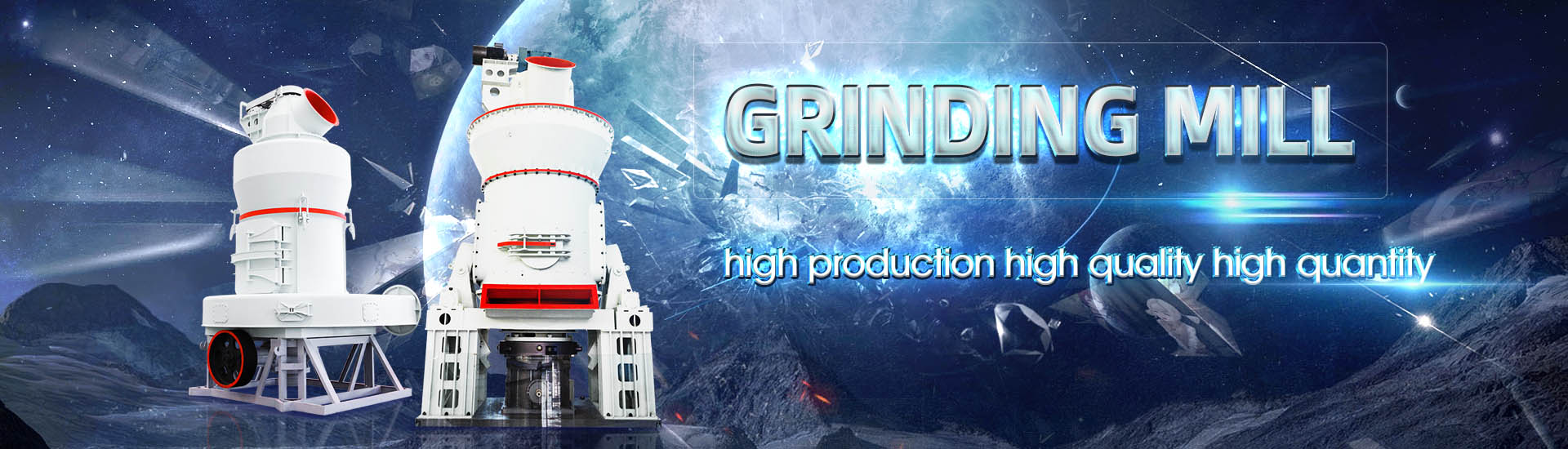
Energysaving mill for cement plant equipment
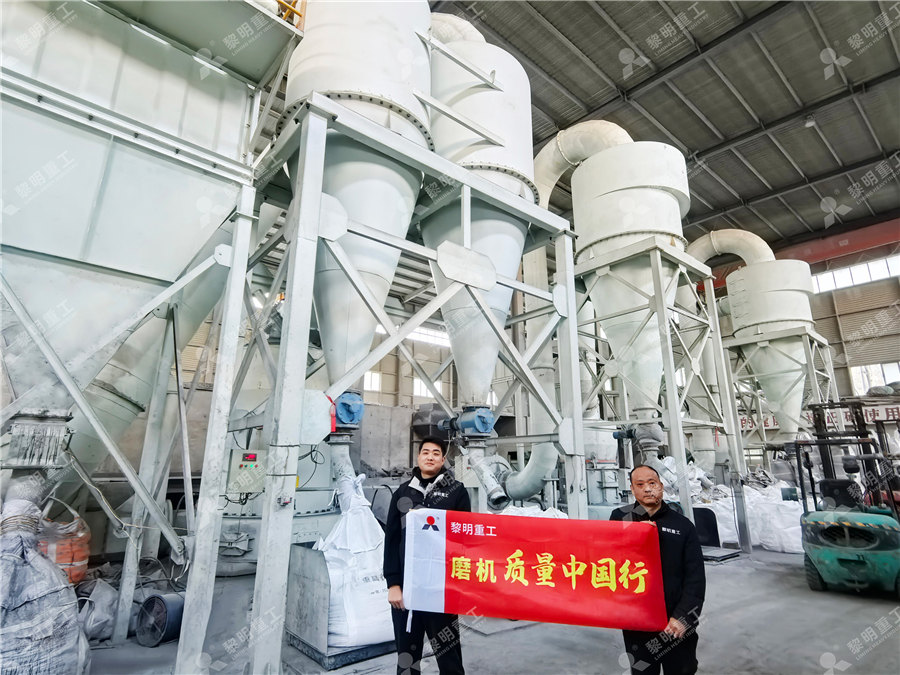
IMPROVING THERMAL AND ELECTRIC ENERGY EFFICIENCY AT
Improving Thermal and Electric Energy Efficiency at Cement Plants: International Best Practice v This report was produced in cooperation between IFC, SNIC (Sindicato Nacional da Indústria do Cimento), ABCP (Associação Brasileira de Cimento Portland), and INT (Brazil’s National 2011年5月1日 Specific energy consumption in cement production varies from technology to technology The dry process uses more electrical but much less thermal energy than the wet A critical review on energy use and savings in the cement industries2013年3月1日 In this paper, energy saving measures in the cement industry, such as energyefficiency measures for the preparation of raw materials, production of clinker, and the An overview of energy savings measures for cement industriesImproving production technology is a good strategy to reduce the energy needs of a cement plant The market offers a wide variety of alternative solutions; An overview of energy savings measures for cement
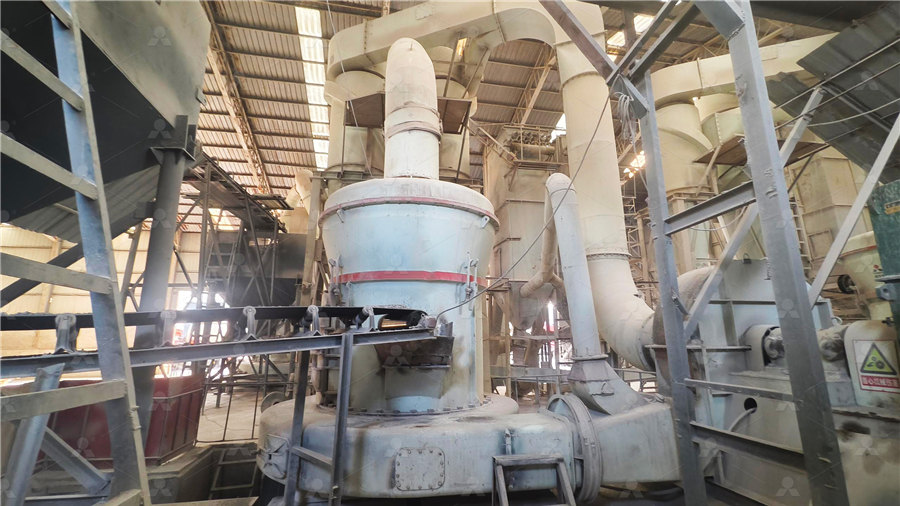
BALL MILLS Ball mill optimisation Holzinger Consulting
As grinding accounts for a sizeable share in a cement plant’s power consumption, optimisation of grinding equipment such as ball mills can provide significant cost and CO 2Thermal energy savings using Expert Optimizer (EO) Cement manufacturing is a complex and energyintensive process A key stage in this process is the conversion of ground raw Energy optimization in cement manufacturing ABBChoose the right cement manufacturing machine is an important influence factor to produce highquality cement The cement making machine frequently used in cement plants includes cement rotary kiln, shaft kiln, cement vertical mill, Cement Manufacturing Machine Cement Making 2019年3月8日 Association of Portland Cement (ABCP), the International Energy Agency (IEA), the Cement Sustainability Initiative (CSI) of the W orld Business Council for Sustainable Development (WBCSD), and IFCIMPROVING THERMAL AND ELECTRIC ENERGY
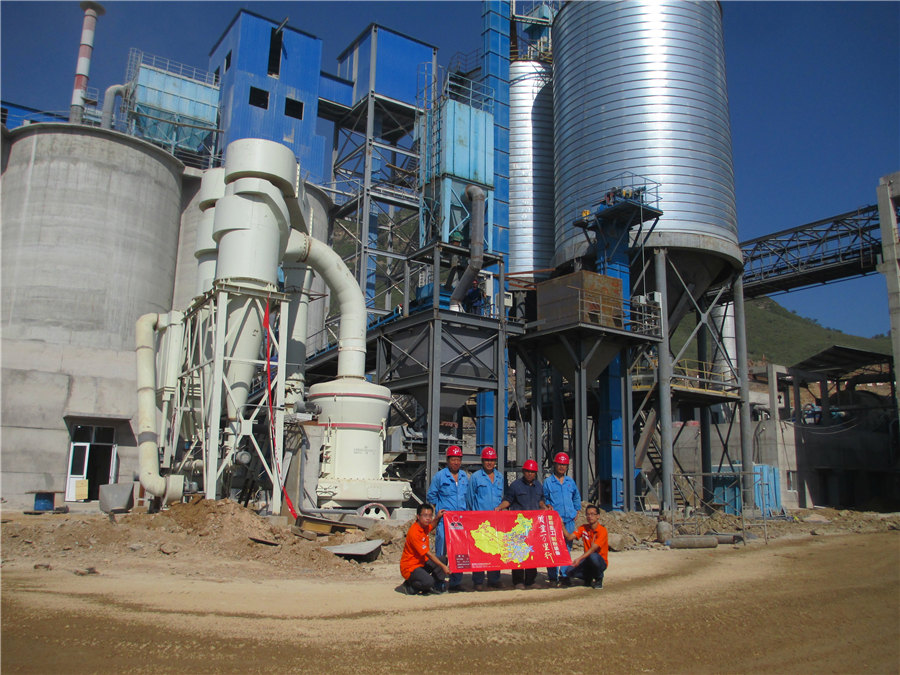
VRM In Cement Plant Maximize Energy Saving CNBMSINOMA
Vertical roller mill manufacturers Vertical roller mill or VRM is a largescale grinding equipment designed for pulverizing cement raw meal, cement clinker, slag, coal, fly ash, limestone, and other hard grinding materialIt integrates grinding, drying, separation, and conveying in one machine The equipment is widely used in many industries such as cement, electric power, metallurgy Cement Mill; Vertical Roller Mill; Cement Mill Separator; Steel Balls for Ball Mill; All the equipment in the cement plant will be built in our factory energysaving and environmentfriendly cement production scheme Advanced Production Equipment Our factory is equipped with a series of advanced manufacturing machines such as Φ8m Cement Plant for Sale Cement Plant Equipment Design AGICO CementKawasaki largescale and energysaving cement plants have so far been supplied around the world and admired by users for the stable running performance has established in China three joint companies, ACK, CKM and CKE, for engineering, procurement and manufacturing of cement plant equipment (Cement Mill 115tons/hour)Cement Plant Kawasaki Heavy IndustriesCement Vertical Mill Cement vertical mill is a kind of highefficiency and closedcircuit grinding equipment, which integrates crushing, drying, grinding, and grading functions In recent years, it has been widely used in new dry cement production lines and gradually replaced ball mill as the main cement equipment in large cement plantsIt not only has a high energy utilization rate and 5 Costsaving Tips for Portland Cement Manufacturers
.jpg)
Indian Cement Sector CMA
2021年7月28日 Energy efficiency in a cement plant is measured as a combination of two factors, viz, Cement Mill Ball Mill Closed Circuit: 2320: Cement Mill Ball Mill with HPRG: 065: Packing Plant: SOx and NOx emissions that require additional power from corresponding ancillary equipment(s)Practical advises to save costs in your Cement plant (complete equipment modification ) – Very Important !!! Leave a Comment / HOME / By admin Previous Post Table Energy saving effect of the vertical roller mill vertical cement mill, vertical coal mill Reference 111 Item : Automatic input facilities for waste tires:Practical advises to save costs in your Cement plant (complete INFINITY FOR CEMENT EQUIPMENT Main Menu Home Page; Contact US; ATTENTION ATTENTION !!!! False air is mostly present in the following areas of a cement plant: * Raw mill grinding area HG,” Possibile ways of saving energy on cement production”, Zement KalkGips, 1992, No5, 222 230Sources of False Air INFINITY FOR CEMENT EQUIPMENTGrinding equipment in the cement industry Barmac screen This section describes measures to improve energy efficiency for the finish grinding process in cement plants 52 Vertical roller mill for Buzzi, S, Sassone, G, 1993 Optimization of clinker cooler operation [82] Birch E Energy savings in cement kiln systems An overview of energy savings measures for cement industries
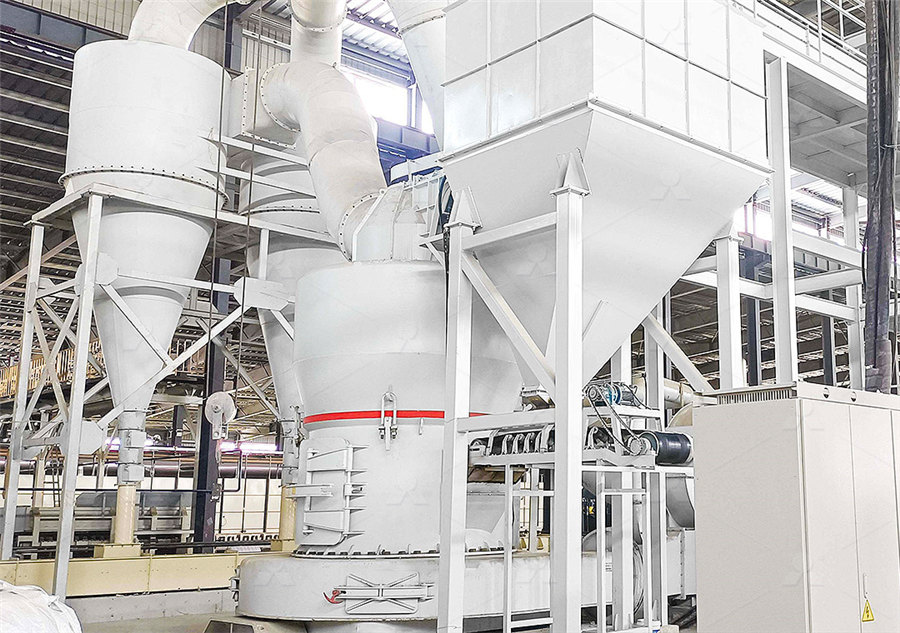
Optimizing Electrical Energy Consumption In Cement Process Plants
adopting the energy saving process and installing machines as a part of modernization 2 OPTIMISATION OF ELECTRICAL ENERGY GENERAL APPLICABILITY TO ANY CEMENT INDUSTRY Comminution Optimisation of operating parameters for ball mill In cement plant about 75% electric power is consumed by comminution equipment such as crushers and ballCement mill maintenance best practices :a guide on best practices for maintaining cement mills TO Download this post and all the books and excel sheets and my personal notes and presentations I collected about cement industry in the last 30 years click the below paypal linkCement mill maintenance best practices :a guide on best 2023年11月1日 The design of the raw material grinding system should focus on the energysaving, vertical mill grinding system because of its power AGICO CEMENT supplies EPC projects for both cement plant and single cement 8 Tips For Cement Plant Design2011年5月1日 Section/Equipment Electrical energy consumption (kWh/tonne and industrial energy users Moreover, this study will create a strong awareness about energy savings in cement industries 11 The WHR generation system design must consider the drying requirements in the cement plant raw mill to optimize the amount of A critical review on energy use and savings in the cement industries
.jpg)
Energy Efficiency Improvement and Cost Saving Opportunities for Cement
PDF On Aug 1, 2013, Ernst Worrell and others published Energy Efficiency Improvement and Cost Saving Opportunities for Cement Making An ENERGY STAR® Guide for Energy and Plant Managers Find 2024年8月23日 A cement ball mill is a kind of grinding equipment specially used in the cement production process, which is widely used in raw material grinding and finished cement grinding in cement plants Its main function is to grind cement clinker and appropriate gypsum, mixed materials, etc into fine powder for use in subsequent productionEnergysaving Ball Mill VS Cement Ball Mill JXSC MineralIn 1980, the first largescale vertical roller mill of the type MPS 3750 C for the grinding of Portland cement and slag cement was commissioned in a German cement plant The results of permanent operation so far reveal that energy savings are as much as 30 % compared to the ball millRoller mills INFINITY FOR CEMENT EQUIPMENTFor example, implementing energysaving opportunities identified through energy audits can result in up to 5% reduction in energy consumption and corresponding cost savings Keyword: Alternative fuels, energyefficient technologies, energy audits, fuel consumption, energy consumption patternsCement Mill Optimization: Practical Strategies for Enhanced
.jpg)
Energy Efficiency and Saving in the Cement Industry
2024年4月26日 Grinding and milling account for 58% of cement/concrete energy consumption These operations have an energy efficiency ranging from 6 to 25% and also offer a large opportunity for energy saving The following figure presents the cement production process Cement production processThe mill can be used for pregrinding and finish grinding This millsystem claims to have advantages of ball mill, roller mill and roller press in terms of reliability and energy savings The energy saving is claimed to be similar to roller press, around 20 % less compared to ball mill, but with a moderate circulating load and grinding pressureModern Processing Techniques to minimize cost in Cement 2016年10月5日 In this chapter an introduction of widely applied energyefficient grinding technologies in cement grinding and description of the operating principles of the related equipments and comparisons over each other in EnergyEfficient Technologies in Cement Grinding2023年11月21日 Innovation of grinding equipment Efficient and energysaving new grinding equipment such as vertical cement mills and cement roller presses will become more popular to reduce energy consumption in the grinding Trend Analysis Of Cement Production Line Design

Cement Roller Press Roller Press In Cement Plant
AGICO is a professional cement plant equipment supplier in China The cement roller press is one of our hotsales products in the cement grinding unit High Grinding Efficiency Energy saving In the cement ball mill, materials are 2021年3月30日 The cement industry is highly energyintensive, consuming approximately 7% of global industrial energy consumption each year Improving production technology is a good strategy to reduce the energy needs of a cement plant The market offers a wide variety of alternative solutions; besides, the literature already provides reviews of opportunities to Technological Energy Efficiency Improvements in Cement Industries 2021年12月31日 The cement industry is an industrial subsector with high energy intensity It represents nearly 15% of the total energy used by industries Many energysaving programs and strategies have been Investigation of Energy Saving Potential In A South African Cement Most of the Cement plants modified the dispersion box height and reduction in their Preheater exit temperature is observed Benefits: Thermal energy savings: 2 – 5 kCal/kg clinker reduction in the thermal energy consumption of the plant 62 Multi channel burner in place of conventional Burner: Conventional Burner:Everything you need to know about Thermal Energy Efficiency in Cement
.jpg)
Energy Efficiency Improvement Opportunities for the Cement
Table 4 EnergyEfficiency Opportunities Applicable to Rotary Kilns 10 Table 5 EnergyEfficiency Opportunities Applicable to Vertical Shaft Kilns 17 Table 6 Energy Efficiency Measures for Final Grinding of Products in Cement Plants 19 Table 7 Energy Efficiency Measures for Plant Wide Measures in Cement Plants 21 Table 8Cement grinding unit is also called the cement grinding plant It consists of cement ball mill, dust collector, belt conveyor, bucket elevator, cement silo, powder concentrator, etc AGICO provides highquality clinker grinders and advanced cement grinding technologyCement Grinding Unit Clinker Grinder AGICO CementRaw mill is generally called cement raw mill, raw mill in cement plant, it refers to a common type of cement equipment in the cement plantIn the cement manufacturing process, raw mill in cement plant grind cement raw materials into the raw mix, and the raw mix is sent to the cement kiln to make cement clinker, next, clinker and other admixtures will be ground into finished cement by Raw mill Cement PlantWith rising energy costs and stringent environmental regulations, optimizing your cement mill’s energy consumption can lead to significant cost savings and a smaller carbon footprint This post outlines actionable tips to improve the energy efficiency of cement mills, helping your plant operate more sustainably and profitablyCement mill energy efficiency tips : actionable tips for improving

Cement Manufacturing Machine Cement Making
Choose the right cement manufacturing machine is an important influence factor to produce highquality cement The cement making machine frequently used in cement plants includes cement rotary kiln, shaft kiln, cement vertical mill, 2019年3月8日 Association of Portland Cement (ABCP), the International Energy Agency (IEA), the Cement Sustainability Initiative (CSI) of the W orld Business Council for Sustainable Development (WBCSD), and IFCIMPROVING THERMAL AND ELECTRIC ENERGY Vertical roller mill manufacturers Vertical roller mill or VRM is a largescale grinding equipment designed for pulverizing cement raw meal, cement clinker, slag, coal, fly ash, limestone, and other hard grinding materialIt integrates grinding, drying, separation, and conveying in one machine The equipment is widely used in many industries such as cement, electric power, metallurgy VRM In Cement Plant Maximize Energy Saving CNBMSINOMACement Mill; Vertical Roller Mill; Cement Mill Separator; Steel Balls for Ball Mill; All the equipment in the cement plant will be built in our factory energysaving and environmentfriendly cement production scheme Advanced Production Equipment Our factory is equipped with a series of advanced manufacturing machines such as Φ8m Cement Plant for Sale Cement Plant Equipment Design AGICO Cement
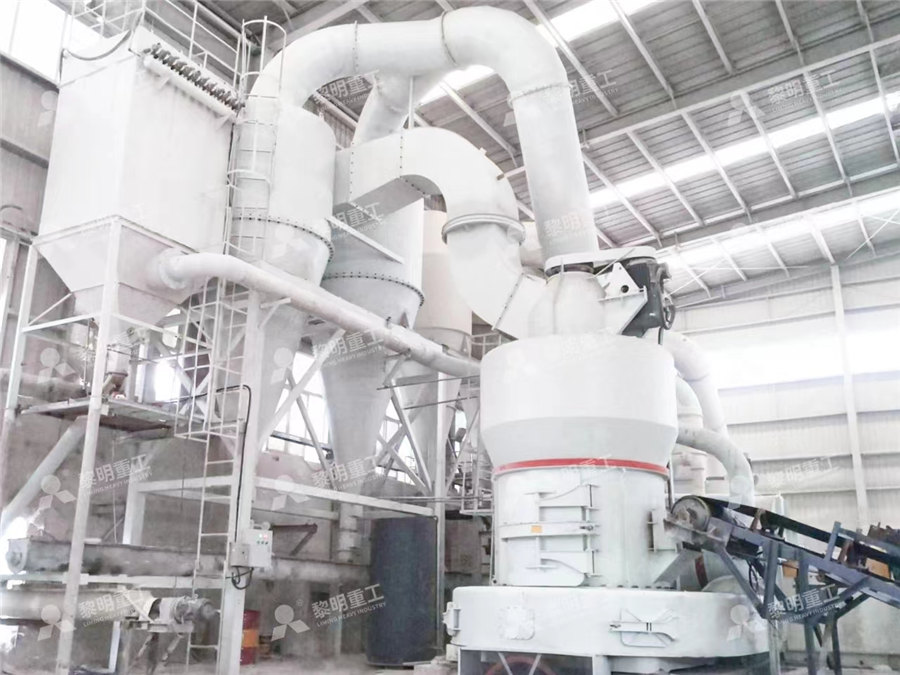
Cement Plant Kawasaki Heavy Industries
Kawasaki largescale and energysaving cement plants have so far been supplied around the world and admired by users for the stable running performance has established in China three joint companies, ACK, CKM and CKE, for engineering, procurement and manufacturing of cement plant equipment (Cement Mill 115tons/hour)Cement Vertical Mill Cement vertical mill is a kind of highefficiency and closedcircuit grinding equipment, which integrates crushing, drying, grinding, and grading functions In recent years, it has been widely used in new dry cement production lines and gradually replaced ball mill as the main cement equipment in large cement plantsIt not only has a high energy utilization rate and 5 Costsaving Tips for Portland Cement Manufacturers2021年7月28日 Energy efficiency in a cement plant is measured as a combination of two factors, viz, Cement Mill Ball Mill Closed Circuit: 2320: Cement Mill Ball Mill with HPRG: 065: Packing Plant: SOx and NOx emissions that require additional power from corresponding ancillary equipment(s)Indian Cement Sector CMAPractical advises to save costs in your Cement plant (complete equipment modification ) – Very Important !!! Leave a Comment / HOME / By admin Previous Post Table Energy saving effect of the vertical roller mill vertical cement mill, vertical coal mill Reference 111 Item : Automatic input facilities for waste tires:Practical advises to save costs in your Cement plant (complete
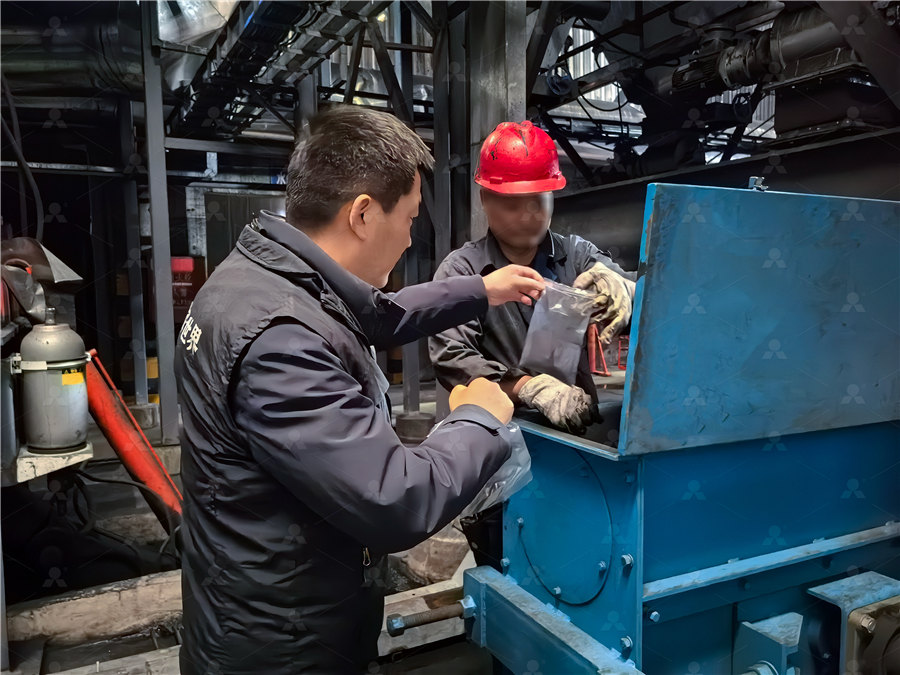
Sources of False Air INFINITY FOR CEMENT EQUIPMENT
INFINITY FOR CEMENT EQUIPMENT Main Menu Home Page; Contact US; ATTENTION ATTENTION !!!! False air is mostly present in the following areas of a cement plant: * Raw mill grinding area HG,” Possibile ways of saving energy on cement production”, Zement KalkGips, 1992, No5, 222 230Grinding equipment in the cement industry Barmac screen This section describes measures to improve energy efficiency for the finish grinding process in cement plants 52 Vertical roller mill for Buzzi, S, Sassone, G, 1993 Optimization of clinker cooler operation [82] Birch E Energy savings in cement kiln systems An overview of energy savings measures for cement industries