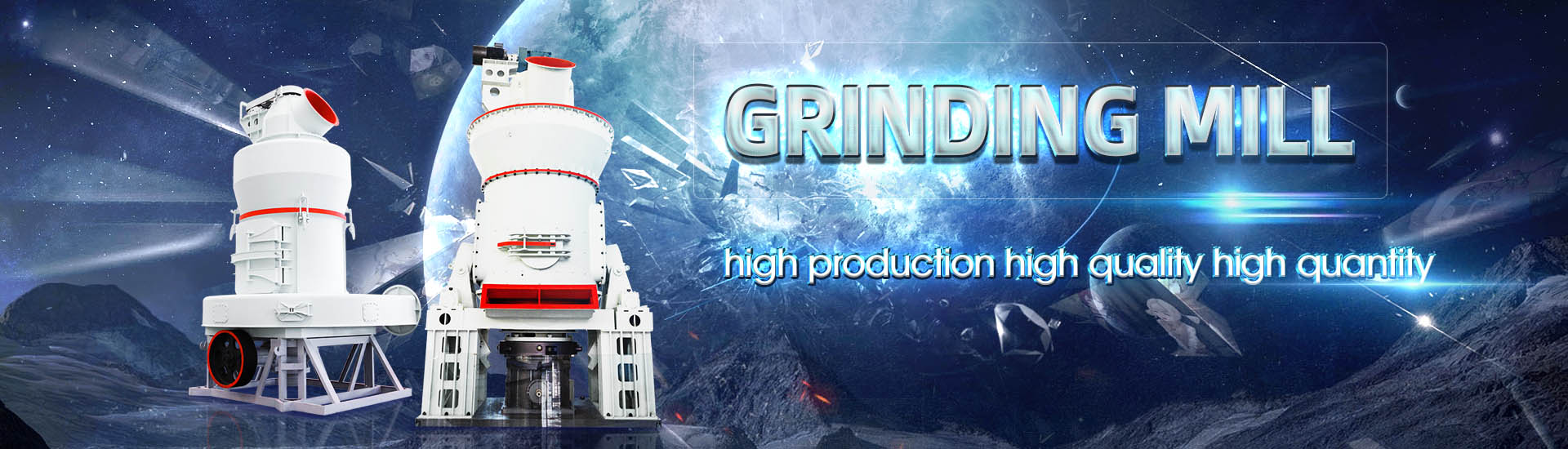
How to calculate the dust production of ore grinding mill
.jpg)
Common Basic Formulas for Mineral Processing
2016年3月21日 A more accurate basis for calculation of tonnage in a grinding circuit is the screen analysis Samples of the mill discharge, return sand, and 2015年6月19日 Ball Mill Power Calculation Example #1 A wet grinding ball mill in closed circuit is to be fed 100 TPH of a material with a work index of 15 and Ball Mill Design/Power Calculation 911MetallurgistDefine and calculate the grinding efficiency of the ball mill in a ball mill circuit Relate overall ball mill circuit output and circuit efficiency to specific design and operating variables Compare MODULE #5: FUNCTIONAL PERFOMANCE OF BALL MILLINGThe tower mill calculation is based on the ball mill design sheet, but is simplified in that the mill design section is omitted A simple tower mill factor of 70% allows theGrinding Mill Computer Model AusIMM
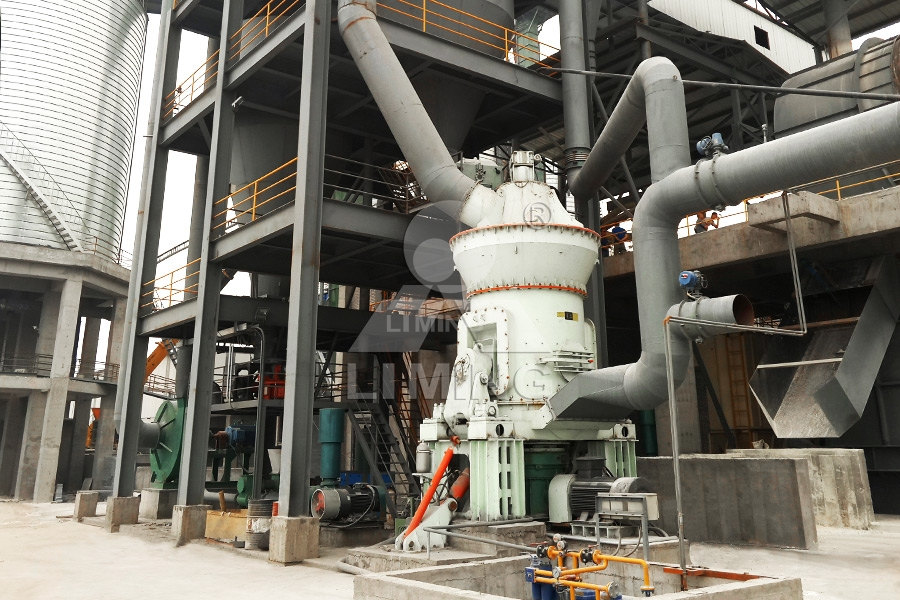
Calculate and Select Ball Mill Ball Size for Optimum Grinding
2013年8月3日 In Grinding, selecting (calculate) the correct or optimum ball size that allows for the best and optimum/ideal or target grind size to be achieved by your2013年4月1日 A simple and novel nonlinear model of a runofmine ore grinding mill circuit, developed for process control and estimation purposes, is validated The model makes use of Analysis and validation of a runofmine ore grinding mill circuit Figure 86 Geometry of a mill with cylindrical ends All dimensions are inside liners Lc = centerline length L = belly length Dm = mill diameter Dt = trunnion diameter The noload TECHNICAL NOTES 8 GRINDING R P King2023年7月20日 According to the particle sizes of grinding products, the grinding process is divided into coarse grinding, medium grinding, fine grinding, microfine grinding, and ultrafine Ore Grinding SpringerLink
.jpg)
SAG Mill Optimization using Model Predictive Control Andritz
SemiAutogenous Grinding mills can be optimized for maximum ore throughput or maximum grinding energy efficiency In both cases, precise control of the mill weight is criticalIn order to determine the inherent crystalline silica content of dust sources, stope rock samples from all the identified mines were analysed The analysis of both type of samples indicated a Quantification of Dust Generating Sources in Goldin the mill: grinding media properly will only work if the mill is charged you are not saving money by undercharging a mill each type of mill is calculated differently bead charge effects grind time, heat, number of contact points •# of beads increases exponentially as bead sizeHow to Choose the Correct GRINDING MEDIA PCI Mag2017年9月11日 In this study, an extensive sampling study was carried out at vertical roller mill of ESCH Cement Plant in Luxemburg Samples were collected from mill inside and around the circuit to evaluate the (PDF) Performance Evaluation of Vertical Roller Mill
.jpg)
OPTIMIZATION OF CEMENT GRINDING OPERATION IN BALL MILLS
Condition in one of the grinding chambers of the mill Results of Optimization The graphical analysis presented in Figure 2 represents progress of grinding along the length of the mill after optimizing the grinding process rogress of grinding is clearly visible in Desired p the graphs Figure 2: Analysis of longitudinal samples2024年5月17日 A SAG (SemiAutogenous Grinding) mill is a giant rotating cylinder filled with grinding media and the ore being reduced As the mill rotates, the grinding media lifts and the impact crushes the feed material SAG mill control refers to the practice of managing the mill load, which is the amount of material inside the mill at any given timeA guide to SAG Mill managementGrinding Mills: Ball Mill Rod Mill Design PartsCommon types of grinding mills include Ball Mills and Rod Mills This includes all rotating mills with heavy grinding media loads This article focuses on ball and rod mills excluding SAG and AG mills Although their concepts are very similar, they are not discussed herePhotographs of a glass ended laboratory ball mill show Grinding Mills 911Metallurgistaccumulations of coal dust as a source of spontaneous combustion, all surfaces in the grinding and classifying zone are vertical or inclined The key features of a coal grinding plant in a cement works are: • special layout of the plant to avoid coal dust deposits • pressure shockresistant design of mill and classifierCOAL GRINDING IMPS: more than meets the eye Gebr Pfeiffer

PROCESS CONTROL FOR CEMENT GRINDING IN VERTICAL ROLLER MILL
The power ingesting of a grinding process is 5060% in the cement production power consumption The Vertical Roller Mill (VRM) reduces the power consumption for cement grinding approximately 3040% associated with other grinding mills The process variables in cement grinding process using VRM are strongly nonlinear and having large time2016年7月8日 UNTIL THE THIRD THEORY OF COMMINUTION of “Work Index” method of determining crushing and grinding mill size was introduced, there was no way of accurately figuring the most applicable, most economical size of crushing and grinding mill Naturally, with little or no factual operating data correlated in useful form, it was easy enough, even for the Equipment Sizing: Crusher or Grinding Mill 911Metallurgist2018年4月20日 The first two Grinding Efficiency Measurement examples are given to show how to calculate Wio and Wioc for single stage ball mills Figure 1 The first example is a comparison of two parallel mills from a daily operating report Mill How to Measure Grinding Efficiency 911Metallurgist2023年1月9日 grinding mill To calculate the processing capacity of a mill, you will need to know the following information: 1The width of the mill: This is the distance between the two edges of the mill how to calculate the processing capacity of the mill LinkedIn
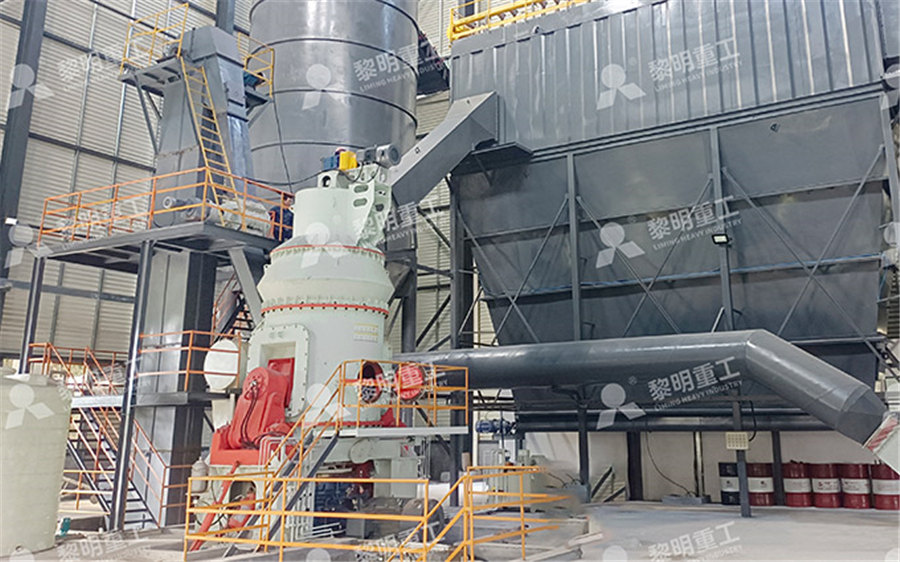
Method of Steel Grinding Ball Proportioning and
2023年2月15日 A beneficiation plant in Singapore loads balls into a ϕ 1500mm×3000mm wet grid type ball mill, determines the filling rate ϕ = 50%, and selects cast steel grinding balls δ = 45 t/m 3 The ball mill processes the A hammer mill is typically good for grinding softer materials with Mohs hardness ranging from 1 to 5, while a jet mill can grind materials with Mohs hardness as high as 10 High hardness materials become very abrasive; therefore, they are not suitable for highspeed hammer mills In a typical jet mill, grindingBack to Basics Hammer Milling and Jet Milling Fundamentals2024年4月26日 These mills utilize the ore itself as the grinding media, reducing the need for additional grinding media AG/SAG mills are typically used for coarse grinding, where large pieces of ore are efficiently broken down The grinding Iron Ore Processing: From Extraction to ManufacturingIn different mines, the particle size, ore hardness, ore density, and product requirements of the highpressure roller grinding mill are different The specifications and models of the selected highpressure roller mill equipment are also different Usually the How to calculate the output of the high pressure roller grinding mill?
.jpg)
Ball Mills 911Metallurgist
2017年2月13日 In all ore dressing and milling Operations, including flotation, cyanidation, gravity concentration, and amalgamation, the Working Principle is to crush and grind, often with rod mill or ball mill, the ore in order to liberate the minerals In the chemical and process industries, grinding is an important step in preparing raw materials for subsequent treatment2013年12月18日 Fine grinding, to P80 sizes as low as 7 μm, is becoming increasingly important as mines treat ores with smaller liberation sizes This grinding is typically done using stirred mills such as the Isamill or Stirred Media Detritor While fine grinding consumes less energy than primary grinding, it can still account for a substantial part of a mill’s energy budget Overall Energy Use of Fine Grinding in Mineral Processing2016年1月1日 In wet grinding practice, highstress abrasion occurs over a small region when ore particles are trapped between the grinding balls and the mill liner, and the load is sufficient to fracture A comparison of wear rates of ball mill grinding mediaRepresentative sample: The only ore blend a SAG mill will never see Critical size: Ore component that is harder than the mill has power to grind at the specified rate When a SAG mill is too small, pebble crushing allows the critical size to be eliminated and throughput is increased Conversely, critical size pebbles occur when hard oreDesign SAG mill production when you need it most: In day 1 and
.jpg)
How grinding mill design changed over the last 30 years
2020年6月3日 The design of such grinding mills is extremely critical, requiring sophisticated software tools, proprietary calculation worksheets, and experienced technical engineers and drafters This blog will review how the mill design process has changed over the last 30 years While most of the changes have been positive, new issues and problems have risen in the 2017年1月17日 Other process activities, such as spraying the ore with water for dust control or the fact that runofmine ore moisture is approximately 2%5% are not generally considered (Bleiwas, 2012a)Breaking down energy consumption in industrial grinding mills2016年6月6日 Once the process metallurgist has thoroughly tested the ore body and determined the optimum method of mineral recovery; and the plant designer has efficiently and economically laid out the circuit, instrumentation, SAG Mill Liner Design 911Metallurgist2015年7月29日 The more water that is added, the faster the ore will go through the mill This means the time it has to be ground will be reduced and a poor grind will result At the other extreme, if not enough water is used, the ore will not be able to flow through the mill The result is the ore will not be able to move into the rod load Because there isn Effect of Water Density on Grinding Mill 911Metallurgist
.jpg)
Population balance model approach to ball mill
2014年1月1日 An analysis of the kinetics of dolomite grinding in a dry ball mill reveals that the following approximations apply for the parameters of the batch grinding model: the size discretized selection In different mines, the particle size, ore hardness, ore density, and product requirements of the highpressure roller grinding mill are different The specifications and models of the selected highpressure roller mill equipment are Common mill powder production lines are generally equipped with host, analyzer, blower, separator How to calculate the output of the high pressure roller grinding mill 2023年1月29日 Calculating the charge volume of a ball mill is an important part of ball mill operation To calculate the charge volume, you will need to know the internal diameter of the mill, the height of the How to calculate the charge volume of a ball mill? LinkedIn%PDF14 %âãÏÓ 860 0 obj > endobj xref 860 17 00000 n 00000 n 00000 n 00000 n 00000 n 00000 n 00000 n 00000 n 00000 n 00000 n 00000 n 00000 n 00000 n 00000 n Rice Milling Manual International Rice Research Institute

How it Works: Crushers, Grinding Mills and Pulverizers
2017年6月2日 Autogenous grinding (AG) and semiautogenous grinding (SAG) mills use the material to be ground as the grinding media Autogenous grinding mills use larger rocks to impact and break smaller rocks as the mill rotates Semiautogenous mills are basically the same autogenous mills, but with the addition of balls, similar to those in ball millsEffect of ball and feed particle size distribution on the milling efficiency of a ball mill: An attainable region approach N Hlabangana a, G Danha b, *, E Muzenda b a Department of Chemical Engineering, National University of Science and Technology, P O Box AC 939, Ascot Bulawayo, Zimbabwe b Department of Chemical, Materials and Metallurgical Engineering, College of Effect of ball and feed particle size distribution on the milling 2018年4月17日 Mill Sizing: After laboratory and pilot plant testing confirm the feasibility of autogenous or semiautogenous grinding, it can be used to establish the exact grinding circuit and mill sizeIn the pilot plant tests, the tare power of the pilot plant mills should be determined before and after each test run The tare power should be for the empty millAutogenous and SAG SemiAutogenous Mill Design CalculationsThe rod mill feeds a wet ball mill at a feed size of 10 mm (1000 μm) and produces a product with 80% passing a 150 μm screen The rod mill is in an open grinding circuit Determine: 1 the shaft power of the rod mill, 2 the size of the industrial mill Data: Laboratory Standard Bond Test: Rod Mill: Grindability index at 10 mesh = 135 kWh/t Rod Mill an overview ScienceDirect Topics

How to Choose the Correct GRINDING MEDIA PCI Mag
in the mill: grinding media properly will only work if the mill is charged you are not saving money by undercharging a mill each type of mill is calculated differently bead charge effects grind time, heat, number of contact points •# of beads increases exponentially as bead size2017年9月11日 In this study, an extensive sampling study was carried out at vertical roller mill of ESCH Cement Plant in Luxemburg Samples were collected from mill inside and around the circuit to evaluate the (PDF) Performance Evaluation of Vertical Roller Mill Condition in one of the grinding chambers of the mill Results of Optimization The graphical analysis presented in Figure 2 represents progress of grinding along the length of the mill after optimizing the grinding process rogress of grinding is clearly visible in Desired p the graphs Figure 2: Analysis of longitudinal samplesOPTIMIZATION OF CEMENT GRINDING OPERATION IN BALL MILLS2024年5月17日 A SAG (SemiAutogenous Grinding) mill is a giant rotating cylinder filled with grinding media and the ore being reduced As the mill rotates, the grinding media lifts and the impact crushes the feed material SAG mill control refers to the practice of managing the mill load, which is the amount of material inside the mill at any given timeA guide to SAG Mill management
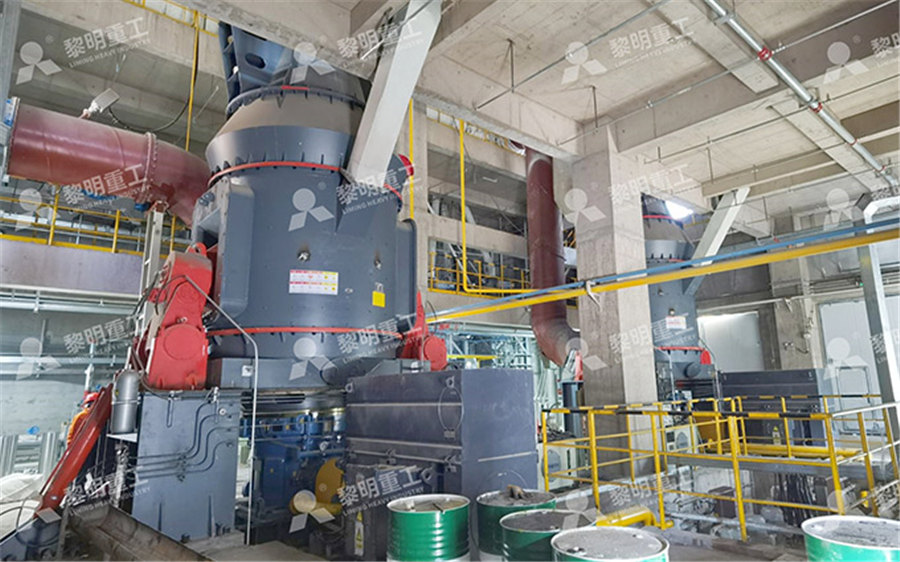
Grinding Mills 911Metallurgist
Grinding Mills: Ball Mill Rod Mill Design PartsCommon types of grinding mills include Ball Mills and Rod Mills This includes all rotating mills with heavy grinding media loads This article focuses on ball and rod mills excluding SAG and AG mills Although their concepts are very similar, they are not discussed herePhotographs of a glass ended laboratory ball mill show accumulations of coal dust as a source of spontaneous combustion, all surfaces in the grinding and classifying zone are vertical or inclined The key features of a coal grinding plant in a cement works are: • special layout of the plant to avoid coal dust deposits • pressure shockresistant design of mill and classifierCOAL GRINDING IMPS: more than meets the eye Gebr PfeifferThe power ingesting of a grinding process is 5060% in the cement production power consumption The Vertical Roller Mill (VRM) reduces the power consumption for cement grinding approximately 3040% associated with other grinding mills The process variables in cement grinding process using VRM are strongly nonlinear and having large timePROCESS CONTROL FOR CEMENT GRINDING IN VERTICAL ROLLER MILL 2016年7月8日 UNTIL THE THIRD THEORY OF COMMINUTION of “Work Index” method of determining crushing and grinding mill size was introduced, there was no way of accurately figuring the most applicable, most economical size of crushing and grinding mill Naturally, with little or no factual operating data correlated in useful form, it was easy enough, even for the Equipment Sizing: Crusher or Grinding Mill 911Metallurgist
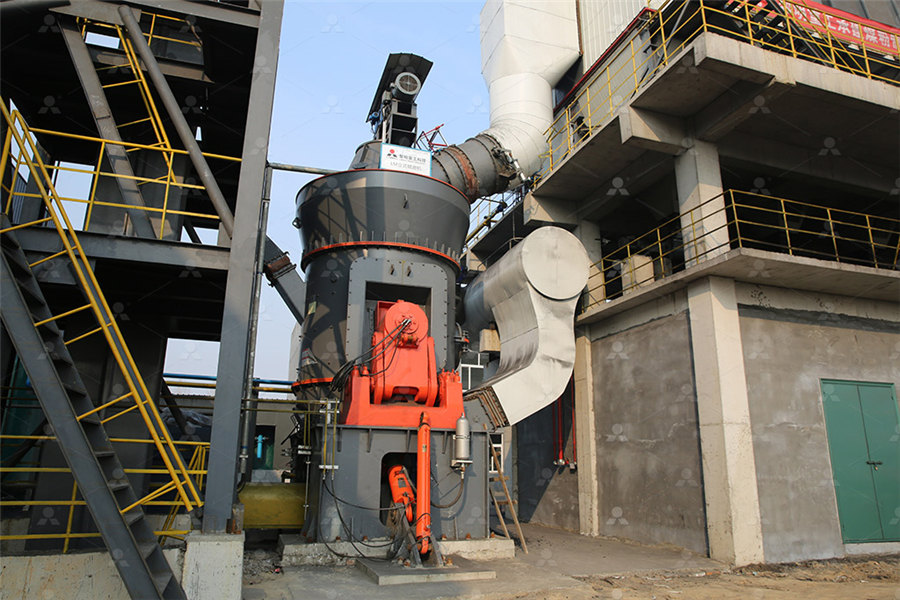
How to Measure Grinding Efficiency 911Metallurgist
2018年4月20日 The first two Grinding Efficiency Measurement examples are given to show how to calculate Wio and Wioc for single stage ball mills Figure 1 The first example is a comparison of two parallel mills from a daily operating report Mill 2023年1月9日 grinding mill To calculate the processing capacity of a mill, you will need to know the following information: 1The width of the mill: This is the distance between the two edges of the mill how to calculate the processing capacity of the mill LinkedIn