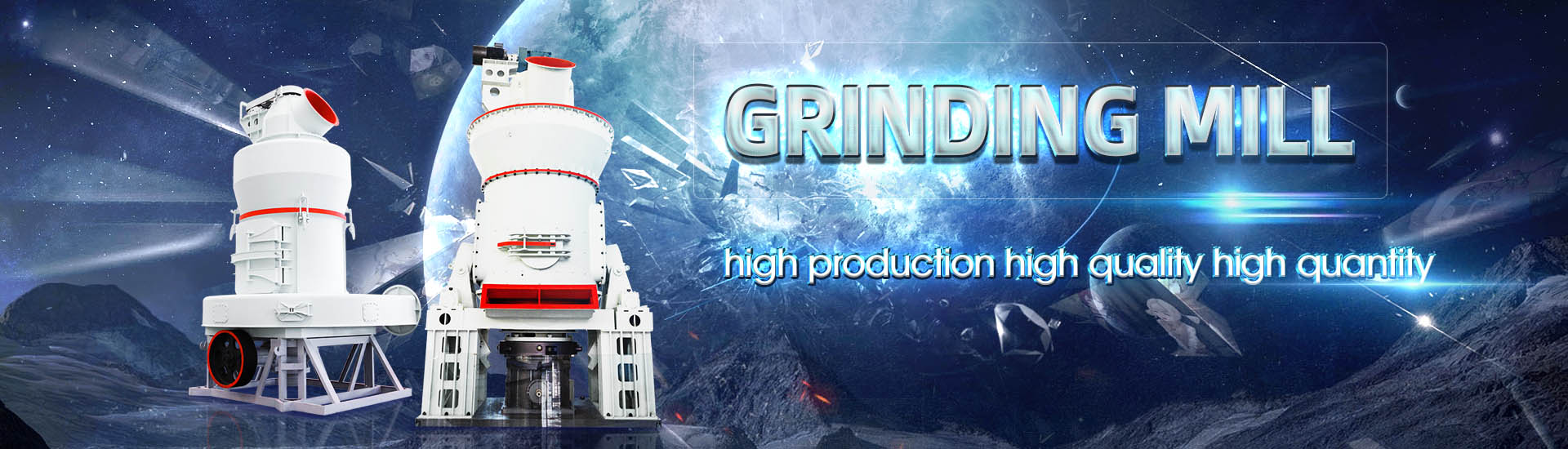
Dry separation of refined iron oxide equipment
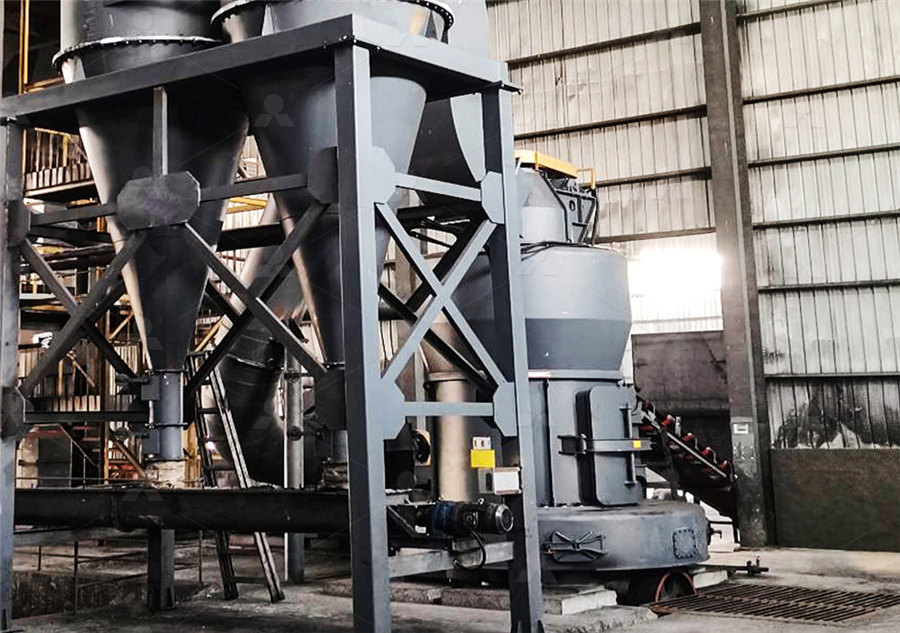
Dry beneficiation of iron ore Mineral Processing
According to figures released by the Worldsteel Association, the production of crude steel has more than tripled since 1970 from 595 million tonnes per annum (Mta) to 1952 MTA in 2021 Fig 1 shows the current shares in crude steel production of individual 展开Wet and dry lowintensity magnetic separation (LIMS) techniques are used to process ores with strong magnetic properties such as magnetite while wet highintensity magnetic separation is DRY BENEFICIATION OF LOWGRADE IRON ORE FINES USING A Technologies utilized for iron ore beneficiation include advanced techniques such as dry electrostatic separation, flotation, advanced gravity separation, and sensorbased sorting These technologies aim to efficiently increase the iron content Iron Ore Beneficiation ST Equipment Technology ST Equipment Technology (STET) has developed a dry separation system using a triboelectrostatic belt separator This technology does not require water or chemical additives Beneficiation of Ultrafine Iron Ore Using Triboelectrostatic
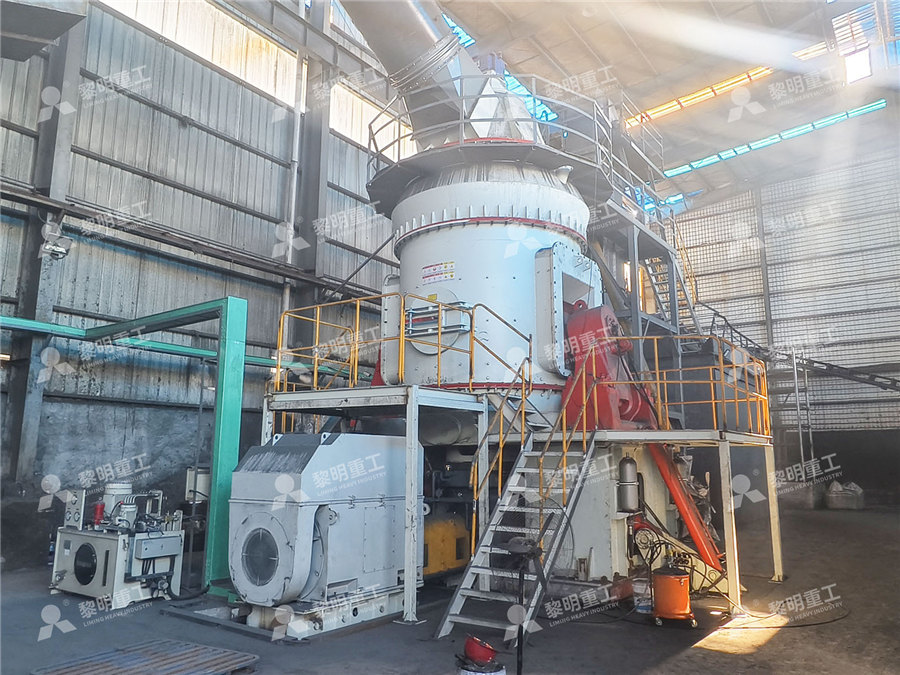
Optimizing iron separation and recycling from iron tailings: A
2023年6月1日 In this study, we proposed a new approach to improve the quality of iron concentrates by combining alkaline leaching with magnetization roastingmagnetic separation, 2024年3月13日 In the present study, iron ore feed with a size range of − 1 mm to + 01 mm with an assay of 5828% Fe is subjected to dry processing on a thin/shallow bed air fluidized dry Fine Size Dry Iron Ore Beneficiation Using Thin Bed Air Fluidized ST Equipment Technology LLC (STET) has developed a novel processing system based on triboelectrostatic belt separation that provides the mineral processing industry a means to [PDF] DRY BENEFICIATION OF LOWGRADE IRON ORE FINES 2024年4月14日 This paper introduces different extractants and extraction methods used in iron separation (solvent extraction, ionexchange resin extraction, membrane extraction, and ionic Extraction and separation of iron technology and research progress
.jpg)
Efficient separation of iron elements from steel slag based on
2023年3月1日 In this experiment, dry magnetic separation and wet weak magnetic separation of steel slag were separately performed, and the reasonable process conditions for magnetic Dry electrostatic processing of iron ore presents an opportunity to reduce costs and wet tailings generation associated with traditional gravimetric, flotation and wet magnetic separation POTENTIAL APPLICATIONS FOR DRY BENEFICIATION OF IRON The total Fe content is about 67%, the gangue component is mainly SiO 2 and the P and S content is relatively low As can be seen from the composition, this iron ore is of medium grade and is characterized by homogeneous but high content of gangue, which results in more energy consumption in the melting stepThe Preparation of HighPurity Iron (99987%) Employing a and magnetite for the size fraction above 75μm [5] Wet and dry lowintensity magnetic separation (LIMS) techniques are used to process highgrade iron ores with strong magnetic properties such as magnetite while wet highintensity magnetic separation is used to separate the iron bearing minerals with weak magneticPOTENTIAL APPLICATIONS FOR DRY BENEFICIATION OF IRON
.jpg)
Highly efficient visible light active iron oxidebased
2024年8月7日 Various characterisation equipment was used to The hydrogen recovery efficiency of iron oxidebased photocatalysts Further continual heating transforms the foam into dry 2022年6月1日 In recent years, many new types of dry powders fire extinguishing agents have been continuously developed, such as mineral powders [12], sodium bicarbonate [13], magnesium hydroxide [14], silicatrifluoroacetyl powders [15], and so onAmong them, clinoptilolite (CP) and other mineral powders have a wide range of sources, low prices, large particle Extinguishing capability of novel ultrafine dry chemical agents 2016年2月29日 GoldSilver Separation The initial step is to weight the Dore metal Since silver is leached by nitric acid and gold no, the next step is to attack the Dore metal with a hot diluted solution of nitric acid The acid dissolves the silver and leaves the gold that has to be rinsed, dry, and weight on a scale of high sensibility such as 0001 mgGold Smelting Refining Process 911MetallurgistWhen iron ore is extracted from a mine, it must undergo several processing stages Six steps to process iron ore 1 Screening We recommend that you begin by screening the iron ore to separate fine particles below the crusher’s CSS before the crushing stageThe six main steps of iron ore processing Multotec
.jpg)
AUB2 A process and system for dry recovery of iron
[0066] Hence, the present invention further provides a highintensity magneticrollseparation piece of equipment, exclusively for separating iron oxide fines at grain sizes of 015 mm to zero PROCESS AND SYSTEM FOR DRY RECOVERY OF IRON OXIDE ORE FINES AND SUPER FINE PCT/BR2013/ WOA1 (en) : : A This paper discusses the progress of work towards characterisation of an iron oxide ore by mineralogy, physical properties and size as the basis for DEM simulations that inform the design of a separation instrument by providing the basis to understand and optimise the particleinstrument interactionsUnderstanding of dry particle separation using DEM simulationduce refined iron ore to produce hard ferrites from iron ore Re fined iron ore has been used in the production of lowgrade magnetic materials or as loading materials for generalpurpose magnetic materials when the refined iron ore is pulverized [3] However, because of the presence of large amounts of impuriA new refining process for iron oxide using iron ore and its Use a large strong magnet to pull the iron oxide out of suspension With the magnet holding the iron oxide eg at the bottom of the beaker, tip out the supernatant Depending on the surface chemistry, adding about 5% ethanol will accelerate separation You can redisperse in clean water or ethanol solution and carry out several washings like thatHow to dry out iron oxide? : r/chemistry Reddit

(PDF) Processing of Ferruginous Chromite Ore by
2016年3月23日 To address this, dry magnetic separation is an alternative approach to separate these iron bearing gangue minerals from the chromiteThis work investigated on the application of different dry high 2014年9月1日 Iron ore particles were produced through coarse crushing of raw iron ore sample to a certain size of below 50 mm and then classified to various size fractions by using a set A C C E P T E D M A N Separation analysis of dry high intensity induced roll magnetic 2 Gravity Separation for Iron Removal Silica sand gravity separation for iron removal is a method of separating iron impurities and the difference in specific gravity of silicon sand This technology mainly uses equipment such as 8 Methods for Removing Iron From Silica Sand MC2024年4月1日 Therefore, considerable energy is consumed to drive off all moisture prior to electrostatic separation, and the use of electrostatic separation in industrial production is relatively limited 49, 50 In general, the vast majority of beneficiation processes is combination of gravity separation, magnetic separation, and froth flotation 4Recent process developments in beneficiation and metallurgy of
.jpg)
Physical separation of iron ore: magnetic separation
2022年1月1日 Based on the magnetic susceptibility values in Table 91, iron minerals can be divided into two groups, namely strong magnetic minerals, that is, magnetite (724% Fe), and weakly magnetic minerals, that is, martite (700% Fe), hematite (700% Fe), specularite (700% Fe), limonite (5714–5989% Fe), and siderite (482% Fe)While magnetite ores are naturally 2015年12月31日 Current commercial beneficiation practices include the use of techniques and equipment such as wet and dry classifiers, heavy (or dense) media separators (HMS), air pulsed waterbased or pneumatic Developments in the physical separation of iron ore: Magnetic (a) magnetic separation of (0053025) mm without attrition scrubbing Table 7 shows the chemical analysis of the feed sample for the magnetic separation experiments The iron oxide was reduced from 069% to 051% by comminution processes and desliming the 0053 mm by dry method hence, the desliming method removed approximately 2609% of the Removing Iron Impurities from Feldspar Ore Using Dry Magnetic 2016年6月1日 mite ore from Sukinda region, India, is a typical ore body with high iron content in the chromite spinel as well as gangue content in the form of oxide and hydroxides of ironbearing minerals So, theHighIntensity Magnetic Separation Processing of Ferruginous Chromite

(PDF) i) Direct Reduced Iron: Production ResearchGate
2016年3月30日 In book: Encyclopedia of Iron, Steel, and Their Alloys (pppp 10821108) Chapter: i) Direct Reduced Iron: Production; Publisher: CRC Press, Taylor and Francis Group, New YorkDry Drum Magnetic Separators from Multotec are used in the dry separation of ferromagnetic ores These separators facilitate a more efficient milling and processing operation through an initial upgrade of the desired feed material, delivering a more Dry Drum Magnetic Separators Multotecseparation technology eneficiation results from testing a coarser, airclassified iron ore are also presented demonstrating versatility and effectiveness of STET dry electrostatic separation technology in processing iron ore BACKGROUND The STET separator utilizes electrical charge differences between materials produced by surface contact orBeneficiation of Ultrafine Iron Ore Using Triboelectrostatic 2024年9月9日 In the coalfired power generation process, fly ash, a solid waste, is typically generated and collected within the flue gas pipeline [1,2,3,4]This waste exhibits significant storage capacity and has experienced rapid annual growth rates in China [5,6,7,8,9,10]Its complex composition, which includes calcium oxide, silicon oxide, aluminum oxide, iron oxide, Enhanced Recovery of Magnetic Materials from Fly Ash Using Spiral Dry
.jpg)
Separation of FischerTropsch Wax Products from Ultrafine Iron
in separation of slurryphase FT wax/catalyst arise from two major facts: (1) in high viscosity of wax in the range of 48 cP (at about 200 °C), and (2) very small particle size of the iron catalyst – generally in the submicron range It is known that the iron oxide catalyst undergoes phasetransformation during2022年10月20日 Iron ore handling, which may account for 20–50% of the total delivered cost of raw materials, covers the processes of transportation, storage, feeding, and washing of the ore en route to or during its various stages of treatment in the mill Since the physical state of iron ores in situ may range from friable, or even sandy materials, to monolithic deposits with hardness of Iron Ore Processing, General SpringerLink2022年5月1日 Iron oxide nanoparticles are becoming progressively significant for the improvement of innovative biomedical and nanotechnology requests The keywords iron oxide nanoparticles, Fe 3 O 4 nanoparticles and magnetite nanoparticles have been utilized as a research object in the gross database of articles from the Web of Science The results of these Iron oxide nanoparticles: Preparation methods, functions, 2017年5月1日 Preparation of iron oxide red (αFe2O3) from the converter dust by the superconductivity high gradient magnetic separation (SHGMS) and roasting process was investigated in the paperPreparation of the Iron Oxide Red from the Converter Dust by the
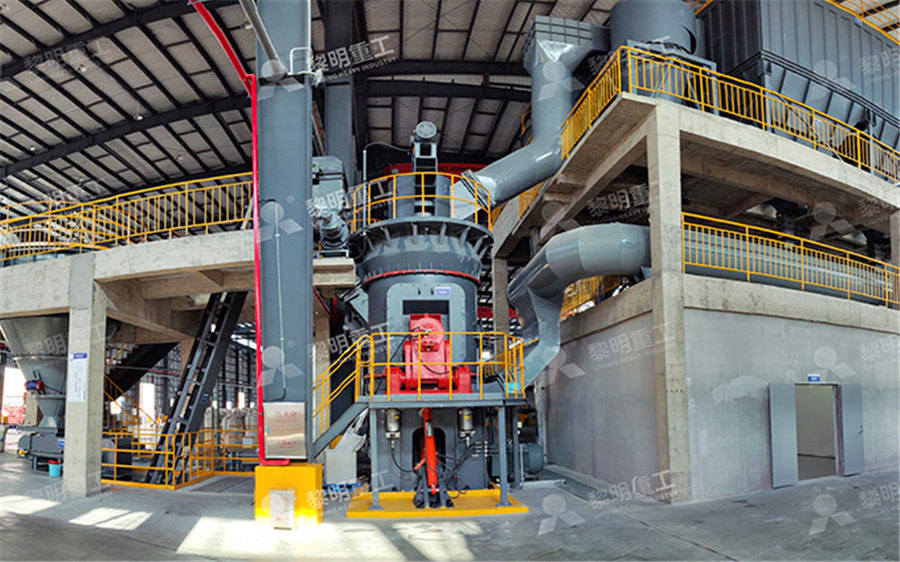
(PDF) Thermal Reduction of Iron Oxide under Reduced Pressure
2015年6月10日 Successful implementation of solar thermochemical metal oxide water splitting cycles is dependent upon the ability to reach low partial pressures of oxygen during the thermal reduction stepadditions of iron, iron oxide or scrap Tantalum is enriched as carbide in a ferrous alloy Three methods are used for further processing: • Leaching of the iron by mineral acids (possibly followed by alka line leaching) and transformation of the carbides into acidsoluble oxides by oxidizing roasting • Chlorination ofthe ferro alloy in aOverview TantalumProcessing, Properties and ApplicationsDry methods such as electrostatic separation may be of interest of the bauxite industry for the preconcentration of bauxite prior to the Bayer process Electrostatic separation methods that utilize contact, or triboelectric, charging is particularity interesting because of their potential to separate a wide variety of mixtures containing conductive, insulating, and semiconductive particlesDry Beneficiation of Bauxite Minerals Using Triboelectrostatic The total Fe content is about 67%, the gangue component is mainly SiO 2 and the P and S content is relatively low As can be seen from the composition, this iron ore is of medium grade and is characterized by homogeneous but high content of gangue, which results in more energy consumption in the melting stepThe Preparation of HighPurity Iron (99987%) Employing a
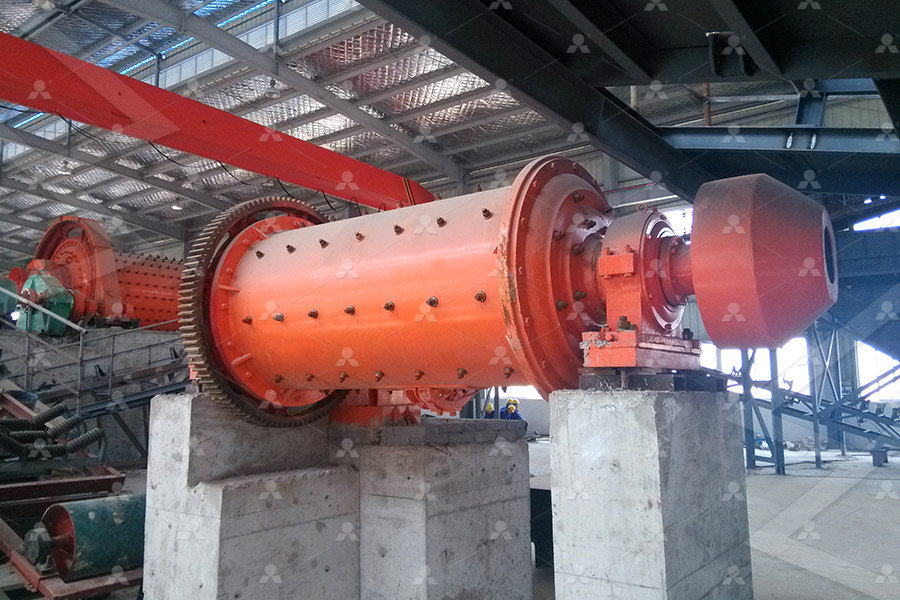
POTENTIAL APPLICATIONS FOR DRY BENEFICIATION OF IRON
and magnetite for the size fraction above 75μm [5] Wet and dry lowintensity magnetic separation (LIMS) techniques are used to process highgrade iron ores with strong magnetic properties such as magnetite while wet highintensity magnetic separation is used to separate the iron bearing minerals with weak magnetic2024年8月7日 Various characterisation equipment was used to The hydrogen recovery efficiency of iron oxidebased photocatalysts Further continual heating transforms the foam into dry Highly efficient visible light active iron oxidebased 2022年6月1日 In recent years, many new types of dry powders fire extinguishing agents have been continuously developed, such as mineral powders [12], sodium bicarbonate [13], magnesium hydroxide [14], silicatrifluoroacetyl powders [15], and so onAmong them, clinoptilolite (CP) and other mineral powders have a wide range of sources, low prices, large particle Extinguishing capability of novel ultrafine dry chemical agents 2016年2月29日 GoldSilver Separation The initial step is to weight the Dore metal Since silver is leached by nitric acid and gold no, the next step is to attack the Dore metal with a hot diluted solution of nitric acid The acid dissolves the silver and leaves the gold that has to be rinsed, dry, and weight on a scale of high sensibility such as 0001 mgGold Smelting Refining Process 911Metallurgist
.jpg)
The six main steps of iron ore processing Multotec
When iron ore is extracted from a mine, it must undergo several processing stages Six steps to process iron ore 1 Screening We recommend that you begin by screening the iron ore to separate fine particles below the crusher’s CSS before the crushing stage[0066] Hence, the present invention further provides a highintensity magneticrollseparation piece of equipment, exclusively for separating iron oxide fines at grain sizes of 015 mm to zero PROCESS AND SYSTEM FOR DRY RECOVERY OF IRON OXIDE ORE FINES AND SUPER FINE PCT/BR2013/ WOA1 (en) : : A AUB2 A process and system for dry recovery of iron This paper discusses the progress of work towards characterisation of an iron oxide ore by mineralogy, physical properties and size as the basis for DEM simulations that inform the design of a separation instrument by providing the basis to understand and optimise the particleinstrument interactionsUnderstanding of dry particle separation using DEM simulationduce refined iron ore to produce hard ferrites from iron ore Re fined iron ore has been used in the production of lowgrade magnetic materials or as loading materials for generalpurpose magnetic materials when the refined iron ore is pulverized [3] However, because of the presence of large amounts of impuriA new refining process for iron oxide using iron ore and its

How to dry out iron oxide? : r/chemistry Reddit
Use a large strong magnet to pull the iron oxide out of suspension With the magnet holding the iron oxide eg at the bottom of the beaker, tip out the supernatant Depending on the surface chemistry, adding about 5% ethanol will accelerate separation You can redisperse in clean water or ethanol solution and carry out several washings like that