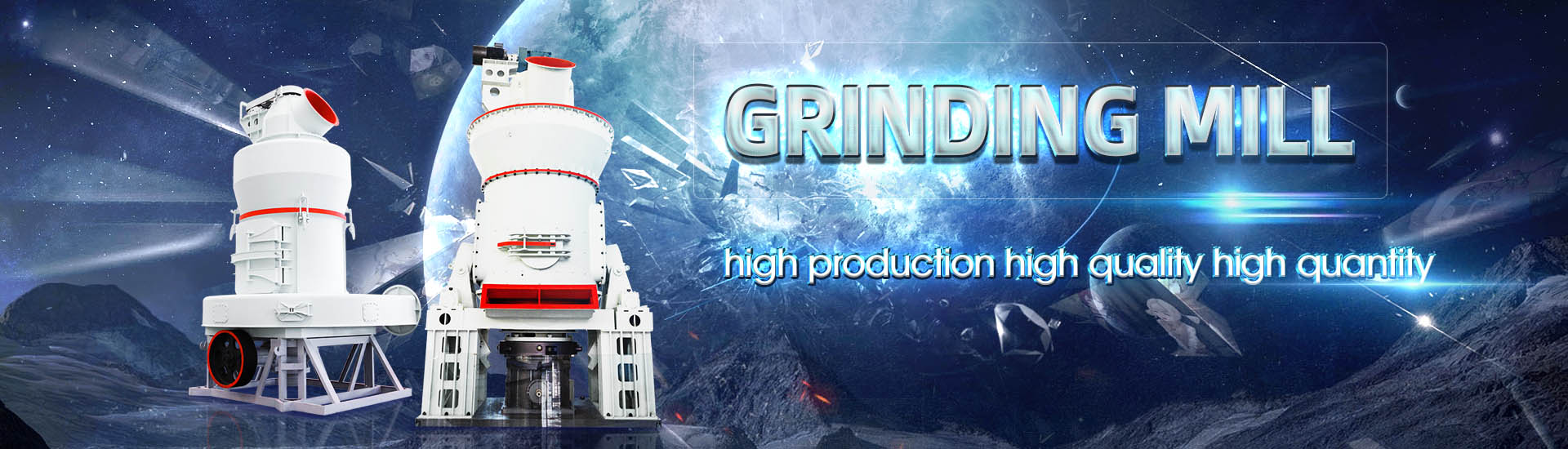
Fixed ore mill for mining
.jpg)
Mills for minerals and ores Loesche
The dry milling of ore in LOESCHE vertical roller mills has shown significant process advantages, as well as economic and ecological benefits To demonstrate these a mobile oregrinding plant the OGPmobile has been Esti mates of costs are based primarily on computed average costs of existing mining projects and operations, with appropriate allow ances for general site conditions, mining methods, and COSTS AND COST ESTIMATION Chapter NUBE MINERACustomized grinding mill parts including heads, shells, trunnions and liners, main bearings, gears and pinions, and more! Metallic, PolyMet™, Megaliner™, Rubber and Orebed™ mill liners for all mill types Whether old or new, we can Grinding mills for mining and minerals processing2024年4月26日 Iron ore, a naturally occurring mineral composed primarily of iron oxides, is mined and processed to extract iron for various industrial applications This article provides a comprehensive overview of the iron ore Iron Ore Processing: From Extraction to Manufacturing
.jpg)
Fixed Plant Mining Equipment Maintenance HMR
We deliver expert fixed plant maintenance services to maximise the reliability and productivity of mining equipment and other industrial plant Our inhouse team includes mechanical fitters, diesel mechanics and boilermakers with extensive 2014年2月1日 This paper provides a breakdown of operating costs in 63 mines by dividing them into three main categories: mining, milling, and general and administrative (G A) costs The Mine operating costs and the potential impacts of ScienceDirectOur Enduron® HPGR can fit into a wide array of mining and aggregate applications within both wet and dry classification including: Iron ore and precious metal beneficiation; Mineral liberation; Pellet feed preparation; Pebble crushingOur Dynamic HPGR Technology for Mineral Grinding2023年11月24日 The ball mill is a rotating cylindrical vessel with grinding media inside, which is responsible for breaking the ore particles Grinding media play an important role in the Grinding Media in Ball Mills for Mineral Processing

Ball Mill (Ball Mills Explained) saVRee saVRee
Ball mills are the most common grinding machine employed in the mining industry Grinding occurs in a single stage, or multiple stages Multiple stages may include a rod mill followed by a ball mill (two stage circuit), or a semi When iron ore is extracted from a mine, it must undergo several processing stages Six steps to process iron ore 1 Screening We recommend that you begin by screening the iron ore to separate fine particles below the crusher’s CSS The six main steps of iron ore processing Multotec2019年8月14日 • Central discharge ball mill: the inlet of medium unloading ball mill is at both ends, and the outlet is in the middle of the ball mill 4 According to the ore discharge of ball mill: • Overflow ball mill: Discharge the ore through hollow shaft • Grid ball mill: Discharge the ore through the plaid plateThe Ultimate Guide to Ball Mills Miningpedia2024年8月7日 01 Fixed factors affecting ball mill The factors that are relatively fixed and do not need to be adjusted frequently in ball mill operation include the hardness of the original ore, the size of the crushed particle size, the mesh of Ball Mill Operation, Maintenance and Common
.jpg)
Net Asset Value in Mining Sell Side Handbook
2017年7月20日 Refining costs include electrorefining (output is pure enough to be sold) Transportation costs include moving ore from the mill after it’s been processed to the smelters (which means very high diesel costs) Operating Costs Mining costs are direct costs involved in taking the ore (rock with desired metals inside) out of the minution is the process by which mined ore is reduced in size to make for easier processing The strict definition is ‘the action of taking a material, specifically mineral ore, and reducing it to minute fragments or particles’ This is typically achieved in several stages of a detailed and professional mining operation Jaw CrusherJaw Crusher Explained saVRee2023年2月17日 Mining has many large and complex assets, and mining is a process driven industry, both business processes and physical and chemical processing of ore, by assetsAI digital twins for mining explained 2022年5月12日 The 16thcentury German scientist Georgius Agricola – known by many as the Father of Mineralogy – utilized hammermills for mining operations during the Renaissance The modern hammermill design is thought to have been developed in the early 19thcentury, with the industrial revolution bringing the use of steampowered hammermillsWhat to Look for in Hammermill Design for Optimum
.jpg)
Innovation in the Mining Industry: Technological Trends and a
2020年7月23日 Innovation plays a critical role in the mining industry as a tool to improve the efficiency of its processes, to reduce costs, but also to meet the increasing social and environmental concerns among communities and authorities Technological progress has also been crucial to allow the exploitation of new deposits in more complex scenarios: lower ore However, emphasis on generating more tonnage to the mill in mining operations has resulted in loss of focus in this area There is a need to close this gap The primary objective of this study was to understand how ore loss and dilution affect the MCF and to subsequently improve the quality of ore mined and fed to the millMonitoring ore loss and dilution for minetomill integration in 2017年6月2日 Industrial crushers reduce large rocks, ore or waste materials to smaller sizes by impact or pressure to fracture or deform the material During the primary crushing operation, boulder size feeds from 20 to 100 in are reduced to secondary crusher sizes of 1 to 20 in or mill feed size of 5 to 3 inHow it Works: Crushers, Grinding Mills and PulverizersUnderstanding Mine to Mill is presented in five parts Part A – Setting the Scene provides some definitions of Mine to Mill (M2M) and the historical background A chronology of Mine to Mill developments is followed by brief descriptions of the very wide range of Mine to Mill applications which have been implemented over the last 15 yearsUNDErsTaNDINg MINE TO MILL 911 Metallurgist
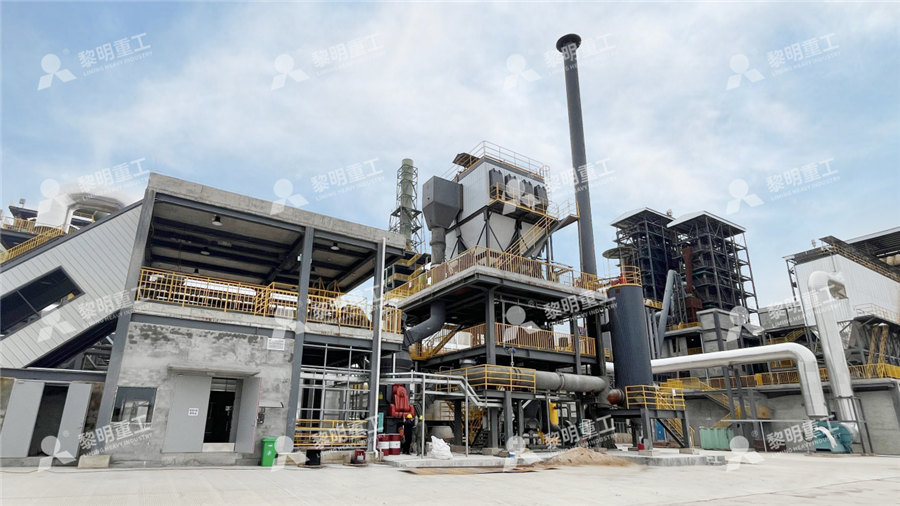
MOBILE HARD ROCK GOLD MINING EQUIPMENT
EFFICIENCY: SPEEDMINER ® Mobile Fully Integrated Hard Rock plant is designed with advanced technology to ensure 100% recovery of gold and other metals production, with no loss PRODUCT RANGE: SPEEDMINER ® Mobile 2018年3月12日 refining/selling/marketing cost, fixed/period cost, (mill) in a given time period, assuming unrestricted availability of input ore from the mining stage(PDF) Comparison of cutoff grade models in mineBall Mill Introduction There are three main stages to mineral processing in the mining industryThese are: Comminution (crushing and grinding); Beneficiation (separation and concentration); Smelting and refining; Ball mills are employed in the comminution stage as grinding machines (size reduction)The purpose of grinders in the mining industry is to reduce Ball Mill (Ball Mills Explained) saVRee saVRee2023年11月16日 Sublevel stope mining is one of the common underground mining methods, which is suitable for steeply deeping and tabular orebodies In this method, large open stopes are created in the vertical direction, as shown in the Fig 1, to extract the materials existing in a competent ore and host rock []The extracted ore from drilling and blasting of sublevels within A New Mathematical Programming Formulation for Production

Grinding mills for mining and minerals processing Metso
When choosing your equipment we not only keep in mind mill performance, but also considering how your Premier™ or Select™ mill will optimize your minerals processing circuit Performance Metso Premier™ mills and Select™ mills are built with a robust design and components to eliminate unplanned downtime leading to high availability and reliability2023年11月24日 The ball mill is a rotating cylindrical vessel with grinding media inside, which is responsible for breaking the ore particles In Proceedings of the 7th UMaT Biennial International Mining and Mineral Conference, Tarkwa, Ghana, 2 August 2022; pp 1–8Grinding Media in Ball Mills for Mineral ProcessingMining Ore Bin Gates Challenge Ore Feeder These are rack and pinion style ore bin gates Two are included in a package In a mill, one gate would feed one ore feeder These kits now include the laser cut chute shown above The fixed scrapers directs ore into the back of the stamp mortar as the table rotatesDetail Parts Mining Wild West Scale Model BuildersBased on the model of mining and processing equipment, the design, putting into production, joint tests of lining with the customer are carried out Warranty is provided Generic Lining Products Overall wearresistant plates Used for cladding large areas of the mill They can also be used to protect the surface of ore passes, trolleys and dump Rubber Lining for Ore Grinding Mills and Mining and Processing
.jpg)
Monitoring ore loss and dilution for minetomill integration in
2016年2月1日 The purpose of this study is to understand how ore loss and dilution affect the mine call factor, with the aim of subsequently improving the quality of ore mined and fed to the mill2021年4月19日 PDF Published in MATERIA 2021;23:6366 The idea of minetomill optimization has been tested in various mines in last decades, resulting in higher Find, read and cite all the research you (PDF) Feasibility and necessity of mine to mill International Financial Reporting Standards (IFRS) provide the basis for financial reporting to the capital markets in an increasing number of countries around theFinancial reporting in the mining industry International Financial Medium ore mine: 3: 13,000: 8,000: Seabed mining vessel: 3: 25,000: 8,800: Large ore mine underground: 4: 18,000: 9,600: Large ore mine: 5: Manufacturing metals requires the ore grinding mill, which is unlocked at the Complete Ore Industry Area Guide for Cities: Skylines
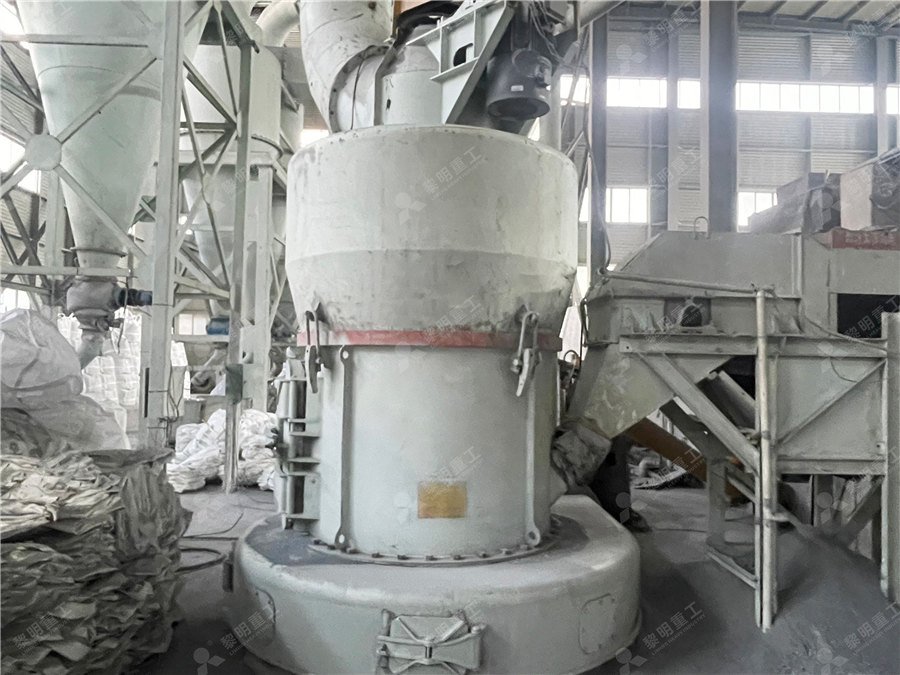
Automation and Robotics in Mining and Mineral Processing
2023年6月17日 The aim of a mineral processing operation is to concentrate a raw ore for the subsequent mineral extraction stage Usually, the valuable minerals are first liberated from the ore matrix by comminution and size separation processes (crushing, grinding, and size classification) and then separated from the gangue using processes capable of selecting the particles Material adapted from: Hudson, TL, Fox, FD, and Plumlee, GS 1999 Metal Mining and the Environment, p 1011 Published by the American Geosciences Institute Environmental Awareness Series Click here to download the full handbook This answer refers specifically to metal mining, but the mining of other Earth materials follows a very similar pattern The mining What happens before, during, and after mining?2020年9月24日 Whittle requires several information with respect to decision making like NPV to Ore Tonnage Since the resource is fixed, sometime it is better to sacrifice NPV for the sake of mining extra quantity of Ore Whittle provides such information, which is helpful in making decision The work flow is given in Fig 1Pit Optimization for Improved NPV and Life of Mine in Springer2022年10月18日 Drones, robotics and autonomous vehicles have been sparking innovative solutions in the mining industry for years Rio Tinto’s most technologically advanced iron ore mine in the Pilbara has taken this to a whole new level – boosting safety, energy efficiency and output, and paving the way for mines of the futureThe transformational technology behind Rio Tinto’s most
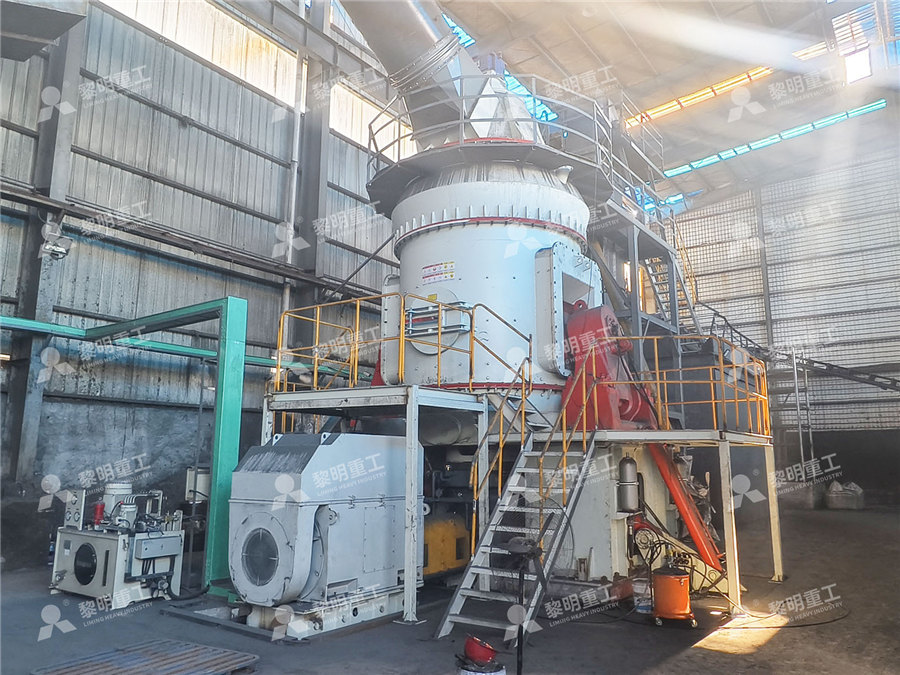
Mill liners: grinding out a legacy Mining Technology
2022年4月25日 After that first installation experiment, carried out in the US in a 4 x 20’ Ball Mill, at the Nipissing Mine in Ontario, Canada, Trelleborg went on to patent the first Mill linings in 1953 and after thorough tests applied for worldwide patent rights in 1963 and 1964 for two mounting systems with either fixed or interchangeable lifters【Working Principle of Disk Mill】The laboratory disk mill is mainly composed of the body, base, shaft, moving disc, fixed disc, cover and hopper cover, and other accessories The power to pass through the belt pulley is driven spindle rotation so that the relative movement of the movable disc fixed disc to crush the materialLaboratory Disk Mill Dust Free Grinding JXSC MachineWhen iron ore is extracted from a mine, it must undergo several processing stages Six steps to process iron ore 1 Screening We recommend that you begin by screening the iron ore to separate fine particles below the crusher’s CSS The six main steps of iron ore processing Multotec2019年8月14日 • Central discharge ball mill: the inlet of medium unloading ball mill is at both ends, and the outlet is in the middle of the ball mill 4 According to the ore discharge of ball mill: • Overflow ball mill: Discharge the ore through hollow shaft • Grid ball mill: Discharge the ore through the plaid plateThe Ultimate Guide to Ball Mills Miningpedia
.jpg)
Ball Mill Operation, Maintenance and Common
2024年8月7日 01 Fixed factors affecting ball mill The factors that are relatively fixed and do not need to be adjusted frequently in ball mill operation include the hardness of the original ore, the size of the crushed particle size, the mesh of 2017年7月20日 Refining costs include electrorefining (output is pure enough to be sold) Transportation costs include moving ore from the mill after it’s been processed to the smelters (which means very high diesel costs) Operating Costs Mining costs are direct costs involved in taking the ore (rock with desired metals inside) out of the Asset Value in Mining Sell Side HandbookComminution is the process by which mined ore is reduced in size to make for easier processing The strict definition is ‘the action of taking a material, specifically mineral ore, and reducing it to minute fragments or particles’ This is typically achieved in several stages of a detailed and professional mining operation Jaw CrusherJaw Crusher Explained saVRee2023年2月17日 Mining has many large and complex assets, and mining is a process driven industry, both business processes and physical and chemical processing of ore, by assetsAI digital twins for mining explained

What to Look for in Hammermill Design for Optimum
2022年5月12日 The 16thcentury German scientist Georgius Agricola – known by many as the Father of Mineralogy – utilized hammermills for mining operations during the Renaissance The modern hammermill design is thought to have been developed in the early 19thcentury, with the industrial revolution bringing the use of steampowered hammermills2020年7月23日 Innovation plays a critical role in the mining industry as a tool to improve the efficiency of its processes, to reduce costs, but also to meet the increasing social and environmental concerns among communities and authorities Technological progress has also been crucial to allow the exploitation of new deposits in more complex scenarios: lower ore Innovation in the Mining Industry: Technological Trends and a However, emphasis on generating more tonnage to the mill in mining operations has resulted in loss of focus in this area There is a need to close this gap The primary objective of this study was to understand how ore loss and dilution affect the MCF and to subsequently improve the quality of ore mined and fed to the millMonitoring ore loss and dilution for minetomill integration in 2017年6月2日 Industrial crushers reduce large rocks, ore or waste materials to smaller sizes by impact or pressure to fracture or deform the material During the primary crushing operation, boulder size feeds from 20 to 100 in are reduced to secondary crusher sizes of 1 to 20 in or mill feed size of 5 to 3 inHow it Works: Crushers, Grinding Mills and Pulverizers