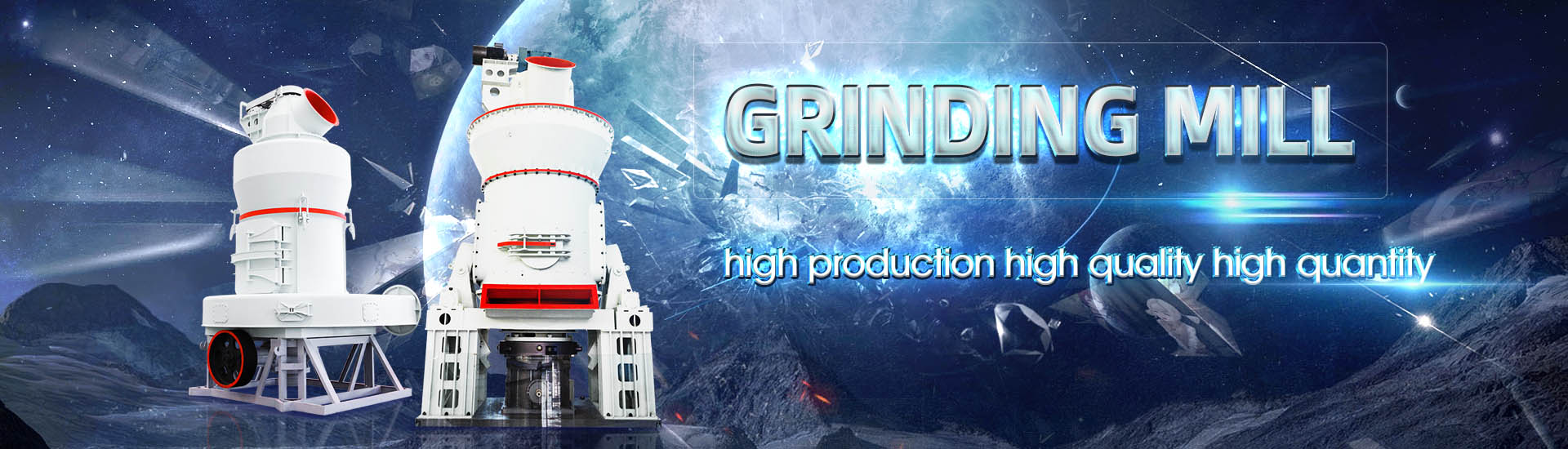
Cement lime and gypsum grinding equipment
.jpg)
Efficient processes for grinding and separation Cement Lime
In 1925, Christian Pfeiffer founded the company and set up a workshop in Beckum for the production of vendor parts for the cement industry Five years later, the first Christian Pfeiffer mill diaphragms were registered for patent approval In 1939, the Heyd separator technology was established on the European market 展开2017年4月21日 Grinding with propylene glycol generates approximately 800 Cm 2 /gram cement more surface than grinding without an aid, given the same energy consumption the most CEMENT GRINDING SYSTEMS INFINITY FOR CEMENT EQUIPMENTTogether with the product of the existing mill dedusting system, the cyclone and the filter products comprised the finished cement, which is transported to the cement storage via existing equipment Figure 3 shows the flowsheet of the Energy and cost savings by retrofitting a stateofthe 2021年4月19日 Grinding of finished cement is performed in a single stage, intergrinding materials with very different grindabilities This intergrinding process has many different interactions among the different components of the finished cement In a context of developing more sustainable and less energy intensive processes, it is important to understand the Resistance to Grinding and Cement Paste Performance of Blends
.jpg)
Cement Manufacturing Process INFINITY FOR
The principal raw materials for cement manufacturing are: Limestone; Silica and alumina from basalt , shale or sand; Iron from iron ore or steel mill scale Sand stone; Pumice (volcanic ash for Portland Pozzolana cement ) Gypsum Gypsum dehydration potential and mean residence time of a stirred media mill during ultrafine grinding of cement clinker and gypsum All VDZ Vertical stirred media mill All VDZ Bildquelle Re Are you interested in the latest news from the cement industry as well as the lime and gypsum sectors? Then subscribe to our free newsletter! 14 2 Gypsum dehydration during cement production ZKG1 Introduction Two mill systems are employed for most coal grinding applications in the cement industry These are, on the one hand, vertical roller mills (VRM) that have achieved a share of almost 90 % and, on the other hand, ball mills whose share decreased to just over 10 %MPS mills for coal grinding Cement Lime Gypsum ZKGFor Siam City Cement Public Co, Ltd (SCCC) from Thailand, KHD Humboldt Wedag engineered and commissioned a new roller pressbased raw meal grinding plant at SCCC’s factory 1 located in the Saraburi province With the new Comflex ® grinding unit, the client is able toKHD hands over a new grinding plant in Thailand Cement Lime Gypsum

GCP Applied Technologies receives European patent on sustainable cement
GCP Applied Technologies receives European patent on sustainable cement grinding methods Are you interested in the latest news from the cement industry as well as the lime and gypsum sectors? Then subscribe to our free newsletter! Cement grinding additive for enabling PVC equipment use (22) 16092014 (45) In order to realise efficient comminution in limited size ranges with a minimum number of mills, ECRA has developed the concept of “multistage grinding” of cement 2 Multistage grinding: An approach for future comminution 21 The general idea of multistage grinding Separate grinding systems for raw meal and cement are state of the artStudy on the production of cements using a multistage grinding Cemtec Cement and Mining Technology GmbH received an order from Daesung Machinery Co Ltd, South Korea, for the supply of main process equipment for the fine grinding of fly ash at 6900 cm 2 /g (Blaine), comprises one ball mill Ø 30 x 70 m and one latest generation separator CTC045 Beforehand, several trials took place in the presence of the customer, at the RD Cemtec’s fly ash grinding equipment delivered to Korea Cement Lime The final manufacturing stage at a cement plant is the grinding of cement clinker from the kiln, mixed with 45% gypsum and possible additives, into the final product, cement In a modern cement plant the total consumption of electrical energy is about 100 kWh/t The cement grinding process accounts for approx 40% if this energy consumptionCEMENT GRINDING SYSTEMS INFINITY FOR CEMENT EQUIPMENT
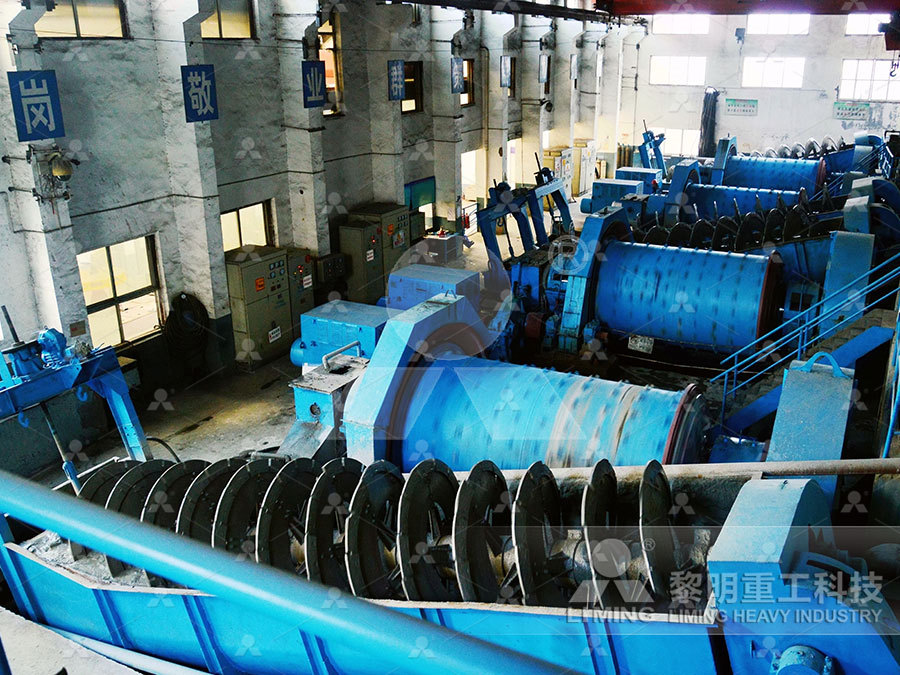
Everything you need to know about clinker/cement
Everything you need to know about clinker/cement Grinding if You read and understand this article , you will be ready to be a cement grinding area manager FEED AND FEED SYSTEM Feed Temperature Plants with satellite coolers However, as greenfield cement plant projects remain scarce, upgrades to existing cement plants will become relatively more important; equipment relating to upgrades (ie, excluding servicerelated spending) will move from representing a quarter of the total cement manufacturing equipment capital spending in 2017 to over 40 % by 2022Cement plant equipment market to reach US$ 90 billion by 2022Are you interested in the latest news from the cement industry as well as the lime and gypsum sectors? Then subscribe to our free newsletter! 14 times a year you will find out about: » the latest findings from research development » current market information » all events of the industries on one click! » product and company newsAlternate grinding of raw material and clinker Cement Lime Gypsum2024年11月23日 Cement Extraction, Processing, Manufacturing: Raw materials employed in the manufacture of cement are extracted by quarrying in the case of hard rocks such as limestones, slates, and some shales, with the aid of blasting when necessary Some deposits are mined by underground methods Softer rocks such as chalk and clay can be dug directly by Cement Extraction, Processing, Manufacturing Britannica
.jpg)
Gambia has decided for Cemtec Cement Lime Gypsum ZKG
In January 2017, right after the newly elected president of Gambia came to power endorsed with the slogan “Gambia has decided”, Cemtec Cement and Mining Technology and Salam Cement Company signed the contract for engineering and supply of the first cement grinding plant in the country, to be located in BanjulZKG Cement Lime Gypsum Newsletter It is especially safe due to the automatic locking of collecting vessel and grinding more Issue 04/2024 CN U Special equipment for burning alternative fuel in cement kiln (22) 06052023 (43) 29032024 (57) Cyclone separator Cement Lime Gypsum ZKG2023年12月26日 As we all know, the dryprocess cement production line is commonly used in the cement industry The new type of dryprocess cement production process includes four main sections: Prehomogenization of raw materials, homogenization of raw materials, clinker firing, cement grinding, etc Raw material conveying system The raw material, including limestone, 6 Cement Equipment For Dryprocess Cement Production LineAfter two hours of grinding, 27 % C02, and after 20 grinding hours 46% C02 was found, although initially no C02 was detectable This indicates a carbonatation of the lime Wear rates of grinding balls Wear rates of grinding balls for wet and dry grinding of cement raw mix slurry (wet) and cement clinker (dry) (see table 751)Grinding ball data INFINITY FOR CEMENT EQUIPMENT

Cement Equipment, Cement Plant Equipment Cement Plant
AGICO CEMENT is a cement plant manufacturer supplies cement equipment with high quality and competitive price, including cement mill, Cement grinding plants; Lime Calcination Plant; Biochar production plant; We also provide customized solutions for cement manufacturing, gypsum board making, aac block manufacturing, lime production, Are you interested in the latest news from the cement industry as well as the lime and gypsum sectors? Then subscribe to our free newsletter! 14 times a year you will find out about: » the latest findings from research development » current market information » all events of the industries on one click! » product and company newsInnovations and trends in grinding technology Cement Lime Gypsum Under a contract with Bilim Makina Insaat San, Turkey as general contractor, Humboldt Wedag GmbH received the order for engineering and equipment supply for a clinker grinding unit (Fig)The new semifinish grinding system, equipped KHD roller press technology for clinker grindingFor slag grinding plant, ball mill generally causes problems of dust accumulation, low grinding efficiency and high grinding temperature The particle size and gradation distribution of the finished product are not as good as those of the Slag Grinding Plant GGBS Plant Slag Mill, Slag

What is the purpose of adding gypsum in cement?
Gypsum is a mineral and is hydrated calcium sulfate in chemical form Gypsum plays a very important role in controlling the rate of hardening of the cement During the cement manufacturing process, upon the cooling of clinker, a small amount of gypsum is introduced during the final grinding process Gypsum is added to control theThe following increase in mill throughput was reported: 1030 % when grinding Portland cement N° 375 (equal to compressive strength of 5321 psi after 28 days), and 25 50 Ofo when grinding Portland cement No 475 (equal to 6740 psi) Coating of grinding mediaFinish grinding INFINITY FOR CEMENT EQUIPMENTIn January 2014, CEMTEC Cement and Mining Technology GmbH from Enns, Austria signed a contract with LLC Stroytel´nye Materialy, a subsidiary of the German HeidelbergCement, for an increase in cement grinding capacity at its plant located in Sterlitamak in the Republic of Bashkortostan, RussiaNew cement grinding line from CEMTEC Cement Lime GypsumPfeiffer for their modular “ready2grind” cement grinding concept All the equipment is also known from conventional VRM grinding plants [1] It includes feed hoppers and weigh Are you interested in the latest news from the cement industry as well as the lime and gypsum sectors? Then subscribe to our free newsletter! 14 times a year you Latest trends in modular cement grinding plants Cement Lime Gypsum
.jpg)
Issue 10/2020 Cement Lime Gypsum ZKG
The conversion or replacement of existing Aumund conveying equipment, as well as nonAumund equipment has been an integral part of the technological expertise of the Aumund Group for more than 302023年11月21日 When discussing the development trend of future cement production line equipment, the following are some specific equipment and technology explanations: Kiln Technology Innovation Kiln technologies such as rotary kiln and vertical kilns will be further optimized, adopting advanced combustion and cooling technologies to improve the production Trend Analysis Of Cement Production Line Design Cement EquipmentThe time allowed for mixing, transporting and placing plays a important role in strength, composition and workabilty of concrete As gypsum retards the process of hydration, it is termed as retarding agent of cement Effects of Gypsum on Cement Gypsum prevents Flash Setting of cement during manufacturing It retards the setting time of cementRole of Gypsum in Cement and its Effects – theconstructorAre you interested in the latest news from the cement industry as well as the lime and gypsum sectors? Then subscribe to our free newsletter! 14 times a year you will find out about: » the latest findings from research development » current market information » all events of the industries on one click! » product and company newsRamco Cement Limited orders three Loesche vertical roller mills
.jpg)
Energy and cost savings by retrofitting a stateofthe
Together with the product of the existing mill dedusting system, the cyclone and the filter products comprised the finished cement, which is transported to the cement storage via existing equipment Figure 3 shows the flowsheet of the 2021年4月19日 Grinding of finished cement is performed in a single stage, intergrinding materials with very different grindabilities This intergrinding process has many different interactions among the different components of the finished cement In a context of developing more sustainable and less energy intensive processes, it is important to understand the Resistance to Grinding and Cement Paste Performance of Blends The principal raw materials for cement manufacturing are: Limestone; Silica and alumina from basalt , shale or sand; Iron from iron ore or steel mill scale Sand stone; Pumice (volcanic ash for Portland Pozzolana cement ) Gypsum Cement Manufacturing Process INFINITY FOR Gypsum dehydration potential and mean residence time of a stirred media mill during ultrafine grinding of cement clinker and gypsum All VDZ Vertical stirred media mill All VDZ Bildquelle Re Are you interested in the latest news from the cement industry as well as the lime and gypsum sectors? Then subscribe to our free newsletter! 14 2 Gypsum dehydration during cement production ZKG
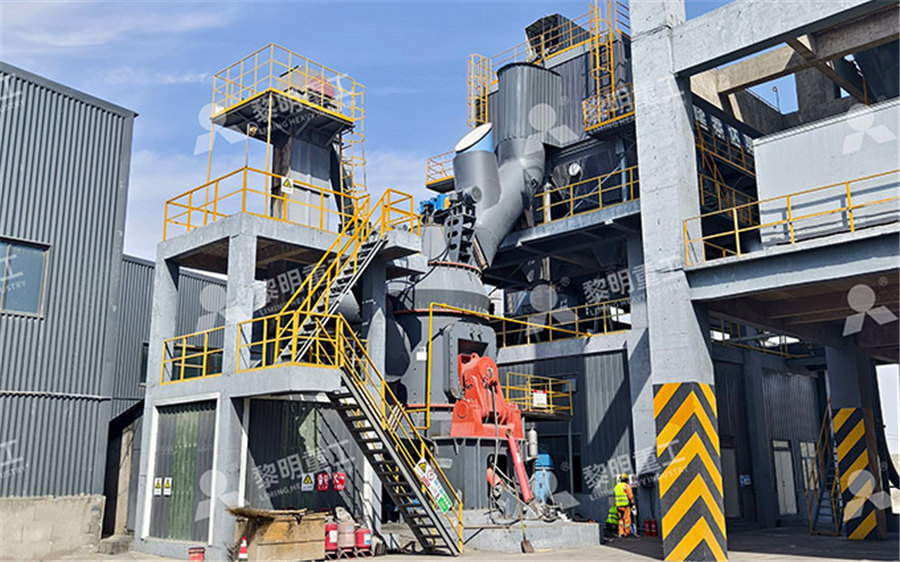
MPS mills for coal grinding Cement Lime Gypsum ZKG
1 Introduction Two mill systems are employed for most coal grinding applications in the cement industry These are, on the one hand, vertical roller mills (VRM) that have achieved a share of almost 90 % and, on the other hand, ball mills whose share decreased to just over 10 %For Siam City Cement Public Co, Ltd (SCCC) from Thailand, KHD Humboldt Wedag engineered and commissioned a new roller pressbased raw meal grinding plant at SCCC’s factory 1 located in the Saraburi province With the new Comflex ® grinding unit, the client is able toKHD hands over a new grinding plant in Thailand Cement Lime Gypsum GCP Applied Technologies receives European patent on sustainable cement grinding methods Are you interested in the latest news from the cement industry as well as the lime and gypsum sectors? Then subscribe to our free newsletter! Cement grinding additive for enabling PVC equipment use (22) 16092014 (45) GCP Applied Technologies receives European patent on sustainable cement In order to realise efficient comminution in limited size ranges with a minimum number of mills, ECRA has developed the concept of “multistage grinding” of cement 2 Multistage grinding: An approach for future comminution 21 The general idea of multistage grinding Separate grinding systems for raw meal and cement are state of the artStudy on the production of cements using a multistage grinding
.jpg)
Cemtec’s fly ash grinding equipment delivered to Korea Cement Lime
Cemtec Cement and Mining Technology GmbH received an order from Daesung Machinery Co Ltd, South Korea, for the supply of main process equipment for the fine grinding of fly ash at 6900 cm 2 /g (Blaine), comprises one ball mill Ø 30 x 70 m and one latest generation separator CTC045 Beforehand, several trials took place in the presence of the customer, at the RD The final manufacturing stage at a cement plant is the grinding of cement clinker from the kiln, mixed with 45% gypsum and possible additives, into the final product, cement In a modern cement plant the total consumption of electrical energy is about 100 kWh/t The cement grinding process accounts for approx 40% if this energy consumptionCEMENT GRINDING SYSTEMS INFINITY FOR CEMENT EQUIPMENT