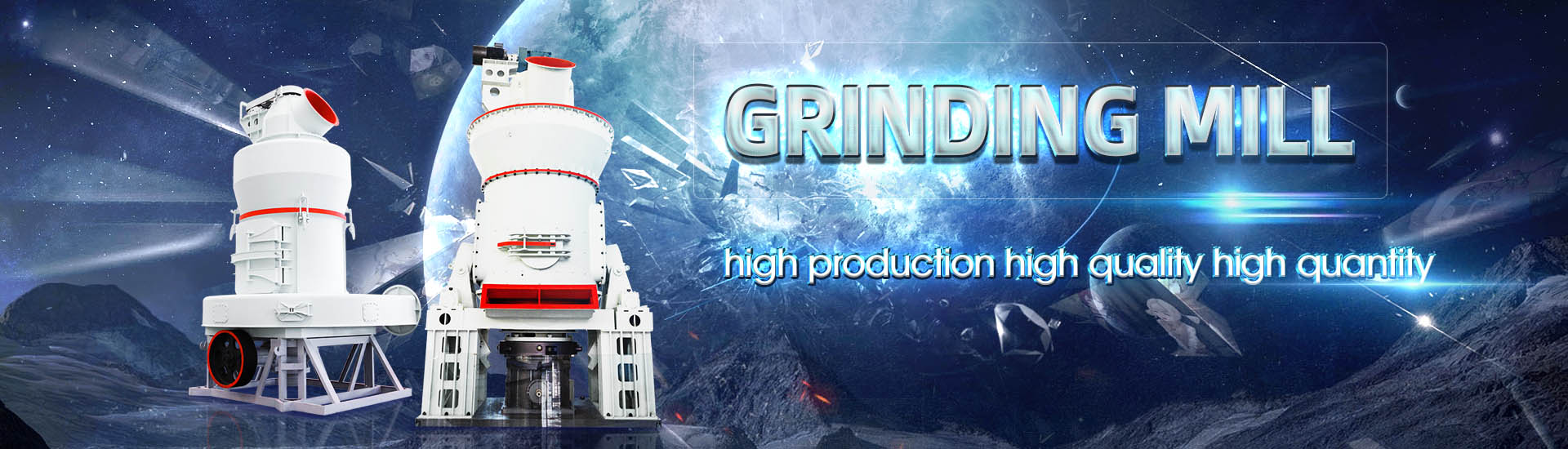
Chengdu coal raw coal mill
.jpg)
Chengdu R D CenterInnovation PlatformR
With an area of 500 m2, Chengdu R D Center is one important research platform of Sinoma Int It is outfit with raw material and fuel analysis lab, engineering lab, CDIDCS lab, technology Nanjing R D Center is outfit with nearly 100 sets of experiment instruments and Nanjing R D Center2012年5月1日 The paper presents development and validation of a coal mill model to be used for improved mill control, which may lead to a better load following capability of power plants Derivation and validation of a coal mill model for controlMills are mechanical devices used to break different types of solid materials in small pieces by grinding, crushing or cutting In pulverised coalfired power plants, a pulveriser coal mill grinds Coal Mill an overview ScienceDirect Topics
.jpg)
A unified thermomechanical model for coal mill operation
2015年11月1日 Coal mills are bottleneck in coal–fired power generation process due to difficulty in developing efficient controls and faults occurring inside the mills In this paper, a dynamic Coal mill is an important component of the thermal power plant It is used to grind and dry the moisturized raw coal and transport the pulverized coal – air mixture to the boiler Poor dynamic Modeling and Control of Coal MillCoal mill is an important component of the thermal power plant It is used to grind and dry the moisturized raw coal and transport the pulverized coal – air mixture to the boiler Poor dynamic performance of coal mill will lead to decrease in the overall efficiency of the power plant, slow load take up rate and frequent shut down(PDF) Modeling and Control of Coal Mill AcademiaThe ATOX mill will grind and dry coal containing more than 20% moisture in one operation The possibility of customersupplied parts, along with the low civil costs that accompany compact mill installation, add to the excellent economy of the ATOX coal mill Working principles The raw coal enters the mill via a rotary sluice and feed chuteATOX COAL MILL
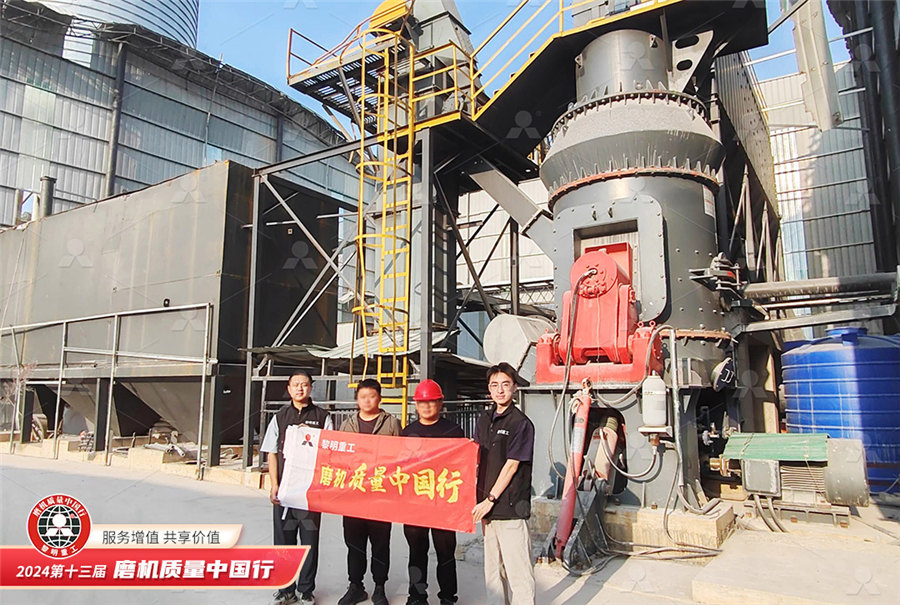
Coal Ball Mill Grinding for Different Kinds of
Raw coal enters the coal ball mill through the feeding device At this time, hot air with a temperature up to 300℃ enters the coal mill barrel from the intake pipe The raw coal falls on the lifting plate of the drying chamber and is continuously 15 Mill Wear and Ash Content in Raw Coal The coal is abrasive in nature due to the presence of hard materials like pyrites, α quartz etc, Due to the grinding nature and abrasiveness of coal, the mill parts tend to wear depending on the hours of service and A Study on 500 MW Coal Fired Boiler Unit’s Bowl Mill 2012年5月1日 A simplified design schematic of a socalled roll mill is presented in Fig 2 Raw coal is transported on a conveyor belt and dropped into the mill, where it falls onto a grinding table and is crushed by rollers Primary air, blown from the bottom of the mill, picks up fine coal particles and transports them into the classifier sectionDerivation and validation of a coal mill model for controlThis flow sheet and sampling map shows the process flow for a cement plant Key components include: 1) Raw materials like iron sand, silica sand, limestone, clay and gypsum being fed into crushers and mills 2) Processed materials being fed into kiln systems for heating and clinkering 3) Clinker being stored and transported to other cement plants or customers 4) A coal mill and Flow Sheet Kiln, Raw Mill N Coal Mill PDF Cement Concrete
.jpg)
Modeling and Control of Coal Mill
Coal mill is an important component of the thermal power pla nt It is used to grind and dry the moisturized raw coal and transport the pulverized coal ± air mixture to the boiler Poor dynamic performance of coal mill will lead to decrease in the overall efficiency of the power plant, slow load take up rate and fr equent shut downSafe operation of coal grinding systems: Raw coal silo protection against fire and explosions Safe operation of coal grinding systems: Raw coal yard management The purchasing process for coal grinding systems needs changes Talk at a virtual seminar, November 2023 Accept the probability that the fire and explosion safety of your coal grinding Best Practices and Precautions Coal Mill Safety, Explosion and A coal mill is also called a coal pulverizer or coal grinder It is a mechanical device used to grind raw coal into pulverized coal powders The most used coal mills in cement plants are airswept ball mills and vertical roller mills At present, most cement plants use coal as the main fuel in the clinker production processCoal Mill in Cement Plant2020年4月2日 Milling system in coal power plant purposely to process the raw coal to become as pulverise fuel before enter to the Coal mill motor power (kW) 0 4171 4548 4390 4586 4562 Analysis of the Coal Milling Operations to the Boiler Parameters
CFB石灰石脱硫剂制备64.jpg)
Modeling and Parameter Identification of Coal Mill
2009年9月20日 A control oriented model was then developed by Fan (1994) and Fan and Rees (1994) In 2009, coal flow and outlet temperature of mill were modelled using mass and heat balance equations for startup Safe operation of coal grinding systems: Raw coal silo protection against fire and explosions Safe operation of coal grinding systems: Raw coal yard management The purchasing process for coal grinding systems needs changes Talk at a virtual seminar, November 2023 Accept the probability that the fire and explosion safety of your coal grinding Coal Mill Safety: A Critical Aspect of Power Plant Operations Coal 2021年8月5日 In bowl mill pulveriser raw coal coming from feeder gets ground between the grinding rolls and bull ring segments installed on the revolving Bowl Bowl is made to rotate at medium speed for proper pulverization of coal Pulveriser in Thermal Power Plant Bowl Mill Ball Mill2024年10月15日 Pulverized coal drying: Raw coal is grinded in the vertical coal mill and dried by hot air (usually below 300°) into the vertical roller coal mill, which meets the drying standard of finished pulverized coal For the safety operation of the following parameter are controlled to avoid the explosion of the coal mill bag filterCashew Nutshell and Raw Coal Cogrinding for Sustainability
.jpg)
Sectional view of MBF coal mill Download Scientific Diagram
Di dalam coal mill, raw coal masuk di antara griding table dan roller untuk digiling Hasil dari penggilingan raw coal, kemudian batubara akan menuju dust collector yang berfungsi untuk menyaring Safe operation of coal grinding systems: Raw coal silo protection against fire and explosions Safe operation of coal grinding systems: Raw coal yard management The purchasing process for coal grinding systems needs changes Talk at a virtual seminar, November 2023 Accept the probability that the fire and explosion safety of your coal grinding system is nothing more than a mirageCoal Mill Safety In Cement Production IndustriesVertical Coal Mill is specially used for ultrafine grinding of raw coal and bituminous coal materials in cement, power plants, iron and steel plants and other fields The GRMC coal vertical mill produced by CHAENG adopts special structural design and production process, which is energysaving and environmentally friendlycoal grinding machine CHAENG– Interruptions in raw coal feed – Lower feeder speeds – This occurs because a minimum airflow through the coal mill must be maintained to insure that burner line velocities are not too low to allow settling of coal in the fuel lines or burner components – Not uncommon to achieve air to fuel ratios of 3 to 5 pounds of air per pound Mill Inerting and Pulverizer/Mill Explosion Mitigation
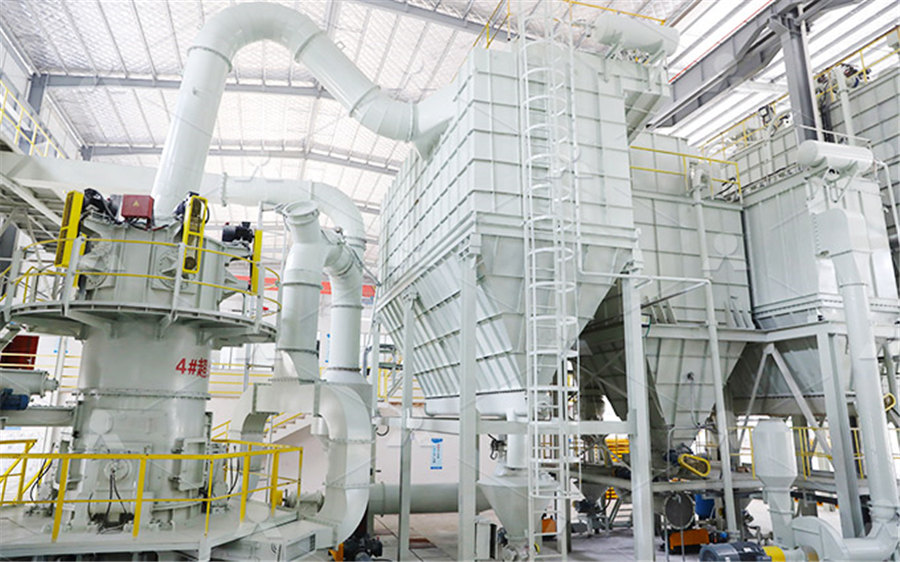
Analysis of the Coal Milling Operations to the Boiler Parameters
functions to grind the raw coal to become pulverised fuel Besides that, mill system to ensure the continuously supply pulverised coal to the firing system of the boiler Each milling circuit is independent and includes: 1 Single bunker of raw coal storage with maximum 608 tonne capacity 2 Single raw coal feeders at maximum flow rate 70 t/hIf the flow of raw coal to the coal mill is interrupted for any reason (for example: plugging, failure of the coal feeder, etc), the outlet temperature of the coal mill can climb to dangerous levels The quickly risk of explosions or fires can be extreme when the coal mill inlet temperature increases toCOAL GRINDING SYSTEMS SAFETY CONSIDERATIONS PEC You will be surprised about what has gone wrong with fire and explosion protection of your system(s) Be sure about that! Evaluation of a coal grinding system’s fire and explosion protection, including the raw coal storage and the fine coal silo storage normally can be done in one day, mostly without having to stop coal grindingSafe operation of coal grinding systems: Raw coal yard Coal Mill Safety Pte Ltd raw coal belt conveyor raw coal silo (bunker) recirculatingprocess air coal grinding system structure stand alone PF silos bagfilter raw coal stockyard CO 2 mill mill low O 2 process air from precalciner bagfilter Raw coal stockyard Raw coal belt conveyorSafety considerations when purchasing a standalone coal mill
.jpg)
A unified thermomechanical model for coal mill operation
2015年11月1日 The coal mill grinds the raw coal into fine powder and hot air entering the mill dries and carries the pulverized coal to the burners of the furnace Maffezzoni (1986) emphasized that coal mills are the primary cause of slow load following capability and regular plant shutdowns2024年1月11日 With a vertical roller mill (VRM) VRMs consist of a rotating table or bowl and rollers 1 To grind the coal, feed raw or initially crushed coal into the mill which is then ground between the rotating components; 2 Finally, hot air removes moisture, carries the pulverized coal out, and a classifier segregates the particles; Here is all you need to know about the VRM:How to Process Coal into Pulverized Coal in 5 Steps?2022年3月25日 Tumbling mill of thermal power plant, grinding the raw coal for the boiler, has high energy consumption, and pulverizing capability is usually used for representing the efficiency of tumbling mill(PDF) A Modeling and Optimizing Method for Electricity Current 2020年8月12日 This study shows the performance of a currently running vertical roller coal mill (VRM) in an existing coalfired power plant In a power plant, the coal mill is the critical equipment, whose An investigation of performance characteristics and energetic
.jpg)
How does a Coal Mill Work? ball mills supplier
Raw Coal Mill Raw coal mills work by crushing the raw coal into small particles and then drying it in a hot air fan The dried coal powder is then transported to the combustion chamber where it is burned to generate heat The process of generating heat from raw coal is similar to that of pulverizer coal mills2021年8月1日 Yukio et al [7] proposed a model consisting of blending, grinding and classifying processes for pulverizer control Agarawal et al [8] differentiated coal powder into ten size groups, divided the bowl mill into four zones, and developed a unified model Palizban et al [9] derived nonlinear differential mass equations of raw coal, recirculation coal and suspension coal in Coal mill model considering heat transfer effect on mass Coal grinding mills LOESCHE coal grinding mills are distinguished by characteristics that improve efficiency, safety and environmental protection, from the standard version to topoftherange installations Special versions are available with characteristics that meet special safety regulation or output control requirementsCoal Mills for Cement Plants LoescheThe pulverized coal is taken out of the mill by hot air Advantages Compared with the vertical roller mill, the advantages of airswept ball mill are strong adaptability to raw coal quality, simple operation and low investment cost; the disadvantages are high power consumption and high noise Vertical Roller Mill Vertical Roller Coal MillCoal Mill in Cement Plant Vertical Roller Mill AirSwept Ball Mill
.jpg)
(PDF) Modeling and Control of Coal Mill Academia
Coal mill is an important component of the thermal power plant It is used to grind and dry the moisturized raw coal and transport the pulverized coal – air mixture to the boiler Poor dynamic performance of coal mill will lead to decrease in the overall efficiency of the power plant, slow load take up rate and frequent shut downThe ATOX mill will grind and dry coal containing more than 20% moisture in one operation The possibility of customersupplied parts, along with the low civil costs that accompany compact mill installation, add to the excellent economy of the ATOX coal mill Working principles The raw coal enters the mill via a rotary sluice and feed chuteATOX COAL MILLRaw coal enters the coal ball mill through the feeding device At this time, hot air with a temperature up to 300℃ enters the coal mill barrel from the intake pipe The raw coal falls on the lifting plate of the drying chamber and is continuously Coal Ball Mill Grinding for Different Kinds of 15 Mill Wear and Ash Content in Raw Coal The coal is abrasive in nature due to the presence of hard materials like pyrites, α quartz etc, Due to the grinding nature and abrasiveness of coal, the mill parts tend to wear depending on the hours of service and A Study on 500 MW Coal Fired Boiler Unit’s Bowl Mill
.jpg)
Derivation and validation of a coal mill model for control
2012年5月1日 A simplified design schematic of a socalled roll mill is presented in Fig 2 Raw coal is transported on a conveyor belt and dropped into the mill, where it falls onto a grinding table and is crushed by rollers Primary air, blown from the bottom of the mill, picks up fine coal particles and transports them into the classifier sectionThis flow sheet and sampling map shows the process flow for a cement plant Key components include: 1) Raw materials like iron sand, silica sand, limestone, clay and gypsum being fed into crushers and mills 2) Processed materials being fed into kiln systems for heating and clinkering 3) Clinker being stored and transported to other cement plants or customers 4) A coal mill and Flow Sheet Kiln, Raw Mill N Coal Mill PDF Cement ConcreteCoal mill is an important component of the thermal power pla nt It is used to grind and dry the moisturized raw coal and transport the pulverized coal ± air mixture to the boiler Poor dynamic performance of coal mill will lead to decrease in the overall efficiency of the power plant, slow load take up rate and fr equent shut downModeling and Control of Coal MillSafe operation of coal grinding systems: Raw coal silo protection against fire and explosions Safe operation of coal grinding systems: Raw coal yard management The purchasing process for coal grinding systems needs changes Talk at a virtual seminar, November 2023 Accept the probability that the fire and explosion safety of your coal grinding Best Practices and Precautions Coal Mill Safety, Explosion and
.jpg)
Coal Mill in Cement Plant
A coal mill is also called a coal pulverizer or coal grinder It is a mechanical device used to grind raw coal into pulverized coal powders The most used coal mills in cement plants are airswept ball mills and vertical roller mills At present, most cement plants use coal as the main fuel in the clinker production process2020年4月2日 Milling system in coal power plant purposely to process the raw coal to become as pulverise fuel before enter to the Coal mill motor power (kW) 0 4171 4548 4390 4586 4562 Analysis of the Coal Milling Operations to the Boiler Parameters