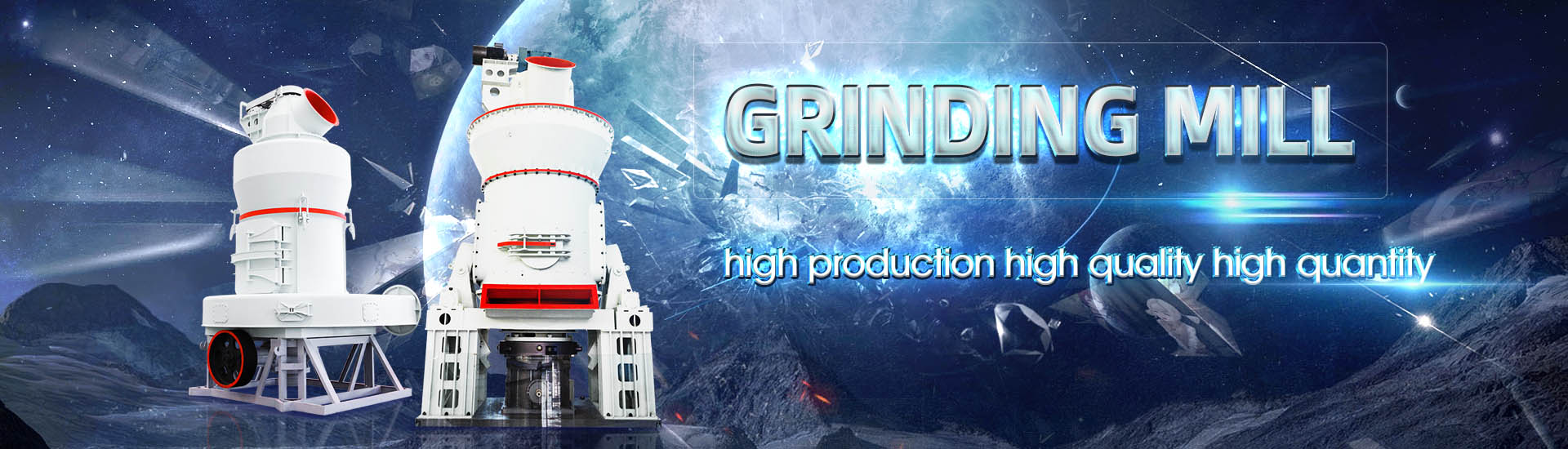
HOME→Relationship between the feed size of 3roller ore mill and the diameter of the grinding roller ring
Relationship between the feed size of 3roller ore mill and the diameter of the grinding roller ring
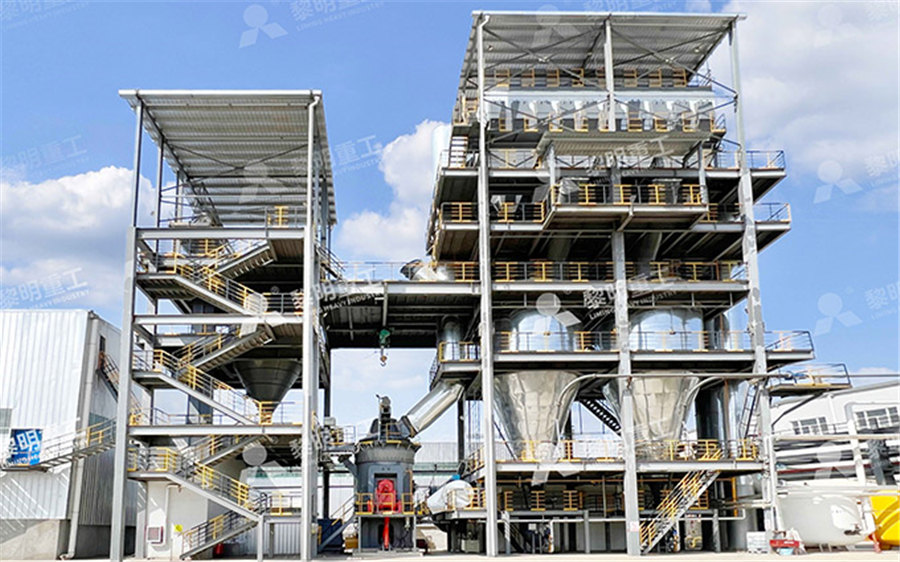
Operational parameters affecting the vertical roller mill performance
2017年4月1日 In this study, pilot scale tests were performed with a mobile verticalrollermill grinding plant to investigate the relationships between operational parameters The identification and quantification of the grinding parameter relationships was carried out to implement these 2021年9月1日 Feed size, product size and energy data from pilot scale grinding tests were evaluated with material characterization tests Based on energysize reduction models Predicting the grinding energy of vrm depending on material 2018年6月1日 In this article the effect of grinding media size distribution and feed material particle size distribution (PSD) on the product fineness requirements were investigated A Effect of ball and feed particle size distribution on the milling Common roll diameters are from 6 to 10 inches, and roll lengths — which vary with the roll diameter to ensure that the roll will be mechanically robust — are from 8 to 52 inches Longer Roller mills: Precisely reducing particle size with greater efficiency
.jpg)
RECENT DEVELOPMENTS IN COARSE GRINDING USING VERTICAL
Due consideration must be given to the grinding density and media size selection for the feed size and final product size To enable use of the vertical stirred mill, the transfer size must be 2022年3月16日 It shows that as the specific energy consumption increases, the product size becomes finer with P 80 of 219 mm from feed size with F 80 of 78 mm as the specific energy Potential of HighPressure Grinding Roll (HPGR) for Size Reduction Roller mill is a type of grinding equipment for crushing materials by pressure between two or more rolling surfaces or between rolling grinding bodies (balls, rollers) and a track (plane, ring, and Roller Mill SpringerIt was determined that the 30 mm diameter balls were most effective of the three sizes during the grinding of the 3 monosize feed material samples The 10 mm diameter balls were the least The Effect of Ball Size Diameter on Milling Performance
.jpg)
Grinding considerations when pelleting livestock feeds
Difference in particle size and standard deviation between roller milled and hammermilled corn Differences in particle size analysis can come from a number of causes, including incorrect Within 20 seconds of entering the pellet mill, feed goes from an airdry (about 1012 percent moisture) condition at ambient temperature, to 1516 percent moisture at 8090°C During Chapter 18 Feed Milling Processes2017年2月13日 The apparent difference in capacities between grinding mills (listed as being the same size) is due to the fact that there is no uniform method of designating the size of a mill, for example: a 5′ x 5′ Ball Mill has a working Ball Mills 911MetallurgistThe ball impact energy on grain is proportional to the ball diameter to the third power: 3 E K 1 d b (3) The coefficient of proportionality K 1 directly depends on the mill diameter, ball mill loading, milling rate and the type of grinding (wet/dry) None of the characteristics of the material being ground have any influence on K 1THE OPTIMAL BALL DIAMETER IN A MILL 911 Metallurgist
.jpg)
Operational parameters affecting the vertical roller mill
2016年9月1日 Tontu [14] investigated the relationships between the current, coal feed, grinding pressure, and primary air and outlet temperatures of coal mills, and proved that a high correlation exists 2024年1月1日 Roller mill is a type of grinding equipment for crushing materials by pressure between two or more rolling surfaces or between rolling grinding bodies (balls, rollers) and a track (plane, ring, and table) The roller mill with several grinding rollers as working components rolls along the grinding ring or the grinding table to crush the Roller Mill SpringerLink2015年6月19日 The basic parameters used in ball mill design (power calculations), rod mill or any tumbling mill sizing are; material to be ground, characteristics, Bond Work Index, bulk density, specific density, desired mill tonnage capacity DTPH, operating % solids or pulp density, feed size as F80 and maximum ‘chunk size’, product size as P80 and maximum and finally the type of Ball Mill Design/Power Calculation 911Metallurgist3 the nip angle when the crusher feed size is 10 cm, 4 the coefficient of friction between roll and gypsum particles 65 At a nip angle of 30°, an approximate relation between peripheral speed ν P (m/min), diameter of rolls D (cm) and sieve size d (cm) through which 80% of ore passes is given by the relationRoll Diameter an overview ScienceDirect Topics
.jpg)
Operational parameters affecting the vertical roller mill
2017年4月1日 The projected area consists out of the mean roller diameter multiplied with the roller width on the grinding table Download fullsize image; Fig 3 Relationship between specific energy consumption (grinding) (a) product rate and (b) Research of iron ore grinding in a verticalrollermill Miner Eng, 73 (2015), pp 1091152017年9月11日 indicated that particle size distributions of mill feed of a vertical roller mill for grinding raw in case 4 cm diameter of bed was utilized and the predictions were Performance Evaluation of Vertical Roller Mill in Cement Grinding2004年11月1日 Despite reservations of a number of researchers concerning the applicability of Bond's equation for relating specific energy to the size reduction of rocks, his approach has become an industry (PDF) An alternative energy–size relationship to that proposed Mill Weight Power Top Size Figure 4: Feed Top Size vs SAG Mill Performance 5000 5500 6000 6500 7000 7500 8000 8500 9000 9500 10000 13:00 14:00 15:00 16:00 17:00 kW 00 500 1000 1500 2000 2500 3000 3500 4000 Top size (mm) Top Size Power Mill Weight Figure 5: Feed Top Size vs AG Mill Performance This is not say that ag mill performance I203 I204 INTRODUCTION SMC Testing

Grinding Mill an overview ScienceDirect Topics
If the classifier is to separate the feed at 200 microns estimate the classifier area and screw diameter if the feed capacity required is 100 A crushing plant delivered ore to a wet grinding mill for further size reduction which is about 7–14 days for the ringball system, while for the roller mill, only 3–7 days2013年8月3日 In Grinding, selecting (calculate) the correct or optimum ball size that allows for the best and optimum/ideal or target grind size to be achieved by your ball mill is an important thing for a Mineral Processing Engineer AKA Calculate and Select Ball Mill Ball Size for Optimum 2021年9月1日 The K parameter for present data was back calculated and a preliminary energysize relationship was developed to predict the grinding energy of the vertical roller mill The feed size was also observed to be effective in grinding energy and reflected on the model The feed size range was divided into two ranges, a coarser and a finer size rangePredicting the grinding energy of vrm depending on material 2018年6月1日 A number of researchers (Deniz, 2012; Bwalya et al, 2014; Petrakis et al, 2016) carried out studies about the effect of feed particle size and grinding media size on the grinding kinetics of different oresKhumalo et al, 2006 postulated that generally larger sized grinding media would break larger particles quicker but a finer product would be obtained by use of Effect of ball and feed particle size distribution on the milling
.jpg)
Effect of ball and feed particle size distribution on the milling
2018年2月1日 In another study to investigate ball size distribution on ball mill efficiency by Hlabangana et al [50] using the attainable region technique on a silica ore by dry milling, a threeball mix of COMPARISON OF GRINDING EFFICIENCY BETWEEN BALL MILLS AND VERTICAL ROLLER MILLS IN COARSE GRINDING Yakup Umucu 1, Vedat Deniz 2,Osman Mart 1 Abdi Kemal Y!ce 1, Mehmet Fahri Sara" 3 1 S leyman COMPARISON OF GRINDING EFFICIENCY BETWEEN BALL MILLS30422 Rollingcompression machines: In such mill the feed material are caught and crushed between a roller member and the face of a grinding ring or casing The most common types are rollingring pulverizers, bowl mills, and roller millsSize Reduction1: Grinding – Unit Operations in Food Processing2017年3月4日 Ball mills are used for wet grinding iron ore, A SAG mill with a 44' diameter and a power of 3 5 MW (47,000 HP) Crushing involves reducing the ore size from various sizes ranging from SIZE REDUCTION BY GRINDING METHODS ResearchGate
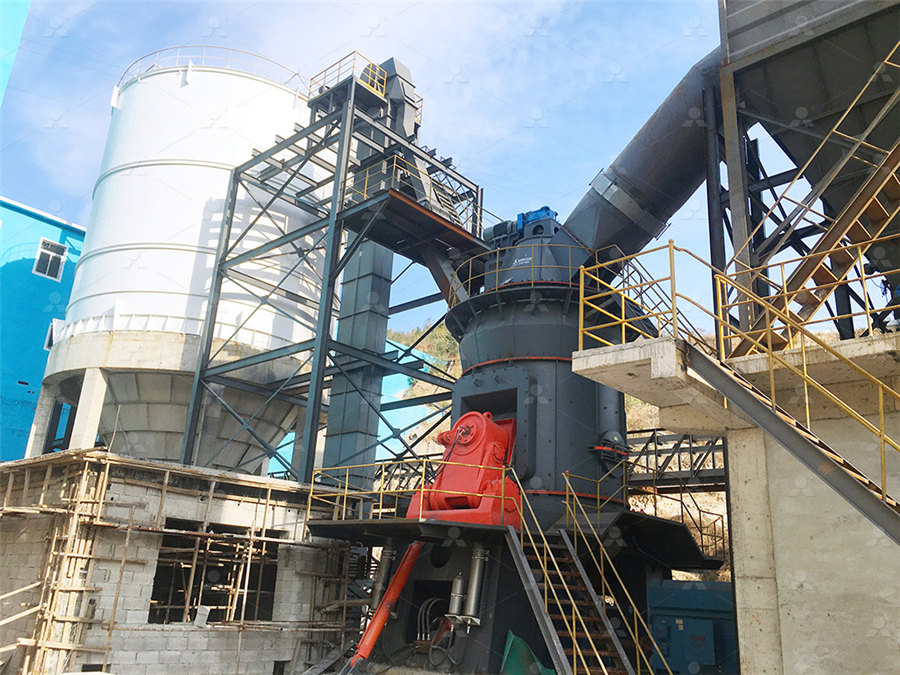
Grinding Mill an overview ScienceDirect Topics
Control of product size is exercised by the properties of the mill charge, the nature of the ore feed, and the type of mill and circuit used Read more View chapter Explore book Read full chapter in which particles between 5 and 250 mm are reduced in size to between 25 and 300 highspeed planetary ringroller grinding millhad decreased for the 2 mm +14 mm monosize feed compared to the bigger 4 mm +28 mm monosize feed This therefore shows that should the material feed size continue to decrease, the smaller balls will perform better than the larger balls during milling, as was mentioned by Katubilwa et al Effect of ball diameter size on mill power drawThe Effect of Ball Size Diameter on Milling Performance2016年6月6日 The ratio of the trunnion thickness to trunnion diameter in a mill of 2,134 m diameter is almost twice that of a mill of 5,8 m diameter, ie a ratio (T/D) of 0,116 to 0,069 for the large mill However the design stress levels at the SAG Mill Grinding Circuit Design 911Metallurgistrelationship between feed size and performance The influence of feed size on AG/SAG mill performance is well documented, though there is no universal rule that quantitatively describes this Feed size and blasting ResearchGate
.jpg)
Types of Crushers Explained: Everything You Need to
2024年4月19日 HighPressure Grinding Rolls (HPGR): In the HPGR crushers two counterrotating rollers with a small gap between them are used They squeeze and crush the stuff They are very good at fine grinding and are often 2016年1月1日 In wet grinding practice, highstress abrasion occurs over a small region when ore particles are trapped between the grinding balls and the mill liner, and the load is sufficient to fracture A comparison of wear rates of ball mill grinding mediaRequest PDF On Mar 15, 2015, Mathis Reichert and others published Research of iron ore grinding in a verticalrollermill Find, read and cite all the research you need on ResearchGateResearch of iron ore grinding in a verticalrollermill2016年10月5日 In this chapter an introduction of widely applied energyefficient grinding technologies in cement grinding and description of the operating principles of the related equipments and comparisons over each other in terms of grinding efficiency, specific energy consumption, production capacity and cement quality are given A case study performed on a EnergyEfficient Technologies in Cement Grinding IntechOpen
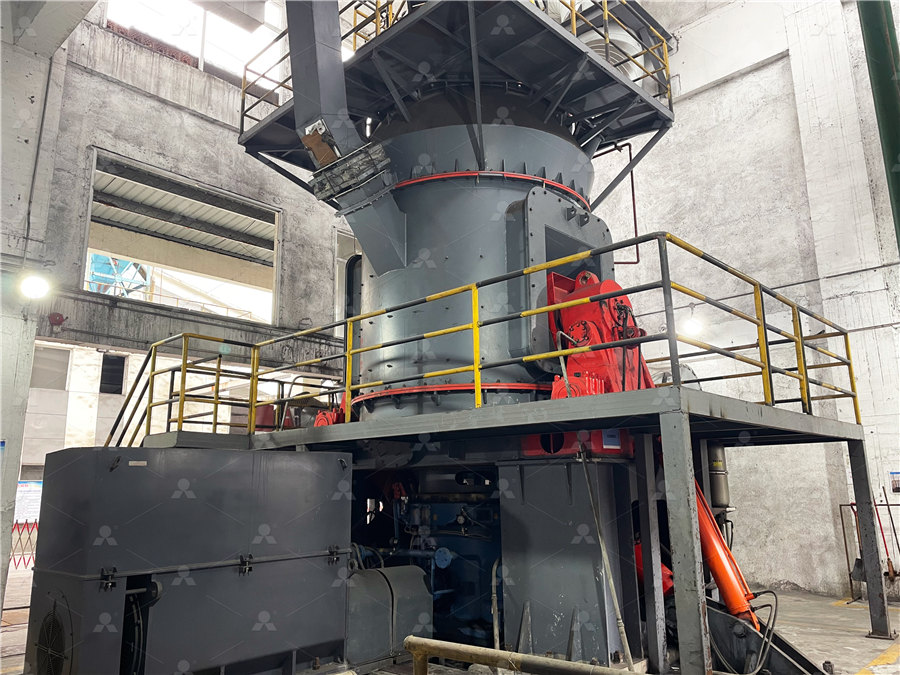
Raymond Roller Mill airswept vertical ringroll
The mill provides efficient control of product size with minimal power, resulting in a flexible, costeffective production Standard size Raymond Roller Mills are available with grinding ring diameters ranging from 30120 in / 7603050mm These sizes are capable of producing a wide range of product fineness from a wide variety of materialDownload scientific diagram Relationship between SAG mill power draw, bearing pressure and feed rate from publication: Supervisory Fuzzy Expert Controller for SAG Mill Grinding Circuits: Sungun Relationship between SAG mill power draw, bearing pressure and feed 2020年7月2日 According to the connection relationship between the ball mill and the of ~5–8 kWh/t during the grinding of apatite ore were the feed size, the product size, the mill diameter and (PDF) Effects of Ball Size Distribution and Mill Speed and Their Download scientific diagram The relationship between energy efficiency and grinding energy consumed; t = 45 min from publication: Effect of ball mill grinding parameters of hydrated lime fine The relationship between energy efficiency and grinding energy
.jpg)
Ball Mills 911Metallurgist
2017年2月13日 The apparent difference in capacities between grinding mills (listed as being the same size) is due to the fact that there is no uniform method of designating the size of a mill, for example: a 5′ x 5′ Ball Mill has a working The ball impact energy on grain is proportional to the ball diameter to the third power: 3 E K 1 d b (3) The coefficient of proportionality K 1 directly depends on the mill diameter, ball mill loading, milling rate and the type of grinding (wet/dry) None of the characteristics of the material being ground have any influence on K 1THE OPTIMAL BALL DIAMETER IN A MILL 911 Metallurgist2016年9月1日 Tontu [14] investigated the relationships between the current, coal feed, grinding pressure, and primary air and outlet temperatures of coal mills, and proved that a high correlation exists Operational parameters affecting the vertical roller mill 2024年1月1日 Roller mill is a type of grinding equipment for crushing materials by pressure between two or more rolling surfaces or between rolling grinding bodies (balls, rollers) and a track (plane, ring, and table) The roller mill with several grinding rollers as working components rolls along the grinding ring or the grinding table to crush the Roller Mill SpringerLink
.jpg)
Ball Mill Design/Power Calculation 911Metallurgist
2015年6月19日 The basic parameters used in ball mill design (power calculations), rod mill or any tumbling mill sizing are; material to be ground, characteristics, Bond Work Index, bulk density, specific density, desired mill tonnage capacity DTPH, operating % solids or pulp density, feed size as F80 and maximum ‘chunk size’, product size as P80 and maximum and finally the type of 3 the nip angle when the crusher feed size is 10 cm, 4 the coefficient of friction between roll and gypsum particles 65 At a nip angle of 30°, an approximate relation between peripheral speed ν P (m/min), diameter of rolls D (cm) and sieve size d (cm) through which 80% of ore passes is given by the relationRoll Diameter an overview ScienceDirect Topics2017年4月1日 The projected area consists out of the mean roller diameter multiplied with the roller width on the grinding table Download fullsize image; Fig 3 Relationship between specific energy consumption (grinding) (a) product rate and (b) Research of iron ore grinding in a verticalrollermill Miner Eng, 73 (2015), pp 109115Operational parameters affecting the vertical roller mill 2017年9月11日 indicated that particle size distributions of mill feed of a vertical roller mill for grinding raw in case 4 cm diameter of bed was utilized and the predictions were Performance Evaluation of Vertical Roller Mill in Cement Grinding
.jpg)
(PDF) An alternative energy–size relationship to that proposed
2004年11月1日 Despite reservations of a number of researchers concerning the applicability of Bond's equation for relating specific energy to the size reduction of rocks, his approach has become an industry Mill Weight Power Top Size Figure 4: Feed Top Size vs SAG Mill Performance 5000 5500 6000 6500 7000 7500 8000 8500 9000 9500 10000 13:00 14:00 15:00 16:00 17:00 kW 00 500 1000 1500 2000 2500 3000 3500 4000 Top size (mm) Top Size Power Mill Weight Figure 5: Feed Top Size vs AG Mill Performance This is not say that ag mill performance I203 I204 INTRODUCTION SMC Testing